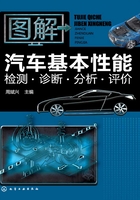
第二节 汽车制动性能检测
汽车制动性能的好坏对行车安全与否有重要的影响,保证良好的制动性能是安全行车的第一要求,制动性能的检测是汽车安全检测中最基本和最重要的一个检测项目。
一、制动性能下降的分析及对制动过程的基本要求
(一)制动性能下降的分析
1.制动效能下降
汽车制动效能下降表现为汽车没有足够的制动力,不能保证汽车迅速、平稳地停车。其具体表现是踩住制动踏板后,制动器制动力不能迅速增大,制动减速度不足,制动距离过长或制动时间过长。
2.制动跑偏
制动跑偏是由制动时左、右不对称因素所引起的,如左、右轮(尤其是转向轮)产生的地面制动力大小不等,轮胎结构或气压不同,悬架刚度有差异,车辆左、右两边载荷不均及路面状况不同等。其结果都会使制动时左、右两侧地面制动阻力不等,车辆就容易驶向阻力大的一侧。图2-6所示给出了一种示例,图中F1、F2、F3和F4分别为各轮所受地面制动力,其中,左前轮制动力偏大。Fi为汽车总的惯性力。显然,制动力的合力并不在汽车中心线上,而是偏向左侧,因此汽车向左跑偏。

图2-6 制动跑偏示例
3.制动侧滑
制动侧滑是制动时车辆产生横向滑移的现象。本来车辆在正常行驶或虽制动而车轮未被抱死的情况下,车轮是有一定的横向(即侧向)附着力的,但车轮在抱死制动时,横向附着力几乎全部丧失,因而很容易受横向力的干扰而发生制动侧滑现象。理论分析和实践都已证明,若制动时前轮先抱死而后轮未抱死,如图2-7(a)所示,则前轮首先失去横向附着力。此时若前轮受到小的干扰力f,就很容易横向移动(侧滑),整车会以其后轴S处为中心发生偏转。但因汽车重心在S点前面,惯性力Fi具有自动回正作用,所以整车尚处于稳定状态,能够按直线减速停车,但在弯道上行驶时容易失去方向控制能力。若后轮比前轮先抱死,如图2-7(b)所示,则后轮失去横向附着力,在受到横向干扰而侧滑时,前轴S处成了偏转中心。此时因惯性力Fi作用在S点的后面,导致车辆立即失去稳定性,极易出现甩尾或打转现象。所以后轴先抱死是非常危险的。若前、后各轮同时抱死,则可以避免后轴侧滑,还可以最大限度地发挥前、后轴的制动效能,是三者中最好的一种状况,但制动过强时汽车也会丧失转向能力。

图2-7 车轮抱死时的运动状态
4.紧急制动时的轴荷转移现象
汽车紧急制动时速度急剧减小,因惯性作用,汽车有继续向前冲的趋势(坐在汽车里可以明显地感受到这种作用)。
汽车受到的惯性力如图2-8中的Fi所示。

