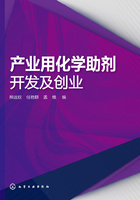
2.2 塑料助剂
加工用的助剂是高分子材料加工过程中应具备的三大要素(聚合物、助剂及设备)之一。由于大部分树脂本身难以满足多种要求,如有的树脂成型性能差,或极易老化,或成本偏高,因此选择适宜的助剂不仅可保证高分子材料顺利地进行加工,而且还可赋予高分子材料不同性能,拓宽高分子材料的使用范围,甚至可使近乎没有实用价值的树脂变为宝贵的材料。一般对塑料加工助剂的要求有以下几条:①应与被添加的合成树脂有较好的相容性,能长期稳定、均匀地分散在树脂中;②尽量使所用的塑料助剂相互间具有协同效应,促进各自功能的发挥;③耐久性好,不渗析,不会发生迁移或被水及溶剂萃取;④适合制品的使用要求,对加工条件的适应性要好。各种助剂可能提供给塑料制品的性能见表2-1。
表2-1 助剂种类及能够提供的性能

助剂效果的优劣与其挥发性及同树脂的相容性有关。如果助剂与树脂的相容性好,助剂在制品中分布均匀,助剂与树脂分子发生作用,助剂分子就不容易向塑料制品表面迁移,因此所起的作用就可持久。对液态助剂则要求沸点高,这样就不会在成型加工的温度下挥发,从而保持塑料制品性能稳定。
有些塑料助剂品种之间存在“协同”“对抗”效应。所谓“协同”指两种助剂配合使用比单独使用的效果明显,而“对抗”则指两种助剂共用时,其使用效能彼此产生冲突,相互削弱。有时候,某种助剂的加入有助于提高塑料制品的某项性能,但又会有碍于塑料的另一性能的情况。如在树脂中加入无机填料后可提高制品的刚度和强度,但会降低制品的电绝缘性能。因此必须根据应用要求正确地选用合适的塑料助剂。
塑料助剂在一定程度上决定了塑料广泛应用的可能性及其使用范围,如何在为数众多的塑料助剂中恰当地选用,需要相关理论的指导和经验的积累。
2.2.1 应用目的及工艺
2.2.1.1 增塑剂
塑料工业的发展离不开增塑剂,增塑剂是最早使用和现代塑料行业用量最大的塑料助剂品种。19世纪下半叶,人们就曾采用樟脑和邻苯二甲酸酯作为硝酸纤维素的增塑剂。1935年聚氯乙烯工业化后,增塑剂更是得到广泛应用。目前,国外消费量已经达到约500万吨/年,全球塑料助剂市场中增塑剂用量占60%左右,约有80%用于聚氯乙烯以及氯乙烯的共聚物,其余用于纤维素衍生物、聚醋酸乙烯酯、聚苯乙烯、天然和合成橡胶、ABS树脂等。我国助剂消费占世界总量的1/4,并以7%的年增长速度持续增长。
添加到聚合物中能使其玻璃化温度降低、塑性增加,使之易于加工并提高产品柔性的物质被称作增塑剂。凡能和树脂均匀混合,对热及化学试剂稳定,混合时不发生化学变化,但能降低物料的玻璃化温度和塑料成型加工时的熔体黏度,且本身保持不变,或虽起化学变化但能长期保留在塑料制品中并能改变树脂的某些物理性质,具有这些性能的液体有机化合物或低熔点的固体,都可用作增塑剂。某些聚合树脂也可用作增塑剂。具有增塑作用的树脂也被称为增塑树脂,如醇酸树脂常被用作氯化橡胶和硝酸纤维涂料的增塑树脂。增塑过程可看作是聚合物分子和增塑剂分子互相“溶解”的过程。然而,增塑剂不同于一般溶剂,当温度变化时,增塑剂分子仍能留在聚合物的分子链间,通过降低聚合物熔体的黏度以及产物的玻璃化温度和弹性模量,其作用机理是基于增塑剂分子对聚合物分子链间引力的削弱,不发生迁移和耐酸/碱等化学物品的溶浸。增塑剂的增塑作用是通过降低基料树脂的玻璃化温度[树脂由硬脆的固体状态(玻璃态)转变成为高弹性的橡胶态(高弹态)的温度]而实现的。
增塑剂通常可分为两类:主增塑剂(溶剂型增塑剂)和助增塑剂(非溶剂型增塑剂)。主增塑剂的某些基团能与树脂中的某些基团产生相互作用,因而主增塑剂和树脂能相互混溶。由于增塑剂分子较小,它进入树脂聚合物的分子结构中而降低树脂的刚性,但其加入也会使工件的力学性能受到一些损失。助增塑剂对基料树脂没有溶解作用,它们只是在加入量不太多的情况下才能与基料树脂混溶。助增塑剂对基料树脂只有物理作用(润滑作用),因而对工件的机械强度影响没有主增塑剂的影响大;助增塑剂容易从工件中迁移或者被萃失掉,因而增塑的效果持久性有限。
在塑料成型加工中,为了制得各种满足人们需要的软、硬、透明、电绝缘良好、发泡等制品,需要加入各种加工助剂。在选择助剂的品种和用量时必须全面考虑各方面的因素,如物理-化学性能、流动性能、成型性能,最终确立理想的配方。另外,根据不同的用途和加工工艺,还需要针对树脂的型号做出选择。在一定的增塑剂加入量之内,制件的渗透性基本上能够保持不变,当加入量继续增加时,工件的强度和韧性以及附着力等性能,先是随着增塑剂的加入而增加,到达一个峰值后则会下降。
除了对制品的力学性能有影响外,增塑剂还会影响其他性能,其最适当的加入量应根据制品的柔软程度要求、用途、工艺及使用环境不同来确定。一般压延工艺生产的PVC薄膜,增塑剂总用量在50份左右,吹塑薄膜略低些,一般在45~50份。增塑剂在10份以下时对机械强度的影响不明显,当加5份左右的增塑剂时,机械强度反而最高,即所谓反增塑现象。一般认为,反增塑现象是加入少量增塑剂后,大分子链活动能力增大,使分子有序化产生微晶的效应。添加少量的增塑剂的硬制品,其冲击强度反而比没有加时小,加大到一定剂量后,其冲击强度就随用量的增大而增大。增塑剂的使用对制品的耐热性和耐腐蚀性均有下降,每增加一份增塑剂,其马丁耐热度下降2~3。因此,一般硬制品通常不加或少加增塑剂,只是在为了提高加工流动性时才加入几份增塑剂。软制品则需要加入大量的增塑剂,增塑剂量越大,制品就越柔软。阻燃增塑剂,如磷酸酯及氯化石蜡的电性能比其他增塑剂优良,但随增塑剂用量增加,电性能总体呈下降趋势。对用于无毒用途的PVC制品,应采用无毒增塑剂,如环氧大豆油等。
增塑剂的添加时机和温度则要依据基料树脂的类型和熔点来确定,通常是在其他助剂添加之前,与基料树脂一起加热,在低于其混合熔点的温度混炼均匀。
2.2.1.2 热稳定剂
在聚合物或其他材料中加入少量某种物质,使得这些材料在加工或使用过程中不因受热而发生化学变化,或延缓这些变化,以达到延长材料使用寿命的目的,这种少量物质称为热稳定剂。
在塑料工业中,热稳定剂主要用于聚氯乙烯及氯乙烯共聚物,因为聚氯乙烯只有在160℃以上才能加工成型,而树脂自身在120~130℃就开始热分解,释放出氯化氢气体,形成共轭多烯结构,这种结构除使制品带色外还极易被氧化,导致进一步降解,这种链反应会大幅度降低树脂的粘接和塑料强度,并使树脂的可塑性损失。因此,为了保证聚氯乙烯能顺利加工成高质量的制品,必须在加工前加入热稳定剂。热稳定剂一般通过吸收氯化氢,取代活泼氯和双键加成等方式达到热稳定化的目的。
热稳定剂主要功能是防止加工时的热降解和交联,也有防止制品在长期使用过程中老化的作用。在软质制品中热稳定剂的用量为2%左右,在硬质制品中为3%~5%。工业上广泛应用的热稳定剂品种大致包括铅盐类、金属皂类、有机锡类和有机锑类等主稳定剂和环氧化合物类、亚磷酸酯类、多元醇类、苯二酮类等有机辅助稳定剂。
铅盐稳定剂主要用于硬制品中。铅盐类稳定剂具有热稳定性好、电性能优异、价廉等特点,但是其毒性较大,易污染制品,只能生产不透明制品。近年来复合稳定剂大量出现,单组分的稳定剂已有被取代的可能。复合稳定剂具有专用性强、污染小、使用时配料简便等优点。
钡镉类稳定剂是一类性能较好的热稳定剂,在PVC农用薄膜中使用较广,通常是钡镉锌和有机亚磷酸酯及抗氧剂并用。
钙锌类稳定剂可作为无毒稳定剂,用在食品包装与医疗器械、药品包装中。但其稳定性相对较低,用量大时透明度差,易产生向制品表面迁移的“吐霜”现象。钙锌类稳定剂一般借助多元醇和抗氧剂来提高其性能。
有机锡类热稳定剂性能较好,是用于PVC硬制品与透明制品的较好品种,尤其辛基锡几乎成为无毒包装制品不可缺少的稳定剂,但其价格较贵。
环氧类稳定剂通常作为辅助稳定剂。这类稳定剂与钡镉、钙锌类稳定剂并用时能提高光与热的稳定性,其缺点是易渗出。作辅助稳定剂的还有多元醇、有机亚磷酸酯类。
近年来还出现了稀土类稳定剂和水滑石系稳定剂,稀土类稳定剂主要特点是加工性能优良,而水滑石则是无毒稳定剂。
2.2.1.3 光稳定剂
当高分子材料受到太阳光的作用时,会吸收紫外线能量而引发自动氧化反应,导致聚合物降解,使制品变色、发脆、性能下降,甚至不能继续使用,这一过程称为光氧化或氧化性光降解,也称为光老化。为了抑制或减缓由于光氧化导致的高分子材料光降解作用而加入的物质称为光稳定剂或紫外线吸收剂。
光稳定剂的作用原理是通过屏蔽或吸收紫外线,使降解的过氧化产物进行非自由基分解,或者使被紫外线激发的高分子激发态猝灭而回到稳定基态,钝化金属离子,有效地捕灭紫外线引发的自由基,从而使高分子材料免受紫外线破坏,提高塑料制品的耐候性。由此,按照光稳定剂的稳定机理,可将光稳定剂分为以下四类。
①光屏蔽剂或遮光剂。光屏蔽剂是一类能反射和吸收紫外线的物质。在制品中起到滤光器的作用,阻止紫外线深入到聚合物的内部,使材料免受紫外线的伤害,有效地抑制制品的老化。属于光屏蔽剂的主要有炭黑、氧化锌及一些无机颜料或填料。
②紫外线吸收剂。紫外线吸收剂能强烈地、选择性地吸收高能量的紫外线,并将吸收的有害光能转变为无害的热能或低辐射能释放出去,使聚合物避免吸收紫外线能量而诱发光氧化反应遭到破坏,从而起到保护作用。
紫外线吸收剂应该具备以下条件:a.可强烈地吸收波长为290~400nm的紫外线;b.热稳定性好,即使在150℃以上的塑料加工温度下也不发生变化,热挥发性小;c.化学稳定性好,不与制品中的材料组分发生化学反应;d.混溶性好,可均匀地分散在材料中,不喷霜,不渗出;e.本身的光化学稳定性好,不分解,不变色;f.无色、无毒、无臭、耐浸洗、价廉、易得。目前紫外线吸收剂主要有二苯甲酮类、水杨酸酯类、苯并三唑类、取代丙烯腈类和三嗪类。
③猝灭剂或消光剂(又称能量转移剂)。通过猝灭受激聚合物分子上的能量,使之回复到基态,防止聚合物链的断裂。猝灭剂主要是含镍、钴等金属的有机配合物。猝灭剂不同于紫外线吸收剂,它的光稳定作用不是吸收紫外线,而是将聚合物分子因吸收紫外线后所产生的激发态能量进行转移,迅速而有效地将激发态的分子“猝灭”,使其再回到稳定基态,避免产生自由基。
猝灭剂主要有镍和钴的取代酚、硫代双酚、二硫代亚磷酸酯、二硫代氨基甲酸酯等的配合物,主要适用于聚丙烯、聚乙烯、聚氯乙烯、ABS等,一般添加量为0.1%~0.5%。含镍配合物与紫外线吸收剂并用时具有协同作用。
④自由基捕获剂。这是近20年里发展起来的新型高效光稳定剂,以受阻胺为官能团,是一类具有空间位阻效应的呱啶衍生物,氮氧自由基是捕获聚合物自由基的根本,简称为受阻胺类光稳定剂(HAIS)。由于这种氮氧自由基在稳定化过程中具有再生性,因此光稳定效果非常突出,迄今已经发展成为品种最多、产耗量最大的光稳定剂类别。当然,受阻胺光稳定剂的作用并不仅仅局限在捕获自由基方面,研究表明,受阻胺光稳定剂往往同时兼备分解氢过氧化物、猝灭单线态氧等作用。
受阻胺类光稳定剂几乎不吸收紫外线,但可通过捕获自由基、分解过氧化物、传递激发态能量等多种途径,使聚合材料得到保护并赋予聚合物高度的稳定性。受阻胺类光稳定剂可用于聚丙烯、高压聚乙烯、ABS、聚氨酯、聚苯乙烯、聚酰胺、聚氯乙烯等塑料及某些橡胶,添加量一般也为0.1%~0.5%。
2.2.1.4 阻燃剂
塑料、橡胶、纤维等有机合成材料均具可燃性,极易在一定条件下燃烧。随着塑料、橡胶、纤维在建筑、包装、交通运输、电子电器、家具、服装以及航空航天领域的用量不断增加,这些材料的燃烧问题,引起世界范围的高度重视。能降低材料燃烧速度或提高材料着火点而增加材料耐燃性的物质称为阻燃剂。准确地讲,阻燃剂称作难燃剂更为恰当,因为“难燃”包含阻燃和抑烟两层含义。
