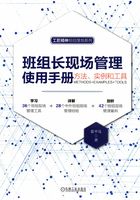
第六节 班组日产效率怎样优化
一、班组作业标准化——作业指导书
作业标准是指为了进行标准化作业,在各工序中,生产出产品设计者所希望的功能和外观,而规定的各种技术标准、作业方法和管理条件。例如,加工时的温度、时间和压力等;刀具的类型、形状、材料、尺寸、切割条件和切削液等;QC工程表、制造标准、作业要点表和检查指导表等。
因企业的不同,其叫法也各种各样,如作业指导书、作业要领书、标准作业卡(标准作业票)、工位能力表、标准作业组合表、要素山积表和标准手持量等,见表1-20。
表1-20 作业标准书主要形式及其内容

【实例11】某机械产品作业指导书
某机械产品作业指导书见表1-21。
表1-21 某机械产品作业指导书

二、效率、稼动率及切换率计算
标准时间、工时运用效率和出勤体制决定了生产能力和综合效率,进而决定了交货周期和合同履约能力。因此,提高生产能力及生产率是现场管理的另一重要目标。
1.有效运转率
每天投入的工时中只有一部分是能有效产出产品的,这部分工时占当天总投入工时的比率,称为有效运转率,其计算公式为
有效运转率=有效作业时间/总投入时间×100%=(总投入工时-非作业时间)/总投入工时×100%
其中,非作业时间包括计划内非作业时间和计划外非作业时间。计划内非作业时间是根据实际需要,有计划地安排的必要的非作业时间,如班前会、设备点检、工间休息等;计划外非作业时间是不希望发生,但实际上又经常发生的非作业时间,如设备故障、设备调整、材料待工、质量问题等。有效运转率是一种效率指标,根据月度工时统计数据可以得到阶段性有效运转率数值。为了提高有效运转率,应减少没有有效产出的非作业时间,使计划内非作业时间合理化、计划外非作业时间最小化。
2.稼动率
稼动率是衡量设备性能的一个重要指标。一般来讲,设备的稼动率越高,说明设备的性能越好,生产率越高。稼动率评价指标如下。
(1)价值稼动时间。价值稼动时间是指能够真正产出合格品的有价值的时间,即
价值稼动时间=性能稼动时间×合格品率×100%
(2)实质稼动率。实质稼动率的计算公式为
实质稼动率=生产量×实际周期时间÷稼动时间×100%
(3)设备综合效率。设备综合效率的计算公式为
设备综合效率=时间稼动率×性能稼动率×合格品率
其中性能稼动率=速度稼动率×生产量×实际周期时间÷稼动时间×100%;合格品率=(投料数-废品数)÷投料数×100%。
(4)废品数。废品数的计算公式为
废品数=起动废品+过程废品+返修品+试验品
在实际的生产过程中,班组长应当加强设备管理,不断改善设备的稼动率,以提高生产率。
3.切换率和切换效率
在每个月的工时投入中,还有一部分用于机型切换的时间也是不能有效产出产品的,这部分时间占月总工时的比率,称为切换率,其计算公式为
切换率=总切换时间/总投入时间×100%
每个月的工时去除机型切换的时间后,有效产出产品时间占月总工时的比率,称为切换效率,即
切换效率=1-切换率
可以用平均每次切换时间衡量生产线的切换能力,即
切换时间=∑切换次数×平均每次切换时间
4.如何提高生产线综合效率
综合有效运转率是工时运用效率的整体反映,可用有效运转率和切换效率的综合效果来表示,其计算公式为
综合有效运转率=有效运转率×切换效率=有效运转率×(1-切换率)
工时运用效率是生产率管理的重要指标,它与标准工时共同决定了生产能力,进而决定了综合生产率。
【实例12】工序工时效率计算实例
某工序出勤体制为两班两倒,每班出勤8h,一天出勤16h。2013年4月21日,该工序工时运用的实际情况见表1-22。
表1-22 某工序工时运用情况

