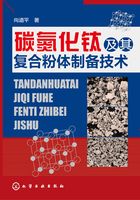
1.3 Ti(C,N)粉体的制备
1.3.1 Ti(C,N)粉体的制备
1.3.1.1 高温扩散法
这是一种制备Ti(C,N)粉体的常规方法,反应式如下:
(1-1)
(1-2)
该法首先是用Ti粉高温氮化法制备TiN并球磨破碎;接下来再取一定量TiN粉体和TiC粉体,球磨均匀混合后,在高温(1500~1800℃)热压固溶或于Ar气氛中在更高的温度下固溶而成。
高温扩散法的缺点是能耗高,难以获得高纯Ti(C,N)粉体以及N/C比不易准确控制。陈森凤等以TiC粉体(纯度99.5%)和TiN粉体(纯度99.5%)为原料,按设定的摩尔比(TiC/TiN)12/88配料,球磨24h,随后在1500℃、Ar气氛下热处理5h,直接反应合成了Ti(C0.12,N0.88)粉体。
1.3.1.2 高温氮化法
该法是以TiC粉体与金属Ti粉为原料,球磨混合后在高温(1700~1800℃)和N2气氛下进行氮化处理的一种方法,其反应式为:
(1-3)
高温氮化法由于反应温度高,保温时间长,因此生产效率低,能耗大,生产成本高。目前,用此法合成Ti(C,N)粉体在文献报道中并不多见。
1.3.1.3 碳热氮化法
TiO2碳热氮化法是应用最广泛、已工业化的制备Ti(C,N)粉体的一种方法,其制备方法简单,工艺流程较短,较之分别合成TiC和TiN再合成Ti(C,N)更节能。该方法总化学反应式为:
(1-4)
目前,人们对TiO2碳热氮化法制备Ti(C,N)粉体的热力学原理、工艺影响因素等方面进行了一些研究,但对其反应机理的研究仍然不多,而且存在较大争议。TiO2碳热氮化法的缺点是反应温度较高,直接制备超细或纳米Ti(C,N)粉体比较困难。徐智谋等用球形亚微米TiO2粉体和纳米炭黑为原料,在C/Ti配比为1.52、N2流量为0.5mm3/L、碳热氮化温度为1600℃、保温时间为3h时,批量生产出Fsss粒度为0.5μm、晶粒度为37nm的单相纳米晶Ti(C,N)粉体。
1.3.1.4 化学热解法
化学热解法制备Ti(C,N)的化学反应式为:
(1-5)
化学热解法以TiCl4为原料,溶于CCl4介质中混合均匀后与C2H8N2反应,然后在1200℃热解合成。该方法尽管耗能较少,但存在工序较麻烦、产物的杂质较多等缺点。
1.3.1.5 钛粉碳氮化法
该方法以钛粉作为原料,与甲氨-氩气混合气体在800~1400℃温度范围内进行碳氮化。
1.3.2 亚微、超细及纳米Ti(C,N)粉体的制备
在粉体硬质材料领域,一般达成了这样的共识:硬质颗粒尺寸大于1μm的称为常规材料;小于1μm的称为细晶粒材料。细晶粒材料可分为:在0.5~1μm之间的称为亚微级材料;在0.1~0.5μm之间的称为超细(或超微)级材料;在0.1μm之下的称为纳米级材料。近年来,为了满足Ti(C,N)基金属陶瓷制备中对Ti(C,N)细粉,特别是对超细或纳米Ti(C,N)粉体的迫切需要,越来越多的研究者进入这一领域,并且取得了不错的进展。下面对其研究现状做一介绍。
1.3.2.1 等离子体法
等离子体法属于气相法,其制备纳米微粒的机理如下:等离子体中存在大量的高活性物质微粒,这样的微粒与反应物微粒迅速交换能量,有助于反应的正向进行。此外,等离子体尾焰区的温度较高,离开尾焰区的温度急剧下降,反应物微粒在尾焰区处于动态平衡的饱和态,该态中的反应物迅速离解并成核结晶,脱离尾焰后温度骤然下降而处于过饱和状态,成核结晶同时猝灭而形成纳米微粒。等离子体法制取纳米微粒的方法有4种:直流电弧等离子体法、直流等离子体射流法、射频等离子体法与混合等离子体法。其中,直流电弧等离子体法用得较多,这一方法是在惰性气氛或反应性气氛下通过直流放电使气体电离产生高温等离子体,使原料熔化、蒸发,蒸气遇到周围的气体就会被冷却或发生反应形成纳米微粒。
