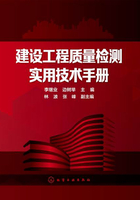
第三节 砂石骨料
在普通混凝土中,骨料是起着骨架和支撑作用,抑制水泥硬化收缩的粒状松散材料。骨料按粒径可分为细骨料和粗骨料。骨料是混凝土的主要组成材料,一般占混凝土体积的80%左右。普通混凝土中采用的骨料材料,主要是砂子和石子。
一、细骨料
根据国家标准《建设用砂》(GB/T 14684—2011)中的规定,粒径在4.75mm以下的骨料称为细骨料。砂子分为天然砂和人工砂两类。天然砂主要有河砂、湖砂、淡化海砂和山砂;人工砂包括机制砂和混合砂。建筑工程一般多采用天然河砂。《建设用砂》中还规定,砂子按细度模数(MX)大小不同,可分为粗砂、中砂、细砂3种规格;按技术要求可分为Ⅰ类、Ⅱ类和Ⅲ类3个类别。其中,Ⅰ类砂宜用于强度等级大于C60的混凝土,Ⅱ类砂宜用于强度等级C30~C60的混凝土,Ⅲ类砂宜用于强度等级小于C30的混凝土和建筑砂浆。
(一)细骨料质量要求
配制普通混凝土时要选用质量良好的砂子,对砂的质量要求主要包括有害杂质的含量、砂的坚固性、砂的碱活性、粗细程度和颗粒级配等。
(1)有害杂质的含量 用于配制混凝土的砂子,要求其清洁、不含过多的杂质,以保证混凝土的质量。但实际上砂中常含有云母、轻物质、有机物、硫化物、氯化物、黏土、泥块等有害杂质,这些杂质混合或黏附在砂的表面,不仅影响水泥与砂的黏结,严重降低混凝土的强度,而且还会增加混凝土的用水量,加大混凝土的收缩,降低混凝土的耐久性。硫酸盐和硫化物对水泥石有腐蚀作用,氯化物会加剧钢筋混凝土中钢筋的锈蚀。因此,对砂中的有害杂质含量,应当进行严格控制。
根据国家标准《建设用砂》(GB/T 14684—2011)中的规定,用于普通混凝土的砂中有害杂质的含量应符合表2-11中的要求。
表2-11 混凝土用砂有害杂质要求

注:贝壳含量只适用于淡化海砂,其他砂不做要求。
(2)砂的坚固性 砂的坚固性是指砂在自然环境或其他物理、化学因素作用下,抵抗破裂的能力。天然砂通常用硫酸钠溶液干湿循环5次后的质量损失来表示其坚固性的高低,人工砂通常采用压碎指标进行检验。混凝土所用的天然砂和人工砂坚固性要求必须符合表2-12中的规定。
表2-12 砂的坚固性要求

(3)粗细程度和颗粒级配 砂的粗细程度是指用不同粒径的砂混合在一起的平均粗细程度。根据砂的粗细程度不同,砂可分为粗砂、中砂和细砂。配制混凝土所用砂的粗细程度应适宜。试验充分证明:在砂用量相同的条件下,若砂子过细,则砂的总表面积就较大,需要包裹在砂粒表面的水泥浆数量多,水泥用量必然就大;若砂子过粗,虽然能减少水泥的用量,但混凝土拌合物的黏聚性变差,容易发生分层离析,严重影响混凝土的质量。所以,用于拌制普通混凝土的砂子不宜过粗,也不宜过细。
砂的颗粒级配是指大小不同粒径的砂粒相互间的搭配情况。在混凝土中砂粒之间的空隙是由水泥浆所填充,为达到节约水泥和提高强度的目的,就应尽量减小砂粒之间的空隙。从图2-1中可以看出:相同粒径的砂,砂粒之间的空隙则大[见图2-2(a)];把2种不同粒径的砂搭配起来,砂粒之间的空隙有所减小[见图2-2(b)];把3种不同粒径的砂搭配起来,砂粒之间的空隙更小[见图2-2(c)]。由此可见,减小砂粒之间的空隙的唯一方法是使大小不同粒径的砂相互搭配,这样才能使砂的级配良好。砂的颗粒级配应符合表2-13中的规定。

