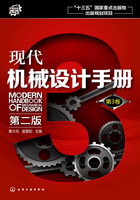
齿轮传动总览
(1)齿轮传动分类

(2)齿轮传动主要特点及适用范围




第1章 渐开线圆柱齿轮传动
1.1 渐开线圆柱齿轮的基本齿廓和模数系列
1.1.1 渐开线圆柱齿轮的基本齿廓(GB/T 1356—2001)
GB/T 1356—2001标准规定了通用机械和重型机械用渐开线圆柱齿轮(外齿或内齿)的标准基本齿条齿廓的几何参数。此标准规定的齿廓没有考虑内齿轮齿高可能进行的修正,因此内齿轮对不同的情况应分别计算。为了确定渐开线类齿轮的轮齿尺寸,标准基本齿条的齿廓仅给出了渐开线类齿轮齿廓的几何参数。它不包括对刀具的定义,但为了获得合适的齿廓,可以根据基本齿条的齿廓规定刀具的参数。
1.1.1.1 标准基本齿条齿廓
标准基本齿条齿廓是指基本齿条的法向截面齿廓,基本齿条相当于齿数z=∞、直径d=∞的外齿轮;相啮标准基本齿条齿廓是指齿条齿廓在基准线P—P上对称于标准基本齿条齿廓,且相对于标准基本齿条齿廓的半个齿距的齿廓。标准基本齿条齿廓代号的意义和单位见表14-1-1;标准基本齿条齿廓的几何参数见表14-1-2。
表14-1-1 标准基本齿条齿廓代号

表14-1-2 标准基本齿条齿廓的几何参数值和几何关系

1.1.1.2 不同使用场合下推荐的基本齿条
(1)基本齿条型式的应用
A型标准基本齿条齿廓推荐用于传递大转矩的齿轮。
根据不同的使用要求可以使用替代的基本齿条齿廓。
B型和C型基本齿条齿廓推荐用于通常的使用场合。用一些标准滚刀加工时,可以用C型。
D型基本齿条齿廓的齿根圆角为单圆弧齿根圆角。当保持最大齿根圆角半径时,增大的齿根高(hfP=1.4m,齿根圆角半径ρfP=0.39m)使得精加工刀具能在没有干涉的情况下工作。这种齿廓推荐用于高精度、传递大转矩的齿轮,齿廓精加工用磨齿或剃齿。在精加工时,要小心避免齿根圆角处产生凹痕,凹痕会导致应力集中。
几种类型基本齿条齿廓的几何参数见表14-1-3。
表14-1-3 基本齿条齿廓

(2)具有挖根的基本齿条齿廓
使用具有给定的挖根量uFP和挖根角αFP的基本齿条齿廓时,用带凸台的刀具切齿,并用磨齿或剃齿精加工齿轮,见图14-1-1。uFP和αFP的具体值取决于一些影响因素,如加工方法等。

图14-1-1 具有给定挖根量的基本齿条齿廓
1.1.1.3 其他非标准齿廓
对于大多数应用场合,利用GB/T 1356—2001标准基本齿条齿廓可以满足啮合要求。
在特殊情况下,当GB/T 1356—2001齿廓不能满足需要时,也可以使用其他非标准齿廓。
①小压力角的齿廓,如αP=14.5°或αP=15°的压力角,它可以增大重合度,降低噪声。
②大压力角的齿廓,用于重载齿轮传动,如αP=22.5°常用于汽车拖拉机齿轮,αP=28°多用于航空齿轮;它可以提高齿面的接触强度和齿根的弯曲强度,但会使端面重合度变小,齿顶圆齿厚变小。
③齿顶高系数的短齿齿廓,
或0.9,主要用于汽车、拖拉机的齿轮;用以降低齿顶齿根间的滑动速度,提高抗胶合能力。
④齿顶高系数的长齿齿廓,如
,主要用于高精度的航空、船舶齿轮;以达到重合度ε>2,降低噪声、提高承载能力。但由于啮合时齿面滑动速度较高,胶合危险增加。
1.1.2 渐开线圆柱齿轮模数(GB/T 1357—2008)
GB/T 1357—2008规定了通用机械和重型机械用直齿和斜齿渐开线圆柱齿轮的法向模型。
模数是齿距(mm)除以圆周率π所得的商,或分度圆直径(mm)除以齿数所得的商。
法向模数定义在基本齿条(见GB/T 1356—2001)的法截面上。
标准模数列于表14-1-4,应优先采用表中给出的第Ⅰ系列法向模数,避免采用第Ⅱ系列中的模数6.5。
新标准与旧标准GB/T 1357—1987相比较,有以下变动。
①删除了GB/T 1357—1987中mn<1的模数值,其中第Ⅰ系列有0.1、0.12、0.15、0.2、0.25、0.3、0.4、0.5、0.6、0.8十个模数值,第Ⅱ系列有0.35、0.7、0.9三个模数值。
表14-1-4 渐开线圆柱齿轮模数

②删除了GB/T 1357—1987中第Ⅱ系列模数值为3.25、3.75的两个模数。
③增加了第Ⅱ系列模数值为1.125和1.375的两个模数。
1.2 渐开线圆柱齿轮传动的参数选择
1.2.1 渐开线圆柱齿轮传动的基本参数
渐开线圆柱齿轮传动的基本参数及选择原则如表14-1-5所示。
表14-1-5 渐开线圆柱齿轮传动的基本参数

1.2.2 变位圆柱齿轮传动和变位系数的选择
1.2.2.1 变位齿轮传动的原理
1)用展成法加工渐开线齿轮,当齿条刀具的基准线与齿轮坯的分度圆相切时,加工出来的齿轮称为标准齿轮;当齿条刀具的基准线与齿轮坯的分度圆不相切时,则加工出来的齿轮称为变位齿轮。齿条刀具的基准线和齿轮坯的分度圆之间的距离称为变位量,用系数x与齿轮模数m的乘积xm表示,x称为变位系数;当刀具由齿轮坯中心移远时(如图14-1-2所示),x为正值(x>0),这样加工出来的齿轮称为正变位齿轮;当刀具移近齿轮坯中心时,x为负值(x<0),这样加工出来的齿轮称为负变位齿轮。

图14-1-2 变位外齿轮形成原理
斜齿圆柱齿轮的变位,可用端面变位系数xt或法向变位系数xn表示,端面变位系数和法向变位系数之间的关系为:xt=xncosβ。
齿轮经变位后,由于基圆未变,其齿形与标准齿轮同属一条渐开线,但其应用的区段却不相同(见图14-1-3)。正变位齿轮(x>0)用曲率半径较大的一段渐开线,其分度圆齿厚比标准齿轮增大2xmtanα,齿根高减少xm;负变位齿轮(x<0)用曲率半径较小的一段渐开线,其分度圆齿厚比标准齿轮减薄,齿根高却增大。利用这一特点,通过选择变位系数x,可以得到有利的渐开线区段,使齿轮传动性能得到改善。应用变位齿轮可以避免根切,提高齿面接触强度和齿根弯曲强度,提高齿面的抗胶合能力和耐磨损性能,此外,变位齿轮还可用于配凑中心距和修复被磨损的旧齿轮。
2)通常内齿轮是用插齿刀加工的,如改变插齿刀与内齿轮坯的相对位置,便可加工出变位内齿轮。用刃磨至原始截面(x0=0)的插齿刀切内齿轮,当插齿刀向外移,使加工中心距大于标准加工中心距时,称为正变位(x>0);反之,使加工中心距小于标准加工中心距时,为负变位(x<0)。为便于分析计算,引用假想标准齿条刀具的概念,把内齿轮齿槽看成外齿轮的轮齿,如图14-1-4所示。这个外齿轮用假想标准齿条加工,当假想标准齿条刀具基准线与内齿轮分度圆移近一段距离,使中心距减小,这时的变位系数-x2(负变位)就作为内齿轮的负变位系数,但此变位系数并不代表用插齿刀加工内齿轮时的实际变位量,而只是借用外齿轮的相应公式来计算内齿轮的几何参数及大部分的尺寸。

图14-1-3 变位齿轮的齿廓
正变位时,假想齿条刀具的另一条直线(节线)与内齿轮的分度圆作纯滚动,刀具节线上的齿槽宽减小,因此加工出的内齿轮的分度圆齿厚减薄;反之,负变位时,内齿轮的分度圆齿厚增加。

图14-1-4 变位内齿轮形成原理
1.2.2.2 变位齿轮传动的分类和特点
表14-1-6 变位齿轮传动的分类和特点


注:1.有“±”或“∓”号处,上面的符号用于外啮合,下面的符号用于内啮合。
2.对直齿轮,应将表中的代号去掉下标t或n。
1.2.2.3 外啮合齿轮变位系数的选择
(1)外啮合齿轮变位系数选择的限制条件
表14-1-7列出了外啮合齿轮变位系数选择的限制条件,设计时可检验变位量是否恰当和合理。若超出这些限制条件,应考虑调整两啮合齿轮的变位量。外啮合齿轮变位系数的选择原则及方法见表14-1-11。
表14-1-7 外啮合齿轮变位系数选择的限制条件

注:本表给出的是直齿轮的公式,对斜齿轮,可用其端面参数按本表计算。
表14-1-8 最少齿数zmin及最小变位系数xmin

表14-1-9 加工标准外齿直齿轮不根切的最少齿数

注:本表中数值是按α=20°、刀具变位系数x0=0时算出的,若x0>0,z'min将略小于表中数值,若x0<0,z'min将略大于表中值。
表14-1-10 不产生顶切的最多齿数

表14-1-11 外啮合齿轮变位系数的选择原则及方法

(2)外啮合齿轮变位系数的选择方法
①利用线图选择变位系数 图14-1-5为用于齿条型刀具加工外齿轮的选择变位系数线图,它是由哈尔滨工业大学提出的变位系数选择方法。本线图用于小齿轮的齿数z1≥12。其右侧部分线图的横坐标表示一对啮合齿轮的齿数和zΣ,纵坐标表示总变位系数xΣ,图中阴影线以内为许用区,许用区内各射线为同一啮合角(如19°,20°,…,24°,25°等)时总变位系数xΣ与齿数和zΣ的函数关系。应用时,可根据所设计的一对齿轮的齿数和zΣ的大小及其他具体要求,在该线图的许用区内选择总变位系数xΣ。对于同一zΣ,当所选的xΣ越大(即啮合角α'越大)时,其传动的重合度ε就越小(即越接近于ε=1.2)。
在确定总变位系数xΣ之后,再按照该线图左侧的五条斜线分配变位系数x1和x2。该部分线图的纵坐标仍表示总变位系数xΣ,而横坐标则表示小齿轮z1的变位系数x1(从坐标原点0向左x1为正值,反之x1为负值)。根据xΣ及齿数比u=(z2/z1),即可确定x1,从而得到x2=xΣ-x1。

图14-1-5 选择变位系数线图(,α=20°)
按此线图选取并分配变位系数,可以保证:
a.齿轮加工时不根切(在根切限制线上选取xΣ,也能保证齿廓工作段不根切);
b.齿顶厚sa>0.4m(个别情况下sa<0.4m但大于0.25m);
c.重合度ε≥1.2(在线图上方边界线上选取xΣ,也只有少数情况ε=1.1~1.2);
d.齿轮啮合不干涉;
e.两齿轮最大滑动率接近或相等(η1≈η2);
f.在模数限制线(图中m=6.5,m=7,…,m=10等线)下方选取变位系数时,用标准滚刀加工该模数的齿轮不会产生不完全切削现象。若使用非标准的滚刀时,可按下式核算滚刀螺纹部分长度l是否够用
式中 da——被加工齿轮的齿顶圆直径;
αa——被加工齿轮的齿顶压力角;
α——被加工齿轮的分度圆压力角。
例1 已知某机床变速箱中的一对齿轮,z1=21,z2=33,m=2.5mm,α=20°,,中心距a'=70mm。试确定变位系数。
解 (1)根据给定的中心距a'求啮合角α'
故 α'=25°1'25″
(2)在图14-1-5中,由0点按α'=25°1'25″作射线。与zΣ=z1+z2=21+23=54处向上引的垂线相交于A1点,A1点的纵坐标值即为所求的总变位系数xΣ(见图中例1,xΣ=1.125),A1点在线图的许用区内,故可用。
(3)根据齿数比u=z2/z1=33/21=1.57,故应按线图左侧的斜线②分配变位系数x1。自A1点作水平线与斜线②交于C1点,C1点的横坐标x1即为所求的x1值,图中的x1=0.55。故x2=xΣ-x1=1.125-0.55=0.575。
例2 一对齿轮的齿数z1=17、z2=100,α=20°,,要求尽可能地提高接触强度,试选择变位系数。
解 为提高接触强度,应按最大啮合角选取总变位系数xΣ。在图14-1-5中,自zΣ=z1+z2=17+100=117处向上引垂线,与线图的上边界交于A2点,A2点处的啮合角值,即为xΣ=117时的最大许用啮合角。
A2点的纵坐标值即为所求的总变位系数xΣ=2.54(若需圆整中心距,可以适当调整总变位系数)。

图14-1-6 选择变位系数的线图
由于齿数比u=z2/z1=100/17=5.9>3.0。故应按斜线⑤分配变位系数。自A2点作水平线与斜线⑤交于C2点,则C2点的横坐标值即为x1,得x1=0.77。
故x2=xΣ-x1=2.54-0.77=1.77
例3 已知齿轮的齿数z1=15,z2=28,α=20°,,试确定高度变位系数。
解 高度变位时,啮合角α'=α=20°,总变位系数xΣ=x1+x2=0,变位系数x1可按齿数比u的大小,由图14-1-5左侧的五条斜线与xΣ=0的水平线(即横坐标轴)的交点来确定。
齿数比u=z2/z1=28/15=1.87,故应按斜线③与横坐标轴的交点来确定x1,得
x1=0.23
故x2=xΣ-x1=0-0.23=-0.23
②利用线图选择变位系数(DIN 3992德国标准) 利用图14-1-6可以按对承载能力和传动平稳性的不同要求选取变位系数,该图适用于z>10的外啮合齿轮。当所选的变位系数落在图(b)或图(c)的阴影区内时,要校验过渡曲线干涉。图(b)中的L1~L17线和图(c)中的S1~S13线是按两齿轮的齿根强度相等、主动轮齿顶的滑动速度稍大于从动轮齿顶的滑动速度、滑动率不太大的条件,综合考虑作出的。
图14-1-6的使用方法如下。
a.按照变位的目的,根据齿数和(z1+z2)。在图(a)中选出适宜的总变位系数xΣ。
b.利用图(b)(减速齿轮)或图(c)(增速齿轮)分配xΣ;按(z1+z2)/2和xΣ/2决定坐标点;过该点引与它相邻的L线或S线相应的射线;过z1和z2做垂线,与所引射线交点的纵坐标即为x1和x2。
c.当大齿轮的齿数z2>150时,可按z2=150查线图。
d.斜齿轮按zv=z/cos3β查线图,求出的是xn。
例4 已知齿轮减速装置,z1=32、z2=64、m=3,该装置传递动力较小,要求运转平稳,求其变位系数。
解 由图14-1-6(a),按运转平稳的要求,选用重合度较大的P2,按z1+z2=96,得出xΣ=-0.20(图中A点)。按表14-1-20算得a=143.39mm,若把中心距圆整为a=143.5mm,则按表14-1-20可算得xΣ=-0.164。由A点向下引垂线,在图14-1-6(b)上找出的点B。过点B引与L9和L10相应的射线,由z1=32,得出x1=0.06,则x2=xΣ-x1=-0.224。由图14-1-8查出εα=1.79,可以满足要求。
例5 已知增速齿轮装置,z1=14、z2=37、mn=5、β=12°,要求小齿轮不产生根切,且具有良好的综合性能,求其变位系数。
解 由表14-1-20算出zv1=15、zv2=39.5。因为要求综合性能比较好,因此选用图14-1-6(a)中的P4,按zv1+zv2=54.5,求出xnΣ=0.3(图中D点)。按表14-1-20算得a=131.79mm,若把中心距调整为a=132mm,则按表14-1-20可算得xnΣ=0.345。过D点向下引垂线,在图14-1-6(c)中找出的点E。过E点引与S6、S7相应的射线,由zv2=39.5得出xn2=0.19,则xn1=xnΣ-xn2=0.155。因为由zv1和xn1确定的点落在不根切线的右侧,所以不产生根切,可以满足要求。
③利用“封闭图”选择变位系数 “封闭图”是按照给定的齿数(z1和z2)及齿形参数(和α),根据上述选择变位系数的限制条件以及一些传动质量指标的要求而绘制的曲线图。利用它可以根据齿轮传动的不同要求,综合地考虑各种性能指标,比较合理地选择变位系数。封闭图比较直观,使用也很方便,但是,要有大量的封闭图才能满足一般工程设计的需要,这是该方法的主要缺点。
1.2.2.4 内啮合齿轮变位系数的选择
(1)内啮合齿轮的干涉
表14-1-12 内啮合齿轮的干涉现象和防止干涉的条件


表14-1-13 加工标准内齿轮时,不产生展成顶切的插齿刀最少齿数z0min (x2=0,x02=0,α=20°)




