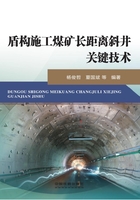
3.1 盾构型式选择及整机系统集成
依托工程新街台格庙矿区斜井的工程及水文地质条件揭示了斜井具有“深埋超长、连续下坡、富水高压、地层多变”的特点,要求盾构具有同时具备开式和闭式两种掘进模式,以保证煤矿斜井施工安全。
3.1.1 双模式盾构技术要求
依据新街台格庙矿区斜井和神东补连塔斜井的工程地质及水文地质特点,双模式盾构需满足以下技术要求:
(1)满足单次连续掘进6500m以上,大埋深、复杂地质条件下的长距离掘进对盾构关键部件及系统的可靠性要求。
(2)满足6°倾角连续下坡掘进对盾构设计与设备配置的特殊要求,包括开挖、出渣、排水、设备布局等。
(3)多物料运输效率须满足不低于600m的月进尺指标。
(4)瓦斯等有害气体的控制须满足设备施工和人员作业的安全要求。
(5)设备具备开式和闭式两种工作模式且能够在硐内实现快速模式转换,为此须将刀盘设计为具有闭式和开式双重模式的功能,需在盾体内可安装适应于闭模式的螺旋出渣机和带式出渣机。
(6)满足无扩大硐室井下大倾角原位拆解对盾构结构设计及拆解工艺的特殊要求。
3.1.2 双模式盾构主机参数确定
双模式盾构主机具有以下特征:
(1)双模式盾构具备两种掘进模式:闭式模式与开式模式,通过拆装主机带式输送机、刀盘溜渣板、刀盘椎板、螺旋输送机,更换回转接头、转换接渣斗等步骤可实现两种掘进模式间的转换,双模式盾构示意如图3.1所示。
(2)斜井管片内径6600mm,管片外径7300mm,管片环宽度1500mm,双模式盾构刀盘开挖直径7620mm,最大破岩能力200MPa,开式模式最大掘进速度120mm/min,闭式模式最大掘进速度80mm/min。
(3)双模式盾构总长度238m,其中主机长度13m(盾体长度10m),后配套拖车数量20节,每节平均长度10m,连接桥长度20m,盾构开式模式和闭式模式下的主机型式分别如图3.2和图3.3所示。