图2-2 砂子的颗粒级配示意
表2-13 砂的颗粒级配

配制普通混凝土所用的砂,当其颗粒较粗、级配良好时,砂的空隙率和总表面积均较小,这样不仅可以节约水泥,降低工程造价,而且还可以提高混凝土的强度和耐久性。因此,严格控制砂的粗细程度和颗粒级配具有重大的技术经济意义。
(4)含泥量、泥块含量和石粉含量 天然砂中含泥量是指粒径小于0.075mm的颗粒含量;泥块含量是指原粒径大于1.18mm,经过水洗、手捏后小于0.60mm的颗粒含量。人工砂中石粉含量是指粒径小于0.075mm的颗粒含量;泥块含量同天然砂。含泥量多会降低骨料与水泥石的黏结力,影响混凝土的强度和耐久性。泥块比泥土对混凝土的性能影响更大,因此必须严格控制其含量。
天然砂的含泥量和泥块含量应符合表2-14中的规定;人工砂的石粉含量和泥块含量应符合表2-15中的规定。
表2-14 天然砂的含泥量和泥块含量

表2-15 人工砂的石粉含量和泥块含量

①根据使用地区和用途,在试验验证的基础上,可由供需双方协商确定。
(5)表观密度、松散堆积密度和空隙率 根据《建设用砂》(GB/T 14684—2011)中的规定,砂的表观密度不小于2500kg/m3,其松散堆积密度不小于1400kg/m3,空隙率不大于44%。
(6)碱集料反应 碱集料反应是指水泥、外加剂等混凝土组成物及环境中的碱与骨料中碱活性矿物,在潮湿环境下缓慢发生并导致混凝土开裂破坏的膨胀反应。现行规范中规定,经碱集料反应试验后,试件应无裂缝、酥裂、胶体外溢等现象,在规定的试验龄期膨胀率应小于0.10%。
(二)细骨料的取样
(1)取样方法
检验批的确定:按同分类、同规格、同适用等级及日产量每600t为一批,不足600t也为一批;日产量超过2000t,按1000t为一批,不足1000t也为一批。
①在料堆上取样时,取样部位应均匀分布。取样前先将取样部位表层铲除,然后从不同部位随机抽取大致等量的砂8份,组成一组样品。
②从皮带运输机上取样时,应用与皮带机等宽的接料器在皮带运输机机头出料处全断面定时随机抽取大致等量的砂4份,组成一组样品。
③从火车、汽车、轮船上取样时,从不同部位和深度随机抽取大致等量的砂4份,组成一组样品。
(2)取样数量 单项取样的最少取样数量应符合表2-16中的规定。若进行几项试验时,如能保证试样经一项试验后不致影响另一项的试验结果,可用同一试样进行几项不同的试验。
表2-16 单项取样的最少取样数量

(3)试样处理
①用分料器法:将样品在潮湿状态下拌和均匀,然后通过分料器,取接料斗中的其中一份再次通过分料器,重复上述过程,直至把样品分缩到试验所需量为止。
②人工四分法:将所取试样置于平板上,在潮湿状态下拌和均匀,并堆成厚度约为20mm的圆饼,然后沿互相垂直的2条直径把圆饼分成大致相等的4份,取其中对角线的2份重新拌匀,再堆成圆饼。重复上述过程,直至把样品分缩到试验所需量为止。
③堆积密度、机制砂的坚固性试验所用试样可不经缩分,在拌匀后直接进行试验。
(三)细骨料的检测
1.砂的检测项目
天然砂必须检测项目为筛分析、含泥量、泥块含量。人工砂必须检测项目为筛分析、石粉含量(含亚甲蓝试验)、泥块含量、压碎指标。如果检测不合格,应重新取样;对不合格项进行加倍复检。如果仍不能满足标准要求,应按不合格品处理。
2.砂的筛分析检测
(1)检测目的 通过砂的筛分析,评定砂的颗粒级配和粗细程度。
(2)仪器设备 鼓风烘箱(温度控制在105℃±5℃)、天平(称量1000g,感量1g)、标准筛(孔径为150μm、300μm、600μm、1.18mm、2.36mm、4.75mm、9.50mm的方孔筛各一只)、摇筛机、搪瓷盘、毛刷等。
(3)检测步骤
①按规定方法取样,并分缩至约1100g。放在105℃±5℃的烘箱中烘至恒重,待冷却至室温后,先筛除大于9.50mm的颗粒,并计算出其筛余百分率,再分为大致相等的2份备用。
②称取试样500g,精确至1g。将试样倒入按孔径大小从上到下组合的套筛(附筛底)上,然后进行筛分。
③先在摇筛机上筛分10min,取下套筛,按筛孔大小顺序再逐个手筛,筛至每分钟通过量小于试样总量0.1%为止。通过的试样并入下一筛中,并和下一号筛中的试样一起过筛,按这样的顺序进行,直至各号筛全部筛完为止。
④称量各号筛的筛余量,精确至1g。如每号筛的筛余量与筛底的剩余量之和同原试样质量之差超过1%时,应重新试验。
(4)结果计量与评定
①计算分计筛余百分率:各号筛的筛余量与试样总量之比,精确至0.1%,填入表2-17。
表2-17 砂的筛余量、分计筛余百分率、累计筛余百分率的关系