表14-1-16 新直齿插齿刀的基本参数和被加工内齿轮不产生径向切入顶切的最少齿数z2min

注:表中数值是按新插齿刀和内齿轮齿顶圆直径计算而得。若用旧插齿刀或内齿轮齿顶圆直径加大
时,表中数值是更安全的。
表14-1-17 不产生重叠干涉的条件

(2)内啮合齿轮变位系数的选择原则
①变位对内啮合齿轮强度的影响 采用(x2-x1)>0的内啮合齿轮传动,可以提高齿面接触强度,但由于内啮合是凸齿面与凹齿面接触,接触强度已较高,因此,提高内啮合齿轮承载能力的主要障碍往往不是接触强度的不够。
对内齿轮进行变位,可以提高其弯曲强度,但内齿轮的弯曲强度不仅与其齿数z2和变位系数x2有关,还与插齿刀齿数z0有关。当z0>18时,变位系数x2越大,弯曲强度越低,此时宜用负变位或小的正变位;当齿数z0<18时,变位系数越大,弯曲强度越高,此时宜用正变位。
由表14-1-13知,加工标准内齿轮时,z0不得小于18,若要用z0<18的插齿刀加工内齿轮以提高其弯曲强度,就需增大内齿轮的变位系数x2才能避免渐开线干涉现象。
②变位对干涉和重合度的影响 由于内齿轮的变位并不能像外啮合齿轮那样显著的提高强度,通常,内啮合齿轮变位多是为了避免加工或啮合时的干涉。
正变位内齿轮(x2>0)可以避免渐开线干涉和径向干涉;采用(x2-x1)>0的正传动内啮合,可以避免过渡曲线干涉和重叠干涉,但重合度将减小。
内啮合齿轮推荐采用高度变位,也可以采用角度变位。选择内啮合齿轮的变位系数以不使齿顶过薄、重合度不过小、不产生任何形式的干涉为限制条件。对高度变位齿轮,一般可选取
x1=x2=0.5~0.65
为综合考虑内啮合传动的各种限制条件,最好利用内啮合“封闭图”来选择变位系数。
1.3 渐开线圆柱齿轮传动的几何尺寸计算
1.3.1 标准圆柱齿轮传动的几何尺寸计算
表14-1-18 标准圆柱齿轮传动的几何尺寸计算


注:有“±”或“∓”号处,上面的符号用于外啮合,下面的符号用于内啮合。
1.3.2 高度变位齿轮传动的几何尺寸计算
表14-1-19 高度变位齿轮传动的几何尺寸计算


注:1.有“±”或“∓”号处,上面的符号用于外啮合,下面的符号用于内啮合。
2.对插齿加工的齿轮,当要求准确保证标准的顶隙时,da和df应按表14-1-20计算。
1.3.3 角度变位齿轮传动的几何尺寸计算
表14-1-20 角度变位齿轮传动的几何尺寸计算



注:1.有“±”或“∓”号处,上面的符号用于外啮合,下面的符号用于内啮合。
2.对插齿加工的齿轮,当不要求准确保证标准的顶隙时,可以近似按滚齿加工的方法计算,这对于x<1.5的齿轮,一般并不会产生很大的误差。
例1 已知外啮合直齿轮,α=20°、、z1=22、z2=65、m=4mm、x1=0.57、x2=0.63,用滚齿法加工,求其中心距和齿顶圆直径。
解 (1)中心距
由表14-1-23查得α'=23°35'。
(2)齿顶圆直径
Δy=(x2+x1)-y=(0.63+0.57)-1.1018=0.0982
da1=mz1+2(+x1-Δy)m=4×22+2×(1+0.57-0.0982)×4=99.77mm
da2=mz2+2(+x2-Δy)m=4×65+2×(1+0.63-0.0982)×4=272.25mm
例2 例1的齿轮用z0=25、的插齿刀加工,求齿顶圆直径。
解 插齿刀按中等磨损程度考虑,x0=0,da0=m(z0+)=4×(25+2×1.25)=110mm
由表14-1-23查得α'01=23°13'。
由表14-1-23查得α'02=21°59'。
df1=2a'01-da0=2×96.11-110=82.22mm
df2=2a'02-da0=2×182.41-110=254.82mm
da1=2a'-df2-2c*m=2×178.41-254.82-2×0.25×4=100mm
da2=2a'-df1-2c*m=2×178.41-82.22-2×0.25×4=272.6mm
1.3.4 齿轮与齿条传动的几何尺寸计算
表14-1-21 齿轮与齿条传动的几何尺寸计算

注:1.表中的公式是按变位齿轮给出的,对标准齿轮,将x1(或xn1)=0代入即可。
2. n1——齿轮转速,r/min;v——齿条速度,m/s。
1.3.5 交错轴斜齿轮传动的几何尺寸计算
交错轴斜齿轮传动用来传递空间两交错轴之间的运动。就单个齿轮而言,都是渐开线斜齿圆柱齿轮。交错轴斜齿轮传动的几何尺寸计算公式列于表14-1-22中。
1.3.6 几何计算中使用的数表和线图
对于压力角α=20°的圆柱齿轮传动,端面啮合角α't可由图14-1-7查得;端面重合度εα可通过图14-1-8或图14-1-9查得。对于压力角α=20°的齿轮齿条传动,其部分端面重合度εα2可由图14-1-10查得。
渐开线函数见表14-1-23,直齿插齿刀的基本参数见表14-1-24。
表14-1-22 交错轴斜齿轮传动的几何尺寸计算

注:交错轴斜齿轮实际上是两个螺旋角不相等(或螺旋角相等,但旋向相同)的斜齿轮,因此其他尺寸的计算与斜齿轮相同,可按表14-1-18进行。

图14-1-7 端面啮合角α't(α=20°)

图14-1-8 端面重合度εα
例1 已知外啮合齿轮传动,z1=18、z2=80、节圆直径d'1=91.84mm、d'2=408.16mm、齿顶圆直径da1=101.73mm、da2=418.13mm、啮合角α't=22°57',试求其端面重合度。
解 根据α't=22°57',按,
,分别由图14-1-8查得
,
,则
。
例2 (1)外啮合斜齿标准齿轮传动,z1=21、z2=74、β=12°,试求其端面重合度。
解 根据z1和β及z2和β由图14-1-9分别查出εα1=0.765,εα2=0.88(图中虚线),则εα=εα1+εα2=0.765+0.88=1.65。

图14-1-9 外啮合标准齿轮传动和高度
变位齿轮传动的端面重合度
εα(α=αn=20°、)
(2)外啮合斜齿高度变位齿轮传动,z1=21、z2=74、β=12°、xn1=0.5、xn2=-0.5,试求其端面重合度。
解 根据和
,由图14-1-9分别查出εα1=0.705、εα2=0.915,则
。
例3 已知直齿齿轮齿条传动,z1=18、x1=0.4,试求其端面重合度。
解 按,β=0°,由图14-1-9查出εα1=0.72;按xn1=0.4,β=0°,由图14-1-10查出εα2=0.586;则εα=(1+x1)×εα1+εα2=(1+0.4)×0.72+0.586=1.59。
使用方法如下:
①标准齿轮(ha1=ha2=mn):按z1和β查出εα1,按z2和β查出εα2,εα=εα1+εα2。
②高度变位齿轮[ha1=(1+xn1)mn、ha2=(1-xn1)mn]:按和β查出εα1,按
和β查出εα2,εα=(1+xn1)εα1+(1-xn1)εα2。

图14-1-10 齿轮齿条传动的部分端面重合度
εα2(α=αn=20°、)
表14-1-23 渐开线函数invα=tanα-α


例 1.inv27°15'=0.039432;inv27°17'=0.039432+×(0.039819-0.039432)=0.039587。
2.invα=0.0060460,由表查得α=14°55'。
表14-1-24 直齿插齿刀的基本参数(GB/T 6081—2001)

注:1.分度圆压力角皆为α=20°。
2.表中是在插齿刀的原始截面中的值。
1.4 渐开线圆柱齿轮齿厚的测量计算
1.4.1 齿厚测量方法的比较和应用
齿轮传动设计时,是按无侧隙啮合计算的,而实际齿轮传动时,考虑到润滑油膜和传动零件的温度变化,又要求齿轮侧面留有一定的间隙。为控制间隙的大小,在中心距一定时,主要是控制齿厚减薄量,齿轮加工中,也用测量齿厚来控制切削深度。常用的测量齿厚方法有:公法线长度W,分度圆弦齿厚,固定弦齿厚
,量柱(球)测量距M,如表14-1-25所示。
表14-1-25 齿厚测量方法的比较和应用


1.4.2 公法线长度(跨距)
卡尺卡爪跨k个轮齿与不同侧齿廓相切两点间的长度即为两侧齿廓的公法线,用W表示。公法线长度和跨测齿数计算式见表14-1-26,使用图表法查公法线长度见表14-1-27。
表14-1-26 公法线长度的计算公式

表14-1-27 使用图表法查公法线长度(跨距)

表14-1-28 公法线长度(跨距)W*(m=mn=1、α=αn=20°) mm






注:1.本表可用于外啮合和内啮合的直齿轮和斜齿轮,使用方法见表14-1-27。
2.对直齿轮z'=z,对斜齿轮。
3.对内齿轮k为跨测齿槽数。
4.黑体字是标准齿轮(x=xn=0)的跨测齿数k和公法线长度W*。
表14-1-29 值(αn=20°)

表14-1-30 假想齿数的小数部分的公法线长度(跨距)(mn=1、αn=20°) mm


图14-1-11 跨测齿数k(α=αn=20°)
表14-1-31 变位齿轮的公法线长度跨距附加量ΔW*(m=mn=1、α=αn=20°) mm

1.4.3 分度圆弦齿厚
分度圆弦齿厚即为轮齿的分度圆弧齿厚对应的弦长,用表示,其对应的弦齿高用
表示。分度圆弦齿高和分度圆弦齿厚计算公式见表14-1-32。
表14-1-32 分度圆弦齿高和分度圆弦齿厚的计算公式

注:有“±”号处,正号用于外齿轮,负号用于内齿轮。
表14-1-33 标准外齿轮的分度圆弦齿厚(或
)和分度圆弦齿高
(或
)(m=mn=1、
) mm

注:1.当模数m(或mn)≠1时,应将查得的结果乘以m(或mn)。
2.当(或
)≠1时,应将查得的弦齿高减去(1-
)或(1-
),弦齿厚不变。
3.对斜齿轮,用zv查表,zv有小数时,按插入法计算。
表14-1-34 变位外齿轮的分度圆弦齿厚(或
)和分度圆弦齿高
(或
)(α=αn=20°、m=mn=1、
) mm



注:1.本表可直接用于高度变位齿轮,对角度变位齿轮,应将表中查出的(或
)减去齿顶高变动系数Δy(或Δyn)。
2.当模数m(或mn)≠1时,应将查得的(或
)和
(或
)乘以m(或mn)。
3.对斜齿轮,用zv查表,zv有小数时,按插入法计算。
1.4.4 固定弦齿厚
固定弦齿厚是指齿轮的轮齿与基本齿廓对称相切时,两切点间的距离,用表示,其对应的弦齿高用
表示。固定弦齿高和固定弦齿厚计算式见表14-1-35。
表14-1-35 固定弦齿厚的计算公式

注:有“±”号处,+号用于外齿轮,-号用于内齿轮。
表14-1-36 标准外齿轮的固定弦齿厚(或
)和固定弦齿高
(或
)(α=αn=20°、
) mm

注:本表也可以用于内齿轮,对于齿顶圆直径按表14-1-18计算的内齿轮,应将本表中的(或
)加上
(
的计算方法见表14-1-35)。
1.4.5 量柱(球)测量距
量柱(球)测量距是将两量柱(球)放入沿直径相对的两齿槽中,测量两量柱(球)外侧面(对外齿轮)或内侧面(对内齿轮)间的距离M值。量柱(球)测量距计算式见表14-1-38。
表14-1-37 变位外齿轮的固定弦齿厚(或
)和固定弦齿高
(或
)(α=αn=20°、m=mn=1、
) mm

注:1.本表可直接用于高度变位齿轮[ha=(1+x)m或han=(1+xn)mn],对于角度变位齿轮,应将表中查出的(或
)减去齿顶高变动系数Δy(或Δyn)。
2.当模数m(或mn)≠1时,应将查得的(或
)和
(或
)乘以m(或mn)。
表14-1-38 量柱(球)测量距的计算公式


注:1.有“±”或“∓”号处,上面的符号用于外齿轮,下面的符号用于内齿轮。
2.量柱(球)直径dp按本表的方法确定后,推荐圆整成接近的标准钢球的直径(以便用标准钢球测量)。
3.直齿轮可以使用圆棒或圆球,斜齿轮使用圆球。

图14-1-12 测量外齿轮用的圆柱(球)直径(α=αn=20°)
1.5 圆柱齿轮精度
在设计渐开线圆柱齿轮时,必须按照使用要求确定其精度等级。1988年,我国首次制定和颁布了GB/T 10095—1988《渐开线圆柱齿轮精度》国家标准。通过贯彻执行,有力地促进了齿轮制造质量水平的提高。1996年之后,根据目前国际上齿轮技术的发展趋势,我国参照国际标准化组织制定的ISO 1328-1:95及ISO 1328-2:97标准,修订了GB/T 10095—1988,提出了渐开线圆柱齿轮精度的新标准(含有GB/T 10095.1—2001与GB/T 10095.2—2001两个部分),它们在具体内容上有较大的变化。在此基础上,于2008年进行了修订,提出了新的渐开线圆柱齿轮精度的标准(含有GB/T 10095.1—2008与GB/T 10095.2—2008两个部分)。本节将主要叙述其规定内容,并对与其相关的四份指导性技术文件(检验实施规范)做简要介绍,以便设计时使用。相关标准名称如下:
①GB/T 10095.1—2008 圆柱齿轮 精度制 第1部分:轮齿同侧齿面偏差的定义和允许值;
②GB/T 10095.2—2008 圆柱齿轮 精度制 第2部分:径向综合偏差与径向跳动的定义和允许值;
③GB/Z 18620.1—2008 圆柱齿轮 检验实施规范 第1部分:轮齿同侧齿面的检验;
④GB/Z 18620.2—2008 圆柱齿轮 检验实施规范 第2部分:径向综合偏差、径向跳动、齿厚和侧隙的检验;
⑤GB/Z 18620.3—2008 圆柱齿轮 检验实施规范 第3部分:齿轮坯、轴中心距和轴线平行度的检验;
⑥GB/Z 18620.4—2008 圆柱齿轮 检验实施规范 第4部分:表面结构和轮齿接触斑点的检验。
1.5.1 适用范围
1)GB/T 10095.1—2008适用于基本齿廓符合GB/T 1356《通用机械和重型机械用圆柱齿轮 标准基本齿条齿廓》规定的单个渐开线圆柱齿轮。齿距偏差、齿廓偏差、螺旋线偏差、切向综合偏差等各参数的范围和分段的上、下界限值如下(单位:mm):

标准的这一部分仅适用于单个齿轮的每个要素,不包括齿轮副。并强调指出:本部分的每个使用者,都应该非常熟悉GB/Z 18620.1《圆柱齿轮 检验实施规范 第1部分:轮齿同侧齿面的检验》所叙述的检验方法和步骤。在本部分的限制范围内,使用GB/Z 18620.1以外的技术是不适宜的。
2) GB/T 10095.2—2008适用于基本齿廓符合GB/T 1356《通用机械和重型机械用圆柱齿轮 标准基本齿条齿廓》规定的单个渐开线圆柱齿轮。

1.5.2 齿轮偏差的代号及定义
表14-1-39 齿轮各项偏差的代号及定义(GB/T 10095—2008)



图14-1-13 齿距偏差


图14-1-14 齿廓偏差

图14-1-15 螺旋线偏差

图14-1-16 切向综合偏差

图14-1-17 径向综合偏差

图14-1-18 一个齿轮(16齿)的径向跳动
1.5.3 齿轮精度等级及其选择
1.5.3.1 精度等级
1) GB/T 10095.1—2008对轮齿同侧齿面偏差规定了13个精度等级,用数字0~12由高到低的顺序排列,0级精度最高,12级精度最低。
2) GB/T 10095.2—2008对径向综合偏差规定了9个精度等级,其中4级精度最高,12级精度最低;对径向跳动规定了13个精度等级,其中0级精度最高,12级精度最低。
1.5.3.2 精度等级的选择
1)一般情况下,在给定的技术文件中,如所要求的齿轮精度为GB/T 10095.1(或GB/T 10095.2)的某个精度等级,则齿距偏差、齿廓偏差、螺旋线偏差(或径向综合偏差、径向跳动)的公差均按该精度等级。然而,按协议对工作齿面和非工作齿面可规定不同的精度等级,或对于不同的偏差项目可规定不同的精度等级。
2)径向综合偏差不一定与GB/T 10095.1中的偏差项目选用相同的精度等级。
3)选择齿轮精度时,必须根据其用途及工作条件(圆周速度、传递功率、工作时间、性能指标等)来确定。
齿轮精度等级的选择,通常有下述两种方法。
(1)计算法
①如果已知传动链末端元件的传动精度要求,可按传动链误差的传递规律,分配各级齿轮副的传动精度要求,确定齿轮的精度等级。
②根据传动装置所允许的机械振动,用“机械动力学”理论在确定装置的动态特性过程中确定齿轮的精度要求。
③根据齿轮承载能力的要求,适当确定齿轮精度的要求。
(2)经验法(表格法)
当原有的传动装置设计具有成熟经验时,新设计的齿轮传动可以参照采用相似的精度等级。目前采用的最主要的是表格法。常用齿轮的精度等级,其使用范围、加工方法见表14-1-40~表14-1-42,供选择齿轮精度等级时参考。
表14-1-40 各类机械传动中所应用的齿轮精度等级

