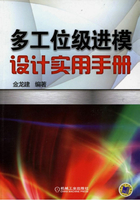
4.5 成形工艺
在级进模冲压中,除了冲裁、弯曲、拉深等主要工序外,成形工序也很常见,如翻边、翻孔、压筋、压包、压字、压花纹、整形及校平等。从变形特点来看,这类工序都以局部变形为主,受力情况各不相同。
下面主要对翻边、翻孔、校平及起伏成形工艺性作介绍。
4.5.1 翻边
翻边是沿制件外形曲线周围将材料翻成侧立短边的冲压工序,又称为外缘翻边。
常见的翻边形式如图4-42所示。图4-42a所示为内凹翻边,也称为伸长类翻边;图4-42b所示为外凸翻边,也称为压缩类翻边。
图4-42 翻边形式
a)内凹翻边 b)外凸翻边 c)复合翻边 d)阶梯翻边
1.翻边的变形程度
内凹翻边时,变形区的材料主要受切向拉伸应力的作用。这样翻边后的竖边会变薄,其边缘部分变薄最严重,使该处在翻边过程中成为危险部位。当变形超过许用变形程度时,此处就会开裂。
内凹翻边的变形程度由下式计算:
式中 E凹———内凹翻边的变形程度(%);
R———内凹曲率半径(mm),如图4-42a所示;
b———翻边后竖边的高度(mm),如图4-42a所示。
外凸翻边的变形情况类似于不用压边圈的浅拉深,变形区材料主要受切向压应力的作用,变形过程中材料易起皱。
外凸翻边的变形程度由下式计算:
式中 E凸———外凸翻边的变形程度(%);
R———外凸曲率半径(mm),如图4-42b所示;
b———翻边后竖边的高度(mm),如图4-42b所示。
翻边的极限变形程度与制件材料的塑性、翻边时边缘的表面质量及凹凸形的曲率半径等因素有关。翻边允许的极限变形程度可以由表4-55查得。
表4-55 翻边允许的极限变形程度(%)
2.翻边力的计算
翻边力可以用下式近似计算
式中 F———翻边力(N);
c———系数,可取c=0.5~0.8;
L———翻边部分的曲线长度(mm);
t———材料厚度(mm);
Rm———抗拉强度(MPa)。
4.5.2 翻孔
翻孔是沿制件内孔周围将材料翻成侧立凸缘的冲压工序,又称为内孔翻边。常见的翻孔为圆形翻孔。如图4-43所示,翻孔前毛坯孔径为d0,翻孔变形区是内径为d0、外径为D的环形部分。当凸模下行时,d0不断扩大,并逐渐形成侧边,最后使平面环形变成竖直的侧边。变形区毛坯受切向拉应力σθ和径向拉应力σr的作用,其中切向拉应力σθ是最大主应力,而径向拉应力σr值较小,它是由毛坯与模具摩擦产生的。在整个变形区内,孔的外缘处于切向拉应力状态,且其值最大,该处的应变在变形区内也最大。因此在翻孔过程中,竖立侧边的边缘部分最容易变薄、开裂。
1.翻孔系数
翻孔的变形程度用翻孔系数K来表示:
翻孔系数K越小,翻孔的变形程度越大。翻孔时孔的边缘不破裂所能达到的最小翻孔系数,称为极限翻孔系数。影响翻孔系数的主要因素如下:
1)材料的性能。塑性越好,极限翻孔系数越小。
2)预制孔的加工方法。冲压出的孔没有撕裂面,翻孔时不易出现裂纹,极限翻孔系数较小。冲出的孔有部分撕裂面,翻孔时容易开裂,极限翻孔系数较大。如果冲孔后对材料进行孔的整修,可以减小开裂。此外,还可以将冲孔的方向与翻孔的方向相反,使毛刺位于翻孔内侧,这样也可以减小开裂,降低极限翻孔系数。
图4-43 翻孔时变形区的应力状态
