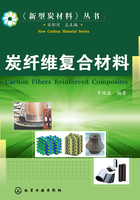
2.2 高性能增强炭纤维
2.2.1 概述
高性能纤维具有高强度、高模量、耐高温和耐腐蚀等特性,是近年来发展迅速的一类特种纤维,而高性能炭纤维是高性能纤维中发展最迅速也是应用最广泛的纤维。炭纤维既具有炭材料的固有特性,又兼备纺织纤维的柔软可加工性,是高科技领域中新型工业材料的典型代表,为世人瞩目。
炭纤维是采用一些含碳的有机纤维(如尼龙、腈纶和人造丝等)作原料,将有机纤维与树脂结合在一起,放在稀有气体的环境中,在一定张力、温度和压强下,经过一定时间的预氧化、炭化和石墨化处理等强热过程制成。按原丝类型可分为聚丙烯腈(PAN)基炭纤维、沥青基炭纤维和黏胶基炭纤维。本小节主要介绍三种炭纤维的结构、主要性能、生产工艺以及发展现状。
2.2.2 聚丙烯腈基炭纤维
2.2.2.1 概述
PAN作为生产炭纤维的原料始于20世纪50年代末期,随后各种制备炭纤维的前驱体应运而生,PAN纤维的应用和生产也得到了很大的发展。PAN炭纤维因其具有强度高、刚度高、重量轻、耐高温、耐腐蚀和电性能优异等特点,在与其他纤维的竞争中发展壮大。
PAN炭纤维是一类具有很高技术含量的纤维材料,综合性能优异,它与树脂、金属、陶瓷及炭素等基体复合,可以用作承力结构材料、耐烧蚀防热功能材料、摩擦材料、导电和导热材料等,是先进复合材料首选的、使用最多的增强材料。PAN炭纤维生产一般要经过四个主要过程[1]:优质共聚PAN原液的合成,高性能共聚PAN纤维的制备,高性能PAN纤维的预氧化,炭化以及炭纤维的表面处理。为了制造出高性能炭纤维并提高生产率,要求原料杂质少、缺陷少、强度高、毛丝少、细度小且均匀,纤维中链状分子沿纤维轴取向度高(通常大于80%),热转化性能好。
2.2.2.2 PAN基炭纤维的结构及性能
2.2.2.2.1 PAN基炭纤维的结构
PAN基炭纤维是PAN基纤维原丝经氧化稳定化、炭化、石墨化和后处理,由有机合成纤维转化为含碳量在90%以上的无机炭纤维。PAN基纤维是由以丙烯腈为主要链结构单元的聚合物经过纺丝加工而制成的纤维,其基本化学结构式是:

人们对PAN基炭纤维的结构进行了大量研究,提出了多种炭纤维结构模型,比较具有代表性的是条带模型和微原纤模型。Perret和Ruland提出了炭纤维的条带模型[2],如图2.1所示。条带模型由平均宽度Lc为5~7nm、平均长度La为几百纳米的带状石墨层组成,条带可以从一个区域进入另一个堆叠区,条带之间连续平行堆叠而存在针形的孔洞,孔洞长度大于条带的平均直线部分。Diefendon和Tokarsky等人提出了微原纤模型[3],如图2.2所示。微原纤结构模型类似于条带模型,但是微原纤是基本的结构单元,由10~30个基本面构成微原纤,再由它堆叠成条带结构。

图2.1 炭纤维的条带结构模型

图2.2 炭纤维的微原纤结构模型
2.2.2.2.2 PAN基炭纤维的性能
由于PAN基炭纤维的含碳量在90%以上,且具有类似微晶化的多环芳香族的结构特征,因此炭纤维最为突出的特点是强度高、模量高、密度低。此外还有如下特点:①耐高温,可在2000℃使用,3000℃非氧化气氛中不熔不软;②能耐浓盐酸、磷酸、硫酸、丙酮和苯等介质的侵蚀;③热膨胀系数相对较小;④热导率大,为10~140W/(m·K);⑤摩擦系数小和导电性好。
(1)力学性能
炭纤维的力学性能主要包括强度、模量和断裂伸长率,由其微观组织结构决定[4]。炭纤维的微观组织结构包括表面结构、石墨微晶结构、孔隙结构和取向结构等。力学性能是PAN基炭纤维非常重要的性能,科研工作者对如何提高炭纤维的力学性能进行了大量研究,发现严重的皮芯结构、芯部组织疏松或有孔洞出现、晶相少且无明显取向、石墨层排列紊乱都会造成炭纤维力学性能降低。因此,提高碳元素的含量和纤维结晶度,减少皮芯结构和孔洞,提高石墨层取向和堆叠程度是获得高性能炭纤维的必要条件[5]。部分国外PAN基炭纤维的主要物理和力学性能如表2.1[6]所示。
表2.1 部分国外PAN基炭纤维的主要物理和力学性能[6]


Orowan根据原子间束缚力(价键力)随原子间距变化而变的基本规律,提出了材料的理论强度σth与材料断裂时所做的功及生成两个新表面能有关,可写为:
(2.1)
式中,σth为理论强度;E为弹性模量;γ为新表面的表面能力(断裂表面能);a为原子间距或晶格常数。
由式(2.1)可知,每一种材料的理论强度与其固有的原子间距、弹性模量和表面能有关,因此每种材料的理论强度又有显著的差异,即理论强度是材料固有的本征特征。
固体材料的理论强度可用Gilman经验式估算。
(2.2)
对于具有层状结构的石墨来说,模量E值取1020GPa,在石墨层的每一层碳原子可提供一个非定域π键,使C—C键长y0由0.154nm缩小到0.142nm,表面能γ取9.7×10-4J/cm2。将上述数据代入式(2.2),得到石墨材料的理论抗拉强度σth为180GPa。目前抗拉强度较高的炭纤维T1000为7.02GPa,仅为理论值的3.9%,实际抗拉强度与理论值相差甚远。换言之,炭纤维的抗拉强度可提高的空间还很大,提高技术措施是使原丝细旦化、结晶化、均质化和致密化,尽可能减少表面缺陷和结构缺陷。调控缺陷大小、缺陷数量以及分布状态是提高炭纤维抗拉强度的基本思路。
①PAN原丝对炭纤维力学性能的影响。PAN原丝在纺丝过程中经常出现诸如表面横向皱折、表面横向裂纹、皮芯结构、轴向裂纹、表面沉积物、竹节丝和并丝等缺陷,这些缺陷都毫无保留地“遗传”给炭纤维,特别是表面横向裂纹、竹节丝、皮芯结构和表面横向皱折以及表面沉积物,在以后的预氧化和炭化工艺中将使炭纤维产生不可弥补的先天性缺陷。这些缺陷的存在极易产生局部应力集中,导致炭纤维力学性能下降。近年来,日本的炭纤维工业使炭纤维从T300发展到T800,再发展到T1000,炭纤维质量能够得到大幅度提高与原丝质量的不断提高和完善有着密切关系。
提高原丝质量的主要方法:a.丙烯腈单体原料要求纯度高,杂质少,聚合物分子量一般控制在8×104左右;b.纺丝液应多次脱泡过滤,除去原料中气泡、粒子等杂质;c.纺丝环境应清洁、干净、灰尘少,空气中灰尘也会造成原丝的缺陷;d.原丝生产中应注意提高其结晶度和取向度,原丝的储存时间对于炭纤维的质量也有一定的影响,因为原丝在储存期间其结晶度和分子链取向都发生了很大变化,取向角度变化大约3°,平均微晶尺寸增加了1.3nm,从而导致了炭纤维力学性能的下降,因此要生产高性能炭纤维,应尽量避免使用储存期过长的原丝[7];e.对原丝进行改性,提高原丝性能。
对PAN基炭纤维原丝的改性:一般可以通过简单的物理、化学方法来提高其力学性能并且可以赋予纤维新的性能。与开发新产品相比,不仅成本低,开发周期短,而且收效明显。
炭纳米管是一种理想的填料,有着优异的力学性能,将炭纳米管与PAN纺丝溶液进行机械掺混,对原丝改性,最终可以使炭纤维的性能得到改善。Sreekumar等[8]利用溶液共混制得单壁炭纳米管(SWNT)/PAN 纺丝原液,含有10%(质量分数)SWNT的PAN湿纺纤维,室温下抗拉模量增加100%,150℃下抗拉模量增加一个数量级。王少军等[9]在凝固浴中加入经酸处理的多壁炭纳米管(MWNTs),制得MWNTs PAN基炭纤维,在凝固浴中加入经过酸处理的 MWNTs,对填补 PAN 基炭纤维原丝内部的微孔有明显的作用,降低了原丝的晶区取向,提高了原丝的断裂强度、断裂伸长率及拉伸韧度。添加MWNTs前后PAN基初生纤维的截面图如图2.3和图2.4所示。

图2.3 在凝固浴中未加MWNTs的PAN基初生纤维截面的SEM图[9]

图2.4 在凝固浴中加入MWNTs的PAN基初生纤维截面的SEM图[9]
采用一定质量浓度的高锰酸钾水溶液,在合适的温度和时间条件下对PAN原丝进行改性可以提高原丝的力学性能。在预氧化过程中高锰酸钾一方面作为增塑剂提高了分子链的择优取向度,另一方面作为催化剂促进直链分子向梯形结构转化,而且高锰酸根可以扩散进入纤维中促进分子链的环化,避免形成壳-芯结构,使纤维结构均一,避免了纤维内部的应力集中。国内专家研究发现,经高锰酸钾改性后,原丝在预氧化过程中的放热量减少,氧化过程更加平稳,使得纤维表面出现的沟槽和裂缝较少,高锰酸根结合到纤维内部,改变了纤维的结构,促使环化反应提前,预氧化过程放热平缓同时使得预氧化时间大幅度减少。高锰酸钾改性使得预氧化反应能够在纤维内外同时进行,减少了皮芯结构的生成,提高了最终炭纤维的力学性能[10,11]。Bahl等人[12]研究了高锰酸钾改性对PAN原丝的影响,发现用高锰酸钾处理原丝可将最终炭纤维的强度由2.1GPa提高到4.2GPa。PAN原丝的高锰酸钾改性需控制最佳时间,过度的改性会损伤纤维性能。
张旺玺等[13]在原丝连续制备的同时采用NiSO4溶液对PAN原丝进行改性,改性后原丝没有损伤,使炭纤维的抗拉强度提高了20%~30%,抗拉模量提高了5%~10%。于法涛等[14]对预氧化纤维用盐酸羟胺进行浸渍改性,并研究了预氧化纤维在低温炭化下的一些性能。研究发现在低温炭化时减少了环化的时间,缓和了环化反应,避免了对炭纤维的性能的损坏,提高了低温炭化后纤维的强度和模量。对炭纤维渗硼改性能够改善炭纤维结构,提高其力学性能。采用某种硼化物对炭纤维浸渍热处理后,其模量和强度可分别提高10.3% 和15.3%。另外渗硼处理可提高炭纤维的择优取向和晶体尺寸,减少表面缺陷,致使渗硼后炭纤维性能明显提高[15]。
很多研究者正在寻找通过对原丝进行物理改性提高炭纤维性能的手段。Ko等[16]在蒸气中拉伸PAN原丝以提高炭纤维的力学性能,预氧化过程在常规电炉加热氧化条件下,由于表面皮部结构的致密特性,外部氧气向纤维内部扩散有较大的阻力,结果使表面皮部氧化过量而芯部不足,产生径向结构氧化程度差异[17,18]。徐海萍等人[19]用射频电场极化改性原丝发现,该射频等离子法可使原丝内外氧化趋于一致,有利于改善预氧化纤维的径向差异。改性后的微纤是由相互缠结、紧密排列的超微纤丝组成,超微纤丝具有沿轴向伸展的左螺旋结构,且表面原子取向排列。等离子法形成的这种结构有利于提高炭化后的力学性能。
②预氧化对力学性能的影响。原丝预氧化的主要目的是使原丝中线型分子环化脱氢,转化为耐热的梯形结构,使其在炭化过程中保持纤维形态,避免出现熔融及并丝,影响后续工序正常进行。若想提高炭纤维的强度,预氧化程度要适当,预氧化程度太低,纤维不能有效的形成梯形结构,不利于下一步炭化;预氧化程度过高,会使聚合物主链损失,减少炭化收率,影响炭纤维质量。
纤维的预氧化程度是指其线型分子转化为梯形结构的程度,环化程度并非越高越好。Watt[20]认为50%左右的氰基发生环化反应可获得最佳力学性能,这可能是因为未环化的线型链段在炭化初期可产生滑动和扭曲,使刚性的环化链区形成平面,为进一步炭化形成石墨平面结构打下基础。
PAN纤维的预氧化主要是氰基的引发和聚合反应,形成梯形的亚胺聚合物,同时这些反应产物与氧结合生成含氧化合物。随着氧化反应的进行,原丝中具有较强内聚能的—CN基团逐渐转变为内聚能较弱的梯形亚胺聚合物,分子间的作用力减弱,其强度和模量降低。由于生成的梯形聚合物分子之间的滑移能力和分子的舒展能力减弱,因此断裂伸长率亦减小。吕春祥等[21]研究发现,随着氧化程度的加深,预氧丝模量、断裂伸长率和强度降低,预氧丝模量和断裂伸长率随氧化温度的变化曲线如图2.5所示。