阻燃剂的阻燃机理可以综述为以下5点:①阻燃剂在塑料燃烧的温度下分解,其分解产物形成不挥发性的保护膜覆盖在表面,隔断空气而阻止燃烧;②阻燃剂分解脱出的水会吸收大量的热量,降低了可燃物表面温度,而且汽化成蒸汽,在可燃物表面形成了一层保护膜,从而减缓塑料分子的分解、蒸发和燃烧,同时,塑料阻燃剂体系里能分解产生不燃性气体,稀释可燃性气体,同样达到阻燃的目的;③由于活性自由基的链锁反应能使氧化燃烧持续,阻燃剂分解产物能够将活性自由基链锁反应切断,从而有效阻止燃烧;④通常单质碳不进行火焰的蒸发燃烧和分解燃烧,阻燃剂分解产物的脱水作用使有机物碳化,不停留在可燃性物质阶段而一直分解到单质碳,这样就能阻止塑料的持续燃烧;⑤阻燃剂分解生成的密度较大的气体或高沸点液体在易燃物表面聚集,具有隔氧阻燃作用。
阻燃剂最初仅在美国使用,20世纪50年代后期才获得广泛应用,至20世纪70年代阻燃剂有了飞速发展,阻燃剂品种和数量迅速增加,对阻燃剂新品种的开发也越来越活跃,已由单一型阻燃剂向复合型发展,由单功能向多功能发展,一些价格低廉、无毒、高效的新型阻燃剂在不断问世。阻燃剂目前用量仅次于增塑剂,消耗阻燃剂最多的塑料品种是聚氯乙烯、聚苯乙烯、聚氨酯泡沫塑料、不饱和聚酯、ABS树脂和聚丙烯。
对于不同材料的不同用途,对材料的阻燃性能要求也不相同,具有实用价值的阻燃剂应具备以下基本条件:①不降低高分子材料的物理力学性能,如耐热性、机械强度、电气性能及加工性能;②阻燃剂的分解温度与塑料的使用要求相适应,即分解温度不应太高,但在加工温度下又不致分解;③有良好的耐候性和持久性,不使制品的阻燃效果在使用中损失;④无毒或低毒,燃烧时产生的气体可燃性低,毒性小;⑤价格低廉。
阻燃剂大多是元素周期表中第Ⅴ、Ⅶ和Ⅲ族元素的化合物,特别是磷、溴、氯、锑和铝的化合物,即含磷、卤素、硼、锑等元素的有机化合物和无机化合物。通常按使用方法将阻燃剂分为添加型阻燃剂和反应型阻燃剂两大类。
①添加型阻燃剂。添加型阻燃剂是在聚合物加工时,加入与聚合物性能及制品用途相适应的液体或固体阻燃剂,它们与树脂之间仅仅是简单的物理混合。其特点是使用方便、适应性强,一般多用于热塑性塑料及合成纤维,但由于添加量达10%~30%,常会影响塑料的性能。添加型阻燃剂主要为磷酸酯、含卤磷酸酯、卤代烃、氧化锑、氢氧化铝、氢氧化镁、氮系阻燃剂和氮磷膨胀型阻燃剂等。
②反应型阻燃剂。反应型阻燃剂是在聚合物合成时作为含阻燃元素的单体之一,通过化学反应使之成为高分子链上的一部分,其分子内包含阻燃元素和反应性基团两种结构。其特点是对塑料性能的影响较小。反应型阻燃剂主要包括用于聚酯的卤代酸酐,用于环氧树脂的四溴双酚A和用于聚氨酯的含磷多元醇等,还有卤代酸酐、含磷多元醇、乙烯基衍生物、含环氧基的化合物等。
在改善聚合物的阻燃性能时,抑烟也是迫切需要解决的问题,所以在文献中所指的阻燃剂实际上是阻燃功能和抑烟功能助剂的总称。
在选用阻燃增塑剂——芳基磷酸酯、芳基-烷基磷酸酯时需要特别慎重,避免在增加阻燃性能的同时恶化了塑料的其他性能,特别是材料的低温柔顺性。抑烟剂的作用在于降低阻燃材料的发烟量和有毒有害气体的释放量,多为钼类化合物、锡类化合物和铁类化合物等。传统的抑烟剂有三氧化二钼、氢氧化镁、八钼酸铵等。添加钼类抑烟剂一般量为2%~3%,可降低30%~80%的生烟量,如与水合氧化铝(ATH,aluminium hydroxid,化学式为HAlO2·H2O或H3AlO3)、氢氧化镁或碳酸钙复合使用会有更好的效果。尽管氧化锑和硼酸锌亦有抑烟性,但常常作为阻燃协剂使用,因此归为阻燃剂体系。
硬质PVC塑料由于含氯量高,本身具有阻燃性。在PVC电缆、装饰墙壁及塑料帏布制品中掺入阻燃剂,可增加其耐火焰性,常用2~5份氯化石蜡、三氧化二锑、磷酸酯等阻燃剂。磷酸酯类和含氯增塑剂也有阻燃性。
2.2.1.5 发泡剂
在高分子材料加工过程中,可使高分子材料产生微孔结构的物质称为发泡剂。发泡剂主要用于制造泡沫塑料、泡沫橡胶、泡沫树脂等。由于这些泡沫制品具有质轻、隔热、隔声、节省材料,又有良好的电性能及机械阻尼性能等,所以用途十分广泛。典型的泡沫制品有海绵板、防滑地板、垫材、聚苯乙烯珠粒料发泡体、泡沫塑料电线电缆等。
根据发泡过程中气孔的形成方式,发泡剂可分为物理发泡剂和化学发泡剂两大类。
①物理发泡剂。物理发泡剂在使用过程中不发生化学反应,依靠本身的物理状态的变化,如易挥发液体的汽化等而使材料产生气孔。物理发泡剂主要是氯代烃或氟氯代烃,如三氯氟甲烷、三氯三氟乙烷等,主要用于生产聚氨酯泡沫塑料。化学发泡剂的主要品种是偶氮二甲酰胺(发泡剂AC)和N,N'-二亚硝基五亚甲基四胺(发泡剂H),前者多用于塑料,后者常用于橡胶。物理发泡剂主要是压缩气体,如空气、二氧化碳和氧气;挥发性液体,如低沸点的脂肪烃,卤代脂肪烃以及低沸点的醇、醚、酮和芳香烃等。
②化学发泡剂。化学发泡剂在发泡过程中因发生化学变化或在一定温度下的热分解产生一种或多种气体,而使高分子材料产生微孔结构。化学发泡过程中,发泡气体的产生有两种途径。一种是发泡气体由聚合物的基体中产生,即聚合物的副产物,如聚氨酯泡沫塑料的制备。另一种是通过加入的化学发泡剂的热分解来产生发泡气体,如酚醛树脂分解产生二氧化碳气体,使酚醛树脂发泡而制得酚醛泡沫塑料。
化学发泡剂包括无机发泡剂和有机发泡剂两大类,它们在聚合物中因受热汽化或分解产生气体,从而使聚合物料产生泡孔。无机发泡剂主要有碳酸、碳酸氢铵、碳酸氢钠等;有机发泡剂包括硝基化合物、偶氮化合物、磺酰肼类和尿素衍生物等。
化学发泡剂的分解温度和发气量是最重要的两个要素。分解温度可以确定发泡剂的适用范围及其发泡的工艺条件,而发气量是衡量化学发泡剂效率的一个主要指标。PVC用的发泡剂主要是偶氮二甲酰胺(ADC发泡剂)和偶氮二异丁腈及无机发泡剂。另外,偶氮物的铅盐和镉盐也有助发泡作用,可使AC发泡剂的分解温度降到150~180℃左右。发泡剂的用量根据发泡倍率而定。
2.2.1.6 固化剂
热固性树脂在未交联固化之前是可溶可熔的线型结构,具有良好的加工成型性。成型时通过交联固化成为不溶不熔的体型结构。热固性塑料成型时所加入的可使树脂完成或加快交联反应的物质,称为固化剂或交联剂。固化剂对高分子化合物的交联反应,大致有两种类型:一类是固化剂分子参与树脂分子的交联反应,并构成固化产物的一部分链段,如多元胺、多元酸及酸酐等;另一类是固化剂分子不参与树脂的交联反应,仅起催化作用,使树脂本身聚合成网状结构,如咪唑、氟化硼、一元酸、一元胺等。固化交联时间和程度可以通过添加量来调整。
固化剂按其化学组成可分为以下四大类。
①多元胺类固化剂。这类化合物主要是含有两个或两个以上氨基的胺类,包括脂肪族多胺、芳香族多胺、多核芳香族多胺和脂环族多胺。多元胺类固化剂广泛应用于环氧树脂的固化及聚氨酯橡胶中。
②有机酸酐。酸酐类固化剂属加热固化剂,主要用于电器领域及黏合剂的制造中。作为环氧树脂固化剂的酸酐主要有邻苯二甲酸酐、四氢邻苯二甲酸酐、六氢邻苯二甲酸酐、甲基纳迪克酸酐(3-甲基内亚甲基邻苯二甲酸酐)等。
③低分子量聚酰胺。二聚酸和过量的多元胺反应制备的聚酰胺树脂也可当作环氧树脂的固化剂,其特点为适用期长、毒性小、树脂固化物的粘接性及可挠曲性良好,在黏结剂和涂料中广泛应用。其缺点为固化速率慢、低温固化性不好,固化时需使用固化促进剂。
④其他类型固化剂。双氰胺、三氟化硼与胺类的配合物,作为潜伏性固化剂起到延长胺类固化剂使用寿命的作用,主要用于电器、层压板及粉末涂料领域。咪唑、叔胺作为酸酐固化剂的促进剂或单独用作固化剂使用。
另外,在由无机材料与有机材料构成复合材料时,还要用到一种称作“偶联剂”的物质。偶联剂是一种能增进无机物与有机高分子材料之间结合力的助剂,主要用于填料和玻璃纤维等增强材料的表面处理。20世纪40年代,硅烷偶联剂开始使用,目前仍是主要类别,主要用于含硅填料(包括硅酸盐类陶瓷和黏土制品)和玻璃纤维。钛酸酯类偶联剂出现于20世纪70年代中期,是很受注目的一类偶联剂,对非硅填料很有效。
2.2.1.7 抗静电剂
普通非极性聚合物的体积电阻率一般高达1~10Ω·cm,易积蓄静电而发生危险。抗静电剂是添加于塑料中或涂敷于塑料制品表面,防止塑料材料的静电危害的化学物质。其作用是降低表面电阻和体积电阻,适度增加导电性,从而减轻塑料在成型和使用过程中的电荷积聚。在日常生活中,不论是在产品的生产还是在运输与使用过程中,静电的危害是不容忽视的。用塑料传送带运输煤炭时,由于产生静电可能引起火灾和爆炸;因泡沫塑料带电导致油船燃烧;电影胶片生产过程中,当产生的静电大于500V时就会发生火花放电,造成胶片曝光。因此,增加高分子材料及其他材料的抗静电性能非常重要,抗静电助剂成为塑料工业中不可忽视的一种助剂。
抗静电剂多是表面活性剂,可使塑料表面亲和水分,离子型表面活性剂还有导电作用,因而可以使静电及时泄漏。阳离子型表面活性剂,如铵盐、季铵盐和烷基咪唑啉等是塑料常用的抗静电剂。按功能的持久性可把抗静电剂分为暂时性和永久性两类;按照使用方法则可把抗静电剂分为内部抗静电剂和外部抗静电剂。内部抗静电剂是添加型的,用量为0.1%~3.0%不等;外部抗静电剂是0.5%~2.0%的稀溶液,采用合适的方法涂布在塑料的表面。
①阴离子型抗静电剂。其耐热性及抗静电性效果好,但对透明制品有不利影响。此类抗静电剂的典型代表是烷基亚磷酸盐或磺酸盐等。
②阳离子型抗静电剂。其抗静电效果优异,但与其他表面活性剂型抗静电剂相比,耐热性低,多用于不受热的涂布型制品。此类抗静电剂多为季铵盐型表面活性剂。
③两性离子型抗静电剂。该抗静电剂既能与阴离子型抗静电剂配合使用,也能与阳离子型抗静电剂配合使用,主要有季铵内盐、两性烷基咪唑啉盐和烷基氨基酸盐等。两性咪唑啉是聚丙烯、聚乙烯优良的内部抗静电剂;烷基氨基丙酸的金属盐或二乙酸铵盐可作为塑料的外部或内部抗静电剂使用;烷基氨基丙酸的金属盐或二乙醇铵盐主要作为塑料的内部抗静电剂使用。
④非离子型抗静电剂。其主要用作材料的内部抗静电剂,包括多元醇、多元醇酯、聚氧乙烯烷基胺和炭黑等。其中,高级脂肪胺-聚氧乙烯加成物用量最大,适用于聚乙烯、聚丙烯等。炭黑可降低塑料的体积电阻率,可用于聚烯烃、聚氯乙烯的内部抗静电剂。
用作抗静电剂的主要表面活性剂见表2-2。
表2-2 用作抗静电剂的主要表面活性剂

2.2.1.8 润滑剂和脱模剂
在高分子材料加工过程中,聚合物熔体分子之间以及聚合物熔体与加工设备表面之间都存在着摩擦力,前者称为“内摩擦”,后者称为“外摩擦”。内摩擦会造成制品性能降低,外摩擦使制品表面粗糙。为改进聚合物熔体的流动性能,保证产品质量,对那些没有自润滑作用的材料,必须加入润滑剂方可便于加工。加到高分子材料中的这类物质被称为润滑剂,润滑剂是配合在聚合物树脂中,旨在降低树脂粒子、树脂熔体与加工设备之间以及树脂熔体内分子间摩擦,改善其成型时的流动性和脱模性的加工改性助剂,多用于热塑性塑料的加工成型过程,包括烃类(如聚乙烯蜡、石蜡等)、脂肪酸类、脂肪醇类、脂肪酸皂类、脂肪酸酯类和脂肪酰胺类等。
润滑剂根据其作用不同,可分为内润滑剂和外润滑剂两类。内润滑剂与聚合物有一定的相溶性,加入后可降低熔体黏度,减小聚合物分子间的结合力,从而削弱聚合物分子间的内摩擦。外润滑剂与聚合物的相容性很小,加入聚合物中的外润滑剂在成型加工过程中,易从熔体内部析出至表面而黏附设备的接触表面,也可将润滑剂直接涂覆于加工设备与聚合物接触的表面,形成润滑剂层,以降低熔体和模具接触表面间的摩擦(即外摩擦)。一般常用的内润滑剂为硬脂酸及其盐类、硬脂酸丁酯、硬脂酰胺等;外润滑剂有硬脂酸、石蜡、矿物油及硅油等。许多润滑剂,特别是外润滑剂都有脱模剂的作用。常用的脱模剂有硅油、脂肪酸皂、脂肪酸、石蜡、甘油、凡士林、滑石粉以及陶土等。
