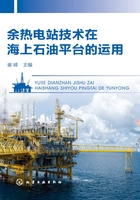
1.2 涠洲终端燃气轮机发电机组
1.2.1 燃气轮机工作原理和结构
1.2.1.1 基本原理
图1-1说明了燃气轮机工作的基本原理。如图1-1(a)所示,在气球内的压缩空气将力作用于气球的边缘上。按照定义,具有重量并占有空间的空气具有质量。空气的质量和它的密度成正比,密度与压力、温度成比例。如Boyle定律和Charles定律(PV/T=K)所述,随着温度升高和压力降低,空气中的分子进一步分开,随着温度降低和压力升高,空气中的分子更接近。

图1-1 燃气轮机工作原理
如图1-1(b)所示,被限制在气球内的空气,当它被释放时,它会加速离开气球,产生力。如同牛顿第二定律(F=MA)中所说的那样,这个力会随着质量加速度的增加而增加。由气球内空气质量加速度产生的力导致一个大小相等而方向相反的力,该力使气球向相反方向推动。
代替气球内的空气,如图1-1(c)所示,不能持续维持所需的作用力;如图1-1(d)所示,允许一个负荷被加速穿过并驱动一个“涡轮”的空气质量的力驱动。
图1-1(e)说明了维持一个加速的空气质量的力被用来驱动一个负荷的更实用的方法。该机壳包含固定体积的空气,空气被由原动机驱动的压气机压缩,被压缩的空气加速离开机壳,驱动被连接到负荷的一个“涡轮”。
如图1-1(f)所示,空气被喷入压气机和涡轮之间,以便进一步加速空气质量,从而增加被用来驱动负荷的力。图中指出,由于负荷增加,驱动压气机的原动机也更大,并且必须更费力地工作。
如图1-1(g)所示,原动机被拆除并且压气机由部分燃气驱动,因此只要提供燃料,就能使发动机自给自足。
图1-1(h)代表典型的燃气轮机工作原理,进气被压缩,与燃料混合并被点火,高温燃气膨胀通过涡轮,提供机械功来驱动压气机,并且剩余的一些功率用来驱动负荷,之后高温燃气被排到大气中。
1.2.1.2 发动机循环设计
燃气轮机的工作循环类似于四冲程活塞式发动机的工作循环。但在燃气轮机中,燃烧是在恒定的压力下产生的;而在活塞式发动机内,燃烧是在恒定的体积下进行的。这两种发动机循环都表明,每种情况下都存在吸入(空气或空气燃料)、压缩、燃烧和排气。在活塞式发动机的情况下,这些过程是间歇的,而在燃气轮机中是连续的。在活塞式发动机内,生产功率中只使用一个冲程,其他冲程被包含在工作流体吸入、压缩和排出中。比较起来,燃气轮机消除了三个“无功”的冲程,因此使得更多的燃料能在更短的时间内燃烧。
燃气轮机工作循环最简单的表现形式是压力-体积图,如图1-2所示,这个过程被称为布雷顿循环,在所有的燃气轮机中都发生这个过程。

图1-2 布雷顿循环示意图
布雷顿循环各阶段工作过程说明如下:
① 点A表示在大气压力下的空气,它沿AB线被压缩。压缩发生在压气机进口与出口之间。在此过程中,空气的压力和温度增加。
② 从B到C,通过引入燃料并在等压下燃烧燃料,把热量加给空气,从而显著增大了空气的体积。燃烧在燃烧室内发生,在燃烧室内,燃料和空气被混合到易爆炸的比例并点火。
③ 当高温燃气离开燃烧室加速时发生膨胀,燃烧室内的压力损失由B与C之间的压力降显示,这些燃气以恒定的压力进入涡轮并通过它膨胀。
④ 从C到D,高温燃气通过涡轮膨胀并排到大气中,在循环的这一部分,超过88%的气流能量由涡轮转变成机械功,在发动机排气管处出现排气,体积增加,压力恒定。
1.2.1.3 单轴与双轴发动机结构的比较
图1-3是传统的单轴与双轴装置示意图。轴流COMP(压气机)、CT(压气机涡轮)和PT(动力涡轮)全是机械连接的。如果把发电机和齿轮箱加到这个轴上,就会有一个具有高惯性矩的轴系,并且这对于发电机是有利的结构,因为在大的负荷波动时,它可以提供电流附加的速度(频率)稳定性。

图1-3 单轴与双轴装置示意图
对工业双轴结构而言,只是压气机和压气机涡轮被连接在一起,并且它们与动力涡轮和输出轴无关(指在机械上不连接),以便独立地旋转。这种结构对于变速驱动成套装置,如泵和压缩机都是有利的,因为燃气发生器可以针对给定的负荷以其最佳的速度运转。这种双轴仍然可用于驱动发电机,但在任何情况下它的负荷接受能力通常被限制为全输出功率的1/3。
