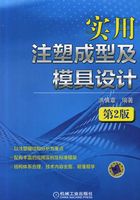
5.9 温度调节系统
5.9.1 简介
在注塑成型过程中,模具的温度直接影响到塑件成型的质量和生产效率。由于各种塑料的性能和成型工艺要求不同,模具的温度要求也不同。一般注射到模具内的塑料温度为200℃左右,而塑件固化后从模具型腔中取出时其温度在60℃以下,温度降低是由于模具通入冷却水,将热量带走了。普通的模具通入常温的水进行冷却,通过调节水的流量就可以调节模具的温度。这种冷却方法一般用于流动性好的低熔点塑料的成型。为了缩短成型周期,还可以把常温的水降低温度后再通入模内。因为成型周期主要取决于冷却时间,用低温水冷却模具,可以提高成型效率。不过需要注意的是,用低温水冷却,大气中的水分可能在型腔表面凝聚,会影响制件质量。
流动性差的塑料如聚碳酸酯、聚苯醚、聚甲醛等,要求模具温度高。若模具温度过低则会影响塑料的流动,增大流动剪切力,使塑件内应力较大,甚至还会出现冷流痕、银丝、注不满等缺陷。尤其是当冷模刚刚开始注射时,这种情况更为明显。因此,对于高熔点、流动性差的塑料,流动距离长(相对壁厚而言)的制件,为了防止填充不足,有时也在水管中通入温水或把模具加热。但模具温度也不能过高,否则要求冷却时间延长,且制件脱模后易发生变形。总之,要做到优质、高效率生产,模具必须能够进行温度调节,应根据需要进行设计。
1.模具温度与塑料成型温度的关系
注入模具的热塑性熔融塑料,必须在模具内冷却固化才能成为制件,所以模具温度必须低于注入型腔的熔融塑料温度。为了提高成型效率,一般通过缩短冷却时间来缩短成型周期。虽然模具温度越低,冷却时间就越短,但是这种规则不能适用于所有的塑料。因塑料自身的性质及制件要求的性能各不相同,要求的模具温度也各不相同。必须根据不同的要求,选择适当的温度。与各种塑料相适应的模具温度见表5-13。
表5-13 各种塑料的成型温度与模具温度 (单位:℃)
2.温度调节对塑件质量的影响
质量优良的塑料制件应满足以下六个方面的要求,即收缩率小、变形小、尺寸稳定、冲击强度高、耐应力开裂性好和表面光洁。模温对以上各点的影响分述如下:
采用较低的模温可以减小塑料制件的成型收缩率。
模温均匀、冷却时间短、注射速度快可以减小塑件的变形。其中均匀一致的模温尤为重要,但是由于塑料制件形状复杂、壁厚不一致、充模顺序先后不同,常出现冷却不均匀的情况。为了改善这一状况,可将冷却水先通入模温最高的地方,甚至在冷得快的地方通温水,慢的地方通冷水,使得模温均匀,塑件各部位能同时凝固。这不仅提高了制件质量,也缩短了成型周期。但由于模具结构复杂,要完全达到理想的调温往往是困难的。
对于结晶型塑料,为了使塑件尺寸稳定应该提高模温,使结晶在模具内尽可能地达到平衡。否则,塑件在存放和使用过程中,由于后结晶会造成尺寸和力学性能的变化(特别是玻璃化温度低于室温的聚烯烃类塑件),但模温过高对制件性能也会产生不好的影响。
结晶型塑料的结晶度还影响塑件在溶剂中的耐应力开裂能力,结晶度越高该能力越低,故降低模温是有利的。但是对于聚碳酸酯一类的高黏度非结晶型塑料,耐应力开裂能力和塑件的内应力关系很大,故提高充模速度、减少补料时间及采用高模温是有利的。
实验表明高密度聚乙烯冲击强度受充模速度影响很大,特别在浇口的附近,高速注射的制件较低速注射的制件在浇口附近冲击强度高1/4,但模温影响较小,以采用较低的模温(45~54℃)为宜。
对塑件表面粗糙度影响最大的除型腔表面加工质量外就是模具温度,提高模温能大大改善塑件表面状态。
上述六点要求有互相矛盾的地方,在选用时应根据使用情况侧重于满足塑件的主要要求。
3.对温度调节系统的要求
前面已经介绍了温度调节系统的重要性,因此,希望设计温度调节系统时,能满足下面要求:
1)根据塑料的品种,确定温度调节系统是采用加热方式还是冷却方式。
2)希望模温均一,塑件各部同时冷却,以提高生产率和提高塑件质量。
3)采用低的模温,快速、大流量通水冷却一般效果比较好。
4)温度调节系统要尽量做到结构简单、加工容易、成本低廉。