图2.5 预氧丝弹性模量、断裂伸长率随氧化温度的变化曲线[21]
为提高纤维性能,在预氧化过程中应该注意以下问题:a.原丝要经过足够长时间的低温处理,因为原丝在240~260℃预氧化时,分子运动激烈,热稳定性差的分子链会裂解;b.预氧化应采用分段式梯度升温,对原丝适当施加拉伸,提高预氧丝强度,为炭化做好准备;c.采取多段牵伸方法,可以在防止过度牵伸的同时,更好地提高纤维强度;d.控制生产过程中油剂的含量,减少预氧化及低温过程中杂质的排出量。
③炭化过程对力学性能的影响。PAN基预氧化纤维在炭化过程中其结构与力学性能的变化大致可划分为三个阶段:300~500℃期间,纤维的抗拉强度与抗拉模量开始有所增加,纤维的结构变化以PAN体系未完全反应的部分进一步环化、脱水和脱氢等为主,材料的断裂形式由韧性断裂向脆性断裂过渡;500~900℃期间,纤维结构变化以分子链间的交联反应以及芳构化为主,力学性能上的表现则为交联网络的形成阻碍链段的运动,抗拉强度和抗拉模量均有明显提高,纤维断裂形式进一步向脆性断裂过渡;900~1250℃期间,力学性能急剧变化,抗拉强度和抗拉模量迅速增加,纤维结构以六元芳环碳层面规整化增长[22]。
在炭化过程中,已稳定化的PAN原丝主要发生脱水、脱氢和脱氮三种反应。对炭化反应而言,温度和升温速率是对炭化效果影响最重要的两个因素。Ko等[23]发现炭化温度决定了炭纤维的抗拉强度和抗拉模量,炭化温度为550℃时,炭纤维的抗拉强度较高;炭化温度为650℃和700℃时,炭纤维的抗拉模量较大。由于预炭化时有大量气体在氧化过程中逸出,如果升温速率过快,会在纤维中产生许多微孔,破坏炭纤维表面的规整结构,因此在现有的工艺中都采用低于5℃/min的升温速率。目前新的炭化工艺为炭化时采用磁场技术,Sung等[24]研究了氧化PAN于1172℃炭化时,沿纤维主轴平行方向施加强度为5T的高磁场后,所制得的炭纤维抗拉强度提高了14%,而且缩短了炭化时间,降低了炭化温度。
预氧丝在炭化过程中,炭化炉温度呈梯度分布,能够防止因氧化不充分形成皮芯结构,降低炭纤维强度。炭化后低的冷却速率可以避免纤维受到过大热冲击,不易造成纤维孔隙裂纹,从而提高纤维强度[25]。
④石墨化对力学性能的影响。PAN基纤维在炭化后已经具有小微晶结构和杂乱交错的无定形碳,但这些微晶大小和排列并不规整,而炭纤维中微晶的尺寸和规整度直接决定了其抗拉强度和抗拉模量这两个关键指标。石墨化通常在温度1500~3000℃的惰性气氛下进行,由于N2在温度高于2000℃时会变成活性分子且与碳原子反应生成氰基,一般选用更加稳定的惰性气体。当同样的炭化PAN基纤维进行石墨化时,相比其他石墨化条件,温度对纤维性能影响最大,随着热处理温度的提高,PAN基纤维的抗拉强度逐渐下降,而弹性模量不断上升。抗拉强度下降的原因是随着热处理温度的升高,炭纤维表面缺陷增多;而弹性模量升高则是由PAN基纤维石墨化程度提高所致[21]。当处理温度为1600~1900℃时,炭纤维的抗拉强度达到3.5GPa以上;若处理温度超过2500℃,炭纤维的抗拉模量超过300GPa。
以通用型PAN基炭纤维为原材料,通过1800~3000℃连续高温石墨化处理,制备不同性能的炭(石墨)纤维。发现随着热处理温度的提高,炭纤维中非碳元素(氮、氢)的含量逐渐减少,而碳元素质量分数从92.62%增加到99.99%,纤维抗拉强度呈下降趋势,弹性模量呈上升趋势。石晓斌[26]分析研究了PAN基1K炭纤维在不同热处理温度下力学性能的变化,通过研究发现炭纤维在1800~1900℃时,随热处理温度的上升,抗拉强度呈上升趋势,一直达到最高点,随着温度的继续上升,抗拉强度逐渐下降。经2500℃处理后炭纤维的抗拉强度保持率在50%~85%区间内,抗拉模量随温度上升而增加[27]。刘洪波[28]采用炭纤维石墨化炉,间歇式的升温降温工艺,并使纤维在炉内保留长的时间,可以使炭化进行得非常充分。对于现有的国产PAN基炭纤维,适当地提高热处理温度,增加炭化时间,可以提高其抗拉强度。
(2)炭纤维的表面结构性能
炭纤维及其复合材料具有优良的综合力学性能,但是多数炭纤维表面光滑、惰性大、表面能低[29],缺乏有活性的官能团,反应活性低[30],与树脂基体的黏结性差[31],高温抗氧化性较差[32],从而直接影响复合材料的力学性能,限制了炭纤维高性能的发挥。炭纤维增强树脂基复合材料作为结构材料,要求层间剪切强度在80MPa以上,最好在90MPa以上。未经表面处理的炭纤维,其树脂基复合材料的层间剪切强度一般在50~60MPa,还达不到使用要求的下限。为了改善炭纤维性能,实现炭纤维与基体的充分润湿,以及良好界面的黏结,人们做了大量研究。目前主要采用对炭纤维进行表面改性的方法来改善复合材料界面黏结性,从而提高炭纤维复合材料的性能。炭纤维表面处理方法很多,在这里主要介绍常用的氧化处理、辐射接枝改性和等离子体处理三种方法。
①氧化处理。影响炭纤维表面吸附活性的主要因素有纤维表面极性(即表面自由能的大小)和表面粗糙度(即表面积的大小)。对炭纤维进行表面氧化处理,一方面可以较大幅度地增加含氧基团数,提高纤维表面的极性成分;另一方面氧化反应过程中纤维表面被刻蚀,在刻蚀深度不是很大的情况下,既增加了纤维与树脂的接触面积,又可形成所谓的机械锁合,从而改善了纤维与树脂的黏结,提高了复合材料的力学性能。
电化学氧化一般是将炭纤维作为阳极置于电解质溶液中,通过改变反应温度、电解质浓度、处理时间和电流密度等条件对炭纤维表面氧化状况进行控制。电化学氧化能在纤维表面引入各种功能基团,从而改善炭纤维的浸润性和纤维与基体的界面结合情况。
在电化学表面改性炭纤维的过程中,存在着氧化反应和氨化反应,其中氧化反应是氨化反应发生的前提条件。—OH、—O—CO、和—NH2(—NH—)是炭纤维表面与树脂黏结的主要官能团,层间剪切强度对—NH2(—NH—)更加敏感。当电解质中存在二价阴离子时,会减小炭纤维抗拉强度的损失,甚至使抗拉强度得到提高[33]。
采用电化学氧化法对PAN基炭纤维进行表面改性,发现炭纤维经电化学氧化后,表面的粗糙度提高1.1倍。电化学氧化法的刻蚀作用致使炭纤维抗拉强度降低了8.1%,但同时也改善了炭纤维表面的物理性质和化学性质,提高了炭纤维与树脂间的黏结性,使复合材料的层间剪切强度提高了26%[34]。曹海琳等[35,36]分别以H3PO4溶液和HNO3/H2SO4混合溶液为电解液对炭纤维进行电化学改性处理,处理后纤维表面氧元素的含量增加,其与胶黏剂的界面黏结力明显增强,并提高了复合材料的整体性能,炭纤维织物复合材料的承载能力提高了60%、磨损率降低了65.9%。
电化学氧化法不仅使炭纤维表面化学键发生改变,而且使炭纤维表面形态发生变化,如果对不同种类炭纤维在1%(质量分数)的硝酸钾溶液中进行电化学氧化,使纤维表面产生大量的微孔(直径<1nm)[37]。随氧化程度的进行,微孔向纵深发展,并在其上生成更多的极性基团,极性基团和微孔的增加使炭纤维的表面活性得到提高。
气相氧化法是将炭纤维在氧化性气氛中进行氧化处理,气相氧化使用的氧化剂有空气、氧气和臭氧等含氧气体。利用具有氧化性的气体对炭纤维氧化处理后,炭纤维表面积增大,官能基团增多,可以提高复合材料的界面黏结强度和材料的力学性能。
贺福等[38]用气相氧化法对炭纤维进行表面处理,处理后的炭纤维的抗拉强度、抗拉模量和断裂伸长率分别提高了11%~13%、5%~14%、4%~11%。炭纤维经气相氧化后表面含氧官能团的浓度由16%增加到45%,改善了纤维与树脂之间的黏结,炭纤维的层间剪切强度可由未处理的48.4MPa提高到84.4MPa。经气相氧化处理后,炭纤维表面的极性官能团量增加,能显著提高复合材料界面黏结强度。经臭氧氧化后,炭纤维表面含氧官能团的浓度显著增加,表面形态结构也引起很大变化,从而改善了对树脂的浸润性和反应性。王耀先等[39]用臭氧气体对炭纤维表面进行了连续氧化处理,发现炭纤维增强树脂基复合材料的界面层间剪切强度明显提高,最高可到提高到80%以上。W. H. Lee等[40]将炭纤维在氧气与氮气的混合气体中进行氧化处理,发现与未处理的纤维表面相比,氧化处理后的纤维表面有较多的羰基,其增强复合材料的剪切强度比未处理的提高了69%。
气相氧化法的优点是方便在线配套使用,一些生产企业将炭纤维从高温炭化炉中取出后,利用其自身所带的余热在空气中进行氧化。但是这种方法对炭纤维氧化均匀性的影响有待商榷,氧化条件的稍许改变就会造成氧化过度,从而对炭纤维的强度造成极大的损伤。
液相氧化法主要是将炭纤维浸入到某种氧化性溶液中,通过氧化剂来氧化刻蚀炭纤维表面。硝酸、酸性重铬酸钾、次氯酸钠、过氧化氢和过硫酸钾等都可以用于炭纤维的表面处理。硝酸是液相氧化中研究较多的一种氧化剂,用硝酸氧化炭纤维,可使其表面产生羧基、羟基和酸性基团,这些基团的量随氧化时间的延长和温度的升高而增多。液相氧化法较气相氧化法温和,不易使纤维产生过度的刻蚀和裂解。
炭纤维经硝酸表面处理后,比表面积和表面含氧官能团浓度都得到显著提高,氧化使表面含氧官能团的浓度增加,不饱和活性碳原子数目增加,使层间剪切强度提高。徐先锋[41]对去胶PAN炭纤维进行硝酸液相氧化处理,发现硝酸氧化处理可以改变炭纤维的表面结构,产生大量的表面微孔,使表面积和累积孔体积增加,从而提高其表面吸附能力。李铁虎[42]采用液相氧化法对PAN基炭纤维进行了表面处理,发现炭纤维表面氧化处理的时间以24h为最佳,处理液的浓度越大效果越显著。赵东宇等[43]的研究结果表明,对炭纤维表面用15%次氯酸钾(KClO3)与40%硫酸混合溶液进行处理,改性效果显著。袁华等[44]对KClO3/H2SO4液相改性处理的炭纤维表面结构进行了研究,发现经过液相氧化处理之后,纤维表面被刻蚀,在结晶缺陷部位产生凹槽,并且纤维表面的沟槽随处理时间的延长而逐渐加深。这表明经过表面改性后炭纤维表面波纹度增加,比表面积增加,可以提高纤维的吸附活性,有利于复合材料界面的机械锁合。改性处理能够增加表面活性官能团羰基(—CO)和酚羟基(—OH),降低炭纤维表面惰性,表面处理后纤维的力学性能均有所下降,液相氧化处理30min和120min后,抗拉强度分别降低约10%和50%。液相氧化改性处理前后炭纤维的表面形貌如图2.6所示。