表14-1-41 圆柱齿轮各级精度的应用范围

表14-1-42 精度等级与加工方法的关系

1.5.4 齿轮检验
1.5.4.1 齿轮的检验项目
GB/Z 18620.1—2008和GB/Z 18620.2—2008分别给出了圆柱齿轮轮齿同侧齿面的检验实施规范和径向综合偏差、径向跳动、齿厚和侧隙的检验实施规范,作为GB/T 10095.1—2008和GB/T 10095.2—2008的补充,它提供了齿轮检测方法和测量结果分析方面的建议。
各种轮齿要素的检验,需要多种测量仪器。首先必须保证在涉及齿轮旋转的所有测量过程中,齿轮实际工作的轴线应与测量过程中旋转轴线相重合。
在检验中,没有必要测量全部轮齿要素的偏差,因为其中有些要素对于特定齿轮的功能并没有明显的影响;另外,有些测量项目可以代替另一些项目。例如切向综合偏差检验能代替齿距偏差的检验,径向综合偏差能代替径向跳动检验。然而应注意的是测量项目的增减,必须由供需双方协商确定。
齿轮的齿距偏差、齿廓偏差、螺旋线偏差、切向综合偏差、径向综合偏差及径向跳动公差的检验要求见表14-1-43。
表14-1-43 齿轮偏差的检验要求


标准没有规定齿轮的公差组和检验组。对产品齿轮可采用两种不同的检验形式来评定和验收其制造质量。一种检验形式是综合检验,另一种是单项检验,但两种检验形式不能同时采用。
①综合检验 其检验项目有:与
。
②单项检验 按照齿轮的使用要求,可选择下列检验组中的一组来评定和验收齿轮精度:
a. fpt、Fp、Fα、Fβ、Fr;
b. fpt、fpk、Fp、Fα、Fβ、Fr;
c. fpt、Fr(仅用于10~12级);
d. F'i、f'i(有协议要求时)。
1.5.4.2 5级精度的齿轮公差的计算公式
5级精度齿轮的齿距偏差、齿廓偏差、螺旋线偏差、切向综合偏差、径向综合偏差及径向跳动公差计算式及使用说明见表14-1-44。
1.5.4.3 齿轮的公差
齿轮的单个齿距偏差±fpt、齿距累积总偏差Fp分别见表14-1-45和表14-1-46;齿廓总偏差Fα、齿廓形状偏差ffα、齿廓倾斜偏差±fHα分别见表14-1-47~表14-1-49;螺旋线总偏差Fβ、螺旋线形状偏差ffβ及螺旋线倾斜偏差±fHβ见表14-1-50和表14-1-51;一齿切向综合偏差f'i(测量一齿切向综合偏差f'i时,其值受总重合度εγ影响,故标准给出了f'i/K值)见表14-1-52;径向综合偏差F″i、一齿径向综合偏差f″i见表14-1-53和表14-1-54;径向跳动公差Fr见表14-1-55。
表14-1-44 齿轮精度公差计算及使用说明

表14-1-45 单个齿距偏差±fpt



表14-1-46 齿距累积总偏差Fp


表14-1-47 齿廓总偏差Fα



表14-1-48 齿廓形状偏差ffα


表14-1-49 齿廓倾斜偏差±fHα


表14-1-50 螺旋线总偏差Fβ



表14-1-51 螺旋线形状偏差ffβ和螺旋线倾斜偏差±fHβ


表14-1-52 f'i/K的比值


注:fi的公差值,由表中的值乘以K计算得出。
表14-1-53 径向综合偏差F″i


表14-1-54 一齿径向综合偏差f″i


表14-1-55 径向跳动公差Fr



1.5.5 齿轮坯的精度
有关齿轮轮齿精度(齿廓偏差、相邻齿距偏差等)的参数的数值,只有明确其特定的旋转轴线时才有意义。当测量时齿轮围绕其旋转的轴如有改变,则这些参数测量值也将改变。因此在齿轮的图纸上必须把规定轮齿公差的基准轴线明确表示出来,事实上整个齿轮的所有几何形状均以其为准。
齿轮坯的尺寸偏差和齿轮箱体的尺寸偏差对于齿轮副的接触条件和运行状况有着极大的影响。由于在加工齿轮坯和箱体时保持较紧的公差,比加工高精度的轮齿要经济得多,因此应首先根据拥有的制造设备的条件,尽量使齿轮坯和箱体的制造公差保持最小值。这种办法,可使加工的齿轮有较松的公差,从而获得更为经济的整体设计。
1.5.5.1 基准轴线与工作轴线之间的关系
基准轴线是制造者(和检验者)用来对单个零件确定轮齿几何形状的轴线,设计者应确保其精确的确定,保证齿轮相应于工作轴线的技术要求得以满足。通常,满足此要求的最常用的方法是确定基准轴线使其与工作轴线重合,即将安装面作为基准面。
在一般情况下首先需确定一个基准轴线,然后将其他所有的轴线(包括工作轴线及可能还有一些制造轴线)用适当的公差与之相联系,在此情况下,公差链中所增加的链节的影响应该考虑进去。
1.5.5.2 确定基准轴线的方法
一个零件的基准轴线一般是用基准面来确定的,有三种基本方法实现。对与轴做成一体的小齿轮可将该零件安置于两端的顶尖上,由两个中心孔确定它的基准轴线。表14-1-56给出了确定基准轴线的方法。
1.5.5.3 基准面与安装面的形状公差
基准面的要求精度取决于:
①规定的齿轮精度,基准面的极限值应确定规定得比单个轮齿的极限值紧得多;
②基准面的相对位置,一般地说,跨距占齿轮分度圆直径的比例越大,给定的公差可以越松。
基准面的精度要求,必须在零件图上规定。所有基准面的形状公差不应大于表14-1-57中所规定的数值,公差应减至最小。
表14-1-56 确定基准轴线方法


注:在与小齿轮做成一体的轴上常常有一段需安装大齿轮的地方,此安装面的公差值必须选择得与大齿轮的质量要求相适应。
表14-1-57 基准面与安装面的形状公差

注:1.齿轮坯的公差应减至能经济地制造的最小值。
2.L——较大的轴承跨距;Dd——基准面直径;b——齿宽。
工作安装面的形状公差,不应大于表14-1-57中所给定的数值。如果用其他的制造安装面时,应采用同样的限制。
1.5.5.4 工作轴线的跳动公差
如果工作安装面被选择为基准面,直接用表14-1-57中所规定的数值。当基准轴线与工作轴线并不重合时,工作安装面相对于基准轴线的跳动必须在图纸上予以控制。跳动公差不大于表14-1-58中规定的数值。
表14-1-58 安装面的跳动公差

注:齿轮坯的公差应减至能经济地制造的最小值。
1.5.6 中心距和轴线的平行度
设计者应对中心距a和轴线的平行度两项偏差选择适当的公差。公差值的选择应按其使用要求能保证相啮合轮齿间的侧隙和齿长方向正确接触。
1.5.6.1 中心距允许偏差
中心距公差是指设计者规定的允许偏差,公称中心距是在考虑了最小侧隙及两齿轮的齿顶和其相啮的非渐开线齿廓齿根部分的干涉后确定的。GB/Z 18620.3—2008中没有推荐偏差允许值。
在齿轮只是单向承载运转而不经常反转的情况下,最大侧隙的控制不是一个重要的考虑因素,此时中心距允许偏差主要取决于重合度的考虑。
在控制运动用的齿轮中,其侧隙必须控制。当轮齿上的负载常常反向时,对中心距的公差必须很仔细地考虑下列因素。
①轴、箱体和轴承的偏斜。
②由于箱体的偏差和轴承的间隙导致齿轮轴线的不一致。
③由于箱体的偏差和轴承的间隙导致齿轮轴线的错斜。
④安装误差。
⑤轴承跳动。
⑥温度的影响(随箱体和齿轮零件间的温差、中心距和材料不同而变化)。
⑦旋转件的离心伸胀。
⑧其他因素,例如润滑剂污染的允许程度及非金属齿轮材料的溶胀。
当确定影响侧隙偏差的所有尺寸的公差时,应该遵照GB/Z 18620.2中关于齿厚公差和侧隙的推荐内容。
1.5.6.2 轴线平行度偏差
由于轴线平行度偏差的影响与其向量的方向有关,对“轴线平面内的偏差”fΣδ和“垂直平面上的偏差”fΣβ作了不同的规定(见图14-1-19和表14-1-59)。每项平行度偏差是以与有关轴轴承间距离L(“轴承中间距”L)相关联的值来表示的。
1.5.7 齿厚和侧隙
GB/Z 18620.3—2008给出了渐开线圆柱齿轮齿厚和侧隙的检验实施规范,并在附录中提供了选择齿轮的齿厚公差和最小侧隙的合理方法。齿厚和侧隙相关项目的定义见表14-1-60。

图14-1-19 轴线平行度偏差
表14-1-59 轴线平行度偏差

注:一定量的垂直平面上偏差导致的啮合偏差将比同样大小的平面内偏差导致的啮合偏差大2~3倍,对这两种偏差要素要规定不同的最大推荐值。
表14-1-60 齿厚和侧隙的定义



图14-1-20 公法线长度与齿厚的允许偏差

图14-1-21 端平面上齿厚

图14-1-22 圆周侧隙jwt、法向侧隙jbn与径向侧隙jr之间的关系
1.5.7.1 侧隙
在一对装配好的齿轮副中,侧隙j是相啮齿轮齿间的间隙,它是在节圆上齿槽宽度超过相啮合的轮齿齿厚的量。侧隙可以在法向平面上或沿啮合线(见图14-1-23)测量,但它是在端平面上或啮合平面(基圆切平面)上计算和规定的。

图14-1-23 用塞尺测量侧隙(法向平面)
相啮齿的侧隙是由一对齿轮运行时的中心距以及每个齿轮的实效齿厚所控制的。所有相啮的齿轮必定要有些侧隙,以保证非工作齿面不会相互接触。运行时侧隙还随速度、温度、负载等的变动而变化。在静态可测量的条件下,必须有足够的侧隙,以保证在带负载运行于最不利的工作条件下仍有足够的侧隙。侧隙的要求量与齿轮的大小、精度、安装和应用情况有关。
(1)最小侧隙
最小侧隙jbnmin(或jwtmin)受下列因素影响。
①箱体、轴和轴承的偏斜。
②由于箱体的偏差和轴承的间隙导致齿轮轴线的不对准。
③由于箱体的偏差和轴承的间隙导致齿轮轴线的歪斜。
④安装误差,例如轴的偏心。
⑤轴承径向跳动。
⑥温度影响(箱体与齿轮零件的温度差、中心距和材料差异所致)。
⑦旋转零件的离心胀大。
⑧其他因素,例如由于润滑剂的允许污染以及非金属齿轮材料的溶胀。
如果上述因素均能很好的控制,则最小侧隙值可以很小,每一个因素均可用分析其公差来进行估计,然后可计算出最小的要求量,在估计最小期望要求值时,也需要用判断和经验,因为在最坏情况时的公差,不大可能都叠加起来。
表14-1-61列出了对工业传动装置推荐的最小侧隙,这些传动装置是用黑色金属齿轮和黑色金属的箱体制造的,工作时节圆线速度小于15m/s,其箱体、轴和轴承都采用常用的商业制造公差。
表14-1-61 对于中、大模数齿轮最小侧隙jbnmin的推荐数据 mm

表14-1-61中的数值,也可用下式进行计算,式中ai必须是一个绝对值。
如果Esns1和Esns2相等,则jbn=2Esnscosαn,小齿轮和大齿轮的切削深度和根部间隙相等,并且重合度为最大。
(2)最大侧隙
一对齿轮副中的最大侧隙jbnmax(或jwtmax),是齿厚公差、中心距变动和轮齿几何形状变异的影响之和。理论的最大侧隙发生于两个理想的齿轮按最小齿厚的规定制成,且在最松的允许中心距条件下啮合。
通常,最大侧隙并不影响传递运动的性能和平稳性,同时,实效齿厚偏差也不是在选择齿轮的精度等级时的主要考虑的因素。在这些情况下,选择齿厚及其测量方法并非关键,可以用最方便的方法。在很多应用场合,允许用较宽的齿厚公差或工作侧隙,这样做不会影响齿轮的性能和承载能力,却可以获得较经济的制造成本。当最大侧隙必须严格控制的情况下,对各影响因素必须仔细地研究,有关齿轮的精度等级、中心距公差和测量方法,必须仔细地予以规定。
1.5.7.2 齿厚公差
(1)齿厚上偏差Esns
齿厚上偏差取决于分度圆直径和允许差,其选择大体上与轮齿精度无关。
(2)齿厚下偏差Esni
齿厚下偏差是综合了齿厚上偏差及齿厚公差后获得的,由于上、下偏差都使齿厚减薄,从齿厚上偏差中应减去公差值。
(3)法向齿厚公差Tsn
法向齿厚公差的选择,基本上与轮齿的精度无关,它主要应由制造设备来控制。齿厚公差的选择要适当,太小的齿厚公差对制造成本和保持轮齿的精度方面是不利的。
1.5.7.3 齿厚偏差的测量
测得的齿厚常被用来评价整个齿的尺寸或一个给定齿轮的全部齿尺寸。它可根据测头接触点间或两条很短的接触线间距离的少数几次测量来计值,这些接触点的状态和位置是由测量法的类型(公法线、球、圆柱或轮齿卡尺)以及单个要素偏差的影响来确定的。习惯上常假设整个齿轮依靠一次或两次测量来表明其特性。
用齿厚游标卡尺测量弦齿厚的优点是可以用一个手持的量具进行测量。但测量弦齿厚也有其局限性,由于齿厚卡尺的两个测量腿与齿面只是在其顶尖角处接触而不是在其平面接触,故测量必须要由有经验的操作者进行。另一点是,由于齿顶圆柱面的精确度和同轴度的不确定性,以及测量标尺分辨率很差,使测量不甚可靠。如有可能,应采用更可靠的轮齿跨距(公法线长度)、圆柱销或球测量法来代替。
(1)公法线长度测量
当齿厚有减薄量时,公法线长度也变小。因此,齿厚偏差也可用公法线长度偏差Ebn代替。
公法线长度偏差是指公法线的实际长度与公称长度之差。GB/Z 18620.2给出了齿厚偏差与公法线长度偏差的关系式。
公法线长度上偏差
公法线长度下偏差
公法线测量对内齿轮是不适用的。另外对斜齿轮而言,公法线测量受齿轮齿宽的限制,只有满足下式条件时才可能。
式中,Wk是指在基圆柱切平面上跨k个齿(对外齿轮)或k个齿槽(对内齿轮)在接触到一个齿的右齿面和另一个齿的左齿面的两个平行平面之间测得的距离。
(2)跨球(圆柱)尺寸的测量
当斜齿轮的齿宽太窄,不允许作公法线测量时,可以用间接地检验齿厚的方法,即把两个球或圆柱(销子)置于尽可能在直径上相对的齿槽内,然后测量跨球(圆柱)尺寸。
GB/Z 18620.2—2008给出了齿厚偏差与跨距(圆柱)尺寸偏差的关系式。
偶数齿时:
跨球(圆柱)尺寸上偏差
跨球(圆柱)尺寸下偏差
奇数齿时:
跨球(圆柱)尺寸上偏差
跨球(圆柱)尺寸下偏差
式中 αMt——工作端面压力角。
1.5.8 轮齿齿面粗糙度
轮齿齿面粗糙度对齿轮的传动精度(噪声和振动)、表面承载能力(点蚀、胶合和磨损)、弯曲强度(齿根过渡曲面状况)都有一定的影响。GB/Z 18620.4—2008中给出了表面粗糙度的检验方法。
1.5.8.1 图样上应标注的数据
设计者应按照齿轮加工要求,在图样上应标出完工状态的齿轮表面粗糙度的适当数据,如图14-1-24所示。

图14-1-24 表面粗糙度的符号
1.5.8.2 测量仪器
触针式测量仪器通常用来测量表面粗糙度。可采用以下几种类型的仪器来进行测量,不同的测量方法对测量不确定度的影响有不同的特性(见图14-1-25)。

