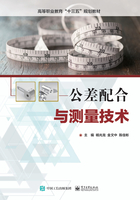
任务二 测量轴径
学习目标
1.了解常用轴径测量方法并能够判断尺寸是否合格;
2.掌握更高精度外径千分尺的使用方法。
任务呈现
图2-22所示为阶梯轴。本任务要求测量阶梯轴的径向尺寸,即轴径,并判断其是否符合要求。

图2-22 阶梯轴
任务分析
阶梯轴图中共有8个径向尺寸,为了完成本次测量任务,我们需要进一步认识一些精度更高的千分尺,了解其原理及读数方法。
知识链接
生产车间一般常用通用量具量仪及量规测量轴径,在教学过程中,测量轴径时使用较多的是游标卡尺及千分尺。对于精度要求不高的轴径尺寸可以使用游标卡尺及普通千分尺进行测量,对于有配合要求且对精度要求较高的轴径尺寸可以使用分度值更小的微米千分尺及数显千分尺等进行测量。
一、认识轴
轴通常指零件的圆柱形外表面,也包括其他由单一尺寸确定的非圆柱形外表面(由两个平行平面或切面形成的被包容面)。轴是机器中的重要零件,用于支承转动零件并传递运动和动力。轴由轴承支承,轴上被轴承支承的部位是轴颈,轴颈和轴承内孔一般采用基孔制配合。轴还要支承轴上零件,并传递运动和动力。一般,轴上安装轮毂的部位为轴头,轴头部分一般与轮毂的内孔配合,且采用键连接等周向固定方式。因为轴颈要与轴承内孔配合、轴头要和轮毂孔配合,所以轴上部分尺寸要求较高,所需要的测量量具精度要求也同样较高。
二、微米千分尺
(一)微米千分尺结构
微米千分尺结构,如图2-23所示。其与一般外径千分尺结构的最大区别在于微米千分尺固定套筒上有纵向的主尺刻度线和游标刻度线。其测量范围为0~15mm、0~25mm、25~50mm、50~75mm、75~100mm,分度值有0.001mm及0.002mm两种。

图2-23 微米千分尺结构
(二)微米千分尺的基本原理及读数方法
微米千分尺的基本原理与普通外径千分尺一样,都是利用螺旋放大原理制成的,具体读数由固定套筒上主刻度值加微分筒上刻度值加游标刻度显示数值三部分组成。以下以图2-24为例具体讲解其读数方法。

图2-24 微米千分尺读数
微米千分尺读数分四步,具体为:
(1)读出固定套筒上刻线显示的最大数值。
(2)在微分筒上找到与固定套筒中线对齐的刻线,再乘以微分筒每小格0.01mm,若固定套筒中线介于微分筒两刻度线之间,则取较小的刻度数值。
(3)找出游标刻度上与微分筒刻度线对齐的刻度线数值,乘以分度值0.001mm。
(4)将所得三个读数相加即为实测的尺寸数值。
图2-24所示微米千分尺分度值为0.001mm,固定套筒上主刻度数值为17.5mm,固定套筒中线介于微分筒49、50两刻度线之间,取较小值49,即微分筒上刻度值为49×0.01=0.49mm,游标刻度线与微分筒刻度线对齐的刻度线数值为3,即游标数值为3×0.001=0.003mm,所以测量结果为17.5+0.49+0.003=17.993mm。
三、数显千分尺
图2-25所示为数显外径千分尺,其分辨率可达0.001mm,数字显示是为了避免读数时产生视觉误差,因此使用更为方便。

图2-25 数显千分尺
任务实施
一、任务准备
在正式测量零件各部分尺寸前准备好所需的物品,包括被测零件、普通外径千分尺、微米千分尺或数显千分尺、擦拭量具用的干净棉布或纱布、维护保养所需的黄油或凡士林、记录笔、记录本等。
二、测量过程
图2-22中8个轴径尺寸为、2个
、2个φ30±0.01;前4个尺寸公差为0.039mm、0.039mm、0.03mm、0.03mm,后4个尺寸公差为0.013mm、0.013mm、0.02mm、0.02mm;前4个轴径尺寸可用普通外径千分尺进行测量,后4个轴径尺寸应用微米千分尺或者数字显示千分尺进行测量才能保证精度要求。测量完成后应认真、真实地记录测量数据。
三、测量注意事项
(1)测量前一定要校对零位,尤其是微米千分尺或者数字显示千分尺。如果测砧上面粘有脏污或灰尘,很容易产生零误差,因此需要准确校对。
(2)使用外径千分尺或微米千分尺测量时,两测量砧头应位于轴颈最大处,并与零件轴线垂直。
(3)测量轴径时,在圆柱长度上应选择2~3处截面位置测量,以确保测量的全面,减少误差。
(4)读数时视线应与刻度线垂直,避免因读数视线角度偏差造成测量结果偏差。
四、整理
将微米千分尺仔细擦净,在微米千分尺测量砧间抹上黄油或凡士林,并将测量爪或测量砧分开0.1~0.2mm。将量具放入盒内,置于干燥处。