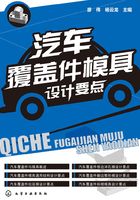
1.3 汽车覆盖件模具设计
随着计算机技术的发展,计算机辅助设计(CAD)在模具设计领域得到广泛的应用并显示其巨大的灵活性、方便性与优越性。当前,传统的二维CAD技术已经不能满足模具的开发周期、质量与成本的要求,三维实体设计技术在模具的开发周期短、质量提升和成本降低等方面有着明显的优势。
三维实体设计能够直观地反应设计的真实状态,使相关人员清楚准确地理解设计者的真正设计意图,方便加工与装配。三维实体设计能通过运动模拟和干涉检查等分析手段,在设计阶段即可发现问题,避免以往只能在生产过程中才能发现的设计错误。另外,三维实体设计还可以进行CAE分析,从而指导和优化工艺方案,如拉延成形模拟分析、回弹补偿分析和修边的展开分析等。同时,直接按三维实体数据进行编程与实型加工,可以缩短工期,保证质量。
除了以上几点之外,模具设计最重要的一点,就是一定要根据本公司(或客户)的现有条件(压力机种类及规格等)来设计汽车覆盖件模具的具体结构。
1.3.1 拉延模具设计
(1)阅读必需的技术资料
汽车覆盖件冲压工艺方案确定之后,便可进行模具设计。在设计拉延模具之前,必须阅读以下技术资料。
①覆盖件产品图。覆盖件产品图(2D图和3D图)是所有工序生产的依据。在设计拉延模之前,要仔细认真地阅读覆盖件产品图,充分理解产品设计思想、产品的各项功能和技术质量要求,并预计或设想拉延时哪些因素会对产品质量产生不良影响。
②覆盖件产品DL图。结合覆盖件产品图,认真阅读覆盖件DL(2D和3D)图,充分理解其设计思想,工艺补充、压料面设计的目的以及需要预防可能出现的问题等,在拉延成形条件方面还存在哪些不足,以便确定在拉延模设计时采取必要的措施来弥补,这对拉延模设计是非常重要的。
(2)拉延变形分析和质量分析
认真研究覆盖件冲压工艺文件,结合工序样件(如果有的话),明确本工序以及后工序对产品件的质量要求。
针对拉延件的结构形状特点,结合CAE分析报告,进行拉延过程中毛坯的流动和变形分析。首先分析判断毛坯各部位的变形性质、变形状态、变形分布以及变形量大小等,然后进一步分析判断毛坯在不同变形状态、变形分布以及变形量下可能出现的破裂、皱褶、表面畸变以及刚度降低等质量问题。同时还要判断拉延过程中可能出现的划伤、冲击线滑移等问题。最后,根据这些分析与判断,决定在拉延模具设计时采取哪些相应的应对措施。
(3)资料准备
准备好有关的拉延模具设计所需的参考资料,如以往的类似件的拉延模具图样、模具国家标准、行业标准以及企业标准、标准件与通用件样本,还应具备有冲压件的公差、产品所用板材的各项性能参数以及客户要求等。
(4)设计要点
①确定压料面及冲压方向。压料面的形状不但要保证压料面上的材料不皱,而且应尽量使凸模下的材料能下凹以降低拉延深度,更重要的是要保证拉入凹模里的材料不皱不裂。
汽车覆盖件的拉延冲压方向选择的是否合理,将直接影响凸模是否能进入凹模、变形是否均匀、最大限度地减少拉延件各部分的高度差、是否能充分发挥材料的塑性变形能力、是否有利于防止破裂和起皱等质量缺陷的产生等等。也就是说,只有选择了合理的拉延冲压方向,才能使拉延成形过程顺利实现。
