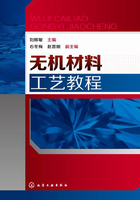
2.3 硅酸盐水泥原燃料及配料
水泥的质量主要取决于熟料的质量,煅烧优质熟料必须先制备适当成分的水泥生料。而生料的化学成分是由原料提供的。只有当原料提供的成分符合要求,加上良好的煅烧与粉磨,才能生产出优质水泥。在自然界很难找到一种单一原料就能完全满足生产水泥的要求,因此需要采取几种不同的原料,根据所生产水泥的种类和性能,进行合理的配料。
2.3.1 原料
制造硅酸盐水泥的主要原料是钙质原料(主要提供氧化钙)和硅铝质原料(主要提供氧化硅和氧化铝,也提供部分氧化铁)。我国硅铝质原料及煤炭灰分一般含氧化铝较高,含氧化铁不足,因此绝大部分水泥厂还需用铁质原料。随着工业生产的发展,利用工业渣进行配料已成为水泥工业的一项重大任务。
2.3.1.1 钙质原料
常用的天然钙质原料有石灰岩、泥灰岩、白垩等,我国大部分水泥厂使用石灰岩。
石灰岩是由碳酸钙所组成的化学与生物化学沉积岩。主要矿物是方解石,并含有白云石、石英或燧石、含铁矿物和黏土质杂质,是一种具有微晶或潜晶结构的致密岩石。纯的方解石含有56%的CaO和44%的CO2,色白。在自然界中因所含杂质不同而呈不同颜色。石灰岩一般呈块状,无层理,结构致密,性脆,普氏硬度为8~10,有白色条痕,密度为2.6~2.8g/cm3,水分随气候而异,通常小于1.0%。耐压强度随其结构和孔隙而异,在30~170MPa之间。
石灰岩中夹杂不均匀的黏土物质,如风化残积的山皮土和裂隙土,不但使石灰石成分波动大,不利于配料,而且不利于运输、破碎与储存,严重时必须剔除。
石灰石中的白云石(CaCO3·MgCO3)是熟料中氧化镁的主要来源,应控制其含量。
石灰岩中夹杂呈结核状或透镜状的燧石(结晶二氧化硅)称为燧石结核。燧石通常以α-石英为主要矿物,色黑,质地坚硬,难以磨细与煅烧,影响窑、磨产量与熟料质量。应控制燧石和石英的含量。
经过地质变质作用,重结晶的大理石(方解石)结构致密,方解石结晶完整、粗大,晶粒往往达100μm以上,虽然化学成分较纯,碳酸钙含量很高,但难以煅烧。
由此可知,当石灰石中含有燧石、石英或方解石时,生料应尽可能磨得细一些。
泥灰岩是由碳酸钙和黏土物质同时沉积所形成的均匀混合的沉积岩。它是一种由石灰岩向黏土过渡的岩石。泥灰岩硬度低于石灰岩,是一种极好的水泥原料,因它含有的石灰岩和黏土混合均匀,易于煅烧,有利于提高窑的产量,降低燃料消耗。
白垩是由海生生物外壳与贝壳堆积而成的,主要是由隐晶或无定形细粒疏松的碳酸钙所组成的石灰岩。我国白垩土一般在黄土层下,土层较薄,故埋藏量不大。白垩易于粉磨和煅烧,是优质的钙质原料。
除天然钙质原料外,电石渣、糖滤泥、碱渣、白泥等也可作钙质原料,但应注意其中杂质的影响。
2.3.1.2 硅铝质原料
天然硅铝质原料有黄土、黏土、页岩、泥岩、砂岩、粉砂岩和河泥等。
黄土与黏土都由花岗岩、玄武岩等经风化分解后,再经搬运和沉积形成;随风化程度不同,所形成的矿物也各异。为了保护耕地,我国水泥厂一般不用黄土和黏土作为硅铝质原料。
页岩是黏土受地壳压力胶结而成的黏土岩,层理明显,颜色不定,一般为灰色、褐色或黑色。其化学成分与黏土类似。主要矿物为石英、长石、云母、方解石以及其他岩石碎屑。页岩硅率较低,一般为2.1~2.8。页岩结构致密坚实,层理发育通常呈页状或薄片状,抗压强度为10~60MPa,含碱量为2%~4%。
砂岩中的矿物主要是石英,其次是长石。其胶结物质有黏土质、石灰质、硅质和铁质等。砂岩中氧化硅的含量一般要求不大于90%,否则难以粉磨和煅烧。粉砂岩是直径为0.01~0.1mm的粉砂经长期胶结变硬后的碎屑沉积岩,颜色呈淡黄色、淡红色、淡棕色、紫红色等;质地取决于胶结程度,一般疏松,但也有较坚硬的。粉砂岩的硅率一般大于3.0,铝率为2.4~3.0,含碱量为2%~4%。