图1-4表示一种更复杂的航改型工业燃气轮机结构。这基本上仍是一种双轴结构,但是燃气发生器的核心(原来的喷气发动机)被设计成具有两个转子、一个低压轴和一个高压轴。

图1-4 航改型工业燃气轮机结构示意图
航改型燃气轮机既在机械驱动装置中得到了广泛的应用,也在发电机驱动装置中得到了广泛的应用。在当前的市场中最著名的发动机是GE(美国通用电气公司)生产的LM系列燃气轮机。
1.2.1.4 多级轴流式压气机基本结构及原理
(1)基本结构
轴流式压气机的通流部分分为三种基本的型式:等内径、等外径、等平均直径。等内径的优点是每级平均直径小而使叶片高,可获得较高的效率,还易于把通流部分分成几个级组,每个级组设计成同一叶型以便于加工。等外径的优点是平均直径逐级增大,即圆周速度逐级增大,故每级的平均做功量大于等内径的而使级数较少,其次是气缸平直且易于加工。等平均直径的级数及效率介于两者之间。在使用中,有将上述两种或三种型式混合应用的方案,以及用内、外径和平均直径都在变的型式。在工业燃气轮中,压气机多数采用等内径的型式。
① 进气机匣 进气机匣(气缸也叫机匣)中收敛器流道截面不断缩小,应满足气流在其中均匀加速的要求,同时使气流较为均匀地流入进口导叶,以保证压气机达到良好的性能。进气机匣一般是铸造的,应注意收敛器流道及筋板表面的清洁处理及打光,而收敛器出口通道则需经机加工来获得所要求的尺寸。
压气机出口扩压器性能的好坏对压气机效率有直接影响。在扩压角2γ为10°~12°时扩压效率较高,这时轴向尺寸较长。在机组的轴向尺寸允许时,采用直线扩压器较好。但有不少机组为使转子的临界转速符合要求,需尽量压缩机组轴向长度来增大转子的刚性,这时将采用弯曲流道的扩压器。
② 压气机转子 压气机转子是高速旋转的部件,它把从透平传来的扭矩传给动叶以压缩空气,这一特点决定了转子对强度有较高的要求。刚度问题主要反映在临界转速上,机组的工作转速应避开临界转速,最大工作转速低于一阶临界转速的称为刚轴,它要求临界转速高于最大工作转速20%~25%。工作转速高于一阶或二阶临界转速的称为柔轴。对于工作转速变化的转子,为使在工作转速范围内避开临界转速,常常希望设计成刚轴。应指出,转子的临界转速除与自身的刚性有关外,还与轴承处的支承刚性密切有关。对于用在车、船等运输机械上的燃气轮机,在工作时还要承受惯性力、陀螺力矩及冲击力等,它对转子的强度和刚度提出更高的要求,使在这些力的作用下不仅强度足够且变形很小。此外,转子上各零件的连接应结实可靠,并准确地相互对中,以确保安全运行。
压气机转子的结构型式可分为鼓筒式、盘式、盘鼓混合式三种。盘鼓混合式按其连接方式的不同,又可分为焊接转子、径向销钉转子、拉杆转子等。另一种分类是把转子分为不可拆卸与可拆卸两类。在轴向装配式的机组中,若装拆压气机时要求转子解体的,就必须采用可拆卸转子,而且要求装拆方便,只有拉杆转子才有可能满足这些条件。
③ 压缩机动叶 压缩机动叶是高速旋转的叶片,又称为工作叶片,它把透平的机械功传给空气,是压缩空气的关键零件。动叶和静叶的好坏对整台机组有很大的影响,同时和机组的安全工作、尺寸、重量等均有很大关系。动叶使用的主要要求有:良好的气动性能、能高效率地压缩空气、有较高的机械强度、能承受巨大的离心力及其他引起的应力、在工作中能避免共振或有良好的振动阻尼、加工方便、便于装拆等。
a. 叶身 叶身即叶片的型线部分。目前的叶型都是经过大量试验得到的,虽然具体的型线有多种,但都有着共同的特点,即叶型较薄、折转角θ较小(与透平叶型相比),这是由扩压流动的特点决定的。亚声速叶型进气边头部因角半径大些,最大厚度约在靠近进气边沿弦长的1/3处,出气边则较薄。而跨声速级的特点是进出气边均较尖,目前用得较多的双圆弧叶型,叶型左右对称,进出气边端部圆角很小。为符合气动要求,动叶沿叶高均设计成扭转叶片,以获得高的效率。为改善叶顶处的流动状况,有的还采用顶部中弧过弯结构,这时叶顶处内弧部分削去一部分材料,剩下的是很薄的叶尖,其折转角要比原来的叶型大。因此,叶尖部分的加功量增大,提高了壁面气流的能级,增大“唧送”作用,使壁面附面层延迟分离,扩大了压气机的稳定工作范围,有利于提高压比及效率。削薄叶顶还允许采用较小的径向间隙来减少漏气损失。为降低叶型根部截面处的应力以及使沿叶高的应力分布差别缩小,动叶都设计成沿叶高逐渐减薄的结构,有的还适当减小叶片弦长。沿叶高各截面的重心应在一条直线上,且希望该线与转子的辐射线不重合而有一夹角,它应偏向于背弧一侧,使工作时产生一离心力弯矩来同气动弯矩相抵消,这也可减小叶根截面处的应力。
