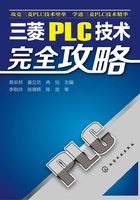
1.1 PLC概述
1.1.1 PLC的诞生与迅猛发展
(1)PLC的诞生
可编程序控制器(Programmable Logic Controller,简称PLC),是随着科学技术的进步与现代社会生产方式的转变,为适应多品种、小批量生产的需要而诞生、发展起来的一种新型的工业控制装置。
PLC是在“继电器-接触器”控制的基础上发展起来的。从1969年问世以来,虽然至今才四十余年,但由于其具有通用灵活的控制性能、可以适应各种工业环境的可靠性与简单方便的使用性能,在工业自动化各领域取得了广泛的应用。PLC技术与数控机床技术(CNC)、工业机器人技术、CAD/CAM技术已被誉为现代工业自动化技术的四大支柱。
①“继电器-接触器”控制系统存在的问题 众所周知,制造业中使用的生产设备与生产过程的控制,一般都需要通过工作机构、传动机构、原动机以及控制系统等部分实现。特别是当原动机为电动机时,还需要对电动机的启/制动、正/反转、调速与定位等动作进行控制。生产设备与生产过程的电气操作与控制部分,称为电气自动控制装置或电气自动控制系统。
最初的电气自动按制装置(包括目前使用的一些简单机械),只是一些简单的手动电器(如刀开关、正反转开关等)。这些电器只适合于电机容量小、控制要求简单、动作单一的场合。
随着科学的迅猛发展和技术的不断进步,生产机械对电气自动控制也提出了越来越高的要求,电气自动控制装置也逐步发展成了各种形式的现代电气自动控制系统。
作为常用电气自动控制系统的一种,人们习惯于把以继电器、接触器、按钮、开关等为主要器件所组成的逻辑控制系统,称为“继电器-接触器”控制系统。
“继电器-接触器”控制系统的基本特点是结构简单、生产成本低、抗干扰能力强、故障检修直观方便、适用范围广。它不仅可以实现生产设备、生产过程的自动控制,而且还可以满足大容量、远距离、集中控制的要求。因此,直到今天“继电器-接触器”控制系统仍是工业自动控制领域最基本的控制系统之一。
但是,由于“继电器-接触器”控制系统的控制元件(继电器、接触器)均为独立元件,它决定了系统的“逻辑控制”与“顺序控制”功能只能通过控制元件间的不同连接实现,因此,它不可避免地存在以下不足。
a.可靠性差,使用寿命较短,排除故障困难。由于继电器、接触器控制系统采用的是“有触点控制”形式,额定工作频率低,工作电流大,长时间连续使用易损坏触点或产生接触不良等故障,直接影响到系统工作的可靠性。如果其一个继电器损坏,其至某一对触点接触不良,都会影响整个系统的正常运行。查找和排除故障往往是非常困难的,有时可能会花费大量的时间。
b.通用性、灵活性差,总体成本较高。继电器本身并不贵,但是控制柜内部的安装、接线工作量极大,为此整个控制柜的价格是相当高的。当生产流程或工艺发生变化、需要更改控制要求时,控制柜内的元件和接线也需要作相应的变动。通常必须通过更改接线或增减控制器件才能实现,但是,这种改造的工期长、费用高,以至于有的用户宁愿放弃旧的控制柜的改造,另外再制作一台新的控制柜;有时甚至需要进行重新设计,因此难以满足多品种、小批量生产的要求。
c.体积大,材料消耗多。“继电器-接触器”控制系统的逻辑控制需要通过控制电器与电器间的连接实现,安装电器需要大量的空间,连接电器需要大量的导线,控制系统的体积大,材料消耗多。
d.运行费用高,噪声大。由于继电器、接触器均为电磁器件,在系统工作时,需要消耗较多的电能,同时,多个继电器、接触器的同时通/断,会产生较大的噪声,对工作环境造成不利的影响。
e.功能局限性大。由于“继电器-接触器”控制系统在精确定时、计数等方面的功能不完善,影响了系统的整体性能,它只能用于定时要求不高、计数简单的场合。
f.不具备现代工业控制所需要的数据通息、网络控制等功能。
正因为如此,“继电器-接触器”控制系统已难以适应现代工业复杂多变的生产控制要求与生产过程控制集成化、网络化需要。
②PLC的诞生 为了解决“继电器-接触器”控制系统存在的通用性、灵活性差,功能局限性大与通信、网络方面欠缺的问题,20世纪50年代末,人们曾设想利用计算机功能完备、通用性和灵活性强的特点来解决以上问题。但由于当时的计算机原理复杂,生产成本高,程序编制难度大,加上工业控制需要大量的外围接口设备,可靠性问题突出,使得它在面广量大的一般工业控制领域难以普及与应用。
到了20世纪60年代末,有人这样没想:能否把计算机通用、灵活、功能完善的特点与“继电器-接触器”控制系统的简单易懂、使用方便、生产成本低的特点结合起来,生产出一种面向生产过程顺序控制,可利用简单语言编程,能让完全不熟悉计算机的人也能方便使用的控制器呢?