一般来说,在覆盖件冲压工艺设计时,已充分考虑了拉延过程中的变形特点和毛坯流动趋势,确定了拉延件的形状和冲压方向。
②确定模具结构形式及导向方式。拉延模具结构形式的确定是设计时必须首先需要考虑的,也是模具设计的关键,它直接影响覆盖件的质量、成本及冲压生产的水平。在汽车覆盖件冲压生产中,采用哪种结构形式的拉延模,主要是根据客户的使用要求来选择(或根据本公司的实际情况)。至于模具的导向方式,应根据所选择的模具结构形式来确定。
③定位方式选择。主要的定位元件有定位器(或带感应器板件定位器)以及半自动化冲压线上使用的气动挡料装置等。
④确定拉延筋形式及布置。拉延筋的形式及布置对拉延过程有很大的影响,它是防止覆盖件起皱和撕裂最有效的方法之一。要根据拉延件的形状特点及相应的毛坯变形、流动规律来设计拉延筋的形式和布置,使其可以有效地控制毛坯的变形与流动,满足拉延要求。
在设置拉延筋时,凹模压料面上的拉延筋槽可以适当加深,但必须保证槽宽W,并注意保证圆角半径R的大小。
⑤确定凸、凹模圆角等参数。汽车覆盖件多数都是一次拉延成形,因此一般情况下拉延凸模的形状、尺寸以及圆角大小都要与产品图相应部位的参数相一致。若覆盖件出现与产品图参数不一致,并且利用其他方法都不能解决时,可以考虑对凸模的局部圆角进行一定的放大,但必须在后工序中对该部位校形来达到产品尺寸要求。
在拉延模设计时,通常都是将凹模圆角设计成略小于产品件上相应部位的圆角。因为在拉延模调试过程中,若对凹模圆角进行修磨,由小圆角修成大圆角比较方便、快捷和经济;反之若将凹模圆角由大变小,需要对凹模进行堆焊修补,修模工作量大,既费时又不经济。
⑥压料的作用。为了防止皱褶的产生,在拉延凸模四周设计一压边圈,由弹簧、氮气弹簧或油、气压元件将力作用于压边圈上。
这个力的大小是非常重要的参数。当压边圈所受的压力不足时,拉延过程中将使材料产生皱褶;当压边圈所受的压力过大时,拉延过程中将使材料受到抑制而使侧壁产生过分拉延而产生破裂。压边圈所受到的压力使材料压紧在凹模上,因此称为压料力。
压料力既要保证有足够的压力使材料在压边圈下面顺利流动,又要有足够的压力以抑制材料产生皱褶。
⑦排气孔。排气孔的位置、数量及直径大小,应根据拉延件的形状设计,以能顺利地排气而又不破坏拉延件表面为宜。一般的,为将空气排出模具以外,应尽可能开较大的排气孔,并且均匀布置。
⑧进出料方式。根据原材料的形式确定进料方法、取出和整理制件的方法。
⑨压料与卸料方式。确定压料或不压料,采用刚性卸料还是弹性卸料,使用多少个氮气弹簧等。
⑩必要的计算。汽车覆盖件各工序都需要进行必要的计算,拉延工序也不例外。
模具材料的选择。主要是指拉延凸模与凹模、压边圈及上、下模座等制造所使用的材料。尽可能选用国产材料,这样可以降低模具制造费用。
其他。包括拉延模具的工艺孔、起吊装置设计等。
除模具加工成本、产品质量等要求外,在模具设计时还必须对其维修性能、操作方便、安全性等,特别是在手工操作模具的安全方面予以充分的考虑。
1.3.2 修边冲孔模具设计
(1)在进行修边冲孔模具设计之前必须阅读的资料
①覆盖件产品图。覆盖件产品图(2D和3D图)是所有工序生产的依据。在设计修边冲孔模之前,要仔细认真地阅读覆盖件产品图,充分理解产品设计思想、产品的各项功能和技术质量要求,并预计或设想修边冲孔时哪些因素会对产品质量产生不良影响。