注:ai=mi/500。
②计算累计筛余百分率:该号筛的筛余百分率加上该号筛以上各筛的筛余百分率之和,精确至0.1%,填入表2-12中。
③根据砂的累计筛余百分率,可以计算出砂的细度模数,划分砂的级配区,以评定砂的粗细程度和颗粒级配。砂的粗细程度用细度模数(MX)表示,可用式(2-3)进行计算:
(2-3)
④累计筛余百分率取2次检测结果的算术平均值,精确至1%。
⑤细度模数取2次检测结果的算术平均值,精确至1%;当2次检测的细度模数之差超过0.20时,应重新检测。根据细度模数评定该试样的粗细程度。
⑥根据各号筛的累计筛分百分率,查表2-8评定该试样的颗粒级配。
3.砂的含泥量检测
(1)检测目的 评定砂中的含泥量是否符合现行规范中的要求,能否用于指定工程中。
(2)仪器设备 包括鼓风烘箱(温度控制在105℃±5℃)、天平(称量1000g,感量1g)、方孔筛(孔径为75μm及1.18mm的筛各1只)、容器(深度大于250mm)、搪瓷盘、毛刷等。
(3)检测步骤
①按规定方法取样,最少取样量为4400g,并缩分至约1100g,放在105℃±5℃的烘箱中烘至恒重,待冷却至室温后,分为大致相等的2份备用。
②称取试样500g,精确至1g。将试样倒入淘洗容器中,注入清水,使水面高于试样面约150mm,充分搅拌均匀后,浸泡2h。然后用手在水中淘洗试样,使尘屑、淤泥和黏土与砂粒分离,把浑水缓缓倒入1.18mm及75μm的套筛上(从大到小排列),滤去小于75μm的颗粒。试验前,筛子的两面应先用水润湿,在整个过程中应小心防止砂粒流失。
③再向容器中注入清水,重复上述操作,直至容器内的水目测清澈为止。
④用水淋洗剩余在筛上的细粒,并将75μm筛放在水中(使水面略高出筛中砂粒的上表面)来回摇动,以充分洗掉小于75μm的颗粒,然后将2只筛余颗粒和清洗容器中已经洗净的试样一并倒入搪瓷盘,放在105℃±5℃的烘箱中烘至恒重,待冷却至室温后,称出其质量,精确至0.1g。
(4)结果计量与评定 可按式(2-4)计算砂的含泥量,精确至0.1%:
Qa=(G0-G1)/G0×100% (2-4)
式中,Qa为砂的含泥量,%;G1为检测后烘干试样的质量,g;G0为检测前烘干试样的质量,g。
砂的含泥量取2个试样检测结果的算术平均值。根据计算结果查表2-17进行评定。
4.砂的泥块含量检测
(1)检测目的 评定砂中泥块含量是否符合现行规范中的要求,能否用于指定工程中。
(2)仪器设备 包括鼓风烘箱(温度控制在105℃±5℃)、天平(称量1000g,感量1g)、方孔筛(孔径为600μm及1.18mm的筛各1只)、容器(深度大于250mm)、搪瓷盘、毛刷等。
(3)检测步骤
①按规定方法取样,最少取样量为20.0kg,并缩分至约5000g,放在105℃±5℃的烘箱中烘至恒重,待冷却至室温后,筛除小于1.18mm的颗粒,分为大致相等的2份备用。
②称取试样200g,精确至0.1g。将试样倒入淘洗容器中,注入清水,使水面高于试样面约150mm,充分搅拌均匀后,浸泡24h。然后用手在水中碾碎泥块,再把试样放在600μm筛上,用水淘洗,直至容器内的水目测清澈为止。
③将保留下来的试样小心地从筛中取出,装入搪瓷盘,放在105℃±5℃的烘箱中烘至恒重,待冷却至室温后,称出其质量,精确至0.1g。
(4)结果计量与评定 可按式(2-5)计算砂的含泥量,精确至0.1%:
Qb=(G1-G2)/G1×100% (2-5)
式中,Qb为砂的泥块含量,%;G1为1.18mm筛筛余试样的质量,g;G2为检测后烘干试样的质量,g。
砂的含泥量取2个试样检测结果的算术平均值。根据计算结果查表2-17进行评定。
5.砂的表观密度检测
(1)检测目的 测定砂的表观密度为计算砂的空隙率和进行混凝土混合比设计提供依据。
(2)仪器设备 鼓风烘箱(温度控制在105℃±5℃)、天平(称量10kg或1000g,感量1g)、容量瓶(500mL)、干燥器、搪瓷盘、滴管、毛刷等。
(3)检测步骤
①按规定方法取样,最少取样量为2600g,并缩分至约660g,放在105℃±5℃的烘箱中烘至恒重,待冷却至室温后,筛除小于1.18mm的颗粒,分为大致相等的2份备用。
②称取试样300g,精确至0.1g。将试样装入容量瓶,注入冷开水至接近500mL的刻度处,用手旋转摇动容量瓶,使砂样充分摇动,排出气泡,塞紧瓶盖,静止24h。然后用滴管小心加水至容量瓶500mL的刻度处,塞紧瓶盖,擦干瓶外水分,称出其质量,精确至1g。
③倒出瓶内的水和试样,洗净容量瓶,再向容量瓶内注入与上述水温相差不超过2℃的冷开水(15~25℃)至500mL的刻度处,塞紧瓶盖,擦干瓶外水分,称出其质量,精确至1g。
(4)结果计量与评定 可按式(2-6)计算砂的表观密度含泥量,精确至10kg/m3:
ρ0=[G0/(G0+G2-G1)]×ρ水 (2-6)
式中,ρ0为砂的表观密度,kg/m3;ρ水为水表观密度,1000kg/m3;G0为烘干试样的质量,g;G1为试样、水及容量瓶的总质量,g;G2为水及容量瓶的总质量,g。
