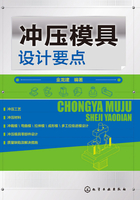
1.3 冲压模具设计一般步骤
(1)制件工艺分析
①根据所提供的产品图样,分析制件的形状特点、尺寸大小、精度要求、断面质量、装配关系等要求。
②根据制件的生产批量,决定模具的结构形式、选用材料。
③分析制件所用的材料是否符合冲压工艺的要求,决定是采用条料、板料、卷料还是边角废料来冲压。
④根据现有设备情况及制件和制件批量对设备的要求选择合适的压力机。
⑤根据现有的制造水平及装备情况,为模具结构设计提供依据。
(2)确定合理的冲压工艺方案
①根据对制件的工艺分析,确定基本的工序性质,如冲孔、落料、弯曲及拉深等。
②进行工艺计算,确定工序数,如拉深次数等。
③根据制件生产批量和条件(材料、设备和制件精度)确定工序组合,如采用复合冲压工序还是连续冲压工序。
④根据各工序的变形特点、尺寸要求等确定工序排列顺序,如采用先弯曲后冲孔还是先冲孔后弯曲等。
(3)工艺计算
①计算毛坯尺寸,合理排样并绘制排样图,计算出材料利用率。
②计算冲压力,其中包括冲裁力、弯曲力、拉深力、卸料力、推件力、压边力及成形力等,以便确定压力机。
③选择合适的压力机型号、规格。
④计算压力中心,以免模具偏心负荷而影响模具的使用寿命。
⑤计算并确定模具的主要零件(如凸模、凹模、凸模固定板及垫板等)的外形尺寸以及弹性元件的大小及高度等。
⑥确定凸、凹模间隙并计算凸、凹模工作部分尺寸。
⑦确定拉深模压边圈、拉深次数、各工序的尺寸分配以及半成品的尺寸计算。
(4)模具总体设计
进行模具结构设计,确定结构件形式和标准。
①确定冲裁、成形零件与标准。如凸模、凹模及凸凹模的结构形式是组合、整体还是镶拼的,以及选用何种固定方式。
②选定定位元件。如采用定位板或挡料板或导正销等,对于多工位级进模还要考虑是否用始用挡料销、导正销和侧刃等。
③确定卸料与推件机构。卸料有弹性卸料和刚性卸料两种形式。弹性卸料一般采用弹簧或橡胶或氮气弹簧作为弹性元件;刚性卸料通常采用固定卸料板的结构形式。
④确定导向零件的种类和标准。包括是否采用导向零件,采用哪种形式的导向零件,设计中最常用的有滑动导柱、导套和滚珠导柱、导套导向,一般选用专业标准件厂的标准规格。
⑤确定模座种类及规格。
(5)冲压设备的选用
根据现有冲压设备情况以及要完成的冲压工序性质,冲压加工所需的变形力、变形功及模具闭合高度和轮廓尺寸等主要因素来选用压力机的型号、规格。选用压力机时必须满足以下4点要求:
①压力机公称压力必须大于冲压力。
②模具的闭合高度应在压力机的最大闭合高度和最小闭合高度之间。当多副模具安装在同一台压力机上时,模具的闭合高度应相同,并考虑冲压力的分布要尽可能地均匀。
③压力机的滑块行程必须满足制件成形要求。单工序拉深时为了便于放料和取料,其行程必须大于拉深高度的两倍。
④为了便于安装模具,压力机工作台面尺寸应大于模具下模座尺寸,台面上的孔应能保证制件或废料能顺利地漏卸。
(6)模具图设计
①绘制模具总装图。
a.主视图。一般指模具的工作位置,采用剖面画法。
b.俯视图和仰视图。俯视图(或仰视图)一般指将模具的上模部分(或下模部分)拿掉,视图只反映模具的下模俯视(或上模仰视)可见部分,这是冲模的一种习惯画法。
c.侧视图和局部视图。在必要时画出,使某些模具结构表达更完善。
d.制件图。常画在图样的右上角,要注明制件的材料、规格,以及制件本身的尺寸、公差及技术要求等。对于由多副模具冲压成的制件,除绘制出本工序的成品制件图外,还要绘出上工序的半成品图(毛坯图一般放在图样的左上角)。
e.排样图。对于落料模、复合模和多工位级进模必须在制件图下面绘出排样图。排样图上应标明料宽、步距和搭边值。复杂的和多工位级进模的排样图一般单独绘制在一张图纸上。
f.技术要求说明。一般在标题栏的上方写出该模具的冲压力、卸料力、模具外形尺寸和闭合高度、模具标记、所选设备(压力机)型号等要求。
g.编写零件的明细表和外购材料申请单。
②绘制模座及模板图。指绘制上模座、下模座、凸模固定板垫板、凸模固定板、卸料板垫板、卸料板、凹模固定板、凹模垫板等。
③绘制模具零部件图。指绘制凸模、凹模、导料板、承料板、导正销、非标准的顶杆等。