②覆盖件产品DL图。结合覆盖件产品图,认真阅读覆盖件DL(2D和3D)图,要明确修边部位、修边质量要求以及冲孔加工内容及要求,以及修边冲孔工序与前、后各道工序之间的关系等。同时,分析和研究工艺设计时所初步确定的修边(冲孔)方式、修边(冲孔)方向等设计思想,认真考虑在模具中实现的可能性和可行性措施,预防可能出现的问题等,这对修边冲孔模设计是非常重要的。
(2)修边冲孔质量问题分析
认真研究覆盖件冲压工艺文件,结合工序样件(如果有的话),根据修边线的空间形状特点对修边(冲孔)时可能会产生的质量问题进行分析、对比,并制订在模具结构、修边方式以及修边刃口等方面的应对措施。
(3)资料准备
准备好有关的修边冲孔模具设计所需的参考资料,如以往的类似件的修边冲孔模具图样、模具国家标准、行业标准以及企业标准、标准件与通用件样本,还应具备有冲压件的公差、产品所用板材的各项性能参数以及客户要求等。
(4)设计要点
①修边方式与修边(冲孔)方向的确定。在冲压工艺设计时,已经初步确定了修边方式与修边(冲孔)方向。因此,在进行修边冲孔模具设计时,首先要对冲压工艺规定的修边方式与修边(冲孔)方向的合理性进行探讨,是否还存在不合理的情况,修边方式与修边(冲孔)方向是否能保证制件的质量要求等。在进行综合分析后,最终确定修边方式与修边(冲孔)方向。
②确定模具结构。根据所确定的修边方式与修边(冲孔)方向,以及生产纲领与公司(客户)实际情况,决定采用何种模具结构。
③拉延件在修边冲孔模具中的定位。选择拉延件在修边冲孔模具中的定位方式时,要充分考虑拉延件的结构与形状特点、修边线的形状与位置以及汽车覆盖件冲压加工的基准等,选择定位最可靠、不影响模具结构布置(特别是斜楔的安放等)、能够保证修边冲孔质量的定位方式。拉延件在修边冲孔工序中的定位形式主要有:型面定位;定位半圆孔;下模导正销 (如一模两件生产)。
④斜楔机构设计。汽车覆盖件修边冲孔模具中,斜楔机构的应用非常普遍。斜楔机构的合理、动作的灵活是保证修边冲孔质量的基本要求。在此基础上,所设计(或选择)的斜楔机构的斜楔角、滑块尺寸以及滑块行程等参数要尽可能使斜楔机构紧凑,以缩小整体模具结构尺寸。
⑤确定修边刃口轮廓。在确定修边刃口轮廓时,要考虑到后面的翻边整形工序的变形。当曲线或曲面的翻边高度不大,可以翻边整形时,则修边轮廓可以由连续光滑曲线组成;当翻边高度较大,加工会出现皱褶、破裂等质量缺陷而不能整形时,则需要在修边轮廓合适的部位进行切口。
⑥冲孔凸、凹(套)形式的确定。冲孔凸、凹(套)形式比较多,应根据不同的情况采用不同的形式,尽可能地选用标准件。非圆形凸模或凹模套,一定要注意防转方向。
⑦修边冲孔间隙的确定。设计修边冲孔模具时一定要选择一个合理的间隙值,确定合理间隙值的方法有计算法、经验法、查表法等三种。
⑧确定刃口镶块形状尺寸及布置方式。根据修边线的空间形状,确定凹模刃口镶块的形状尺寸和布置方式
⑨确定废料分块及废料刀布置。根据修边废料的形状和尺寸,按废料分块原则进行废料分块,并在相应的位置布置废料刀。
⑩确定废料处理方式。根据修边(冲孔)废料的具体情况确定废料的处理方式。