图14-1-25 仪器特性以及与制造方法相关的测量行程方向
①在被测表面上滑行的一个或一对导头的仪器(仪器有一平直的基准平面)。
②一个在具有名义表面形状的基准平面上滑行的导头。
③一个具有可调整的或可编程的与导头组合一起的基准线生成器,例如,可由一个坐标测量机来实现基准线。
④用一个无导头的传感器和一个具有较大测量范围的平直基准对形状、波纹度和表面粗糙度进行评定。
根据国家标准,触针的针尖半径应为2μm或5μm或10μm,触针的圆锥角可为60°或90°。在表面测量的报告中应注明针尖半径和触针角度。
在对表面粗糙度或波纹度进行测量时,需要用无导头传感器和一个被限定截止的滤波器,它压缩表面轮廓的长波成分或短波成分。测量仪器仅适用于某些特定的截止波长,表14-1-62给出了适当的截止波长的参考值。必须要认真选择合适的触针针尖半径、取样长度和截止滤波器,见GB/T 10610和ISO 16610—21—2011,否则测量中就会出现系统误差。
根据波纹度、加工纹理方向和测量仪器的影响的考虑,可能要选择一种不同的截止值。
表14-1-62 滤波和截止波长

1.5.8.3 齿轮齿面表面粗糙度的测量
在测量表面粗糙度时,触针的轨迹应与表面加工纹理的方向相垂直,见图14-1-25和图14-1-26中所示方向,测量还应垂直于表面,因此,触针应尽可能紧跟齿面的弯曲的变化。

图14-1-26 齿根过渡曲面粗糙度的测量
在对轮齿齿根的过渡区表面粗糙度测量时,整个方向应与螺旋线正交,因此,需要使用一些特殊的方法。图14-1-26中表示了一种适用的测量方法,在触针前面的传感器头部有一半径为r(小于齿根过渡曲线的半径R)的导头,安装在一根可旋转的轴上,当该轴转过角度约100°时,触针的针尖描绘出一条同齿根过渡区接近的圆弧。当齿根过渡区足够大,并且该装置仔细的定位时方可进行表面粗糙度测量。导头直接作用于表面,应使半径r大于50λc(截止波长),以避免因导头引起的测量不确定度。
使用导头形式的测量仪器进行测量还有另一种办法,选择一种适当的铸塑材料(如树脂等)制作一个相反的复制品。当对较小模数齿轮的齿根过渡部分的表面粗糙度进行测量时,这种方法是特别有用的。在使用这种方法时,应记住在评定过程中齿廓的记录曲线的凸凹是相反的。
(1)评定测量结果
直接测得的表面粗糙度参数值,可直接与规定的允许值比较。
参数值通常是按沿齿廓取的几个接连的取样长度上的平均值确定的,但是应考虑到表面粗糙度会沿测量行程有规律地变化,因此,确定单个取样长度的表面粗糙度值,可能是有益的。为了改进测量数值统计上的准确性,可从几个平行的测量迹线计算其算术平均值。
为了避免使用滤波器时评定长度的部分损失,可以在没有标准滤波过程的情况下,在单个取样长度上评定粗糙度。图14-1-27为消除形状成分等,将(没有滤波器)轨迹轮廓细分为短的取样长度l1、l2、l3等所产生的滤波效果。为了同标准方法的滤波结果相比较,取样长度应与截止值λc为同样的值。

图14-1-27 取样长度和滤波的影响
(2)参数值
规定的参数值应优先从表14-1-63和表14-1-64中所给出的范围中选择,无论是Ra还是Rz都可作为一种判断依据,但两者不应在同一部分使用。
表14-1-63 算术平均偏差Ra的推荐极限值 μm

表14-1-64 微观不平度十点高度Rz的推荐极限值 μm

注:表14-1-63和表14-1-64中关于Ra和Rz相当的表面状况等级并不与特定的制造工艺相应,这一点特别对于表中1级到4级的表列值。
1.5.9 轮齿接触斑点
检验产品齿轮副在其箱体内所产生的接触斑点,可用于评估轮齿间载荷分布。产品齿轮和测量齿轮的接触斑点,可用于评估装配后齿轮的螺旋线和齿廓精度。
1.5.9.1 检测条件
①精度 产品齿轮和测量齿轮副轻载下接触斑点,可以从安装在机架上的齿轮相啮合得到。为此,齿轮轴线的不平行度,在等于产品齿轮齿宽的长度上的数值不得超过0.005mm。同时也要保证测量齿轮的齿宽不小于产品齿轮的齿宽,通常这意味着对于斜齿轮需要一个专用的测量齿轮。相配的产品齿轮副的接触斑点也可以在相啮合的机架上获得。
②载荷分布 产品齿轮副在其箱体内的轻载接触斑点,有助于评估载荷的可能分布,在其检验过程中,齿轮的轴颈应当位于它们的工作位置,这可以通过对轴承轴颈加垫片调整来达到。
③印痕涂料 适用的印痕涂料有装配工的蓝色印痕涂料和其他专用涂料,油膜层厚度为0.006~0.012mm。
④印痕涂料层厚度的标定 在垂直于切平面的方向上以一个已知小角度移动齿轮的轴线,即在轴承座上加垫片并观察接触斑点的变化,标定工作应该有规范地进行,以确保印痕涂料、测试载荷和操作工人的技术都不改变。
⑤测试载荷 用于获得轻载齿轮接触斑点所施加的载荷,应恰好够保证被测齿面保持稳定地接触。
⑥记录测试结果 接触斑点通常以画草图、照片、录像记录下来,或用透明胶带覆盖接触斑点上,再把粘住接触斑点的涂料的胶带撕下来,贴在优质的白卡片上。
要完成以上操作的人员,应训练正确地操作,并定期检查他们的效果,以确保操作效能的一致性。
1.5.9.2 接触斑点的判断
接触斑点可以给出齿长方向配合不准确的程度,包括齿长方向的不准确配合和波纹度,也可以给出齿廓不准确性的程度,必须强调的是,做出的任何结论都带有主观性,只能是近似的并且依赖于有关人员的经验。
(1)与测量齿轮相啮的接触斑点
图14-1-28~图14-1-31所示的是产品齿轮与测量齿轮对滚产生的典型的接触斑点示意图。

图14-1-28 典型的规范,接触近似为:齿宽b的80%,有效齿面高度h的70%,齿端修薄

图14-1-29 齿长方向配合正确,有齿廓偏差

图14-1-30 波纹度

图14-1-31 有螺旋线偏差、齿廓正确,有齿端修薄
(2)齿轮精度和接触斑点
图14-1-32和表14-1-65、表14-1-66给出了在齿轮装配后(空载)检测时,所预计的在齿轮精度等级和接触斑点分布之间关系的一般指示,但不能理解为证明齿轮精度等级的可替代方法。实际的接触斑点不一定同图14-1-32中所示的一致,在啮合机架上所获得的齿轮检查结果应当是相似的。图14-1-32和表14-1-65、表14-1-66对齿廓和螺旋线修形的齿面是不适用的。

图14-1-32 接触斑点分布的示意图
表14-1-65 斜齿轮装配后的接触斑点

表14-1-66 直齿轮装配后的接触斑点

1.5.10 新旧标准对照
表14-1-67 新旧标准对照



1.6 齿条精度
齿条是圆柱齿轮分度圆直径为无限大的一部分,端面齿廓和螺旋线均为直线。齿条副是圆柱齿轮和齿条的啮合,形成圆周运动与直线运动的转换。GB/T 10096—1988齿条精度国家标准是由GB/T 10095—1988渐开线圆柱齿轮精度国家标准派生配套而形成的。目前因GB/T 10095—1988标准是等效采用已被作废的ISO 1328—1975国际标准,被等同采用ISO 1328-1:1995和ISO 1328-2:1997国际圆柱齿轮精度标准的国家标准GB/T 10095.1—2008和GB/T 10095.2—2008替代,因此GB/T 10096—1988齿条精度国家标准失去现行实用的意义。
国际ISO和德国DIN、美国INSI/AGMA等都没有专门的齿条精度标准,他们的齿条精度由圆柱齿轮精度标准体现。齿条副的圆柱齿轮和齿条是相同的偏差允许值,若圆柱齿轮的参数为未知,则齿条的精度等级以齿条长度折算为分度圆的圆周值进行计值。
1.7 渐开线圆柱齿轮承载能力计算
本节主要根据GB/T 3480—1997渐开线圆柱齿轮承载能力计算方法和GB/T 10063—1988通用机械渐开线圆柱齿轮承载能力简化计算方法,初步确定渐开线圆柱齿轮尺寸。齿面接触强度核算和轮齿弯曲强度核算的方法,适合于钢和铸铁制造的、基本齿廓符合GB/T 1356的内、外啮合直齿、斜齿和人字齿(双斜齿)圆柱齿轮传动,基本齿廓与GB/T 1356相类似但个别齿形参数值略有差异的齿轮,也可参照本法计算其承载能力。
由于GB/T 3480—1997精度质量是GB/T 10095—1988标准,现已由等同采用ISO 1328-1:1995的GB/T 10095.1—2008和等同采用ISO 1328-2:1997的GB/T 10095.2—2008替代GB/T 10095—1988标准,因此与ISO 6336比较可达等效水平。最近又将ISO 6336-5:2003等同到了GB/T 3480.5—2008。本手册以下部分主要取材于GB/T 3480—1997,试验齿轮的接触疲劳极限和弯曲疲劳极限参照GB/T 3480.5—2008,各专业领域请参照各自专业标准。
1.7.1 可靠性与安全系数
齿轮工作的可靠性要求是根据其重要程度、工作要求和维修难易等方面的因素综合考虑决定的。不同的使用场合对齿轮有不同的可靠度要求。一般可分为下述几类情况。
①低可靠度要求 齿轮设计寿命不长,对可靠度要求不高的易于更换的不重要齿轮,或齿轮设计寿命虽不短,但对可靠性要求不高。这类齿轮可靠度可取为90%。
②一般可靠度要求 通用齿轮和多数的工业应用齿轮,其设计寿命和可靠性均有一定要求。这类齿轮工作可靠度一般不大于99%。
③较高可靠度要求 要求长期连续运转和较长的维修间隔,或设计寿命虽不很长但可靠性要求较高的高参数齿轮,一旦失效可能造成较严重的经济损失或安全事故,其可靠度要求高达99.9%。
④高可靠度要求 特殊工作条件下要求可靠度很高的齿轮,其可靠度要求甚至高达99.99%以上。
目前,可靠性理论虽已开始用于一些机械设计,且已表明只用强度安全系数并不能完全反映可靠性水平,但是在齿轮设计中将各参数作为随机变量处理尚缺乏足够数据。所以,标准GB/T 3480仍将设计参数作为确定值处理,仍然用强度安全系数或许用应力作为判据,而通过选取适当的安全系数来近似控制传动装置的工作可靠度要求。考虑到计算结果和实际情况有一定偏差,为保证所要求的可靠性,必须使计算允许的承载能力有必要的安全裕量。显然,所取的原始数据越准确,计算方法越精确,计算结果与实际情况偏差就越小,所需的安全裕量就可以越小,经济性和可靠性就更加统一。
具体选择安全系数时,需注意以下几点。
①本节所推荐的齿轮材料疲劳极限是在失效概率为1%时得到的,可靠度要求高时,安全系数应取大些;反之,则可取小些。
②一般情况下弯曲安全系数应大于接触安全系数,同时断齿比点蚀的后果更为严重,也要求弯曲强度的安全裕量应大于接触强度安全裕量。
③不同的设计方法推荐的最小安全系数不尽相同,设计者应根据实际使用经验或适合的资料选定。如无可用资料时,可参考表14-1-106选取。
④对特定工作条件下可靠度要求较高的齿轮安全系数取值,设计者应做详细分析。
⑤不同使用场合评定齿轮失效的准则各异,最小安全系数的选取也应有所不同。
⑥最小安全系数的选取,建议由设计制造部门与用户协商确定。
1.7.2 轮齿受力分析
渐开线圆柱齿轮受力分析如图14-1-33所示,轮齿上所受的作用力可用表14-1-68所列的公式计算。

图14-1-33 渐开线圆柱齿轮受力分析
表14-1-68 圆柱齿轮轮齿上的作用力计算

注:1. 代号意义及单位:
T1(或2)——小齿轮(或大齿轮)的额定转矩,N·m;
n1(或2)——小齿轮(或大齿轮)的转速,r/min;
PkW——额定功率,kW;
PPS——额定功率,hp(PS);
其余代号和单位同前。
2. 将表中的d用节圆直径d'代入,即可计算得到节圆上的作用力F't、F'r、F'x和F'n。
1.7.3 齿轮主要尺寸的初步确定
齿轮传动的主要尺寸可按下述任何一种方法初步确定。
①参照已有的相同或类似机械的齿轮传动,用类比法确定。
②根据具体工作条件、结构、安装及其他要求确定。
③按齿面接触强度的计算公式确定中心距a或小齿轮的直径d1,根据弯曲强度计算公式确定模数m。对闭式传动,应同时满足接触强度和弯曲强度的要求;对开式传动,一般只按弯曲强度计算,并将由公式算得的m(或mn)值增大10%~20%。
主要尺寸初步确定之后,原则上应进行强度校核,并根据校核计算的结果酌情调整初定尺寸。对于低精度的、不重要的齿轮,也可以不进行强度校核计算。
1.7.3.1 齿面接触强度
在初步设计齿轮时,根据齿面接触强度(GB/T 10063—1988),可按下列公式之一估算齿轮传动的尺寸
对于钢对钢配对的齿轮副,常系数值Aa、Ad见表14-1-69,对于非钢对钢配对的齿轮副,需将表中值乘以修正系数,修正系数列于表14-1-70。以上二式中的“+”用于外啮合,“-”用于内啮合。
齿宽系数按表14-1-71圆整。“+”号用于外啮合,“-”号用于内啮合。ψd的推荐值见表14-1-72。
载荷系数K,常用值K=1.2~2,当载荷平稳,齿宽系数较小,轴承对称布置,轴的刚性较大,齿轮精度较高(6级以上),以及齿的螺旋角较大时取较小值;反之取较大值。
许用接触应力σHP,推荐按下式确定
表14-1-69 钢对钢配对齿轮副的Aa、Ad值

表14-1-70 修正系数

式中 σHlim——试验齿轮的接触疲劳极限,见1.7.4.1节中的(13)。取σHlim1和σHlim2中的较小值。
表14-1-71 齿宽系数ψa

注:对人字齿轮应为表中值的2倍。
表14-1-72 齿宽系数ψd的推荐范围

注:1.括号内的数值用于人字齿轮,其齿宽是两个半人字齿轮齿宽之和。
2.齿宽与承载能力成正比,当载荷一定时,增大齿宽可以减小中心距,但螺旋线载荷分布的不均匀性随之增大。在必须增大齿宽的时候,为避免严重的偏载,齿轮和齿轮箱应具有较高的精度和足够的刚度。
3.,对中间有退刀槽(宽度为l)的人字齿轮:
。
4.螺旋线修形的齿轮,ψd值可大于表列的推荐范围。
1.7.3.2 齿根弯曲强度
在初步设计齿轮时,根据齿根弯曲强度(GB/T 10063—1988),可按下列公式估算齿轮的法向模数
(mm)
系数Am列于表14-1-73。
表14-1-73 系数Am值

许用齿根应力σFP,推荐按下式确定:
轮齿单向受力
轮齿双向受力或开式齿轮
式中 σFlim——试验齿轮的弯曲疲劳极限,见1.7.4.2节中的(8);
YFs——复合齿廓系数,YFs=YFaYSa;
σFE——齿轮材料的弯曲疲劳强度的基本值,见1.7.4.2节中的(8)。
1.7.4 疲劳强度校核计算
本节介绍GB/T 3480—1997渐开线圆柱齿轮承载能力计算方法。该方法适用于钢、铸铁制造的,基本齿廓符合GB/T 1356—2001的内、外啮合直齿、斜齿和人字齿(双斜齿)圆柱齿轮传动。
1.7.4.1 齿面接触强度核算
GB/T 3480—1997把赫兹应力作为齿面接触应力的计算基础,并用来评价接触强度。赫兹应力是齿面间应力的主要指标,但不是产生点蚀的唯一原因。例如在应力计算中未考虑滑动的大小和方向、摩擦因数及润滑状态等,这些都会影响齿面的实际接触应力。
齿面接触强度核算时,取节点和单对齿啮合区内界点的接触应力中的较大值,小轮和大轮的许用接触应力σHP要分别计算。
在任何啮合瞬间,大、小齿轮的接触应力总是相等的。齿面最大接触应力一般出现在小轮单对齿啮合区内界点B、节点C及大轮单对齿啮合区内界点D这三个特征点之一处上(B、C、D三点见图14-1-34)。由于上述除赫兹应力外的其他因素影响,产生点蚀危险的实际接触应力通常出现在C、D点或其间(对大齿轮),或在C、B点或其间(对小齿轮)。基于节点区域系数ZH计算的节点C处接触应力基本值σH0,当单对齿啮合区内界点处的应力超过节点处的应力时,即ZB或ZD大于1.0时,在确定大、小齿轮计算应力σH时应乘以ZD、ZB予以修正;当ZB或ZD不大于1.0时,取其值为1.0。
表14-1-74中的公式,适用于端面重合度εα<2.5的齿轮副。对于斜齿轮,当纵向重合度εβ≥1时,一般节点接触应力较大;当纵向重合度εβ<1时,接触应力由与斜齿轮齿数相同的直齿轮的σH和εβ=1的斜齿轮的σH按εβ作线性插值确定。
(1)齿面接触强度核算公式
齿面接触强度校核的强度条件和计算公式见表14-1-74。