5.9.2 模具冷却系统的设计
1.冷却时间的计算
塑件在模具内的冷却时间,通常是指塑料熔体从充满型腔时起到可以开模取出塑件时为止这一段时间。可以开模取出塑件的时间,常以塑件已充分固化,且具有一定的强度和刚度为准。具体有三种标准及计算公式。
1)塑件最厚部位断面中心层温度达到热变形温度以下时,所需冷却时间的简化计算公式为
式中 t1——塑件所需冷却时间(s);
δ——塑件壁厚(mm);
k——塑件的热扩散率(m2/s);
Tm——塑料熔体温度(℃);
Tω——模具温度(℃);
Ts——塑料的热变形温度(℃)。
2)塑件截面内平均温度达到规定的脱模温度时,所需冷却时间的简化计算公式为
式中 t2——塑件所需冷却时间(s);——塑件脱模时截面内平均温度(℃)。
3)结晶性塑料制件的最大壁厚中心层达到凝固点时,所需冷却时间的经验公式如下:
①聚乙烯(PE)
棒类
板类
以上两式的适用范围:Tm=193.3~248.9℃,Tω=4.4~79.4℃。
②聚丙烯(PP)
棒类
板类
以上两式的适用范围:Tm=232.2~282.2℃,Tω=4.4~79.4℃。
③聚甲醛(POM)
棒类
板类
以上两式的适用范围:Tm>;190℃,Tω<125℃。
式中 t3——塑件所需冷却时间(s);
Tm——棒类或板类塑件的初始成型温度(℃);
Tω——模具温度(℃);
R——棒类塑件的半径(mm);
δ——板类塑件的厚度(mm)。
2.热交换系统
注塑成型过程中,模具的温度对塑料熔体的充模流动、固化定型、生产率、制件的形状和尺寸精度、机械强度、应力开裂和表面质量等均有影响。为了保证制件质量和较高的生产率,模具温度必须适当、稳定、均匀。
塑料模是塑料模塑成型必不可少的工艺装备,同时又是一个热交换器。输入热量的方式是加热装置的加热和塑料熔体带进的热量;输出热量的方式是自然散热和向外热传导,其中95%的热量是靠传热介质(冷却水)带走。在模塑过程中,要保持模具温度的稳定,就应保持输入热与输出热平衡。为此,必须设置模具的热交换系统,对模具进行加热和冷却,以控制模具温度。
(1)确定加热与冷却的原则 注塑模的热交换系统必须具有冷却或加热的功能,必要时还二者兼有。通常所采用的冷却或加热介质有水、热油和蒸汽,也可采用电加热方式。水又分为常温水、温水和冷水三种。常温水是指不经加热或冷却处理的自然水流;温水是指经过一定程度加热的水流;冷水则是指经冷却处理后的水流。
究竟在何种情况下需要对模具进行冷却或加热,与不同特性的塑料品种、制件结构形状、尺寸大小、生产率及成型工艺对模具温度的要求有关。确定冷却或加热的原则如下所述:
1)对于黏度低、流动性好的塑料(如聚乙烯、聚丙烯、聚苯乙烯和聚酰胺等),因为成型工艺要求的模具温度不太高,通常可用常温水对模具进行冷却,并通过调节水的流量大小控制模具温度。若要提高这类塑料制件的生产率,缩短制件在模内的冷却时间及成型周期,可采用冷水控制模温。
2)对于黏度高、流动性差的塑料(如聚碳酸酯、硬聚氯乙烯、聚苯醚、聚砜和氟塑料等),为了改善充模性能,成型工艺常要求模具具有较高的温度,需要对模具采取加热措施。
3)对于低黏流温度或低熔点塑料,一般需要采用常温水或冷水对模具进行冷却。但是,如果需要改善充模流动性,或是为了解决某些成型质量方面的问题,也可采取加热措施。
4)对于高黏流温度或高熔点塑料,可用温水控制模温。其目的是使温水对塑料制件产生冷却作用,并比常温水和冷水更有利于促使模温分布趋于均匀化。
5)对于热固性塑料,模温要求在150~220℃,必须对模具采取加热措施。
6)由于制件几何形状的影响,制件在模具内各处的温度不一定相等,常会因温度分布不均导致成型质量差。为此,可对模具采用局部加热或局部冷却的方法,以改善制件温度的分布情况。
7)对于流程长、壁厚又较大的制件,或者是黏流温度或熔点虽然低,但成型面积很大的制件,为保证塑料熔体在充模过程中不因温度下降而难以流动,也可对模具采取适当的加热措施。