图2-8 紧急制动时汽车的受力情况
Fi作用于汽车的质心,并指向汽车前进方向,而向后的制动阻力FF、FR却是作用在车轮与地面的接触点。由力学分析很容易知道,这些力的共同作用,有使图2-8中的汽车向前倾的趋势。而汽车质量是通过有弹性的悬架系统作用在车轮上的,这就造成了紧急制动时汽车的“点头”和“翘尾”现象。其最终结果是,尽管汽车的总质量未变,但与静态时相比,前轴动态载荷增大,而后轴动态载荷减小。
由于汽车紧急制动时后轴动态载荷减小,轮胎与路面之间的附着力明显下降,很容易引起车后部侧滑(甩尾)。因此,某些汽车装置了比例阀来调整紧急制动时的前、后轴制动力比例,以减轻紧急制动时侧滑(甩尾)。ABS系统也能较好地减轻紧急制动时的侧滑(甩尾)。
(二)对制动过程的基本要求
为保证行车和停车的安全,对制动过程有以下基本要求。
①要有足够的制动力,以保证汽车能够迅速、可靠地停车。
②制动操作要轻便,以免引起驾驶员的疲劳,降低制动操作能力。国家标准规定了驾驶员在进行制动时的施力大小。
③应具有驻车制动功能,以保证车辆停放在停车场或有一定坡度的坡路上原地不动而不至于滑溜。
④应具有应急制动功能,以利于在行车制动失效之后,能在规定的制动距离内将车辆停住和保证汽车有效减速。
⑤不能自行制动。在不需制动时,不能因车体振动或转向等引起制动作用;放松制动踏板后,制动力应能迅速消失,不应出现残余制动力(这种现象称为拖滞或阻滞),以免使行车阻力增加。
⑥应具有制动方向稳定性,使汽车在紧急制动时能够保持稳定的行驶方向,避免跑偏、侧滑等现象发生。
⑦应具有制动效能恒定性,使制动器尽量不受制动器工作时产生的高温和外界进入的水的影响而减退效能。
二、汽车制动检测设备
汽车制动检测的路试设备和工具主要有第五轮仪、减速度仪或米尺、秒表、标杆等,台试的设备主要是制动试验台,包括滚筒式和平板式制动试验台,下面分别予以介绍。
(一)第五轮仪
第五轮仪简称五轮仪,它可以测量制动过程中的制动距离、制动时间和制动初速度。五轮仪由机械和电子两部分组成。其机械部分(图2-9)主要是一个车轮,使用时拖在车后,故称为“第五轮”。为保证车轮转动时与地面可靠接触而不致跳动,轮旁装有储气筒、气缸、活塞杆等装置,以保持车轮和地面间的压力。

图2-9 第五轮仪的机械结构
电子部分包括传感器和单片机等信号采集和处理装置。电磁传感器装在第五轮轴上,它由磁环、齿轮和线圈等组成。当车行驶时,第五轮跟随转动,内、外齿轮相对运动,引起磁路磁阻发生变化,线圈内便感应出交变电压信号。经放大处理后,形成频率与车轮转速成正比的脉冲信号。由于车轮外径是固定的,所以根据单片机在一定时间内记录的脉冲数,就可以计算出汽车的车速及走过的路程。例如在检测制动性能时,可以首先监视车速使之达到规定的速度,然后立即踩制动踏板,同时记录脉冲个数,直到车停下为止。通过制动过程中记录的脉冲个数就可以算出该车的制动时间,同时可换算为制动距离。
(二)减速度仪
减速度仪用来测量制动减速度的大小。减速度仪有摆锤式和滑块式两种。两者所依据的基本原理,都是牛顿第二定律。通过直接或间接测量所受的阻力的大小,就可以计算出物体的减速度。
图2-10所示为摆锤式减速度仪结构示意。如果把减速度仪安装在汽车内,当汽车处于静止或匀速运动时,摆锤会保持铅垂位置。若汽车作加速或减速运动,则摆锤会因惯性作用(可将这种作用称为惯性力)而偏斜一个角度θ。由于减速度与角度θ的关系为a=gtanθ,即减速度与摆锤的偏斜角θ的正切成正比,所以只要测量出摆锤的偏斜角θ,就可以计算出减速度的大小。g为重力加速度。

图2-10 摆锤式减速度仪结构示意
如果没有以上设备,也可以用米尺、标杆、秒表等简单工具在道路上检测制动距离和制动时间。为保证检测精度,在路试法检测制动性能中常使用第五轮仪检测制动距离、制动时间和制动初速度,用减速度仪或用其他测试方法测量车辆充分发出的平均减速度(MFDD)。
(三)汽车制动试验台
汽车制动试验台有多种类型,按试验台测试原理的不同,分为反力式和惯性式两类;按试验台支承车轮形式的不同,分为滚筒式和平板式两类。目前,单轴反力式滚筒制动试验台(测力式)在国内应用最为普遍。
1.反力式滚筒制动试验台的结构
图2-11所示为单轴反力式滚筒制动试验台结构示意,主要由驱动装置、滚筒装置、测量装置、举升装置、指示与控制装置等组成,其具体说明见表2-2。