这一设想最早由美国最大的汽车制造商——通用汽车公司(GM公司)于1968年提出。当时,该公司为了适应汽车市场多品种、小批量的生产需求,需要解决汽车生产线“继电器-接触器”控制系统中普遍存在的通用性、灵活性差的问题,提出了对一种新颖控制器的十大技术要求,并面向社会进行招标。十大技术要求具体如下:
a.编程方便,且可以在现场方便地编辑、修改控制程序;
b.价格便宜,性能/价格比要高于继电器系统;
c.体积要明显小于继电器控制系统;
d.可靠性要明显高于继电器控制系统;
e.具有数据通信功能;
f.输入可以是AC115V;
g.输出驱动能力在AC115V/2A以上;
h.硬件维护方便,最好采用“插接式”结构;
i.扩展时,只需要对原系统进行很小的改动;
j.用户存储器容量至少可以扩展到4KB。
以上就是著名的“GM十条”。这些要求的实质内容是提出了将“继电器-接触器”控制系统的简单易懂、使用方便、价格低廉的优点与计算机的功能完善、灵活性、通用性好的优点结合起来,将“继电器-接触器”控制系统的硬连线逻辑转变为计算机的软件逻辑编程的设想。
根据以上要求,美国数字设备公司(DEC公司)在1969年首先研制出了全世界第一台可编程控制器,并称之为“可编程序逻辑控制器”(Programmable Logic Controller,简称PLC)。该样机在GM公司的应用获得了成功。此后,PLC得到了快速发展,并被广泛用于各种开关量逻辑运算与处理的场合。
早期PLC的硬件主要由分立元件与小规模集成电路构成,它虽然采用了计算机技术,但指令系统、软件与功能相对较简单,一般只能进行逻辑运算的处理,同时通过简化计算机的内部结构与改进可靠性等措施,使之能与工业环境相适应。
正因为如此,在20世纪70年代初期曾经出现过一些由二极管矩阵、集成电路等器件组成的所谓“顺序控制器”;20世纪70年末期曾经出现过以MC14500工业控制单元(Industrial Control Unit,简称ICU)为核心,由8通道数据选择器(MC14512)、指令计数器(MC14516)、8位可寻址双向锁存器(MC14599)、存储器(2732)等组成的“ICU可编程序控制器”等产品。这些产品与PLC相比,虽然具有一定的价格优势,但最终还是由于其可靠性、功能等多方面的原因,未能得到进一步的推广与发展;而PLC则随着微处理器价格的全面下降,最终以其优良的性能价格比,得到了迅猛发展,并最终成为了当代工业自动控制技术的重要支柱技术之一。
(2)PLC的迅猛发展
PLC技术随着计算机和微电子技术的发展而迅猛发展,由最初的1位机发展为8位机。随着微处理器CPU和微型计算机技术在PLC中的应用,形成了现代意义上的PLC。进入20世纪80年代以来,随着大规模和超大规模集成电路等微电子技术的迅猛发展,以16位和32位微处理器构成的微机化PLC得到了惊人的发展,使PLC在概念、设计、性能价格比以及应用等方面都有了新的突破。不仅控制功能增强,功耗、体积减小,成本下降,可靠性提高,编程和故障检测更为灵活方便,而且远程I/O和通信网络、数据处理以及人机界面(HMI)也有了长足的发展。现在PLC不仅能得心应手地应用于制造业自动化,而且还可以应用于连续生产的过程控制系统,所有这些已经使其成为现代工业的四大支柱之一,即使在现场总线技术已成为自动化技术应用热点的今天,PLC仍然是现场总线控制系统中不可缺少的首选控制器。
总结PLC的发展历程,大致经历了五个阶段。
①初级阶段 从第一台PLC问世到20世纪70年代中期。这个时期的PLC功能简单,主要完成一般的继电器控制系统的功能,即顺序逻辑、定时和计数等,编程语言为梯形图。
