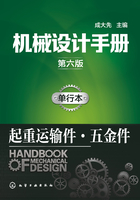
7 车轮及安全装置
7.1 车轮
7.1.1 车轮的校验计算(摘自GB/T 3811—2008)
车轮应根据等效工作轮压进行疲劳强度校验计算,应根据最大轮压进行静强度校验计算。
表9-1-121

表9-1-122 车轮的许用比压K

注:σb为车轮或滚轮材料未热处理时的抗拉强度(σb值是泛指所有采用的车轮材料,包括铸造、锻造或轧制钢和球墨铸铁等,若材料采用合金结构钢时,很难取到热处理前的σb值,故建议按合金结构钢标准规定的σb取值。对翼缘板上运行车轮计算时,考虑两者的匹配关系,许用比压K值不宜取得太小,建议取K=(3.8~5)N/mm2,甚至更小些)。
表9-1-123 车轮转速系数C1

表9-1-124 车轮直径、运行速度与转速系数C1

表9-1-125 工作级别系数C2

7.1.2 车轮
表9-1-126 车轮轮压



注:1.车轮材料60Mn。
2.轨道材料(摘自GB/T 3811—2008)。
起重机轨道材料推荐如下:轻轨推荐用力学性能不低于GB/T 11264中的55Q;铁路用热轧钢轨推荐用力学性能不低于GB2 585中的U71Mn;起重机钢轨推荐用力学性能不低于YB/T 5055中的U71Mn;当采用其他型钢、方钢、扁钢等做轨道时,应注意其材质和硬度的实际情况,必要时可降低轮压,以保证有足够的使用寿命。
7.1.3 车轮组
桥门式起重机车轮组

表9-1-127 车轮组尺寸表

CD、MD电动葫芦车轮组

表9-1-128

注:CD、MD型电动葫芦的走轮轮数与最大轮压见表9-1-129供选用车轮组时参考。
表9-1-129

7.1.4 起重机车轮型式与尺寸、踏面形状和尺寸与钢轨的匹配(摘自JB/T 6392—2008)
起重机车轮型式与尺寸

标记示例:
a.直径D=710mm,轮宽B=155mm的双轮缘车轮,标记为:车轮 SL-710×155JB/T6392;
b.直径D=315mm,轮宽B=110mm的单轮缘车轮,标记为:车轮 DL-315×110JB/T6392;
c.直径D=630mm,轮宽B=145mm的无轮缘车轮,标记为:车轮 WL-630×145JB/T6392。
表9-1-130 基本尺寸

注:本表中的基本参数(除括号内)宜优先使用。
踏面形状和尺寸与钢轨的匹配

表9-1-131

注:1.表中B值和c值分子用于小车车轮,分母用于大车车轮。
2.9kg/m、12kg/m、15kg/m、22kg/m、30kg/m轻轨按照GB/T 11264选取。
3.38kg/m、43kg/m、50kg/m、60kg/m、75kg/m热轧钢轨按照GB/T 2585—2007选取。
4.QU70、QU80、QU100、QU120起重机钢轨按照YB/T 5055—2005选取。
5.钢轨可以采用方钢,方钢顶部宽度为B2,边缘圆角为r1时,对于车轮则B=B2+2(b+c),r=r1―2,r≥2。
技术要求:
(1)材料
①轧制车轮应选用力学性能不低于GB/T 699中规定的60钢的材料。
②踏面直径不大于400mm的锻造车轮应选用力学性能不低于GB/T 699中规定的55钢的材料;直径大于400mm的锻造车轮应选用力学性能不低于60钢的材料。
③铸钢车轮应选用力学性能不低于GB/T 11352中规定的ZG340—640钢的材料。
(2)热处理
①任何加工方法制造的车轮都应进行消除内应力(如,影响使用性能的热应力)处理。铸钢车轮在机加工之前应进行退火以消除内应力,并要清砂、切割浇冒口,检验质量缺陷。
②轮辋应进行表面淬火,淬火前进行细化组织处理。热处理后,车轮表面状态宜符合表9-1-132的规定。
表9-1-132

注:根据起重机具体使用工况,允许选用硬度更高或更低的车轮。
(3)精度
①车轮踏面直径的尺寸偏差不应低于GB/T 1801—2009中规定的h9。轴孔直径的尺寸偏差不应低于H7。
②车轮踏面和基准端面(其上加工出深1.5mm的V形沟槽作标记)相对于孔轴线的径向及端面圆跳动不应低于GB/T 1184—1996中规定的8级。
(4)成品车轮的表面质量
①车轮表面不应有目测可见的裂纹。
②铸造车轮表面的砂眼、气孔、夹渣等缺陷应符合表9-1-133的规定。
表9-1-133

注:δ为缺陷处壁厚,D为车轮踏面直径。
③车轮踏面和轮缘内侧面的表面粗糙度按GB/T 1031—2009的规定为Ra6.3,轴孔表面粗糙度为Ra3.2。
④车轮踏面和轮缘内侧面上的缺陷不允许焊补。
⑤车轮的切削加工表面应涂防锈油,其他表面均应涂防锈漆。
(5)成品车轮的内部质量
对于铸造车轮,其质量应符合JB/T 5000.14—2007中2级的规定。对于锻造、轧制车轮,其质量应符合JB/T 5000.15—2007中Ⅲ级的规定。
7.1.5 CD、MD电动葫芦用钢轮

材料:45钢
调质硬度235~260HB
表9-1-134 齿的参数

表9-1-135