图2.6 液相氧化改性处理前后炭纤维表面形貌[44]
阳极氧化法具有氧化缓和,反应均匀,易于控制,处理效果显著,经济、安全,无公害和可连续化大批量进行处理等特点,是适用于实际工业化生产的一种在线配套方法。
低模PAN基炭纤维在 NaOH溶液中阳极氧化表面处理时,同时存在均匀氧化刻蚀和不均匀氧化刻蚀。不均匀氧化刻蚀是炭纤维平均抗拉强度提高的主要原因,而均匀氧化刻蚀则主要引起抗拉强度的下降,两者共同作用可减小抗拉强度的分散性。刘洪波[45]以NaOH为电解质溶液,采用阳极氧化法对国产中强低模 PAN基炭纤维进行表面处理。研究发现,降低NaOH溶液的浓度能够提高阳极氧化电流密度,可以在中强低模PAN基炭纤维抗拉模量基本不变的情况下,提高其抗拉强度。
采用NH4HCO3为电解质溶液对炭纤维进行阳极氧化表面处理,有利于增加纤维表面粗糙度,提高炭纤维表面与树脂间的机械锁合作用。通过适当地控制参数,可有效地增加炭纤维表面羟基含量,提高活性碳原子与非活性碳原子数量比,改善炭纤维复合材料的使用性能,使复合材料层间剪切强度提高23%以上[46]。侯永平[47]以NH4HCO3为电解液,对PAN基高模炭纤维进行连续阳极氧化表面处理,发现纤维增强树脂基复合材料的层间剪切强度从28.4MPa增大到80MPa以上,提高了1.8倍以上。
②辐射接枝改性。对炭纤维进行电子束辐射接枝,在炭纤维表面上引入极性官能团,使炭纤维的表面浸润性和它与树脂基体间的黏结性得到改善,进而提高复合材料的界面性能[48]。炭纤维表面经电子束辐射之后,C—C键含量减少,活性官能团含量增加较为明显。在电子束辐照下炭纤维表面和接枝溶液中的单体被激活,产生活性自由基,单体分子自由基和纤维表面自由基发生反应,从而使单体接枝到炭纤维表面上。
臧真娟[49]采用电子静电加速器辐射接枝方法对PAN基炭纤维进行表面改性,从而提高了炭纤维与树脂的界面黏结性能。其对比改性前后炭纤维/环氧树脂复合材料层间剪切断口断裂形貌,发现电子束接枝处理的炭纤维增强复合材料断口较为平整,纤维从基体中拔脱现象明显减少,表明辐射接枝使纤维与树脂的界面结合力提高。
用γ 射线辐照接枝技术对炭纤维表面进行处理,纤维表面引入了含氧官能团,炭纤维表面极性提高。辐射能够刻蚀炭纤维表面,炭纤维表面的粗糙度增加,提高了炭纤维与树脂基体间的界面黏结力和炭纤维复合材料的层间剪切强度。纤维表面极性有利于纤维与树脂结合,表面粗糙利于树脂浸润,加强炭纤维和树脂间锚固效应[50,51]。
③等离子体处理法。等离子体法主要是通过等离子体撞击炭纤维表面,从而刻蚀炭纤维表层,使其表面的粗糙度增加,表面积也相应增加。采用低温等离子或微波等离子对炭纤维进行表面处理也是行之有效的方法,该方法的特点是气-固反应无污染,处理时间较短,氧等离子体的处理效果较好。但是,等离子体的产生需要一定的真空环境,因此设备复杂,给连续、稳定和长时间处理带来一定的困难。
炭纤维经等离子体聚合处理后,纤维表面的粗糙度以及表面条纹都增多,这有利于纤维与树脂间的机械锁合;同时纤维表面的活性成分增加,可以改变纤维表面的极性和结构,增强纤维与基体间的结合强度[52]。刘新宇等[53]用冷等离子体接枝处理的炭纤维来增强环氧树脂基复合材料,处理后炭纤维的表面活性提高,改善了纤维与树脂间的界面粘接性能,使复合材料的层间剪切强度提高了21%。张志谦[54]用冷等离子体对炭纤维表面进行连续接枝处理。研究结果表明合适的接枝单体及接枝条件可使炭纤维增强树脂基复合材料的抗拉强度及抗拉模量分别提高39.9%和11.3%。贾玲等[55]将炭纤维预浸芳基乙炔后进行空气等离子处理,使芳基乙炔接枝在炭纤维上,冷等离子体接枝处理提高了炭纤维表面活性,从而改善了炭纤维织物/环氧复合材料的界面粘接性能,层间剪切强度最大提高了12.4%,而炭布接枝了丙烯酸单体以后,层间剪切强度最大提高了51.3%。
2.2.2.3 PAN基炭纤维的制备工艺
PAN基炭纤维的制备过程是一个非常复杂的系统过程,工艺流程如下:
PAN原丝制备→预氧化→炭化→表面处理→卷曲→炭纤维
为了制得具有较高模量的炭纤维,还需要对炭纤维进行高温热处理。炭纤维的制备过程如图2.7[56]所示。

图2.7 PAN基炭纤维生产制备过程示意图
(1)原丝制备
PAN原丝的制备是将丙烯腈单体聚合成纺丝原液,然后纺丝成型。聚合过程中要使用能够溶解聚合物的溶剂,一般常用的溶剂都具有强极性分子结构,极性基团吸引氰基,从而破坏氰基的双偶极键,生成初生自由基。溶液聚合中添加引发剂促进聚合反应,常用的引发剂有过氧化物、过硫酸盐、偶氮类化合物(偶氮二异丁腈)以及氧化还原体系。引发剂提供自由基,自由基再引发丙烯腈分子形成更大的自由基。下式中,R·代表自由基。

PAN的纺丝方法有很多种,按聚合和纺丝的连续性分为一步法与两步法;按纺丝工艺可分为湿法、干法、熔融法和干湿法。纺丝溶剂有NaSCN、ZnCl2、HNO3、二甲基甲酰胺(DMF)、二甲基乙酰胺(DMAc)、二甲基亚砜(DMSO)等,目前以DMSO溶剂生产的原丝产量最多,且技术成熟,性能稳定,经炭化处理后品质最好。
原丝生产在整个炭纤维生产过程中至关重要,因为原丝的质量决定炭纤维的性能,而且原丝生产的投资约占整个炭纤维生产投资的80%。以DMSO为溶剂的湿法纺丝过程主要包括聚合、凝固浴牵伸、水洗、上油、干燥致密化、蒸汽牵伸、热定型以及收丝等步骤。首先,丙烯腈和其共聚单体在反应釜中反应生成聚合物溶液,聚合物溶液按一定流量经过喷丝板进入凝固浴,形成初生纤维,再经过几段不同温度以及不同浓度的凝固浴,通过双扩散作用,使初生纤维的固含量得到提高;经过凝固浴后,通常会采用沸水牵伸的方法提高凝固丝的取向度和强度,即在一定的张力作用下经过100℃的沸水;为了去除残留在 PAN 纤维中的溶剂,需要经过水洗步骤,且温度控制在70~80℃;经水洗的PAN初始纤维在后续的纺丝过程中,可能会出现并丝现象,因此有必要对纤维进行上油处理,以降低纤维的毛丝率;上油后的 PAN 初生纤维中含有一定的水分,经过干燥致密化可以除去其中的水分,并且可以使PAN初生纤维中的空洞逐渐融合,以达到致密化的目的;为了进一步提高纤维的取向度,减少毛丝和断丝现象,通常将纤维在蒸汽中进行牵伸,并提高牵伸倍数,牵伸温度一般在150℃左右;最后经过一定温度下的热定型,去除纤维中的内应力;以上一系列工艺完成后,利用收丝机收取PAN原丝。
①原液聚合。纺丝原液的合成遵从自由基聚合机理,自由基聚合主要有溶液聚合、乳液聚合、悬浮聚合和本体聚合。一般采用溶液聚合和悬浮聚合两种聚合工艺,其中以溶液聚合为主。一般选用的共聚单体能够加速氰基环化,促进预氧化的丙烯酸类和丙烯类的衍生物,如衣康酸、丙烯酸、甲基丙烯酸和丙烯酸甲酯等[57]的生成。除此之外,目前许多研究者开发出新的共聚单体和聚合方法。崔传生[58]开发了衣康酸铵[(NH4)IA-AIA]作为共聚单体,并使用多种方法合成了丙烯腈/衣康酸共聚物,研究发现丙烯腈/衣康酸共聚物作为炭纤维前驱体具有许多优异的性能,制得的原丝皮芯结构不明显,残留溶剂较少。H.Chen等[59,60]研究了丙烯腈与n-乙烯基吡咯烷酮(NVP)在H2O/DMSO混合溶剂的沉淀聚合方法。
合成PAN树脂所使用的聚合溶剂DMSO和聚合单体丙烯腈均含有大量的金属离子杂质,含有的主要金属离子有Mg、Ca、K和Fe 等,这些金属杂质对提高炭纤维的性能有很大影响。日本三菱人造丝公司采用0.45μm级过滤器对纺丝原液进行过滤,并采用磺酸基团的离子交换树脂除去纺丝原液中的金属离子[61]。杨煜[62]使用D315、D311、D301和D335四种商品化的大孔弱碱型丙烯酸系阴离子交换树脂,来吸附丙烯腈和DMSO中的Fe3+,实验结果证明D315大孔弱碱型丙烯酸系阴离子交换树脂的吸附效果是最佳的,能够在室温下达到高效率、低成本地纯化丙烯腈和DMSO,除去其中的 Fe3+,产品纯化的收率达97.5%。
②纺丝。作为原丝成型的重要步骤,PAN原丝的纺丝技术是炭纤维研制开发的关键技术,日本在PAN原丝领域呈一支独秀状态。日本东丽公司采用以DMSO为溶剂的间歇溶液聚合技术开发出了纺PAN原丝的产业化技术,先后开发出T300、T800、T1000、M40、M50和M60等系列牌号的高模炭纤维。日本东邦公司采用氯化锌水溶液为溶剂的溶液聚合技术开发出了高性能炭纤维用原丝的产业化技术,该公司生产的PAN原丝经炭化后所得炭纤维的性能相当于T800产品的水平。日本三菱人造丝公司开发出了两步法PAN原丝的生产技术。该公司生产的原丝经炭化后,炭纤维的性能相当于T800产品的水平[63]。
DMSO法制造PAN基原丝与NaSCN、ZnCl2、HNO3和DMF等方法相比,DMSO法生产工艺简单,聚合物浓度较高,纺出的纤维较致密,同时可共溶不同的聚合物成纤,因此共聚或共混成分的选择自由度大,有利于生产不同系列的高性能炭纤维[64]。按照DMSO一步法湿法纺丝工艺生产的高强炭纤维原丝性能良好,其中1K原丝经多次炭化实验,所得炭纤维经测试其力学性能接近日本的T300,达到了高强炭纤维的要求[65]。
制取高强度高模量炭纤维,DMSO法原丝优于NaSCN法原丝和HNO3法原丝[66]。从DMSO法和HNO3法两种原丝制备的炭纤维性能看,DMSO法产品获得的抗拉强度等主要指标更好。两种方法所制得炭纤维的性能比较如表2.2所示。
表2.2 DMSO和HNO3两种原丝制备的炭纤维性能比较[67]

目前生产PAN基炭纤维原丝常用的方法有干法、湿法和干喷湿纺法等。其中,干法在纤维的成型过程中会在纤维内残留不易去除的溶剂,造成纤维在预氧化阶段因溶剂挥发而留下孔洞,影响炭纤维的强度,此法已处于淘汰阶段;湿法成型的纤维纤度变化小,纤维上残留的溶剂少,容易控制原丝质量,是PAN原丝生产中较为广泛应用的纺丝工艺;与湿法纺丝相比,干喷湿纺法可进行高倍喷丝头拉伸,因此纺丝速度快。为了提高原丝的取向度、减小表面缺陷和致密度高等性能,目前最先进的纺丝工艺为干喷湿纺,与一般常用的纺丝工艺如湿法、干法和熔融法等相比,所制得原丝的结构均匀致密,不易产生大的孔洞,原丝的截面也容易成圆形,其力学性能亦可以获得提高。B.J.Qian等[68]研究过PAN干喷湿纺法的工艺过程,认为干喷湿纺法可在空气层中形成一层致密的薄层,可以阻止大孔洞的形成,从而优于湿法纺丝。用干喷湿纺法得到的纤维,结构比较均匀,皮芯层差异小,强度和弹性均有提高,截面结构近似圆形,纤维表面光滑,纤维内部缺陷少[69]。用此法得到的PAN纤维适合作为炭纤维的原丝。毛萍君[70]对PAN干喷湿纺法的纤维成型工艺做了研究,发现干喷湿纺法工艺中,所用凝固浴温度较低,浓度较高,则纺制得到的纤维综合性能指标较好。干喷湿纺法时可进行高倍率的喷头拉伸,这对降低纤维的纤度和提高强度非常有效。徐粱华[71,72]对湿法纺丝与干湿法做了比较,研究结果表明,湿法纺丝所得的纤维存在各种表面缺陷,其中,表面沟槽是纺丝工艺本身所致,无法消除;干湿纺纤维的表面则光洁无沟槽。干喷湿纺法中,纺丝液中PAN质量分数的提高有利于凝固牵伸倍数和总牵伸倍数增大。
(2)预氧化
PAN原丝的预氧化也称为热稳定化,是炭纤维制备过程中耗时最长的工艺,一般为60~120min,预氧化过程中纤维结构的转变很大程度上决定着最终炭纤维的结构和性能。预氧化的方法一般有三种:等温预氧化、连续升温预氧化和梯度升温预氧化[73]。前两种是早期炭纤维连续生产所采用的方法,现在主要用于实验室研究;后一种是目前工业化生产所普遍采用的方法。
预氧化处理的目的是使PAN的线型分子链转化为耐热的梯形结构,以便保证其在高温下不熔化不燃烧,炭化时保持纤维形态。预氧化温度、升温速率、预氧化时间、牵伸和氧化气氛等是影响预氧化过程的主要工艺参数。预氧化温度的控制对预氧化过程来说是非常关键的,温度区间一般为200~300℃[74,75]。温度过低,预氧化反应缓慢或不充分,耗时太长,生产效率大大降低;温度过高,则易导致过度氧化、熔丝甚至燃丝,总之温度过高或过低都不利于获得高质量的炭纤维。R.B.Mathur等[76]研究发现PAN原丝在空气介质中得到的差热分析法(DTA)曲线出现双峰,第一个突出的放热峰峰值温度在270℃,在350℃还有一个弱的放热峰,所以预氧化的上限温度应达到350~400℃,以得到良好的稳定结构,提高炭纤维的力学性能。
在预氧化过程中,PAN预氧化纤维主要发生线型分子链的氧化、环化反应,最终形成耐热、不溶且不熔的稳定结构;纤维在氧化环化的同时,不断地放出小分子物质,且随着预氧化程度的加深,释放小分子的量逐渐减少,释放温度向高温方向移动。在预氧化后期,相同的预氧化温度下,纤度较小的 PAN纤维发生了更多的氧化反应,具有较高的相对环化率和略高的密度;纤度较小的预氧化纤维具有较小的芯,相对容易获得均质结构[77]。
Z.Bashir[78]回顾了PAN预氧化机理的研究进展,归纳为4种类型:①氰基合形分子内含CN环化梯形聚合物结构;②分子间氰基反应,产生交联链;③偶氮次甲基交联反应;④脱氢反应形成C
C共轭结构。K.Jain Mukesh[79]认为PAN原丝的预氧化最少应分为三个阶段:①形态结构开始快速重排;②主要发生在无序区的反应;③反应增长到有序区。为了发挥PAN原丝制备高性能炭纤维的最大潜力,就必须严格控制预氧化条件。
PAN基炭纤维预氧化工艺条件对其结构和性能有一定影响。随着预氧化温度的升高,预氧丝的密度、氧质量分数和芳构化指数均增大;随着预氧化时间的增长,密度和氧质量分数也增加[80]。Jin-sky Tsai[81]对比研究了间歇与连续不同的预氧化工艺条件对预氧丝及最终炭纤维的性能的影响。升温速率从10℃/min提高到20℃/min时,预氧丝及炭纤维的强度都降低;在210℃连续预氧化,纤维的走丝速率从5m/min提高到7m/min时,预氧丝及炭纤维的强度和模量都有明显下降。王文胜等[82]研究了预氧化时间的控制对炭纤维性能的作用。随着预氧化时间的延长,炭纤维的抗拉强度升高到最大值,超过10h后,炭纤维强度有明显下降。同时还发现,慢的加热速率易于制得高强度炭纤维。
为了制备高性能炭纤维,需要高性能原丝,原丝通过预氧化工艺的合理控制,得到所需结构和性能的预氧丝,预氧化与炭纤维性能间的关系如表2.3所示。
表2.3 预氧化与炭纤维性能间的关系[83]