②崛起阶段 从20世纪70年代中期到80年代初期。由于PLC在取代“继电器-接触器”控制系统方面的卓越表现,所以自从它在电气自动控制领域开始普及应用后得到了飞速的发展。这个阶段的PLC在其控制功能方面增强了很多,例如数据处理、模拟量的控制等。
③成熟阶段 从20世纪80年代初期到90年代初期。这之前的PLC主要是单机应用和小规模、小系统的应用;但随着对工业自动化技术水平、控制性能和控制范围要求的提高,在大型的控制系统(如冶炼、饮料、造纸、烟草、纺织、污水处理等)中,PLC也展示出了其强大的生命力。对这些大规模、多控制器的应用场合,就要求PLC控制系统必须具备通信和联网功能。这个时期的PLC顺应时代要求,在大型的PLC中一般都扩展了遵守一定协议的通信接口。
④飞速发展阶段 从20世纪90年代初期到90年代末期。由于对模拟量处理功能和网络通信功能的提高,PLC控制系统在过程控制领域也开始大面积使用。随着芯片技术、计算机技术、通信技术和控制技术的发展,PLC的功能得到了进一步的提高。现在PLC不论从体积上、人机界面功能、端子接线技术,还是从内在的性能(速度、存储容量等)、实现的功能(运动控制、通信网络、多机处理等)方面都远非过去的PLC可比。从20世纪80年代以后,是PLC发展最快的时期,年增长率一直都保持在30%~40%之间。
⑤开放性、标准化阶段 从20世纪90年代中期以后。其实关于PLC开放性的工作在20世纪80年代就已经展开;但由于受到各大公司利益的阻挠和技术标准化难度的影响,这项工作进展得并不顺利。所以,PLC诞生后的近30年时间里,各种PLC通信标准、编程语言等方面都存在着不兼容的地方,这为在工业自动化中实现互换性、互操作性和标准化都带来了极大的不便,现在随着PLC国际标准IEC61131的逐步完善和实施,特别是IEC61131-3标准编程语言的推广,使得PLC真正走入了一个开放性和标准化的新时代。
(3)PLC进一步的飞速发展趋势
PLC总的发展趋势是向高集成度、小体积、大容量、高速度、易使用、高性能、信息化、软PLC、标准化、与现场总线技术紧密结合等方向发展。
①向小型化、专用化、低成本方向发展 随着微电子技术的发展,新型器件性能的大幅度提高,价格却大幅度降低,使得PLC结构更为紧凑,操作使用十分简便。从体积上讲,有些专用的微型PLC仅有一块香皂大小。PLC的功能不断增加,将原来大、中型PLC才有的功能部分地移植到小型PLC上,如模拟量处理、复杂的功能指令和网络通信等。PLC的价格也不断下降,真正成为现代电气控制系统中不可替代的首选控制装置。据统计,小型和微型PLC的市场份额一直保持在70%~80%之间,所以对PLC小型化的追求永远不会停止。
②向大容量、高速度、信息化方向发展 现在大中型PLC采用多微处理器系统,有的采用了32位微处理器,并集成了通信联网功能,可同时进行多任务操作,运算速度、数据交换速度及外设响应速度都有大幅度提高,存储存量大大增加,特别是增强了过程控制和数据处理的功能。为了适应工厂控制系统和企业信息管理系统日益有机结合的要求,信息技术也渗透到了PLC中,如设置开放的网络环境、支持对象链接与嵌入(OLE for Process Control,OPC)技术,等等。