脱模剂时常涂敷于模具或加工机械的表面,有时也添加于基础树脂中,使模型制品易于脱模,并改善其表面光洁性。前者称为涂敷型脱模剂,是脱模剂的主体,后者为内脱模剂。酚醛、环氧、聚酯等塑料易与金属模具黏附,需在模具上擦脱模剂。石蜡、金属皂和有机硅是常用的脱模剂,尤其是聚二甲基硅氧烷,效果最佳,具有操作简便等特点,是工业上应用最为广泛的脱模剂。
2.2.1.9 防雾剂
在对日常生活和工作现象的观察中,人们时常会发现,用塑料膜包装果蔬或食品时,内壁气雾的形成使其透明度大大降低,看不清内装物;汽车用的塑料挡风玻璃或后视镜表面,由于湿度、温差大或者水沫凝结成雾,会严重影响驾驶者对周边以及道路的观察,进而会引发交通事故;农用塑料温室或大棚中,水分在薄膜表面凝结,会减小光照强度,影响农作物的生长和开花结果。因此,在使用中,塑料制品产生雾化是经常遇到的现象。
防雾剂又称防雾滴剂,是为了防止透明塑料薄膜、片材或板材在潮湿环境中,当温度达到水的露点以下时表面凝结成微细水珠,产生雾化而使用的一种助剂。防雾剂既可以少量掺加在透明制品的塑料配方中,也可以做成液态、膏剂,临时涂抹在塑料的表面。其防雾原理是提高塑料制品表面对水液的接触角,使水雾不能凝结和滞留。
2.2.1.10 防黄剂
所有的高分子材料,包括塑料、橡胶、纤维、涂料、油墨、胶黏剂等,当它们长期处于大气环境中时,在一定条件,如热能、光能、机械力等作用下会发生氧化老化反应,其现象表现为变色、泛黄、失重、透明度下降、粉化、表面开裂、力学性能(耐冲击和拉伸强度)下降等,其结果导致高分子材料失去使用价值。为了防止高分子材料变黄,在合成树脂的合成过程及高分子材料的加工过程中,需要加入防黄剂。通常的防黄剂为分子量较大的带有叔胺基团的低聚物,它们可以有效地防止高分子材料因热能、光能引起的泛黄和老化。因此,上面提到的热稳定剂、光稳定剂亦具有防黄效能,抗氧剂也能发挥防黄效果。在橡胶工业中,抗氧剂被习惯称为防老剂。
抗氧剂即抗氧化剂,在室温和较高的温度下,大多数聚合物都会发生速度不等的自动氧化反应,引起塑料发黄、降解和强度下降,凡能抑制或延缓此反应的物质均可称为抗氧剂。1918年人们开始用低分子的酚类抑制橡胶的氧化,20世纪30年代,烷基酚类、对苯二胺类等现代抗氧剂品种陆续问世。抗氧剂在塑料中用量虽较少(0.1%~1.0%),但却是聚烯烃、苯乙烯类树脂、聚氯乙烯、聚酰胺、聚缩醛等大吨位塑料的重要助剂。
塑料制品防黄剂的作用原理是:叔胺基团对氧化气氛不稳定,受到氧化“先行牺牲”,由此保护塑料免受“氧化”。
需要注意的是,防黄剂与氨纶纤维的相容性不好,又因为洗涤剂中常常添加含氯漂洗剂,氨纶纤维遇到含氯漂洗剂时会产生性能退化,这些防黄剂对染色氨纶纤维的褪色没有明显的抑制作用,耐高温性能也差,因此,防黄剂还未应用于较大规模的连续法生产氨纶纤维的工艺中。
2.2.1.11 填充增强助剂
填充和增强是提高塑料制品物理力学性能和降低配方成本的重要途径。塑料工业中所涉及的增强材料一般包括玻璃纤维、碳纤维、金属晶须等纤维状材料。填充剂是一种增量材料,具有较低的配合成本,包括碳酸钙、滑石粉、陶土、云母粉、二氧化硅、硫酸钙、粉煤灰、红泥以及木粉和纤维素等天然矿物、合成无机物和工业副产物。事实上,增强剂和填充剂之间很难区分清楚,因为几乎所有的填充剂都有增强作用。由于填充剂和增强剂在塑料中的用量很大,有的已经自成一个行业体系,习惯上已不在加工助剂的范畴讨论。应当说明的是,而今广泛研究的纳米增强材料对塑料的改性作用已经远远超出填充和增强的意义,它们的应用将给塑料工业带来一场新的革命。偶联剂是无机和天然填充与增强材料的表面改性剂,由于塑料工业中的增强和填充材料多为无机材料,配合量又大,与有机树脂直接配合时往往导致塑料制品加工和应用性能的下降。偶联剂作为表面改性剂能够通过化学作用或物理作用使无机材料的表面有机化,进而增加配合量并改善配合物的加工和应用性能。已经报道的偶联剂大致包括长碳链脂肪酸、硅烷类化合物、有机铬化合物、钛酸酯类化合物、铝酸酯类化合物、锆酸酯类化合物以及酸酐接枝的聚烯烃等。
在PVC中加入某些无机填料作为增强剂以降低成本,同时提高某些物理力学性能(如硬度、热变形温度、尺寸稳定性)与降低收缩率、增加电绝缘性和耐燃性。近年来,将无机填料纳米化,并将它应用到塑料中作为改性剂一直是研究热点,并已经有了部分研究成果,如纳米碳酸钙对PVC的增韧增强。这其中要解决的重要问题就是如何将纳米产品均匀而稳定地分散于塑料中。
在硬质挤压成型过程中,PVC制品一般的填料为碳酸钙和硫酸钡。对注塑制品,要求有较好的流动性和韧性,一般选用钛白粉和碳酸钙。硬质制品的填料量在10份以内,对制品的性能影响不大。近年来,某些企业为了降低成本,“无节制”地添加填料,这对制品的性能是致命的损害。
在软制品方面,加入适量的填料,会使薄膜具有手感很好的弹性,光面干燥而不显光亮,并有耐热压性高和永久形变小等优点。在软制品配方中常用到滑石粉、硫酸钡、碳酸钙、钛白粉与陶土等填料,其中滑石粉对透明性影响较小。生产薄膜时填料用量可达3份,过量则会影响性能,同时要注意填料的细度,否则易形成僵块,使塑料断裂。在普通级电缆附层中主要添加碳酸钙,绝缘级电缆附层中加入煅烧陶土则可以提高塑料耐热性和电绝缘性。此外,三氧化二锑也可作为填料加入软制品中,以提高制品耐燃性。
特别提出,普通的钙锌稳定剂在高填充量时会出现不同的颜色反应,主要为发红,这往往是钙锌稳定剂稳定性不够,而可能是碳酸钙中某种杂质的影响。建议选材时,尽量选用白度好的、未加活性成分的超微细轻质碳酸钙粉作填料,有可能减轻这种不良颜色反应。
对于聚丙烯材料,添加成核剂可以用来改变其结晶行为,进而改变其结晶形态、力学性、热学性和光学性的功能。在聚丙烯塑料材料中,适量添加成核剂HBP{一种以二[2,2'-亚甲基-双-(4,6-二叔丁基苯氧基)磷酸]羟基铝为主要组分,与有机羧酸盐复配得到的有机磷酸盐类},改性后的聚丙烯制品具有透明性好、光泽度高、力学性能和加工性能优良等特点,其使用范围也比较广泛。
研究发现,结晶性高聚物的冲击强度与球晶的大小和分布有关。例如聚甲醛(POM)虽然是一种具有优良综合性质的高结晶工程塑料,其强度和硬度高、刚性好,并且有良好的耐磨性和耐疲劳性,因而被用来代替有色金属和合金,广泛应用于汽车、电子电器、建筑、机械等行业。但由于聚甲醛的结晶度高(一般结晶度超过60%),制品存在缺口冲击强度低、成型收缩率大的缺点,与其他各种优异性能不匹配,需要进一步改进。改进聚甲醛材料性能的主要方法有两种:严格控制加工条件和加入成核剂。
2.2.2 技术发展趋势
塑料助剂作为塑料制品的重要原料,不仅在加工过程中能起到改善性能、提高效率的作用,还能改进塑料制品的性能,延长使用寿命,增加它的使用价值。据中国前瞻产业研究院发布的《中国塑料助剂行业深度调研与投资战略规划分析报告前瞻》报道,我国的塑料助剂行业是随PVC行业的发展而发展起来的。同时,随着合成树脂行业的发展,塑料助剂行业的应用领域不断拓宽,产品品种有了较大幅度的增加,塑料助剂行业已成为门类比较齐全、产品品种繁多的重要行业,在技术水平、产品结构、生产规模和科技人员的素质等方面都有了长足的发展,基本满足了下游行业对塑料助剂产品的需求。目前,我国塑料助剂行业已经形成产值300亿元以上的产业,其中约有50亿元的出口。
根据Marketsand Markets预计,2014~2019年期间,全球塑料助剂市场复合年增长率将达5%,至2019年达455亿美元,届时中国将替代美国成为全球最大的塑料助剂消费国。2013年,包装行业是塑料助剂消费增长最迅速的应用领域,其次是汽车行业。就品种而言,增塑剂所占的份额仍然是最大的,增长速率最大的类别则是阻燃剂。塑料助剂作为通用塑料工程化、工程塑料高性能化不可或缺的关键成分。我国“十一五”期间,塑料工业呈现明显的产业聚集发展态势,规模企业数量增长迅速,产业结构逐渐向规模化、集约化调整,塑料助剂产业也正向规模化、集约化方向调整,这在增塑剂、热稳定剂、冲击改性剂和加工助剂方面尤为明显。助剂行业的发展主要集中在通用品种的规模化生产,较少看到结构性创新产品出现,同时生产大多采用国外企业专利技术。所以,高性能的绿色、环保、无毒、高效塑料助剂的研发和生产已成为未来我国塑料助剂行业发展的主攻方向。增塑剂要提高非邻苯二甲酸酯类产量,如环氧大豆油和偏苯三酸酯类稳定剂;应降低铅盐类比例,提高钙/锌复合类、低铅稀土类、水滑石类以及有机热稳定剂产量;阻燃剂应降低卤素类比例,大力发展无机阻燃剂。同时要积极应对欧盟的环保法规,以及国内外对无毒环保产品的要求。塑料助剂企业应该和高校、科研院所联合起来改变不合理的产品结构,开发环保型助剂品种。
塑料助剂行业的技术发展方向是适应市场的发展变化,调整、优化产品结构;重视技术储备,积极开发新产品、新技术;努力搞好节能减排,推进清洁生产;加强管理,降低生产成本。应关注聚氯乙烯树脂的改性和聚氯乙烯制品加工中使用的助剂、石墨烯在塑料加工中的应用以及工程塑料改性和所用助剂等热点问题,尤其是生物基塑料及其使用助剂的热点。
替代邻苯二甲酸酯类增塑剂的无毒品种是柠檬酸酯类,主导产品是柠檬酸三丁酯和柠檬酸三辛酯。与低分子量增塑剂相比,聚酯类物质的挥发性低,耐油及耐脂肪族或芳香族碳氢化合物的抽出,在油漆与橡胶中耐迁移,且耐老化性能优异,具有耐抽出、耐高温和迁移性小等特点,享有“永久性增塑剂”之称,是发展较快的一类增塑剂。
世界各国热稳定剂消费结构不同,但总体发展趋势是向着低毒、无害、高效、多功能的方向发展。尤其是无镉和低铅无尘化的开发,在世界范围内受到重视,无铅化已经成为热稳定剂的主流发展方向。我国具有稀土资源优势,稀土类热稳定剂应作为我国发展无铅热稳定剂的首选方向。我国已有企业在全球率先实现了稀土热稳定剂的产业化,主要是镧、铈类稀土产品,安全卫生,无放射性,已在儿童塑料玩具生产中使用多年,在国际市场上享有相当的知名度。
自20世纪70年代国外阻燃剂开始迅速发展,消费量和品种急剧上升,每年大约以6%~8%的速度增长。在塑料行业众多的助剂中阻燃剂消费量已跃居第2位,成为仅次于增塑剂的大品种。美国商业通信公司(BCC)预计阻燃剂年增长率为5.2%。阻燃剂通常分为添加型和反应型:添加型阻燃剂多用于热塑性塑料中,是目前世界各国产量最大的阻燃剂,占阻燃剂总产量的90%;反应型阻燃剂多用于热固性塑料中。阻燃剂按化学结构可分为无机阻燃剂和有机阻燃剂:无机阻燃剂主要有锑化合物、无机硼化合物、无机磷系阻燃剂、无机氢氧化物等;有机阻燃剂包括有机卤系阻燃剂和有机磷系阻燃剂。
①锑阻燃剂。锑产品价格高、发烟量大,三氧化二锑是卤素阻燃剂必不可少的协同剂,因此对三氧化二锑颗粒细度要求越来越细,不仅可大大减少用量、提高阻燃性,而且发烟量也大大减少。现在的细度一般均在几微米到0.01μm,如日本的精工株式会社开发的Patox,平均粒径为0.01~0.02μm。贵州榕江风华锑品化工厂开发的超细高纯活性氧化锑,平均粒径为0.02μm,含量99.999%。PolycomHuntsman公司开发的NyacoIADP480是粒径小于0.1μm的五氧化二锑,添加1%可在PP中起到良好阻燃作用,且不会对PP的冲击强度、透明性等产生影响。另外,采用三氧化二锑与氢氧化铝、硼酸锌、氟硼酸盐等复配,不仅可减少三氧化二锑的用量,且发烟量也大为降低。
