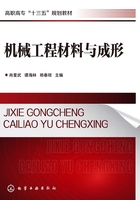
3.6 钢的化学热处理
化学热处理是将工件置于特定介质环境加热和保温,使介质中的活性原子渗入工件表层,改变表层的化学成分和组织,从而达到强化表层性能的一种热处理工艺。与表面淬火相比,化学热处理后的工件表层不仅有组织的变化,而且有化学成分的变化,所以,化学热处理使工件表层性能提高的程度超过了表面淬火的水平。
化学热处理不仅可以显著提高工件表层的硬度、耐磨性、疲劳强度和耐腐蚀性能,而且能够保证工件心部具有良好的强韧性。因此,化学热处理在工业生产中已获得越来越广泛的应用。
化学热处理种类很多,根据渗入元素的不同,可分为渗碳、渗氮(氮化)、碳氮共渗(氰化)、渗硼、渗硫、渗金属、多元共渗等。在机械制造工业中,最常用的化学热处理工艺有钢的渗碳、渗氮和碳氮共渗。
3.6.1 化学热处理的基本过程
化学热处理过程是一个比较复杂的过程。一般将它看成由渗剂的分解、工件表面对活性原子的吸收和渗入工件表面的原子向内部扩散三个基本过程组成。
(1)介质分解
在一定温度下渗剂的化合物发生分解,产生渗入元素的活性原子(或离子)。例如:
2COCO2+[C]
CO+H2H2O+[C]
CH42H2+[C]
2NH33H2+2[N]
值得注意的是,作为化学热处理渗剂的物质必须具有一定的活性,即具有易于分解出被渗元素原子的能力。然而并非所有含被渗元素的物质都能作为渗剂。例如:N2在普通渗氮温度下就不能分解出活性氮原子,因此不能作为渗氮的渗剂。
(2)表面吸收
刚分解出的活性原子(或离子)碰到工件时,首先被工件表面所吸附;而后溶入工件表面,形成固溶体;在活性原子浓度很高时,还可能在工件表面形成化合物。
(3)原子扩散
工件表面吸收被渗元素的活性原子后,造成了工件表面与心部的浓度差,促使被渗元素的原子由高浓度表面向内部的定向迁移,从而形成一定深度的扩散层。
3.6.2 渗碳
将低碳钢放入渗碳介质中,在900~950℃下保温,使活性碳原子渗入钢件表面以获得高碳渗层的化学热处理工艺称为渗碳。渗碳的主要目的是提高工件表面的硬度、耐磨性和疲劳强度,同时保持心部具有一定强度和良好的塑性与韧性。渗碳钢的含碳量一般为0.1%~0.3%,常用渗碳钢有20、20Cr、20CrMnTi、12CrNi、20MnVB等。因此,一些重要的钢制机器零件经渗碳、淬火和回火处理,通过碳原子的表层渗入使钢能兼有高碳钢和低碳钢的性能;从而使它们既能承受磨损和较高的表面接触应力,同时又能承受弯曲应力及冲击载荷的作用。
(1)渗碳方法
根据所用渗碳剂的不同,渗碳方法可分为三种,即气体渗碳、固体渗碳和液体渗碳。常用的是前两种,尤其是气体渗碳应用最为广泛。
1)气体渗碳
气体渗碳是零件在含有气体渗碳介质的密封高温炉罐中进行渗碳处理的工艺。通常使用的渗碳剂是易分解的有机液体,如煤油、苯、甲醇、丙酮等。这些物质在高温下发生分解反应,产生活性碳原子,造成渗碳条件:
CH42H2+[C]
2COCO2+[C]
CO+H2H2O+[C]
2)固体渗碳
固体渗碳如图3-24所示。将工件装入渗碳箱中,周围填满固体渗碳剂,密封后送入加热炉内,进行加热渗碳。渗碳温度一般为900~950℃。

图3-24 固体渗碳装置箱示意图
(2)渗碳层成分
低碳钢渗碳后,表层含碳量可达过共析的程度,由表往里碳浓度逐渐降低,直至渗碳钢的原始组织成分,如图3-25所示。所以渗碳件缓冷后,表层组织为珠光体加二次渗碳体(表层含碳量达0.85%~1.05%);心部为铁素体加少量珠光体组织;两者之间为过渡层,越靠近表层铁素体越少。一般,从表面到过渡层一半处的厚度为渗碳层的厚度。
渗碳层的厚度主要根据零件的工作条件来确定。渗碳层太薄,易产生表面疲劳剥落;太厚则使承受冲击载荷的能力降低。一般机械零件的渗碳层厚度在0.5~2.0mm之间。工作中磨损轻、接触应力小的零件,渗碳层可以薄些;渗碳钢含碳量较低时,渗碳层应厚些;合金钢的渗碳层可以比碳钢的薄些。

图3-25 低碳钢渗碳缓冷后的组织
(3)渗碳后的热处理
为了充分发挥渗碳层的作用,使渗碳件表面获得高硬度和高耐磨性,渗碳后一般还要继续进行直接淬火或一次淬火。
直接淬火:工件渗碳后预冷到一定温度直接进行淬火。这种方法一般适用于气体或液体渗碳,固体渗碳时较难采用。
一次淬火:渗碳后让工件缓慢冷却下来,然后再次加热淬火。与直接淬火相比,一次淬火可使钢的组织得到一定程度的细化。对于心部性能要求较高的工件,淬火温度应略高于心部成分的Ac3;对于心部强度要求不高而要求表面有较高硬度和耐磨性的工件,淬火温度应略高于Ac1;对介于两者之间的渗碳件,要兼顾表层与心部的组织及性能,淬火温度可选在Ac1~Ac3之间。
不论采用哪种方法淬火,渗碳件在最终淬火后都应进行低温回火。回火温度一般为180~200℃。
3.6.3 渗氮
向钢的表面渗入氮元素,以获得富氮表层的化学热处理称为渗氮,通常叫作氮化。与渗碳相比,钢件氮化后表层具有更高的硬度和耐磨性。氮化后的工件表层硬度高达950~1200HV。
目前较为广泛应用的氮化工艺是气体渗氮,即将氨气通入加热到氮化温度的密封氮化罐中,使其分解出活性氮原子,反应如下:
2NH33H2+2[N]
3.6.4 碳氮共渗
碳氮共渗又称氰化,是在钢件表面同时渗入碳和氮原子的化学热处理工艺。其目的是在表面形成碳氮共渗层,以提高工件的硬度、耐磨性和疲劳强度。目前以中温气体碳氮共渗和低温气体碳氮共渗应用较为广泛。
中温气体碳氮共渗的主要目的是提高钢的硬度、耐磨性和疲劳强度。
低温气体碳氮共渗以渗氮为主,其主要目的是提高钢的耐磨性和抗咬合性。将钢件放入密封炉罐内加热到820~860℃,并向炉内滴入煤油或其他渗碳剂,同时通入氨气。