砂的表观密度取2次检测结果的算术平均值,精确至10kg/m3;如果2次检测结果之差大于20kg/m3,应重新检测。砂的表观密度的计算结果应大于2500kg/m3。
6.砂的堆积密度与空隙率检测
(1)检测目的 测定砂的堆积密度为计算砂的空隙率和进行混凝土混合比设计提供依据。
(2)仪器设备包括鼓风烘箱(温度控制在105℃±5℃)、天平(称量10kg或1000g,感量1g)、容量筒(圆柱形金属筒,内径108mm,净高109mm,壁厚2mm,筒底厚5mm,容积为1L)、方孔筛(筛孔为4.75mm)、垫棒(直径10mm,长500mm的圆钢)、直尺、漏斗或料勺、搪瓷盘、毛刷等。
(3)检测步骤
①按规定方法取样,最少取样量为5000g,用搪瓷盘装取试样约3L,放在105℃±5℃的烘箱中烘至恒重,待冷却至室温后,筛除小于4.75mm的颗粒,分为大致相等的2份备用。
②松散堆积密度。取试样一份,用漏斗或料勺将试样从容量筒中心上方50mm处徐徐倒入,让试样以自由落体落下。当容量筒上部试样呈锥体,且容量筒四周溢满时,即停止加料。然后用直尺沿筒口中心线向两边刮平(试验过程应防止触动容量筒),称出试样和容量总质量,精确至1g。
③紧密堆积密度。取试样一份,分2次装入容量筒。装完第一层后,在筒底垫放一根直径10mm的圆钢,将容量筒按住,左右交替击地面各25次。然后装入第二层,第二层装满后用同样方法颠实(但筒底所垫钢筋的方向与第一层时的方向垂直)后,再加试样直至超过筒口,然后用直尺沿筒口中心线向两边刮平,称出试样和容量筒总质量,精确至1g。
(4)结果计量与评定 可按式(2-7)计算砂的松散或紧密堆积密度含泥量,精确至10kg/m3:
ρ1=(G1-G2)/V (2-7)
式中,ρ1为砂的松散或紧密堆积密度,kg/m3;V为容器筒的容积,L;G1为容器筒和试样总质量,g;G2为容器筒的质量,g;
砂的空隙率可按式(2-8)计算,精确至1%:
V0=(1-ρ1/ρ0)×100% (2-8)
式中,V0为砂的空隙率,%;ρ1为砂的松散或紧密堆积密度,kg/m3;ρ0为砂的表观密度,kg/m3。
堆积密度取2次检测结果的算术平均值,精确至10kg/m3;空隙率取2次检测结果的算术平均值,精确至1%。松散堆积密度计算结果应大于1400kg/m;空隙率应小于44%。
7.砂的含水率检测
(1)检测目的 测定砂的含水率和进行混凝土混合比设计提供依据。
(2)仪器设备 包括鼓风烘箱(温度控制在105℃±5℃)、天平(称量1000g,感量1g)、搪瓷盘、毛刷等。
(3)检测步骤
①称取试样500g,放入已知质量(m1)的干燥容器中,记下试样与容器的总质量(m2)。
②将容器连同试样放入温度为105℃±5℃的烘箱中烘干至恒重,称量烘干后的试样与容器的总质量(m3)。
(4)结果计量与评定 砂的含水率按式(2-9)计算,精确至0.1%:
Wwc=(m2-m3)/(m3-m1)×100% (2-9)
式中,Wwc为砂的含水率,%;m1为容器的质量,g;m2为未烘干的试样与容器的总质量,g;m3为烘干后的试样与容器的总质量,g。
砂的含水率取2次检测结果的算术平均值作为测定值。
二、粗骨料
混凝土所用的粗骨料,一般是指粒径大于4.75mm的岩石颗粒,在普通混凝土中常用的粗骨料有卵石(砾石)和碎石。卵石是由天然岩石经自然条件作用形成的岩石颗粒,按其产源不同可分为河卵石、海卵石和山卵石等,其中河卵石应用最多;碎石大多由天然岩石经破碎、筛分而成,也可将大块卵石轧碎、筛分而得。
根据国家标准《建设用卵石、碎石》(GB/T 14685—2011)中的规定,按卵石、碎石的技术要求,可分为Ⅰ类、Ⅱ类和Ⅲ类。其中,Ⅰ类宜用于强度等级大于C60的混凝土;Ⅱ类宜用于强度等级大于C30~C60及抗冻、抗渗或其他要求的混凝土;Ⅲ类用于强度等级小于C30的混凝土。
(一)粗骨料质量要求
为了保证混凝土的强度、工作性和耐久性等,国家标准《建设用卵石、碎石》(GB/T 14685—2011)对粗骨料的各项质量指标做出了具体规定,主要包括颗粒级配、有害物质含量、含泥量和泥块含量、针状和片状颗粒含量、强度、坚固性、表观密度和连续级配松散堆积空隙率、吸水率、碱集料反应。
(1)颗粒级配 根据国家标准《建设用卵石、碎石》(GB/T 14685—2011)中的规定,石子的级配通过筛分析方法进行评定,即用一套孔径分别为2.36mm、4.75mm、9.50mm、16.0mm、19.0mm、26.5mm、31.5mm、37.5mm、53.0mm、63.0mm、75.0mm和90.0mm的筛进行筛分,称得每个筛上的筛余量,计算出分计筛余百分率和累计筛余百分率(分计筛余百分率和累计筛余百分率的计算与细骨料相同)。粗骨料的颗粒级配分为连续级配和单粒级配,普通混凝土用粗骨料的颗粒级配应符合表2-18中的规定。
表2-18 混凝土用粗骨料的颗粒级配要求