修边冲孔模具的材料选择。根据不同材料厚度,修边(冲孔)模具的刃口形式主要有铸造镶块、堆焊及锻造镶块,使用的材料主要有:铸CH-1、7CrSiMnMoV和Cr12MnV等,热处理硬度58~62HRC。
其他。包括卸料板的设计以及必要的计算等。
1.3.3 翻边整形模具设计
(1)在进行翻边整形模具设计之前必须阅读的资料
①覆盖件产品图。覆盖件产品图(2D和3D图)是所有工序生产的依据。在设计翻边整形模之前,要仔细认真地阅读覆盖件产品图,充分理解产品设计思想、产品的各项功能和技术质量要求,并预计或设想翻边整形时哪些因素会对产品质量产生不良影响。
②覆盖件产品DL图。结合覆盖件产品图,认真研究覆盖件DL(2D和3D)图,明确翻边(整形)部位、翻边方向,以及翻边整形工序与前、后各道工序之间的关系等。预防可能出现的问题,这对翻边整形模设计是非常重要的。
(2)翻边整形质量问题分析
认真研究覆盖件冲压工艺文件,结合工序样件(如果有的话),根据翻边线的空间形状特点对翻边(整形)时可能会产生的质量问题进行分析、对比,并制订在模具结构、翻边方式和整形内容以及翻边镶块端面轮廓形状等方面的应对措施。
(3)资料准备
准备好有关的翻边整形模具设计所需的参考资料,如以往的类似件的翻边整形模具图样、模具国家标准、行业标准以及企业标准、标准件与通用件样本,还应具备有冲压件的公差、产品所用板材的各项性能参数以及客户要求等。
(4)设计要点
①翻边和整形方向。对冲压工艺文件给出的翻边和整形方向进行确认,翻边和整形方向要能够保证翻边整形加工的顺利进行,能保证翻边整形工序件的质量要求。
②翻边整形模具结构。首先根据翻边与整形部位和翻边与整形方向,确定修边冲孔件(上道工序件)在翻边整形模具中的摆放位置和定位方式。零件在模具中依靠零件型面或导正销定位,然后确定翻边整形模具结构。合理的翻边整形模具结构能使各翻边整形部位的加工顺利进行而不发生干涉,出件方便,结构尽量简单实用。
③斜楔机构设计(选择)。当必须使用斜楔机构时,要准确计算斜楔和滑块的行程。选择斜楔时,尽可能用标准结构,或客户指定的斜楔机构。
④翻边行程设计。应按不同的情况确定翻边行程。特别是当翻边线变化大,一个冲压方向不能成形,要分成两序完成。
⑤翻边(整形)凸、凹模镶块设计。根据翻边整形凸、凹模的分块原则,沿翻边(整形)线进行凸模和凹模镶块的分块。
根据翻边(整形)线的位置及所在型面等,确定翻边变形性质和变形程度。然后按伸长类翻边或压缩类翻边的变形性质的不同,确定翻边(整形)凹模镶块前端面的曲面形状,同时确定镶块的安装位置。
确定合适的翻边(整形)凸、凹模镶块交接部位、交接量等。
⑥退件机构设计。对需要两面或两面以上向内翻边的制件,要考虑退件机构(翻边顶出器)。若选择凸模开花结构,必须正确设计凸模的扩张范围、初始和最终位置,保证制件能顺利地从翻边凸模上退下。设计的退件机构,必须运动灵活、方便与实用。
⑦压料面尺寸确定。主要是确定压料板和凸模的压料面尺寸。对于汽车覆盖件平坦与斜面形状的压料面尺寸,外板和内板要求是不同的。另外,压料面的符型区应与托料面相互对应。
⑧压料板设计。应注意压料板强度和刚性,以及压料板的行程,压料板与凹模的间隙必须确定好。
⑨导向腿的吃入量一定要大于弹性元件的受压缩量,导滑面长度一定大于压料板的行程(一定考虑开模状态和闭合状态以及存放状态)。