图2-11 单轴反力式滚筒制动试验台结构示意
表2-2 反力式滚筒制动试验台的结构


图2-12 制动试验台的指示与控制装置框图
此外,由于对汽车制动性能的评判与轴重有关,现在很多制动试验台都装有配套的轴重计量设备。
2.反力式滚筒制动试验台的检测原理
准备检测时,升起举升器,将被测汽车驶上制动试验台,车轮置于主、从动滚筒之间,降下举升器。通过延时电路启动电动机,电动机则通过减速器及链传动驱动滚筒,从而带动车轮低速旋转。当驾驶员踩下制动踏板,在制动器摩擦力矩Mμ作用下[图2-13(a)],车轮开始减速旋转。此时电动机驱动滚筒,而滚筒则对车轮轮胎周缘的切线方向作用着驱动力Fx1、Fx2,以克服制动器摩擦力矩,维持车轮继续旋转。与此同时,车轮轮胎在滚筒表面切线方向作用着与滚筒驱动力数值相等而方向相反的反作用制动力F'x1、F'x2。在F'x1、F'x2对滚筒轴线形成的反作用制动力矩作用下,浮动的减速器壳体与测力杠杆一起朝与滚筒转动相反的方向摆动[图2-13(b)],而测力杠杆另一端的力F1经传感器转换成与反作用制动力大小成比例的电信号。此信号经放大变换处理后,由指示装置显示出由车轮制动器产生、经轮胎传递、作用在滚筒上的制动力。在制动过程中,当左、右轮制动力之和大于某一数值时,微机即开始采集数据,采集过程所经历的时间是一定的。经历了规定的采集时间后,微机发出指令使电动机停转,以防止轮胎剥伤。检测过程结束后,将举升器举起,车辆即可驶离试验台。

图2-13 制动力检测原理
GK—车轮所受的载荷;F—车轴对车轮的水平推力;N1,N2—滚筒对车轮的支承反力;Fx1,Fx2—滚筒对车轮的驱动力;F'x1,F'x2—车轮对滚筒的切向反作用力;Mμ—制动器摩擦力矩;Mf1,—滚动阻力矩;α—安置角;L—滚筒的中心距
车轮阻滞力的测量在行车和驻车制动装置处于完全释放状态、变速器置于空挡位置时进行。此时,电动机通过减速器、链传动及滚筒来带动车轮维持稳定转动所需的力,即为车轮的阻滞力,该力可通过指示装置读取。
制动协调时间的测量是与测量制动力同步进行的,它以驾驶员踩踏板的瞬间作为计时起点,由制动踏板上套装的踏板开关向控制装置发出一个“开关”信号,开始时间计数,直至制动力达到标准规定的制动力的75%时为止。其计时终点通常由试验台微机执行相应的程序来控制。
3.反力式滚筒制动试验台的检测特点
①检测迅速、安全、经济,不受外界条件的限制,测试条件稳定,重复性较好。
②能定量地测得各车轮的制动力大小、左轮和右轮制动力差值、制动协调时间、车轮阻滞力等,因而可全面评价汽车的制动性,并给制动系统的故障诊断、维修和调整提供可靠依据。
③不能反映防抱死制动系统(ABS)的性能。制动检测时的车速较低(一般不超过5km/h),与实际制动状况相差甚远,因而无法对具有防抱死制动系统汽车的制动性能进行准确测试。
④进行制动检测时,汽车没有平移运动,因而也就没有因惯性作用而引起的轴负荷前移作用,故车辆处于空载检测时,前轴车轮容易抱死而难以测得前轴制动器能够提供的最大制动力,从而导致整车的制动力不够,易引起误判。同时,汽车的无移动检测也不能反映汽车其他系统(如转向机构、悬架)的结构、性能对制动性能的影响。
⑤试验台制动时的最大测试能力,受检测因素的影响较大。根据图2-13(a)所示的受力图列出平衡方程,可得车轮制动时试验台能提供的制动力极限值为
式中 ϕ——滚筒与车轮表面的附着系数。
由上式可知,试验台的最大测试能力受安置角α、附着系数ϕ、水平推力F三方面因素的影响。当α、ϕ、F增加时,制动力的最大测试能力增加;而当车轮直径增大,附着系数减小,非测试车轮制动力过小时,则被测车轮容易抱死,其最大制动力难以测出,从而导致整车制动力过小,易引起误判。
要提高反力式滚筒制动试验台的测试能力,就要增加轮胎与滚筒的附着力,避免制动时车轮抱死。为此,常用的措施如下。
①在车辆上增加足够的附加质量,或施加相当于附加质量的作用力,而这些均不计入轴荷。
②在非测试车轮上加三角垫块或采取牵引方法阻止车辆移动。
③保持轮胎及滚筒表面的干燥、清洁。
4.惯性式滚筒制动试验台和平板式制动试验台介绍
(1)惯性式滚筒制动试验台 利用其旋转飞轮的动能模拟车辆在道路上行驶的动能,使车辆在试验台上能呈现路试制动时的工况来检测制动性能。惯性式滚筒制动试验台检测的是制动距离、制动减速度和制动时间。
惯性式滚筒制动试验台,按同时检测的轴数多少可分为单轴式和双轴式。双轴惯性式滚筒制动试验台结构简图如图2-14所示,该试验台可以同时测试双轴车辆所有车轮的制动性能,它可根据车辆的轴距调节前、后滚筒组之间的距离。该距离可用驱动移动架液压缸17调节,使滚筒组在导轨上移动,调节合适后用夹紧液压缸18进行夹紧定位。前后左右各滚筒及飞轮通过连接部件相连。为防止汽车制动时车轮向后窜出,在后滚筒组后部装有第三滚筒19。

