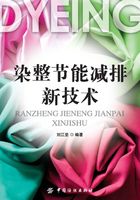
第四节 织物松堆丝光
棉织物经过丝光处理后可获得耐久性的光泽,提高染料的吸附能力,并且还可提高成品尺寸的稳定性,降低缩水率。传统针织物的丝光加工有筒状、筒状平幅和剖幅三种形式。其中筒状或筒状平幅丝光容易出现布边轧痕,织物的经、纬斜以及织物的拉长现象;剖幅平幅丝光需要控制卷边和张力,还要多一道开幅工艺。传统的针织物丝光大多采用剖幅平幅丝光,基本上是以提高织物光泽为主的一种“常规紧式”布铗丝光。
近年来出现了圆筒针织松堆气胀式丝光工艺,织物在松堆过程可以获得足够的碱作用时间和溶胀效果。该工艺是对织物在进入轧点之前进行空气吹鼓胀,以避免织物产生折痕。织物在没有过分张力的条件下,碱液对纤维进行充分和均匀的渗透。织物以圆筒状进行加工,既省去开幅工序,同时还可避免织物的卷边和张力过大,尤其适于含有弹力纤维的针织物的丝光。
一、常规紧式丝光存在的问题
由丝光原理得知,纤维素纤维经浓碱处理后发生剧烈溶胀,纤维横截面由腰子形转变为近似圆形或椭圆形。此时若对纤维不施加张力任其收缩,即使横截面形态发生变化,也不会有明显光泽现象。只有在纤维浸渍碱液后或者在洗碱过程中,同时对纤维实施纵向张力减少纤维表面的皱纹,才能够使纤维获得明显的光泽,并且光泽的程度会随着张力的加大而增强。当施加的张力足以使纤维在含碱液情况下保持长度不收缩,或者收缩后再将其拉伸至原有长度时,纤维的光泽可达到最佳效果。这就是棉织物采用常规紧式丝光的目的所在。然而,紧式丝光工艺对织物所施加的张力,会影响到织物吸附碱液均匀性,以及碱对麻类织物的品质影响。
1.张力的影响 紧式丝光工艺虽然可以使织物获得一定的光泽效果,但由于织物在张紧状态下,碱液很难渗入纤维内部,尤其是在经、纬纱线的交织点处,影响到纤维的溶胀性。此外,织物在丝光过程中的张力作用下连续运行,设备的长度限制了烧碱和纤维的作用时间(45~50s)。而实践证明,织物碱处理的作用时间,即使在松堆下也必须保持在5min以上,纤维才能达到较好的溶胀效果。因此,紧式丝光工艺无法满足碱对纤维作用实际所需的时间,纤维不能获得充分溶胀。这种没有充分溶胀的纤维除了增加织物的光泽效果外,并没有使其他如吸收染料的能力、染色的均匀度、降低缩水率及节约用碱等方面得到改善。
2.丝光工艺的适用性 纤维素纤维的丝光作用与织物纤维特性、混纺织物中棉纤维所占的比例以及提高染色性等因素有关,必须根据这些相关因素以及具体的使用要求,确定是否需要进行丝光处理。例如,苎麻织物本身就具有良好的光泽,若采用常规紧式丝光处理,就会导致苎麻纤维在浓碱下受到损伤,并使纤维手感粗硬。但是采用松堆丝光处理,就会提高染色性能,降低内应力,并改善手感。又如,涤/棉(65/35)织物本身已经具有良好的光泽,即使浸轧烧碱后在松堆状态下,也不会因有1/3的棉产生溶胀而使织物收缩。因而对涤/棉织物进行丝光处理的目的,应该是提高染色的上染量,减少上染不均匀的发生。况且在丝光之前还要经过一次拉幅定形处理,织物幅宽可以得到有效控制,织物的缩水率完全可以控制在允许范围内。由此可见,纯棉织物目前的丝光要求,不仅是为了改善织物外观的光泽,更重要的是获得染整加工的其他品质。
二、松堆丝光的作用