在预氧化过程中,常用的低温加热方式为电热丝加热,常用的高温加热方式为硅钼棒或石墨棒加热。它们的缺点是难以形成均匀温区,同时热量需要经过介质传导才能到达原丝表面,这样就造成了炉温的调节不能随机快速反应,热效率低、设备造价高等问题。朱波等[84]采用气固流态化技术研制出了一种新型预氧化炉,发现使用这种预氧化炉升温速度快,控温精度高,保温阶段精度为±2℃;所制备的预氧丝表面缺陷少,没有明显损伤,所需预氧化时间仅为45min,纤维的氧含量达到10.05%,体密度达到1.38g/cm3。该设备在保证预氧化质量的前提下,缩短了预氧化时间。我国也拥有PAN纤维预氧化及炭化时用高频负压等离子加热装置的专利[85]和微波加热反应装置的专利[86]。虽然这些新工艺实现了缩短反应时间、改变纤维结构的目的,但是在提高所制备的炭纤维的力学性能方面还需继续研究。
日本东丽公司的千吨级预氧化装置为外热侧吹式预氧化炉,由于外热式预氧化炉靠加热元件直接加热为主,热空气循环加热为辅,以及炉外热空气循环鼓入炉膛,不仅炉内温度均匀性提高,同时循环空气还有利于将PAN纤维反应热迅速带走,提高预氧化纤维的均匀性。另外热式氧化炉可利用废气进行热交换,利于节能[87]。美国DESPAT公司的中央到两端吹风(CTE)预氧化炉,平均气流速度可达3.5m/s,最高温度300℃,从室温加热到260℃约需2h;该设备能够减少热损失,有效去除排放物。CTE技术比侧吹风技术的预氧化效率高出25%,同时预氧化均匀度和最终制得炭纤维的品质也有所提高[88]。
(3)炭化
PAN纤维预氧化后的炭化过程经低温炭化和高温炭化处理后,转化为具有乱层石墨结构的炭纤维,低温炭化温度一般为300~800℃,高温炭化温度一般为1000~1600℃。低温炭化过程中,纤维发生裂解反应,释放出大量小分子气体,如H2O、CO、CO2、NH3和HCN等,非碳元素逐渐被脱除,此过程中纤维发生环化、交联、裂解和缩合等一系列复杂的反应,纤维中成分随之发生变化,最终生成碳元素相对含量90%以上的炭纤维[89,90]。
在炭化和石墨化时多用高纯氩气,这些保护性气体使炉内保持在正常压力,去除副反应产物,促进反应的进行。在炭化时排出瞬时热解产物是炭化的关键技术之一。在炭化时,如果纤维内部的热分解产物不能瞬时排出,将对纤维造成污染,使纤维之间粘连而造成炭纤维的表面缺陷或者断丝。在炭化阶段PAN原丝的缺陷影响很大,原丝的外部缺陷在低温炭化时就表现出来,而原丝的内部缺陷在高温炭化时表现比较明显,这些缺陷包括物理缺陷(如空洞和沟槽等)和化学结构缺陷(如分子结构的变异和酮化),缺陷越多,炭化时越容易断丝。
在炭化过程中预氧丝的应力变化趋势大体上可分为4个区域:应力快速增长的370℃以下温度区、应力明显下降的370~500℃温度区、应力再次迅速增高的500~900℃温度区以及应力保持稳定的900℃以上温度区。这种应力的变化是由纤维的收缩引起的[91],因此可以通过控制炭化过程中纤维热应力的变化来控制连续制备过程中纤维的结构。
炭化工艺条件对最终炭纤维的强度有直接影响。从工艺参数角度看,炭化炉温的梯度分布和纤维的冷却速度是主要因素。在1400~1600℃以下,随着炭化温度的升高,炭纤维的抗拉强度逐渐增大,达到最高值后开始下降。除炭化最高温度外,低温炭化温度也会影响炭纤维强度。王成国[92]进行了两步梯度温度炭化实验,发现低于450℃的炭化处理使纤维发生交联和芳构化等放热反应,提高了纤维结构的稳定性;450~750℃下的炭化处理则使纤维的线型链段发生大规模的无规裂解,裂解反应迅速且有大量自由基产生。裂解后的纤维主要由芳构结构组成,随温度的升高,碳基面缓慢形成;1000℃以上温度的炭化处理使非碳元素大量脱除,纤维逐渐转变为乱层石墨结构的炭质材料。当温度达到1400℃,纤维具有较高的结晶度和较大的晶粒尺寸,但是在乱层石墨层面之间或边缘仍然存在大量的sp3原子结构,晶区结构很不完善[93]。
PAN预氧化纤维在炭化过程中,纤维结构在600℃左右有一明显转变。600℃前主要是预氧化对未反应的PAN分子进一步环化,分子链间交联及主链、侧链与末端基分解,而600℃以上则是分子间脱N2。潘鼎[94]采用了以600℃为分界点的两段炭化工艺,其研究发现低温炭化段的最佳上限温度为600℃,最佳处理时间为2min。在低温段施加合适的张力,使纤维获得良好的取向度,可使纤维的强度提高10%左右。
随着超导磁体技术的发展,人们研究发现高强磁场可以影响炭纤维的炭化过程,进而提高炭纤维的抗拉强度。高强磁场对纤维炭化过程的影响机理主要如下:根据自由基理论,磁场可促进炭化过程中分子间的交联反应,有利于提高炭纤维的抗拉强度;同时磁场还可以促进结晶取向度的提高,使平行于轴向的共价键数目增多[95],磁场还可以使纤维表面缺陷减少。
(4)石墨化
影响炭纤维石墨化的关键因素是石墨化设备和高温热处理技术,为此人们利用不同的热工业源研制了多种石墨化炉进行炭纤维的石墨化[96]。
炭纤维石墨化的主要设备包括电阻炉、感应炉和太阳炉等。目前,在国内外工业上普遍采用的炭纤维石墨化设备多为高温电阻炉。在工业上为了提高设备的使用寿命,常常在石墨发热体上涂以抗氧化保护层材料进行保护或将其密封起来;同时为了提高产量,降低成本,常采用往复式走丝;另外,在一定压力下进行石墨化,也可抑制石墨发热体的升华而延长其使用寿命。
利用等离子体技术进行炭纤维石墨化是一个新的研究方向,等离子体是大量带电粒子组成的非凝聚系统,是气体在加热或强电磁场作用下电离而产生的,主要由电子、正负离子、原子、分子、活性自由基以及射线等组成。王浩静等[97]发明了一项利用直流电弧等离子体进行炭纤维石墨化装置,该装置利用惰性气体氩气作为工作介质,并在0.3~0.5MPa的压力下向两个电极之间施加80A的直流电,通过放电产生连续高温电弧等离子体,将炭纤维通过等离子体2500~3500℃的局部高温区而进行石墨化。美国的Felix等发明了一项利用微波等离子技术和电磁辐射进行炭纤维炭化和石墨化的技术,该方法利用频率为2.45GHz、功率为6kW的微波发生器,由微波放电产生等离子体,其等离子体为非平衡态,气态原子处于室温,而电子具有非常高的温度,并具有足够的能量而使纤维内部的化学键断裂[98]。
石墨化能够提高炭纤维的抗拉强度和抗拉模量,但是此方法存在处理成本高的问题,用γ射线辐照可以改变这种状况。因为炭纤维存在皮芯结构,皮层微晶较大,排列比较整齐有序,由皮层到芯部,微晶减小且排列逐渐紊乱,结构不均匀性越来越显著。而γ射线粒子的能量高、穿透力强,能够在较厚材料内部引发活性点,与材料周围的介质发生反应,γ射线粒子所提供的能量可以使芯部石墨微晶重新排列和提高沿纤维轴向的取向,从而提高炭纤维本体的强度和模量,因此国内科研工作者提出了采用γ射线辐照提高炭纤维强度和模量的办法[99]。其方法一是将炭纤维直接放入辐照源室进行γ射线辐照,辐照剂量率为0.6~6kGy/h,辐照剂量为30~600kGy。另一个方案是先将炭纤维置于密闭容器内,抽真空使密闭容器内压力低于0.1MPa,再充入惰性气体使密闭容器内的压力达到0.1MPa,然后将装有炭纤维的装置放入辐照源室进行γ射线辐照。采用这些方法处理后,炭纤维的抗拉强度提高了9.4%,抗拉模量提高了12%。
目前,国内外科研工作者对预氧丝的炭化石墨化的工艺、结构和性能相关性等做了大量研究,取得了很大进展,我国在这方面存在一些问题:
①目前针对国产预氧丝炭化过程的基础性研究较少,因此亟待进行针对国产预氧丝的系统炭化研究;
②我国大部分研究将炭化过程与预氧化过程相分离,炭化工艺与预氧化过程相匹配的问题需要进一步研究;
③国产纤维的炭化工艺优化、工艺对纤维结构以及性能的影响问题需深入研究。
2.2.2.4 PAN基炭纤维发展现状
PAN炭纤维起源于20世纪50年代末,1961年日本大阪工业研究所进藤昭男博士用美国杜邦公司的奥伦为原料成功研究开发出PAN基炭纤维。随后,为了提高炭纤维的性能,在丙烯腈的共聚单体上进行了大量的试验工作,研制出了专用于炭纤维制造的前驱体,即PAN原丝。1964年英国皇家航空研究所的Watt等人,在预氧化过程中对纤维施加张力,为制取高强度高模量的炭纤维开辟了新的途径。1969年日本东丽公司成功研制出特殊的PAN纤维,并结合美国Union Carbide公司的炭化技术,生产出高强度、高模量的炭纤维。除了日本东丽公司外,东邦人造丝和三菱人造丝等公司也发展自己的技术,进行了炭纤维的工业化生产。
日本发展PAN基炭纤维的独特优势在于这些炭纤维公司皆起源于腈纶生产厂家,拥有较强的丙烯腈共聚、成纤技术与基础研究实力,这是决定目前日本原丝均领先于世界其他国家的根本原因。与日本的炭纤维公司相比,美国的炭纤维公司都是非腈纶生产厂家,原丝皆依赖于日本。由于至今美国的原丝仍受制于日本,所以其炭纤维产业始终屈居二流。我国台湾的台塑公司是一家石化等综合性公司,过去既未生产过腈纶,也从未生产过炭纤维,仅靠自己雄厚的经济实力和该地区炭纤维体育休闲用品市场的牵引,与逢甲大学等单位协作来发展自己的原丝及炭纤维技术,在短短的几年时间内,一跃而成为世界上举足轻重的炭纤维生产厂家,占据了我国的一部分市场。其主要原因是该公司选用了世界上最先进的生产装置生产原丝和炭纤维。例如,其纺丝原液的脱单体装置是购买意大利著名厂家的设备,预氧化和炭化设备是美国Harper的产品,因此保持了总体设备的先进性和高精度,保证了自己的竞争力。
目前世界炭纤维格局呈现发达国家产业成熟,行业集中度高的局面。世界炭纤维的生产主要集中在日本、英国、美国等少数发达国家和我国台湾地区,其中日本三家炭纤维企业的产量就占据了78%左右的市场份额。PAN基炭纤维自20 世纪80年代中期相继推出一系列新品种,高性能及超高性能的炭纤维相继出现。经过多年的发展,炭纤维的产量出现很大飞跃,质量和性能逐渐提高,种类也日益丰富。世界PAN基炭纤维已进入发展旺盛的成熟期,主要表现为:①PAN基炭纤维产量急剧提高,生产规模大型化,产品价格下降;②PAN基炭纤维生产工艺、设备和技术不断改进,炭纤维性能不断提高,例如日本东丽公司已开发出高强型T1000系列炭纤维,其抗拉模量295GPa,抗拉强度7105MPa,而其高强高模MSJ型抗拉模量达640GPa,抗拉强度为3162MPa;③应用范围从少数高科技领域、军事部门扩展到工业和民用的各个部门。炭纤维现在已分化为以美国为代表的大丝束炭纤维和以日本为代表的小丝束炭纤维两大类。日本和美国所产的炭纤维约占全球总供应量的80%[100]。日本以生产PAN基小丝束(≤24K)炭纤维为主,2010年产能之和占小丝束总产能的69.3%。其中日本Toray为世界最大的炭纤维生产企业,其产能为1.79万吨/年。美国的Zoltek公司以生产PAN基大丝束(>24K)炭纤维为主,2010年其产能占大丝束总产能的54.1%[101]。
炭纤维生产公司主要有三大系列的炭纤维,即高强T系列、高模M系列以及兼备高强高模的MJ系列,其中高强型包括T300、T600、T700、T800和T1000,高模型炭纤维主要有M30、M40和M46,市场流通的高模炭纤维主要是M40。高强高模型的炭纤维主要有M46J、M50J、M55J、M60J和M65J等,其中东丽公司的炭纤维种类和性能如表2.4所示。
表2.4 东丽公司的炭纤维种类与性能 [102]