连续级配是石子粒级呈连续性,即颗粒由大到小,每级石子占一定的比例。连续级配的石子颗粒间的粒差小,配制的混凝土和易性好,不易发生离析现象。连续级配是粗骨料最理想的级配形式,目前在建筑工程中最为常用。
单粒级配是人为剔除某些粒级颗粒,从而使粗骨料的级配不连续,也称为间断级配。单粒级配较大粒径骨料之间的空隙,是直接由比它小很多的小粒径颗粒填充,使空隙率达到最小,密实度增加,并可以节约水泥。但由于颗粒粒径相差较大,混凝土拌合物容易产生离析现象,导致施工比较困难,在一般工程中很少采用。单粒级配一般不宜单独使用,常用于组合成连续粒级,也可与连续级配配合使用。
(2)有害物质含量 粗骨料中的有害杂质主要有黏土、淤泥、有机物、硫化物及硫酸盐等,其对混凝土的危害作用与细骨料相同,所以应当按规定加以限制。另外,粗骨料中有害杂质及针、片状颗粒的含量应符合表2-19中的规定。
表2-19 粗骨料中有害杂质的含量

(3)针状和片状颗粒含量 粗骨料中还可能含有针状(颗粒的长度大于相应粒级平均粒径的2.4倍)和片状(其厚度小于平均粒径的0.4倍)颗粒。针、片状颗粒的应力集中程度较高,在拌制和使用中很容易折断,当含量较多时,会降低新拌混凝土的和易性和硬化后混凝土的强度。粗骨料中的针状和片状颗粒含量应符合表2-20中的规定。
表2-20 粗骨料中的针状和片状颗粒含量

(4)强度 粗骨料的强度包括岩石抗压强度和压碎指标。岩石抗压强度的要求是在水饱和状态下,其抗压强度火成岩应不小于80MPa,变质岩应不小于80MPa,水成岩应不小于30MPa。压碎指标应符合表2-21中的规定。
表2-21 粗骨料压碎指标

(5)坚固性 石子采用硫酸钠溶液法进行试验,卵石和碎石经5次循环后,其质量损失应符合表2-22中的规定。
表2-22 石子的坚固性指标

(6)表观密度和连续级配松散堆积空隙率 石子的表观密度不小于2600kg/m3;连续级配松散堆积空隙率符合表2-23中的规定。
表2-23 石子的连续级配松散堆积空隙率