③智能化模块的发展 为了实现某些特殊的控制功能,PLC制造商开发出了许多智能化的I/O模块。这些模块本身带有CPU,使得占用主CPU的时间很少,减少了对PLC扫描速度的影响,提高了整个PLC控制系统的性能。它们本身有很强的信息处理能力和控制功能,可以完成PLC的主CPU难以兼顾的功能。由于在硬件和软件方面都采取了可靠性和便利化的措施,所以简化了某些控制系统的系统设计和编程。典型的智能化模块主要有高速计数模块、定位控制模块、温度控制模块、闭环控制模块、以太网通信模块和各种现场总线协议通信模块等。
④人机界面(接口)的发展 人机界面(接口)(Human-Machine Interface,HMI)在工业自动化系统中起着越来越重要的作用,PLC控制系统在HMI方面的进展主要体现在以下几个方面。
a.编程工具的发展。过去绝大部分中小型PLC仅提供手持式编程器,编程人员通过编程器和PLC打交道。首先是把编制好的梯形图程序转换成语句表程序,然后使用编程器一个字符、一个字符地敲到PLC内部;另外,调试时也只能通过编程器观察很少的信息。现在编程器已被淘汰,基于Windows的编程软件不仅可以对PLC控制系统的硬件组态,即设置硬件的结构、类型、各通信接口的参数等,而且可以在屏幕上直接生成和编辑梯形图、语句表、功能块图和顺序功能图程序,并且可以实现不同编程语言之间的自动转换。程序被编译后可下载到PLC,也可以将用户程序上传到计算机。编程软件的调试和监控功能也远远超过手持式编程器,可以通过编程软件中的监视功能实时观察PLC内部各存储单元的状态和数据,为诊断分析PLC程序和工作过程中出现的问题带来了极大的方便。
b.功能强大、价格低廉的HMI。过去在PLC控制系统中进行参数的设定和显示时非常麻烦,对输入设定参数要使用大量的拨码开关组,对输出显示参数要使用数码管,它们不仅占据了大量的I/O资源、而且功能少、接线烦琐。现在各种单色、彩色的显示设定单元、触摸屏、覆膜键盘等应有尽有,它们不仅能完成大量数据的设定和显示,还能直观形象地显示动态图形画面和完成数据处理等功能。
c.基于PC的组态软件。在中大型的PLC控制系统中,仅靠简单的显示设定单元已不能解决人机界面的问题,所以基于Windows的PC机成为了最佳的选择。配合适当的通信接口或适配器,PC机就可以和PLC之间进行信息的互换,再配合功能强大的组态软件,就能完成复杂的和大量的画面显示、数据处理、报警处理、设备管理等任务。这些组态软件国外的品牌有WinCC、iFIX、Intouch等,国产知名公司有业控、力控等。现在组态软件的价格已下降到非常低的位置,所以在环境较好的应用现场,使用PC加组态软件来取代触摸屏的方案也是一种不错的选择。
⑤在过程控制领域的使用以及PLC的冗余特性 虽然PLC的强项是在制造业领域使用,但随着通信技术、软件技术和模拟量控制技术发展并不断地融合到PLC中,它现在也被广泛地应用到了过程控制领域。但在过程控制系统中使用必然要求PLC控制系统具有更高的可靠性。现在世界上顶尖的自动化设备供应商提供的大型PLC中,一般都增加了安全性和冗余性的产品,并且符合IEC61508标准的要求。该标准主要为可编程电子系统内的功能性安全设计而制定,为PLC在过程控制领域使用的可靠性和安全设计提供了依据。现在PLC的冗余产品包括CPU系统、I/O模块以及热备份冗余软件等。大型PLC以及冗余技术一般都是在大型的过程控制系统中使用。
⑥开放性和标准化 世界上大大小小的电气设备制造商几乎都推出了自己的PLC产品,但由于没有一个统一的规范和标准,所有PLC产品在使用上都存在着一些差别,而这些差别的存在对PLC产品制造商和用户都是不利的。一方面它增加了制造商的开发费用;另一方面也增加了用户学习和培训的负担。这些非标准化的使用结果,使得程序的重复使用和可移植性都成为不可能的事情。
