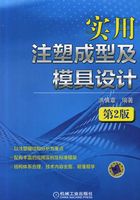
5.4 成型零部件
直接与塑料接触构成塑件形状的零件称为成型零件,其中构成塑件外形的成型零件称为凹模,构成塑件内部形状的成型零件称为凸模(或型芯)。由于凹、凸模件直接与高温、高压的塑料接触,并且脱模时反复与塑件摩擦,因此,要求凹、凸模件具有足够的强度、刚度、硬度、耐磨性、耐腐蚀性,以及足够低的表面粗糙度。
5.4.1 成型零件结构设计
1.凹模结构
(1)整体式凹模 直接在选购的模架板上开挖型腔,如图5-39所示。其优点是加工成本低。但是,通常模架的模板材料为普通的中碳钢,用作凹模,使用寿命短。若选用好材料的模板制作整体凹模,则制造成本高。
通常,对于成型1万次以下塑件的模具或塑件精度要求低、形状简单的模具可采用整体式凹模。
图5-39 整体式凹模
图5-40 整体嵌入式凹模
(2)整体嵌入式凹模 将稍大于塑件外形(大一个足够强度的壁厚)的较好的材料(高碳钢或合金工具钢)制成凹模,再将此凹模嵌入模板中固定,如图5-40a、b、c、d所示。
其优点是“好钢用在了刀刃上”,既保证了凹模使用寿命,又不浪费价格昂贵的材料,并且凹模损坏后,维修、更换方便。
(3)局部镶拼式凹模 对于形状复杂或局部易损坏的凹模,将难以加工或易损坏的部分设计成镶件形式,嵌入型腔主体上,如图5-41a、b、c、d所示。
图5-41 局部镶拼式凹模
(4)四壁拼合式凹模架 对于大型的复杂凹模,可以采用将凹模四壁单独加工后镶入模套中,然后再和底板组合,如图5-42所示。
(5)螺纹型环 螺纹型环是用来成型塑件外螺纹的一类活动镶件,成型后随塑件一起脱模,在模外卸下。图5-43a所示为整体式螺纹型环,配合长度5~8mm,为了便于安装,其余部分制成3°~5°斜度,下端加工出四侧平面,便于用工具将其从塑件上拧下来。图5-43b为对开组合式型环,用于成型精度不高的粗牙螺纹。对开两半之间用销子定位,上部制出撬口,便于成型后在模外用工具将两对开块分开。
图5-42 四壁拼合式凹模
图5-43 螺纹型环
综上所述,凹模结构用的最多的是整体嵌入式和局部镶拼式。
2.凸模结构
整体式凸模浪费材料且切削加工量大,在当今的模具结构中几乎没有这种结构。凸模结构主要是整体嵌入式凸模和镶拼组合式凸模,如图5-44a、b、c、d和图5-45a、b、c所示。
图5-44 型芯的结构形式
图5-45 镶拼式组合型芯
3.小型芯
细小的凸模通常称为型芯,用于塑件孔或凹槽的成型。各种孔的成型方法如图5-46、图5-47、图5-48所示。
图5-46 小型芯组合
图5-47 中心距相近时多型小孔
图5-48 小型芯的固定方法
图5-49 活动型芯的安装形式
4.活动型芯
有时为了使模具简单,将螺纹型芯或安放螺纹型环嵌件用的型芯做成活动的镶件。这种形式的型芯成型前在模具中常以H8/f8配合活动放置,成型后随塑件一起在模外取出,如图5-49所示。
5.4.2 成型零件工作尺寸的计算
成型零件的工作尺寸是指凹模和凸模直接构成塑件的尺寸。凹、凸模工作尺寸的精度直接影响塑件的精度。
1.影响工作尺寸的因素
(1)塑件收缩率的影响 由于塑料热胀冷缩的原因,成型冷却后的塑件尺寸小于模具型腔的尺寸。表5-6列出了部分热塑性塑料的标准成型收缩率。
表5-6 部分热塑性塑料的标准成型收缩率
(2)凹、凸模工作尺寸的制造公差 它直接影响塑件的尺寸公差。通常凹、凸模的制造公差取塑件公差的1/3~1/6,表面粗糙度取Ra值为0.8~0.4μm。
(3)凹、凸模使用过程中的磨损量及其他因素的影响 生产过程中的磨损以及修复会使得凸模尺寸变小,凹模的尺寸变大。
因此,成型大型塑件时,收缩率对塑件的尺寸影响较大;而成型小型塑件时,制造公差与磨损量对塑件的尺寸影响较大。常用塑件的收缩率通常在百分之几到千分之几之间。