由于叶片进口气流总是不均匀的,因而叶片要受到周期性变化的力的作用,此即激振力,它将使叶片振动。当激振力的频率和叶片的自振频率相重合时,叶片就要共振。在燃气轮机运行的事故中,叶片因振动发生裂纹甚至断裂的事故相当多,故设计时必须充分注意,应使叶片自振频率避开激振频率。对一些长的压气机叶片来说,由于叶片长而薄,振动应力大,在无法避免振动时应采取阻尼措施。在叶片上加装阻尼凸台是目前普遍采用的措施。当叶片装在轮盘上后,各叶片上的阻尼凸台相互靠着而形成一环状箍带,在叶片振动时,凸台接触面处发生高频摩擦而起减振作用。此外,阻尼凸台还同时作为叶片的辅助支点,以降低根部截面的弯曲应力。阻尼凸台的位置一般在叶高的一半以上,不少机组在2/3叶高左右。凸台的接触面应喷涂硬质合金以抗磨损,例如等离子喷涂碳化钨与纯钴。
某些压气机长叶片在工作时还会发生颤动,它是叶片在高速气流中产生的自激振动,对叶片的危害和强迫振动是一样的。但是,颤动不可能像发生强迫振动时那样通过叶片调频或改变激振力的频率来避开,而主要依据气动特性改进的实验研究来设法消除。
目前,由于叶片精密成型工艺进展迅速,各种复杂形状的叶片均可得到且保证质量,故设计叶片型面主要是考虑和满足气动及强度的要求,以获得良好的性能。但是,为了降低加工成本,工业型燃气轮机往往把相邻几级叶片设计成同样的型面,用顶截的办法来获得不同的动叶高度。于是,压气机就分成了几个级组,每个级组为同一种叶型,使整台压气机中只有几种叶型,减少了工艺装备,降低了制造成本。叶身的加工精度要求高,型面的偏差一般为0.05~0.15mm。叶片表面要抛光,以获得光滑的流道和提高叶片表面的疲劳强度。
b.叶根 叶根是动叶与轮盘连接紧固之处,对它的要求是:保证连接处有足够的强度、应力集中小、对轮盘强度的削弱少;连接可靠、保证安装位置准确;便于加工、拆装方便;对航空机组来说,还要求叶根重量轻、尺寸小。压气机动叶的叶根,按其装配方式来说,有周向装入、轴向装入及插入式等几种。叶片装在轮盘的圆周向根槽中,常用于鼓筒式转子和焊接转子。
叶根的型式包括T形叶根、齿形叶根等。T形叶根的结构较简单,加工较方便,但其承截面积较小,主要用于不太长的叶片。为使叶片能装入转子上的根槽中,必须在根槽上开专门的槽口。把两相邻根槽之间铣出一燕尾形槽口,这两级叶片即可从该处装入转子的根槽中,然后把叶片推至需要的位置。在装入最后几片叶片之前,应先把锁紧块放入槽口内,在装入最后一片叶片后,将锁紧块推向两侧,中间打入楔块,再用骑缝螺钉把楔块固定在转子上。这种叶根结构的缺点是叶片装拆不方便。齿形叶根的优点是承截面积比T形叶根大,缺点是加工难度要大些。在两动叶之间采用隔叶块的结构,用隔叶块使叶片装配简化。原因是叶根及隔叶块的平行四边形,其短的一条对角线与根槽边的夹角α大于90°,把叶片放入根槽后再按顺时针方向旋转,叶根就可和根槽相配合,之后再将叶片与已装好的相邻隔叶块推紧。隔叶块的装配也一样。当装至最后的隔叶块时,把隔叶块分为三块,先装入两旁的那两块,再打入中间楔块并冲铆之,有时甚至焊住以确保可靠。当一个隔叶块的位置空着但还不够装入一片叶片时,需要将最后两个隔叶块都做成相同的锁紧结构,使多空一个隔叶块的位置来装末叶,在末叶装入后再装该两锁紧隔叶块。因此,齿形叶根结构不仅叶片装拆方便,且转子上不需开装叶片的槽口。但是,当叶根平行四边形的夹角α≤90°时,就无法将叶根旋转至和根槽相配合的位置,这时仍需开槽口,装配方法同T形叶根。
④ 气封 气封是减少漏气的装置,是压气机气流通道中不可缺少的部件。透平中亦然,并广泛用它来控制转子的冷却空气流量。气封的功能是减少漏气量。但在不同的应用部位,它的作用不同。