现在的PLC采用了各种工业标准,如IEC61131、IEEE802.3以太网、TCP/IP、UDP/IP等,以及各种事实上的工业标准,如Windows NT、OPC等。特别是PLC的国际标准IEC61131,为PLC从硬件设计、编程语言、通信联网等各方面都制定了详细的规范。其中的第3部分IEC61131-3是PLC的编程语言标准。IEC61131-3的软件模型是现代PLC的软件基础,是整个标准的基础性的理论工具。它为传统的PLC突破了原有的体系结构(即在一个PLC系统中装插多个CPU模块),并为相应的软件设计奠定了基础。IEC61131-3不仅在PLC系统中被广泛采用,在其他的工业计算机控制系统、工业编程软件中也得到了广泛的应用。越来越多的PLC制造商都在尽量往该标准上靠拢,尽管由于受到硬件和成本等因素的制约,不同的PLC和IEC61131-3兼容的程度有大有小,但这毕竟已成为了一种发展的强劲趋势。
⑦通信联网功能的增强和易用化 在中大型PLC控制系统中,需要多个I/O以及智能仪器仪表连接成一个网络,进行信息的交换。PLC通信联网功能的增强使它更容易与PC和其他智能控制设备进行互联,使系统形成一个统一的整体,实现分散控制和集中管理。现在许多小型,甚至微型PLC的通信功能也十分强大。PLC控制系统通信的介质一般有双绞线或光纤,具备常用的串行通信功能。在提供网络接口方面,PLC向两个方向发展:一是提供直接挂接到现场总线网络中的接口(如PROFIBUS、AS-i等);二是提供Ethernet接口,使PLC直接接入以太网。
⑧软PLC的概念 所谓软PLC就是在PC机的平台上,在Windows操作环境下,用软件来实现PLC的功能。这个新概念是在20世纪90年代中期提出的。安装有组态软件的PC机既然能完成人机界面的功能,为何不能把PLC的功能也用软件来实现呢?PC机价格便宜,有很强的数学运算、数据处理、通信和人机交互的功能。如果软件功能完善,则利用这些软件可以方便地进行工业控制流程的实时和动态监控,完成报警、历史趋势和各种复杂的控制功能,同时节约控制系统的设计时间。配上远程I/O和智能I/O后,软PLC也能完成复杂的分布式的控制任务。在随后的几年,软PLC的开发也呈现了上升的势头。但后来软PLC并没有出现人们希望的那样占据相当市场份额的局面,这只是因为软PLC上本身存在的一些缺陷造成的:
a.软PLC对维护和服务人员的要求较高;
b.电源故障对系统影响较大;
c.在占绝大多数的低端应用场合,软PLC没有优势可言;
d.在可靠性方面和对工业环境的适应性方面,和PLC无法比拟;
e.PC机发展速度太快,技术支持不容易保证。
随着生产厂家的努力和技术的发展,软PLC肯定也能在其最适合的地方得到认可。
⑨PAC的概念 在工控界,对PLC的应用情况有一个“80-20”法则,即:
a.80%的PLC上应用场合都是使用简单的低成本的小型PLC;
b.78%(接近80%)的PLC都是使用的开关量(或数字量);
c.80%的PLC应用使用20个左右的梯形图指令就可解决问题。
其余20%的应用要求或控制功能要求使用PLC无法轻松满足,而需要使用别的控制手段或PLC配合其他手段来实现。于是,一种能结合PLC的高可靠性和PC机的高级软件功能的新产品应运而生。这就是PAC(Programmable Automation Controller),或基于PC机架构的控制器。它包括了PLC的主要功能,以及PC-based控制中基于对象的、开放的数据格式和网络能力。其主要特点是使用标准的IEC61131-3编程语言、具有多控制任务处理功能,兼具PLC和PC机的优点。PAC主要用来解决那些所谓的剩余的20%的问题,但现在一些高端PLC也具备了解决这些问题的能力,加之PAC是一种较新的控制器,所以其应用市场还有待于进一步的开发和推动。