(7)吸水率 石子的吸水率应符合表2-24中的规定。
表2-24 石子的吸水率

(8)碱集料反应 经碱集料反应试验后,试件应无裂缝、酥裂、胶体外溢等现象,在规定的试验龄期膨胀率应小于0.10%。
(二)粗骨料的取样
(1)检验批的确定 按同品种、同规格、同适用等级及日产量每600t为一检验批,不足600t也为一检验批;日产量超过2000t,按1000t为一检验批,不足1000t也为一检验批;日产量超过5000t,按2000t为一检验批,不足2000t也为一检验批。
(2)取样方法如下。
①在料堆上取样时,取样部位应均匀分布,取样前先将取样部位表层铲除,然后从不同部位抽取大致等量的石子15份(在堆料的顶部、中部和底部均匀分布的15个不同部位取得)组成一组试样。
②从皮带运输机上取样时,应用与皮带机等宽的接料器在皮带运输机机头出料处全断面定时随机抽取大致等量的砂8份,组成一组样品。
③从火车、汽车、轮船上取样时,从不同部位和深度随机抽取大致等量的砂16份,组成一组样品。
(3)取样数量 粗骨料单项检测的最少取样数量应符合表2-25中的规定。
表2-25 粗骨料单项检测的最少取样数量

(4)试样缩分 除堆积密度检测所用试样不经缩分,在拌匀后直接进行检测外,其他检测用试样均应进行缩分。先将所取样品置于平板上,在自然状态下拌和均匀,并堆成锥体,然后沿互相垂直的2条直径把锥体分成大致相等的4份,取其中对角线的2份重新拌匀,再堆成锥体。重复上述过程,直至把样品大致缩分到检测所需要量为止。
(三)粗骨料的检测
1.粗骨料颗粒级配检测
(1)检测目的 评定粗骨料的颗粒级配。
(2)仪器设备 包括鼓风烘箱(温度控制在105℃±5℃)、台秤(称量10kg,感量1g)、方孔筛(筛孔径为2.36mm、4.75mm、9.50mm、16.0mm、19.0mm、26.5mm、31.5mm、37.5mm、53.0mm、63.0mm、75.0mm及90.0mm的筛各1只,并附有筛底和筛盖,筛框内径为300mm)、摇筛机、搪瓷盘、毛刷等。
(3)试验步骤如下。
①按规定方法取样后,将试样缩分至略大于表2-26中规定的数量,烘干或风干后备用。
表2-26 颗粒级配测试所需试样数量

②称取按表2-26规定数量的试样一份,精确至1g。将试样倒入按孔径大小从上到下组合的套筛(附筛板)上,然后进行筛分。
③将套筛置于摇筛机上,摇10min,取下套筛,按筛孔大小顺序再逐个用手筛,筛至每分钟通过量小于试样总量0.1%为止。通过的颗粒并入下一号筛中,并和下一号筛中的试样一起过筛,这样顺序进行,直至各号筛全部筛完为止。
④称出各号筛的筛余量,精确至1g。如每号筛的筛余量与筛底的筛余量之和和同原试样质量之差超过1%时,应重新检测。
(4)结果计量与评定
①计算分计筛余百分率:各号筛的筛余量与试样总质量之比,计算精确至0.1%。
②计算累计筛余百分率:该号筛的筛余百分率加上该号筛以上各分计筛余百分率之和,计算精确至1%。
③根据各号筛的累计筛余百分率,与表2-18对照检查,评定该试样的颗粒级配。
2.粗骨料含泥量检测
(1)检测目的 评定粗骨料的含泥量是否达到技术要求,能否用于指定工程中。
(2)仪器设备 包括鼓风烘箱(温度控制在105℃±5℃)、台秤(称量10kg,感量1g)、方孔筛(筛孔径为75μm及1.18mm的筛各1只)、容器、搪瓷盘、毛刷等。
(3)试验步骤
①按规定方法取样后,将试样缩分至略大于表2-25中规定的数量,放在烘箱中于105℃±5℃下烘干至恒重,待冷却至室温后,分为大致相等的2份备用。
②称取按表2-27规定数量的试样1份,精确至1g。将试样放入淘洗容器中,注入清水,使水面高于试样面约150mm,充分搅拌均匀后,浸泡2h。然后用手在水中淘洗试样,使尘屑、淤泥和黏土与砂粒分离,把浑水缓缓倒入1.18mm及75μm的套筛上(从大到小排列),滤去小于75μm的颗粒。试验前,筛子的两面应先用水润湿,在整个过程中应小心,防止大于75μm的颗粒流失。
表2-27 含泥量测试所需试样数量