图14-1-34 节点C及单对齿啮区B、D处的曲率半径
表14-1-74 齿面接触强度核算的公式

(2)名义切向力Ft
可按齿轮传递的额定转矩或额定功率按表14-1-68中公式计算。变动载荷时,如果已经确定了齿轮传动的载荷图谱,则应按当量转矩计算分度圆上的切向力,见1.7.4.4。
(3)使用系数KA
使用系数KA是考虑由于齿轮啮合外部因素引起
附加动载荷影响的系数。这种外部附加动载荷取决于原动机和从动机的特性、轴和联轴器系统的质量和刚度以及运行状态。使用系数应通过精密测量或对传动系统的全面分析来确定。当不能实现时,可参考表14-1-75查取。
原动机及工作机的工作特性示例分别见表14-1-76和表14-1-77。
表14-1-75 使用系数KA

注:1.对于增速传动,根据经验建议取上表值的1.1倍。
2.当外部机械与齿轮装置之间挠性连接时,通常KA值可适当减小。
3.数据主要适用于在非共振区运行的工业齿轮和高速齿轮,采用推荐值时,至少应取最小弯曲强度安全系数SFmin=1.25。
4.某些应用场合的使用系数KA值可能远高于表中值(甚至高达10),选用时应全面分析工况和连接结构,如在运行中存在非正常的重载、大的启动转矩、重复的中等或严重冲击,应当核算其有限寿命下承载能力和静强度。
表14-1-76 原动机工作特性示例

表14-1-77 工作机工作特性示例

①额定转矩=最大切削、压制、冲击转矩。②额定载荷为最大启动转矩。③额定载荷为最大轧制转矩。④转矩受限流器限制。⑤带钢的频繁破碎会导致KA上升到2.0。
(4)动载系数KV
动载系数KV是考虑齿轮制造精度、运转速度对轮齿内部附加动载荷影响的系数,定义为
影响动载系数的主要因素有:由基圆齿距偏差和齿廓偏差产生的传动误差;节线速度;转动件的惯量和刚度;轮齿载荷;轮齿啮合刚度在啮合循环中的变化。其他的影响因素还有:跑合效果、润滑油特性、轴承及箱体支承刚度及动平衡精度等。
在通过实测或对所有影响因素作全面的动力学分析来确定包括内部动载荷在内的最大切向载荷时,可取KV等于1。不能实现时,可用下述方法之一计算动载系数。
①一般方法 KV的计算公式见表14-1-78。
表14-1-78 运行转速区间及其动载系数KV的计算公式

注:1.表中各式均将每一齿轮副按单级传动处理,略去多级传动的其他各级的影响。非刚性连接的同轴齿轮,可以这样简化,否则应按表14-1-81中第2类型情况处理。
2.亚临界区中当(FtKA)/b<100N/mm时,;其他情况时,Ns=0.85。
3.表内各式中:
N——临界转速比,见表14-1-79;
CV1——考虑齿距偏差的影响系数;
CV2——考虑齿廓偏差的影响系数;
CV3——考虑啮合刚度周期变化的影响系数;
CV4——考虑啮合刚度周期性变化引起齿轮副扭转
共振的影响系数;
CV5——在超临界区内考虑齿距偏差的影响系数;
CV6——在超临界区内考虑齿廓偏差的影响系数;
CV7——考虑因啮合刚度的变动,在恒速运行时与轮齿弯曲变形产生的分力有关的系数;
Bp,Bf,Bk——分别考虑齿距偏差、齿廓偏差和轮齿修缘对动载荷影响的无量纲参数。其计算公式见表14-1-83。
CV1~CV7按表14-1-82的相应公式计算或由图14-1-35查取。
表14-1-79 临界转速比N

表14-1-80 行星传动齿轮的诱导质量mred

表14-1-81 较特殊结构形式的齿轮的诱导质量mred

表14-1-82 CV系数值


图14-1-35 系数CV1~CV7的数值
表14-1-83 参数BP、Bf、Bk的计算公式

②简化方法 KV的简化法基于经验数据,主要考虑齿轮制造精度和节线速度的影响。KV值可由图14-1-36选取。该法适用于缺乏详细资料的初步设计阶段时KV的取值。
对传动精度系数C≤5的高精度齿轮,在良好的安装和对中精度以及合适的润滑条件下,KV为1.0~1.1。C值可按表14-1-84中的公式计算。
对其他齿轮,KV值可按图14-1-36选取,也可由表14-1-84的公式计算。
(5)螺旋线载荷分布系数KHβ
螺旋线载荷分布系数KHβ是考虑沿齿宽方向载荷分布不均匀对齿面接触应力影响的系数:
式中 ωmax——单位齿宽最大载荷,N/mm;
ωm——单位齿宽平均载荷,N/mm;
Fm——分度圆上平均计算切向力,N。

图14-1-36 动载系数KV
注:曲线6~12为齿轮传动精度系数。
表14-1-84 KV的简化计算公式

影响螺旋线载荷分布的主要因素有:
①齿轮副的接触精度,它主要取决于齿轮加工误差、箱体镗孔偏差、轴承的间隙和误差、大小轮轴的平行度、跑合情况等;
②轮齿啮合刚度、齿轮的尺寸结构及支承型式及轮缘、轴、箱体及机座的刚度;
③轮齿、轴、轴承的变形,热膨胀和热变形(这对高速宽齿轮尤其重要);
④切向、轴向载荷及轴上的附加载荷(例如带或链传动);
⑤设计中有无元件变形补偿措施(例如齿向修形)。
由于影响因素众多,确切的载荷分布系数应通过实际的精密测量和全面分析已知的各影响因素的量值综合确定。如果通过测量和检查能确切掌握轮齿的接触情况,并作相应地修形,经螺旋线修形补偿的高精度齿轮副,在给定的运行条件下,其螺旋线载荷接近均匀分布,KHβ接近于1。在无法实现时,可按下述
两种方法之一确定。
①一般方法 按基本假定和适用范围计算KHβ。基本假定和适用范围:
a.沿齿宽将轮齿视为具有啮合刚度cγ的弹性体,载荷和变形都呈线性分布;
b.轴齿轮的扭转变形按载荷沿齿宽均布计算,弯曲变形按载荷集中作用于齿宽中点计算,没有其他额外的附加载荷;
c.箱体、轴承、大齿轮及其轴的刚度足够大,其变形可忽略;
d.等直径轴或阶梯轴,dsh为与实际轴产生同样弯曲变形量的当量轴径;
e.轴和小齿轮的材料都为钢;小齿轮轴可以是实心轴或空心轴(其内径应<0.5dsh),齿轮的结构支承形式见表14-1-89,偏心距s/l≤0.3。
KHβ的计算公式见表14-1-85,当KHβ>1.5时,通常应采取措施降低KHβ值。
表14-1-85 KHβ计算公式

①yβ、xβ分别为螺旋线跑合量(μm)和螺旋线跑合系数,用表14-1-86公式计算。
②fma为制造、安装误差产生的啮合螺旋线偏差分量(μm),用表14-1-87公式计算。
③fβ6为GB/T 10095.1—2008或ISO 1328-1:1995规定的6级精度的螺旋线总偏差的允许值Fβ(μm)。
④γ为小齿轮结构尺寸系数,用表14-1-88公式计算。
表14-1-86 yβ、xβ计算公式

注:1.σHlim——齿轮接触疲劳极限值,N/mm2,见本节(13)。
2.当大小齿轮材料不同时,yβ=(yβ1+yβ2)/2,xβ=(xβ1+xβ2)/2,式中下标1、2分别表示小、大齿轮。
表14-1-87 fma计算公式 μm

表14-1-88 小齿轮结构尺寸系数γ

注:l——轴承跨距,mm;s——小轮齿宽中点至轴承跨距中点的距离,mm;d1——小轮分度圆直径,mm;dsh——小轮轴弯曲变形当量直径,mm;k'——结构系数,见表14-1-89;bB——单斜齿轮宽度,mm。
表14-1-89 小齿轮结构系数k'

注:1.对人字齿轮或双斜齿轮,图中实、虚线各代表半边斜齿轮中点的位置,s按用实线表示的变形大的半边斜齿轮的位置计算,b取单个斜齿轮宽度。
2.图中,d1/dsh≥1.15为刚性轴,d1/dsh<1.15为非刚性轴。通常采用键连接的套装齿轮都属非刚性轴。
3.齿轮位于轴承跨距中心时(s≈0),最好按下面典型结构齿轮的公式计算KHβ。
4.当采用本表以外的结构布置形式或s/l超过本表规定的范围,或轴上作用有带轮或链轮之类的附加载荷时,推荐做进一步的分析。
②典型结构齿轮的KHβ 适用条件:符合①中a、b、c,并且小齿轮直径和轴径相近,轴齿轮为实心或空心轴(内孔径应小于0.5 dsh),对称布置在两轴承之间(s/l≈0);非对称布置时,应把估算出的附加弯曲变形量加到fma上。
符合上述条件的单对齿轮、轧机齿轮和简单行星传动的KHβ值可按表14-1-90~表14-1-92中的公式计算。
表14-1-90 单对齿轮KHβ的计算公式

注:1.本表各公式适用于全部转矩从轴的一端输入的情况,如同时从轴的两端输入或双斜齿轮从两半边斜齿轮的中间输入,则应做更详细的分析。
2.部分修形指只补偿扭转变形的螺旋线修形;完全修形指同时可补偿弯曲、扭转变形的螺旋线修形。
3.B——包括空刀槽在内的双斜齿全齿宽,mm;bB——单斜齿轮宽度,mm,对因结构要求而采用超过一般工艺需要的大齿轮宽度的双斜齿轮,应采用一般方法计算;Fm——分度圆上平均计算切向力,N。
表14-1-91 轧机齿轮的KHβ计算公式

注:1.如不修形,按双斜齿或人字齿轮公式计算的KHβ>2,应核查设计,最好用更精确的方法重新计算。
2.B为包括空刀槽在内的双斜齿宽度,mm;bB为单斜齿轮宽度,mm。
3.k表示当采用一对轴齿轮,u=1,功率分流,被动齿轮传递k%的转矩,(100-k)%的转矩由主动齿轮的轴端输出,两齿轮皆对称布置在两端轴承之间。
表14-1-92 行星传动齿轮KHβ的计算公式

注:1.Ⅰ、Ⅱ表示行星轮及其轴承在行星架上的安装形式:Ⅰ—轴承装在行星轮上,转轴刚性固定在行星架上;Ⅱ—行星轮两端带轴颈的轴齿轮,轴承装在转架上。
2.ds——太阳轮分度圆直径,mm;dp——行星轮分度圆直径,mm;lp——行星轮轴承跨距,mm;B——包括空刀槽在内的双斜齿宽度,mm;bB——单斜齿轮宽度,mm;B、bB见表14-1-91。
3.Fm=FtKAKVKγ/np
Kγ——行星传动不均载系数;np——行星轮个数。
③简化方法 适用范围如下。
a.中等或较重载荷工况:对调质齿轮,单位齿宽载荷Fm/b为400~1000N/mm;对硬齿面齿轮,Fm/b为800~1500N/mm。
b.刚性结构和刚性支承,受载时两轴承变形较小可忽略;齿宽偏置度s/l(见表14-1-89)较小,符合表14-1-93和表14-1-94限定范围。
c.齿宽b为50~400mm,齿宽与齿高比b/h为3~12,小齿轮宽径比b/d1对调质的应小于2.0,对硬齿面的应小于1.5。
d.轮齿啮合刚度cγ为15~25N/(mm·μm)。
e.齿轮制造精度对调质齿轮为5~8级,对硬齿面齿轮为5~6级;满载时齿宽全长或接近全长接触(一般情况下未经螺旋线修形)。
f.矿物油润滑。
符合上述范围齿轮的KHβ值可按表14-1-93和表14-1-94中的公式计算。
表14-1-93 调质齿轮KHβ的简化计算公式

表14-1-94 硬齿面齿轮KHβ的简化计算公式

①GB/T 3480-1997误为0.47×10-3。
(6)齿间载荷分配系数KHα、KFα
齿间载荷分配系数是考虑同时啮合的各对轮齿间载荷分配不均匀影响的系数。影响齿间载荷分配系数的主要因素有:受载后轮齿变形;轮齿制造误差,特别是基节偏差;齿廓修形,跑合效果等。
应优先采用经精密实测或对所有影响因素精确分析得到的齿间载荷分配系数。一般情况下,可按下述方法确定。
①一般方法 KHα、KFα按表14-1-95中的公式计算。
②简化方法 简化方法适用于满足下列条件的工业齿轮传动和类似的齿轮传动:钢制的基本齿廓符合GB/T 1356的外啮合和内啮合齿轮;直齿轮和β≤30°的斜齿轮;单位齿宽载荷FtH/b≥350N/mm(当FtH/b≥350N/mm时,计算结果偏于安全;当FtH/b<350N/mm时,因KHα、KFα的实际值较表值大,计算结果偏于不安全)。
KHα可按表14-1-97查取。
表14-1-95 KHα、KFα计算公式

①对于斜齿轮,如计算得到的KHα值过大,则应调整设计参数,使得KHα及KFα不大于εα。同时,公式KHα、KFα仅适用于齿轮基节偏差在圆周方向呈正常分布的情况。
表14-1-96 齿廓跑合量yα

注:1.fpb——齿轮基节偏差,μm;σHlim——齿轮接触疲劳极限,N/mm2,见本节(13)。
2.当大、小齿轮的材料和热处理不同时,其齿廓跑合量可取为相应两种材料齿轮副跑合量的算术平均值。
表14-1-97 齿间载荷分配系数KHα、KFα

注:1.经修形的6级精度硬齿面斜齿轮,取KHα=KFα=1。
2.若表中εα/cos2βb≥1.4的计算值,则取
。
3.Zε见本节(11),Yε见1.7.4.2中(6)。
4.硬齿面和软齿面相啮合的齿轮副,齿间载荷分配系数取平均值。
5.小齿轮和大齿轮精度等级不同时,则按精度等级较低的取值。
6.本表也可以用于灰铸铁和球墨铸铁齿轮的计算。
(7)轮齿刚度——单对齿刚度c'和啮合刚度cγ
轮齿刚度定义为使一对或几对同时啮合的精确轮齿在1mm齿宽上产生1μm挠度所需的啮合线上的载荷。直齿轮的单对齿刚度c'为一对轮齿的最大刚度,斜齿的c'为一对轮齿在法截面内的最大刚度。啮合刚度cγ为端面内轮齿总刚度的平均值。
影响轮齿刚度的主要因素有:轮齿参数、轮体结构、法截面内单位齿宽载荷、轴毂连接结构和形式、齿面粗糙度和齿面波度、齿向误差、齿轮材料的弹性模量等。
轮齿刚度的精确值可由实验测得或由弹性理论的有限元法计算确定。在无法实现时,可按下述方法之一确定。
①一般方法 对于基本齿廓符合GB/T 1356—2001、
单位齿宽载荷KAFt/b≥100N/mm、轴-毂处圆周方向传力均匀(小齿轮为轴齿轮形式、大轮过盈连接或花键连接)、钢质直齿轮和螺旋角β≤45°的外啮合齿轮,c'和cγ可按表14-1-98给出的公式计算。对于不满足上述条件的齿轮,如内啮合、非钢质材料的组合、其他形式的轴-毂连接、单位齿宽载荷KAFt/b<100N/mm的齿轮,也可近似应用。
②简化方法 对基本齿廓符合GB/T 1356的钢制刚性盘状齿轮,当β≤30°,1.2<εα<1.9且KAFt/b≥100N/mm时,取c'=14N/(mm·μm)、cγ=20N/(mm·μm)。非实心齿轮的c'和cγ用表14-1-98中轮坯结构系数CR折算。其他基本齿廓的齿轮的c'、cγ可用表14-1-98中基本齿廓系数CB折算。非钢对钢配对的齿轮的c'、cγ可用表14-1-98中cγ计算式折算。
表14-1-98 c'、cγ计算公式

注:1.当。
2.一对齿轮副中,若一个齿轮为平键连接,配对齿轮为过盈或花键连接,由表中公式计算的c'增大5%;若两个齿轮都为平键连接,由公式计算的c'增大10%。
3.啮合刚度cγ的计算式适用于直齿轮和螺旋角β≤30°的斜齿轮。对εα<1.2的直齿轮的cγ,需将计算值减小10%。
4.zn1、zn2为小、大(斜)齿轮的当量齿数,分别见表14-1-18中的zv1、zv2。
(8)小轮及大轮单对齿啮合系数ZB、ZD
εα≤2时的单对齿啮合系数ZB是把小齿轮节点C处的接触应力折算到小轮单对齿啮合区内界点B处的接触应力的系数;ZD是把大齿轮节点C处的接触应力折算到大轮单对齿啮合区内界点D处的接触应力的系数,见图14-1-34。
单对齿啮合系数由表14-1-99公式计算与判定。
表14-1-99 ZB、ZD的确定