在20世纪80年代初,T300被国际公认为通用级标准炭纤维。近年来,在高强T系列产品中,东丽公司逐步用性能较好的T700取代T300,T700将成为未来的新一代通用级炭纤维。日本东丽公司以生产高性能小丝束炭纤维闻名于世,主要生产1K、3K、6K和12K的小丝束炭纤维。但近年来,由于大丝束炭纤维在价格上的优势,已经转向发展“准”大丝束炭纤维,即发展比大丝束炭纤维丝束小,但比一般小丝束炭纤维丝束大的18K和24K的“准”大丝束炭纤维。从表 2.4中可以清楚地看到,日本东丽公司最新发展的炭纤维品种,像T600S、T700S、T700G、M30S和 M30G等,都属于这个范畴。在美国第四十五届材料与加工工程促进学会年会与展览上提供的炭纤维产品目录中,M系炭纤维中M30和M50等高模炭纤维已从目录中消失,这种类别的炭纤维已被性能更好的MJ系列产品所取代。
日本GRAFIL公司(日本三菱人造丝公司子公司)生产的炭纤维,全部是PAN基炭纤维。PAN基炭纤维包括各种档次,从标准模量、中等模量到高模量,模量覆盖从235~450GPa。每束炭纤维有不同的K数,包括1K、3K、6K、12K和48K,从小丝束到大丝束。炭纤维有不同的上浆量,最少的为0.4%,最多的达1.4%。炭纤维又分为一般束宽和宽束(WD)两种类型,以满足制造预浸料、编织、缠绕和拉挤不同工艺的需求。
GRAFIL公司的炭纤维产品分成两大类:GRAFIL和 PYROFIL。GRAFIL属标准模量炭纤维,抗拉模量为234GPa,最初生产的 GRAFIL 33-500炭纤维已被性能更好的GRAFIL 34-700(抗拉强度4500MPa、抗拉模量234GPa)所取代。 GRAFIL 34-700是一种高应变炭纤维,延伸率达1.9%。每束炭纤维数为12K或24K,纤维表面经过处理和上浆,与高分子材料有很好的黏结性,可用于制造预浸料、编织、缠绕和拉挤。GRAFIL公司炭纤维及其性能如表2.5所示。
表2.5 GRAFIL公司炭纤维及其性能[103]

PYROFIL炭纤维是由新一代高级 PAN原丝制成,可以与各种不同体系高分子材料基体复合制得力学性能好、适应性强的复合材料,可用一般的预浸料设备、缠绕机、编织机和拉挤设备来制备相应的预浸料和复合材料构件。PYROFIL炭纤维包括标准模量炭纤维,TR40、TR30S、TRSOS和TRSOH,模量在235~255GPa,其中TR40为1K炭纤维,TR30S为3K、6K炭纤维,TRSOS和TRSOH为 6K、12K炭纤维;中模量炭纤维 MR40、MRS0和 MS40,模量在295~345GPa;高模量炭纤维HR40和HS40,模量在390~450GPa,抗拉强度在4410~5400MPa。PYROFIL炭纤维及其性能如表2.6所示。
表2.6 PYROFIL炭纤维及其性能[103]

东邦公司自1975 年开始进行PAN基炭纤维开发生产,其生产的炭纤维按照抗拉模量分类,主要有HT和UT通用级别(抗拉模量230~250GPa),IM中弹性模量级别(抗拉模量280~310GPa),HM、UM 高弹性模量级别(抗拉模量340GPa以上)。东邦公司生产的放热PAN基炭纤维主要是TENAX系列,该系列炭纤维的种类及其基本性能如表2.7所示。另外Semipreg是东邦TENAX炭纤维与丰田汽车共同开发的大型成型用新型炭材料。
表2.7 日本东邦公司TOHO/TENAX炭纤维种类及基本性能[104]

美国HEXEL(赫克塞尔)公司是美国最大的生产和研发炭纤维的公司,其生产的炭纤维共有三个系列,九个牌号,它们分别是:AS系列的AS4C、AS4和AS4D;IM系列的IM4、IM6、IM7、IM8和 IM9以及UHM系列的高模UHM石墨纤维。AS系列炭纤维的抗拉强度在3860~4207MPa,比日本东丽公司的T300的抗拉强度高,与T300J或T600S相近。IM系列炭纤维的抗拉强度在4138~6343MPa,与东丽公司的T600S、T700S、T800H和T1000G相当。该公司生产炭纤维的牌号与性能如表2.8所示。
表2.8 美国HEXEL公司炭纤维的牌号与性能[105]

美国Zoltek(卓尔泰克)公司是世界上最有名的大丝束炭纤维公司,也是世界上首先研制、开发并生产廉价且高性能大丝束炭纤维的公司。美国卓尔泰克公司生产的大丝束连续炭纤维最有代表性的是PANEX 33,PANEX 33虽然是大丝束炭纤维,但性能达到甚至超过宇航级小丝束炭纤维,抗拉强度3800MPa,超过日本东丽公司抗拉强度为3530MPa的T300炭纤维,其抗拉模量为228GPa,与日本东丽公司抗拉模量230GPa的T300相当。PANEX 33连续炭纤维采用各种上浆配方,与不同树脂体系都有很好的相容性,可用于制备多种先进复合材料。美国卓尔泰克公司还生产高纯研磨炭纤维PANEX 33ME,高纯研磨炭纤维的抗拉强度3600MPa、抗拉模量207GPa、体密度0.45g/cm3、电阻率 0.0014Ω·m、碳含量99%、纤维长度150μm[106]。
在亚洲地区,除日本外,我国台湾是炭纤维及其复合材料的重要生产和使用地区。20世纪80年代,台湾塑胶公司能够向民用和航天工业提供炭纤维粗纱和炭纤维相关产品。该公司的炭纤维商品名称为台丽TAIRYFIL,该公司的炭纤维种类以及性能如表2.9所示。
表2.9 我国台湾台塑台丽TAIRYFIL炭纤维种类及基本性能[104]

我国大陆地区对炭纤维的研究起步并不晚,也取得了一些进展,但是发展较为缓慢。我国大陆的PAN基炭纤维大致可分为三个阶段,如表2.10所示。目前大陆生产炭纤维的企业有20余家[107],各厂家生产能力如表2.11所示。
表2.10 我国大陆PAN基炭纤维发展的三个标志性阶段

表2.11 我国大陆炭纤维生产能力[108] 103t


我国大陆炭纤维至今发展较为缓慢,关键问题是PAN原丝质量不过关;另外受产业化水平和制备技术的限制,国产炭纤维制备成本偏高,从而影响了其应用的拓展;我国大陆制备炭纤维的制备技术相对滞后,造成炭纤维制备技术不完整,成套装备的设计和制造基础薄弱,关键技术有待突破。
经过T300、T700级炭纤维的技术研发与工程化研究和863、973等项目的实施,现阶段我国在一定程度上突破了高性能纤维的制备瓶颈,对应于炭纤维工业化生产所需的大量大型设备的设计、制造、安装和维护等也积累了丰富的经验,为高性能炭纤维的工程化建设及研制提供了必要的技术基础。下一阶段我国主要目标是优化炭纤维的生产工艺,控制生产成本,同时要提高T300、T700和M40级炭纤维的稳定性和使用可靠性。通过各界努力,我国的炭纤维以及复合材料技术与应用必将具有更广阔的发展前景。
2.2.3 沥青基炭纤维
2.2.3.1 概述
沥青基炭纤维的研究开发始于20世纪50年代末期,60年代初由日本群马大学研制成功,60年代末在日本吴羽化学公司实现工业化生产。沥青基炭纤维因其具有高强度、高模量、耐高温、耐腐蚀、抗疲劳、抗蠕变、导电与导热等优良性能,是航空航天工业中不可缺少的工程材料。
沥青基炭纤维的抗压强度比较低,其加工性能亦不如PAN基炭纤维。然而高性能沥青基炭纤维是由中间相沥青转化而来,液晶中固有的分子定向排列被保留下来,可在较低热处理温度下得到模量较高的产品,它还具有优良的传热性能、导电性能和极低的热膨胀系数,因此可在要求这些特殊性能的军工及航天领域发挥其独特作用。
现在世界上生产沥青基炭纤维的主要公司有日本吴羽化学公司、日本三菱人造丝公司和美国Amoco公司。表2.12为吴羽化学公司和Amoco公司生产的沥青基炭纤维的牌号和性能。其他国家的一些大型化学公司、石油公司和钢铁企业都致力于焦油和沥青等副产物的有效利用和炭纤维市场,进行着沥青基炭纤维的开发研究,从而达到实现炭纤维生产的工业化。
表2.12 吴羽化学公司和Amoco公司生产的沥青基炭纤维的牌号和性能[109]

2.2.3.2 沥青基炭纤维的结构及性能
沥青基炭纤维是指以沥青等富含稠环芳烃的物质为原料,通过聚合、纺丝、不熔化、炭化或石墨化而制得的含碳量大于92%的特种纤维。按沥青的原料来源,可分为石油系和煤系沥青基炭纤维;按其性能的差异,又可分为通用级沥青基炭纤维和高性能沥青基炭纤维,前者由各向同性沥青制备,又称各向同性沥青基炭纤维,后者由中间相沥青制备,故又称为中间相沥青基炭纤维。通用型沥青基炭纤维的强度为600~800MPa,模量为30~35GPa;高性能沥青基炭纤维强度达2000~6000MPa,模量高达900GPa以上。
2.2.3.2.1 沥青基炭纤维的结构
沥青基炭纤维的微观结构主要包括碳的乱层结构、微晶尺寸、择优取向、微小孔隙的直径、结构、空间三维结构及表面结构等方面。考察微晶沿轴向的取向和乱层结构在径向的排列是研究炭纤维结构的主要方法[110]。沥青基炭纤维的形态结构主要取决于原丝结构和热处理条件,在炭化过程中,原丝纤维的各种形态结构特征如分子排列、择优取向和单丝的截面形状等基本都被保留下来。
(1)纵向结构及取向度
在微晶中,碳原子层面与纤维轴构成一定角度的取向,称为择优取向,常用择优取向来表示微晶沿纤维轴取向的程度。沥青熔体在纺丝过程中,受到剪切和拉伸作用而使分子沿纤维轴向发生取向,经过氧化处理,这种取向被固定下来。炭化时,缩聚反应在取向的分子间进行,最终得到沿轴向取向的微晶结构[111]。微晶取向度越高,结构越规整,炭纤维的力学性能越优良。通过不同手段提高原丝中分子的取向,并使取向在热处理中进一步固定发展,便可获得高强度高模量的沥青基炭纤维[112,113]。
对于各向同性沥青基炭纤维,基本上没有微晶的取向,这种形态结构使其抗拉强度和模量降低,断裂伸长率减小,总体性能较差,只能作为一般应用,但是在应力石墨化处理时,微晶的择优取向随着纤维的应变有所改善。中间相沥青基炭纤维具有各向异性,经300℃处理后微晶取向度可达到90%以上。因此,中间相沥青更容易制取高模量炭纤维。
(2)径向结构与规整性
通用级沥青基炭纤维大多数为非晶态结构,这种形态结构使其抗拉强度和抗拉模量降低,断裂伸长率减小,总体性能较差。对于高性能沥青基炭纤维,由于所用沥青原料和调制方法不同,特别是受喷丝板结构的影响,纤维的断面结构有多种类型,如无规则结构、辐射状结构、褶皱结构和洋葱形结构,除此之外,还有表层为辐射状,内部为褶皱形或洋葱形的结构等[114]。
制取高强度炭纤维应避免辐射状结构,因为在辐射状结构热处理过程中容易产生裂纹,导致抗拉强度降低;而无规则结构、褶皱结构和洋葱形结构能赋予其高的抗拉强度等许多优异性能。因此应尽量减少表层幅射状结构所占的比例,以提高其抗拉强度,同时根据不同的用途,在制造过程中可调控其不同结构所占的比例。
借助拉伸反弹技术对PAN基炭纤维与中间相沥青基炭纤维的压缩性能进行研究,发现中间相沥青基炭纤维比PAN基炭纤维的压缩强度低。通过扫描电镜(SEM)观察发现PAN基炭纤维的表层石墨晶体无序度更高,因此它更趋于各向同性的力学性能,压缩性能更好。在此基础上研究人员提出了维持纤维拉伸性能和提高压缩性能的最优化晶体结构[115]。中间相沥青基炭纤维具有较高的抗拉模量、抗拉强度和优越的热传导性能,然而其压缩强度却不高。为了解决沥青基炭纤维压缩强度低的问题,Fumitaka Watanabe等将合成各向同性与各向异性沥青熔融混纺,热处理后得到高压缩强度的沥青基炭纤维[116]。
2.2.3.2.2 沥青基炭纤维的性能
沥青基炭纤维与PAN基炭纤维相比,具有以下性能特点[117]:①模量更高,中间相沥青生产的炭纤维属于易制得、易石墨化的高模量炭纤维,其模量已经达到930GPa,是理论值的91%左右,相当于PAN基石墨纤维模量的1.5倍左右;②热导率较高,高性能中间相沥青基炭纤维的热导率高达600~800W/(m·K),是钢的1.5~2倍,是PAN基石墨纤维的4~5倍,这一特征在电子工业、信息产业以及航空航天工业得到了广泛应用;③热膨胀系数(CTE)小,PAN石墨纤维的CTE约为-1.1×10-6/K,沥青基石墨纤维的CTE约为-1.5×10-6/K,同时沥青基石墨纤维的设计自由度大,可制得零膨胀产品;④抗冲击性好,各向同性沥青基炭纤维的断裂伸长率可达2.9%,比同类性能的PAN基炭纤维高,较高的断裂伸长率可提高制品的抗冲击性能,进而提高制品强度;⑤沥青基炭纤维的原料资源丰富、价格低,在生产成本上是一大优势;⑥炭化收率高,沥青基纤维制取炭纤维的炭化收率高达80%~90%,比PAN基炭纤维和黏胶基炭纤维的炭化收率都高。
(1)导热性
沥青基炭纤维的热导率远远高于PAN基炭纤维。PAN基炭纤维的热导率一般在200W/(m·K)左右,而沥青基炭纤维高达1100W/(m·K),即便是热导率高的铜也无法与其比拟。日本东洋公司[118]开发出热导率超过900W/(m·K)的超高热导率的沥青基炭纤维,该产品已被列入市场出售导热材料中最高类别。中间相沥青基炭纤维具有的高导热特性源于其内部三维有序堆积的类石墨层状结构和生长较为完整的石墨晶体。热处理温度越高,其类石墨晶体生长越完善,层片取向程度越高,电阻率越低,热导率越高[119]。
贺福、杨永岗[120]采用中间相含量高的沥青原料制取超高导热性能的沥青基炭纤维。所制沥青基炭纤维的密度高达2.18g/cm3,是理论值的93%,热导率达到1100W/(m·K),是理论值的55%~61%。Amoco公司[121]采用与K-1100X相同的中间相沥青为原料,经初生中间相纤维预氧化、热模压、炭化和约3000℃石墨化后制得无粘接自增强Thermal Graph板,其中炭纤维体积含量为82%时,室温热导率可达746W/(m·K)。该公司生产的部分中间相沥青基炭纤维的性能如表2.13所示。马兆昆等人[122]利用中间相沥青基纤维中沥青分子的高度择优取向和适度的热塑性热压制备了高导热块体。制备过程是通过纺丝获得沥青大分子有序排列结构的带状纤维,然后对纤维进行氧化处理,再经铺层、压制及2800℃左右石墨化处理制得室温热导率大于600W/(m·K)的自增强块体材料。
表2.13 Amoco公司生产的部分商业化沥青基炭纤维的性能[121]