在压气机的进气端的空气是被吸入的,即在进口导叶处的静压低于大气压力,因而该处转子和静子之间的间隙有空气被吸入。通常该处紧靠着轴承座,运行时将有油雾自轴承座中漏出,正好随空气被吸入压气机而粘在叶片表面,形成污垢使效率降低。因此,在该处应采取措施,不让有油雾的空气被吸入,常用的是气封封气装置,如图1-5所示。

图1-5 气封封气装置示意图
它从压气机中间某级引来一股比大气压力高的压力空气,在气封中气流分为两股,一股流入大气,另一股流至压气机进口回到通流部分中,这时含有油雾的空气就不会被吸入了,该封气装置中的气封起着减少消耗引来的压力空气的作用。另有一种是把压力空气引到空腔中,然后一部分经轴端气封漏至大气,另一部分流回通流部分。这时在进口导叶底部与转子之间亦需装气封,以减少向通流部分的漏气。该种引气方式使A腔中的压力升高,变为引来空气的压力,同时起着平衡转子轴向推力的作用。当然,也有一些机组只是采用气封来减少被吸入的空气量,而不是用来平衡轴向推力。但是,这时轴承座处的密封应采取措施,以防油雾漏出。
在压气机出口处是高压空气,需用气封来减少漏气。整体式结构的单轴燃气轮机,当转子采用两端支承时,该气封正好在压气机出口和透平进口之间,作用是控制流到透平中的冷却空气量。
有静叶内环的压气机,由于静叶出口侧的压力高于进口侧,故出口侧的空气要从内环与转子之间的间隙漏至进口侧。因此在静叶内环上要加气封,以减少漏气来提高效率。
(2)压气机喘振机理
① 发生喘振现象的原因 如果流经压气机的空气流量减小到一定程度,那么空气流量会忽大忽小,压力会时高时低,甚至会出现气流由压气机倒流到外界大气中的现象,同时还会发生巨大的声响,使机组伴随强烈的振动,这种现象通称为喘振现象。在机组的实际运行中,决不能允许压气机在喘振工况下工作。
那么,喘振现象究竟是怎样产生的呢?通常认为:喘振现象的发生总是与压气机通流部分中出现的气流脱离现象有密切关系。
当压气机在设计工况下运行时,气流进入工作叶栅时的冲角接近于零。但是当空气体积流量增大时,气流的轴向速度就要加大。假如压气机的转速n恒定不变,将会产生负冲角(i<0)。当空气体积流量继续增大,而使负冲角加大到一定程度,在叶片的内弧面上就会发生气流边界层的局部脱离现象。但是,这个脱离区不会继续发展。这是由于当气流沿着叶片的内弧侧流动时,在惯性力的作用下,气体的脱离区会朝着叶片的内弧面方向聚拢和靠近,因而可以防止脱离区的进一步发展。此外,在负冲角的工况下,压气机的级压比有所减小,即使产生了气流的局部脱离区,也不至于发展成气流的倒流现象。
可是,当流经工作叶栅的空气体积流量减小时,情况将完全相反。那时,气流的β1和α2角都会减小。然而,当β1和α2角减小到一定程度后,就会在叶片的背弧侧产生气流边界层的脱离现象。只要这种脱离现象一出现,脱离区就有不断发展扩大的趋势。这是由于当气流沿着叶片的背弧面流动时,在惯性力的作用下,存在着一种使气流离开叶片的背弧面而分离出去的自然倾向。此外,在正冲角的工况下,压气机的级压比会增高,因而当气流发生较大的脱离时,气流就会朝着叶栅的进气方向倒流,这就为发生喘振现象提供了前提。
试验表明:在叶片较长的压气机级中,气流的脱离现象多半发生在叶高方向的局部范围内(例如叶片的顶部)。但是在叶片较短的级中,气流的脱离现象却有可能在整个叶片的高度上同时发生。研究表明:在环形叶栅的整圈流道内,可以同时产生几个比较大的脱离区,而这些脱离区的宽度只不过涉及一个或几个叶片的通道。而且,这些脱离区并不是固定不动的,它们将围绕压气机工作叶轮的轴线,沿着叶轮的旋转方向,以低于转子的旋转速度连续地旋转。因而,这种脱离现象又称为旋转脱离(旋转失速)。当压气机在低转速区工作时,经常会出现旋转失速现象。它最严重的后果是会使叶片损坏,从而有可能使整台压气机破坏。
通过以上分析可以看清:气流脱离现象(失速)是压气机工作过程中有可能出现的一种特殊的内部流动形态。当空气体积流量减少到一定程度后,气流的正冲角就会加大到某个临界值,以致在压气机叶栅中,迫使气流产生强烈的旋转失速流动。那么,在压气机中发生的强烈旋转失速为什么会进一步发展成为喘振现象呢?