除天然硅铝质原料外,赤泥、煤矸石、城市污泥、油页岩渣、矿石开采尾矿和粉煤灰等工业渣也可作为硅铝质原料。
实验表明:氧化钙在二氧化硅晶格中的扩散速率比二氧化硅在氧化钙晶格中高3~4倍,因此二氧化硅相往往是生料活性的决定性因素。马卡切夫(M.D.Makashev)认为,不同类型二氧化硅的活性按如下次序增高:石英<玉髓<蛋白石<α-方石英<α-鳞石英<长石中的SiO2<云母和角闪石中的SiO2<黏土矿物中的SiO2<玻璃质矿渣中的SiO2。
2.3.1.3 铁质原料
常用的铁质原料有硫酸渣、低品位铁矿石、铜矿渣和铅矿渣等。铜矿渣或铅矿渣不仅可代替铁粉,而且其中所含的氧化亚铁能降低熟料烧成温度和液相黏度,起到矿化剂作用。
2.3.1.4 原料的质量要求
为了充分合理地利用资源,国家不再对原料的质量作统一要求,而是由各工厂根据实际情况自行确定。因此,只要通过各种原材料的搭配能够满足工艺配方的要求,没有必要拘泥于原料的某些质量指标。
2.3.2 燃料
燃料按其物理状态的不同可分为固体燃料、液体燃料和气体燃料。我国煅烧水泥熟料主要采用煤。影响煤使用性能的主要因素有发热量、挥发分、灰分、水分和细度等。
在煅烧条件相同的情况下,较高热值的煤有利于强化煅烧。
煤燃烧时,挥发分低的煤不易着火,火焰短,高温集中;挥发分高的煤着火快,火焰长。我国预分解窑过去大多使用的是挥发分较高的烟煤,但近年随着科技进步,不少水泥回转窑已成功地全部或部分使用无烟煤。
煤的灰分不仅影响其发热量,还影响熟料的化学成分,从而影响熟料质量,这是因为煤灰基本全部进入熟料中。若煤来源多,又未能均化,其灰分的波动必然导致熟料化学成分及质量的波动。
煤粉水分高,使燃烧速率减慢,降低火焰温度。但少量水分的存在能促进碳和氧的化合,并且在着火后,能提高火焰的辐射能力。因此,煤不应过分干燥,一般水分控制在1.0%~1.5%。
煤粉越细,越容易着火,燃烧迅速,形成的火焰短;反之,煤粉过粗,燃烧所需时间长,形成火焰过长,不易燃烧完全。煤粉过细会降低磨机产量,增加煤磨电耗。对于烟煤,其80μm方孔筛筛余一般控制在8%~12%。若采用劣质煤和无烟煤,煤粉应更细一些。
为了充分利用煤炭资源,预分解窑用原煤除要求其全硫含量不大于2.5%外,其热值大小、挥发分和灰分含量由企业根据实际生产情况确定。
2.3.3 生料易烧性
水泥原料和生料的特性及其评价,对于实现生料的正确设计,以及水泥窑的顺利操作都是十分重要的。生料的化学、物理和矿物性质对易烧性和反应活性影响很大。
水泥生料的易烧性可按照JC/T 735—2005进行测定:将备好的生料先于950℃预烧30min,然后将其分别在1350℃、1400℃和1450℃煅烧30min。生料的易烧性用所烧制熟料的f-CaO含量来衡量。显然,f-CaO含量越低,生料的易烧性越好。
在水泥熟料的煅烧过程中,温度必须很好地满足阿利特相的形成。生料的易烧性越好,生料所需的煅烧温度越低。通常生料的煅烧温度为1420~1480℃。有关实验表明,生料的最高煅烧温度与生料成分也就是与熟料潜在矿物组成的关系如下。
T(℃)=1300+4.51C3S-3.74C3A-12.64C4AF (2-27)
影响水泥生料易烧性的主要因素如下。
(1)生料的潜在矿物组成 KH、SM高,生料难烧;反之易烧,还可能易结圈;SM、IM高,难烧,要求较高的煅烧温度。
(2)原料的性质和颗粒组成 原料中石英和方解石含量多,难烧;结晶质粗粒多,难烧。
(3)生料中次要氧化物和微量元素 生料中含有少量次要氧化物如MgO、K2O、Na2O、F和SO3等,有利于熟料形成;但含量过多,不利于煅烧。