与紧式丝光工艺相比,松堆丝光的一个重要过程就是松堆。它是织物经过第一道浸轧碱液后,不经绷布辊而直接进入“J”形箱或履带箱进行松式堆置。在松式堆置中织物纤维可被碱液充分渗透,并且持续作用5min以上,使织物纤维能够获得均匀的溶胀。纤维素纤维经松堆丝光后,溶胀性、纤维吸附性、匀染度、幅宽和缩水率、用碱量和能耗等都得到了很大改善。
1.纤维素纤维的溶胀性 没有经过烧碱处理的纤维素纤维主要是纤维素Ⅰ型,经碱处理后,纤维结晶区,c轴和a轴的晶胞参数以及β角发生了变化,部分纤维素Ⅰ型转变为纤维素Ⅱ型。从I型转变为Ⅱ型的多少可反映出纤维的溶胀程度。纤维素I型和Ⅱ型的X射线衍射图谱各有其特征峰,通过电脑对图谱进行分峰处理可得到纤维素I和维纤素Ⅱ含量的数据,并由此可计算出纤维的结晶度。经纱在紧式丝光中受到强烈拉伸,经纱伸直紧贴在纬纱上,实际上是对纬纱施加了纬向张力。而紧贴着的经、纬交织点处,就难以透入碱液,尤其是经密高的织物更明显。相比之下,松堆丝光就不会发生这种现象。
丝光对苎麻的作用效果要比棉小,主要是苎麻的结晶度较高、纤维壁较厚以及杂质含量较高,加之紧式工艺张力大,碱液很难渗入纤维。而常规紧式丝光工艺虽然通过提高碱浓度可提高苎麻的溶胀,但会损伤纤维的强力,并且造成纤维的手感粗硬。若采用松堆丝光工艺,则可延长作用时间,改善纤维溶胀效果。
2.纤维素纤维的吸附性 纤维素纤维织物经碱处理后,可降低纤维的结晶度和密度。这意味着增加了纤维的无定形区,为染料向纤维内部的扩散提供了有利条件。松堆工艺的这种作用效果要比常规紧式工艺更明显。试验表明,松堆丝光工艺的碱液浓度降低至常规紧式工艺的70%,对麻类织物染色的得色率仍可提高20%以上;涤/棉织物中即使只染其中占1/3的棉,其得色率也可提高5%~10%,某些染料甚至可达20%。因此,采用松堆工艺,具有显著的节约染料效果,并且颜色的鲜艳程度也有所提高。
3.织物的匀染度 松式丝光工艺在提高纤维素纤维吸附性的同时,还可使纤维获得均匀的吸附能力,为染料均匀上染纤维提供了条件。松堆丝光工艺能够使碱液容易透入纤维内部,碱可对织物纤维不同部位进行均匀作用,使纤维获得均匀和充分的溶胀,进一步提高了染料对织物的匀染度。此外,对于不同成熟度的棉纤维,通过松式丝光工艺的纤维均匀溶胀,可以减小不同成熟度的棉纤维对染料吸附能力的差异,提高匀染性,甚至对棉结“白芯”也会起到改善作用。
4.织物的幅宽和缩水率 紧式丝光工艺对织物产生的经向张力较大,布铗拉幅时织物门幅不易伸展。另外,织物纤维在生长过程中,纤维分子间自由形成的氢键在纤维之间产生的内应力,也会阻碍织物纱线的伸展。这些因素影响到织物幅宽,导致织物的缩水率高。如果采用松堆丝光工艺,碱对纤维均匀和透彻的溶胀,可将纤维分子间的氢键进行解键,消除或减小内应力的影响,使得织物幅宽可进行拉伸。经洗碱和烘干后,纤维分子间在新的位置上能够形成新的且有规则的氢键,将织物的尺寸相对稳定下来,从而达到所需的织物缩水率。
5.用碱量和能耗 松堆丝光工艺可显著降低丝光浸轧碱液的浓度。与常规紧式丝光工艺相比,碱浓度可降低25%~30%,补给碱液的浓度也降低30%,从而减少了碱用量。由于碱浓度的降低,回收碱时也减少了蒸发水分所用蒸汽量。
三、织物松堆丝光工艺与设备