下面用图1-6来简单地说明一下喘振现象的发生过程。假如压气机1后面的工作系统2可以用一个容积为V的容器来表示。流经压气机的流量可以通过装在容器出口处的阀门3来调节。那么,当压气机的工作情况正常时,随着空气体积流量的减少,容器中的压力就会增高。但是,当体积流量减少到一定程度时,在压气机的通流部分中将开始产生旋转失速现象。假如空气的体积流量继续减小,旋转失速就会强化和发展。当它发展到某种程度后,由于气流的强烈脉动,就会使压气机的出口压力突然下降。那时,容器中的空气压力要比压气机出口的压力高,这将导致气流从容器侧倒流到压气机中去;而另一部分空气则仍然会继续通过阀门流到容器外面去。由于这两个因素的同时作用,容器的压力就会立即降低下来。假如当时压气机的转速恒定不变,那么随着容器压力的下降,流经压气机的空气体积流量就会自动地增加上去;与此同时,在叶栅中发生的气流失速现象逐渐消失,压气机的工作情况将恢复正常。当这种情况继续一个很短的时间后,容器的压力会再次增高,流经压气机的空气流量又会重新减少下来,在压气机通流部分中发生的气流失速现象又会再现。上述过程就会周而复始地进行下去。这种在压气机和容器之间发生的空气流量和压力参数的时大时小的周期性振荡,就是压气机的喘振现象。

图1-6 喘振现象示意图
1—压气机;2—工作系统;3—阀门
总之,在压气机中出现的喘振现象是一种比较复杂的流动过程,它的发生是以压气机通流部分中产生的旋转失速现象为前提的,但也与压气机后面的工作系统有关。试验表明:工作系统的体积越大,喘振时空气流量和压力的振荡周期就越长,而且对于同一台压气机来说,如果与它配合进行工作的系统不同,那么在整个系统中发生的喘振现象也就不完全一样。
喘振对压气机有极大的破坏性,出现喘振时,压气机的转速和功率都不稳定,整台发动机都会出现强烈的振动,并伴有突发的、低沉的气流轰鸣声,有时会使发动机熄火停车。倘若喘振状态下的工作时间过长,压气机和燃气涡轮叶片以及燃烧室的部件都有可能因振动和高温而损坏,所以在燃气轮机的工作过程中决不允许出现压气机的喘振工况。最后应该指出:喘振和旋转失速是两种完全不同的气流脉动现象。喘振时通过压气机的流量会出现较大幅度的脉动。而旋转失速会造成压气机轴旋转区域的流量降低,但通过压气机的平均流量是不变的。
研究表明:当压气机在低于设计转速的情况下工作时,在压气机的前几级中将会出现较大的正冲角,而后几级中却会形成负冲角。因而当空气流量降低到某个极限时,在压气机中容易发生因前几级出现旋转失速而导致的喘振现象。反之,当压气机在高于设计转速情况下工作时,压气机的后几级中则会发生正冲角,那时喘振现象多半是由于发生在后几级中的旋转失速现象引起的。
最后,对压气机的喘振现象可以归纳出以下几点看法:
a.级压比越高的压气机或者是总压缩比越高和级数越多的压气机,就越容易发生喘振现象。这是在这种压气机的叶栅中,气流的扩压程度比较大,因而也就容易使气流产生脱离(失速)现象。
b.多级轴流式压气机的喘振边界线不一定是一条平滑的曲线,而往往可能是一条折线。据分析认为:其原因可能是在不同的转速工况下,进入喘振工况的级并不相同。
c.在多级轴流式压气机中,因最后几级气流的旋转失速而引起的喘振现象会更加危险,因为那时机组的负荷很高,而这些级的叶片又比较短,气流的失速现象很可能在整个叶高范围内发生,再加上当地的压力又高,压力的波动比较厉害,因而气流的大幅度脉动就会对机组产生非常严重的影响。
d.进排气口的气流流动越不均匀的压气机就越容易发生喘振现象。
② 防止喘振的措施 概括起来说,防止发生喘振现象的措施有以下五个方面:
a.在设计压气机时应合理选择各级之间的流量系数,力求扩大压气机的稳定工作范围。