(4)生料的均匀性和粉磨细度 生料均匀性好,粉磨细度细,易烧性好。
(5)液相 生料煅烧时,液相出现温度低、数量多、黏度小、表面张力小,则生料中各种离子迁移速度快,其易烧性好。
2.3.4 熟料组成设计
熟料矿物组成的选择,一般应根据水泥的品种和强度等级、原料和燃料的品质、生料制备和熟料煅烧工艺综合考虑,以达到优质、高产、低消耗和设备长期安全运转的目的。
(1)水泥品种 国家标准对于硅酸盐水泥除了规定具有正常凝结时间、良好的安定性以及符合相应强度等级等基本性能外,没有其他特殊要求。其化学成分可在一定范围内变动,可以采用多种配料方案。但要注意三个率值配合适当,不能过分强调某一率值。生产专用水泥或特性水泥应根据其特殊要求,选择合适的矿物组成。当熟料组成与要求指标偏离过大时,会给生产带来较多困难,甚至影响熟料质量。
生产特殊用途的硅酸盐水泥,应根据它的特殊技术要求,选择合适的熟料组成。若生产快硬硅酸盐水泥,则要求硅酸三钙和铝酸三钙含量高,因此应提高KH和IM。如果提高铝酸三钙含量有困难,可再适当提高硅酸三钙的含量。前者由于易烧性下降,为易于烧成,可适当降低SM以增加液相量;后者由于KH值较高,对易烧性不利,但液相黏度并未增大,熟料并不一定过分难烧,因而SM不一定过多降低。
生产中热或低热硅酸盐水泥时,为避免水化热过高,应适当降低水泥熟料中的C3A和C3S含量。但水泥强度、抗冻性与耐磨性会因C3S含量过分减少而显著降低。因此,首先应降低熟料中C3A的含量,同时适当降低C3S的含量,即生产中控制适当低的IM值和KH值。
(2)原料品质 原料的化学成分和工艺性能对熟料矿物组成的选择有很大影响,在一般情况下,应尽量减少原料种类数,除非其配料方案不能保证正常生产。当石灰石的燧石含量和硅铝质原料的粗砂含量较高时,因原料难磨,熟料难烧,饱和系数不能过分提高。
(3)燃料品质 当回转窑采用煤作燃料时,煤的灰分将掺入熟料中。理论上,在配料计算时应把煤灰作为原料的一个组分考虑,但实际上煤灰掺入很不均匀,结果造成熟料矿物形成不均,岩相结构不良。煤粉越粗、灰分越高、热值越低,影响也越大。因此,当煤质变化时,适当调整熟料组成是十分重要的。
近年来,燃煤的均化受到水泥厂的广泛重视。特别是应用低品位燃料以及煤质变化较大时,应该进行燃煤的均化,才能保证熟料成分的稳定和水泥质量的提高。
(4)生料细度和均匀性 生料化学成分的均匀性,不但影响窑的热工制度的稳定和运转率的提高,而且还影响熟料的质量以及配料方案的确定。
一般来说,生料均匀性好,粒度细,KH可高些。若生料成分波动大,生料粒度粗,由于化学反应难以进行完全,KH应适当降低。
(5)窑型与规格 物料在不同类型窑内受热和煅烧的情况不同,因此熟料的组成也应有所不同。对于目前广泛使用的预分解窑来说,由于生料预热好,分解率高,烧成温度高,热工制度稳定,为了有利于保持窑皮和防止结皮、堵塞和结大块,目前趋于低液相量的配料方案。我国大型预分解窑大多采用“两高一中”配料方案,有的采用“三高”配料方案。具体三率值变化范围为:KH=0.87~0.93;SM=2.4~2.8;IM=1.4~1.9。
影响熟料组成的因素很多,一个合理的配料方案既要考虑熟料质量,又要考虑物料的易烧性;既要考虑各率值或矿物组成的绝对值,又要考虑它们之间的相互关系。
2.3.5 配料计算
2.3.5.1 配料依据
配料计算的依据是物料平衡,即反应物的量等于生成物的量。随着温度升高,生料煅烧成熟料经历以下过程:生料干燥蒸发物理水;黏土矿物分解放出结晶水;有机物质的分解挥发;碳酸盐分解放出二氧化碳;液相出现使熟料烧成。因为有水分、二氧化碳以及某些物质逸出,所以,计算时必须采用统一基准。
物理水蒸发以后,生料处于干燥状态。以干燥状态质量所表示的计算单位,称为干燥基准。干燥基准用于计算原料的配合比和干燥原料的化学成分。