3)如果翻孔前预制孔径d0与材料厚度t的比值d0/t较小,在开裂前材料的绝对伸长可以较大,因此极限翻孔系数可以取较小值。
4)采用球形、抛物面形或锥形凸模翻孔时,孔边圆滑地逐渐胀开,所以极限翻边系数可以较小,而采用平面凸模则容易开裂。
低碳钢的极限翻孔系数见表4-56。翻圆孔时各种材料的翻孔系数见表4-57。
表4-56 低碳钢的极限翻孔系数
表4-57 翻圆孔时各种材料的翻孔系数
2.翻孔尺寸计算
图4-44 平板毛坯翻孔
平板毛坯翻孔的尺寸如图4-44所示。
在平板毛坯上翻孔时,按制件中性层长度不变的原则近似计算。预制孔直径d0由下式计算,即
其中D1=D+2r+t h=H-r-t
翻孔后的高度H由下式计算,即
将式(4-62)代入式(4-64),即可求出最大翻孔高度。当制件要求的高度大于最大翻孔高度时,就难以一次翻孔成形。这时应先进行拉深,在拉深件的底部先加工出预制孔,然后再进行翻孔,如图4-45所示。
3.翻孔力计算
有预制孔的翻孔力由下式计算,即
式中 F———翻孔力(N);
σs———材料屈服强度(MPa);
D———翻孔后中性层直径(mm);
d0———预制孔直径(mm);
t———材料厚度(mm)。
图4-45 拉深后再翻孔
无预制孔的翻孔力要比有预制孔的翻孔力大1.3~1.7倍。
例4-2固定套翻孔件的工艺计算。制件如图4-46所示,材料为08钢,料厚t=1.0mm。
解1)计算预制孔。
图4-46 固定套翻孔件
预制孔直径为32.3mm。
2)计算翻孔系数。
由d0/t=32.3,查表4-56,若采用圆柱形凸模,得低碳钢极限翻孔系数为0.65,小于计算值,所以该制件能一次翻孔成形。
3)计算翻孔力。
查有关手册:
4.翻孔凸模、凹模设计
(1)翻孔时凸模与凹模的间隙 因为翻孔时竖边变薄,所以凸模与凹模的间隙小于厚度,其单边间隙值可按表4-58选取。
表4-58 翻孔凸模与凹模的单边间隙 (单位:mm)
(2)翻孔凸模与凹模 翻孔凸模及凹模设计的好坏直接影响翻孔的质量,翻孔时凸模圆角半径一般较大,甚至做成球形或抛物线形,有利于变形。以下介绍几种常见的翻孔凸模及凹模设计要点。
1)平顶凸模(见图4-47)。平顶凸模常用于大口径且对翻孔质量要求不高的制件,用平顶凸模翻孔时,材料不能平滑变形,因此翻孔系数应取大些。
2)抛物线形凸模(见图4-48)。抛物线的翻孔凸模,工作端有光滑圆弧过渡,翻孔时可将预制孔逐渐地胀开,减轻开裂,比平顶凸模效果好。
3)无预制孔的穿刺翻孔(见图4-49)。无预制孔的穿刺翻孔凸模端部呈锥形,α取60°。凹模孔带台肩,以控制凸缘高度,同时避免直孔引起的边缘不齐。
图4-47 平顶凸模翻孔
图4-48 抛物线形凸模翻孔
图4-49 无预制孔的穿刺翻孔
4)有导正段的凸模(见图4-50)。此凸模前端有导正段,工作时导正段先进入预制孔内,先导正工序件的位置再翻孔。其优点是:工作平稳,翻孔四周边缘均匀对称,翻孔的位置精度较高。
5)带有整形台肩的翻孔凸模(见图4-51)。此凸模后端设计成台肩,其工作过程是:压力机行程降到下极点时,翻孔后靠肩部对制件圆弧部分整形,以此来克服回弹,起到了整形作用。
图4-50 有导正段的凸模翻孔
图4-51 带有整形台肩的翻孔凸模
6)凹模入口圆角设计要点(见图4-52)。凹模入口圆角对翻孔质量的控制至关重要。入口圆角r主要与材料厚度有关:
制件凸缘圆角小于上值时应加整形工序。
图4-52 凹模入口圆角设计要点
5.变薄翻孔
当翻孔制件要求具有较高的竖边高度,而竖边又允许变薄时,可以采用变薄翻孔。这样可以节省材料,提高生产效率。
变薄翻孔要求材料具有良好的塑性,变薄时凸、凹模采用小间隙,材料在凸模与凹模的作用下产生挤压变形,使厚度显著减薄,从而提高了翻孔高度。图4-53所示为变薄翻孔的尺寸变化。
图4-53 变薄翻孔的尺寸变化
变薄翻孔时的变形程度用变薄系数k表示:
式中 t1———变薄翻孔后的竖边厚度(mm);
t———毛坯厚度(mm)。
试验表明:一次变薄翻孔的变薄系数k可达0.4~0.5,甚至更小。
变薄翻孔的预制孔尺寸及变薄后的竖边高度,应按翻孔前后体积不变的原则确定。
变薄翻孔多采用阶梯形凸模成形,如图4-54所示。变薄翻孔力比普通翻孔力大得多,并且与变薄量成正比。翻孔时凸模受到较大的侧压力,可以把凹模压入套圈内。变薄翻孔时,凸模与凹模之间应具有良好的导向,以保证间隙均匀。
图4-54 采用阶梯形凸模的变薄翻孔
变薄翻孔通常用在平板毛坯或半成品的制件上冲制小螺钉孔(一般为M6以下)。在螺孔加工中,为保证使用强度,对于低碳钢或黄铜制件的螺孔深度不小于直径的1/2,而铝件的螺孔深度不小于直径的2/3。为了保证螺孔深度,又不增加制件厚度,生产中常采用变薄翻孔的方法加工小螺孔。常用标准螺纹变薄翻孔数据见表4-59、表4-60。
表4-59 粗牙螺纹翻孔数据 (单位:mm)
(续)
(续)
表4-60 细牙螺纹翻孔数据 (单位:mm)
(续)
(续)
注:表中有关物理量符号见表4-59图。
6.异形孔的翻孔
异形孔由不同半径的凸弧、凹弧和直线组成,各部分的受力状态与变形性质有所不同,直线部分仅发生弯曲变形,凸弧部分为拉深变形,凹弧部分则为翻孔变形。
图4-55所示为异形翻孔件的轮廓,其预制孔可以按几何形状的特点分为三种类型:圆弧a为凸弧,按拉深计算其展开尺寸;圆弧b为凹弧,按翻孔计算其展开尺寸;直线c,按弯曲计算其展开尺寸。
图4-55 异形翻孔件的轮廓
在计算时,可以按上述三种情况分别考虑,将理论计算出来的孔形状再加以适当的修正,使各段平滑连接,即为所求预制孔的形状。
异形翻孔时,曲率半径较小的部位,切向拉应力和切向伸长变形较大;曲率半径较大的部位,切向拉应力和切向伸长变形都较小。因此核算变形程度时,应以曲率半径较小的部分为依据。由于曲率半径较小的部分在变形时受到相邻部分材料的补充,使得切向伸长变形得到一定程度的缓解,因此异形孔的翻孔系数允许小于圆孔的翻孔系数,一般取:
式中 K′———异形孔的翻孔系数;
K———圆孔的翻孔系数。
4.5.3 校平
校平是提高局部或整体平面型零件平直度的冲压工序。在多工位级进模中,校平工序大都在冲裁之后进行。一般来说,对于零件平直度要求较高的冲压件都要经过校平工序。
1.校平工序模具类型
校平工序主要是消除其穹弯造成的不平。对于薄料且表面不允许有压痕的制件,一般用光面校平;对于材料较厚且表面允许有压痕的制件,通常采用齿形校平,如图4-56所示。
图4-56a为细齿校平凸、凹模结构,一般用于材料较厚且表面允许有压痕的制件。齿形在平面上呈正方形或菱形,齿尖磨钝,上、下模的齿尖相互叉开。
图4-56 齿形校平
a)细齿 b)粗齿