该工序有效运转率为
有效运转率=807÷960×100%=84.06%
该工序主要生产A、B两大系列产品。2013年4月,该工序生产26天,机型切换52次,机型切换消耗的总工时为1254min。
解析:该工序切换率为
切换率=1254÷(16×26×60)×100%=5.02%
切换效率为
切换效率=1-5.02%=94.98%
三、生产线平衡分析与生产最优化
生产线的生产能力是由其能力最低的工序决定的,工序之间能力差别越大即能力越不平衡,生产线的效率损失就越大。要提高生产线的整体效率,务必改善生产线的工序能力平衡。
1.生产线平衡分析
生产线平衡分析是指分析生产线中各工序的时间差异状态,并将差异时间消除,使生产线保持顺畅的方法,也称为“工序平衡分析”“工时平衡分析”。通过生产线平衡分析,可以提高人员、机械的运作效率,实现机械化(省人化)、自动化(省力化)。
(1)生产线平衡分析的基本步骤。生产线平衡分析的基本步骤:①确定分析对象的范围,即对象生产线和对象工序;②把握分析对象的现状;③明确标准工时或观测各工序纯工时;④制作工序作业速度分析图(棒形图);⑤计算生产线平衡率和平衡损失率;⑥找到能力富余及不足的工序;⑦研究分析结果,制订改进方案。
(2)生产线平衡的计算。生产线平衡率的计算公式为
生产线平衡率=实际作业所需时间总和/作业时间总和
Er=∑Ti/(Ci×N)
式中 Er——生产线平衡率;
Ti——各作业工时时间;
Ci——瓶颈工序单位产品产出时间;
N——作业数总和。
生产线的平衡损失率计算公式为
生产线平衡损失率=非加工时间总和/作业时间总和
η=∑LTi/(Tb×N)=1-Er
式中 η——生产线平衡损失率;
LTi——各作业非加工时间;
Tb——生产节拍,即生产线上相继出产两件相同产品之间的时间间隔。
(3)生产线平衡的改善方法。通过生产线平衡分析,发现瓶颈工序,制订并实施改善方案消除瓶颈工序,提高作业资源的产出,调整工序的作业内容,使各工序作业时间达到平衡,以提高生产线的整体效率,实施时可采用以下六大方法,如图1-26所示。
1)分担转移。将瓶颈工序的部分作业内容转移到相邻工序或其他工时短的工序,由作业负荷小的工序分担。
2)作业压缩改善。将瓶颈工序的不必要部分的作业进行压缩,进行改善。
3)加入改变。对于工时长的工序,可以通过增加人员来分担瓶颈工序的工作量。
4)拆解。将瓶颈工序的作业内容拆解。
5)重排。将瓶颈工序的作业内容拆解后,再将整条生产线的作业内容进行重新编排、分配。
6)作业改善后合并。合并相关工序,重新排布生产工序或形成新的作业工序。在精益生产中,可凭借生产线U形布局和多技能员工轻易达到此目的。

图1-26 生产线平衡改善的方法
a)分担转移 b)作业压缩改善 c)加入改变 d)拆解 e)重排 f)作业改善后合并
四、如何进行切换线管理
机型切换是工业生产中的重要工作,切换效率的高低直接影响到生产率,尤其是在当前多品种、小批量的市场环境中,改善切换效率是提升生产率的重要内容。
1.机型切换四大内容
一般来说,机型切换包括四大内容:生产准备、材料切换、标准切换和工装切换(见图1-27)。

