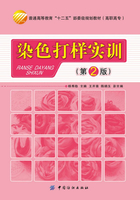
任务一 常用染料性能指标
一、直接性
1.定义
染料分子(或离子)舍弃水溶剂,自动向纤维转移的性能。
2.解读
(1)染料直接性产生的内因是染料分子或离子与纤维之间总是存在分子间作用力(又称为范德华力,简称范氏力)、氢键或库仑引力(离子键)等作用力,而这种作用力又大大超过染料分子或离子与水分子之间的作用力,故而表现为染料的直接性。
(2)染料直接性的大小主要影响染料在上染过程中与纤维之间的吸附作用,如果把纤维作为吸附剂,把染料看成被纤维吸附的吸附质,那么,染料的直接性越大,越容易被纤维吸附。
(3)染料直接性的大小主要与染料自身结构、纤维在水中的带电状态有关。一般而言,染料分子结构越复杂,相对分子质量越大,染料的直接性越大;染料分子中的芳香环共平面性越好,染料的直接性越大;染料分子中的极性基团数目越多,染料的直接性越大。而染料分子中水溶性基团数目越多,则染料的直接性降低。
(4)染料直接性的大小通常用染料平衡上染百分率表示。染料的平衡上染百分率越大,表示染料的直接性越大。
3.直接性测定
在规定的染色条件下,测定染料的平衡上染百分率(见平衡上染百分率测定)。
二、移染性
1.定义
浸染时,上染到织物某个部位的染料,通过解吸、扩散和染液的流动,再转移到另一部位重新上染的性能。
2.解读
(1)染料移染性产生的内因是染料在上染过程中,染料与纤维一般不发生共价键结合,上染是可逆的,即同时存在吸附和解吸现象。染色开始阶段,染料的吸附速率大于解吸速率,随着纤维上染料浓度的提高,染液中染料浓度的降低,染料的吸附速率逐渐减小,直到某一时刻,吸附和解吸速率相等,假设其他染色条件不变,达到染色平衡后再延长染色时间,纤维上的染料量不再增加,即所谓染色达到平衡。
(2)染料的移染性主要影响染料在纤维上均匀分布的程度。移染性能好的染料,纤维得色均匀。
(3)染料移染性主要与染料自身结构、纤维在水中的带电状态及染色工艺条件有关。一般而言,直接性越大的染料,其移染性越差。
3.移染性测定
通过在染色空白液中,色布对白布的沾色量计算出移染指数,判断染料的移染性能。方法如下:
(1)用待测染料,按规定的染色工艺对相应织物进行染色(不要固色处理),得到该染料的色织物,裁剪成4cm×2cm大小。
(2)取一块相同规格的半制品白织物,裁剪成4cm×2cm大小。
(3)将裁剪好的白织物与色织物缝合,缝合后的组合体润湿后放在染色空白液(除染料和促染剂之外的染液)中,在规定条件下进行处理(浴比1∶50,时间30min,温度根据染料的染色性能确定)。
(4)取出组合体,洗涤,晾干,拆开组合体。
(5)用合适的萃取液将两块织物上的染料萃取剥色,通过测定萃取液的吸光度值,计算织物上染料量。
(6)计算移染指数:
三、配伍性
1.定义
所谓染料的配伍性是指两只或两只以上染料进行拼混染色时,上染速率相一致的性能。
2.解读
(1)配伍性是染料拼混使用时的重要性能。配伍性好的染料拼色染色,随染色时间的延长,在任意染色时刻,纤维上的颜色只有浓淡变化,而颜色的色相(或色调)保持不变(最大反射光波长不变)。
(2)配伍性差的染料拼混染色时存在竞染现象,随染色时间等因素的改变,纤维上的颜色色相、色光等发生改变,纤维得色稳定性、重现性差,难以对色。
(3)发生定位吸附的染料在染色时,拼色染料的配伍性更具有重要意义,染色时必须选用配伍性良好的染料,以保证染色产品颜色的稳定。例如阳离子染料对腈纶染色、强酸性染料对羊毛染色等。
3.配伍性测定
染料的配伍性试验是采用两种或两种以上的染料在同一染浴先后染色数块织物或纱线,根据染后织物的颜色深浅和色光变化来测定的。方法如下:
(1)准确称取一定质量的织物(或纱线),并将其均匀分成5份。
(2)将配制好的染液(染液按常规配制)加热至规定温度后,投入第一份染3min后取出,再投入第二份染3min后取出,重复此操作,连续染5份。