美国Clemson大学的Gallego等人[123]用Mitsubishi Gas Chemical 公司提供的牌号为ARA24R-6U21的中间相沥青制备的带状沥青基炭纤维,经2400℃石墨化处理后,其热导率与目前商业化的圆形炭纤维经3000℃石墨化处理后的热导率相当。以中间相沥青为原料,采用氮压式单孔纺丝机进行熔融纺丝,然后使用Ti-B催化体系对所获得的中间相沥青基纤维进行催化,再经适度的预氧化处理后,通过热压自烧结成型工艺制备出热导率高达996.45W/(m·K)的炭板[124]。
应用在星载反射器的天线对尺寸的稳定性要求特别高,因为此种反射器只要有稍微的热变形就会改变天线的辐射范围,而具有高热导率和低热变形特性的沥青基炭纤维能够满足这种天线的特殊要求。
(2)吸波性
吸波材料作为隐身技术中重要的组成部分,其本质是将入射的电磁波吸收掉或衰减掉,同时将电能转化为热能或其他形式的能。
炭纤维是一种电损耗型吸波材料,由于其电阻率较低,是优良的导体,电磁波入射到纤维的表面就被反射出来,不能直接用于吸波涂层,通过对沥青基炭纤维进行表面金属化处理或者掺杂改性,可以改善其导磁性,使它变成电磁损耗型吸波材料。
在沥青基炭纤维表面镀镍可使其变成电磁损耗型吸波材料,在镀镍中间相沥青基炭纤维的吸波涂层中,镀镍中间相沥青基炭纤维作为偶极子在电磁场的作用下会产生耗散电流,在周围基体作用下,耗散电流被衰减,从而电磁波能量转换为其他形式的能量,主要为热能。刘辉[125]通过化学镀工艺在中间相沥青基炭纤维表面均匀包覆了金属镍。以镀镍中间相沥青基炭纤维作为吸收剂,环氧树脂为基体制备了单层吸波涂层,涂层的厚度为1.02mm时,吸波涂层在15.4~18GHz,反射率R小于-10dB,最大吸收峰在18GHz。
杨国伟等[126]采用氮压式纺丝机制备了中空截面沥青基炭纤维。当炭化温度为900℃时,中空炭纤维具有最大电磁损耗。炭纤维交叉铺层时,吸波合格带宽为10GHz,最大吸收峰在-25dB。在双层结构设计中,以中空多孔炭纤维为主体,分别添加炭黑、炭纤维和羰基铁粉,制备出双层轻质雷达吸波材料。以羰基铁粉作为吸收剂的匹配层比以炭黑和炭纤维作为吸收剂的匹配层对中空多孔炭纤维的吸波性能影响更为显著[127]。
分别用电磁搅拌法和超声波法两种镀镍工艺制备出表面镍含量较高的中间相沥青基炭纤维,超声波法制备的镀镍炭纤维的连续性优于电磁搅拌法,适合后续结构型吸波复合材料的制备。研究发现,镀镍后炭纤维的电损耗参数下降,磁导率提高,利于低频带吸收。镀镍后的炭纤维较未镀镍炭纤维提高了在低频带和高频带的吸波效果,在14.9GHz 的吸收峰峰值为-27.6dB,低于-5dB 的累积频宽约14GHz,低于-10dB 的累积频宽约6.5GHz,吸波效果明显[128]。
改变炭纤维的截面形状和大小,对吸收雷达波具有显著影响,异形截面炭纤维具有更加优异的力学性能和光电磁功能。美国Clementon大学的先进工程纤维中心对异形截面沥青基炭纤维进行了详细研究,发现其可以承受较大压应力和纤维特有转动惯量,而采用异形炭纤维与聚醚醚酮(PEEK)等树脂制成的复合材料可有效吸收雷达波,能使频率为0.1~50GHz的脉冲大幅度衰减[129]。
在电磁场作用下连续炭纤维中会形成较大的连续传导电流,导致其对雷达波容易产生强反射作用,而短切炭纤维在复合材料中随机分布,在与雷达波作用时形成偶极子或者谐振子,不形成连续传导电流,因此短切炭纤维复合材料相对于连续炭纤维复合材料对雷达波有较好的吸波效果。以中间相沥青为原料,采用熔融纺丝法制备出中间相沥青基纤维,经炭化、石墨化处理后进行短切和化学镀镍处理,最终获得短切镀镍沥青基石墨纤维材料。该材料在低频段的吸波效果较好,吸波频带在-10dB的频段为4.6~10.8GHz,带宽为6.2GHz,最大吸收峰在-23dB[130]。
(3)电学性能
碳和石墨的载流子密度随温度的上升而增加,因此炭纤维的电阻率随温度的升高而增加。在特定的测试温度下,电阻率随抗拉模量的增加而降低,这是因为随着抗拉模量增加,缺陷浓度降低,而缺陷是导致载波散射的原因。
降低炭纤维电阻率最有效的方法是增加夹层。夹层就是在碳层间插入的外界原子在层间形成的夹层化合物。这种夹层作为电子受体或供给体掺杂在炭纤维中,导致载流子浓度增加,使炭纤维的电阻率下降。但是夹层只存在于相对的石墨纤维中。例如,经溴化处理后Amoco公司Thornel系列的炭纤维P-120、P-100和P-75炭纤维的电阻率减少73%~79%,而P-55只减少4%。将P-100-4进行溴化处理(P-100-4的石墨化度高于P-100),其电阻率变为11.0μΩ·cm[131]。另外,夹层在高石墨化度放热纤维中发生剧烈反应,会导致纤维发生机械力损伤,因此炭纤维的力学性能和抗氧化性都有所降低[132]。因此,有个最佳的石墨化度,即像P-100炭纤维被溴化处理后的中间层。插入电阻率低中间层的炭纤维复合的材料具有电磁干扰屏蔽的作用。
2.2.3.3 沥青基炭纤维的制备技术及发展概况
1964 年,日本群马大学的大谷杉郎发明了用沥青制造炭纤维的技术路线,1970年,日本吴羽化学工业公司开始批量生产通用级沥青基炭纤维。1975年,美国联合炭化物公司(UCC)公布了用中间相沥青制造高模量炭纤维“Thornel P”的方法,并很快投入商业生产。从此,沥青基炭纤维进入发展的快车道,成为继 PAN基炭纤维之后的第二大类炭纤维。
沥青是带有烷基侧链的稠环芳烃化合物和杂环化合物的混合物,其结构和化学组成非常复杂,分子量在200~800,含碳量高于80%,软化点低于120℃,通常为黑色有光泽的固体。各种沥青的性质随沥青来源及低分子组成物的去除方式而变化。缩合芳烃是沥青中的主要组分,沥青中的H/C原子比可很好地代表其芳香度,其值越小,沥青的芳香度越高。
沥青的主要来源有:石油原油分馏后的渣油制得的石油沥青;石油分馏热解制取乙烯时副产的热解沥青;煤碳焦化工业副产物煤焦油沥青以及液化煤沥青。为了得到无杂质和分子量分布狭窄的产品,也有用合成树脂如聚乙烯树脂(PVC)或纯芳烃类如萘、蒽及其馏分油缩聚制得的合成沥青。
沥青中,特别是煤焦油沥青中常含有游离碳和固体杂质等细小颗粒,它们在纺丝过程中可能堵塞纺织孔或残留在初生纤维中成为所制炭纤维的断裂源。含有杂质的沥青也不易转变为流变性能好和各向异性突出的中间相沥青。因此,无论是通用级纤维还是中间相沥青基纤维,原料沥青都必须精制。
2.2.3.3.1 制备技术
(1)沥青基纤维及其炭纤维的制备
煤沥青基炭纤维的制备一般包括原料调制、缩聚反应、纺丝和炭化等流程。合成炭纤维的关键步骤是前驱体的缩聚反应和炭纤维的高温炭化反应。
目前,在实现工业化制备沥青基炭纤维的过程中,存在下列问题:
①沥青的高度精制;
②热稳定性高的中间相沥青的制备;
③高轴比和高分子性能的中间相沥青的制备;
④纺丝时纤维内取向的控制;
⑤纺丝后沥青基纤维强度的提高;
⑥不熔化处理生产能力的提高;
⑦炭纤维性能(强度、弹性模量和伸长率等)的改进。
(2)原料的调制
调制是通过沥青的热缩聚、加氢预处理及溶剂萃取的方法制取可纺沥青。沥青调制的目的:一是除去沥青中的轻组分,防止在纺丝过程中产生气泡而造成纺丝的断裂;二是提高软化点,使分子量分布均匀。
①各向同性沥青的调制。在工业上应用较广的调制方法是日本吴羽化学公司的各向同性沥青调制方法:采用石油沥青在900~1200℃,接触时间1/100s的条件下高温裂解得到聚芳烃结构的残渣油,然后在380℃左右通入N2,热处理渣油,干馏1h再减压蒸馏1~5h,以去除低分子量物质。
②中间相沥青的调制。中间相沥青的制备是把石油裂解后残存的重质杂质加以去除,制成高品质的各向同性粗料的过程。该过程在惰性媒介中进行,在380~450℃下加热1~5h并在400℃时过滤熔液,除去不熔性颗粒。
杜邦公司[133]在380~430℃沥青原料热处理中,每千克石油沥青原料通入0.16~0.22m3/h的N2或蒸汽,并以300~500r/min进行机械搅拌,可以得到100%的中间相沥青。Singer[134]以美国Ashland公司生产的商品为原料,在惰性气体保护和机械搅拌下升温至400℃,恒温保持17~20h,得到中间相沥青的软化点达到330℃以上。之后经过多次改进,采用较低的温度(370~390℃)和较长的反应时间(30h),在不降低中间相含量的情况下适当改善中间相沥青的流动性和可溶性。
(3)沥青基纤维的不熔化处理
由于纺丝沥青是软化点较低的热塑性体,为了在炭化过程中保持其形态和择优取向,需将沥青基纤维置于氧化条件下处理,得到结构稳定的不熔性纤维,才能顺利进行沥青基纤维的炭化和活化。不熔化方法主要有气相氧化法和液相氧化法。沥青基纤维在工业上普遍采用气相不熔化方法,即用热空气氧化交联沥青分子,氧气分子扩散进入纤维中,与沥青分子发生复杂的氧化反应。不熔化处理一般在200~350℃的氧化气体中进行,处理时间为1~3h。
沥青基纤维的氧化大致可以分为三个阶段:①在150~260℃的温度范围内,纤维氧化以氧原子的吸收为主,表现为纤维快速增重,纤维经分子氧化生成羰基、羧基和醚基等含氧基团,同时生成H2O;②在260~320℃的温度区间内,反应除析出H2O外,还析出CO2,且随温度升高,两者的析出量迅速增加,形成网状化分子,逐步形成醚基、酮基、酸酐和内酯型热稳定氧桥结构;③320℃以上则出现纤维的氧化热解,导致CO、CO2的释放量急剧增加,同时纤维开始失重[135]。
沥青基纤维在200~300℃氧化气氛条件下发生热氧化反应,生成的氧桥连接分子网络结构提高了沥青基纤维的耐热性能,为炭化提供了结构条件。不熔化处理使沥青基纤维增重率提高,碳氧基团含量增大,形成碳氧网络结构,使纤维熔点提高,强度上升。不熔化温度、时间、氧化剂浓度及升温速率是不熔化处理的主要影响因素,它们不但影响不熔化纤维的结构与性能,而且影响沥青基纤维的炭化和活化[136]。
不熔化温度越高,纤维表面的氧化反应速率越快,从而阻碍了氧原子从表面向内部的扩散,增加了纤维在径向的氧浓度梯度,纤维完全不熔化则需要更长时间。不同温度下的氧化扩散机理不同。在氧化温度较低,氧化时间较短时,纤维中的氧含量与氧化温度呈线性关系;但是在较高氧化温度下不满足这种关系,纤维整体的氧含量反而偏低[137]。在不熔化过程中,随着不熔化温度的升高,炭纤维的强度开始呈上升趋势,达到最大值后,则随着温度的升高呈降低趋势。分子量高、芳香度高的中间相石油沥青基纤维在较低温度下就可以达到不熔化,不熔化温度比各向同性沥青基纤维低40℃,各向同性沥青基纤维的不熔化温度为340℃[138]。短时间完成不熔化,则不熔化的最终温度需要很高;而长时间不熔化,则可以在较低不熔化终温下完成。不熔化气体分布方式对炭纤维最终力学性能有较大影响,更均匀的氧分布和更快速地排出反应生成物是不熔化反应的关键[139]。
(4)沥青基炭纤维的炭化和石墨化处理
为提高纤维的力学性能,应对不熔化沥青基纤维在惰性气氛中进行炭化或石墨化处理。通常炭化是指1700℃以下对沥青基纤维进行热处理,而石墨化则是指在接近3000℃对沥青基纤维进行热处理。炭化的目的在于除去不熔化处理后纤维中的杂原子,得到网层结构。石墨化处理可以进一步完善网层结构而使炭纤维具有优异的性能。
炭化后PAN纤维的收缩率约为60%,人造丝约为20%,沥青基纤维则高达80%,因而炭化后沥青基炭纤维有可能达到更高的密度。而且沥青基炭纤维的石墨化程度高,所以弹性模量高。
日本石油公司[140]研究出一种先制备含氧炭化纤维再用石墨化处理的方法,可大大提高炭纤维石墨化处理的升温速率,缩短处理时间,同时提高炭纤维的机械性能。具体方法是:沥青基纤维经不熔化处理后,在450~600℃惰性气体中处理,制得含氧3%~10%的预炭化纤维。预炭化时间不限,通常为1~30min。预炭化纤维在惰性气体中以1000~1500℃/min石墨化处理5s~10min即可制成高质量、高性能的沥青基炭纤维。
中间相沥青预氧丝在炭化过程中发生脱氧脱氢增碳的反应,在低温区主要发生脱氧反应,在高温区主要发生脱氢反应,炭化温度高于1000℃以后,C、H和O 三种元素的组成比例趋于定值。纤维的断裂伸长率随炭化温度的升高而减小,当温度大于1100℃以后断裂伸长率逐渐趋于定值。在600~1200℃范围内,中间相沥青基炭纤维的抗拉强度、抗拉模量及密度均随炭化温度的升高而增大[141]。
N.C.Gallego等[142]研究高导热炭纤维结构与性能的关系,发现随着石墨化温度的升高,纤维的导热导电性增强。M.L.Greene等[143]研究发现,高温石墨化使得纤维的石墨化程度在较短时间内迅速提高,中间相沥青基炭纤维在3000℃停留0.75s,其石墨化程度可达到50%,密度达到1.98g/cm3,热导率为200W/(K·m)。
(5)新的制备方法
随着沥青基炭纤维的发展,新的制备方法不断涌现。
以各向同性煤沥青为原料,采用熔融纺丝工艺,经石墨化后制得的炭/石墨纤维具有与沥青原料相似的各向同性的光学结构。随着热处理温度升高,炭/石墨纤维界面逐渐变粗糙,且内部石墨微晶逐步发育长大,3000℃下石墨化纤维微晶增长较明显。1600℃下炭化纤维的力学性能较好,其抗拉强度和抗拉模量分别达到0.57GPa和32.19GPa,进一步提高热处理温度,纤维抗拉强度逐步降低,但是其抗拉模量逐渐增加,3000℃下石墨化纤维的抗拉强度和抗拉模量分别为0.26GPa和40.57GPa;炭/石墨纤维室温轴向电阻率随热处理温度的升高而降低,3000℃下热处理与1000℃下热处理的纤维相比,室温轴向电阻率降低25.60μΩ·m[144]。
用萘基中间相沥青制备炭纤维,发现各向异性含量80%~100%的萘基中间相沥青存在一热稳定温度区间,随着聚合反应的深入,此区间变化不大,但萘基中间相沥青纺丝温度提高,尤其当中间相含量达到100%后,如果纺丝温度超过热稳定温度区间,纺丝性能变差,且所得炭纤维极易劈裂,性能降低[145]。
李旦、张庆宇[146]探索了流化催化裂化(FCC)重芳烃试制沥青基炭纤维的可行性,初步实验表明,FCC重芳烃中芳烃含量高,分子量分布和环结构较均匀,是制备中间相沥青基炭纤维的优良原料,并能制备出接近中强水平(抗拉模量在80~100GPa)的中间相沥青基炭纤维。中间相沥青的纯度是影响炭纤维性能的一个关键因素,固体杂质和杂原子都会大大降低炭纤维的性能。降低杂质含量,同时将废催化剂脱除干净,则有可能大幅度地提高沥青基炭纤维的性能。
2.2.3.3.2 沥青基炭纤维生产现状
目前通用级的沥青基炭纤维全世界需求量大概在2000t,产量约2000t,在国际市场上基本产销平衡。我国通用级沥青基纤维产量不到100t,产需也基本平衡,但是国内开发高性能炭纤维的生产技术以及生产设备还有难度。另外,由于高性能炭纤维及复合材料属于高科技产品,是发展航空航天、尖端技术必不可少的新材料,国外严格限制相关技术的出口,这也制约着国内高性能炭纤维的开发应用。
研究沥青基炭纤维的单位较多,生产通用级沥青基炭纤维的主要是日本吴羽化工工业公司,能批量生产高性能炭纤维的单位有日本的三菱化学公司、日本的石墨纤维公司和美国的BP公司。
日本吴羽化学公司主要生产通用级沥青基炭纤维,和其他炭纤维一样,可以以纤维、织物形式使用,但大多数用于复合材料。通用级沥青基炭纤维最初主要用于高温绝热材料、填料和工程塑料。目前通用级沥青基炭纤维大量用于取代石棉制品和制造汽车、机动车等的刹车盘,还大量用于水泥增强和塑料、橡胶等非结构材料的增强。其中间制品的形式有:①切成短丝(长度为3~6mm)或磨成粒状(100~1600μm);②炭纤维纸:由短纤维和黏结剂采用湿法制成;③无纺垫:由部分炭纤维长丝与短纤维模压而成;④强化垫:将无纺垫多层叠合,模压制得;⑤针织垫:将无纺垫或压合垫用特殊的纤维缝合而成[147]。
日本石墨纤维公司的产品主要为各种沥青基炭纤维,包括:Granoc XN系列沥青基炭纤维、Granoc CN系列沥青基炭纤维、Granoc YSH-50A-10H宇航级沥青基炭纤维和Granoc YS-A 系列超高模、高热导率沥青基炭纤维等。此外,还生产Granoc预浸料和Granoc炭布,包括供航天工业使用的超轻和超薄炭布等。
Granoc XN系列沥青基炭纤维属于低模量、低强度炭纤维,纤维直径10μm,每束纤维3K根,该纤维一般用于制备体育休闲用品和一般工业用品。
宇航级沥青基炭纤维牌号包括Granoc YSH、 YSH-50A、YSH-60A和YSH-70A等牌号,丝束有1K、3K和6K。宇航级沥青基炭纤维的热导率较高,一般为140~260W/(m·K),电阻率较低,为5×10-4~7×10-4Ω·m,热膨胀系数是负值,为-1.4×10-6/K。Granoc YS-A系列是超高模、高热导率沥青炭基纤维,Granoc YS-95A的抗拉模量最高,达920GPa。Granoc YS-A系列沥青基炭纤维的热导率高达320~600W/(m·K)[148]。
日本三菱化学公司是世界上有名的煤化学技术研究、开发和生产单位,已经有50多年的历史,它的产品包括:炭纤维、针状焦、沥青焦、黏结沥青、炭黑、电极和活性炭等。三菱化学公司的DIALEAD沥青基炭纤维有连续长丝和短切纤维。沥青基炭纤维最大的特色是它们具有DIALEAD高模量和高热导率。某些牌号的沥青基炭纤维模量高达935GPa,热导率为800W/(m·K),是铜热导率的1.57~2.03倍。三菱公司生产的宇航级炭纤维包括K1352U、K1392U、K13B2U、K13C2U、K13D2U和K13A1L等,宇航级沥青基炭纤维的抗拉强度在3600~3800MPa,抗拉模量在620~930GPa,热导率在140~800W/(m·K)[149]。
美国BP公司在20世纪70年代研制沥青基石墨纤维取得很大进展,80年代研制开发出高性能、高模量的沥青基石墨纤维。其中沥青基石墨纤维的牌号系列包括P系列的P-25、P-30X、P-55S、P-75S、P-100S和P-120S以及K系列的K-800X和K-1100X。该系列沥青基石墨纤维和性能如表2.14所示。
表2.14 P系列和K系列沥青基石墨纤维和性能[150]