②溴系阻燃剂。溴系阻燃剂尽管发烟量大,因环保问题受欧盟限制,但由于阻燃性能好、用量少、对产品性能影响小,在今后的相当长时间内仍为阻燃剂的主力。国际上溴系阻燃剂发展的新特点是继续提高溴含量和增大分子量。如美国Ferro公司的PB-68主要成分为溴化聚苯乙烯,分子量15000,含溴68%。溴化学法斯特公司和Ameribrom公司分别开发的聚五溴苯酚基丙烯酸酯,分子量30000~80000,含溴70.5%。这些阻燃剂特别适合于各类工程塑料,在迁移性、相容性、热稳定性、阻燃性等方面均大大优于许多小分子阻燃剂,有可能成为今后的更新换代产品。
③磷系阻燃剂。磷系阻燃剂大都是液体,主要用于PU、PVC等塑料。小分子磷系阻燃剂的主要缺点是挥发性大、耐热性不高,目前正努力开发大分子量的化合物和低聚物,如GreatLake公司的Firemacster836为卤化磷酸酯,含有磷、溴、氯,具有很低的黏度,特别适合用于浇注制品和PU软泡塑料中。具有阻燃和增塑、阻燃和交联的多功能化是磷系阻燃剂发展的另一个主要方面,阻燃增塑剂(特别是低温下有增塑作用)主要用于PVC制品中,如国内生产的二异丙苯磷酸酯。阻燃交联剂是一些具有反应活性的含磷多元醇类,不仅可用作PU的反应型阻燃剂,而且还与溴系阻燃剂并用于环氧树脂中,可大大减少溴阻燃剂的用量。
磷系阻燃剂今后还要向低毒化发展,不仅解决产品本身的毒性,还要考虑燃烧分解产物的毒性以及废品的环境污染问题,甚至还要考虑生产、销售、储运过程中的毒性问题。
④非卤化无机阻燃剂。绝大多数有机阻燃剂含有卤素,在燃烧时发烟大且产生有毒气体,因此近年来阻燃材料非卤化要求越来越迫切。发达国家的一些塑料制品已开始禁止使用卤素阻燃剂。欧盟关于环保的“两个指令”已作出明确限制;此前德国环境团体PAL从1995年开始在电子设备的外壳中禁用溴化物及氧化锑;瑞典TC095规定在电气及电子设备中凡是超过25g的塑料零件,均禁用有机溴化物及有机氯化物。虽然目前卤素阻燃剂在全球仍占主流,但被非卤素阻燃剂取代的趋势已明朗化。在非卤素阻燃剂中无机阻燃剂是一个重要组成部分,高性能非卤化无机阻燃剂可大量添加到聚烯烃中,而不影响制品力学性能。
⑤氢氧化铝新品种。开发新品种,主要包括:a.增加氢氧化铝粒子表面积(即微细化及超微细化),使粒子表面水蒸气分压下降,可提高氢氧化铝耐热性能且使材料力学性能、阻燃效果明显增强,有试验表明,同样配方情况下氢氧化铝平均粒径为5μm时氧指数为28,粒径小于1μm时氧指数达到33。美国SOLEM公司开发的新品种Micrai1000、Micrai1500,公称粒径分别为1.0μm、1.5μm,而且粒度分布范围窄,且可改善注塑和挤塑加工工艺。美国Climax公司的Hydrax系列氢氧化铝有5个品种,均有极窄的粒度分布范围。Alcoa公司的S-13超细氢氧化铝粒径在0.2~0.5μm间,粒度分布范围控制严格,而且硅含量低,同时还能与较大粒径的氢氧化铝混合,以提高装填密度和降低黏度。b.氢氧化铝与热分解温度高的物质反应,可合成热分解温度介于两者之间的新品种,如氢氧化铝和碳酸钠的混晶在300~350℃下分解放出水和二氧化碳,对氯化氢和烟有较强抑制作用,是PVC、聚烯烃的优良阻燃剂。c.减少氢氧化铝中离子不溶物(特别是氧化钠)的含量,使其质量分数小于0.2%,如:日本轻金属推出的高纯度氢氧化铝品种氢氧化铝含量大于99.9%;美国SOLEM公司开发的新品种氧化钠含量低超微细化、比表面积大、电气性能优异,可在290℃下使用。
⑥改进表面的新品种。氢氧化铝一般用硅烷偶联剂、钛酸酯偶联剂和硬脂酸(盐)等进行表面处理,国内这方面刚刚起步,国外已更进一步进行了新型特殊功能氢氧化铝表面改性剂的开发。SOLEM公司用硅烷新工艺处理及有机硅酮包覆处理的氢氧化铝,在PP、PE中添加量达60%~70%仍可很好加工,且对物性和阻燃性有提高。
氢氧化镁新品种:a.有许多人认为氢氧化镁可作氢氧化铝的代用品,但由于氢氧化镁内部的物理结晶水、强极性等,导致与聚烯烃相容性差,虽然偶联剂偶联后力学性能有所提高但不太明显,大量填充氢氧化镁于聚烯烃中技术上还不成熟。但是低填充量(<30%)的氢氧化镁与氢氧化铝共用时可提高材料碳化作用,且w[Mg(OH)2]∶w[Al(OH)3]=1∶1时,在PE中有最佳协同作用。b. Morton国际工业化学和添加剂公司在Versamag702氢氧化镁上涂覆专有的脂肪酸,可改进填充聚合物的流变性和物理性能,添加50%~60%时填充物流动性仍很好。还有用控制微米级晶体生长的方法制取的氢氧化镁固溶体Finemagsn,其结构特点为高浓度的二价金属离子,主要分布在晶体表面附近并有高的防酸防水性,使其在配方中的加入量低于普通高纯氢氧化镁。
添加无机增效剂的新品种:少量的阻燃增效剂可使氢氧化铝填充材料性能有明显的改善,如抑制滴落、改善力学性能。与氢氧化铝能起到协同作用的无机阻燃增效剂范围很广,主要有金属氧化物与硼酸锌、磷系化合物(红磷、磷酸酯)、硅系化合物、金属硝酸盐(硝酸铜、硝酸银)、聚磷酸铵等。
⑦膨胀型阻燃剂。膨胀阻燃聚合物的研究为聚合物阻燃技术开辟了新途径,膨胀阻燃聚合物基本克服了传统阻燃技术中的缺点,有如下优点:高阻燃性、无熔滴行为,对长时间或重复暴露在火焰中有较好的抵抗性;无卤、无氧化锑;低烟、少毒、无腐蚀性气体产生。膨胀型阻燃剂主要成分:a.酸源,一般指无机酸或能在燃烧加热时在原位生成酸的盐类,如磷酸、硫酸、硼酸及磷酸酯等;b.碳源,一般指多元醇化合物,如季戊四醇、乙二醇及酚醛树脂等;c.发泡源,含氮的化合物,如尿素、双氰胺、聚酰胺、脲醛树脂等。膨胀型阻燃剂的研究主要是针对PP进行的,已经商品化的膨胀型阻燃剂大部分用于PP、聚氨酯中。如Montefluos公司的SpinflamMF 82,以磷、氮为活性协同组分,不含卤素和氧化锑,含磷21%、氮18%。它阻燃的PP阻燃剂用量24%时氧指数达37、抗弯模量增加30%~40%。此外还有Great Lake公司的NH-1197、NH-1151等。直到20世纪90年代初才有人致力于膨胀阻燃PE的阻燃研究,并取得了一些较好的效果。
⑧消烟技术。在火灾中烟是最先产生和最易致死且贻误救火时机的因素,据统计,火灾中的死亡人数有80%是窒息所致,所以当代的“阻燃”是与“抑烟”相提并论的,而且对某些高聚物,如对PVC而言“抑烟”比“阻燃”更为重要。含卤高聚物和卤系阻燃剂以及锑化合物是主要的发烟源,因此除了阻燃剂的非卤化是减少发烟量的主要途径外,对PVC含卤高聚物采用添加消烟剂和三氧化二锑复配是解决发烟的另一条措施。钼化物迄今被认为是最好的消烟剂,如Shemlnwilliams公司开发的Kegad911A是含少量锌和钼的配合物,在PVC中添加4%可减少发烟量1/3。由于钼化物价格昂贵,采用硼酸锌、二茂铁、氢氧化铝、硅的化合物与少量钼化物复配,是解决消烟问题较现实的途径,如Climax公司开发的Moly-FR-201是钼酸铵和氢氧化铝的复合物,在PVC中添加5~10份,发烟量可减少43%。
⑨阻燃剂微胶囊化技术。微胶囊化技术具有可防止阻燃剂迁移、提高阻燃效力、改善热稳定性、改变剂型等许多优点,对组分之间复合与增效及制造多功能阻燃材料也十分有利。国内目前正在探索,如湖南塑料研究所已研制了微胶囊化红磷母料,成功应用在PE、PP、PS、ABS树脂中且阻燃效果良好。安徽化工研究院研制出的微胶囊化磷酸二溴苯酯、微胶囊化氯蜡-70等,也取得了很好的效果。
⑩交联技术。交联高聚物的阻燃性能比线型高聚物好得多,因此在热塑性塑料加工中添加少量交联剂使高聚物变成部分网状结构,不仅可改善阻燃剂的分散性,还有利于高聚物燃烧时在凝聚相产生结炭作用,有效提高阻燃性能并能增加制品的物理力学性能及耐候、耐热性能等,如在软质PVC中加入少量的季铵盐,使其受热形成交联的阻燃材料。
另外,还可采用辐射法加入金属氧化物及交联剂等方法,也可采用高聚物交联直接生成阻燃单体技术,即直接在聚合反应前使单体具有阻燃性,从而使生成的聚合物成为阻燃材料。
2.2.3 现行主要品种简介
塑料助剂新品种的不断开发,极大地促进了塑料在增强、增韧、阻燃、耐候、耐腐蚀、抗静电、抗菌和多功能化等方面的作用,提高了塑料的性能和应用范围,从而推动了塑料工业的进一步发展。随着人们对塑料产品质量、性能要求的提高,开发高效、多功能的塑料添加剂产品已经成为国内外企业及大公司的投资重点。近几年来,塑料助剂行业大部分企业根据市场需求,积极开发新产品,革新工艺,提高产品质量,适应经济形势的发展对企业提出的要求。高效、特效、无毒、无公害、复配多功能化是塑料添加剂总的发展趋势。
下面就常用塑料助剂中的增塑剂、热稳定剂、抗冲击改性剂、抗氧化剂进行简要介绍。
2.2.3.1 增塑剂
作为现代塑料工业最大的助剂品种,在数量、产量、消费量上为最大的一类助剂,增塑剂对促进塑料工业特别是聚氯乙烯工业的发展起着决定性的作用。目前,各种新型塑料已渗透到工农业、运输、交通、医药、食品、服装、建筑、国防等各个领域,使用的产品包括塑料、橡胶、黏合剂、纤维素、树脂、医疗器械、电缆等成千上万种。比如一般常使用的保鲜膜,一种是无添加剂的PE(聚乙烯)材料,但其黏性较差;另一种广被使用的是PVC(聚氯乙烯)保鲜膜,有大量的增塑剂,以让PVC(聚氯乙烯)材质变得柔软且增加黏度,非常适合生鲜食品的包装。除此之外的广泛添加增塑剂的产品是PVC制造的儿童玩具,欧盟已经明确规定塑料玩具中增塑剂的含量需在0.1%以下。女性经常使用的香水、指甲油等化妆品,则以邻苯二甲酸酯类作为定香剂,以保持香料气味,或使指甲油薄膜更光滑。至2012年,全球增塑剂总产能约750万吨/年,全球增塑剂总产量为590万吨/年,其中北美占22%、亚太地区占38%、欧洲占25%、其他地区占15%。PVC是增塑剂的最大用户,占全球增塑剂总用量的95%,在北美所占比例也稍高于90%。因为增塑剂与非常成熟的软PVC市场密切相关,因此发展缓慢,但保持稳定增长势头,预计将以年均2.5%的速率增长。聚烯烃、苯乙烯、工程塑料、聚乙烯缩丁醛和纤维素类所用增塑剂的量很少。在增塑剂品种上,邻苯二甲酸酯类占主要地位(占69%),其余是脂肪族类(占8%)、环氧类(占7%)、苯三酸酯类(占4%)及其他(占2%)。
增塑剂生产趋势向大型化、连续化、计算机控制化发展,单套生产能力已经达到10万吨/年。多品种系列化生产具有适应市场能力强、生产灵活性大的特点,以满足不同塑料加工制品对特殊功能增塑剂品种的需求。DOP的性价比较高,产量及消费量仍占邻二甲酸酯类的主导地位,下来是DINP(邻苯二甲酸二异壬酯)、DIDP(邻苯二甲酸二异癸酯)。另外,直链醇酯的发展也很快,有望成为邻苯二甲酸酯类的重要品种。除邻苯二甲酸酯类增塑剂外,耐寒性优良的脂肪酸酯类、无毒且稳定性强的环氧酯类、耐高温的偏苯三酸酯类、不迁移的聚酯类、阻燃性好的磷酸酯类等在增塑剂结构中都占一定的比例,形成结构合理的增塑剂生产体系。
一种理想的塑料增塑剂应具有如下性能:①与树脂有良好的相容性;②塑化效率高;③对热、光稳定;④挥发性差;⑤迁移性差;⑥耐水、油和有机溶剂的抽出;⑦低温柔性良好;⑧阻燃性好;⑨电绝缘性好。根据分子量的大小,增塑剂可分为单体型塑料增塑剂和聚合型塑料增塑剂;根据物状可分为液体塑料增塑剂和固体塑料增塑剂;根据性能可分为通用塑料增塑剂、耐寒塑料增塑剂、耐热塑料增塑剂、阻燃塑料增塑剂等。根据塑料增塑剂化学结构分类是常用的分类方法。
(1)邻苯二甲酸酯类 邻苯二甲酸酯类是目前最广泛使用的主增塑剂,品种多、产量高,并具有色泽浅、毒性低、电性能好、挥发性差、气味少、耐低温性一般等特点。
①邻苯二甲酸二辛酯(代号DOP),无色油状液体,有特殊气味。
②邻苯二甲酸二异辛酯(代号DIOP),几乎是无色的黏稠液体,溶于大多数有机溶剂和烃类。
