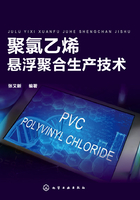
2.8 其他影响氯乙烯悬浮聚合的因素
2.8.1 氧对氯乙烯悬浮聚合的影响
在氯乙烯悬浮聚合中,存在氧气时,会导致pH值的降低,当聚合釜内不含氧或含很少量氧时,体系pH值下降缓慢,若含氧量高时,反应体系pH值在反应开始后则急剧下降。一般反应2.5h后下降幅度增大。
氧的存在对聚合反应起阻聚作用,这是由于长链的游离基吸收氧而生成氧化物,使链终止。其反应如下:
CH2—CHCl+nO2CH2—CHCl—O—O
生成的氧化物在PVC中,使热稳定性也显著变坏,产品易于变色。
氧含量对聚合反应中聚合物聚合度的影响,如表2-8所示。
表2-8 氧含量对聚合度的影响

氧含量对聚合反应速率的影响见表2-9,由于氧的存在会引起聚合体系pH值降低,随之粘釜也会加重。
表2-9 氧含量对聚合反应速率的影响

氯乙烯的悬浮聚合中的氧,一是来自于水相,常温下水中含氧约10mg/L,二是来自于气相,气相的含氧则与加料方式、加料系数、釜内气体置换有关。
如采用密闭的入料和连续的入料聚合工艺,则气相的含氧可以大大降低,只要认真地将清釜开盖后第一釜的排气置换彻底就可以了。但是水相中含氧的彻底解决,要向等温水入料方向和入水的真空脱氧方向发展,这样含氧所带来的弊病才能克服。
2.8.2 铁对悬浮聚合的影响
铁的存在除了对产品的热性能产生极大的影响之外,尚有延长聚合反应的诱导期、降低产品的热性能和电性能的作用,粘釜也相应加重。
在使用纤维素醚类的分散剂时,铁的存在会降低凝胶温度,易于产生粗料。
铁的存在主要是单体中的HCl所致,为此除了严格地控制VCM中的铁含量(一般要求1mg/L以下)之外,对聚合物料接触的管道、阀门、设备一般使用耐腐蚀材料。利用固碱干燥脱除VCM原料的水也是有效的除铁方法。
在聚合体系中,为了减轻铁离子的影响,常加入铁离子螯合剂,EDTA是较好的铁离子螯合剂,它不但可以螯合部分铁离子,达到稳定体系的作用,而且对树脂的白度、增塑剂吸收性能也会无不良影响。
2.8.3 高沸点物对悬浮聚合的影响
高沸物的主要来源是单体,单体中的乙烯基乙炔、乙醛、1,1-二氯乙烯、1,1-二氯乙烷、1,2-二氯乙烷等,都是比较活泼的链转移剂。
在聚合反应中,它们能使增长着的聚氯乙烯链发生转移,从而降低聚合度和聚合反应速率。较低含量的高沸物的存在,可以消除高分子长链端基的双键,似乎对热稳定性略有好处,但是较大量的高沸物的存在对产品的聚合度、反应速率产生较大影响这是肯定无疑的。乙醛、1,1-二氯乙烷对聚合产品聚合度的影响见表2-10、表2-11。
表2-10 乙醛对聚合产品聚合度的影响

表2-11 1,1-二氯乙烷对聚合产品聚合度的影响

提高单体纯度,是减少这些杂质的关键。
2.8.4 氯离子对悬浮聚合的影响
聚合用水中Cl-的存在,对聚合物颗粒度影响很大,特别是使用PVA分散体系时,会使颗粒变粗,其影响如表2-12所示。
表2-12 Cl-对PVC颗粒度的影响