如果不考虑生产损失,则干燥原料的质量应等于生料的质量,即:
干钙质原料+干硅铝质原料+干铁质原料=干生料
去掉烧失量(结晶水、二氧化碳与挥发物质等)以后,生料处于灼烧状态。以灼烧状态质量所表示的计算单位,称为灼烧基准。灼烧基准用于计算灼烧原料的配合比和熟料的化学成分。
如果不考虑生产损失,在采用基本上无灰分掺入的气体或液体燃料时,则灼烧原料、灼烧生料和熟料三者质量应相等,即:
灼烧钙质原料+灼烧硅铝质原料+灼烧铁质原料=灼烧生料=熟料
如果不考虑生产损失,在采用有灰分的燃煤时,则灼烧生料与掺入熟料的煤灰之和应与熟料的质量相等,即:
灼烧生料+煤灰(掺入熟料的)=熟料
在实际生产中,由于总有生产损失,且飞灰的化学成分不可能等于生料成分,煤灰的掺入量也并不相同。因此,在生产中应以生、熟料成分的差别进行统计分析,对配料方案进行校正。
熟料中的煤灰掺入量可按下式计算:
(2-28)
式中 GA——熟料中煤灰掺入量,%;
q——熟料单位热耗,kJ/kg熟料;
Qnet,ad——煤的空气干燥基低热值,kJ/kg煤;
Aad——煤的空气干燥基灰分含量,%;
S——煤灰沉落率,%,对于预分解窑,一般取100%(收尘器窑灰不入窑者,取90%)。
2.3.5.2 配料计算方法
配料计算的方法很多,比较常用的人工计算方法是递减试凑法,但计算工作量较大。随着计算机的普及和应用,现在可以通过计算机程序方便地进行配料计算,EXCEL工具就是其中的一种。以下仅介绍递减试凑法。
【例2-1】 某预分解窑采用四组分原料进行配料。已知熟料率值控制目标值分别为KH=0.90±0.02;SM=2.5±0.1;IM=1.6±0.1,熟料热耗为3000kJ/kg。已知原料、煤灰的化学成分和煤的工业分析资料见表2-5和表2-6,试求各原料的配合比。
表2-5 原料和煤灰的化学成分

表2-6 煤的工业分析

表2-6中化学分析数据总和往往不等于100%,这是由于某些物质没有分析测定,因而通常小于100%,但不必换算为100%。此时,也可以加上其他一项补足为100%。有时,分析总和大于100%,除了没有分析测定的物质以外,大都是由于该种原、燃料,特别是一些工业废渣,含有一些低价氧化物,如FeO、甚至金属Fe等,经分析灼烧后,被氧化为Fe2O3等增加了质量所致,这与熟料煅烧过程一致。因此,也不必换算。
解:1.计算煤灰掺入量
2.根据熟料设计率值,计算要求的熟料化学成分
设Σ=97.0%,则:
Al2O3=IM·Fe2O3=5.46%
SiO2=SM(Al2O3+Fe2O3)=22.18%
CaO=Σ-(SiO2+Al2O3+Fe2O3)=65.95%
3.递减试凑法计算干生料的配合比
以100kg熟料为基准,列表递减见表2-7。
表2-7 熟料的化学成分计算

第9步各组分均相差不大,不再递减计算;其他一项差别不大,说明Σ设定值合适。经过计算,共加入124kg石灰石;20kg粉砂岩;5.1kg粉煤灰;2.1kg铁粉。所以,各干原料的质量分数为干石灰石:干粉砂岩:干粉煤灰:干铁粉=82.01:13.23:3.37:1.39。
4.核算熟料化学成分与率值
生料的化学成分见表2-8。
表2-8 生料的化学成分

煤灰掺入量GA=2.66%,则灼烧生料配合比为100%-2.66%=97.34%。按此计算熟料的化学成分,见表2-9。
表2-9 熟料的化学成分

则熟料率值计算如下:
所得率值在要求范围内,计算符合要求。
5.计算湿原料的配合比
设原料操作水分:石灰石为1%,粉砂岩为0.8%,粉煤灰为1%,铁粉为12%,则湿原料质量配合比为湿石灰石:湿粉砂岩:湿粉煤灰:湿铁粉=81.89:13.19:3.36:1.56。