棉纺织品的丝光经过了五十多年的发展,人们看到更多的是获得织物光泽效果所带来的商用价值,而对丝光对其他纤维素纤维(如苎麻)以及在棉混纺织物中棉纤维的作用并没有太深入的研究。因而没有真正发挥出丝光的应用效果。随着节能减排形势的发展,以及松堆丝光工艺的出现,丝光工艺的使用意义又重新得到了印染工作者的认识和重视。这里对织物松堆的工艺和设备作一简单介绍。
1.织物“紧式”与“松堆”丝光工艺 国内有研究者结合紧式和松堆两者的丝光功能,曾设计出可实现“松堆”和“紧式”丝光功能的工艺和设备,可用于苎麻织物、涤棉或涤麻混纺织物以及纯棉织物。该工艺分为两次浸轧碱液,第一次浸轧后松堆,目的是使织物经向、纬向均获得充分的溶胀或收缩;第二次浸轧碱液目的是防止织物松堆因露在空气中可能产生的带碱不均匀。经过绷布辊后再进入轧车,目的是调节第二次浸轧碱液时轧辊的线速度,控制织物张力,使织物恢复到收缩前的长度,并控制纬密。最后经拉幅、水洗和烘干。
工艺流程:
浸轧碱液(浓度为180g/L)→松堆5min→浸轧碱液→进入绷布辊5~8只→两辊小轧车→布铗拉幅→水洗→烘干
2.圆筒针织物松堆气胀式丝光 上海协曼特机电设备有限公司开发的圆筒针织物松堆气胀式丝光机采用充气鼓胀形式,可防止织物产生折痕。织物在进入轧车之前处于气胀状态,使其保持无折痕运行处理。这样圆筒状针织物就不会发生卷边和擦伤现象。该机采用了浓碱浓度、温度、反应时间以及织物经纬向张力的在线检测控制,不仅可进一步保证织物的丝光品质,而且具有显著的节能效果。图2-17为该机设备流程示意图。
设备流程:
浸碱单元(3个)→松式渗透单元→热水去碱定形箱→水洗单元
图2-17 Lztsg(A)-120型圆筒针织物松堆气胀式丝光机设备流程示意图
(1)浸碱单元(图2-18)。碱浸渍槽采用“三浸一轧”形式,保证织物能够得到充分浸透。5个直径为300mm导布辊,由链条独立传动,辊表面带有网孔。2个导布辊在上,3个导布辊浸在碱液中。这样有利于碱液浸入双层织物。3个碱浸渍槽的碱液相连通,织物连续通过每个槽。织物经最后浸渍后,进入轧辊之前可形成气胀状态,避免织物产生折痕。
碱浸渍槽内的碱浓度可在线检测,并有配碱和加液自动控制,以保证碱浓度稳定在工艺要求范围内。槽内碱循环管路中配有清洁过滤装置,可去除循环液中的毛绒和杂质。
(2)松式渗透单元(图2-19)。该单元由进布辊、打手机构、网状输送履带、堆布量控制、提布辊和环状扩幅器等组成。织物在透风过程中,处于无张力和松堆状态,可减少织物受到挤压和拉伸影响。与传统针织物处于紧张状态输送相比,可避免织物产生折痕。织物浸渍浓碱后,以松弛状态堆置在输送网带上,堆置时间3~10min,且可调。织物在堆置的过程中,其纤维可获得充分的渗透、扩散和溶胀,以达到最佳的丝光效果。
图2-18 浸碱单元
图2-19 松式渗透单元
(3)热水去碱定形箱(图2-20)。气胀式扩幅装置可检测圆筒针织物的鼓胀直径,并将检测到的数据传送到充气装置,以确定是否对圆筒针织物充气。该装置可控制织物的纬向定形尺寸。热水去碱定形箱中有三组热水喷淋装置,每一组有三个圆环喷淋管,其圆周上分布了多个扁平型喷嘴,可将热淡碱以水珠状对织物进行强力冲洗。喷淋淡碱液形成逐格逆流,循环热水经过清洁过滤后,由大流量输送泵输入喷淋管。气胀圆筒针织物在运行中,上方是轧车(控制织物带液量),下方是大直径网孔辊筒,均为独立主动辊。通过调节轧车与网辊线速度及每组喷淋装置之间的气动松紧架张力,可控制织物经向定形尺寸。对于任何直径的针织物,在保持圆筒状态下,均可获得稳定的长度和宽度。并且受到充分收缩的棉纤维,在张紧状态下能够进行冲洗去碱。