(9)节点区域系数ZH
节点区域系数ZH是考虑节点处齿廓曲率对接触应力的影响,并将分度圆上切向力折算为节圆上法向力的系数。
式中
(“+”用于外啮合,“-”用于内啮合)
对于法面压力角αn为20°、22.5°、25°的内、外啮合齿轮,ZH也可由图14-1-37、图14-1-38和图14-1-39根据(x1+x2)/(z1+z2)及螺旋角β查得。
(10)弹性系数ZE
弹性系数ZE是用以考虑材料弹性模量E和泊松比ν对赫兹应力的影响,其数值可按实际材料弹性模
量E和泊松比ν由下式计算得出。某些常用材料组合的ZE可参考表14-1-101查取。
(11)重合度系数Zε
重合度系数Zε用以考虑重合度对单位齿宽载荷的影响。Zε可由表14-1-100公式计算或按图14-1-40查得。
表14-1-100 Zε计算式

(12)螺旋角系数Zβ
螺旋角系数Zβ是考虑螺旋角造成的接触线倾斜对接触应力影响的系数,,也可根据分度圆螺旋角β由图14-1-41查得。

图14-1-37 αn=20°时的节点区域系数ZH

图14-1-38 αn=22.5°时的节点区域系数ZH

图14-1-39 αn=25°时的节点区域系数ZH

图14-1-40 重合度系数Zε
(13)试验齿轮的接触疲劳极限σHlim
σHlim是指某种材料的齿轮在某一接触应力下运转到规定的应力循环次数(对大多数材料其应力循环数为5×107)而未发生齿面扩展性点蚀时的极限应力。主要影响因素有:材料成分,力学性能,热处理及硬化层深度、硬度梯度,结构(锻、轧、铸),残余应力,材料的纯度和缺陷等。
表14-1-101 弹性系数ZE


图14-1-41 螺旋角系数Zβ
σHlim可由齿轮的负荷运转试验或使用经验的统计数据得出。此时需阐明线速度、润滑油黏度、表面粗糙度、材料组织等变化对许用应力的影响所引起的误差。无资料时,可参考图14-1-42~图14-1-46根据材料和齿面硬度查取。图中的σHlim值是试验齿轮的失效概率为1%时的轮齿接触疲劳极限。对于其他失效概率的疲劳极限值,可用适当的统计分析方法得到。图中硬化齿轮的疲劳极限值对渗碳齿轮适用于有效硬化层深度δ=0.15mn~0.2mn的精加工齿轮,对于氮化齿轮,其有效硬化层深度δ=0.4~0.6mm。
在σHlim图中,代表材料质量等级的ML、MQ和ME线所对应的材料处理要求见GB/T 3480.5—2008。
ML——表示对齿轮加工过程中材料质量和热处理工艺的一般要求。
MQ——表示对有经验的制造者在适度成本下可达到的质量等级。
ME——表示必须具备高可靠度的制造过程控制才能达到的质量等级。
图14-1-42~图14-1-46中提供的σHlim值是基于基准试验条件和基准试验齿轮参数得到的,具体条件如下。

当满足上述条件时,以轮齿齿面点蚀面积比率作为齿轮失效判据:对于调质齿轮,其大小齿轮点蚀面积占全部工作齿面的2%,或者对单齿占4%;对于表面硬化齿轮,其大小齿轮点蚀面积占全部工作齿面的0.5%,或者对单齿占4%。

图14-1-42 正火低碳锻钢和铸钢的σHlim
(14)接触强度计算的寿命系数ZNT
寿命系数ZNT是考虑齿轮寿命小于或大于持久寿命条件循环次数Nc时(见图14-1-47),其可承受的接触应力值与其相应的条件循环次数Nc时疲劳极限应力的比例的系数。

图14-1-43 铸铁的σHlim

图14-1-44 调质锻钢及铸钢的σHlim

图14-1-45 渗碳锻钢和表面硬化(火焰或感应淬火)铸、锻钢的σHlim
当齿轮在定载荷工况工作时,应力循环次数NL为齿轮设计寿命期内单侧齿面的啮合次数;双向工作时,按啮合次数较多的一侧计算。当齿轮在变载荷工况下工作并有载荷图谱可用时,应按1.7.4.4的方法核算其强度安全系数;对于缺乏工作载荷图谱的非恒定载荷齿轮,可近似地按名义载荷乘以使用系数KA来核算其强度。
条件循环次数Nc是齿轮材料S-N(即应力-循环次数)曲线上一个特征拐点的循环次数,并取该点处的寿命系数为1.0,相应的S-N曲线上的应力称为疲劳极限应力。
接触强度计算的寿命系数ZNT应根据实际齿轮实验或经验统计数据得出S-N曲线求得,它与一对相啮合齿轮的材料、热处理、直径、模数、齿面粗糙度、节线速度及使用的润滑剂有关。当直接采用S-N曲线确定和S-N曲线实验条件完全相同的齿轮寿命系数ZNT时,应将有关的影响系数ZR、Zv、ZL、ZW、Zx的值均取为1.0。
当无合适的上述实验或经验数据可用时,ZNT可由表14-1-102的公式计算得出,也可由图14-1-47查取。

图14-1-46 氮化钢、氮化调质钢和氮碳共渗钢的σHlim

图14-1-47 接触强度的寿命系数ZNT
表14-1-102 接触强度的寿命系数ZNT


注:当优选材料、制造工艺和润滑剂,并经生产实践验证时,这几个式子可取ZNT=1.0。
(15)润滑油膜影响系数ZL、Zv、ZR
齿面间的润滑油膜影响齿面承载能力。润滑区的油黏度、相啮面间的相对速度、齿面粗糙度对齿面间润滑油膜状况的影响分别以润滑剂系数ZL、速度系数Zv和粗糙度系数ZR来考虑。齿面载荷和齿面相对曲率半径对齿面间润滑油膜状况也有影响。
确定润滑油膜影响系数数值的理想方法是总结现场使用经验或用具有可类比的尺寸、材料、润滑剂及运行条件的齿轮箱实验。当采用与设计的齿轮完全相同的参数、材料和条件实验决定其承载能力或寿命系数时,应取ZL、Zv和ZR的值均等于1.0。当无资料时,可按下述方法之一确定。
①一般方法 计算公式见表14-1-103。
表14-1-103 ZL、Zv、ZR计算公式

① v50——在50℃时润滑油的名义运动黏度,mm2/s(cSt);
v40——在40℃时润滑油的名义运动黏度,mm2/s(cSt)。
② 公式及图14-1-48适用于矿物油(加或不加添加剂)。应用某些具有较小摩擦因数的合成油时,对于渗碳钢齿轮ZL应乘以系数1.1,对于调质钢齿轮应乘以系数1.4。
③ Rz10——相对(峰—谷)平均粗糙度
Rz1,Rz2——小齿轮及大齿轮的齿面微观不平度十点高度,μm。如经事先跑合,则Rz1,Rz2应为跑合后的数值;若粗糙度以Ra值(Ra=CLA值=AA值)给出,则可近似取Rz≈6Ra。
ρred——节点处诱导曲率半径,mm;ρred=ρ1ρ2/(ρ1±ρ2)。式中“+”用于外啮合,“-”用于内啮合,ρ1,ρ2分别为小轮及大轮节点处曲率半径;对于小齿轮-齿条啮合,ρred=ρ1;ρ1,2=0.5db1,2tanα't,式中db为基圆半径。

图14-1-48 润滑剂系数ZL

图14-1-49 速度系数Zv

图14-1-50 粗糙度系数ZR
②简化方法 ZL、Zv、ZR的乘积在持久强度和静强度设计时由表14-1-104查得。对于应力循环次数NL小于持久寿命条件循环次数NC的有限寿命设计,(ZLZvZR)值由其持久强度(NL≥NC)和静强度(NL≤N0)时的值参照表14-1-103的公式插值确定。
表14-1-104 简化计算的(ZLZvZR)值

(16)齿面工作硬化系数ZW
工作硬化系数ZW是用以考虑经光整加工的硬齿面小齿轮在运转过程中对调质钢大齿轮齿面产生冷作硬化,从而使大齿轮的许用接触应力得以提高的系数。
ZW可由公式ZW=1.2-(HB-130)/1700计算或由图14-1-51查取(式中HB为大轮齿面布氏硬度值)。此公式和图的使用条件为:小齿轮齿面微观不平度10点高度Rz<6μm,大齿轮齿面硬度为130~470HB。当HB<130时,取ZW=1.2;当HB>470时,取ZW=1.0。
(17)接触强度计算的尺寸系数Zx
尺寸系数是考虑因尺寸增大使材料强度降低的尺寸效应因素。确定尺寸系数最理想的方法是通过实验或经验总结。当用与设计齿轮完全相同尺寸、材料和工艺的齿轮进行实验得到齿面承载能力或寿命系数时,Zx=1.0。静强度(NL≤N0)的Zx=1.0。
当无合适的实验或经验数据可用时,持久强度(NL≥NC)的尺寸系数Zx可按表14-1-105所列公式计算或由图14-1-52查取。有限寿命(N0<NL<NC)的尺寸系数由持久强度和静强度时的尺寸系数值参照表14-1-103左栏公式插值确定。

图14-1-51 工作硬化系数ZW
表14-1-105 接触强度计算的尺寸系数Zx

注:mn是单位为mm的齿轮法向模数值。
(18)最小安全系数SHmin(SFmin)
安全系数选取的原则见1.7.1节。如无可用资料时,最小安全系数可参考表14-1-106选取。
表14-1-106 最小安全系数参考值

注:1.在经过使用验证或对材料强度、载荷工况及制造精度拥有较准确的数据时,可取表中SFmin下限值。
2.一般齿轮传动不推荐采用低可靠度的安全系数值。
3.采用低可靠度的接触安全系数值时,可能在点蚀前先出现齿面塑性变形。
1.7.4.2 轮齿弯曲强度核算
GB/T 3480—1997以载荷作用侧的齿廓根部的最大拉应力作为名义弯曲应力,并经相应的系数修正后作为计算齿根应力。考虑到使用条件、要求及尺寸的不同,标准将修正后的试件弯曲疲劳极限作为许用齿
根应力。标准给出的轮齿弯曲强度计算公式适用于齿根以内轮缘厚度不小于3.5mn的圆柱齿轮。对于不符合此条件的薄轮缘齿轮,应作进一步应力分析、实验或根据经验数据确定其齿根应力的增大率。

图14-1-52 接触强度计算的尺寸系数Zx
a—结构钢、调质钢、静强度计算时的所有材料;
b—短时间液体渗氮钢,气体渗氮钢;
c—渗碳淬火钢、感应或火焰淬
火表面硬化钢
(1)轮齿弯曲强度核算的公式
轮齿弯曲强度核算公式见表14-1-107。
表14-1-107 轮齿弯曲强度核算公式


①对于计算精确度要求较高的齿轮,应优先采用方法一。在对计算结果有争议时,以方法一为准。
②若大、小齿轮宽度不同时,最多把窄齿轮的齿宽加上一个模数作为宽齿轮的工作齿宽;对于双斜齿或人字齿轮b=bB×2,bB为单个斜齿轮宽度;轮齿如有齿端修薄或鼓形修整,b应取比实际齿宽较小的值。
③薄轮缘齿轮齿根应力基本值的计算见1.7.4.5。
(2)弯曲强度计算的螺旋线载荷分布系数KFβ
螺旋线载荷分布系数KFβ是考虑沿齿宽载荷分布对齿根弯曲应力的影响。对于所有的实际应用范围,KFβ可按下式计算
式中 KHβ——接触强度计算的螺旋线载荷分布系数,见1.7.4.1中(5);
N——幂指数
式中 b——齿宽,mm,对人字齿或双斜齿齿轮,用单个斜齿轮的齿宽;
h——齿高,mm。
b/h应取大小齿轮中的小值。
图14-1-53给出了按以上二式确定的近似解。

图14-1-53 弯曲强度计算的螺旋线载荷分布系数KFβ
(3)弯曲强度计算的齿间载荷分配系数KFα
弯曲强度计算的螺旋线载荷分配系数KFα的含义、影响因素、计算方法及使用表格与接触强度计算的螺旋线载荷分配系数KHα完全相同,且KFα=KHα。详见1.7.4.1中(6)。
(4)齿廓系数YF、YFa
齿廓系数是用以考虑齿廓对名义弯曲应力的影响,以过齿廓根部左右两过渡曲线与30°切线相切点的截面作为危险截面进行计算。
①齿廓系数YF 齿廓系数YF是考虑载荷作用于单对齿啮合区外界点时齿廓对名义弯曲应力的影响(见图14-1-54)。
外齿轮的齿廓系数YF可由下式计算:
式中 mn——齿轮法向模数,mm;
αn——法向分度圆压力角;
αFen,hFe,sFn的定义见图14-1-54。

图14-1-54 影响外齿轮齿廓系数YF的各参数
用齿条刀具加工的外齿轮,YF可用表14-1-108中的公式计算。但计算需满足下列条件:
a.30°切线的切点应位于由刀具齿顶圆角所展成的齿根过渡曲线上;
b.刀具齿顶必须有一定大小的圆角,即ρfP≠0。刀具的基本齿廓尺寸见图14-1-55。

图14-1-55 刀具基本齿廓尺寸
表14-1-108 外齿轮齿廓系数YF的有关公式


注:1.表中长度单位为mm,角度单位为rad。
2.本计算适用于标准或变位的直齿轮和斜齿轮。对于斜齿轮,齿廓系数按法截面确定,即按当量齿数zn进行计算。大、小齿轮的YF应分别计算。
内齿轮的齿廓系数YF不仅与齿数和变位系数有关,且与插齿刀的参数有关。为了简化计算,可近似地按替代齿条计算(见图14-1-56)。替代齿条的法向齿廓与基本齿条相似,齿高与内齿轮相同,法向载荷作用角αFen等于αn,并以脚标2表示内齿轮。YF可用表14-1-109中的公式进行计算。

图14-1-56 影响内齿轮齿廓系数YF的各参数
表14-1-109 内齿轮齿廓系数YF的有关公式(适用于z2>70)

注:表中长度单位为mm,角度单位为rad。
②齿廓系数YFa 齿廓系数YFa是考虑当载荷作用于齿顶时齿廓对名义弯曲应力的影响,用于近似计算,且YFa只能与Yε一起使用。
外齿轮的齿廓系数YFa可由下式确定(参见图14-1-57)。
公式适用于εαn<2的标准或变位的直齿轮和斜齿轮。大、小轮的YFa应分别确定。
对于斜齿轮,齿廓系数按法截面确定,即按当量齿数zn确定,当量齿数zn可用表14-1-108中公式计算。
用齿条刀具加工的外齿轮的YFa可按表14-1-110中的公式计算,或按图14-1-59~图14-1-63相应查取。不同参数的齿廓所适用的图号见表14-1-112。

图14-1-57 影响外齿轮齿廓系数YFa的各参数
图14-1-59~图14-1-63的图线适用于齿顶不缩短的齿轮。对于齿顶缩短的齿轮,实际弯曲力臂比不缩短时稍小一些,因此用以上图线查取的值偏于安全。
表14-1-110 外齿轮齿廓系数YFa的有关公式

注:长度单位为mm,角度单位为rad。
内齿轮的齿廓系数YFa可近似地按替代齿条计算。此替代齿条的法向齿廓与基本齿条相似,齿高与内齿轮相同,并取法向载荷作用角αFan等于αn(参见图14-1-58)。以脚标2表示内齿轮。有关计算公式见表14-1-111(适用于z2>70)。
与图14-1-59~图14-1-63各齿廓参数相对应的内齿轮齿廓系数YFa可由表14-1-112查取。
(5)应力修正系数YS、YSa
应力修正系数YS和YSa是将名义弯曲应力换算成齿根局部应力的系数。它考虑了齿根过渡曲线处的应力集中效应,以及弯曲应力以外的其他应力对齿根应力的影响。

图14-1-58 影响内齿轮齿廓系数YFa的各参数
表14-1-111 内齿轮齿廓系数YFa的有关公式

注:1.对变位齿轮,仍取标准齿高。
2.长度单位为mm,角度单位为rad。





图14-1-63 外齿轮齿廓系数YFa
αP=25°;haP/mn=1;hfP/mn=1.25;ρfP/mn=0.318
表14-1-112 几种基本齿廓齿轮的YFa