图3.1 双模式盾构示意
(4)可适应的最大坡度为12%及最小曲线半径为500m。

图3.2 开式模式下的盾构主机型式

图3.3 闭式模式下的盾构主机型式
为满足上述技术要求,确定双模式盾构主要参数见表3.1。
表3.1 双模式盾构主要参数

3.1.2.1 盾构所需推力确定
盾构前进所需推力FA由主机滑行的摩擦阻力FA1、后配套拖车的摩擦阻力FA2、刀盘最大承载能力FA3和斜井坡度影响的斜向推力FA4组成,即
FA=FA1+FA2+FA3-FA4 (3.1)
盾体外壳与围岩的滑动摩擦系数取0.3,主机重量5000kN,则FA1=1500kN。拖车车轮与管片的滚动摩擦系数取0.15,拖车重量6000kN,FA2=900kN。刀盘安装的滚刀数量n=46,单个滚刀最大承载能力N=250kN,则FA3=11500kN。由于斜井坡度(向下6°)影响导致盾构主机及后配套设备的斜向推力,则FA4=1150kN,则双模式盾构掘进所需推力FA=12750kN。
双模式盾构推进液压系统额定压力30MPa,油缸数量为34,油缸内径0.23m,则双模式盾构推进系统总推力F=42364kN。因盾构闭式掘进所需推力小于开式掘进模式所需推力,推进力FA计算是基于盾构开式掘进模式;推进系统的极限压力为35MPa,即双模式盾构最大推进力49424kN,推进能力储备充裕。
3.1.2.2 双模式盾构刀盘驱动扭矩与转速
因盾构闭式模式掘进施工时,土仓内充满渣土并保持有一定的压力,刀盘驱动扭矩相对较大,而盾构开式模式掘进时,开挖仓内岩渣较少且无压力,一般采用低扭矩高转速的策略实现快速掘进,其刀盘驱动阻力矩相对较小。因此,双模式盾构刀盘扭矩计算主要依据盾构闭式模式进行。
在盾构闭式模式下,刀盘驱动扭矩的载荷来源主要包括:刀具切削扭矩(切刀、滚刀)、渣土在土仓内与刀盘之间的摩擦、刀盘搅拌棒等装置对土体的搅动以及主驱动齿轮传动与密封系统的扭矩传递损耗等。驱动扭矩大小主要取决于工程地质及盾构刀盘结构形式。以成都地铁(砂卵石地层)和上海地铁(淤泥质黏土地层)为例,其6250mm系列直径级盾构施工刀盘最大驱动扭矩的估算结果分别为3910kN·m和2366kN·m,估算结果与实际测量数据的偏差在±5%以内。
双模式盾构及其应用工程,采用估算法计算刀盘驱动所需扭矩为Tc,采用校核法确定双模式盾构实际配置的额定扭矩为Td。
(1)刀盘驱动扭矩估算值Tc
Tc=α1×α2×α3×D3=6371(kN·m) (3.2)
式中 D——刀盘开挖直径(m),D=7.62m;
α1——刀盘支承结构影响系数,一般为0.8~1.0,中间支承方式刀盘取0.9;
α2——工程地质影响系数,一般为0.8~1.0,对于砂岩、泥岩地质取值0.8;
α3——掘进机开挖模式影响系数,一般为14~23kN/m2,当为土压平衡闭式掘进方式时取20kN/m2。
(2)额定驱动扭矩实际配置值Td
Td=nd×Te×id1×id2≈8300(kN·m) (3.3)
式中 nd——驱动电机数量;
Te——单个驱动电机额定输出扭矩,Te=3500N·m;
id1——减速器减速比;
id2——减速器减速比,当采用土压平衡闭式掘进方式时,id2=148/15。
计算分析表明,刀盘在额定转速2.9r/min时,刀盘额定扭矩为8300kN·m,大于工况所需扭矩5734kN·m;刀盘最大回转速度由周边滚刀速度决定(18英寸滚刀允许最大线速度为3m/s),而刀盘最高转速为6.4r/min,对应的滚刀最大线速度为2.55m/s<3m/s,刀盘扭矩和转速参数配置满足要求。
3.1.2.3 双模式盾构螺旋输送机参数
盾构采用闭式模式掘进时,需采用螺旋输送机出渣。
(1)主要计算参数
螺旋输送机叶片外径D=0.9m,螺杆直径d=0.22m;螺旋节距S=0.63m,螺旋输送机总长度Lm=13m;最大转速ns=19r/min。螺旋输送机自身倾角β1=+25°,斜井坡度β2=+6°。
(2)螺旋输送机理论生产率Q
Q=3600×S×ψ×V=450(m3/h) (3.4)
式中 S——螺旋输送断面面积,S=π(D2-d2)/4=0.62m2;
V——渣料轴向最大运动速度,V=Sns/60=0.2m/s;
ψ——充填系数,ψ=1.0(渣料全部充满螺旋输送机仓内)。
(3)螺旋输送机渣料与筒体内壁的摩擦消耗的功率N1
N1=q×Lm×V×f1×ε=36421(W) (3.5)
式中 q——单位荷载, (输送物料的容积密度γ=2.0t/m3);
f1——渣料与筒体内壁的摩擦系数,为0.85;
ε——渣料对筒体的摩擦力影响系数,为1.344。
(4)渣料对螺旋叶片的摩擦消耗的功率N2