我国对沥青基炭纤维的开发从20世纪70年代初期开始,上海焦化厂使用煤焦油作为原料成功开发出沥青基炭纤维,但由于产品质量和研究结果不稳定等原因,最终没能实现工业化生产。70 年代末期,中国科学院山西煤炭化学研究所开始研究沥青基炭纤维,经过了一系列的研究,取得了一定的研究成果。随后,原冶金工业部在山东烟台筹建的新材料研究所开始生产通用级沥青基炭纤维,规模为70~100t/a,主要用作飞机刹车片,90年代初扩大到150t/a,但由于关键设备不过关和缺乏改造资金等问题,迄今仍处于停产状态。20世纪90年代初期,辽宁省鞍山东亚炭纤维有限公司投资1.2亿元从美国阿西兰德公司引进了一条200t/a的熔喷法沥青基炭纤维生产线,经过一段时间的技术改造后,正逐步根据新的市场应用拓宽研究领域。近年来,我国炭纤维的产量虽有增加,但与不断增长的需求相比仍有较大的差距。最近,山东省淄博矿业集团自主研发的煤炭热解提取煤沥青技术获得成功,每吨煤的沥青提取率可由10%提高到50%。企业总共投入2000多万元,最终研制出炭纤维和活性炭纤维。
2.2.4 黏胶基炭纤维
2.2.4.1 黏胶基炭纤维的结构和性能
黏胶基炭纤维是以黏胶纤维为原料,在低温热处理后,于非氧化性气氛中进行800℃以上的高温热处理,最终制得以碳为主要成分的纤维材料。
纤维素是自然界存在量最大的一类有机化合物,是棉、麻和木材等的主要成分。它的化学结构式为(C6H10O5)n,含碳量44.44%,含氧量49.39%,含氢量6.17%,聚合度n一般在10000~15000。通常用来制造黏胶纤维的木浆或棉浆,经过一系列化学处理,其平均聚合度(DP)降低到350~400,以提高强度等力学性能。

图2.8 纤维素Ⅱ的结构单元
(1)黏胶基炭纤维的结构
黏胶纤维又称为再生纤维,主要由纤维素Ⅱ组成。其结构单元如图2.8所示,每个纤维素分子单元中含有1个伯羟基和2个仲羟基,因此黏胶纤维具有强吸水性。由于分子间强的氢键作用,它的裂解温度低于熔融温度,因此成为制造炭纤维比较理想的原料之一。
黏胶基炭纤维六元环中两相邻碳原子之间的距离是1.46nm,两个碳环的中心距离为0.25 nm,与规整的石墨结构相近,但有微弱差别:理想的石墨结构两相邻碳原子之间的距离是1.42nm,两个碳环的中心距离为0.25nm。黏胶基炭纤维表面碳网结构是非理想的稍有变形的石墨六元环[151]。
房宽峻等[152]提出了如图2.9所示的微结构模型来描述国产黏胶基炭纤维的微结构。图中所示的纤维呈腰果形,纤维表面上沟槽、坑洞和裂纹的分布是不均匀的。纤维内部存在许多尺寸较小的微晶体,这些晶体呈乱层石墨结构,由3~7层碳网平面组成。