2.凹、凸模的工作尺寸计算
通常,凹、凸模的工作尺寸根据塑料的收缩率,凹、凸模零件的制造公差和磨损量三个因素确定。
(1)凹模的工作尺寸 凹模是成型塑件外形的模具零件,其工作尺寸属包容尺寸,在使用过程中凹模的磨损会使包容尺寸逐渐增大。因此,为了使得模具的磨损留有修模的余地,以及装配的需要,在设计模具时,包容尺寸尽量取下限尺寸,尺寸公差取上偏差。具体计算公式如下:
凹模的径向尺寸计算公式为
L=[L塑(1+k)-(3/4)Δ]+δ0 (5-2)
式中 L塑——塑件外形公称尺寸;
k——塑料的平均收缩率;
Δ——塑件的尺寸公差;
δ——模具制造公差,取塑件相应尺寸公差的1/3~1/6。
凹模的深度尺寸计算公式为
H=[H塑(1+k)-(2/3)Δ]+δ0 (5-3)
式中 H塑——塑件高度方向的公称尺寸。
(2)凸模的工作尺寸 凸模是成型塑件外形的,其工作尺寸属被包容尺寸,在使用过程中凸模的磨损会使被包容尺寸逐渐减小。因此,为了使得模具的磨损留有修模的余地,以及装配的需要,在设计模具时,被包容尺寸尽量取上限尺寸,尺寸公差取下偏差。具体计算公式如下:
凸模的径向尺寸计算公式为
l=[l塑(1+k)+(3/4)Δ]-0δ (5-4)
式中 l塑——塑件内形径向公称尺寸。
凸模的高度尺寸计算公式为h=[h塑(1+k)+(2/3)Δ]-0δ (5-5)
式中 h塑——塑件深度方向的公称尺寸。
(3)模具中的位置尺寸(如孔的中心距尺寸)计算公式为
=C塑(1+k)±δ/2 (5-6)
式中 C塑——塑件位置尺寸。
(4)计算实例 如图5-50所示塑件结构尺寸及相应的模具型腔结构,塑件材料为聚丙烯,计算收缩率为1%~3%,求凹、凸模构成型腔的尺寸。
图5-50 塑件及相应的凹、凸模
解:塑料的平均收缩率为2%。
①凹模有关尺寸的计算:
径向尺寸
L=[L塑(1+k)-(3/4)Δ]+δ0=[110×(1+0.02)-(3/4)×0.8)]00.8×1/6=111.6+0.130
深度尺寸
H=[H塑(1+k)-(2/3)Δ]+δ0=[30×(1+0.02)-(2/3)×0.3)]00.3×1/6=30.4+0.050
②凸模有关尺寸的计算:
径向尺寸
l=[l塑(1+k)+(3/4)Δ]-δ0=[80×(1+0.02)+(3/4)×0.6]0-0.6×1/6=82.05-0.10
高度尺寸
h=[h塑(1+k)+(2/3)Δ]-δ0=[15×(1+0.02)+(2/3)×0.2)]0-0.2×1/5=15.43-0.040
型芯直径d=[d塑(1+K)+(3/4)Δ]-δ0=[8×(1+0.02)+(3/4)×0.1]0-0.1×1/5=8.24-0.020
③模具型芯位置尺寸计算:
C=C塑(1+k)±δ/2=30×(1+0.02)±(0.3×1/6)/2=30.6±0.025
3.螺纹型环和螺纹型芯的尺寸计算
(1)螺纹型环的尺寸计算
D中=[D塑中(1+k)-Δ]+δ0(5-7)
D大=[D塑大(1+k)-Δ]+δ0(5-8)
D小=[D塑小(1+k)-Δ]+δ0 (5-9)
式中 D中——螺纹型环的中径尺寸;
D大——螺纹型环的大径尺寸;
D小——螺纹型环的小径尺寸;
D塑中——塑件外螺纹的中径公称尺寸;
D塑大——塑件外螺纹的大径公称尺寸;
D塑小——塑件外螺纹的小径公称尺寸;
Δ——塑件外螺纹的中径公差;
δ——螺纹型环的制造公差值,对于中径,δ=Δ/5,对于大径和小径,δ=Δ/4。
(2)螺纹型芯的尺寸计算
d中=[d塑中(1+k)-Δ]-δ0 (5-10)
d大=[d塑大(1+k)-Δ]-δ0 (5-11)
d小=[d塑小(1+k)-Δ]-δ0 (5-12)
