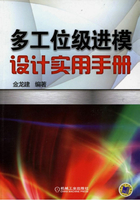
2.4 变形趋向性的控制及其运用
针对冲压加工中分离和变形两大类工序各自的特点,在工艺方案的制定及冲模设计时的侧重点也有所不同。
分离类工序由于变形及加工过程较为简单,因此,冲模设计中更侧重于模具结构的思考,主要是依据零件的具体结构和不同生产批量的要求,使设计的模具结构简单、巧妙而又实用,以满足生产及产品质量的需要。在实际设计过程中可先采用套用或仿照等方法,通过借助适当加工实例的剖析与自身的生产实践相结合,经过一定时间的锻炼,设计能力便会有较大的提高。
对变形工序类零件,由于板料塑性成形较为复杂,冲压成形时,毛坯内各处的应力与应变关系都不相同,影响正常成形过程的因素,可能发生在变形区,也可能发生在非变形区。因此,该类零件工艺方案制定和模具设计时,除了在生产实践中不断地总结和积累经验外,还必须掌握一些基本理论,学会对零件成形过程进行分析。尤其要注意到材料成形遵循“弱区先变形,变形区应为弱区”的条件。
基于这一成形条件,要使冲压工艺过程顺利地进行,在制定工艺方案时,就应针对性地创造外部条件,保证变形的趋向性符合工艺的要求,以实现对金属流动的控制。为此,必须合理确定毛坯的初始尺寸及中间毛坯的尺寸。
如图2-14a所示的环形毛坯,当其外径D0、内孔d0及凸模直径d凸具有不同的尺寸及比例时,有三种可能的变形趋向:拉深、翻边和胀形,从而形成三种形状完全不同的零件。
在图2-14b中,D0、d0都比较小,D0/d凸<2,d0/d凸<0.15,宽度为(D0-d凸)的外环部分成为弱区,于是产生外径收缩的拉深变形。
在图2-14c中,D0、d0都比较大,D0/d凸>2.5,d0/d凸>0.2,宽度为(d凸-d0)的内环部分成为弱区,于是产生内孔扩大的翻边变形。
在图2-14d中,D0比较大,d0比较小甚至等于零,D0/d凸>2.5,d0/d凸<0.15,这时,毛坯外环的拉深变形和内环部分的翻边变形的阻力都增大了,使中间部分的材料成为需要变形力最小,因而最易实现变形的部分,于是产生毛坯中间部分变薄的胀形工艺。
图2-14 环形毛坯的变形趋向
a)变形前的模具与毛坯 b)拉深 c)翻边 d)胀形
F—冲压力FQ—压边力R凸—凸模圆角半径R凹—凹模圆角半径
在模具设计过程中,对金属流动实行控制的基本原则是:开流与限流。
开流是在需要金属流动的地方减小阻力,让其顺利流动,当某处需要金属流动而又不能流入时,就会产生变薄甚至导致断流而破裂;限流则是在不需要金属流动的地方加大阻力,限制其流动,当某处不需要金属流入,而又任其流入时,金属就会多余,就会发生波浪形甚至起皱。
尽管材料本身的特性及其应力状态是影响金属流动的主要因素,但具体到模具结构的设计时,通过改变凸模与凹模工作部分的圆角半径,改变摩擦(正确的润滑,调整压边力,采用拉深筋等方法)和改变间隙等措施还是能实现对金属流动的有效控制,这些措施既可单独使用,也可综合使用。
上述措施具体实施的前提是分清变形区的部位及变形性质,这除了可通过塑性力学的分析方法来描述冲压加工中的应力、应变分布,建立主应力图、主应变图分析外,在生产实践中常利用成形试验(或试模)进行判断,因为金属流动受各种因素的影响,从试验中得到的结果既方便、准确又真实可靠。根据试验结果,可以进行有针对性的开流和限流。
1)改变凸模和凹模圆角半径。圆角半径增大,可以减小变形时的阻力,起到开流作用。如在图2-14a中,增大凸模的圆角半径R凸,减小凹模的圆角半径R凹,从而可使翻边的阻力减小,拉深变形的阻力增大,因而有利于翻边的进行;反之,R凸减小,R凹增大,则有利于拉深变形。
2)改变毛坯和模具之间的摩擦阻力。例如,增大图2-14所示的压边力FQ,使毛坯和压边圈及凹模端面之间的摩擦阻力增大,结果不利于拉深变形而有利于翻边或胀形的实现。减小压边圈的压力,在毛坯和凹模之间加润滑油,可以减小毛坯和凹模表面的摩擦阻力,从而有利于拉深变形。
此外,采取改变毛坯局部区域的温度也可获得最大程度的板料变形,这主要包括局部加热或局部冷却的方法。例如,在拉深和缩口时,采用局部加热变形区的方法,使变形区得到软化,从而有利于变形的进行。又如在不锈钢工件拉深时,采用局部深冷传力区的方法,来增大其承载能力,防止大变形下拉裂。
材料“弱区先变形,变形区应为弱区”是成形的条件,金属的“开流与限流”则是对金属流动实行控制的基本原则,掌握并合理运用好,既有助于工艺方案的制定,又有利于模具的结构设计,同时还可运用于生产中缺陷件的修复,往往能产生“出奇制胜”之效。