③邻苯二甲酸二异癸酯(代号DIDP),黏稠液体,溶于大多数有机溶剂和烃类,不溶于或微溶于甘油、乙二醇和某些胺类。它的挥发性比DOP小,耐迁移,是一种低挥发性增塑剂,又耐老化,电性能好,但相容性差些。
④邻苯二甲酸二异壬酯(代号DINP),透明油状液体,在高温下其挥发性只有DOP的一半。
⑤邻苯二甲酸二丁酯(代号DBP),无色透明液体,具有芳香族气味,溶于大多数有机溶剂和烃类。DBP对PVC的临界塑化温度为90~95℃。
⑥邻苯二甲酸二异丁酯(代号DIBP),无色透明液体。在PVC农用薄膜中使用DIBP时,曾发现由于它的析出致使水稻烂秧的问题。
⑦邻苯二甲酸丁苄酯(代号BBP),透明油状液体,溶于有机溶剂和烃类,不溶于水。BBP对PVC的临界塑化温度为96~100℃。
⑧邻苯二甲酸二甲酯(代号DMP),无色油状液体,微带芳香族气味,常温下不溶于水,和脂肪烃混溶,与大多数树脂相容性良好。
⑨邻苯二甲酸二乙酯(代号DEP),无色油状液体,无毒,微带芳香族气味,溶于大多数有机溶剂。
⑩邻苯二甲酸二环己酯(代号DCHP),具有芳香族气味的白色结晶状粉末,溶于大多数有机溶剂,在热的汽油和矿物油中完全溶解,微溶于乙二醇类和某些胺类。
对苯二甲酸二辛酯(代号DOTP),与DOP的物理性能相似,制品的力学性能也相似,但DOTP的挥发性比DOP差得多。
(2)脂肪酸酯类 脂肪酸酯类的低温性能很好,但与聚氯乙烯的相容性较差,通常只作为耐寒的聚氯乙烯制品的副增塑剂与邻苯二甲酸酯类并用,最常用的品种是己二酸二辛酯和癸二酸二辛酯。
①己二酸二辛酯(代号DOA),无色无臭液体,无毒,溶于大多数有机溶剂,微溶于乙二醇类,不溶于水,DOA对PVC的临界塑化温度为121~125℃。
②己二酸二异癸酯(代号DIDA),清澈易流动的油状液体。
③壬二酸二辛酯(代号DOZ),几乎是无色的透明液体。
④癸二酸二丁酸(代号DBS),几乎是无色的液体。
⑤癸二酸二辛酯(代号DOS),无色的油状液体,不溶于水,溶于醇、苯、醚等有机溶剂。
⑥癸二酸二异辛酯(代号DIOS),无色清澈液体,溶于酮、醇、酯、芳香烃和脂肪烃等大多数有机溶剂,微溶于胺和多元醇。
⑦二(2-乙基丁酸)三缩乙二醇酯(代号3GH),是安全玻璃用聚乙烯醇缩丁醛薄膜中最为广泛使用的增塑剂,同时,对于纤维素塑料、丙烯酸酯塑料和聚氯乙烯也是良好的增塑剂。
(3)磷酸酯类 磷酸酯与聚氯乙烯等树脂有良好的相容性,透明性也好,但有毒性,既是增塑剂,又是阻燃剂。芳香族磷酸酯的低温性能很差,而脂肪族磷酸酯的低温性能较好,但热稳定性较差,耐久性不如芳香族磷酸酯。其主要品种是磷酸三甲苯酯和磷酸三苯酯。
①磷酸三甲苯酯(代号TCP)。
②磷酸三苯酯(代号TPP),微带芳香气味的白色针状结晶,微溶于乙醇、醚、苯、氯仿、丙酮。
③磷酸二苯一辛酯(代号DPOP),浅黄色透明油状液体。
④磷酸甲苯二苯酯(代号CDPP),清澈无臭的油状液体。
(4)环氧酯类 环氧增塑剂是近年来应用很广的助剂,它既能吸收聚氯乙烯树脂在分解时放出的氯化氢,又能与聚氯乙烯树脂相容,所以它既是增塑剂又是稳定剂,主要用作耐候性高的聚氯乙烯制品的副增塑刑。其主要品种有环氧大豆油、环氧脂肪酸辛酯等。
①环氧大豆油。大豆油是一甘油的脂肪酸酯混合物,环氧大豆油是一种黄色油状液体,无毒,溶于大多数有机溶剂和烃类。环氧大豆油与聚酯类增塑剂并用,可以避免后者向外迁移。
②环氧脂肪酸丁酯。因脂肪酸成分不一,环氧脂肪酸丁酯有环氧硬脂酸丁酯、环氧糠油酸丁酯、环氧大豆油酸丁酯、环氧棉子油酸丁酯、环氧菜油酸丁酯、环氧妥尔油酸丁酯、环氧苍耳油酸丁酯、环氧猪油酸丁酯等品种。
③环氧脂肪酸辛酯(代号ED3)。因脂肪酸结构的不同而有不同品种,如环氧硬脂酸辛酯、环氧大豆油酸辛酯、环氧妥尔油酸辛酯等。
④环氧四氢邻苯二甲酸二辛酯(代号EPS),无色至浅黄色油状液体。
(5)聚酯类和偏苯三酸酯类 聚酯增塑剂一般塑化效率都很低、黏度大、加工性和低温性都不好,但挥发性差、迁移性差、耐油和耐肥皂水抽出,因此是很好的耐久性增塑剂,通常需要与邻苯二甲酸酯类主增塑剂并用。聚酯类多用于汽车、电线电缆、电冰箱等长期使用的制品中,主要品种有己二酸、癸二酸等脂肪族二元酸与一缩二乙二醇、丙二醇、丁二醇等二元醇缩聚而成的低分子量聚酯。偏苯三酸酯是一类性能十分优良的增塑剂,兼有单体型增塑剂和聚合型增塑剂的优点,挥发性差、迁移性差,耐抽出和耐久性类似于聚酯增塑剂,而相容性、结合性和低温性又类似于邻苯二甲酸酯类。
①聚癸二酸丙二醇酯,不同分子量的聚癸二酸丙二醇酯增塑剂都可以溶于丙酮、二氯乙烷、乙醚、苯、甲苯、二甲苯、氯仿,部分溶于乙醇、丁醇和脂肪烃。
②偏苯三酸三辛酯(代号TOTM),无色至淡黄色黏稠油状液体。
③偏苯三酸三(正辛正癸酯)(代号NODTM),无色至淡黄色油状液体。
(6)含氯增塑剂 目前最广泛使用的含氯增塑剂是氯化石蜡。氯化石蜡价格低、电性能优良、具有难燃性,但相容性较差,热稳定性也差,仅用作辅助增塑剂。
①氯化石蜡,它是一种金黄色或琥珀色黏稠液体,不燃,挥发性极微,溶于大部分有机溶剂,不溶于水和乙醇,加热至120℃以上会自行分解,放出氯化氢气体。铁、锌等金属的氧化物会促进其分解,而含氯量较高的氯化石蜡的阻燃性也较好。
②氯烃-50是一种清澈黏稠液体,无味无毒,不燃,不溶于水,微溶于醇,易溶于苯、醚。
(7)烷基磺酸酯类 这类增塑剂与树脂的相容性较好,可作主增塑剂用。若与邻苯二甲酸酯类主增塑剂并用则效果更好。它的力学性能、电性能、耐候性良好,但耐寒性较差。
①石油磺酸苯酯(代号M-50),淡黄色透明油状液体。
②氯化石油酯,氯化烷基磺酸苯酯和氯化石蜡的混合物,淡黄色透明油状液体。
(8)多元醇酯类 多元醇酯主要有双季戊四醇酯和乙二醇酯。双季戊四醇酯的挥发性弱、耐抽出性良好、难于热分解和氧化、电绝缘性能好,是优良的耐热增塑剂,适用于高温电线绝缘配方中,但价格昂贵。乙二醇酯耐寒性虽然很好,但色泽较深、挥发性较强。
①双季戊四醇酯(代号PCB),可分为醚型和酯型,这两类双季戊四醇酯均为淡黄色黏稠油状液体,能溶于有机溶剂,不溶于水。
②59酸乙二醇酯(代号0259),淡黄色透明状液体。
(9)其他 樟脑,有特殊气味的结晶物,挥发性极强,微溶于水,溶于大多数漆用溶剂。它是硝酸纤维素和纤维素酯的优良增塑剂。
毒性情况:增塑剂种类繁多,各种增塑剂毒性数据差别很大,比较而言,氯化烃类增塑剂(氯化石蜡)因为含有感光物质(荧光物质)而毒性较高,柠檬酸酯类、环氧大豆油(ESO)增塑剂则被视为无毒增塑剂。
常见的邻苯二甲酸酯(也叫酞酸酯)类中,DEHP的毒性系数T=200,大白鼠和家兔的经口LD50大于3000mg/kg(体重,下同),因此为低毒物质。法国癌症研究所用含该品0.05%的饲料饲喂四代大白鼠,结果表明无致畸性和致癌性。美国环境卫生署科学研究所用更大剂量DEHP喂养的雄性小白鼠和雄性大鼠输精管退化,前肢下垂,体细胞肥大。猴子(狨)在多次接受含有DEHP的血浆后,肝组织发生病变。其他常见邻苯二甲酸酯类塑化剂的毒性:DBP(邻苯二甲酸二丁酯)毒性系数T=50,对动物(大白鼠、家兔、狗)的经口LD50大于8000mg/kg,因此为无毒物质。100mg/kg的剂量喂饲大白鼠五代,300mg/kg和500mg/kg的剂量饲喂大白鼠三代,动物的生殖、生长曲线、组织学检查等均未出现任何异常,也无致癌性。有研究报告称,将啮齿动物暴露于DBP中会引起睾丸萎缩,或是生殖力下降,另有研究报告则称DBP有抗癌作用。DBP在抗癌研究中具有新的药理功能,小鼠腹膜内注射S180细胞而不注射DBP时,38天后,小鼠出现腹水肿瘤,全部死亡。但注有DBP的S180细胞的小鼠存活时间延长,而且有33.3%的小鼠在3个月内很正常。骨髓悬浮液在马血清和鼠肺的培养液中加入DBP时,可见白血病细胞明显减少,且迅速退化。对自身移植骨髓,净化残余的癌细胞非常有效,但是其他邻苯二甲酸酯塑化剂则无此功能。
2.2.3.2 热稳定剂
热稳定剂是塑料加工助剂中重要类别之一,热稳定剂与PVC树脂的诞生和发展同步,也主要用于PVC树脂加工中,因此热稳定剂与PVC树脂、PVC中软硬制品的比例有密切关系。
由于聚氯乙烯能和许多其他材料,如增塑剂、填料及其他聚合物相容,因而被认为是最通用的聚合物之一。其主要缺点就是热稳定性差。添加剂的使用可改变聚氯乙烯的物理外观和工作特性,但不能防止聚合物的分解。虽然在物理的(如热、辐射)和化学的(氧、臭氧)因素作用下,聚合物材料总是会逐渐被破坏,但其中添加的稳定剂可有效阻止、减缓材料的降解。
关于PVC的破坏过程,人们提出了各种机理:热氧化分解,无氧情况下自由基的交联,立规结构对降解的影响,光降解,氧化脱氯化氢,辐射降解,制件加工过程中引起的临界应力导致的分子链断裂以及PVC分子中支化点对降解的影响等。从化学上来说这些机理是非常相似的,并且可以直接与PVC的物理状态相联系。PVC降解最重要的原因是脱氯化氢。随着脱氯化氢过程的继续,出现共轭双键,聚合物吸收光的波长发生变化,当在一个共轭体系中出现6或7个多烯结构时,PVC分子吸收紫外光,从而呈现黄色。这里最多能产生0.1%的氯化氢。随着降解过程的继续,双键增加,吸收光波长变化,PVC的颜色也逐渐变深(深黄色、琥珀色、红棕色,直至完全变黑)。当聚合物进一步受损时,继而发生氧化,链断裂,最后交联。
为了最大限度地弥补PVC均聚物和共聚物的严重缺陷,需要用稳定剂消除引起开始脱氯化氢的不稳定部位,或作为氯化氢的清除剂,或当自由基产生时便与之反应,或作为抗氧剂,或改变多烯结构以阻止颜色变化、分子链断裂和交联。稳定剂必须与PVC体系相容,不会损害材料体系整体的美感,并且还应具有调节润滑的性能。
如要防止或延缓像PVC类的聚合材料的热老化,要么消除高分子材料中热降解的引发源,如PVC中烯丙基氯结构和不饱和键;要么消除所有对非链断裂热降解反应具有催化作用的物质,如由PVC上解脱下来的氯化氢等,才能阻止或延缓此类聚合材料的热降解。因此,所选择和使用的热稳定剂应具有以下的功能:
①能置换高分子链中存在的活泼原子(如PVC中烯丙位的氯原子),以得到更为稳定的化学键和减小引发脱氯化氢反应的可能性;
②能够迅速结合脱落下来的氯化氢,抑制其自动催化作用;
③通过与高分子材料中所存在的不饱和键进行加成反应而生成饱和的高分子链,以提高该合成材料热稳能,抑制聚烯结构的氧化与交联;
④对聚合材料具有亲和力,而且是无毒或低毒的;
⑤不与聚合材料中已存在的添加剂,如增塑剂、填充剂和颜料等发生作用。
当前使用的热稳定剂并不能完全满足上述的要求,所以在使用过程中必须结合不同聚合材料的特点来选用不同性能的热稳定剂。有时还必须与抗氧剂、光稳定剂等添加剂配合使用,以减小氧化老化的可能。
对某一具体的树脂、复合组分、最终用途选定好稳定剂,可得到优良的PVC掺混物。PVC树脂的敏感性以及各种添加剂的稳定作用或有害效应可能是多种多样的,这需要逐一加以注意。因此,必须注意到像树脂对锌的敏感性,金属皂润滑剂的稳定性能,环氧及磷类增塑剂的工作特性,以及各种颜料及其他组分的影响等现象。加工技术和产品用途决定了对最终稳定性的要求,因此也决定了具体配方的稳定剂类型和用量。必须对加工设备的类型、剪切速率以及PVC掺混物可能经受的热过程给予重视,在必须知道管理机关要求的同时,还必须考虑到制成品的物理外观和耐久性。