图2-20 热水去碱定形箱三维立体图
(4)水洗单元。丝光后经过六格相同的水洗单元,每个水洗单元采用“三上四下”导布辊形式,其中上导布辊为主动辊。每格水洗槽具有独立的温度控制,可根据工艺要求分别设置。第四格水洗槽配置了酸中和装置,可以设定pH。该单元能够进行多种酸剂的自动配液和加液,并可保持洗涤水的pH恒定。
3.高效布铗松堆丝光 山东源丰印染机械有限公司开发的YF 1098-180型高效布铗松堆丝光机,具有干、湿两用功能。干进布时,织物直接进入高给液装置,带液率可提高10%~15%;湿进布时,织物经预浸渍槽和高效轧车,获得均匀稳定的低轧液率后再进入高给液装置,可减少烘干的蒸汽消耗。
设备流程:
平幅干进布(平幅湿进布→预浸渍槽→高效轧车)→高给液轧车→落布松式堆置→对中进布→浓碱浸渍槽→高效低轧液率轧车→定长牵伸段→三辊轧车→热淡碱预洗槽→三辊轧车→布铗拉幅机(3冲3吸)→三辊轧车→直辊去碱槽→三辊轧车→高效去碱蒸箱→(二辊轧车→高效水洗箱)×3格→三辊轧车→烘筒烘燥机→平幅落布
(1)轧碱渗透单元。采用立式三辊透芯给液结构,织物经浸渍槽进入重轧辊并在液下轧点进行气液交换,织物经纬交织点空间织物的“无定形区”可获得充分的碱液。从液下轧点出来后进入增效槽,织物呈“微真空”状态,迫使碱液透芯。经开幅辊扩幅后进入上轧点(空气环境),可控制织物表面带液。
(2)碱液循环。高位槽中的配液浓度取决于工艺处方,并根据浓度变化可进行追加。通过液位自动控制系统可将液位控制在合理的范围内。前后轧碱槽连通,通过循环泵自动定时循环碱液,确保织物始终能够获得均匀和稳定的新鲜碱液。循环泵通过旁通管路可将碱液输入高位槽内进行碱液浓度自控,避免直接排放造成浪费和污染。
(3)碱浓度自动控制。轧碱槽的碱液浓度采用碱浓度自动在线控制,控制精度高,可避免人为影响因素,并且可提高工艺重现性和减少碱的消耗。
(4)定长控制。由热淡碱预洗单元、绷布牵伸单元和轧碱单元组成的定长控制系统,可控制织物经向牵伸长度,并通过在线设置牵伸比例,与工艺线速度同步稳速运行。织物松堆后经向长度收缩为7%~17%,经定长控制段在比例稳速“串联”跟随线速度控制下,可将牵伸单元出布预设在95%~100%。这样可避免松堆丝光而影响织物长度。
(5)热淡碱预洗单元。松堆丝光在定长牵伸段设置热淡碱预洗,可提高丝光光泽,并且可降低织物的含碱量,有利于后续布铗拉幅。该单元可将轧碱槽溢流碱液和布铗段倒流碱液混合为浓度85g/L±5g/L,通过加热到65℃,产生流量为30L/min的喷淋液。这种配碱方式使全线逆流无排放,减少碱消耗和污染。
(6)采用“三冲三吸”。松堆丝光工艺碱液浓度要比常规紧式丝光工艺浓度下降30%,将常规“五冲五吸”改为“三冲三吸”,真空抽吸水盘表面滑动摩擦改为滚动摩擦,可减少对织物的摩擦力,避免产生“极光”、“凹纬”等缺陷。