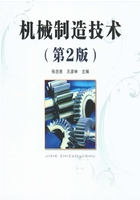
1.5 切削液的合理选用
在切削过程中,合理地使用切削液(又称冷却润滑液),可以减小刀具与切屑、刀具与加工表面的摩擦,降低切削力和切削温度、减小刀具磨损、提高加工表面质量。合理使用切削液是提高金属切削效益的有效途径之一。
1.切削液的种类
金属切削加工中最常用的切削液可分为四大类:水溶液、切削油、极压切削油和乳化液。
1)水溶液
水溶液的主要成分是水,冷却性能好,若配成透明状液体,还便于操作者观察。但纯水易使金属生锈、润滑性能也差,故使用时常加入适量的防锈添加剂(如亚硝酸钠、磷酸三钠等),使其既保持冷却性能又有良好的防锈性能和一定的润滑性能。
2)切削油
切削油的主要成分是矿物油,特殊情况下也可采用动、植物油或复合油。切削油润滑性能好,但冷却性能差,常用于精加工工序。
3)极压切削油
极压切削油是在矿物油中添加氯、硫、磷等极压添加剂配制而成。它在高温下不破坏润滑膜,具有良好的润滑效果,故被广泛采用。
4)乳化液
乳化液是用95%~98%的水将由矿物油、乳化剂和添加剂配制成的乳化油膏稀释而成,外观呈乳白色或半透明状,具有良好的冷却性能。因其含水量大,润滑、防锈性能较差,所以常加入一定量的油性、极压添加剂和防锈添加剂,配制成极压乳化液或防锈乳化液。
2.切削液的作用
切削液主要起冷却和润滑的作用,同时还具有良好的清洗和防锈作用。
1)冷却作用
切削液主要靠热传导带走大量的热来降低切削温度。一般来说,水溶液的冷却性能最好,油类最差,乳化液的介于两者之间而接近于水溶液。
2)润滑作用
切削液渗透到切削区后,在刀具、工件、切屑界面上形成润滑油膜、减小摩擦。润滑性能的强弱取决于切削液的渗透能力、形成润滑膜的能力和强度。
3)清洗作用
切削加工中产生细碎切屑(如切铸铁)或磨料微粉(如磨削)时,要求切削液具有良好的清洗作用和冲刷作用。清洗作用的好坏,与切削液的渗透性、流动性和使用的压力有关。为了提高切削液的清洗能力,及时冲走碎屑及磨粉,在使用时往往给予一定的压力,并保持足够的流量。
4)防锈作用
为了减小工件、机床、刀具受周围介质(如空气、水分等)的腐蚀,要求切削液具有一定的防锈作用。防锈作用的好坏,取决于切削液本身的性能和加入的防锈添加剂的作用。在气候潮湿地区,对防锈作用的要求更为突出。
3.切削液的合理选用和使用方法
1)切削液的合理选用
切削液的种类很多,性能各异,应根据工件材料、刀具材料、加工方法和加工要求合理选用。一般有如下选用原则:
(1)粗加工。粗加工时切削用量较大,产生大量的切削热容易导致高速钢刀具迅速磨损。这时适宜选用以冷却性能为主的切削液(如质量分数为3%~5%的乳化液),以降低切削温度。
硬质合金刀具耐热性好,一般不用切削液。在重型切削或切削特殊材料时,为防止高温下刀具发生黏结磨损和扩散磨损,可选用低浓度的乳化液或水溶液,但必须连续充分地浇注,不可断断续续,以免因冷热不均产生很大热应力,使刀具因热裂而损坏。
在低速切削时,刀具以硬质点磨损为主,适宜选用以润滑性能为主的切削油;在较高速度下切削时,刀具主要是热磨损,要求切削液有良好的冷却性能,适宜选用水溶液和乳化液。
(2)精加工。精加工以减小工件表面粗糙度值和提高加工精度为目的,因此应选用润滑性能好的切削液。
加工一般钢件时,切削液应具有良好的润滑性能和一定的冷却性能。高速钢刀具在中、低速下(包括铰削、拉削、螺纹加工、插齿、滚齿加工等),应选用极压切削油或高浓度极压乳化液。硬质合金刀具精加工时,采用的切削液与粗加工时基本相同,但应适当提高其润滑性能。
加工铜、铝及其合金和铸铁时,可选用高浓度的乳化液。需要注意的是,因硫对铜有腐蚀作用,因此切削铜及其合金时不能选用含硫切削液。铸铁床身导轨加工时,选用煤油作切削液效果较好,但较浪费能源。
(3)难加工材料的加工。切削高强度钢、高温合金等难加工材料时,由于材料中所含的硬质点多、导热系数小,加工均处于高温高压的边界摩擦润滑状态,因此适宜选用润滑和冷却性能均好的极压切削油或极压乳化液。
(4)磨削加工。磨削加工速度高、温度高,热应力会使工件变形,甚至产生表面裂纹,且磨削产生的碎屑会划伤已加工表面和机床滑动表面。所以适宜选用冷却和清洗性能好的水溶液或乳化液。但磨削难加工材料时,适宜选用润滑性好的极压乳化液和极压切削油。
(5)封闭或半封闭容屑加工
钻削、攻螺纹、铰孔和拉削等加工的容屑为封闭或半封闭方式,需要切削液有较好的冷却、润滑及清洗性能,以减小刀屑摩擦生热并带走切屑,因此宜选用乳化液、极压乳化液和极压切削油。
常用切削液的选用示例如表1-4所示。
表1-4 常用切削液的选用

注:本表中数字的意义如下:
0—干切削液;1—润滑性不强的水溶液;2—润滑性强的水溶液;3—普通乳化液;4—极压乳化液;5—普通矿物油;6—煤油;7—含硫、含氯的极压切削液,或动植物油的复合油;8—含硫、氯、磷的极压切削液。
2)切削液的使用方法
切削液不仅要选择合理,而且要正确使用,才能取得更好的效果。其使用方法包括如下三种:
(1)浇注冷却法。浇注冷却法是最普通的使用方法,如图1-30所示。虽使用方便,但流量小、压力低,难直接渗透到切削刃最高温度处,效果较差。切削时,应尽量浇注到切削区。车、铣时,切削液流量为10~20L/min。车削时,从后面喷射比在前面浇注好,刀具耐用度可提高一倍以上。
(2)高压冷却法。高压冷却法适于深孔加工,将工作压力1~l0MPa,流量50~150L/min的切削液直接喷射到切削区,并可将碎断的切屑驱出。此法也可用于高速钢车刀切削难加工材料,以改善渗透性,可显著提高刀具耐用度,但飞溅严重,需要加护罩。
(3)喷雾冷却法。以0.3~0.6MPa的压缩空气及喷雾装置使切削液雾化,从直径1.5~3mm的喷嘴中高速喷射到切削区。高速气流带着雾化成微小液滴的切削液渗透到切削区,在高温下迅速汽化,吸收大量热量,达到较好的冷却效果,如图1-31所示。这种方法综合了气体的速度高和渗透性好,以及液体的汽化热高、可加入各类添加剂的优点,用于难切削材料加工及超高速切削时,可显著提高刀具耐用度。

图1-30 浇注冷却法

图1-31 喷雾冷却法