图1-27 机型切换的四大内容
1)生产准备。
①新的型号生产前的机型切换准备,如切换用具准备、切换人员安排等。
②前一型号生产结束后的材料撤离、数据统计、现场整理等。
③新型号生产的技术资料、作业文件、工具用具等的准备。
2)材料切换。不同型号的产品会用到不同型号的原材料、零件、辅助材料等,正确准备新材料、切换时将前一型号产品材料撤离生产线、将新型号材料配送上线,是机型切换的重要内容。切换时的材料配送错误将直接导致产品型号错误,造成大批量不合格。因此,结合物流配送和质量首检工作,确保材料正确配送,是材料切换的关键点。
3)工装切换。设备加工常利用工装对工件进行定位、导向、成形等。工装的形式很多,包括模具、刀具、定位夹具、导向夹具等。根据产品的形状、尺寸、结构等特点,不同的型号用到的工装不同。切换工装以适应新型号产品的生产,是机型切换的第三大内容,通常也称之为“换模”。
4)标准切换。根据产品技术和生产工艺,不同型号的产品在生产时要达到的技术标准不同,所采用的工艺条件、作业程序也不同,所以必须进行标准切换,以满足新型号产品的技术要求和质量要求。
在四大切换内容中,工装切换和标准切换往往伴随着工装调整、设备调整、工艺条件调整和质量确认等过程。要提高切换效率,最直接的方法就是减少切换次数、缩短每次切换时间,从而减少切换造成的停线时间。
2.快速切换的七大要点
为了实现快速切换,要遵循下述七大要点,不断地进行切换改善。
(1)事前充分准备。在切换组织和分工上也要进行改善,密切配合,动态把握生产进度,及时、合理安排切换作业,并实施标准化内外切换作业,减少外作业的时间消耗和人力投入。
1)对于简单的、技术要求低的切换内容,可以由作业者进行,如工具准备。
2)对于复杂的、技术要求高的切换内容,可以由骨干进行;必要时由班组长或专业人员进行确认。
3)对于关键的、复杂的、技术要求高的切换内容,可以由专业人员或班组长其中一方进行;必要时由另一方进行确认。
4)编制必要的标准化作业文件,对切换人员进行标准化切换培训,提高其熟练度和切换技术能力。
(2)不要变动标准。由于硬件切换完成后的调整时间占整个切换时间的50%~70%,换型后的调整费时费力,所以,不要变动标准,使切换时设备条件、基准、标准无须调整,这是切换改善的一大原则。常用的方法有:①将内作业转化为外作业;②变整体切换为局部切换;③切换作业标准化,如切换程序化、切换模板化等。更重要的是,要取消以刻度或仪表读取数值的方式来确认工艺条件,尽量改用量规、限位块等容易取放、设定的方式来减少调整时间。
(3)平行作业。所谓平行作业,是指将原来一个人单独进行的切换作业改由两个人同时、共同进行,从而缩短内作业时间。
(4)手动脚勿动。切换时员工将切换所需要的物品、模具、材料和工具等充分、有序地准备好,放置在切换人员伸手可及的范围内,以双手完成切换动作,务必减少双脚移动或走动的机会。
(5)使用“道具”不用工具。日本企业把通用的工具称为“工具”,专用的工具称为“道具”。专门为切换制作合适的“道具”,同时尽可能减少道具的种类,以缩短寻找和取放时间,这样可以提高切换的速度和效率。例如,某工序切换时要用到M12的梅花扳手和M8的内六角扳手。可以将扳手M12的一头与M8的内六角扳手焊接在一起,并将中间握手的部分做成纺锤形以便抓握,进行切换作业。
(6)尽量不用螺栓。装卸螺栓费时费力,且螺栓使用久后容易滑丝,所以设备的切换部分尽量不要使用螺栓进行联接固定,可改用插销、压杆、中介夹具、卡式插座、定位板、燕尾槽、轴式凸轮锁定等方式取而代之,这样切换就会快捷方便。
(7)不要取下螺栓。如果限于某些情况、某些部位必须使用螺栓时,则要设法减少拧紧及取下螺栓的时间。例如,可采用只旋转一次即可拧紧或放松的方式,或使锁紧部位高度固定化。
【中外班组管理经验6】导轨组装分厂生产线平衡分析范例
某精密制造公司导轨组装分厂为增加产出、提高效率,聘请生产管理顾问进行指导,成立以顾问、班组长、IE工程师、质量经理、技术工程师等组成的改善小组,进行生产线平衡分析。如图1-28所示的是流水线布置图。

图1-28 流水线布置图
通过生产管理顾问为改善小组人员实施生产线平衡的知识培训后,改善小组对导轨组装进行现状分析并绘图,如图1-29所示。

图1-29 改善前平衡图
通过平衡图(见图1-29)分析,改善小组发现,导轨组装制造二部各工序的作业时间存在相当差异,平衡率经计算为68.7%,生产线平衡损失率较高。
现场改善小组对导轨组装相近的工序进行研究,发现在作业改善上能采取较简便的方法是合并工序内容,调整并取消时间过短工序,把其中部分工作分配到其他工序中,所形成的具体改善方案见表1-23,平衡图如图1-30所示,评价表见表1-24。如此达到了提高平衡率、减少工时损失、提高整体效率的目的。
表1-23 工序作业改善方案对策表

表1-24 改善前后各项产能指标比较


图1-30 改善后平衡图
【实例13】机械加工生产线和装配生产线换线快速化方法
机械加工生产线和装配生产线换线快速化方法见表1-25。
表1-25 机械加工生产线和装配生产线换线快速化方法