式中 f2——渣料与螺旋叶片间的摩擦系数,为0.8;
λ——物料距轴中心线平均半径处的螺旋线升角,λ=16.55°。
(5)空载情况下回转轴承自身摩擦消耗的功率N3
N3=G×f3×V×π×Dc/S=415(W) (3.7)
式中 G——回转轴承承载自重,为5050kg;
f3——轴承摩擦系数,为0.15;
Dc——轴承回转半径,Dc=0.55m。
(6)向上倾斜输送时提升物料所消耗的功率N4
N4=q×H×V=16431(W) (3.8)
式中 H——倾斜输送时距离的垂直投影长度,H=Lmsin(β1+β2)=6.7m。
(7)满载工况下回转轴承摩擦所消耗的功率N5
N5=f3×(N1+N2+N4)=17837(W) (3.9)
(8)螺旋输送机的总功率消耗Nz
Nz=N1+N2+N3+N4+N5=137(kW) (3.10)
螺旋输送机配置功率为200kW,额定转速19r/min下的输出扭矩180kN·m,最大出渣能力为450m3/h,而盾构闭式掘进模式下最大掘进速度为80mm/min时对应的出渣量为437m3/h,螺旋输送机的参数配置能够满足最快掘进要求。
3.1.2.4 双模式盾构主机带式输送机参数
盾构采用开式模式掘进时,需采用带式输送机出渣。
(1)原始数据及工作条件
输送物料为砂岩/泥岩/黏土,输送能力为Qmax=850t/h,带宽B=900mm,带速V=2.5m/s,带式输送机水平长度Lh=12m,导料槽长度L=4m,提升高度H=2.43m;带式输送机倾角δ1=12°,物料原始密度ρ1=2500kg/m3,物料堆积密度ρ2=1600kg/m3,上托辊平均间距a1=1000mm,下托辊平均间距a1=2500mm,托辊槽角λ=35°;托辊直径ф=108mm;托辊前倾角δ2=1.5°。
(2)输送物料与导料栏板的摩擦阻力Fz1

式中 Iv——单位长度输送带输送的物料质量, 。
(3)输送带清扫器的摩擦阻力Fs1=1700N。
(4)输送带倾斜阻力
Fr=q×H×g=2266(N) (3.12)
(5)输送带输送圆周驱动力Fu
Fu=i1×(Fz1+Fs1+Fr)=5095(N) (3.13)
式中 i1——托辊影响系数,i1=1.2,取值大小与带式输送机托辊直径、质量及材料有关。
(6)输送带运行功率
P1=Fu×V/1000=12.74(kW) (3.14)
实际选用的主机带式输送机驱动方式为液压马达驱动,马达装机功率为30kW,考虑到功率损失,实际运行最大功率将不低于25kW,能够满足主机带式输送机最大输送能力850t/h(12.74kW)的工作要求。
3.1.3 双模式盾构总体设计
双模式盾构在不同模式下的特征区别主要体现在主机部分,盾构开式模式和闭式模式下的主机结构组成如图3.4和图3.5所示。
双模式盾构的主要机械结构由螺旋输送机(盾构闭式模式下)、主机带式输送机(盾构开式模式下)、盾构闭式模式刀盘、盾构开式模式刀盘、主驱动、盾体(前盾、中盾及盾尾)和管片拼装机等组成,如图3.6~图3.12所示。另外,在刀盘后方安装有正面超前钻机两台,斜向超前钻机一台。

图3.4 盾构开式模式主机结构组成

图3.5 盾构闭式模式主机结构组成

图3.6 关键部件——螺旋输送机

图3.7 关键部件——主机带式输送机

图3.8 关键部件——刀盘(盾构闭式模式)

图3.9 关键部件——刀盘(盾构开式模式)

图3.10 关键部件——主驱动

图3.11 关键部件——盾体

图3.12 关键部件——管片拼装机
另外,由于双模式盾构施工期间将穿越不同的地层,特别是在岩石地层掘进时,仅仅依靠主机自重产生的摩擦力有可能无法提供足够的掘进反力矩,为此采取了在主机底部加设防扭条和盾体径向布置多个液压稳定器的方式来提高主机反扭性能。