图2-14 双轴惯性式滚筒制动试验台结构简图
1—飞轮;2—传动器;3,6—变速器;4—测速发电机;5,9—光电传感器;7—可移导轨;8,12—电磁离合器;10一移动架;11—传动轴;13—万向节;14—后滚筒;15—前滚筒;16—举升托板;17—驱动移动架液压缸;18—夹紧液压缸;19—第三滚筒;20—调节第三滚筒液压缸
惯性式滚筒制动试验台的滚筒相当于一个移动的路面,试验台上各对滚筒分别带有的飞轮,其惯性质量应与受检汽车的惯性质量相当。检测时,先使滚筒与车轮处于某一转速旋转,然后切断驱动滚筒旋转的动力,踩制动踏板,制动后的车轮对滚筒表面产生切向阻力,而滚筒在其飞轮系统的惯性作用下继续旋转,其转动的圈数相当于车轮的制动距离,在规定的检测车速下,该制动距离的大小可以充分反映被测车轮制动器和整个制动系统的技术状况。而滚筒的制动初速度、制动减速度及滚筒依靠惯性旋转的圈数均可通过测量系统测得。
利用惯性式滚筒制动试验台检测制动性能时,
可以在任意车速下进行,试验条件接近汽车实际行驶情况,其测试结果与实际工况较为接近。但这种试验台要求旋转部分的转动惯量大,结构较复杂,占地面积大,且不适应多种车型,因此在实际检测中应用并不多。
(2)平板式制动试验台 如图2-15所示,它是一种低速动态惯性式制动试验台,由四块测试平板、传感器、控制和显示装置等组成。检验时,汽车以5~10km/h的速度驶上测试平板,置变速器于空挡并紧急制动。汽车在惯性作用下,通过车轮在平板上附加与制动力大小相等、方向相反的作用力,使平板沿纵向位移,经传感器测出各车轮的制动力,并由显示装置显示检测结果。这种试验台结构简单,测试过程与实际路试条件较接近,能反映车辆的实际制动性能,也能反映制动时轴荷前移及其他系统(如悬架)对汽车制动性能产生的影响,试验台不需要模拟汽车平移惯量,较容易与轴重仪、侧滑仪组合在一起,车辆测试方便且效率较高。但这种试验台存在测试重复性差、占地面积大、需要助跑车道和不安全等问题。

