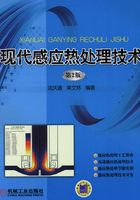
3.2 加热功率的选择
1.加热功率密度选择
电源装置的功率取决于工件表面以kW/cm2为单位计算的功率密度值(P0)和以cm2计的一次加热面积A。选择功率密度要根据加热表面积及其淬火技术条件而定。电流频率越低,工件直径越小及所要求的硬化层深度越浅,则所需功率密度应越大。碳钢在不同频率及功率密度下得到的硬化层深度见表3-6。当使用高频及超音频电源时,P0常用0.6~2.0kW/cm2。当使用中频电源时,P0常用0.8~2.5kW/cm2。
表3-6 碳钢在不同频率及功率密度下得到的硬化层深度
① 齿轮沿齿廓淬火,在3~10kHz电流频率下建议用低功率密度
相同硬化层深度值可以用不同的功率密度与不同加热时间来达到。较高功率密度与较短加热时间适合于较低电流频率,较低功率密度与较长加热时间适合于较高电流频率。前者加热工件表面向心部传导热能少,热效率较高;而后者热传导作用增强,热效率较低。从节能角度与工件硬化层过渡区不要太长两个观点出发,表面淬火工件的加热时间最好不超过10s,略长一点也不要超过15s,特殊要求例外。
现代化的感应淬火机床,相当部分已配有能量监控仪,以单位为kW·s的电能来控制淬火工件的加热温度与硬化层深度。根据所需电能xkW·s,先设定加热时间ys,再以xkW·s/ys求出所需功率zkW(能量监控器上一般指振荡功率)。
表3-7是不同电流频率时,硬化层深度与所耗电能的关系。根据此表,可根据不同频率时,各种硬化深度所需的能耗密度值计算出一定加热面积所耗电能(kW·s)。
表3-7 硬化深度与所耗电能的关系
2.经验法选取功率密度与加热时间
生产实践中,常常根据已有生产实践数据,考虑工件所需电流频率与所需设备功率。
表3-8是拖拉机磨损零件感应淬火所需电源。
表3-8 拖拉机磨损零件感应淬火所需电源
(续)
采用10kHz频率取代2.5kHz频率,是由于频率越高,所需配的电容器等电器装置尺寸越小,因此,曲轴颈淬火加热,从早期应用2.5kHz逐步改为8~10kHz。
3.计算机模拟选取P和f
由于计算机模拟技术的发展,现在已有计算机模拟软件,供用户通过计算机模拟进行模拟工艺试验,求出最佳的设备频率与所需功率。例如用ELTA计算机软件研究一个Φ40mm的轴,硬化层深度为5mm,推荐频率范围为1.2~10kHz,最佳频率大致在2.5kHz。设钢的奥氏体化的最低温度为800℃,最高加热温度为1000℃(45钢),采用一个不变的感应器进行模拟试验。计算机模拟感应淬火结果见表3-9。
表3-9 Φ40mm轴计算机模拟感应淬火结果
注:1.效率、感应器电压、功率因数均为加热周期中的平均值。2.感应淬火工艺上能耗习惯单位用kW·s,现国外生产的能量监控仪仍用kW·s作单位,1kW·s=1000J。
1)从3.1节可知,Ds/d=0.5时,能提供最快、最高效的加热(f=2.5~3.0kHz)。从表3-9中也可看出,当f=2500Hz和3000Hz时,功率因数在此时也高,其意义是电容量减少而变压器效率高。
2)用比最佳频率为高的频率,得到较高的电效率,但加热时间大大增加(在30kHz时,增长达4倍),总能耗也增加了,但不超过10%。
3)用比最佳频率低的频率时,能得到较快的加热,但电效率及功率因数下降,感应器所需功率大大增加,而感应器损耗可达到一个不能接受的数值。
4)当频率大大低于最佳频率时(如为1000Hz),加热过程变为较低效率而操作条件对参数的变化显得特别敏感。
5)感应器端电压在上述最佳频率左右很大范围内基本上是相同的,说明在改变频率时,电压比基本上可以不变。
4.同一感应器在不同频率与功率密度下的淬火结果
图3-5所示为履带拖拉机支重轮在不同频率、不同功率密度下的淬火结果。
图3-5 支重轮在不同频率、不同功率密度下的淬火结果
a)2.5kHz,100kW,加热35s b)2.5kHz,200kW加热16s c)2.5kHz,500~450kW,加热7s d)1kHz,400~300kW,加热11s
从图3-5可知,图c淬硬结果最好,这说明采用电流频率2.5kHz比1kHz好,采用功率500~450kW比小功率100或200kW好。功率大时,其淬硬区域比小功率为宽。
5.钢加热到淬火温度的能耗
硬化层加热到淬火温度所需能耗,从理论上纯能量转换来讲,其能耗数值是较小的,但由于电源系统的损耗,变压器、感应器的损耗,工件向心部传热辐射等,能耗值就增加很多。部分金属感应加热的理论与实际能耗见表3-10(Ajax公司资料)。
我国某厂在生产中得出:钢感应透热到锻造温度的能耗值为315kW·h/t最近我国在钢坯透热的能耗指标已小于此值,更加节能。
表3-10 部分金属感应加热的理论与实际能耗