8)对于工作温度高于室温的大型模具,可在模内设置加热装置,以保证在生产之前预热模具。
9)为了实现准确地控制模温,可在模具中同时设置加热器和冷却器。
10)对于小型薄壁制件,且成型工艺要求模温不太高时,可不设置冷却装置。
11)结构简单,加工容易,成本低廉。
(2)冷却系统 对于小型注塑模,塑料熔体传给模具的热量可以依靠自然对流和辐射的方式散发,但在更多的情况下,熔体传给模具的绝大多数热量只能依靠冷却水对流传导扩散出去。因此,需在模具中合理地设计冷却水的通道截面尺寸及长度,以便准确地计算控制模温所需的热传导面积。
1)冷却水孔数量尽量多,尺寸尽量大。型腔表壁的温度与冷却水道的数量、截面尺寸以及冷却水的温度有关。图5-195所示是在冷却水道数量和截面尺寸不同的条件下,向模具内通入不同温度(45℃和59.83℃)的冷却水后,模具内同一截面上的等温曲线分布情况。采用5个直径较大的水道时,型腔表壁的温度分布比较均匀,温差只有0.05℃左右(分型面附近的温度约60.05℃,型腔表壁温度约60℃),见图5-195a;而采用两个直径较小的水道时,型腔表壁温度分布的均匀性变差,温差达6.67℃左右(分型面附近的温度约60℃,型腔表壁的温度约53.33℃),见图5-195b。据此可知,为了使型腔表壁的温度分布趋于均匀,防止制件出现温度不均以及由此而产生的不均匀性收缩和制件残余应力,在模具结构和尺寸允许的情况下,应尽量多设冷却水道,并使用较大的截面尺寸。
图5-195 热传导与温度梯度
2)冷却水孔至型腔表面距离相等。当塑件壁厚均匀时,冷却水孔与型腔表面各处最好有相同的距离,如图5-196a所示。当壁件壁厚不均匀时,如图5-196b所示,厚壁处冷却水通道要靠近型腔,间距要小。一般水孔边离型腔的距离大于10mm,常用12~15mm。
3)浇口处加强冷却。普通熔融的塑料充填型腔的时候,浇口附近温度最高,距浇口越远温度越低。因此,浇口附近要加强冷却,通入冷水,而在温度低的外侧使经过热交换了的温水通过即可。图5-197所示为侧浇口,图5-198所示为薄膜浇口,图5-199所示为多点浇口的冷却水管分布。
图5-196 冷却水孔的位置
图5-197 两个型腔侧浇口的循环冷却水路
图5-198 薄膜浇口的循环冷却水路
4)降低入水与出水的温度差。如果入水温度和出水温度差别太大时,使模具的温度分布不均,特别是对流动距离很长的大型制件,料温越流越低。为取得整个制件大致相同的冷却速度,可以改变冷却水通道排列的形式,如图5-200所示。对于大型塑件,型腔比较长时,图5-200a所示的形式会使入水与出水的温差大,塑件冷却不均匀;图5-200b所示的形式可使入水与出水温差小,冷却效果好。
图5-199 多点浇口的循环冷却水路
图5-200 冷却水道排列形式
5)冷却水孔的排列形式。对于收缩大的塑料(如聚乙烯)应沿其收缩方向设冷却水通道。图5-201所示是四方形塑件中心浇口的情况,收缩沿放射线上和同放射线垂直的方向进行,所以应把水从中心通入,向外侧螺旋式进行热交换,最后流出模外。
图5-201 中心直浇口动模冷却水槽图
冷却水通道的开设应该尽可能按照型腔的形状,对于不同形状的塑件,冷却水道位置也不同。
①薄壁、扁平塑件:侧面浇口的情况如图5-202所示,动模和定模都是距型腔等距离钻孔。
②中等深度壳形塑件:图5-203所示为侧浇口的塑件,定模距型腔等距离钻孔,动模开设冷却水槽。
图5-202 薄壁、浅的塑件的冷却水槽
图5-203 中等深度制件的冷却水槽
图5-204 深腔冷却水槽
③深型腔塑件:深的塑件最困难的是型芯的冷却。对于深度浅的情况钻通孔并堵塞得到和塑件形状类似的回路,如图5-204所示。对于深腔的大型制件不能那样简单,应如图5-205所示,定模采取自浇口附近入水,在周围回转由外侧的钻孔把水导出的方式。型芯的底部如A—A断面所示加工出螺旋状的槽,在型芯中打出的不通孔中放入图中所示的隔板,沿着型芯的形状开设冷却水道。
图5-205 深腔大型制件的冷却水槽