图2-15 平板式制动试验台结构简图
三、制动性能的检测方法、评价指标及其相关规定
1.制动性能的检测方法
利用反力式滚筒制动试验台检测汽车制动性能时,具体检测方法如下。
①将试验台指示与控制装置上的电源开关打开,按使用说明书要求预热至规定时间。
②如果指示装置为指针式仪表,检查指针是否在零位,否则应加以调整。
③检查试验台滚筒上是否有泥、水、砂、石等杂物,如有应加以清除。
④核实汽车各轴轴荷,不得超过试验台允许的载荷。
⑤检查汽车轮胎气压是否符合汽车制造厂的规定,否则应充气至规定值。
⑥检查汽车轮胎是否有泥、水、砂、石等杂物,如有应加以清除。
⑦检查试验台举升器是否在升起位置,否则应升起举升器。
⑧汽车被测车轴在轴重计或轮重仪上检测完轴荷后,应尽可能顺垂直于滚筒的方向驶入试验台。先前轴、再后轴,使车轮处于两滚筒之间。
⑨汽车停稳后,变速杆置于空挡位置,行车、驻车制动器处于完全放松状态,能测制动协调时间的试验台还应把脚踏开关套在制动踏板上。
⑩降下举升器,至轮胎与举升器完全脱离为止。
如果制动试验台本身带有内藏式轴重测量装置的,则应在此时测出轴荷。
启动电动机,使滚筒带动车轮转动,先测出制动拖滞力。
用力踩下制动踏板,一般试验台在1.5~3.0s后或所带第三滚筒发出信号后,滚筒自动停转。
读取并打印检测结果。
升起举升器,驶出已测车轴,将下一车轴驶入,按与上述同样的方法检测制动力。
当与驻车制动相关的车轴在试验台上时,检测完行车制动后应重新启动电动机,在行车制动完全放松的情况下用力拉紧驻车制动杆,检测驻车制动性能。
所有车轴的行车制动性能及驻车制动性能检测完毕后,升起举升器,汽车开出试验台。
检测结束,切断试验台电源。
2.制动性能的评价指标
汽车的行车制动性能是指汽车在行驶中能够强制减速、停车或下坡时限速的能力。可以从制动效能、制动效能的恒定性和制动时方向的稳定性三个方面综合评价汽车的行车制动性能。
(1)制动效能 是指制动距离、制动减速度、制动时间和制动力等方面的性能,其具体说明见表2-3。
表2-3 制动效能


图2-16 MFDD示意

图2-17 简化的制动力随制动时间的变化过程
(2)制动效能的恒定性 是指车辆良好的制动效能能够持久作用下去的性能,它包括制动器材料抗热衰退的能力和制动器水湿恢复能力。
制动器摩擦材料因制动时摩擦生热,温度升高,可能引起摩擦因数减小,制动力下降,甚至摩擦片磨损烧坏,而影响制动性能,即出现热衰退现象。因此,摩擦片应具有高的抗热衰退能力,在汽车高速制动、短时间重复制动或下坡连续制动时尤其应当如此。
当制动器被水浸湿后制动力会下降,即出现水衰退现象。因此,在进水后,要求制动器能够尽快恢复其制动性能。
(3)制动时方向的稳定性 表示制动时车辆不出现跑偏、侧滑等现象的能力。制动时方向的稳定性要求车辆制动时任何部位都不得超出给定宽度的车道。
3.国家标准对检验制动性能的有关规定
国家标准GB 7258—2004对检验制动性能的规定,按检验方法分为路试和台试两类。
(1)路试检验 是在规定的路面上进行测试。用路试的方法主要检验行车制动性能和应急制动性能。这些检验应在平坦、坚实、清洁、干燥的水泥或沥青路面上进行,以保证轮胎与地面间足够的附着系数。
机动车在规定初速度下的制动距离和制动稳定性应符合表2-4所列的要求。
表2-4 制动距离和制动稳定性要求