应力修正系数不仅取决于齿根过渡曲线的曲率,还和载荷作用点的位置有关。YS用于载荷作用于单对齿啮合区外界点的计算方法(方法一),YSa则用于载荷作用于齿顶的计算方法(方法二)。
①应力修正系数YS 应力修正系数YS仅能与齿廓系数YF联用。对于齿廓角αn为20°的齿轮,YS可按下式计算。对于其他齿廓角的齿轮,可按此式近似计算YS
)
式中 L——齿根危险截面处齿厚与弯曲力臂的比值
sFn——齿根危险截面齿厚,外齿轮由表14-1-108序号7的公式计算,内齿轮按表14-1-109序号7的公式计算;
hFe——弯曲力臂,外齿轮由表14-1-108序号17的公式计算,内齿轮由表14-1-109序号8的公式计算;
qS——齿根圆角参数,其值为
ρF——30°切线切点处曲率半径,外齿轮由表14-1-108序号8公式计算,内齿轮由表14-1-109序号5的公式计算。
YS不宜用图解法确定。
②应力修正系数YSa 应力修正系数YSa仅能与齿廓系数YFa联用,并且只能用于εαn<2的齿轮传动。
对于齿廓角αn为20°的齿轮,YSa可按下式计算。对于其他齿廓角的齿轮,可按此式近似计算YSa。
式中 La=sFn/hFa;
sFn——外齿轮由表14-1-108序号7的公式计算,内齿轮由表14-1-109序号7的公式计算;
hFa——外齿轮由表14-1-110序号11的公式计算,内齿轮由表14-1-111序号8的公式计算。
用齿条刀具加工的外齿轮,其应力修正系数YSa也可按当量齿数和法向变位系数从图14-1-64~图14-1-68查取。对于短齿和有齿顶倒角的齿轮来说,使用这些图中的YSa值,其承载能力是偏向安全的。不同参数的齿廓所适用的图号见表14-1-113。

图14-1-64 外齿轮应力修正系数YSa
αP=20°;haP/mn=1;hfP/mn=1.25;ρfP/mn=0.38




表14-1-113 几种基本齿廓齿轮的YSa

③齿根有磨削台阶齿轮的应力修正系数 靠近齿根危险截面的磨削台阶(参见图14-1-69),将使齿根的应力集中增加很多,因此其应力集中系数要相应增加。计算时应以YSg代替YS,YSag代替YSa。

图14-1-69 齿根磨削台阶
上述二式仅适用于的情况。
当磨削台阶高于齿根30°切线切点时,其磨削台阶的影响将比上二式计算所得的值小。
YSg和YSag也考虑了齿根厚度的减薄。
(6)弯曲强度计算的重合度系数Yε
重合度系数Yε是将载荷由齿顶转换到单对齿啮合区外界点的系数。
Yε可用下式计算
式中 εαn——当量齿轮的端面重合度,。
(7)弯曲强度计算的螺旋角系数Yβ
螺旋角系数Yβ是考虑螺旋角造成的接触线倾斜对齿根应力产生影响的系数。其数值可由下式计算
Yβmin=1-0.25εβ≥0.75
上式中:当εβ>1时,按εβ=1计算,当Yβ<0.75时,取Yβ=0.75;当β>30°时,按β=30°计算。
螺旋角系数Yβ也可根据β角和纵向重合度εβ由图14-1-70查取。

图14-1-70 螺旋角系数Yβ
(8)试验齿轮的弯曲疲劳极限σFlim
σFlim是指某种材料的齿轮经长期的重复载荷作用(对大多数材料其应力循环数为3×106)后,齿根保持不破坏时的极限应力。其主要影响因素有:材料成分、力学性能、热处理及硬化层深度、硬度梯度、结构(锻、轧、铸),残余应力、材料的纯度和缺陷等。
σFlim可由齿轮的负荷运转试验或使用经验的统计数据得出。此时需阐明线速度、润滑油黏度、表面粗糙度、材料组织等变化对许用应力的影响所引起的误差。无资料时,可参考图14-1-71~图14-1-75根据材料和齿面硬度查取。图中的σFlim值是试验齿轮的失效概率为1%时的轮齿弯曲疲劳极限。对于其他失效概率的疲劳极限值,可用适当的统计分析法得到。图中硬化齿轮的疲劳极限值对渗碳齿轮适用于有效硬化层深度δ=0.15mn~0.2mn的精加工齿轮,对于氮化齿轮,其有效硬化层深度δ=0.4~0.6mm。
在σFlim的图中,给出了代表材料质量等级的三条线,其对应的材料处理要求见GB/T 3480.5—2008。
在选取材料疲劳极限时,除了考虑上述等级对材料质量和热处理质量的要求是否有把握达到外,还应注意所用材料的性能、质量的稳定性以及齿轮精度以外的制造质量同图列数值来源的试验齿轮的异同程度。这在选取σFlim时尤为重要。要留心一些常不引人注意的影响弯曲强度的因素,如实际加工刀具圆角的控制、齿根过渡圆角表面质量及因脱碳造成的硬度下降等。有可能出现齿根磨削台阶而计算中又未计YSg时,在选取σFlim时也应予以考虑。
图14-1-71~图14-1-75中提供的σFlim值是基于基准试验条件和基准试验齿轮参数得到的,具体条件如下。

以上图中的σFlim值适用于轮齿单向弯曲的受载状况;对于受对称双向弯曲的齿轮(如中间轮、行星轮),应将图中查得σFlim值乘上系数0.7;对于双向运转工作的齿轮,其σFlim值所乘系数可稍大于0.7。

图14-1-71 正火低碳锻钢和铸钢的σFlim和σFE
图中,σFE为齿轮材料的许用弯曲疲劳极限(它是用齿轮材料制成无缺口试件,在完全弹性范围内经受脉动载荷作用时的名义弯曲疲劳极限)。σFE=YSTσFlim,YST=2.0。

图14-1-72 铸铁的σFlim和σFE
(9)弯曲强度的寿命系数YNT
寿命系数YNT是考虑齿轮寿命小于或大于持久寿命条件循环次数NC时(见图14-1-76),其可承受的弯曲应力值与相应的条件循环次数NC时疲劳极限应力的比例系数。
当齿轮在定载荷工况工作时,应力循环次数NL为齿轮设计寿命期内单侧齿面的啮合次数;双向工作时,按啮合次数较多的一面计算。当齿轮在变载荷工况下工作并有载荷图谱可用时,应按1.7.4.4所述方法核算其强度安全系数,对于无载荷图谱的非恒定载荷齿轮,可近似地按名义载荷乘以使用系数KA来核算其强度。

图14-1-73 调质锻钢及铸钢的σFlim和σFE

图14-1-74 渗碳锻钢和表面硬化(火焰或感应淬火)铸、锻钢的σFlim和σFE

图14-1-75 氮化钢、氮化调质钢和氮碳共渗钢的σFlim和σFE
弯曲强度寿命系数YNT应根据实际齿轮实验或经验统计数据得出的S-N曲线求得,它与材料、热处理、载荷平稳程度、轮齿尺寸及残余应力有关。当直接采用S-N曲线确定和S-N曲线实验条件完全相同的齿轮寿命系数YNT时,应取系数YδrelT、YRrelT、Yx的值为1.0。
当无合适的上述实验或经验数据可用时,YNT可由表14-1-114中的公式计算得出,也可由图14-1-76查取。
表14-1-114 弯曲强度的寿命系数YNT

注:当优选材料、制造工艺和润滑剂,并经生产实践验证时,这些计算式可取YNT=1.0。

图14-1-76 弯曲强度的寿命系数YNT
(10)弯曲强度尺寸系数Yx
尺寸系数Yx是考虑因尺寸增大使材料强度降低的尺寸效应因素,用于弯曲强度计算。确定尺寸系数最理想的方法是通过实验或经验总结。当用与设计齿轮完全相同尺寸、材料和工艺的齿轮进行实验得到齿面承载能力或寿命系数时,应取Yx值为1.0。静强度(NL≤N0)的Yx=1.0。当无实验资料时,持久强度(NL≥NC)的尺寸系数Yx可按表14-1-115的公式计算,也可由图14-1-77查取。

图14-1-77 弯曲强度计算的尺寸系数Yx
a—结构钢、调质钢、球墨铸铁(珠光体、贝氏体)、珠光体可锻铸铁;
b—渗碳淬火钢和全齿廓感应或火焰淬火钢,渗氮或氮碳共渗钢;
c—灰铸铁,球墨铸铁(铁素体);
d—静强度计算时的所有材料
(11)相对齿根圆角敏感系数YδrelT
齿根圆角敏感系数表示在轮齿折断时,齿根处的理论应力集中超过实际应力集中的程度。
相对齿根圆角敏感系数YδrelT是考虑所计算齿轮的材料、几何尺寸等对齿根应力的敏感度与试验齿轮不同而引进的系数。定义为所计算齿轮的齿根圆角敏感系数与试验齿轮的齿根圆角敏感系数的比值。在无精确分析的可用的数据时,可按下述方法分别确定YδrelT值。
①持久寿命时的相对齿根圆角敏感系数YδrelT 持久寿命时的相对齿根圆角敏感系数YδrelT可按下式计算得出,也可由图14-1-78查得(当齿根圆角参数在1.5<qS<4的范围内时,YδrelT可近似地取为1,其误差不超过5%)。
式中 ρ'——材料滑移层厚度,mm,可由表14-1-116按材料查取;
X*——齿根危险截面处的应力梯度与最大应力的比值,其值
qS——齿根圆角参数,见本节(5)中①;
——试验齿轮齿根危险截面处的应力梯度与最大应力的比值,仍可用上式计算,式中qS取为qST=2.5,此式适用于m=5mm,其尺寸的影响用Yx来考虑。
表14-1-115 弯曲强度计算的尺寸系数Yx

表14-1-116 不同材料的滑移层厚度ρ'

表14-1-117 静强度的相对齿根圆角敏感系数YδrelT


图14-1-78 持久寿命时的相对齿根圆角敏感系数YδrelT
注:图中材料数字代号见表14-1-116中的序号
②静强度的相对齿根圆角敏感系数YδrelT 静强度的YδrelT值可按表14-1-117中的相应公式计算得出(当应力修正系数在1.5<YS<3的范围内时,静强度的相对敏感系数YδrelT近似地可取为YS/YST;但此近似数不能用于氮化的调质钢与灰铸铁)。
③有限寿命的齿根圆角敏感系数YδrelT 有限寿命的YδrelT可用线性插入法从持久寿命的YδrelT和静强度的YδrelT之间得到
式中,YδrelTc、YδrelT0分别为持久寿命和静强度的相对齿根圆角敏感系数。
(12)相对齿根表面状况系数YRrelT
齿根表面状况系数是考虑齿廓根部的表面状况,主要是齿根圆角处的粗糙度对齿根弯曲强度的影响。
相对齿根表面状况系数YRrelT为所计算齿轮的齿根表面状况系数与试验齿轮的齿根表面状况系数的比值。
在无精确分析的可用数据时,按下述方法分别确定。对经过强化处理(如喷丸)的齿轮,其YRrelT值要稍大于下述方法所确定的数值。对有表面氧化或化学腐蚀的齿轮,其YRrelT值要稍小于下述方法所确定的数值。
①持久寿命时的相对齿根表面状况系数YRrelT 持久寿命时的相对齿根表面状况系数YRrelT可按表14-1-118中的相应公式计算得出,也可由图14-1-79查得。
表14-1-118 持久寿命时的相对齿根表面状况系数YRrelT

注:Rz为齿根表面微观不平度10点高度。

图14-1-79 相对齿根表面状况系数YRrelT
a—灰铸铁,铁素体球墨铸铁,渗氮处理的渗氮钢、调
质钢;b—结构钢;c—调质钢,球墨铸铁(珠光体、
铁素体),渗碳淬火钢,全齿廓感应或火焰淬
火钢;d—静强度计算时的所有材料
②静强度的相对齿根表面状况系数YRrelT 静强度的相对齿根表面状况系数YRrelT等于1。
③有限寿命的相对齿根表面状况系数YRrelT 有限寿命的YRrelT可从持久寿命的YRrelT和静强度的YRrelT之间用线性插入法得到
式中,YRrelTc、YRrelT0分别为持久寿命和静强度的相对齿根表面状况系数。
1.7.4.3 齿轮静强度核算
当齿轮工作可能出现短时间、少次数(不大于表14-1-102和表14-1-114中规定的N0值)的超过额定工况的大载荷,如使用大启动转矩电动机,在运行中出现异常的重载荷或有重复性的中等甚至严重冲击时,应进行静强度核算。作用次数超过上述表中规定的载荷应纳入疲劳强度计算。
静强度核算的计算公式见表14-1-119。
1.7.4.4 在变动载荷下工作的齿轮强度核算
在变动载荷下工作的齿轮,应通过测定和分析计算确定其整个寿命的载荷图谱,按疲劳累积假说(Miner法则)确定当量转矩Teq,并以当量转矩Teq代替名义转矩T按表14-1-68求出切向力Fteq,再应用1.7.4.1和1.7.4.2所述方法分别进行齿面接触强度核算和轮齿弯曲强度核算,此时取KA=1。当无载荷图谱时,则可用名义载荷近似校核齿轮的齿面强度和轮齿弯曲强度。
图14-1-80是以对数坐标的某齿轮的承载能力曲线与其整个工作寿命的载荷图谱,图中T1、T2、T3、…为经整理后的实测的各级载荷,N1、N2、N3、…为与T1、T2、T3、…相对应的应力循环次数。小于名义载荷T的50%的载荷(如图中T5),被认为对齿轮的疲劳损伤不起作用,故略去不计,则当量应力循环次数Neq为
式中 Ni——第i级载荷下的应力循环次数;
ni——第i级载荷下的齿轮转速,r/min;
k——齿轮每转一周,同侧齿面的接触次数;
hi——第i级载荷下齿轮的工作小时数,h。
根据Miner法则,当量载荷Teq为
常用齿轮材料的疲劳曲线指数p值列于表14-1-120。

图14-1-80 承载能力曲线与载荷图谱
表14-1-119 静强度核算公式

注:1.因已按最大载荷计算,取使用系数KA=1。最大载荷可取启动载荷、堵转载荷、短路或其他最大过载转矩。
2.对在启动或堵转时产生的最大载荷或低速工况,可取动载系数KV=1;其余情况KV按1.7.4.1中(4)取值。
3.螺旋线载荷分布系数KHβ,KFβ见1.7.4.1中(5)和1.7.4.2中(2),但此时单位齿宽载荷应取。
4.齿间载荷分配系数KHα,KFα取值同1.7.4.1中(6)和1.7.4.2中(3)。
表14-1-120 常用的齿轮材料的疲劳曲线指数

当计算Teq时,若Neq<N0(材料疲劳破坏最少应力循环次数)时,取Neq=N0;当Neq>NC时,取Neq=NC。
在变动载荷下工作的齿轮又缺乏载荷图谱可用时,可近似地用常规的方法即用名义载荷乘以使用系数KA来确定计算载荷。当无合适的数值可用时,使用系数KA可参考表14-1-75确定。这样,就将变动载荷工况转化为非变动载荷工况来处理,并按1.7.4.1和1.7.4.2有关公式核算齿轮强度。
1.7.4.5 薄轮缘齿轮齿根应力基本值
计算分析表明,当齿轮的轮缘厚度SR相对地小于轮齿全齿高ht时(SR及ht见图14-1-81),齿轮的齿根弯曲应力将明显增大。当轮缘齿高比mB=SR/ht≥2.0时,mB对齿根弯曲应力没有影响。
轮缘系数YB没有考虑加工台阶、缺口、箍环、键槽等结构对齿根弯曲应力的影响。
在薄轮缘齿轮齿根应力基本值σF0计算时,应增加轮缘系数YB,用以考虑轮缘齿高比mB对齿根弯曲应力的影响。即采用表14-1-107中方法一计算σF0时,应改写成下式
或采用表14-1-107中方法二计算σF0时,应改写成下式
式中 YB——轮缘系数,其他符号同前。
轮缘系数YB可按以下各式计算或由图14-1-81查取。
当mB<1.0时
当1.0≤mB<1.56时
当mB≥1.56时
YB=1.0

图14-1-81 轮缘系数YB
1.7.5 开式齿轮传动的计算
开式齿轮传动一般只需计算其弯曲强度,计算时,仍可使用表14-1-107的公式,考虑到开式齿轮容易磨损而使齿厚减薄,因此,应在算得的齿根应力σF上乘以磨损系数Km。Km值可根据轮齿允许磨损的程度,按表14-1-121选取。
表14-1-121 磨损系数Km

对重载、低速开式齿轮传动,除按上述方法计算弯曲强度外,还建议计算齿面接触强度,此时许用接触应力应为闭式齿轮传动的1.05~1.1倍。
1.7.6 计算实例
表14-1-122 计算实例




1.8 渐开线圆柱齿轮修形计算
齿轮传动由于受制造和安装误差、齿轮弹性变形及热变形等因素的影响,在啮合过程中不可避免地会产生冲击、振动和偏载,从而导致齿轮早期失效的概率增大。生产实践和理论研究表明,仅仅靠提高齿轮制造和安装精度来满足日益增长的对齿轮的高性能要求是远远不够的,而且会大大增加齿轮传动的制造成本。对渐开线圆柱齿轮的齿廓和齿向进行适当修形,对改善其运转性能、提高其承载能力、延长其使用寿命有着明显的效果。
1.8.1 齿轮的弹性变形修形
齿轮装置在传递功率时,由于受载荷的作用,各个零部件都会产生不同程度的弹性变形,其中包括轮齿、轮体、箱体、轴承等的变形。尤其与齿轮相关的弹性变形,如轮齿变形和轮体变形,会引起齿轮的齿廓和齿向的畸变,使齿轮在啮合过程中产生冲击、振动和偏载。近年来,在高参数齿轮装置中,广泛采用轮齿修形技术,减少由轮齿受载变形和制造误差引起的啮合冲击,改善了齿面的润滑状态并获得较为均匀的载荷分布,有效地提高了轮齿的啮合性能和承载能力。
齿轮修形一般包括齿廓修形和齿向修形两部分。
1.8.1.1 齿廓修形
齿轮传递动力时,由于轮齿受载产生的弹性变形量以及制造误差,实际啮合点并非总是处于啮合线上,从动齿轮的运动滞后于主动齿轮,其瞬时速度差异将造成啮合干涉和冲击,从而产生振动和噪声。为减少啮合干涉和冲击,改善齿面的润滑状态,需要对齿轮进行齿廓修形。实际工作中,为了降低成本,一般将啮合齿轮的变形量都集中反映在小齿轮上,仅对小齿轮进行修形。
表14-1-123 齿廓修形