b.在轴流式压气机的第一级或者前面若干级中装设可转导叶,当流进压气机的空气流量发生变化时,可以关小或开大可转导叶的安装角γp来减小或消除气流进入动叶时的正冲角,从而达到防喘的目的。由于在低转速工况下,压气机的前几级最容易进入喘振工况,因而通常把压气机的第一级入口导叶设计成可以旋转的。采用可转导叶的措施不仅可以防止压气机的第一级进入喘振工况,而且还能使其后各级的流动情况得到改善。因为当压气机动叶中气流的正冲角减小时,级的外加功量就会下降,也就是说,在压气机第一级出口处空气的压力比较低,这样就可以增大流到其后各级中的空气体积流量,使这些级的气流冲角适当减小,因而有利于改善这些级的稳定工作特性。
c.在压气机通流部分的某一个或若干个截面上安装防喘放气阀。
鉴于机组在启动工况和低转速工况下,流经压气机前几级的空气流量过少,以致发生较大的正冲角,而使压气机进入喘振工况,于是人们就设想出在容易进入喘振工况的某些级的后面开启一个或几个旁通放气阀,迫使大量空气流过放气阀之前的那些级,那么就有可能避免在这些级中产生过大的正冲角,从而达到防喘的目的。
d.合理地选择压气机的运行工况点,使机组在满负荷工况下的运行点离压气机喘振边界线有一定的安全裕量。
e.把一台高压比的压气机分解成两个压缩比较低的高、低压压气机,依次串联工作,并分别采用两个转速可以独立变化的涡轮来带动的双轴(转子)燃气轮机方案,可以扩大高压比压气机的稳定工作范围。
总之,通过以上五个措施,可以防止在压气机中发生具有破坏性的喘振现象,有利于扩大整台机组稳定工作的范围。
1.2.1.5 燃烧室基本结构及原理
燃烧室是组成燃气轮机的又一个主要部件,燃烧室的功能是保证压气机提供的高压气流与外部燃料系统注入的燃料充分混合燃烧。燃烧室结构通常由下列部件组成:外壳、火焰管、火焰稳定器、燃料喷嘴、点火设备和观察孔等。燃烧室的型式按布置方式可划分为分管型、环型、环管型、管头环型、双环腔型和圆筒型等。按气流通过燃烧室的流程来划分,又可分成直流式、回流式、角流式和旋风式等。
对于典型的“管式”燃烧室,火焰稳定的流谱如图1-7所示,大多数工业燃气轮机以圆周方向排列不同数目的火焰筒(管)的型式使用这种型式的燃烧室,航改型燃气轮机已从这种设计演变到一种单环燃烧室,多个燃料喷嘴沿圆周方向均匀分布,全部等压燃烧的燃气轮机的燃烧室均依据同样的原理工作。

图1-7 燃烧室结构示意图
为了使系统能有效地工作,燃气轮机的燃烧室必须满足以下三个主要的功能:
① 保护燃烧室外机匣免受对流和辐射的传热,这是因为该机匣是一个压力容器。
② 减小空气速度到能使火焰稳定的量级。
③ 在热燃气冲击到涡轮静止的和旋转的组件的部件上以前,把燃烧产物温度降到可接受的范围。
当发动机正以满负荷运行时,在火焰的顶部(末端)接近1760℃,在燃烧室结构内的金属材质无法承受这一范围内的温度。所以,在燃烧室内壁和外壁之间设计空气流通通道,用于冷却和火焰成形,流入内室的空气通过小孔被引导,使火焰在燃烧室内成形,防止它与燃烧室(火焰筒)壁接触,进入燃烧室的82%空气流用于冷却和火焰成形,仅仅18%被用作燃料燃烧。
在设计条件下,燃烧室内火焰的稳定性是极为重要的,当火焰锋面以高的频率前进和后退时,产生不稳定的火焰。这引起一个压力波系,该波系将加速涡轮热部分的机械疲劳破坏。按照图1-8所示,通过设计可以避免出现这种情况,从图说明中可以看到,如果燃烧室被限定在稳定性回路内的质量流量和空气/燃料比的整个范围内运行,则火焰将稳定运行。该回路的边界同时指示了出现不稳定性的条件。

图1-8 稳定回路示意图
1.2.1.6 透平叶片基本结构及原理
透平叶片是燃气轮机的又一主要部件,它的功能是将高温高压燃气中的能量转变为机械能,其中约3/5~2/3的能量用以带动空气压气机压缩空气,其余的能量则作为燃气轮机的输出功率以带动负载。