⑩PLC在现场总线控制系统中的位置 现场总线的出现,标志着自动化技术步入了一个新的时代。现场总线(field bus)是“安装在制造和过程区域的现场装置与控制室内的自动控制装置之间的数字式、串行、多点通信的数据总线”,是当前工业自动化的热点之一。随着3C(Computer Control and Communication)技术的迅猛发展,使得解决自动化信息孤岛的问题成为可能。采用开放化、标准化的解决方案,把不同厂家遵守同一协议规范的自动化设备连接成控制网络并组成系统已成为可能。现场总线采用总线通信的拓扑结构,整个系统处在全开放、全数字、全分散的控制平台上。从某种意义上说,现场总线技术给自动控制领域所带来的变化是革命性的。到今天,现场总线技术已基本走向成熟和实用化。现场总线控制系统的优点是:
a.节约硬件数量与投资;
b.节省安装费用;
c.节省维护费用;
d.提高了系统的控制精度和可靠性;
e.提高了用户的自主选择权。
在现场总线控制系统FCS(Field bus Control System)中,增加了相关通信协议接口的PLC,既可以作为主站成为FCS的主控制器,也可以作为智能化的从站实现分散式的控制。一些软PLC配合通信板卡也可以作为FCS的主站。
综上所述,将来的新一代PLC将要实现:
①CPU处理速度进一步加快;
②控制系统分散化;
③可靠性进一步提高;
④控制与管理功能一体化;
⑤向两极化(大型化和小型化)方向发展;
⑥编程语言和编程工具向标准化和多样化发展;
⑦I/O组件标准化、功能组件智能化;
⑧通信网络化;
⑨大记忆容量,快处理速度发展;
⑩发展故障诊断技术和容错技术。
PLC的新发展还可概括为以下几个方面:
a.在系统构成规模上,向超大型、超小型方向发展;
b.在增强控制能力和扩大应用范围上,进一步开发各种智能I/O模块;
c.在系统集成方面进一步提高安全性、高可靠性;
d.在控制与管理功能一体化方面,进一步增强通信联网能力;
e.在编程语言与编程工具方面,达到多样化、高级化、标准化。
目前,世界上有二百多个厂家生产三百多种PLC产品,比较著名的厂家有美国的AB(被ROCKWELL收购)、GE、MODICON(被SCHNEIDER收购),日本的三菱、欧姆龙、富士、松下电工,德国的西门子和法国的施耐德公司等。在全球PLC制造商中,根据美国Automation Research Corp(ARC)调查,世界PLC主导厂家的五霸分别为日本的MIT-SUBISHI(三菱)公司、OMRON(欧姆龙)公司;德国的SIEMENS(西门子)公司;美国的Allen-Bradley(AB)公司;法国的SCHNEIDER(施耐德)公司。其销售额约占全球总销售额的2/3。
我国的PLC生产目前也有一定的发展,小型PLC已批量生产;中型PLC已有产品;大型PLC已开始研制。国内PLC形成产品化的生产企业约三十多家,国内产品市场占有率不超过10%,主要生产单位有苏州电子计算机厂、苏州机床电器厂、上海兰星电气有限公司、天津市自动化仪表厂、杭州通灵控制电脑公司、北京机械工业自动化所和江苏嘉华实业有限公司等。目前国内产品在价格上占有明显的优势,而在质量上还稍有欠缺和不足。随着新一代开放式PLC走向市场,国内的生产厂家,如和利时、浙大中控等生产的基于IEC61131-3编程语言的PLC有可能会在未来的PLC市场中占有一席之地。