(3)染毕进行相应的后处理、晾干并进行编号。然后对比5份试样得色情况,若5份试样色相相同,仅有浓淡的变化,则说明拼色用染料配伍性能好,可以拼色;若5份试样的颜色既发生了浓淡的变化,又发生了色相的变化,说明拼色用染料不配伍,不能拼色。
(4)配伍性试验时,根据染料具体上染速率快慢,可选择不同的染色时间,若染料的上染速率慢,每份试样的染色时间可适当延长。
四、染色亲和力
1.定义
染液中染料标准化学位和纤维上染料标准化学位之差,称为染料对纤维的标准亲和力,简称亲和力。
2.解读
(1)亲和力是染料从溶液向纤维转移趋势的度量。亲和力越大,染料从溶液转移至纤维上的趋势(即推动力)越大。因此,可从亲和力的大小来定量地衡量染料上染纤维的能力。亲和力的大小用kJ/mol表示。
(2)设染料在溶液中及在纤维上的化学位分别为:
式中:μs,μf——染料在溶液中和纤维上的化学位;
,
——染料在溶液中和纤维上的标准化学位;
as,af——染料在溶液中和纤维上的活度(有效浓度)。
(3)染料从染液向纤维转移的必要条件是μs>μf,当染色平衡时,μs=μf,即得:
式中定义为染料对纤维的染色标准亲和力,简称亲和力。其数值为染料在染液中的标准化学位与其在纤维上的标准化学位的差值。
(4)亲和力具有严格的热力学概念,在指定纤维上,它是温度和压力的函数,是染料的属性,不受其他条件的影响。
3.亲和力测定
常用比移值法。
比移值是指将纤维素制成的滤纸条垂直浸渍于染液中,30min内染料上升高度(cm)与水线上升高度(cm)之比值。具体测定方法如下:
(1)将待测染料配成一定浓度(如4g/L等)的染液,取100mL置于烧杯中。
(2)取2#慢速定性滤纸裁成3cm×15cm的纸条,并在距离纸条底边1cm左右处用铅笔画一横线,作为浸渍染液时的起始标志,压平纸条待用。
(3)将滤纸条垂直吊入染液,使纸条底边画线处与染液面持平,计时浸渍30min。
(4)取出纸条后吹干,测量水线和染料线的高度(cm)。
(5)计算比移值Rf:
Rf越小,染料对纤维的亲和力越大;Rf越大,染料对纤维的亲和力越小。
五、染料的泳移
1.定义
织物在浸轧染液以后的烘干过程中,染料随水分的移动而移动的现象称为染料的泳移。
2.解读
(1)染料的泳移是轧染生产中影响染色匀染度的主要因素之一,主要与织物中的含水量、烘干工艺有关。
(2)在轧染生产中为防止泳移现象发生,保证染色匀染度,一方面根据纤维吸湿性控制合适的轧液率(不能过高);另一方面可在染液中加入适量防泳移剂,采取适当的烘干方式。
3.泳移性能测定
可参见GB/T 4464—2006《染料泳移性的测定》。
六、染料的力份
1.定义
染料生产厂指定染料的某一浓度作为标准(常规定其力份为100%),其他批次生产的染料浓度与之相比较,所得相对比值的百分数即为染料的力份,又称染料强度。
2.解读
(1)染料力份百分数不是纯染料的含量。
(2)不同企业生产的染料,因标准染料浓度没有严格规定,因此力份百分数标注相同的同一品种染料,其中纯染料的含量不一定相同,即使同一个企业生产的同品种染料,因生产批次不同,染料的力份和色光也可能不完全一致。
(3)印染企业在实际生产中,对每批购入的每只染料按规定的工艺,分浅、中、深几档浓度进行单色样染色,制成单色样卡后,通过比较染色物颜色情况了解不同批次染料的力份(即打单色样)。
3.染料力份测定
染料力份测定的方法有两种。一种是利用分光光度计,通过测定标准染料和待测染料溶液的吸光度值,比较计算得到力份百分数,这种方法在染料厂常采用。另一种为对比染制单色样法,是在染色工艺完全相同的条件下,通过用标样染料(参照染料)和待测染料以相同浓度对同种纤维制品染色,对比染色物颜色,做出力份判断或计算,这种方法多用于印染厂。利用分光光度计测定染料力份的方法如下:
(1)配制浓度不大于0.01g/L的染料稀溶液(符合朗伯—比尔定律要求)。先准确称取0.25g标准染料和待测染料各一份,溶解后,转移并定容至250mL,该染料溶液浓度为1g/L。分别吸取1mL,稀释定容至100mL,得到需要的染料稀溶液。
(2)选择染料的最大吸收波长,以溶剂作参比(如蒸馏水),测定标准染料和待测染料的吸光度,记为A0、A1。