PVC稳定剂通常是无机物或有机金属化合物,这就表明含有阳离子或有机化合物,通常按化学类别进行分类。通常,无机物和金属有机化合物是基本的(或主要的)稳定剂,而有机物则是次要的或辅助的稳定剂。稳定剂主要根据锡、铅以及含A族金属的混合物(如钡、铜、锌)进行分类。稳定剂协同的混合物很普遍,通常包括各种烷基有机锡化合物和烷基盐(化合物)以及辅助的添加剂,如锌皂、亚磷酸盐、环氧化物、甘油酯、紫外线吸收剂、抗氧剂等。显然,大多数协同组合物具有专用性,因此还没有发现它们具有全面的共性。
热稳定剂的主要类别有碱式铅盐、金属皂类、复合稳定剂、有机锡和副热稳定剂。
(1)碱式铅盐 即盐基性铅盐,是用于聚氯乙烯最早,目前仍大量采用的一种热稳定剂,呈碱性,故能与产生的HCl反应而起稳定作用。其耐热性、电绝缘性、耐候性均较好,价格低,但有毒,不透明,分散性差。从毒性、抗污性和制品透明性来看,铅盐不理想。但它的稳定效果好、价格低廉,故仍大量用于廉价的PVC挤出和压延制品中。因它有优良的电性能和低吸水性,故被广泛地用作PVC的电绝缘制品、唱片和泡沫塑料的稳定剂。
①三碱式硫酸铅,也称三盐基硫酸铅,白色粉末,相对密度7.10,有甜味,有毒,易吸湿,无可燃性和腐蚀性,不溶于水,但能溶于热的乙酸胺,潮湿时受光后会变色分解,折射率2.1,常用作电绝缘产品的稳定剂。
②二碱式亚磷酸铅,是一种细微针状结晶粉末,相对密度6.1,有味甜,有毒,200℃左右变成灰黑色,450℃左右变成黄色。该物质不溶于水和有机溶剂,溶于盐酸。其折射率2.25,有抗氧化作用,是一种优良的耐气候性稳定剂。
(2)金属皂类 金属皂类也是一类广泛使用的聚氯乙烯热稳定剂,主要是硬脂酸和月桂酸的镉、钡、钙、锌、镁盐。通常将镉皂和钡皂、钙皂和锌皂并用,以产生协同效应。镉皂毒性大,钡皂也有一定毒性,但钙皂和锌皂无毒。其稳定作用是由于它能在聚氯乙烯分子链上开始分解的地方起酯化作用。稳定作用的强弱与金属皂的金属比、羧酸类型以及配方中是否存在诸如亚磷酸酯、环氧化油、抗氧剂等协合剂有关,其中镉皂和锌皂的稳定作用最大。
①硬脂酸铅是一种细微粉末,它不溶于水,溶于热的乙醇和乙醚,在有机溶剂中加热溶解,再经冷却成为胶状物。其遇强酸分解为硬脂酸和相应的铅盐,易受潮,有良好润滑性,熔点低而确保其有良好分散性。
②2-乙基乙酸铅,它可溶于溶剂和增塑剂,通常配成57%~60%的矿物油或增塑剂的溶液出售,广泛用作泡沫塑料中发泡剂偶氮二甲酰胺的活化剂。
③水杨酸铅,一种白色结晶粉末,相对密度2.36,折射率1.76,兼有PVC热稳定剂和光稳定剂作用。
④三盐基硬脂酸铅,白色粉末,相对密度2.15,280~800℃时分解,遇100℃以上高温易结块,溶于乙醚,有毒,无可燃性和腐蚀性,折射率1.60,润滑性较好,有良好的光稳定性,广泛用于PVC唱片配方中。
⑤二盐基邻苯二甲酸铅,白色细微结晶粉末,相对密度4.5,不溶于普通溶剂,为弱酸性,其盐基部分易碳酸化,折射率1.99,当配方中含有易皂化的增塑剂时,其稳定作用优于三盐基硫酸铅。
⑥三盐基马来酸铅(三盐基顺丁烯二酸铅),微黄色细粉末,相对密度6.0,折射率2.08,有毒,无可燃性和腐蚀性,有良好的色泽稳定性,具有消灭不稳定双烯结构作用。
⑦硬脂酸钡,白色细微粉末,钡含量19.5%~20.6%,相对密度1.145%,熔点225℃以上,不溶于水,但溶于热的乙醇,在有机溶剂中加热溶解经冷却后成胶状物。其遇强酸分解为硬脂酸和相应的钡盐,易受潮,是必须避免硫酸时供选用的热稳定剂,也是高温下加工时采用的润滑剂。
⑧蓖麻酸钡,这是一种带黄白色的粉末,熔点116~124℃,是能使制品得到良好透明性的稳定剂。同类型的产品还有月桂酸钡。
⑨硬脂酸镉,白色细微粉末,镉含量16.5%~17.5%,不溶于水,溶于热的乙醇,在有机溶剂中加热溶解后经冷却成为胶状物,遇强酸分解成硬脂酸和相应的镉盐,易受潮,广泛应用于要求具有良好透明性的PVC制品的热和光稳定剂。
⑩蓖麻酸镉,白色粉末,熔点96~104℃,PVC用稳定剂,兼有热和光稳定剂作用。
硬脂酸钙,白色细微粉,不溶于水,溶于热的乙醇和乙醚。其遇强酸分解为硬脂酸和相应的钙盐,易受潮,是PVC用的无毒稳定剂和润滑剂。其一般不单独使用,而常与锌皂、镁皂或环氧类稳定剂配合使用。与其相似的还有白色粉末的蓖麻酸钙,熔点74~82℃,适宜作PVC的无毒稳定剂。
硬脂酸锌,白色细微粉末,不溶于水,溶于热的乙醇、松节油、苯等有机溶剂,在有机溶剂中加热溶解后冷却成为胶状物,遇强酸分解为硬脂酸和相应的锌盐,易受潮,可以兼作PVC的无毒稳定剂和润滑剂。
硬脂酸镁,白色粉末,相对密度1.07,工业品熔点为108~115℃(纯品熔点为85℃),微溶于水,溶于热的乙醇,遇强酸分解为硬脂酸和镁盐。它常常被选作PVC的无毒稳定剂兼润滑剂,也是酚醛和脲醛树脂的润滑剂。
(3)复合稳定剂 复合稳定剂是各种化合物的聚集体,通常根据具体的PVC用途和用户来设计。这类稳定剂已经由单独添加琥珀酸钡和棕榈酸镉,发展到加钡皂、镉皂、锌皂、有机亚磷酸酯,再加上抗氧剂、溶剂、增量剂、塑解剂、着色剂、紫外吸收剂、光亮剂、黏度控制剂、润滑剂、增黏剂以及人工香料等进行物理混拼。
ⅡA族金属稳定剂,如钡、钙、镁不保护早期的颜色,但能为PVC提供良好的长期热稳定性。以这种方式稳定的PVC起始是黄/橙色,然后持续受热,逐渐变成橙/棕色,最后变黑。
镉和锌化合物首先被用作稳定剂,是由于它们透明,并能保持PVC制品的原来颜色。但是,由镉和锌化合物提供的长期热稳定性远小于钡化合物,往往会在极小先兆或毫无先兆的情况下,突然发生完全降解。
除了与金属比例有关外,钡-镉稳定剂的效果还与所结合的阴离子有关,常见的复合金属稳定剂的阴离子是2-乙基己酸盐、酚盐、苯甲酸盐、硬脂酸盐,其影响主要表现在以下方面:润滑性、迁移性、透明性、颜料颜色的变化等。
①液体钡-镉和液体钡-镉-锌复合稳定剂
a.钡盐——可以是烷基酚钡、2-乙基己酸钡、月桂酸钡、苯甲酸和取代苯甲酸钡、新癸酸钡等。钡盐在复合物中占6%~7%,即与镉盐的比例大约是2∶(1~32)(以金属记,质量比,下同)。
b.镉盐——可以是2-乙基己酸镉、月桂酸镉、油酸镉、苯基酸和取代苯甲酸镉、环烷酸镉、新癸酸镉等。镉盐在复合物中约占3%~4%。
c.锌盐——可以是2-乙基己酸锌、月桂酸锌、环烷酸锌、新癸酸锌、苯甲酸和取代苯甲酸锌等。锌盐在复合物中占0.5%~1%。
d.亚磷酸酯——可以是亚磷酸三苯酯、亚磷酸二苯一辛酯、亚磷酸二苯一癸酯、亚磷酸三(壬基苯酯)等。亚磷酸酯在复合物中约占15%~20%(质量分数),作螯合剂用。
其他的包括少量2,6-二叔丁基对甲酚、双酚A,壬基苯酚等酚类抗氧剂及紫外线吸收剂,以及液体石蜡、白油、柴油、锭子油等作溶剂,另外还需加入少量高级醇等消泡剂。
由于液体钡-镉-锌复合稳定剂的组成不同,性质也各异,但一般都是浅黄色至黄色清澈液体,常温下相对密度0.95~1.02,黏度小于100cP(1cP=1×10-3Pa·s),凝固点在-15℃左右。液体钡-镉和液体钡-镉-锌相似,都有优良的热、光稳定性,初期着色性小,具有良好的透明性和色泽稳定性。它们的稳定作用较固体的复合皂类强,故用量可减少,一般为2~3份,不会发生粉尘中毒,且在一般增塑剂中完全溶解,有良好的分散性,析出倾向小。其中,液体钡-镉-锌的初期着色性比液体钡-镉更小些。
②液体钡-锌复合物。一般都是浅黄色至黄棕色油状液体,常温下相对密度1.0~1.1,耐热性良好,不受硫化物污染,与环氧增塑剂并用可提高稳定效果,它对发泡剂有活化体用。
③液体钙-锌复合物。钙-锌稳定剂一般都为无毒液体,主要成分有硬脂酸钙、蓖麻油酸钙、硬脂酸锌、蓖麻油酸锌以及环氧大豆油、紫外线吸收剂等。通常是浅黄色至黄色的清澈油状液体,常温下相对密度为1.0~1.05,属于PVC的无毒稳定剂。液体钙-锌稳定剂主要用作食品包装薄膜、器皿和泡沫人造革的稳定剂。
(4)有机锡稳定剂 有机锡稳定剂分为含硫和不含硫两类,是各种羧酸锡和硫醇锡的衍生物,主要产品是二丁基锡和二辛基锡化合物,其中二辛基锡化合物被更多的国家作为无毒稳定剂使用。有机锡主要用来稳定硬质PVC制品,特别是那些需要有优良透明性和热稳定性的产品。当然也能稳定软质制品,但由于其价格较贵,所以一般不采用。二巯基乙酸异辛酯、二正辛基锡是应用最广的无毒稳定剂,含有1个或2个碳—锡键,其余价键为氧或硫—锡阴离子键饱和的锡化合物,是PVC的最有效稳定剂。这些化合物是有机锡氧化物或有机锡氯化物与适当的酸或酯的反应产物。
含硫稳定剂在所有稳定性能方面都是杰出的,但存在与含硫化合物类似的味道和交叉污染的问题。典型的含硫化合物是巯基化物—SR、巯基酸酯—S(CH)nCOOR或单质硫。非硫阴离子通常是基于马来酸或马来酸半酯,非硫有机锡是效果较小的热稳定剂,但是却具有较好的光稳定性。
①二月桂酸二丁基锡,一种淡黄色清澈液体,溶于所有工业用增塑剂和溶剂,有毒。它是有机锡中最老的品种,有优良的润滑性、透明性、耐候性、耐硫污性,但耐热性差,用作软质透明制品的主稳定剂,在硬质透明制品中用作润滑剂。
②马来酸二丁基锡,一种白色非晶形粉末,熔点和挥发性随聚合度而异,约在100~140℃之间。其有毒,有催泪性,主要用于要求高软化点和高冲击强度的硬质透明制品。因无润滑作用,故常与二月桂酸二丁基锡并用,用量0.5~2份。
③双(马来酸单丁酯)二丁基锡,淡黄色透明液体,无毒(允许用量3份以下)。其有良好的耐候性、透明性、防止着色性和热稳定性,不发生硫污,常用于PVC透明硬质制品,用量2.0~4.0份。
④双(巯基乙酸异丁酯)二正辛锡,一种淡黄色液体,不溶于水,易溶于酯、醚、醇、脂肪烃和芳烃、氯化烃类以及主要类型的增塑剂。它是硫醇锡中的主要品种,是最普遍使用的无毒有机锡稳定剂之一,用于硬质透明PVC(2~3份)和软质透明PVC(1份)。其缺点是耐候性差、有臭味、硫污染、无润滑作用。此外,因含有酯基,故有一定的增塑作用。
⑤二月桂酸二正辛基锡,一种黄色液体,25℃时的相对密度为1.01~1.02,折射率为1.46~1.47,30℃时的黏度在60cP以下。其无毒,润滑性良好,主要用于硬质透明PVC食品包装材料,用量1.5份以下。
⑥马来酸二正辛基锡,一种白色粉末,熔点87~105℃,不溶于水,溶于苯、乙醇、丙酮。其无毒,具有优异的长期耐热性,主要用作硫醇锡的副稳定剂,用量常在0.3~0.5份。
液体有机锡热稳定剂透明度最好,这是因为无论是未参加热稳定化反应的热稳定剂,还是已参加稳定化反应后生成的R2SnCl2,在PVC树脂中均有很好的相容性,而Ba/Zn、Ba/Cd、Ca/Zn的硬脂酸皂在PVC中有一定的相容性,透光率亦比较高,但因其相容性有限,分子线型长又较大,参加热稳定化后的生成物是典型的金属盐类(如CaCl2、BaCl2等),与PVC的相容性较差,因而用量大时有较多折射光,影响其透光率而变浑浊。
(5)副热稳定剂 根据作用效果的不同,热稳定剂又分为主稳定剂和副稳定剂两类。主稳定剂是指那些单独使用时就有稳定效果的一类化合物。副稳定剂是指单独使用时无效果,而与主稳定剂配合使用时却起增效作用的一类化合物。主稳定剂或主副稳定剂复合使用可以产生协同作用效果。
①环氧化合物副热稳定剂,与上述主稳定剂配合使用有较好的协同作用,具有光稳定性和无毒的优点,适用于软质,特别是暴露于阳光下使用的软质PVC制品,通常不用于硬质PVC制品。常用品种包括环氧大豆油、环氧亚麻子油、环氧妥尔油酸酯、环氧硬脂酸丁酯及环氧硬脂酸辛酯等化合物。
②亚磷酸酯、亚磷酸二苯一癸酯、亚磷酸一苯二癸酯也是聚氯乙烯的副热稳定剂,特别在含钡/镉和钙/锌稳定剂体系中使用可改善制品的透明性。但会水解,因此不能在需与水接触的聚氯乙烯制品中用作副稳定剂。
③其他有机化合物,如二苯基硫脲、2-苯基吲哚、三羟甲基丙烷、硫代月桂酸酐以及高沸点的多元醇(如季戊四醇、山梨糖醇和甘露醇)等与主热稳定剂并用时也可发挥协同作用。