③再向容器中注入清水,重复上述操作,直至容器内的水目测清澈为止。
④用水淋洗剩余在筛上的细粒,并将75μm筛放在水中(使水面略高出筛中砂粒的上表面)来回摇动,以充分洗掉小于75μm的颗粒,然后将2只筛余颗粒和清洗容器中已经洗净的试样一并倒入搪瓷盘,放在105℃±5℃的烘箱中烘至恒重,待冷却至室温后,称出其质量,精确至0.1g。
(4)结果计量与评定 可按式(2-10)计算粗骨料的含泥量,精确至0.1%:
Qa=(G0-G1)/G0×100% (2-10)
式中,Qa为粗骨料的含泥量,%;G1为检测后烘干试样的质量,g;G0为检测前烘干试样的质量,g。
粗骨料的含泥量取2个试样检测结果的算术平均值。根据计算结果查表2-14进行评定。
3.粗骨料表观密度检测
根据国家标准《建设用卵石、碎石》(GB/T 14685—2011)中的规定,粗骨料表观密度检测方法有液体比重天平法与广口瓶法2种,最常用的是广口瓶法,但此法不宜用于最大粒径大于37.5mm的碎石或卵石的表观密度。
(1)检测目的 测定石子的表观密度和进行混凝土混合比设计提供依据。
(2)仪器设备 包括鼓风烘箱(温度控制在105℃±5℃)、天平(称量2000g,感量1g)、广口瓶(1000mL,磨石,带玻璃片)、方孔筛(筛径为4.75mm的筛1只)、温度计、搪瓷盘、毛巾等。
(3)检测步骤
①按规定方法取样,最少取样数量见表2-25将试样缩分至略大于表2-28中规定的数量,风干后筛涂小于4.75mm的颗粒,然后洗刷干净,分为大致相等的2份备用。
表2-28 粗骨料表观密度检测所需试样数量

②将试样浸水饱和,然后装入广口瓶中。装试样时,广口瓶应倾斜放置,注入饮用水,用玻璃片覆盖瓶口,上下左右摇晃排除气泡。
③气泡排完后,向瓶中添加饮用水,直至水面凸出瓶口边缘。然后用玻璃片沿瓶口迅速滑行,使其紧贴瓶口水面。擦干净瓶外水分后,称出试样、水、瓶和玻璃片的总质量,精确至1g。
④将瓶中试样倒入搪瓷盘,放在105℃±5℃的烘箱中烘至恒重,待冷却至室温后,称出其质量,精确至1g。
⑤将瓶洗净,重新注入饮用水,用玻璃片紧贴瓶口水面。擦干净瓶外水分后,称出试样、水、瓶和玻璃片的总质量,精确至1g。
注意:检测时各项称量可以在15~25℃范围内进行,但从试样加水静止的2h起至检测结束,其温度变化不应超过2℃。
(4)结果计量与评定 可按式(2-11)计算粗骨料表观密度,精确至10kg/m3:
ρ0=[G0/(G0+G2-G1)]×ρ水 (2-11)
式中,ρ0为粗骨料的表观密度,kg/m3;ρ水为水表观密度,1000kg/m3;G0为烘干试样的质量,g;G1为试样、水及容量瓶和玻璃片的总质量,g;G2为水及容量瓶和玻璃片的总质量,g。
粗骨料的表观密度取2次检测结果的算术平均值,精确至10kg/m3;如果2次检测结果之差大于20kg/m3,应重新检测。对颗粒材质不均匀的试样,如果2次检测结果之差大于20kg/m3,可取4次检测结果的算术平均值。粗骨料的表观密度的计算结果应大于2500kg/m3。
4.堆积密度与空隙率检测
(1)检测目的 测定石子的堆积密度、空隙率和进行混凝土混合比,为设计提供依据。
(2)仪器设备 包括台秤(称量10kg,感量10g)、磅秤(称量50kg或100kg,感量50g)、容量筒(规格要求见表2-29)、垫棒(直径为16mm、长60mm的圆钢)、直尺、小铲等。
表2-29 容量筒规格要求