曾达权等以TiCl4、CH4、N2或NH3为原料,在自制的直流电弧氢等离子体反应器中合成了三元超细Ti(C,N)固溶体微粉,并且考察了不同氮源及其加入量对产物组成的影响。研究结果表明,用N2作为氮源所得产物的固溶度低,用NH3作为氮源则可以进一步提高产物的固溶度;试验所得不同固溶体微粉为单一结晶相的立方Ti(C,N)晶体,各自都具有均一的化学组分;黑色超细Ti(C,N)粉体平均粒径<100nm,比表面积>10m2/g,主相含量>97%。
白万杰发明了一种等离子体化学气相合成法制备Ti(C,N)陶瓷粉体的工艺,其特征在于首先向等离子体发生器中通入等离子体工作气体N2-H2-Ar,按N2为9~13m3/h、H2为27~32m3/h的流量连续注入,及注入30L/min的Ar,启动等离子体电源,在等离子体发生器中产生等离子体电弧(起弧正常后关闭Ar)。经过电弧的气体被加热到4800~5200℃高温后进入反应器中,然后分别将经蒸发器加热蒸发的TiCl4和经流量计输送的液化气及NH3送入反应器中快速发生分解,保持液化气、NH3和TiCl4的比例为1:1:(7~11)(单位时间内注入液态质量比)连续注入,等离子体反应器内反应温度保持在1200~1300℃。在等离子体反应器中快速发生分解并利用自由沉降及淬冷条件生成固态Ti(C,N)微粉,生成的Ti(C,N)经极短的时间(毫秒级)的结晶、长大,冷却后经布袋收粉器实现气固分离得到Ti(C,N)粉体。采用此发明工艺生产的Ti(C,N)纯度高,粒度分布均匀,而且粒径超细,生产成本低,产量高,适合规模化生产。
1.3.2.2 高温自蔓延法
高温自蔓延合成法(self-propagating high-temperature synthesis,SHS),或称燃烧合成法(combustion synthesis,CS),是近年来发展起来的难熔化合物合成工艺。该工艺利用化学反应自身放热来合成产物,反应中不需要外部热源的供给;通过快速自动波燃烧的自维持反应得到所需成分和结构的产物;可通过改变热释放方式和传输速度来控制反应过程的速度、温度、转换率及产物的成分和结构。该工艺具有生产效率高、能耗小、设备工艺简单、产品纯度高等优点。不过,SHS工艺只有当反应体系化合物生成热与比热容(在298K下)之比大于2000K(也即反应体系绝热温度Tad>1800K)时,反应才能自我维持;否则,反应需要采用“预热”、“化学炉”、“热爆”等辅助方法才可维持自发反应。在获得纳米粉体的SHS反应中,一般还要求反应前驱体在升温过程中有大量气体产生并释放,从而避免前驱物因熔融而粘连,达到减小产物粒径的目的;而反应过程高发热特征,使得反应温度难以控制,对于制备细小的纳米碳化物粉体不利。
康志君等对Ti(C,N)粉体的SHS工艺做了较系统的试验研究。分析了钛粉及炭黑品种、成分配比,压坯密度,氮气压力等因素对SHS合成过程及产物性能的影响。结果表明,钛粉粒度对SHS过程影响很大,炭黑种类对反应产物状态(空隙、游离碳)也有明显影响。炭黑的加入量增加,产物的碳含量也增加,而氮含量则相应减少。随着压坯密度的增加,燃烧波蔓延速度减小,反应产物较硬,而且芯部与边缘成分不同。氮气压力增大,产物的氮含量相应提高。SHS产物球磨8h后得到Ti(C,N)粉体的平均粒度为0.8μm。研究发现,钛粉粒度对SHS过程影响很大,当粒度大于40目时,反应不能进行,随着钛粉变细,由于钛粉与炭黑的接触面增加及粉体活性增大,导致反应加快、燃烧波蔓延速度增加,但是随着钛粉粒度的减小,钛粉的氧含量提高,最终反应产物的氧含量也比较高。
Eslamloo-Grami等以钛粉和炭黑为原料,在N2气氛下用SHS法制备了Ti(C,N)粉体。研究显示要完全反应,必须满足以下条件:添加TiN作为稀释剂;N2的压力≥0.6MPa。该方法同传统粉体制备工艺相比,具有设备简单、生产效率高、节时省能等优点,适合于大批量的生产。
赫晓东等燃烧合成了亚微米级Ti(C,N)粉体,其工艺步骤如下。
(1)将基础原料和稀释剂进行配料,基础原料包含二氧化钛、镁粉和炭黑,质量分数为:二氧化钛55%~62%、镁粉20%~40%、炭黑0~20%,稀释剂为碳氮化钛粉体,质量为基础原料的0~2.3倍。