图5-206所示是为了较好地对型芯进行冷却,而从型芯中心进入水,在端面(浇口处)冷却后沿型芯顺序流出模具,定模也是这样冷却。此法用于非常深的塑件冷却。
④狭窄的、薄的、小型的制件:因为型芯细,在型芯中心开不通孔,放进管子,由管中进入的水喷射到浇口附近,进行冷却,管的外侧和孔壁间的水通向出水口。图5-207所示是典型的例子。
当型芯非常细,不能开孔时,可以选用导热性好的铍铜合金作为型芯的材料,如图5-208所示。
图5-206 非常深的塑件冷却水槽
图5-207 狭窄型芯的冷却水道
图5-208 铍铜型芯
1—铍铜型芯 2—导管
对于壁较厚的小制件,可将铍铜芯棒一端加工成翅片状以扩大散热面积,如图5-209所示。
图5-209 扩大散热面积结构
1—型芯铍铜 2—镶件铍铜 3—水管
此外,冷却水通道要尽量避开塑件的熔接痕部位,以免影响塑件的强度。
6)便于加工和清理。冷却水通道要易于机械加工,便于清理,一般孔径设计为8~12mm。
3.冷却参数的计算
(1)传热面积计算 如果忽略模具因空气对流、热辐射与注射机接触所散失的热量,假设塑料熔体在模内释放的热量,全部由冷却水带走,侧模具冷却时所需冷却水的体积流量可按下式计算:
式中 V——冷却水的体积流量(m3/min);
G——单位时间内注入模具内的塑料熔体的质量(kg/h);
h——塑料成型时在模具内释放的比焓(J/kg);
c——冷却水的比热熔[J/(kg·K)];
ρ——冷却水的密度(kg/m3);
t1——冷却水的出口温度(℃);
t2——冷却水的进口温度(℃)。
求出冷却水的体积流量V后,可以根据冷却水处于湍流状态下的流速v与通道直径d的关系(见表5-14),确定模具冷却水孔的直径d。
表5-14 冷却水流速与水孔直径的关系
冷却水孔总传热面积A由下式计算:
式中 A——冷却水孔总传热面积(m2);
G——单位时间内注入模具中的塑料质量(kg/h);
h——塑料成型时在模内释放的比焓(J/kg);
Tω——模具温度(℃);
Tθ——冷却水的平衡温度(℃);
K——冷却介质在圆管内呈湍流状态时,冷却管道冷却孔壁与冷却介质间
的传热系数(J/m2·h·℃),数值由下式确定:
式中 f——与冷却介质温度有关的物理系数,数值由表5-15确定;
ρ——冷却介质的密度(kg/m3);
v——冷却介质的流速(m/s);
d——冷却管道的直径(m)。
表5-15 水温与f的关系
(2)冷却水孔总长度计算 由于传热面积A=πdL,代入式(5-36),且K用式(5-37)表示,可得
式中 L——冷却水孔总长度(m)。
(3)冷却水孔数目的计算 设因模具尺寸之限制,每一根水孔的长度为l,则模具内应开设水孔数由下式计算:
图5-210 水的运动黏度与温度关系
(4)冷却水流动状态的校验 冷却水介质处于层流还是湍流,其冷却效果相差10~20倍。因此,在模具冷却系统设计完成后,尚须对冷却介质的流动状态进行校核。规定实用的雷诺数为
式中 v——冷却水的流速(m/s);
d——冷却水孔直径(m);
η——冷却水的运动黏度(m2/s),可按图5-210选取。
(5)冷却水入口与出口处温差校核 冷却水的进出口温差由下式校验
5.9.3 常见的各种冷却系统结构
由于塑件的形状是各种各样的,必须根据型腔内的温度分布、浇口位置等设计不同的冷却系统。下面介绍型腔、型芯的冷却结构以及局部冷却和加热装置。
1.型腔冷却系统结构
最常见的型腔冷却结构如图5-211所示,采用钻孔的方法比较容易加工,用堵头使冷却水沿指定方向流动。图5-212所示为型腔开设环形冷却水槽的形式,这种结构一定要很好地密封。图5-213所示是比较深的圆形制件型腔冷却的形式。
图5-211 冷却水槽结构
图5-212 型腔冷却
1—型腔 2、4—密封圈 3—固定板
图5-213 深腔冷却
图5-214 喷射式冷却
2.型芯冷却系统结构