对于不同结构类型的塑料制品,所使用的稳定剂也稍有差别。
①硬质制品。在北美的硬质PVC制品市场上,尽管也有一些锡、混合金属、烷基酯类使用,但大多数是采用有机锡的稳定剂。在世界的其他地区,特别是制作异形材时,铅稳定剂正逐步取代钡-镉稳定剂,这是由于上述提到的镉的问题。但是,由于潜在的环境因素,在这些应用领域中正逐步用钙-锌和有机锡来取代铅。
②管材。硬质PVC管材是PVC独有的最大的市场,大多数管材是在双螺杆挤出机上加工的。由于受热时间短,因而采用了较低浓度的烷基有机锡稳定剂。这些管材的稳定剂可含有少至4%~10%的锡,使用量通常为每100份聚合物用0.4份(双螺杆挤出时),而单螺杆挤出时为0.6~1.0份。用于饮用水管的稳定剂,必须符合独立认证机构的要求。
③注塑。随着往复移动螺杆注塑模具对合适树脂的要求的出现,已成功地开发了高效稳定剂并制得非常大的部件(35lb,1lb=0.45359237kg)。虽然树脂的分子量越低,加工也越易,但注塑模具的高剪切通常需要含14%~25%锡的有机锡硫基酯。
④吹模。有机锡的恰当选择对吹模工艺非常关键,这是因为起始就有的颜色、香料、透明性的附加要求,在通用制品中起决定性作用的是硫酸丁基锡酯和硫酸甲基锡酯。尽管甲基锡和锡酯也有FDA的许可,但在食品级应用中主要使用辛基锡。
⑤膜材和片材。挤出和压延都被用来加工硬质PVC膜材和片材,通常对于膜材和片材采用与瓶子使用的一样的稳定剂。
⑥披叠板(一种带雪松木纹表面的、中密度的、低吸水率的硅酸钙板,常用于别墅或多层高档建筑外墙帷幕板)及外型材。对于用于披叠板及窗户外框材料的PVC的稳定剂,耐候性和保持颜色的耐久性是额外的要求。
热稳定剂在各国的消费结构不尽相同,在美国,复合稳定剂占总消费量的40%~50%,有机锡占近40%。热稳定剂中,无镉、低铅、无尘化及代替铅盐成为该行业的发展重点。环保法规的要求严格化正推动着热稳定剂的改变,为了保护人类的生存环境,许多国家已通过法律限制有毒的重金属类在PVC加工中的应用。欧洲许多国家正在使用基于有机锡或基于钙-锌的替代物代替。欧洲铅稳定剂用量从1999年的12万吨/年减少到2010年的8万吨/年。预计亚太地区含铅热稳定剂需求量也将大幅降低,包括基于有机锡系统(OBS)在内的新稳定剂已在美国广泛应用。在北美,单/双有机锡硫酸盐是现行首选的稳定剂,而在传统上一直使用金属混合物的欧洲,其吸引力也在增大。在北美,高添加量的二氧化钛用于很好地防止紫外线。这一事实再加上较高的生产率,均要求有机锡提供更优良的加工稳定性。
热稳定剂的安全性问题也越来越受到人们的重视。PVC稳定剂的安全性应从三方面考虑,一是使用原材料加工者的安全,二是使用者的安全防护,三是废弃物对环境的安全。加工者的安全防护可通过稳定剂的液化、膏状化、颗粒化等措施加以解决。对于使用者的安全防护,可将稳定剂高分子量化或制备反应性稳定剂来提高其耐油性,但考虑到稳定化作用是分子级的化学反应,上述方法不是最合适的方法,最好的方法还是选用高安全性的稳定剂。在选择稳定剂时,还必须考虑稳定化过程中树脂与稳定剂,或稳定剂相互间发生反应所生成的化学物质安全性。
从各类PVC稳定剂的安全性看,镉类稳定剂在不久的将来会停止使用。这是一个缓慢的过程,原因之一是大多数无镉稳定剂在使用时候成本要上升10%~20%,而且无镉类稳定剂不能通用于较大范围的PVC混合物(如加工范围较窄),还常需要用辅助型稳定剂弥补其性能缺陷。如今无镉稳定剂的性能已达到有镉稳定剂的性能,钙-锌稳定剂得到快速发展,并以粉末、膏状和液体,以及标准级和无毒级出售,第二代钙-锌稳定剂在食品和药物包装方面已经取代辛基锡和甲基锡。
铅类稳定剂因其抽出性极小,故使用时的安全性不成问题,但存在危害环境的安全性问题。由于铅类稳定剂成本低、效率高,很多企业都使用它。由于多个国家的禁铅,铅类稳定剂正在退出市场,能够提供与铅体系相近的加工稳定性的新型共稳定剂正不断开发出来,以实现无铅稳定剂。在大多数通用场合,钡-锌和钙-锌稳定剂正在迅速取代更有效的钡-铅配方。这种情况的出现是由于相关法规和废物处理的高费用。但鉴于铅化合物独特的电性能,许多柔性的和刚性的、均聚物和共聚物材料的稳定性都能得到实现,在电线电缆包覆市场中仍占优势。
钙-锌稳定剂与食品级的亚磷酸酯和辅助组分的组合,在食品包装袋方面得到了应用。在大多数软质制品中,常使用环氧化酯(如环氧甘油酯、环氧脂肪酯)作增塑剂,环氧化物与氯化氢反应则具有辅助稳定剂的功能。
2.2.3.3 抗冲击改性剂
顾名思义,抗冲击改性剂的主要作用是改善高分子材料的低温脆化,赋予其更高的韧性。据美国塑料工业咨询公司报告,全球塑料抗冲击改性剂需求量为60万吨(市值约15亿美元),其中苯乙烯共聚物[如ABS和甲基丙烯酸甲酯-丁二烯-苯乙烯(MBS)]成为冲击性改性剂的大类,约占45%市场份额;丙烯酸类占近30%;弹性体,包括EPDM和热塑性弹性体(TPE)约占10%市场份额;氯化聚乙烯(CPE)占10%;其他占5%。由于PVC是冲击性改性剂的最大使用品种,约占用量的80%,所以PVC需求增长也将带动冲击改性剂需求增加。工程塑料树脂,如PC、聚酰胺(PA)、聚酯等消耗冲击改性剂约10%,由于工程塑料需求正强劲增长,推动冲击改性剂的用量增长。聚烯烃类树脂约消耗10%的抗冲击改性剂。专家指出,未来冲击性改性剂的发展趋势是性能更好、价格更廉、作用更快,使主材料性能提高或保证性能前提下使构件更薄。国外公司中,如Arkema的Durastrength产品可以显著改善PVC的抗冲击性能,此外,康普顿、杜邦、陶氏化学等公司都推出了自己的适用产品。常用的抗冲击改性剂有ACR、MBS、CPE、ABS、EVA和EPT 等,但从对塑料制品的改性效果来看,ACR(丙烯酸酯类树脂)是抗冲击改性剂中综合性能最好的。另外MBS是透明制品的重要原料,因而在抗冲击改性剂中也有着重要的地位。抗冲击改性剂除用于PVC加工外,正扩展至PC、PBT、尼龙、ABS等树脂中。
抗冲击改性剂不仅能提高树脂的冲击强度,还可改善树脂的加工性能。抗冲击剂通常用于硬质聚氯乙烯中,但在聚丙烯、聚苯乙烯及改性塑料中已普遍应用。目前,硬质聚氯乙烯所用的抗冲击剂主要是一些共聚树脂或改性树脂,如ABS、MBS、EVA、CPE及热塑性橡胶、热塑性弹性体等,广泛用作PVC、PE、PP、PS、AS、ABS、PMMA、PA、PC、PBT、PET等。添加抗冲击剂可以将脆性塑料变为韧性塑料,可以将只能在常温下应用的塑料变为低温下使用的塑料,此外,还能有效地改善塑料的加工性能。
理想的抗冲击改性剂应具备如下性能:①必须具备与改性基材有良好的相容性;②改性剂的颗粒大小、形态适中,粒径200nm左右,以保障较高的抗冲击强度效果;③改性剂的玻璃化温度以较低为佳;④抗冲击改性剂最好有轻度的交联,以提高增强效果;⑤改性剂对树脂的加工性能无损害,对其表观性能及物理力学性能无不良影响;⑥要求无毒、无污染及价格适中。
目前生产抗冲击改性剂的公司,特别是ACR、MBS生产公司实行技术垄断,基本不转让技术,单独或联合在靠近市场地区的亚洲设厂,以便占领潜在市场。今后全球抗冲击改性剂的发展以ACR、MBS两大品种为主。
PVC抗冲击改性剂有时也会同时起增塑作用,因此也可以看作增塑剂,用于PVC树脂的抗冲击改性剂有如下几种。
①氯化聚乙烯(CPE)是利用HDPE在水相中进行悬浮氯化的粉状产物,随着氯化程度的增加,使原来结晶的HDPE逐渐成为非结晶的弹性体。作为增韧剂使用的CPE,由高密度聚乙烯(HDPE)氯化而得,含氯量一般为30%~45%,依树脂分量、含氯量、分子结构和形态的不同,呈现出从硬质塑料到橡胶弹性体的不同状态变化。分子量在100万以上的CPE,不仅抗冲击性良好,而且耐候性非常优秀,克服了ABS和MBS耐候性差的缺点。此外,CPE中氯含量大小对改性效果影响很大,含氯量过低,本身结晶性高而韧性差,玻璃化温度高,与PVC相容性差。含氯量过高时,CPE的内聚作用强,但分散性比较差。CPE在PVC中用量一般为5%~15%。CPE的耐寒性、化学稳定性、阻燃性、耐油性和电绝缘性能均良好。CPE来源广,价格低,除具有增韧作用外,还具有耐寒性、耐候性、耐燃性及耐化学药品性。目前在我国CPE是占主导地位的抗冲击改性剂,尤其在PVC管材和型材生产中,加入量一般为5~15份。CPE可以同其他增韧剂协同使用,如橡胶类、EVA等,效果更好,但橡胶类的助剂不耐老化。
②ACR为甲基丙烯酸甲酯、丙烯酸酯等单体的共聚物,ACR为近年来开发的最好的抗冲击改性剂,它可使材料的抗冲击强度增大几十倍。ACR属于核壳结构的抗冲击改性剂,甲基丙烯酸甲酯-丙烯酸乙酯高聚物组成的外壳,以丙烯酸丁酯类交联形成的橡胶弹性体为核的链段分布于颗粒内层。尤其适用于户外使用的PVC塑料制品的冲击改性,在PVC塑料门窗型材使用ACR作为抗冲击改性剂与其他改性剂相比,具有加工性能好,表面光洁,耐老化好,角焊接强度高的特点,但价格比CPE高1/3左右。国外常用的牌号有K-355,一般用量6~10份。目前国内生产ACR抗冲击改性剂的厂家较少,使用厂家也较少。
③MBS是甲基丙烯酸甲酯、丁二烯及苯乙烯三种单体的共聚物,它是向聚丁二烯或聚丁二烯-苯乙烯乳液中,加入甲基丙烯酸甲酯进行接枝共聚而得。MBS的溶度参数在9.4~9.5之间,与PVC的溶度参数接近,因此同PVC的相容性较好,它的最大特点是:MBS树脂的加入,可提高PVC的冲击韧性,增加聚氯乙烯的透明度,但MBS的耐老化性差,MBS中橡胶含量越高,其冲击韧度也越高。一般在PVC中加入10%~17%,可将PVC的冲击强度提高6~15倍,但MBS的加入量大于30份时,PVC冲击强度反而下降。MBS本身具有良好的冲击性能,透明性好,透光率可达90%以上,且在改善冲击性同时,对树脂的其他性能,如拉伸强度、断裂伸长率等影响很小。MBS价格较高,常与其他抗冲击改性剂,如EAV、CPE、SBS等并用。MBS耐热性不好,耐候性差,不适用于户外长期使用制品,一般不用作塑料门窗型材生产的抗冲击改性剂。
④SBS为苯乙烯、丁二烯、苯乙烯三元嵌段共聚物,也称为热塑性丁苯橡胶,属于热塑性弹性体,其结构可分为星型和线型两种。SBS中苯乙烯与丁二烯的比例主要为30/70、40/60、28/72、48/52几种,主要用作HDPE、PP、PS的增韧、耐寒和抗冲击强度改进,其加入量为5%~15%,可大大提高低温冲击韧度,其主要作用是改善低温耐冲击性。SBS耐候性差,不适用于户外长期使用制品。
⑤ABS为苯乙烯(40%~50%)、丁二烯(25%~30%)、丙烯腈(25%~30%)三元共聚物,它是一种接枝共聚物,是向聚丁二烯胶乳中加入苯乙烯和丙烯腈单体进行共聚而得。ABS自身常用作工程塑料,作为PVC的抗冲击剂具有良好的增韧效果,而拉伸强度和伸长率下降小,对低温冲击改性效果也很好。ABS的加入量一般为10%~20%,当加入量达到50份时,PVC的冲击强度可与纯ABS相当。ABS因含有不饱和结构,耐候性差,不适用于长期户外使用制品,一般不用作塑料门窗型材生产的抗冲击改性剂。ABS树脂与PVC的相容性不及MBS,故制品透明性也不如MBS共聚物好,如用透明ABS与PVC共混也可以得到透明的制品。当ABS添加量为20%~30%时,其冲击强度效果极佳。
⑥EVA是乙烯和乙酸乙烯酯的共聚物,乙酸乙烯酯的引入改变了聚乙烯的结晶性,乙酸乙烯酯含量大,模量差,而且EVA与PVC折射率不同,难以得到透明制品,因此,常将EVA与其他抗冲击树脂并用。EVA的添加量一般在5%~10%,EVA作为改性剂,还可以用在聚烯烃的改性,改善其耐候、耐寒性能。EVA用作PVC的改性剂时,其乙酸乙烯含量应在40%以上。EVA耐候性好,改性PVC制品可用于户外,但透明性和拉伸强度都有所下降。