图4-56b为粗齿校平凸、凹模结构,一般用于薄料及铝、铜等有色金属,制件不允许有较深的压痕。齿顶有一定的宽度,上、下模的齿尖也是相互叉开的。
2.校平力的计算
校平力可以按下式计算,即
式中 F———校平力(N);
S———制件校平面积(mm2);
q———单位校平力(N/mm2),对于软钢或黄铜,光面凸、凹模校平,q值为50~100N/
mm2,细齿凸、凹模校平,q值为100~200N/mm2,粗齿凸、凹模校平,q值为
200~300N/mm2。
4.5.4 起伏成形
在多工位级进模中,起伏成形是依靠材料的延伸使工序件形成局部凹陷或凸起的冲压工序。起伏成形中材料厚度的改变是非意图性的,即厚度改变是变形过程中自然形成的,而不是设计指定要求的。
起伏成形主要用于压制加强筋、文字图案、凸包等。
1.起伏成形变形限值
起伏成形的变形程度可用伸长率表示,即
式中 ε———伸长率(%);
L1———变形后沿截面的材料长度(mm);
L———变形前材料原有长度(mm)。
一次起伏成形的伸长率ε不能超过材料拉深试验的伸长率A的70%~80%,即
ε<(0.7~0.8)A (4-70)
伸长率从图4-57可以看出。图4-57中曲线1是计算值,曲线2是实际值。在冲压时,因成形区域外围的材料也被拉长,故实际伸长率略低于计算值。
2.压加强筋、压凸包工艺
(1)压加强筋工艺 在平面或曲面压加强筋的形式和尺寸见表4-61;直角形制件压加强筋的形式和尺寸见表4-62。
图4-57 压加强筋时材料的伸长率
(2)压凸包工艺 在多工位级进模中的工序里,压凸包可看成带有很宽凸缘的低浅空心件。由于凸缘很宽,在压凸包成形时,凸缘部分材料不产生明显的塑性流动,主要由凸模下方及附近的材料参与变薄变形形成的。
压凸包时,如果一次成形的伸长率ε超过材料拉深试验的伸长率A的75%,那么应增加一道工序,先压出球形,再成形所需要的凸包尺寸,如图4-58所示。球形的表面积要比凸包的表面积多20%左右,因为在后一道成形工序中有部分材料又重新返回到凸缘处。
表4-61 在平面(曲面)上压加强筋 (单位:mm)
表4-62 在直角形制件上压加强筋 (单位:mm)
如图4-59所示,带孔的凸包在条件允许的情况下,应在成形前冲出一个较小的孔,成形时孔的材料向外流动,有利于变形。
图4-58 两道工序压成的凸包
1—第一道先压出球形 2—第二道压凸包
图4-59 预先冲出小孔的凸包成形方式
常用的压凸包尺寸和间距见表4-63。
表4-63 压凸包的相关尺寸和间距
3.起伏成形的压力计算
1)带料(条料)在1.5mm以下起伏成形(加强筋除外)的近似压力,可按以下经验公式计算,即
式中 F———起伏成形压力(N);
S———起伏成形的面积(mm2);
k———系数(N/mm4),通常对于钢取300~400N/mm4,对于黄铜取200~250N/mm4;
t———带料(条料)厚度(mm)。
2)压加强筋近似压力可按以下公式计算,即
式中 F———压加强筋压力(N);
k———系数,与筋的宽度和深度有关,k一般取0.7~1.0;
L———加强筋周长(mm);
t———带料(条料)厚度(mm);
Rm———材料的抗拉强度(MPa)。
如压筋带整形在多工位级进模上同一工序进行冲压,那么其压力可按式(4-71)计算。