(2)在80~150℃真空条件下干燥600~1200min,将基础原料和稀释剂的混合物装入混料罐,机械球磨混合1200~1500min。
(3)将混合均匀的粉体装入石墨舟,然后放入高压容器中,反应器采用循环水冷却,充入氮气的压强为0~15MPa,采用Ni-Cr丝点火使之发生自蔓延反应,点火剂为粒度小于300目的纯Ti粉与炭黑的混合物。
(4)冷却后取出产物,产物为碳氮化钛和氧化镁的混合物,产物在盐酸溶液中酸洗去除氧化镁,剩余的碳氮化钛经水洗、过滤、干燥后,得到最终的产品。同其他SHS法一样,该法具有反应速率快、节约能源、成本低、效率高、产物纯度高的优点。
1.3.2.3 溶胶-凝胶法
溶胶-凝胶法是20世纪60年代发展起来的一种制备高技术陶瓷(如热电、超导材料)以及高纯玻璃、陶瓷纤维、薄膜、催化剂载体、磨料等的一种方法。最近几年,溶胶-凝胶法被用于制备纳米粉体并取得了很大进展。该方法的制备原理是将无机盐或金属有机醇盐首先经水解制成溶胶,再经进一步聚合制成凝胶,最后经干燥、煅烧得到纳米粉体。溶胶-凝胶法的优点是合成的纳米粉体的化学均匀性好,纯度高。由于反应温度较低,可以得到颗粒尺寸小、粒度分布窄的粉体。缺点是粉体烧结性差,干燥时收缩大,如果制备时以水为介质,粉体容易产生团聚。
Xiang Junhui等以偏钛酸[TiO(OH)2,工业生产钛白粉的中间产物]、炭黑(工业槽法炭黑,粒径为15~20nm)为原料,将TiO(OH)2溶胶按一定比例加入炭黑,同时高速搅拌;加入少量的OP乳化剂,使炭黑分散均匀;加入去离子水,使溶胶充分水解而凝胶化。在空气中120~150℃干燥,得到的干凝胶装入石墨坩埚,在碳管式电阻炉中及流动N2气氛下,于1400~1600℃温度范围内反应得到平均粒径小于100nm的Ti(C1-x,Nx)超细粉体(x值为0.2~0.7)。
肖汉宁等研究了氨解对溶胶-凝胶法合成Ti(C,N)粉体的影响,发现氨解钛溶胶改变了凝胶中TiO2的结构,在氨解的钛溶胶中,H+和占据了一部分Ti+的位置,使网络结构变得不完整。这一方面增加了网络的活性基团,另一方面则有利于TiO2颗粒细化,表面能增加,提高系统中Ti与C的混合均匀性,降低反应活化能,使合成反应能够在较低的温度下进行。根据差热分析的结果,氨解的钛溶胶与未氨解的钛溶胶相比,其起始反应温度可提前20~30℃。前者的DTA曲线与后者的大致相同,但在250℃和400℃附近出现了两个吸热峰,这是其脱去结构水和氨的标志,使原来结构中的Ti—O—H键和Ti—O—NH4键破坏,出现Ti—和Ti—O—空键,成为活性基团。在随后的氮化、碳化反应中,Ti—可以直接进行反应,而Ti—O—必须先打破Ti—O之间的结构才能进行反应。因此,由于两者之间的反应活性存在差异,导致了氨解钛溶胶反应后产物中形成分相。
1.3.2.4 低温化学法
Shen Guozhen等报道了一种合成纳米级Ti(C,N)的简单方法。其工艺流程为:取分析纯C3N3Cl3为1.0g、过量的TiCl4为5mL、金属Na为4g放入一个体积大约30mL的不锈钢高压反应釜中密封,整个过程都是在保护气氛为流动N2的手套箱中完成。将反应釜升温至600℃,保温10h后在室温下冷却,然后收集反应产物。对反应产物用无水乙醇、去离子水、弱酸进行多次清洗以去除杂质,最后在真空中70℃烘干,时间为3h,得到最终的产物Ti(C0.7,N0.3),其颗粒尺寸大约为30nm。研究发现,当反应温度低于550℃,保温时间少于5h,反应没有生成Ti(C,N)。当反应温度高于650℃,保温时间超过20h时,Ti(C,N)的尺寸长大很严重。该方法虽然为生产Ti(C,N)粉体开辟了一条新的道路,但其原料成本较高,工艺较烦琐。
白玉俊等发明了一种Ti(C,N)粉体的制备方法,其特征在于,以四氯化钛(TiCl4)作钛源、以碳化钙(CaC2)作碳源、以叠氮钠(NaN3)作氮源,在不锈钢反应釜中进行化学交换反应,对反应产物经过清洗、抽滤、烘干得Ti(C,N)粉体。化学反应式为:
(1-6)
制备工艺如下。