图2.9 黏胶基炭纤维的微结构模型[152]
理论上,黏胶基炭纤维的固有强度可以达到150GPa,但由于炭纤维内部的微结构与缺陷的影响,其抗拉强度远远小于这个数值。黏胶基炭纤维中的结构缺陷是影响其抗拉强度的关键因素,此类缺陷包括裂纹、内部孔洞和杂质等等。黏胶基炭纤维中的缺陷主要有以下两个来源:一是黏胶基炭纤维原丝的缺陷;二是黏胶基炭纤维在炭化过程中形成的孔洞及形成炭丝后因机械或人为因素对炭丝表面造成的损伤等。
(2)黏胶基炭纤维的性能
1981年,美国人克罗斯和贝文发明了黏胶基炭纤维,1959年出现间歇法生产的黏胶基炭纤维织物,1961年连续黏胶基炭纤维产品上市。但随着PAN基炭纤维的问世,黏胶基炭纤维的产量逐渐下降,造成此种局面的原因是:生产黏胶基炭纤维的工艺流程较长,工艺条件苛刻,炭化收率较低,不适宜大批量生产,成本高。同时黏胶基炭纤维的整体性能指标比PAN 基炭纤维要差,因此其应用也受到限制。
黏胶基炭纤维具有独特的性能,主要表现在:难石墨化碳,类似玻璃碳,层间距d002大,石墨微晶不发达、排列紊乱、取向度低、强度低、模量低且伸长度大;密度小,一般比PAN基炭纤维和沥青基炭纤维小15%左右,所制复合材料更易实现轻量化;属于大伸长型炭纤维,韧性好,易深加工;由天然纤维素转化而来,生物相容性好,这也是其他类型炭纤维无法与其比拟的;碱和碱土金属含量低,抗氧化和热稳定性好,耐烧蚀。
黏胶基炭纤维具有独特的性质,在某些领域得到广泛的应用,虽然产量低,但不可能完全被淘汰,因此美国和俄罗斯等国家的生产公司在黏胶基炭纤维生产方面有一定的实力。美国生产黏胶基炭纤维的公司主要有UCC和HITC。这两家公司生产的黏胶基炭纤维牌号及性能如表2.15 所示。俄罗斯在黏胶基炭纤维的研究、开发和应用方面有很大的成就,整体水平居世界之冠。
表2.15 美国生产的高性能黏胶基炭纤维及其性能[153]

航天级高纯黏胶基炭纤维是导弹大面积放热层的主要骨架材料,其性能关系到导弹的命中精度。导弹在高空的高速飞行以及重返大气层的高速坠落过程中,导弹外壳与空气的剧烈摩擦,使温度达到上千摄氏度,任何耐高温的金属在如此高的温度下都将气化,从而造成导弹失去平衡或者是导航系统的失误。在此种情况下,航天级高纯黏胶基炭纤维具有很高的耐烧蚀性,因此就成了导弹的防护服。
酚醛树脂/黏胶基炭纤维复合材料的烧蚀性能优于酚醛树脂/PAN基炭纤维复合材料,其中氧-乙炔线烧蚀率前者是后者的65%,氧-乙炔质量烧蚀率前者是后者的92%[154],且前者的烧蚀沟槽浅,烧蚀面均匀。但是酚醛树脂/黏胶基炭纤维复合材料的弯曲性能差,因此更适用于工作压力低、冲刷环境较为缓和的航天大口径战略战术弹箭武器热防护部件。美国和俄罗斯利用了黏胶基炭纤维耐烧蚀的特性和酚醛树脂残碳量高、焦化强度高和发烟量少的性能,把黏胶基炭纤维增强酚醛树脂复合材料用于战略武器的隔热材料,两者的性能叠加,使其复合材料的综合性能优异无比,成为当今不可取代的防热材料。
黏胶基炭纤维具有良好的耐烧蚀特性,国内外已将其作为防热结构的重要增强材料。目前洲际战略导弹弹头的大面积防热材料采用黏胶基炭纤维增强树脂基复合材料,但是黏胶基炭纤维表面光滑,与树脂粘接性能差,不仅导致材料的剪切强度低,而且在弹头再入大气层过程中,在气流的强烈冲刷下,会产生不均匀烧蚀剥离现象,对导弹的制导精度产生不良影响,因此实际应用中要对黏胶基炭纤维表面进行处理[155]。用连续式电化学氧化表面处理黏胶基炭纤维表面,能够有效地在纤维表面产生活性官能团,提高表面粗糙度,从而有效地提高表面润湿性[156]。
黏胶基炭纤维具有优异的隔热保温性能,因为材料的热导率与其密度成正比,黏胶基炭纤维的密度较低,其热导率较低。另外,黏胶基炭纤维靠晶格波传热,其微晶高度较小,因此具有隔热保温性能。
黏胶基炭纤维具有良好的生物相容性,故可以制造医用生物材料,例如假肢和骨夹板,医用电极和电头。俄罗斯等国家已经广泛应用黏胶基炭纤维制得的外伤包扎带。
2.2.4.2 制造方法
生产黏胶基炭纤维的工艺流程大致包括:黏胶纤维→水洗→酸洗→浸渍催化→预氧化→炭化→表面处理→炭纤维。
黏胶基炭纤维原丝的主要技术指标[157]:
①纤度 (184±30)dtex
②纤度不均匀率 ≥84N
④强力不匀率 ≤4%
⑤绝对断裂伸长率 ≥8%
⑥伸长不匀率 ≤5%
⑦残硫 250mg/100g纤维
⑧残锌 70mg/100g纤维
其中生产黏胶基炭纤维的技术关键有:
①提高原丝质量。原丝纯度高才可制得高质量炭纤维,原丝的结晶细晶化是提高炭纤维性能的有效途径,最好选用圆形截面的黏胶纤维原丝。
②浸渍催化剂的选择。使用浸渍催化剂后可降低活化能,降低热失重速率,使起始反应温度向低温侧移动,使热解反应变得缓和,从而工艺上易于控制,实现稳定和连续生产。
③高温炭化技术与设备。生产黏胶基炭纤维的高温炭化温度达到1500~2400℃,方可产出连续长度的长丝炭纤维。在如此高的炭化温度下,炉体内的微量氧对石墨发热体的氧化十分严重,因此需要抗氧化处理技术和设备。
④表面处理技术。为提高材料的层间剪切强度,需将炭纤维表面的憎液性改性为亲液性。
⑤上浆量与上浆剂的选择。上浆的目的是改善深加工性能和保护已表面处理后的炭纤维表面不再受污染。上浆量一般为0.5%~0.8%,一般不大于1.2%。上浆剂是所制复合材料中增强纤维与基体两相的真正界面,因此需选择与炭纤维和树脂基体具有双亲性的上浆剂。
与制取高性能PAN基炭纤维一样,优质黏胶纤维(原丝)是制取高性能黏胶基炭纤维的前提。黏胶原丝的皮芯结构、内部微孔、表面沟槽在预氧化和炭化过程中虽有所改变,但都不同程度地得以保留,而炭纤维的微结构、裂纹和缺陷、表面形态是影响炭纤维强度的主要因素。研究结果也表明[158,159]:原丝的直径不均率(CV)小,截面形状近似圆形,纤度和强度小,将易于制得高强度的炭纤维。
通过对比国产和俄罗斯产的原丝发现,在低温区,俄罗斯原丝的收缩应力较小,具有较大的结晶度、结晶尺寸和结晶取向度。从纤维的SEM图观察到,俄罗斯原丝不仅细而圆,且表面光滑。国产原丝有严重的沟槽和空穴结构,界面呈不规则形状,从而导致纤维的热机械和力学性能差[160]。因此我国还需在原丝的开发方面做出更多的研究和努力。
(1)黏胶纤维的前处理
使用40~60℃的无离子水洗去黏胶纤维表面的油剂。所用油剂一般为锭子油、仪表油、矿物油和表面活性剂聚氧乙烯化合物以及其他辅助剂。用温水洗掉油剂后还需要用酸水洗净黏胶纤维中所含的碱、碱金属和铁离子,降低这些金属离子的浓度,有利于提高黏胶基炭纤维的力学性能,同时提高其抗氧化性能和耐腐蚀性能。为提高水洗效果,采用喷淋水洗与漂洗相结合的方法为好。
(2)催化处理
黏胶纤维在热处理前需浸渍催化处理,其目的是促进羟基脱水,以提高炭纤维性能和炭纤维收率。黏胶纤维含碳量低,炭化收率也低。通过浸渍催化剂,使黏胶纤维的实际炭化收率由18%~20%提高到30%以上。催化剂及催化技术是生产黏胶炭纤维的核心技术,各生产厂家所用的催化剂种类有很大差异。采用的催化剂大多为硫酸、硫酸盐、硼酸、硼酸盐、磷酸、磷酸盐、磷化物、盐酸和铵盐等无机催化剂。在生产黏胶基炭纤维时,常用铵盐作脱水催化剂,催化效果较好。因为铵盐具有以下特性:溶解后的水溶液亲水性好,可润湿纤维,浸渍均匀;浸渍纤维的NH4Cl等铵盐,可在较低温度下分解,释放出NH3,促进烯链烃残片的热缩聚,有利于乱层石墨的形成;超过1100℃炭化时,铵盐全部逸出,可制得杂质少、纯度高的黏胶基炭纤维。
在黏胶纤维低温热处理时加入硫酸作为催化剂,发现硫酸在黏胶纤维热分解过程中起着催化脱水的作用,使得脱水温度大大提前,温度范围变宽,封闭了纤维素环上的—OH,从而抑制左旋葡萄糖的产生,提高碳产率,对黏胶纤维热解过程中结构和热收缩性能产生很大影响[161]。李辉、温月芳[162,163]研究了有机硅在制备黏胶基炭纤维时的作用。研究发现有机硅可与纤维素分子中的羟基形成分子间氢键,使纤维素大分子处于溶胀状态,促进了无机催化剂分子向纤维芯部渗透的能力,改善了催化剂的浸渍效果;有机硅还可与黏胶纤维大分子发生适度的交联,提高纤维在中温炭化过程中的可拉伸性,进而提高黏胶基炭纤维的性能;在黏胶纤维低温裂解时,有机硅会在纤维表面形成一层保护膜,减少了纤维表面的裂纹和沟槽;有机硅还可使黏胶纤维的裂解反应缓慢地由表及里地进行,减缓黏胶基炭纤维的皮芯结构。他们还研究了硫酸铵/氯化铵处理对黏胶纤维热裂解行为的影响,结果表明硫酸铵/氯化铵处理黏胶纤维与传统的硫酸/尿素处理黏胶纤维相比,其裂解反应的温度更低,炭化收率更大;硫酸铵/氯化铵催化体系的活性催化组分在一个宽温度范围内缓慢释放,对黏胶纤维裂解反应的催化效果更佳;黏胶纤维经硫酸铵/氯化铵催化剂处理后,反应级数由1.1增大到3.2,反应活化能由237kJ/mol降低到94kJ/mol。采用此催化体系制备的黏胶基炭纤维抗拉强度达到1.05GPa。
(3)黏胶纤维的热处理
黏胶纤维的热解是一个包括脱水、热裂解、缩合交联和原子重排等复杂的化学变化过程。由热固性黏胶纤维经过一系列热处理转化为无机炭纤维的过程大致可以分为四个阶段。
①25~150℃,主要脱除约12%物理吸附水,在此阶段侧向有序性增加。
②150~240℃,优先从赤道位置的氢和羟基分子碎片脱除结构水。红外光谱分析证明有CO、C
C形成,说明是分子内脱水。
③240~400℃,C—O、C—C键热解生成大量的焦油、水、二氧化碳和一氧化碳。在400℃时,纤维素环破坏生成新的C4残链。C4残链是转化为炭纤维结构的基础。
④400~700℃,进行芳构化生成碳的六元环,同时释放氢和甲烷等;900℃时生成类石墨结构;温度再升高,生成的乱层石墨层片沿纤维轴取向;温度升高到2200~2800℃的石墨化温度时,利于其塑性拉伸,使抗拉强度和抗拉模量得到大幅度提高。
黏胶纤维的热解动力学方程可以用反应速率表示,即
(2.3)
式中,a为黏胶在时间t时的热解分数;k为反应速率常数;t为反应时间。
反应速率常数k也遵守阿累尼乌斯方程,即
k=AeE/(RT) (2.4)
式中,A为频率因子;E为分解反应的活化能;R为气体常数;T为热力学温度。
将上述两个方程合并,则得:
(2.5)
式(2.5)是总的热解反应动力学方程。黏胶纤维的热解反应一般为一级反应。
热解过程中的升温速率对黏胶纤维的裂解所得产品产率和产品性能有一定影响:较慢的加热速率将会促进纤维素充分脱水,形成较稳定的中间产物,提高最终产率[164]。
(4)黏胶基纤维的炭化
炭化是含碳物质在惰性气体或真空氛围下的热解过程。黏胶基纤维布或纤维毡的炭化一般要在氮气保护下,通过热解反应排除纤维丝中的非碳物质(如图2.10所示)。

图2.10 纤维素热解机理
非碳元素以H2O、CO或CO2的形式排除以后,剩余的碳元素会重新排列形成无定形碳或类石墨结构。炭化过程受到多种因素的影响,温度、时间和保护气流量都必须严格控制。炭化过程优的标准是:较高的炭化收率、较低的挥发成分和较大的纤维强度。黏胶基炭纤维在2200~3000℃下石墨化可大幅度提高弹性模量和抗拉强度。它在2200℃以上有塑性区,借助外力使石墨层片沿轴向取向、重排,从而制得弹性模量高的黏胶基石墨纤维。
由于炭纤维的结构取决于原丝结构的炭化工艺,因此通过提高炭化温度或进行石墨化处理,可以增加表面的碳网平面比例,使表面原子排列更加规则有序;并且通过恰当的表面处理,可以减少表面缺陷,从而大幅度提高纤维的抗拉强度,改善纤维与其他基体的黏结性能。彭平等[165]采用以多元胺为主体的化学改性剂和烧结工艺,大大缩短了制备所需时间,同时提高了黏胶基炭纤维的性能。有机多元胺通过与纤维素发生化学反应促进了其分子间的交联,使黏胶丝在600℃后的残重率明显提高,从而提高了碳的收率。表面活性剂的加入使多元胺等在纤维表面分散渗透,增加了润湿性和均匀性,改善了涂层性质,提高了纤维各温区下的分散性和柔软性。