式中 d中——螺纹型芯的中径尺寸;
d大——螺纹型芯的大径尺寸;
d小——螺纹型芯的小径尺寸;
d塑中——塑件内螺纹的中径公称尺寸;
d塑大——塑件内螺纹的大径公称尺寸;
d塑小——塑件内螺纹的小径公称尺寸;
Δ——塑件内螺纹的中径公差;
δ——螺纹型芯的制造公差值,对于中径,δ=Δ/5,对于大径和小径,δ=Δ/4。
(3)螺距工作尺寸计算
P=P塑(1+k)±δ/2 (5-13)
式中 P塑——塑料螺纹制件螺距的公称尺寸;
δ——螺距的制造公差值,见表5-7;
P——螺纹型环或螺纹型芯的螺距尺寸。
一般情况下,当螺纹牙数少于7~8牙时,可不进行螺距工作尺寸计算,而是靠螺纹的旋合间隙补偿。
表5-7 螺纹型芯或型环螺距的制造公差 (单位:mm)
5.4.3 型腔侧壁及底板厚度的计算
在注塑成型过程中,型腔承受塑料熔体的高压作用。因此,凹模与凹、凸模的底板必须具有足够的强度和刚度。如果凹模和底板的厚度过小,则强度、刚度会不足。强度不足会导致型腔产生塑性变形,甚至破裂;刚度不足将产生过大的弹性变形,并产生溢料间隙。表5-8列出了常用塑料的刚度条件[δ]值的允许范围。
表5-8 常用塑料[δ]值允许范围
模具型腔受力状况如图5-51所示。
图5-51 各种形式模具型腔受力分析
1.型腔侧壁的厚度计算
对型腔厚度分别作强度和刚度计算,图5-51a结构的强度、刚度为最差,取计算所得数值大者作为厚度设计依据,则这个厚度值也能够满足后两种情况。
若型腔为圆形,则刚度计算公式为
强度计算公式为
式中 S——型腔侧壁厚度(mm);
r——型腔半径(mm);
[σ]——模具材料的许用应力(MPa);
p——型腔所受压力(MPa);
E——模具材料的弹性模量(MPa),碳钢为2.1×105MPa;
[δ]——刚度条件,即允许变形量(mm),由表5-8选取;
μ——模具材料的泊松比,碳钢为0.25。
若型腔为矩形(见图5-51b),则刚度计算公式为
强度计算公式为
a)零件
式中 S——矩形型腔长边侧壁厚度(mm);
p——型腔所受压力(MPa);
L——型腔长边长度(mm);
a——型腔侧壁受压高度(mm);
a′——型腔侧壁全高度(mm);
[δ]——允许变形量(mm),由表5-8查得;
E——模具材料的弹性模量(MPa);
[σ]——模具材料的许用应力(MPa)。
2.型腔底板厚度计算
通常凹、凸模下面有一底板能起到支承作用,在动模一侧的底板因其下面顶出机构的空间,故此底板应具有足够的强度与刚度,其厚度可根据下列公式计算。
若型腔为圆形(见图5-51a),则刚度计算公式为
强度计算公式为
若型腔为矩形(见图5-51b),则刚度计算公式为
强度计算公式为
若型腔压力通过型芯或型腔镶块传递到支承板上,如图5-52所示。
图5-52 支承板受力情况
在利用以上公式时将型腔压力换算成支承板上的压力p1,即p1=(A/A1)p (5-22)
式中 p——型腔压力(MPa);
p1——支承板承受压力(MPa);
A——型芯或镶块受压面积(mm2);
A1——型芯或镶块底面面积(mm2)。
由于注塑成型受温度、压力、塑料特性及塑件形状复杂程度等因素的影响,所以以上计算并不能完全真实地反映结果。通常模具设计中,型腔壁厚及支承板厚度不通过计算确定,而是凭经验确定的。表5-9、表5-10列举了一些经验数据供设计时参考。
表5-9 型腔侧壁厚度S的经验数据
注:型腔为整体式,L>100mm时,表中值需乘以0.85~0.9。
表5-10 支承板厚度h的经验数据 (单位:mm)
注:当压力p<29MPa,L≥1.5b时,取表中数值乘以1.25~1.35;当29MPa≤p<49MPa,L≥1.5b时,取表中数值乘以1.5~1.6。