(1)在无水无氧手套箱中,将碳化钙(CaC2)、叠氮钠(NaN3)和四氯化钛(TiCl4)装入高温高压不锈钢反应釜中并搅拌均匀,封釜后,将反应釜在加热炉中加热到400~450℃,使三种反应物之间发生化学交换反应。
(2)反应釜自然冷却到室温后,反应产物经无水乙醇清洗、抽滤,除去残余反应物,直到滤液无色为止。
(3)再用去离子水清洗,以除去反应副产物NaCl、CaCl2。
(4)所得产物在60℃温度下烘干3h后,得到棕红色Ti(C,N)粉体。
1.3.2.5 淀粉还原法
李喜坤等采用TiH2(钛源,钛质量分数99%,粒度<67μm)、淀粉(碳源,碳质量分数44.4%)为原料,将两者按照1:2的质量比配料,以乙醇为介质在聚氨酯球磨罐中球磨24h,经60℃干燥后,在碳管炉中氮气气氛下1650~1800℃保温1~3h合成可控制碳氮比的Ti(C,N)粉体。在1750℃、保温2h、氮气流量为5L/min条件下,可获得颗粒尺寸为40~80nm的单相Ti(C0.5,N0.5)粉体。
淀粉还原法是以TiH2和淀粉分别作为Ti源和C源,利用淀粉在无氧的条件下分解时得到相对较细的新生碳颗粒;而TiH2同时热分解释放出新生钛颗粒,新生的碳颗粒和新生的钛颗粒具有很高的表面活性,可以生成很细的TiC粉体;同时新生的钛颗粒与氮气反应生成TiN,最终得到碳氮化钛超细粉体,同时还可以使反应温度降低,达到节能高效的目的。
1.3.2.6 机械球磨法
高能球磨引起的机械合金化技术是美国人Benjamin在制备弥散强化镍基高温合金时发明的。与传统的球磨方法相比,高能球磨最大的特点是有相当大的球料比,一般为(10~20):1,最大可达100:1以上,并且可实现真空或气氛保护。在如此大的球料比下,其混合粉体在球磨过程中受到球的碰撞、挤压,球间中心线上的粉体受到强烈的塑性变形,冷焊和破断,从而形成洁净的“原子化”表面。这些相互接触的不同元素的新鲜表面在压力下相互冷焊在一起,形成界面有一定原子结合力的复合颗粒。因磨球的反复碰撞、挤压作用,使复合颗粒界面处存在大量的空位缺陷,这非常有利于原子进行扩散,从而实现成分合金化。机械高能球磨被认为是一种很有前途的纳米材料制备方法,设备、工艺过程简单,制备成本较低。该法可以在常温下制备纳米粉体,特别是可以制备用其他方法不能制备的高熔点纳米粉体,近年来已受到高度重视。
S.Zhang等用TiC粉体(2~5μm)和TiN粉体(10~20μm)作为原料,用行星式球磨机对70%TiC+30%TiN及50%TiC+50%TiN(质量分数)两个体系,分别进行机械合金化处理,其结果表明,在机械化球磨过程中TiC和TiN生成了固溶体,而且最终晶粒大小与最初研磨粉体的大小关系不大。J.Jung等通过在氮气气氛下球磨钛粉和碳粉的混合粉体20h(行星式球磨机,250r/min)制备了粒度尺寸在100~200nm范围内的Ti(C,N)超细粉。研究结果表明,球磨气氛中存在的氧会干扰N原子向TiC晶格的扩散。此外,在形成Ti(C,N)的过程中,发现N对Ti的亲和力比C强。S.Zhang等利用行星式球磨机,在球料比为20:1时,机械球磨Ti(C0.3,N0.7)、WC、TaC的混合粉体(质量比70:20:10)至一定时间后,发现TaC可以与Ti(C0.3,N0.7)形成固溶体,而WC则较难完全固溶。
1.3.3 Ti(C,N)粉体制备发展趋势
由前述可知,在超细或纳米Ti(C,N)基金属陶瓷刀具的研究和应用中,超细或纳米Ti(C,N)粉体的制备是基础。目前,采取新工艺、新方法制得粒度很小的超细、纳米Ti(C,N)粉体是总的发展趋势。尽管文献报道了一些制备Ti(C,N)超细或纳米粉体的方法,但相关研究仍嫌不足,亟待加强。此外,分析目前出现的一些新方法,会发现它们一般具有原料成本高、工艺烦琐、产量低、合成产物不纯、设备昂贵等一种或几种缺点,这些方法与规模化工业生产还有相当大的距离。因而,探索一种经济适用且可工业推广的方法制备Ti(C,N)超细或纳米粉体,满足制备超细或纳米Ti(C,N)基金属陶瓷的需要,已是当务之急。