⑦合成橡胶与热塑性弹性体抗冲击改性剂。合成橡胶与热塑性弹性体均具有优异的柔软韧性、高弹性和优良的耐低温性能,本身具有良好的抗冲击性能,也就是良好的抗冲击改性剂。POE为乙烯/辛烯共聚物,作为PE、PP、PA的抗冲击改性剂,效果良好,在增韧的同时,刚性下降低。三元乙丙橡胶(EPDM),具有良好的柔软性、弹性、抗撕裂性、耐酸碱、耐候性和抗冲击性。由乙烯、丙烯共聚而成的二元乙丙胶(EPR),是无定形橡胶,具有很好的抗冲击性能。丁腈橡胶(NBR),一般选用丙烯腈含量为26%~32%的作为抗冲击剂。其他的还有丁苯橡胶、顺丁橡胶、氯丁橡胶、丁二烯橡胶等,均可作为抗冲击改性剂,一般添加量为10%~20%。目前比较常用的还有乙丙橡胶与丁腈橡胶,用于改性PVC、PP、HIPS、PS等热塑性树脂。
经过比较,MBS树脂的抗冲击性优于EVA,但差于ACR、CPE及ABS;耐候性方面MBS与ABS相近,却劣于其他三者;光及热稳定性方面MBS也近于ABS,但低于ACR与CPE。应强调的是,MBS树脂在透明型PVC树脂制品加工中的重要作用,尚无法替代。MBS树脂通常可使PVC的冲击强度提高5~6倍,并对抗张强度、伸长率影响很小。MBS树脂是综合性能优异的抗冲击改性剂品种,尤以透明性和配位性为佳。具体比较:透明性为MBS>ACR>CPE、EVA;加工性为MBS、ACR>CPE>EVA;配伍性为MBS>ACR>CPE>EVA。
加工改性剂是针对塑料加工性能差而添加的一类助剂,在聚合物中能改善熔融树脂的流动性,并具有热稳定性、耐热变形性和制品表面光泽性。目前,加工改性剂主要是改善聚氯乙烯的熔融黏度,改善流动性和加工性能。应用比较多的加工改性剂是丙烯酸类共聚物,如甲基丙烯酸甲酯/丙烯酸乙酸共聚物体系(MMA/FA体系)、甲基丙烯酸甲酯/甲基丙烯酸丁酯/丙烯酸乙酯/甲基丙烯酸乙酯共聚物体系(MMA/BMA/EA/EMA体系)、甲基丙烯酸甲酯/丙烯酸乙酯/丙烯腈共聚体系(MMA/EA/AN体系)等,添加量通常为树脂用量的3%~8%。
①ACR。ACR是甲基丙烯酸甲酯与丙烯酸酯的共聚物,是具有核/壳结构的高分子聚合物。其以交联的丙烯酸丁酯(BA)橡胶状聚合物为核,以聚甲基丙烯酸甲酯(PMMA)为壳,外壳层PMMA与PVC相容性好,内层为轻度交联的核,在核与壳之间通过浓度梯度或与其他聚合物控制的方法逐渐过渡,形成过渡层,使得核与壳的相容性得到改善,由此大大提高了抗冲击效果。它不仅是PVC的加工改性剂,也是热塑性聚烯烃的冲击改性剂和偶联剂。ACR品种型号比较多:ACR-201,白色粉末,相对密度1.05~1.20,粒度为98%(通过30目),其与PVC的溶解度参数相接近,所以具有良好的相容性和加工成型性。作为PVC的加工改性剂,一般ACR添加量为1%~3%。ACR-401,外观白色粉末,是由甲基丙烯酸甲酯、丙烯酸乙酯、丙烯酸丁酯、苯乙烯四种单体共聚而成。其分子结构为核壳结构,分子量为25万~75万,特性黏度0.5~1,细度98%(通过40目),玻璃化温度54℃,热分解温度268℃,不溶于水,溶于丙酮、丁酮,无毒、阻燃。由于其以丙烯酸丁酯交联形成橡胶弹性体为核壳结构,所以具有良好的加工流动性和抗冲击韧性。
②P-83。P-83全名为CHEMIGUM-P83,它是丁二烯与丙烯腈的共聚物,呈松散粉末状,具有特殊的立体结构。其特点是与PVC相容性好,可全面改善PVC性能,提高加工性、热稳定性、耐低温性、耐磨性、柔软性等。与P-83相似的加工助剂还有加拿大产KPYNAC-1122和美国杜邦的ELVALOY-741、ELVALOY-742等。
③聚α-甲基苯乙烯。其为α-甲基苯乙烯的低聚物,也称AMS或R-18,是生产苯酚、丙酮时的副产品,也可由异丙苯脱氢制得。AMS的分子量为300~350时为液体;分子量为700~1000时,称作M-80树脂,为脆性固体,软化点在93~105℃。AMS除用于PVC之外,还用于PU、PS、ABS和CPE等耐寒和耐候的加工改性剂。
④820-G。其是由氯化石蜡与氧化聚丙烯-乙烯通过自由基接枝而成的表面活性剂,再经过氯硅烷偶联剂表面处理的载体所组成,可明显改善硬质PVC的加工流动性,当添加10%~15%时,可提高冲击强度和增加表面光泽度,取代部分ACR,使制品成本下降。
⑤NPA。其是由聚烯烃树脂、含氟树脂、聚硅氧烷、蜡类等配制而成。NPA-6、NPA-8是线型低密度聚乙烯的加工助剂,外观为白色粉末,熔点105~110℃,分子量1000~1500,熔体指数50~55g/10min。NPA具有爽滑性和加工流动性,添加量一般为2%~4%。
⑥有许多抗冲击改性剂,如MBS、ABS、CPE、EVA、SBS等既是抗冲击改性剂,也是加工改性剂。
2.2.3.4 抗氧化剂
以抑制聚合物树脂热氧化降解为主要功能的助剂,属于抗氧化剂(简称抗氧剂)的范畴。抗氧剂是保障塑料稳定化的最主要助剂类型,几乎所有的聚合物树脂都涉及抗氧剂的应用。按照作用机理,传统的抗氧剂体系一般包括主抗氧剂、辅助抗氧剂和碳自由基等。
①主抗氧剂又称自由基捕捉剂,是抗氧剂中起主要作用的一类。它能捕捉在聚合物热氧化老化中生成的过氧自由基(·OH、RO·、ROO·)和捕获氧化降解中产生的活泼碳自由基(但效果差),从而中止或减缓聚合物的链式降解反应。主抗氧剂又有“过氧自由基捕获剂”和“链终止型抗氧剂”之称,涉及芳胺类化合物和受阻酚类化合物两大系列产品。
②辅助抗氧剂又称氢过氧化物分解剂,它能够将热氧化(老化)链反应中生成的氢过氧化物分解,使之生成失去活性的化合物,从而终止或减缓热氧老化。它与主抗氧剂常有协同效应,并只在与主抗氧化剂并用时才能发挥最大的效果,故通称辅助抗氧剂,包括硫代二羧酸酯类和亚磷酸酯化合物。
③碳自由基(即烷基自由基)通常在热氧化老化的链反应中,在无氧及高温的情况下生成。这种自由基捕获剂有别于传统意义上的主抗氧剂,它们能够捕获聚合物烷基自由基,相当于在传统抗氧体系中增设了一道防线。此类稳定化助剂主要包括芳基苯并呋喃酮类化合物、双酚单丙烯酸酯类化合物、受阻胺类化合物和羟胺类化合物等,它们和主抗氧剂、辅助抗氧剂配合构成的三元抗氧体系能够显著提高塑料制品的抗氧稳定效果。必须注意,胺类抗氧剂具有着色污染性,多用于橡胶制品,而酚类抗氧剂及其与辅助抗氧剂、碳自由基捕获剂构成的复合抗氧体系更多地用于塑料及浅色橡胶制品。
目前全球的抗氧剂市场几乎被国外公司垄断,我国的抗氧剂自主化生产还有很长的一段路要走。目前以维生素E为基础的绿色抗氧剂产品,由于其符合全球环保要求,颇受消费市场的欢迎,代表了未来抗氧剂的发展方向。随着塑料工业的快速发展,尤其各种新型功能性塑料的不断开发与应用,全球抗氧剂工业正朝专用化、系列化、复合化、高效化、绿色化方向发展,主要种类有:磷类抗氧剂、酚类抗氧剂、硫类抗氧剂、天然抗氧剂、聚合酚抗氧剂、复合型抗氧剂、金属离子钝化剂等。
①磷类抗氧剂。亚磷酸酯作为辅助抗氧剂,由于传统的亚磷酸易水解,影响了储存和应用性能,提高亚磷酸酯的耐水解稳定性一直是抗氧剂研发的热点,目前国外推出的Mark HP-10,Ethanox398,Doverphos S-686、S-687都具有很高的水解稳定性及色、光稳定性。高分子量的亚磷酸酯产品具有挥发性低、耐析出性高等特点,耐久性好,典型产品有Sandstab PEPQ、Phosphite A等。将亚磷酸酯与酚类抗氧剂复合使用,可充分发挥协同作用,目前主要有Irgafos168、Ultranox626、Mark PEP-36、Cyanox2777等。
②酚类抗氧剂。酚类抗氧剂是塑料中应用最为广泛、用量最大的抗氧剂。曾经的主打品种为2,6-二叔丁基酚(BHT),由于分子量低、挥发性大,且有泛黄变色等缺陷,用量正逐年减少。以1010[学名β-(3,5-二叔丁基-4-羟基苯基)丙酸季戊四醇酯]、1076[学名β-(3,5-二叔丁基-4-羟基苯基)丙酸十八酯]为代表的高分子量受阻酚品种消费比例逐年提高,成为酚类抗氧剂市场上的主导产品。
③硫类抗氧剂。与磷类抗氧剂相比,硫类抗氧剂开发与应用显得十分单调,硫代酯类仍占据主导地位。今后高分子量化和功能化品种的开发是硫类抗氧剂的发展方向。目前上市的主要有SumilizerTP-D、TM610、MarkAO-23、Irganox1035、1192等。近年来阿托化学开发的Anoxsyn442的新产品,结合了硫酯和亚磷酸酯两种辅助抗氧剂的优点,具有良好的稳定性、色泽改变性和耐候性,而且在高温条件下无异味逸出,可与UV光稳定剂产生良好的协同稳定效果。汽巴化学公司也开发出具有分子内部自协同作用的液体硫类抗氧剂Irganox1520。
④天然抗氧剂。随着人们对用于食品、医药等包装的塑料制品的安全性提出更高的要求,特别是近年来BHT出现致癌的嫌疑,作为安全有效措施,一方面高效、耐热的高分子量的受阻酚不断开发与应用,另一方面天然无毒抗氧剂品种付诸实施应用,其中VE最具代表性,汽巴化学公司的Irganox E17、217、218等,Hoffman-La Roche公司推出的Ronotec17等都是目前广泛应用于食品、医疗器具等与人体直接接触的聚合物领域中的以VE为基础的绿色天然抗氧剂。另外,韩国Woorichem Tech公司提出采用0.01%~10%天然生育酚类和绿原酸作为抗氧剂,可制造对人体非常安全的聚烯烃。目前天然抗氧剂仅限于食品及医疗器械等塑料制品,今后可能开发在α-生育酚多个位置引入辅助抗氧剂结构的基团来提高其抗氧性,拓展VE类抗氧剂的应用领域。
⑤聚合酚抗氧剂。抗氧化剂Wingstay L是高效多酚添加物,具有高活性和很低的挥发性,而且不会脱色,也不会变红,适于对基于异戊二烯和丁二烯的天然和合成聚合物的保护,非常适合保护浅色或不着色的天然橡胶、乳胶、SBR和羧化SBR乳胶、ABS、NBR、BR、SBS和SIS等的衍生物。Wingstay L 的应用包括生产过程中的聚合物的稳定化,以及各种制品的稳定化,如弹力丝、地毯背衬、泡沫橡胶垫、家用手套和医用手套、医疗产品、婴儿奶嘴、浴室垫、热水瓶、汽车部件、家庭用具(垫圈、衬垫、零件、外壳等)、电子设备外壳、纸涂层。
⑥复合型抗氧剂。高效复合型抗氧剂是受阻酚、亚磷酸酯和硫代脂的复合物,另外还有受阻酚类抗氧剂和紫外线吸收剂的复合产品。复合型产品具有开发周期短、效果好、综合性能佳、多种助剂充分发挥协同作用,方便用户使用。比较有代表的品种有汽巴化学公司的Irganox B、Irganox LC、Irganox LM、Irganox HP、Irganox XP,通用公司的Ultranox815A、Ultranox817A、Ultranox875A、Ultranox877A等,以及再生塑料专用复合抗氧剂品种Recyclestab411、Recyclestab811等;美国康普顿公司推出的复合抗氧化剂Naugard900系列产品,据称该产品具有低挥发及无析出的特点;Cytec公司开发的抗氧剂CyanoxXS4是含有受阻酚和亚磷酸酯的复合体系,在聚烯烃中使用,用于增强加工稳定性和长效稳定性等。
⑦金属离子钝化剂。目前金属离子钝化剂以双亚水杨基二胺为主,从其品种开发趋势来看,多功能化是其主要特征,功能性金属离子钝化剂多为键合受阻酚官能团的产品,它们同时赋予制品的抗铜钝化性和抗热氧老化性。其代表品种有汽巴化学公司和尤尼罗伊尔公司相继推出的Irganox MD1024、NouguardXL-1。