(3)计算染料的力份:
(4)应引起注意的是,如果待测染料与标准染料的颜色在色光、鲜艳度甚至色相上不一致,两者不能作比较(无可比性),这可以通过比较染料的吸收光谱曲线得知。水溶性的染料以蒸馏水溶解,非水溶性的染料应选择其他有机溶剂溶解后测定。
七、活性染料染色性能指标
(一)活性染料染色特征值
1.定义
活性染料浸染时,用于表示染料的直接性、移染性(或匀染性)、固色速率(或反应活性)、最终固色率等染色特性的数值。也称作活性染料染色特征参数。
2.解读
(1)活性染料最重要的染色特征值有S、E、R和F值,它们是通过活性染料浸染两个阶段染色的上染率、固色率曲线求得的。这些特征值大小能综合评价染料的直接性、匀染性、反应性、配伍性、重现性和易洗除性等性能,并为活性染料制订最佳工艺提供较为准确的科学依据。
(2)活性染料特征值的具体含义如图1-3-1所示。
图1-3-1 活性染料浸染吸色率及固色率曲线
1—吸附率曲线 2—固色率曲线
S值即规定染色工艺下,中性盐存在浸染开始30min时(未加碱),测定的染料吸附率(第一阶段上染率)。数值越大,直接性越大,染料的上染越快,匀染性越差。S值即染料一次吸附率/直接性一般在70%~80%较好。
E值即规定染色工艺下,加碱后(第二阶段)染色达到平衡时,测定的染料最终吸附率(染料上染竭染率)。数值越大,染料的上染率越高。
F值即规定染色工艺下,加碱后染色达到平衡时,经皂煮后,测定的染料固色率(最终固色率)。数值越大,染料的得色量(利用率)越高。
R值即规定染色工艺下,加碱后固色10min时,测定的染料固色率与最终固色率F的比值。数值越大,染料反应活性越强,染料固色速率快,匀染性差。R值一般在15%~30%较好。
(3)活性染料特征值是在一定染色条件下得到的,染色条件和工艺的变化会引起特征值的变化。但用相同染色工艺染色,若染料的特征值相近,则染料配伍性或配伍因子RCM(Reactive dye Compatibility Matrix)良好。
(二)活性染料固色率
1.定义
活性染料染色时,与纤维发生共价键结合的染料量占投入染浴中染料总量的百分比。
2.解读
(1)因为活性染料水解及浮色等原因,活性染料固色率始终比上染率低。提高活性染料固色率是活性染料染色中追求的终极目标。
(2)提高活性染料固色率的途径有两种:一方面,从染料结构上加以改进提高固色率,如染料分子结构中含有两个或两个以上的活性基团(目前应用较多的一类,中温型活性染料多含有两个相异活性基);另一方面,在染色工艺上加以控制,如为减少染料水解,固色碱在染色后期加入,加入固色碱的量不能过多(pH≤11);浴比不宜过大,否则会造成水解染料增多,降低染料的利用率;染色时加入中性电解质促染等;在工艺温度方面可低温染色、高温固着,提高固着率。
3.固色率测定
可以采用洗涤法和剥色法进行测定,洗涤法测定固色率易于操作。即纤维经染色后,用分光光度计测定其残液中以及皂洗液中染料含量,与原染液中的染料含量对比,求出固色率。方法如下:
(1)按所制订的处方计算0.5g棉织物试样需用的染化料质量,并称取两份完全相同的染料(染料要精确称取或吸取,两份相差不大于0.0004g),分别配置A、B两个相同的染浴,放入同一水浴中。
(2)A染浴不加试样,但其操作均按B染浴规定进行。当B染浴中的试样开始皂煮时,也向A染浴加入相同质量的皂粉,经15min后取出A染浴并冷却至室温,然后冲稀至一定体积VA,在其最大吸收波长处测其吸光度AA。
(3)B染浴加入试样,按规定条件染色。染毕取出试样水洗、皂煮(皂粉2g/L,93~95℃,15min,浴比1∶25)、水洗(用少量的水多次洗至不掉色为止)。然后将洗液、皂煮液与染色残液合并,冲稀至一定体积VB,在其最大吸收波长处测其吸光度AB。
(4)按下列公式计算染料的固色率:
式中:X——染色残液中(包括洗涤液、皂煮液)中的染料量(以占总量的百分率表示);
VA——A染浴冲稀后的体积;
AA——A染浴冲稀后的吸光度;
VB——B染浴冲稀后的体积;
AB——B染浴冲稀后的吸光度。