(3)检测步骤
①按规定方法取样,烘干或风干试样,拌匀并把试样后分为大致相等的2份备用。
②松散堆积密度。取试样一份,用小铲将试样从容量筒中心上方50mm处徐徐倒入,让试样以自由落体落下。当容量筒上部试样呈锥体,且容量筒四周溢满时,即停止加料。除去凸容量筒口表面的颗粒,并以合适的颗粒填入凹陷部分,使表面稍凸起的部分和凹陷部分的体积大致相等(试验过程应防止触动容量筒),称出试样和容量总质量。
③紧密堆积密度。取试样一份,分3次装入容量筒。装完第1层后,在筒底垫放一根直径16mm的圆钢,将容量筒按住,左右交替击地面各25次。然后装入第2层,第2层装满后用同样方法颠实(但筒底所垫钢筋的方向与第1层时的方向垂直),然后装入第3层并填实。试样装填完毕,再加试样直至超过筒口,然后用钢尺沿筒口边缘刮去高出的试样,并以适合的颗粒填平凹处,使表面稍凸起的部分和凹陷部分的体积大致相等,称出试样和容量筒总质量,精确至10g。
(4)结果计量与评定 可按式(2-12)计算粗骨料的松散或紧密堆积密度,精确至10kg/m3:
ρ1=(G1-G2)/V (2-12)
式中,ρ1为粗骨料的松散或紧密堆积密度,kg/m3;V为容器筒的容积,L;G1为容器筒和试样总质量,g;G2为容器筒的质量,g;
砂的空隙率可按式(2-13)计算,精确至1%:
V0=(1-ρ1/ρ0)×100% (2-13)
式中,V0为粗骨料的空隙率,%;ρ1为粗骨料的松散或紧密堆积密度,kg/m3;ρ0为粗骨料的表观密度,kg/m3。
堆积密度取2次检测结果的算术平均值,精确至10kg/m3;空隙率取2次检测结果的算术平均值,精确至1%。粗骨料松散堆积密度计算结果应大于2500kg/m;空隙率应小于47%。
5.粗骨料压碎指标值检测
(1)检测目的 测定石子的抵抗压碎的能力,推测石子的强度。
(2)仪器设备 包括压力试验机(量程300kN,示值相对误差2%)、台秤(称量10kg,感量10g)、天平(称量1kg,感量1g)、方孔筛(孔径为2.36mm、9.50mm、19.0mm)、垫棒(直径10mm、长500mm圆钢)、压碎值测定仪等。
(3)检测步骤
①按规定方法取样,最少取样数量见表2-28,风干后筛除大于19.0mm及小于9.50mm的颗粒,并除去针片状颗粒,分成大致相等的3份备用。
②称取试样3000g,精确至1g。
③将试样分2层装入圆模(置于底盘上)内,每装完一层试样后,在底盘下面垫放直径为10mm垫棒,将筒按住,左右交替颠击地面各25次,2层颠实后,平整模内试样表面,盖上压实。当试样中粒径在9.50~19.0mm之间的颗粒不足时,允许将粒径大于19.0mm的颗粒破碎成粒径在9.50~19.0mm之间的颗粒作压碎指标值检测。当圆模装不下3000g试样时,以装至距圆压上口10mm为准。
④将装有石子的压碎值测定仪放在压力试验机上,开动试验机,按1kN/s速度均匀加荷至200kN并稳荷5s,然后卸荷。
⑤取下加压头,倒出试样,用孔径2.36mm的方孔筛子筛除被压碎的细粒,称出留在筛上的试样质量,精确至1g。
(4)结果计量与评定 可按式(2-14)计算粗骨料的压碎指标值:
Qc=(G1-G2)/G1×100% (2-14)
式中,Qc为粗骨料的压碎指标值,%;G1为试样的质量,g;G2为压碎检测后筛余的试样的质量,g。
粗骨料的压碎指标值取3次检测结果的算术平均值,精确至1%。将压碎指标计算结果与表2-16对照,进行评定。
6.粗骨料针片状颗粒含量检测
(1)检测目的 检测粗骨料中针片状颗粒含量,评定其质量。
(2)仪器设备 包括针状规准仪、片状规准仪、台秤(称量10kg,感量1g)、方孔筛(孔径为4.75mm、9.50mm、16.0mm、26.5mm、31.5mm、37.5mm的筛各一个)。
(3)检测步骤
①按规定方法取样,最少取样数量见表2-25,并将试样缩分至略大于表2-30规定的数量,烘干或风干后备用。
表2-30 针片状颗粒含量检测所需试样数量

②称取按表2-30规定数量的试样一份,精确至1g,然后按表2-31规定的粒级进行筛分。
表2-31 针片状颗粒含量检测的粒径划分及其相应的规准仪孔宽或间距

③按表2-31规定的粒径分别用规准仪逐粒检验,凡颗粒长度大于针状规准仪上相应间距者,为针状颗粒;颗粒厚度小于片状规准仪上相应孔宽者,为片状颗粒。称出其总质量,精确至1g。
④石子粒径大于37.5mm的碎石或卵石可用卡尺检验针片状颗粒,卡尺卡口的设定宽度应符合表2-32中的规定。
表2-32 大于37.5mm针片状颗粒含量检测的粒级划分及其相应的卡尺卡口设定宽度

(4)结果计量与评定 可按式(2-15)计算粗骨料的针片颗粒含量:
Qc=G2/G1×100% (2-15)
式中,Qc为粗骨料的针片颗粒含量,%;G1为试样的质量,g;G2为试样中所含针片颗粒含量的总质量,g。
将针片颗粒含量计算结果与表2-15对照,进行评定。