①指最高设计车速小于或等于50km/h的,具有三个车轮的货车。
②指最高设计车速小于70km/h的具有四个车轮的货车。
③对质量大于3.5t并小于或等于4.5t的汽车,试车道宽度为3m。
④指在其设计和技术特性上主要用于载运乘客及其随身行李和临时物品的汽车,包括驾驶员座在内最多不超过9个座位。
⑤指由一辆汽车(三轮汽车和低速货车除外)牵引一辆挂车组成的机动车,包括乘用车列车、货车列车和铰接列车。
在规定的初速度下紧急制动时,MFDD和制动稳定性应符合表2-5所列的要求,并且汽车单车制动协调时间应不大于0.6s,汽车列车制动协调时间应不大于0.8s。
表2-5 制动减速度和制动稳定性要求

汽车在空载和满载情况下进行应急制动性能检验,应急制动性能应符合表2-6所列的要求。
表2-6 应急制动性能要求

在空载状态下,驻车制动装置应能保证车辆在坡度为20%(总质量为整备质量的1.2倍以下的车辆为15%)、轮胎与路面间的附着系数不小于0.7的坡道上正、反两个方向保持不动,其时间不少于5min。检验时手制动操纵力应符合有关规定。
国家标准规定,对空载检验制动性能有质疑时,可按满载检验的制动性能要求进行检验。
应急制动时性能要求:汽车(三轮汽车除外)在空载和满载状态下,按表2-7所列初速度进行应急制动性能检验,测量从应急制动操纵始点至车辆停住时的制动距离,应急制动性能应符合表2-7的要求。
表2-7 应急制动性能要求

①指在其设计和技术特性上主要用于载运乘客及其随身行李的商用车,包括驾驶员座位在内座位数超过9个。
(2)台试检验 就是利用试验台进行测试。与路试相比,台试更省时、省地、不受道路和气候的影响,更方便,所以得到普遍应用。
①制动力检验:汽车、汽车列车在制动试验台上测出的制动力,应符合表2-8的要求,对空载检测制动力有质疑时,可用表2-8中规定的满载检验制动力要求进行检验。
表2-8 台试检验制动力要求

①用平板制动试验台检验乘用车时应按动态轴荷计算。
②空载和满载状态下测试均应满足此要求。
②制动力平衡要求:就是对左、右轮制动力差的限制性要求,用以保证汽车制动方向稳定性。国家标准规定在制动力增长全过程中同时测得的左、右轮制动力差的最大值,与全过程中测得的该轴左、右轮最大制动力中大者之比,对前轴不得大于20%,对后轴在后轴制动力大于或等于后轴轴荷的60%时不得大于24%,当后轴制动力小于后轴轴荷的60%时,在制动力增长全过程中同时测得的左、右轮制动力差的最大值不得大于后轴轴荷的8%。
③制动协调时间:普通汽车制动协调时间应不大于0.6s,汽车列车制动协调时间应不大于0.8s。
④阻滞力:即解除制动后车轮转动时受到的残余阻力。国家标准GB 7258—2004规定,各车轮的阻滞力均不得大于该轴轴荷的5%。
⑤驻车制动性能检验:用制动试验台检验驻车制动力时,车辆应空载,乘坐1名驾驶员,驻车制动力的总和应不小于该车在测试状态下整车重量的20%,对总质量为整备质量1.2倍以下的车辆,此值为15%。
应该指出,上述路试和台试的各种方法,并不需要全部检验。按国家标准规定,只要选择检验以下三项之一即可全面评价行车制动系统的制动性能:制动距离及制动方向稳定性(路试);制动减速度、制动协调时间及制动方向稳定性(路试);制动力、制动协调时间及阻滞力(台试)。