透平叶片分成向心式、轴流式等。由于向心式结构复杂,而且单级功率有限又难以串接多级,所以实际使用的机组主要采用轴流式燃气涡轮发动机。其特点是功率大、流量大、效率高。向心式透平是一种径流透平,主要在一些小功率燃气轮机中应用。相对于压气机来说,透平的一个显著不同是工作气体温度高。目前,工业用燃气透平机透平进口燃气温度为900~1100℃,而航机还要高,最高已在1400℃以上。另一个不同是透平级中能量转换大,如部分透平焓降高达75kcal/kg(1kcal=4186.8J),因而透平级的气动负荷大,整个透平的级数少。一些小功率燃气轮机的透平只有一级,而大多数燃气轮机的透平则为2~4级,多的达5~7级,我们所使用的为4级透平。多数透平的通流部分,通常用的是等内径或等平均直径流道,或与该两者相近的流道,等外径的则应用较少。
与压气机相类似,气流在透平中流动的通道也是由静叶片和动叶片交替排列而成的。虽然压气机和透平都是由动、静叶片组成,但二者本质上是不同的,压气机的动、静叶片组成一个沿轴向逐渐收缩的通道,使空气由外界吸入后逐级被压缩,而透平的动、静叶片组成一个沿轴向逐渐扩张的通道,使高压、高温燃气在这个通道中逐级膨胀做功。由于透平的工作温度相比压气机的工作温度要高得多,所以透平的结构设计上在考虑冷却、热膨胀等问题上要做出特殊处理。一般来说,透平进口的几级静叶采用一定的冷却,尤其是与燃烧室出口相连的首级燃气涡轮静叶。一般都在结构设计上在压气机的某一级出口处引出部分压缩空气到燃气涡轮发动机作为冷却空气,用于冷却透平叶片、叶片轮盘等热部件。
(1)透平静叶
透平静叶又称喷嘴,在航机中叫作导向叶片,它的作用是使高温燃气在其中膨胀加速,把燃气的内能转化为动能,然后推动转子旋转做功。
工作时,透平静子所处的条件是很恶劣的,最主要的是被高温燃气所包围,特别是第1级静叶,它所接触的是温度最高且温度差别最大的气体。在启动和停机时,它又是受到热冲击最为厉害的零部位。因此,要求静叶必须满足耐高温、耐热腐蚀、耐热冲击、耐热应力、具有足够的刚度和强度等要求。
耐高温和耐热冲击首先是靠材料的性能来保证。目前,工作温度在800℃以上的高温的静叶,国外广泛采用铸造钴基合金,它不仅有好的高温机械性能和好的抗热腐蚀性能,还有好的抗热疲劳性能,而且铸造工艺性能好。透平静叶广泛采用精铸叶片,在它的叶身两端整体铸有外缘板和内缘板,在它们上面还有安装边。内外缘板和安装边的作用是安装固定静叶,以及把燃气与安装它的零部件隔开。为减少叶身的热应力,对处于高温部件的静叶,通常采用空心铸造叶片。空心叶片的叶身材料显著减薄,厚度趋于均匀,使叶身的热应力降低,并且还提高了抗热冲击的能力。静叶由于工作温度高和温度场的不均匀,在叶片刚度不够时较易发生扭曲和弯曲变形,单片静叶的刚性较差,在运行时易发生故障,当采用叶片时,则静叶的刚性明显增强,从而可有效地避免故障。
目前,静叶的固定方式主要是直接固定方式,虽然这种方式结构简单,但却存在着重大缺陷,即透平气缸直接与燃气相接触,因而气缸工作温度高。随着燃气初温的不断提高,上述缺点越来越严重,因而被淘汰了。所以透平静叶的固定方式最常采用持环结构。持环又称隔板套,是专门安装固定静叶的零件,静叶安装在持环上,持环再固定在气缸上。
(2)透平动叶
透平动叶是把高温燃气的能量转变为转子机械功的关键部件之一,工作时,动叶不仅被高温燃气所包围,而且由于高速旋转而产生巨大的离心力,同时还承受着气流的气动力,以及较多作用力可能引起的振动等,当燃气温度沿周围不均匀时,将使动叶承受周期性的温度变化,这在第一级动叶中较明显。此外,动叶还要承受高温燃气引起的腐蚀和侵蚀,因而透平动叶的工作条件是很恶劣的,它是决定机组寿命的主要零件之一。