⑩一定要保证翻边刀块同时翻边。
存在翻孔时,必须有顶出器,而且顶出器要有初定位作用。
在对沿周翻边使用翻边顶出器时,一定要考虑翻边顶出器的行程,必须保证板件没有任何干涉,即在自由状态下顶出。
如果不是垂直翻边,必须区分翻边刀块的轮廓线和翻边分模线。
其他。包括翻边整形模具的导向与导向间隙以及必要的计算等。
1.3.4 斜楔模具设计
(1)在进行斜楔模具设计之前必须阅读的资料
①覆盖件产品图。覆盖件产品图(2D和3D图)是所有工序生产的依据。在设计修边冲孔模之前,要仔细认真地阅读覆盖件产品图,充分理解产品设计思想、产品的各项功能和技术质量要求,并预计或设想修边冲孔时哪些因素会对产品质量产生不良影响。
②覆盖件产品DL图。结合覆盖件产品图,认真研究覆盖件DL(2D和3D)图,明确修边(或翻边)部位、修边(翻边)方向和冲孔部位与方向,以及该工序与前、后各道工序之间的关系等。预防可能出现的问题,这对斜楔模设计是非常重要的。
(2)产品质量问题分析
认真研究覆盖件冲压工艺文件,参考工序样件(如果有的话),结合斜楔模具的特点,对修边(或翻边、冲孔等)时可能会产生的质量问题进行分析、对比,并制订在模具结构、修边(或翻边、冲孔等)方式和内容以及镶块轮廓形状等方面的应对措施。
(3)资料准备
准备好有关的斜楔模具设计所需的参考资料,如以往的类似件的斜楔模具图样、模具国家标准、行业标准以及企业标准、标准件与通用件样本,还应具备有冲压件的公差、产品所用板材的各项性能参数以及客户要求等。
(4)设计要点
①修边、翻边(整形)及冲孔方向。对冲压工艺文件给出的修边、翻边(整形)及冲孔方向进行确认,修边、翻边(整形)及冲孔方向要能够保证修边、翻边(整形)及冲孔等加工的顺利进行,能保证修边、翻边(整形)及冲孔工序件的质量要求。
②斜楔模具结构。首先根据修边(或翻边、整形、冲孔等)部位和方向,确定斜楔机构在模具中的摆放位置和定位方式,然后确定其模具结构。
③斜楔机构设计(选择)。在设计斜楔模具时,首先根据工艺要求,设计(选择)相应的斜楔机构类型,主要是斜楔和滑块设计。准确计算斜楔和滑块的行程及回位力,确定采用哪种滑块的回位方式。选择斜楔时,尽可能用标准结构,或客户指定的斜楔机构。
④斜楔机构行程设计。应按不同的情况确定其行程。修边与翻边及冲孔等的斜楔机构行程要求是不同的。
⑤凸、凹模镶块设计。根据不同模具类型(修边、翻边、整形及冲孔等),确定凸模和凹模镶块的分块及端面形状与安装位置。特别是斜楔机构的定位和防侧向力措施一定要设计好。
⑥压料板设计。斜楔模具的压料板有上压料板、侧压料板及侧压料和正压料共用压料板三种类型。应根据压料板凸起形状、动作方向和个数等,选择压料板的类型。
压紧力的大小可根据修边冲孔模或翻边整形模等不同情况确定。对侧冲孔工序,压料板的行程必须大于冲头进入压料板的长度+5mm,否则将导致冲头折断。
⑦斜楔模具的废料处理。斜楔模具的废料处理分三种情况,即修边废料的处理、冲孔废料的处理和切断(或切口)的废料处理。
⑧其他。包括斜楔模具的导向与导向间隙、斜楔机构力和行程的关系、斜楔行程示意图的作法及必要的计算等。
1.3.5 模具设计常用符号
汽车覆盖件模具设计(2D)常用符号见表1-3。
表1-3 汽车覆盖件模具设计(2D)常用符号