型芯的冷却结构根据塑件的深度、宽度等大小不同而异。除图5-204~图5-209所示结构外,还使用喷射式循环水路或冷却水与压缩空气并用的情况。图5-214所示为主要冷却回路在定模型腔,沿浇口附近成环状回路,型芯为喷射式冷却。图5-215所示为冷却水与压缩空气并用的例子,在推出杆内设有喷射的冷却水路,压缩空气起冷却及进气作用。图5-216所示是为了扩大冷却型芯的上面,使用了没有冷却水通孔的特殊隔板,提高了冷却效果。
图5-215 冷却水与压缩空气并用的结构
图5-216 特殊隔板冷却型芯结构
5.9.4 加热装置的设计
当注塑成型工艺要求模具在80℃以上工作时,模具中必须设置具有加热功能的温度调节系统,换句话说,就是模具中必须带有加热装置。根据热源不同,模具加热装置的种类很多,如采用各种热水、热油和蒸汽的加热装置以及各种电加热装置等。除了电加热之外,对于各种加热介质,均需要在模内开设相应的循环回路,其设计方法可以类比冷却水路。电加热装置是当前应用比较普遍的温度调节系统,它具有结构简单、温度调节范围较大和加热清洁、没有污染等优点。
1.电加热的方式
模具中可以使用的电加热装置有两大类型,一种是电阻加热,另一种是感应加热。由于感应加热装置结构复杂,体积又大,通常很少采用。下面是三种常用的电阻加热方式:
(1)电阻丝直接加热 这种方式将事先绕制好的螺旋弹簧状电阻丝作为加热元件,外部穿套特制的绝缘瓷管后,装入模具中的加热孔道,一旦通电,便可对模具直接加热。这种方式的特点是加热结构简单、价格低廉;但电阻丝与空气接触后容易氧化损耗、使用寿命不长、耗电量也比较大,并且也不够安全,必须注意模具加热部分与其他部分的绝缘问题。
图5-217 电热环形式
a)方形 b)圆形c)瓷块组合式
(2)电热环加热 电热环也称为筒式加热元件,它是将电阻丝绕制在云母片上之后,再装夹进一个特制框套内而制成的。如果框套为金属材料,则框套与电阻丝之间须用云母片绝缘。图5-217所示是三种电热环的形状示例,使用时可以根据模具加热部位的形状进行选用。如果模具中不便使用电热环,也可以采用平板框套构成的电热板。
电热环式加热的特点是框架结构简单,制造容易,使用和更换也比较方便,必要时也可按照模具加热部分的形状进行制造;它的缺点是耗电量较大。
(3)电热棒加热 如图5-218所示,电热棒是一种标准加热元件,它由具有一定功率的电阻丝和带有耐热绝缘材料的金属密封管构成(见图5-218a)。使用时,只要将其插入模具或加热板中的加热孔内进行通电即可。电热棒式加热的特点是使用和安装方便;但是开设加热孔时,受型芯、成型镶块和推出脱模零件安装位置限制。
图5-218 电热棒及其安装
a)电热棒 b)电热棒的安装
1—电阻丝 2—耐热填料(硅砂或氧化镁) 3—金属密封管 4—耐热绝缘垫片(云母或石棉) 5—加热板
2.电加热装置的功率计算
(1)计算法 电加热装置加热模具需用的总功率可用下式计算:
式中 P——加热模具需用的电功率(kW);
m——模具的质量(kg);
cp——模具材料的比热容[kJ/(kg·K)];
θ1——模具的初始温度(℃);
θ2——模具要求的加热温度(℃);
η——加热元件的效率,约为0.3~0.5;
t——加热时间(h)。
(2)经验法 计算模具电加热装置所需的总功率是一项很复杂的工作,事先必须对模具进行准确的热分析和热计算。因此,式(5-42)实质上也是一种比较粗略的概算方法。生产中为了方便起见,也可以根据加热方式和模具的大小,采用下面经验数据计算单位质量模具的电加热功率Pu:
1)电热环加热。小型模具:Pu=40W/kg;大型模具Pu=60W/kg。
2)电热棒加热。小型模具(40kg以下):Pu=35W/kg;中型模具(40~100kg);Pu=30W/kg;大型模具(100kg以上):Pu=20~20W/kg。
3.电加热装置的设计要求
设计电阻式电加热装置时,除了设计加热元件之外,模具中加热孔道的布排、电热环的安装部位和电气控制系统也非常重要。通常均要求能在模具中合理地开设加热孔道、合理地选择电热环的安装部位及其形状,以便能使模具温度保持均匀一致。对于电气控制系统,均要求系统能够准确地控制和调节加热功率及加热温度,防止因功率不够达不到模温要求,或因功率过大超过模温要求。