所以一般聚合用水的Cl-浓度控制在10mg/L以下。
2.8.5 聚合工艺对悬浮聚合的影响
除了上述种种因素之外,工艺对聚合反应及产品质量也将产生较大的影响,分述如下。
2.8.5.1 加料顺序
众所周知,加料顺序与产品质量有直接的关系。对于悬浮聚合来讲,正常的加料方式是先加入水,再加助剂及原辅材料,之后搅拌进行聚合反应。此种加料方式称之为正加料。
正加料的顺序不利于引发剂均匀地分散在每个单体油珠之内,根据国外的经验,每个单体油珠只有通过搅拌使之反复进行聚集又分散,才能使引发剂均匀地分配。这个过程是相当长的,在瘦长型的釜内,如13.5m3釜,约3h或更长的时间才能完成。在强烈的剪切力存在下,也至少需要1h。所以在加料后、聚合反应进行之前需要冷搅拌一段时间。离开了这个过程,引发剂在单体内溶解得不均匀,会产生快速粒子,使产品鱼眼大幅度增加。
为了使引发剂溶解在单体内,产生了另一种加料方式——倒加料。即先加单体及引发剂,后加水及助剂。
这种加料方式能使引发剂均匀地溶解在单体中,对解决引发剂分配不均带来的鱼眼是行之有效的。尤其对固体的引发剂就显得更重要了。
这两种加料方式哪一种较好呢?首先分析一下悬浮过程。在加料时,悬浮过程就已经开始:正加料时,加水之后,开始加入单体,水是大量的连续相,此时单体即迅速地被搅拌剪切、分散,在分散剂的作用下形成一个个油珠。倒加料时,加入单体之后,开始加水,单体是连续相,开始加入的水悬浮在单体中,形成一个个水珠。只有随着水的不断加入,才使水相逐渐地变成连续相。这个变相,称为相逆转。悬浮在单体中的水珠,外层有单体,最后被分散开来,很难冲破分散剂的保护,再回到水相中去。最终可能形成空壳粒子和变形颗粒,对颗粒形态产生不利的影响。所以悬浮聚合在解决了引发剂溶解问题之后,采用正加料方式较为理想。
2.8.5.2 中途注水
要改善聚合釜的传热性能,缩小釜内反应的温差,就必须保持传热介质水的稳定。
结合我国目前条件,尚不具备随着反应进行不等量注水的工艺,大多数仍采用等量注水的工艺措施。
①注水时间和注水量的确定。关于注水时间,在等温水入料的情况下,以加入引发剂后即开始注水为宜。因为普遍情况下,在使用复合引发剂时,反应基本在1.5h左右开始加剧放热,需用水补充其收缩部分,而此时再注水就有些来不及了,故以在加完引发剂就开始注水为宜。关于注水量的计算,在笔者实践中,应计算两个用量:VCM的体积收缩量;所生成树脂增塑剂的吸收量,二者合起来为宜。
下面以70m3聚合釜为例加以说明:
首先计算70m3釜的装填系数,70m3聚合釜,内冷管、搅拌轴和搅拌叶占据的容积约为2m3左右,有效容积为70-2=68(m3)。总加入量为68×0.9=61.2(m3)
加料容积:
加单体25~27m3;
加料过程的各种冲洗水,大约3m3;
加入水大约30m3;
按此计算至少还留有1.2m3空间。
下面来计算单体的体积收缩量:
转化率按85%计算:
27m3×0.85=22.95m3
单体体积收缩量约为0.3
22.95×0.3=6.885(m3)
这个量为注水的第一计算量。
第二注水量计算:
第二注水量应为实际转化为聚氯乙烯的数量乘上实际产PVC的增塑剂吸收率,实际上70m3聚合釜单釜产约21m3左右PVC,增塑剂吸收率依型号不同有些差异,以21%来计算,则21×0.21=4.41(m3)
将上述两个注水量相加:
4.41+6.885=11.295(m3)
由于聚合釜有下轴封注水,注水量一般均为0.5m3/h,则反应开始前已开始注下轴封水,大约1h,加上反应时间,共4.5h,则注水量应为:11.295-2.25=9.045(m3)≈9(m3)
通过以上计算得出,70m3聚合釜反应中途注水量应该为9m3。
反应时间以加完引发剂开始计算,每小时注水量应为2m3/h。
当然注水量在反应后期已经意义不大了,也可以增加前期、中期注水量,在反应结束前1h可以少注水或不注水。
②注水的方法。注水一般采用流量计计量,其小时注水量由计算得到。在通常生产中,为保证注水泵连续、可靠工作,应考虑使用两台,而且注水泵是连续操作的,其压力应大于釜内所生产型号的最大压力。
对注水管线的要求:装有限流孔板,其孔径要预先进行流量的测量,主要目的是一旦流量计发生损坏或偏差时,可转而由时间测定,完成该釜的注水;釜上装有止逆阀,以防一旦注水泵发生故障,釜内的VCM排入水泵。
在不具备仪表、流量计时,也可以简单地用限流孔板计算,靠控制注水时间完成注水工艺。