表14-1-124 方式一的齿廓修形量 mm

表14-1-125 方式二的齿廓修形量 mm

表14-1-126 方式三的齿廓修形量 mm

1.8.1.2 齿向修形
齿轮传递动力时,由于作用力的影响齿轮轴将产生弯曲、扭转等弹性变形,由于温升的影响斜齿轮螺旋角将发生改变;制造时由于齿轮材质的不均匀将导致齿轮热后变形不稳定,产生齿向误差;安装时齿轮副轴线存在平行度误差等。这些误差使轮齿载荷不能均匀地分布于整个齿宽,而是偏载于一端,从而出现局部早期点蚀或胶合,甚至造成轮齿折断,失去了增加齿宽提高承载能力的意义。因此为获得较为均匀的齿向载荷分布,必须对高速、重载的宽斜齿(直齿)齿轮进行齿向修形,见表14-1-127。
表14-1-127 齿向修形




表14-1-128 v=100~125m/s的小齿轮热变形量Δ2 mm

表14-1-129 v≥125mm/s的小齿轮的修形量Δ1、Δ2 mm

1.8.2 齿轮的热变形修形
渐开线圆柱齿轮传动在工作时,啮合齿面间和轴承中都会因摩擦产生热,从而引起齿轮的热变形。由于一般齿轮传动的热变形非常小,对齿轮的运行影响不大,因此可不予考虑。但是,对于高速齿轮传动,尤其是单斜齿的高速齿轮传动,由于传递的功率大、产生的热量多,热变形的影响必须适当考虑。本节所述内容主要指的是高速单斜齿的热变形修形。
1.8.2.1 高速齿轮的热变形机理
高速齿轮运转时,由齿轮副、轴系、轴承、箱体等组成了一个热平衡系统。在这个系统中,由高速旋转齿轮的齿面滑动摩擦和滚动摩擦造成的齿轮啮合损失、高速齿轮轴在滑动轴承内转动引起的润滑油膜的剪切摩擦损失、轮齿对空气的搅动损失、斜齿轮轮齿进入啮合造成的高速油气混合体的流动与齿面的摩擦损失等,都将转化为大量的热能,这些热能通过传导、对流及辐射等形式分布在齿轮箱内,与润滑油的内部冷却和空气的外部冷却结合在一起,形成处于平衡状态的高速齿轮的不均匀的温度场。
在影响高速齿轮不均匀温度场的诸因素中,最主要的因素是齿轮进入啮合时造成的沿齿轮轴向高速流动的油气混合体与齿面摩擦产生的热。由于斜齿轮的啮合作用(形成泵效应),喷入齿轮齿槽中的压力油与箱体内的空气组成的油气混合体,从齿轮的啮入端被挤向啮出端,形成高速流动的油气流。这种油气流的流动速度就是斜齿轮的轴向啮合速度。对于螺旋角为8°~15°的高速齿轮来说,其油气流的速度远大于齿轮的节圆线速度,约为节圆线速度的3~7倍。对于节圆线速度大于100m/s的单斜齿轮来说,这种油气流的速度就会达到声速的2倍以上。
1.8.2.2 高速齿轮齿向温度分布
根据郑州机械研究所的高速齿轮测温试验得出的高速齿轮沿齿向的温度分布情况,如图14-1-82所示。由图可见,从啮入端到啮出端温度逐渐升高,在啮入端的大约半个齿宽范围内,温度变化缓慢,在啮出端的半个齿宽内,温度变化较大。在距啮出端面约1/6个齿宽处,温度基本达到最大值。对于不同的工况,齿向温度分布特征都相同,只是随着齿轮节圆线速度的增加,齿向温度分布不均匀程度增大。对于直径200mm、螺旋角12°、齿宽130mm的齿轮,在正常润滑油流量的情况下,节圆线速度为110m/s时,齿向温差约为12.5℃,线速度为120m/s、130m/s时温差分别约为14℃、17℃,而当线速度达到140m/s、150m/s时温差分别约为27.5℃、35℃。在润滑油流量低于正常值20%左右的情况下,齿轮整体温度升高,齿向温差增大,在150m/s时温差可达41℃。

图14-1-82 齿轮齿向温度分布
轮齿温度与节圆线速度的关系如图14-1-83所示。从图中可以看出,齿轮轮齿温度与节圆线速度成正比关系,温度随齿轮线速度的增加而升高。

图14-1-83 齿轮温度与节圆线速度的关系
1—啮出端温度;2—轮齿中部温度;3—啮入端温度
1.8.2.3 高速齿轮的热变形修形计算
要进行高速齿轮的热变形修形计算,首先要了解其温度场的分布。此处结合测温试验,给出一个工程上能够应用的简化的近似计算方法。
要对齿轮温度场的分布进行近似计算,需先作如下假设:把高速旋转着的齿轮看成是处于稳定温度场中的匀质圆柱体,沿齿轮外圆柱面有一个均匀分布的热源,同时把齿轮的热导率看成常数,温度沿圆周方向的变化等于零。另外把齿轮沿轴向垂直于齿轮轴线切成许多个薄圆盘,在每个薄圆盘上认为温度在轴向不发生变化,即认为齿轮温度场的分布仅与齿轮的半径有关。
由工程热力学可知,满足以上假设条件的齿轮的温度分布为
式中 t——齿轮半径r处的温度, ℃;
tc——齿轮轴心处的温度, ℃;
ts——齿轮外圆处的温度, ℃;
r——齿轮任一点的半径,mm;
ra——齿轮外圆半径,mm。
在前述的假设条件下,可以认为齿轮的热应力和热变形是相对于齿轮轴线对称的。由弹性理论得知,轴对称温度分布圆盘的径向热变形量的表达式为
式中 u——齿轮半径r上的径向热变形,mm;
ν——材料的泊松比;
ξ——材料的线胀系数,℃-1。
根据以上假设和上述两个公式可以推导出计算高速齿轮齿向热变形修形量的公式为
式中 Δδ——齿向热变形修形量,mm;
r1——分度圆半径,mm;
λ——热变形修正系数;
tsh——齿向温度最高点处的外表面温度, ℃;
tch——齿向温度最高点处的轴心温度, ℃;
tsl——齿向温度最低点处的外表面温度, ℃;
tcl——齿向温度最低点处的轴心温度, ℃;
αt——端面压力角,(°)。
根据试验结果与工业现场的应用经验,同时参考国内外的有关修形方面的资料,认为修正系数λ取0.75比较合适,利用上述公式计算出的热变形修形量见表14-1-130。
表14-1-130 高速齿轮齿向热变形修形量Δδ mm

1.8.2.4 高速齿轮热变形修形量的确定
高速齿轮的热变形主要对轮齿齿向产生影响,对齿廓影响很小。因此,热变形修形主要是对齿向修形。试验表明,对于节圆线速度低于100m/s的齿轮,齿向温度差异很小,可不予考虑,对于线速度高于100m/s的齿轮,应考虑热变形的影响。
(1)齿廓修形量的确定
高速齿轮齿廓修形通常采用图14-1-84的方式。考虑到大小齿轮温度差异对基节的影响,对齿廓未修形部分的公差带加以控制,以提高齿轮的运转性能。
(2)齿向修形量的确定
高速齿轮齿向修形量通常采用图14-1-85的方式。其中Δ2主要是考虑热变形的影响Δ2=Δδ。修形曲线简化成一条以啮入端为起始点的斜直线。Δ1主要考虑弹性变形的影响,按表14-1-127中的单斜齿综合变形公式计算,且0.013mm≤Δ1≤0.035mm。
Δδ可按1.8.2.3节公式进行计算。在实际应用中,由于式中的参数计算较困难,可参考表14-1-130中的数据来确定Δδ。

图14-1-84 高速齿轮齿廓修形曲线
[δ=0.003mm,其余各量同表14-1-123中图(d)]

图14-1-85 高速齿轮齿向修形曲线
(3)修形示例
一对增速齿轮副,最大传递功率P=8400kW,n2/n1=3987/10664r/min,模数mn=6mm,螺旋角β=11°28'40″,小齿轮分度圆直径d1=244.9mm,齿宽b=280mm,单位齿宽载荷ωt=219N/mm,节圆线速度v=136.7m/s,支撑跨距L=640mm。
齿廓修形采用图14-1-84(b)方式,因齿轮节圆线速度高于100m/s,故齿向修形曲线应为图14-1-85的形式。
齿廓修形量的确定:
根据表14-1-126,
齿廓修形曲线如图14-1-86(a)所示。

图14-1-86 热变形修形曲线
齿向修形量的确定:
由表14-1-127中的单斜齿综合变形公式
因δ<0.013mm,取Δ1=0.013mm
根据小齿轮直径和线速度查表14-1-130,选取Δ2=0.013mm。
齿向修形曲线如图14-1-86(b)所示。
1.9 齿轮材料
齿轮材料及其热处理是影响齿轮承载能力和使用寿命的关键因素,也是影响齿轮生产质量和成本的主要环节。选择齿轮材料及其热处理时,要综合考虑轮齿的工作条件(如载荷性质和大小、工作环境等)、加工工艺、材料来源及经济性等因素,以使齿轮在满足性能要求的同时,生产成本也最低。
齿轮用材料主要有钢、铸铁、铜合金。
1.9.1 齿轮用钢
齿轮用各类钢材和热处理的特点及适用条件见表14-1-131,调质及表面淬火齿轮用钢的选择见表14-1-132,渗碳齿轮用钢的选择见表14-1-133,渗氮齿轮用钢的选择见表14-1-134,渗碳深度的选择见表14-1-135,常用齿轮钢材的化学成分见表14-1-136,常用齿轮钢材的力学性能见表14-1-137,齿轮工作齿面硬度及其组合应用示例见表14-1-138。
表14-1-131 各类材料和热处理的特点及适用条件

表14-1-132 调质及表面淬火齿轮用钢的选择

表14-1-133 渗碳齿轮用钢的选择

注:其中一部分可进行碳氮共渗。
表14-1-134 渗氮齿轮用钢的选择

表14-1-135 渗碳深度的选择

注:1.本表是气体渗碳的概略值,固体渗碳和液体渗碳略小于此值。
2.近来,对模数较大的齿轮,渗碳深度有大于表值的倾向。

表14-1-137 常用齿轮钢材的力学性能




表14-1-138 齿轮工作齿面硬度及其组合的应用举例

注:1.滚刀和插齿刀所能切削的齿面硬度一般不应超过HB=300(个别情况下允许对尺寸较小的齿轮将其硬度提高到HB=320~350)。
2.对重要传动的齿轮表面应采用高频淬火并沿齿沟进行。
3.通常渗碳后的齿轮要进行磨齿。
4.为了提高抗胶合性能建议小轮和大轮采用不同牌号的钢来制造。
1.9.2 齿轮用铸铁
与钢齿轮相比,铸铁齿轮具有切削性能好、耐磨性高、缺口敏感低、减振性好、噪声低及成本低的优点,故铸铁常用来制造对强度要求不高、但耐磨的齿轮。
常用齿轮铸铁性能对比见表14-1-139,常用灰铸铁、球墨铸铁的力学性能见表14-1-140,球墨铸铁的组织状态和力学性能见表14-1-141,球墨铸铁齿轮的齿根弯曲疲劳强度见表14-1-142,球墨铸铁齿轮的接触疲劳强度见表14-1-143、石墨化退火黑心可锻铸铁和珠光体可锻铸铁的力学性能见表14-1-144。
1.9.3 齿轮用铜合金
常用齿轮铜合金材料的化学成分见表14-1-145,各种铜合金的主要特性及用途见表14-1-146,常用齿轮铜合金的力学性能见表14-1-147,常用齿轮铸造铜合金的物理性能见表14-1-148。
表14-1-139 常用齿轮铸铁性能对比

①弯曲疲劳比,弯曲疲劳极限与抗拉强度之比,设计时推荐使用0.35的疲劳比。
②分别为珠光体灰铸铁范围:154~216MPa,216~309MPa和大于309MPa的对应值。
③按ISO R946标准,在直径20mm的试棒上测得。
④无缺口试样。
⑤有缺口试样(45°,V形),上贝氏体球墨铸铁。
⑥V形缺口(单铸试块),球墨铸铁QT 400-18,括号外数据分别为试验温度23℃±5℃和-20℃±2℃时3个试样的平均值;括号内的数据则分别为前述2种试验温度下单个试样的值。
表14-1-140 常用灰铸铁、球墨铸铁的力学性能

表14-1-141 球墨铸铁的组织状态和力学性能

表14-1-142 球墨铸铁齿轮的齿根弯曲疲劳强度

表14-1-143 球墨铸铁齿轮的接触疲劳强度

表14-1-144 石墨化退火黑心可锻铸铁和珠光体可锻铸铁的力学性能

表14-1-145 常用齿轮铜合金材料的化学成分(质量分数)


表14-1-146 各种铜合金的主要特性及用途


表14-1-147 常用齿轮铜合金的力学性能


①软态为退火态。②硬态为压力加工态。③S——砂型铸造。④J——金属型铸造。
表14-1-148 常用齿轮铸造铜合金的物理性能

注:表中序号与表14-1-146和表14-1-147相对应。
1.10 圆柱齿轮结构
圆柱齿轮的结构一般根据动力参数、几何尺寸以及箱体条件的限制,结合生产加工方式与工艺水平进行选择。通常有以下齿轮结构形式和尺寸,见表14-1-149。




表14-1-150 钢制齿圈与铸铁轮心配合的推荐过盈

注:对于用两个齿圈镶套的人字齿轮(见图14-1-87),应该用于转矩方向固定的场合,并在选择轮齿倾斜方向时应注意使轴向力方向朝齿圈中部。

图14-1-87 用两个齿圈镶套的人字齿轮
表14-1-151 标准滚刀切制人字齿轮的中间退刀槽尺寸 mm

注:用非标准滚刀切制人字齿轮的中间退刀槽宽e可按下式计算
式中 l0——滚刀长度,其他代号同前。
1.11 圆柱齿轮零件工作图
1.11.1 需要在工作图中标注的一般尺寸数据
①顶圆直径及其公差。
②分度圆直径。
③齿宽。
④孔(轴)径及其公差。
⑤定位面及其要求(径向和端面跳动公差应标注在分度圆附近)。
⑥轮齿表面粗糙度(轮齿齿面粗糙度标注在齿高中部圆上或另行标注)。
1.11.2 需要在参数表中列出的数据
①齿廓类型。
②法向模数mn。
③齿数z。
④齿廓齿形角α。
⑤齿顶高系数
⑥螺旋角β。
⑦螺旋方向R(L)。
⑧径向变位系数x。
⑨齿厚,公称值及其上、下偏差。
a.首先选用跨距(公法线长度)测量法,其WK公称值及上偏差Ebns、下偏差Ebni和跨测齿数K。
b.齿轮结构和尺寸不允许用跨距测量法时,也可采用跨球(圆柱)尺寸测量法或弦齿厚测量法。
⑩配对齿轮的图号及其齿数。
齿轮精度等级。
a.当单件或少量数件圆柱齿轮生产时,选用等级GB/T 10095.1—2008。
b.当批量生产圆柱齿轮时,选用等级GB/T 10095.1—2008和等级GB/T 10095.2—2008。
c.齿轮工作齿面和非工作齿面,一般选用同一精度等级,也可选用不同精度等级的组合。
检验项目、代号及其允许值。
a.GB/T 10095.1—2008规定:切向综合偏差(F'i、f'i),齿廓和螺旋线的形状和斜率偏差(ffα、ffβ、fHα、fHβ)不是必检项目。根据齿轮产品特殊需要,供需双方协商一致,可以标明其中的部分或全部偏差项目。
b.检验项目要标明相应的计值范围Lα和Lβ。
1.11.3 其他数据
①对于带轴的小齿轮,以及轴、孔不作为定心基准的大齿轮,在切齿前必须规定作定心检查用的表面最大径向跳动。
②为检验轮齿的加工精度,对某些齿轮尚需推出其他一些技术参数(如基圆直径),或其他作为检验用的尺寸参数和形位公差(如齿顶圆柱面等)。
③当采用设计齿廓或设计螺旋线时,应在图样上详述其参数。
④给出必要的技术要求,如材料热处理、硬度、探伤、表面硬化,齿根圆过渡,以及其他等。
1.11.4 齿轮工作图示例
图样中参数表,一般放在图样右上角。参数表中列出参数项目可以根据实际情况增减,检验项目的允许值确定齿轮精度等级。图样中技术要求,一般放在图形下方空余地方。具体示例见图14-1-88和图14-1-89。