透平动叶是用耐热材料的锻造毛坯经过机加工得来。近来,由于铸冶铸造工艺的进展以及耐高温的镍基铸造合金的发展,透平现已大多数采用精铸动叶,用空气内部冷却的动叶。精铸叶片不仅比锻造挤压叶片的工艺简便,且能获得复杂的内部冷却空气流道的形状,增强冷却效果,因而优点甚为显著。通常,用无裕量精铸得到的叶片叶身只需抛光即可,叶根由于精度要求高还需经加工得到。动叶的基本结构为叶身扭转,顶部带冠,根部是带工字形长柄的枞树形叶根,在叶根两侧和叶冠上有气封齿。由于透平中能量转换大,即气流速度高且转弯折转大,故相对于压气机叶型来说,透平叶型厚且折转角大,就透平自身的叶型来说,由于级中反动度的不同,分为冲动级和反动级,冲动级的焓降要比反动级的大,故冲动级的叶片更为厚实,折转角更大。透平动叶的叶冠全部拼合起来就会在叶顶处形成一个环带,将燃气限制在叶片流道内流动,有利于提高透平的效率,还可以对透平振动起阻尼作用。
(3)透平冷却系统
从燃气轮机的工作原理知,燃气初温对机组效率有很大影响,燃气初温高时效率高。故人们总希望用高的燃气初温。目前,人们从两个方面努力来不断提高燃气初温:一方面是不断研制新的耐高温的合金材料;另一方面是采用冷却叶片并不断地提高其冷却效果。
冷却叶片的方法有两类:一类是以冷却空气吹向叶片外表进行冷却;另一类是把冷却空气通入叶片内部的专门流道进行冷却。前面的叶根间隙吹风冷却就是外表冷却,它对叶根的冷却很有效,而叶身则是通过叶片本身的热传导把热量传至叶根而被冷却,故只有在靠近叶根处的叶身能得到一定冷却,其余部分叶身的冷却效果很差。这种冷却一般可使叶身的根部截面温度比该处的燃气温度低50~100℃左右。
把空气引入叶片内部的冷却方式,则能使叶片沿整个叶高都得到冷却,且可获得降温100℃以上乃至数百摄氏度的冷却效果。因而叶片内部冷却能有效地提高燃气初温。
图1-9为GE公司MS9001燃气轮机透平冷却系统图,该机组的燃气初温在基本负荷时为1004℃,尖峰负荷时可达1065℃,其一级静叶和动叶为冷却叶片。该透平上装有一个持环和三列分段护环,第一级静叶装在持环上,另两级静叶则装在护环上,气缸与燃气完全隔绝。转子是外围拉杆结构,在三级轮盘之间的两个小轮盘外缘加工有气封槽,其一端侧面加工有多条均布槽道以通过冷却空气。各级动叶均用工字形截面的长柄枞树形叶根。

图1-9 GE公司MS9001燃气轮机透平冷却系统图
该机组的压气机共十七级,按照透平冷却部位所需压力的高低,冷却空气自压气机的不同处引来,气缸及静叶的分两股,转子的分三股。静子冷却的第一股空气自压气机出口,经燃烧室的燃气导管周围空腔引来。其中一部分流入持环,再流入一级静叶内部冷却后,自静叶出气边的小孔排至主燃气流中。另一部分经一级动叶的护环流入二级静叶顶部空腔,再经二级静叶内的孔道流至静叶内环,对一级轮盘出气侧和二级轮盘进气侧进行冷却。第二股冷却空气自压气机第十级后引来,通过气缸上均布的一圈孔道对气缸进行冷却。
转子的冷却空气,分别引至其进气侧、转子内部、排气侧。进气侧处空气自压气机出口引来,用轴向间隙中的气封来控制其流量。出气侧面引来的是一股低压冷却空气。转子内部的冷却空气自压气机第十六级后引来,经转子上的孔流入转子中间,大部分经第一个小轮盘的流道流至一级动叶根部,进入动叶内部冷却后自叶顶排至主燃气流中。另一部分经第二个小轮盘的流道去冷却二级轮盘的出气侧及三级轮盘的进气侧。
从上述看出,该透平的气缸不仅与燃气隔绝,且得到了良好的冷却。静子的其他部件,如持环和前两列护环也得到了冷却。而转子,由于各级轮盘的所有表面全部被冷却空气所包围,与燃气隔绝,也得到了良好的冷却。