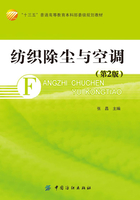
第二节 纺织环境治理的方法
一、防止纺织粉尘燃爆的措施
1.粉尘爆炸的条件 粉尘爆炸必须同时具备三个条件:粉尘悬浮在空气达到爆炸危险浓度,具有足够的空气供氧充足,接触火源。爆炸危险浓度由下限和上限构成,随粉尘的类别而异。在封闭的系统中,低于或高于爆炸危险浓度范围都属于安全范围。除尘系统是粉尘起爆的危险场合。一般纺织厂都有通风换气装置,粉尘周围气流畅通,有足够的助燃氧气,蕴藏着起火的危险性。引爆火源有电气火源(电气火花、静电火花和雷电)、高温火源(高温物体表面和辐射热)、力学火源(冲击摩擦和绝热压缩)和化学火源(明火和自燃起火)等。纺织粉尘爆炸大多是由明火、静电火花、冲击、摩擦和自燃起火等火源引爆的。例如,粉尘进入除尘系统的输尘风管和滤尘器时,粉尘在与管壁、化纤布袋的摩擦中易产生静电,由于大量纤维尘堆积在滤布表面上,达到一定厚度时,静电压增高可导致产生火花。又如,吸尘装置将螺钉、螺帽或铁丝、铁块吸入输尘管道,进入风机和滤尘设备,金属间撞击时会产生火花。再如,除尘系统的动力、照明设备及其电线,由于安装不良,或年久失修,电线裸露等原因造成短路火花。还有,粉尘进入尘室,由于长时间沉积慢慢出现氧化反应而造成自燃起火,甚至引起粉尘爆炸。此外,电动机表面温度升高到纤维尘的最低着火温度时,纤维尘会自燃起火。从以上分析可以看出,粉尘爆炸必须同时具备的三个条件中,第二条总是具备的。因此,防火防爆应以降低系统空气含尘量和杜绝火源为工作重点。
2.防火防爆措施
(1)在工艺设备方面,应采用不产生粉尘或少产生粉尘的操作方法和机器结构,缩短工艺流程减少粉尘散发量。密闭尘源,防止粉尘外溢。采用清梳联合机可使喂棉管道化,避免因落卷、运卷和上卷等工序造成的棉尘外溢。采用装有排风除尘装置或巡回吹吸清洁器的清棉机、梳棉机、并条机、粗纱机、细纱机等机械。
(2)在除尘系统设计方面,更应采取多项而有效的措施。除尘系统划分以独立的小系统为好。与空调系统连接利用回风时需设置防爆、泄爆装置。严格核算滤尘设备内的粉尘浓度,使其控制在爆炸浓度下限以下或爆炸浓度上限以上。系统排风量要保证其风管内的含尘浓度不超过爆炸浓度下限的50%。对于以收集粉尘为目的的输送管道,其含尘浓度应高于粉尘浓度爆炸上限,并将所收集的粉尘进行压紧、打包。应连续排尘,使粉尘不至于长时间停留在除尘系统内。输尘管道应尽量短,以减少积尘。在粉尘多的管网上应加装金属捕捉器,以防止产生火源。除尘系统风机的电动机应选用表面温度低的电动机,必要时采用防爆型,最好将电气设备和电动机放在除尘室之外。通风管道、空调设备的表面保温材料应采用不燃材料。
(3)在设备管理方面,必须加强对除尘设备、除尘室内的电气设备和线路的维修。经常检查风机是否缺油,避免因干摩擦发热引起火灾。除尘系统各金属部件均应接地,消除静电现象。及时清理散落在设备上、车间围护结构上的粉尘,以免因氧化分解反应而导致自燃起火。滤尘袋的粉尘要及时震落,并及时清理灰斗内的积尘。在车间内严禁吸烟,加强尘室附近气焊、电焊时的安全防火工作。各除尘设备和消防系统应有专人负责安全工作,经常检查消防器材是否处于完好状况。
(4)在纺织厂房设计方面应满足防火防爆的要求。亚麻厂的除尘室应布置在直接对车间外开门窗的附房或独立建筑物内,除尘室建筑应采用框架结构,严禁采用砖墙承重的混合结构。现有砖墙承重的混合结构的除尘室,应采用钢筋混凝土框架结构予以加固。棉纺厂滤尘室的门窗应直接开向室外无人经常走动的地方,滤尘室也应采用框架或砖墙承重结构,严禁用木结构建筑。通风设备房间的围护结构,必须按建筑物耐火等级进行设计。除尘室的上面不允许布置生产车间、辅助车间和生活间。除尘室内不允许设置办公室和休息室。
(5)在火灾报警及预防方面,应提高准确度和减少报警滞后时间。在清棉机内应安装金属检测器,使混在纺织原棉中的金属尽早排除。在滤尘室内或滤尘设备上应安装火警自动报警器,并在报警的同时能自动停止风机,自动开启灭火装置。采用泄爆装置及防火闸门、防火墙等措施。
二、防止纺织粉尘向车间扩散的措施
局部除尘系统与工艺设备相结合,防止粉尘向车间扩散。纺织、印染、化纤工厂中,凡是有集中散发灰尘处和大量散发水汽、有害气体及烘房等地方都应设有局部排风设备(如排气罩和密封罩等),以抽除热量、湿量和灰尘量以及其他有害气体。防止粉尘散入车间最有效的方法是在尘源直接用局部排风方法进行排尘,它所需要的风量小,效果好,应优先考虑。因此,要减少车间工作区含尘量,重要措施之一是局部除尘系统与工艺设备相结合,尽量使工艺设备密闭,增加必要的吸尘、滤尘装置,控制尘源。工艺设备的密闭,实质上是一种防止粉尘扩散的隔离措施,同时为吸风除尘创造条件;而局部除尘的目的是在密闭罩内造成一定的负压,防止粉尘逸散至工作区。近年来新型纺织机械一般都有防尘、吸尘、滤尘设备。
现代化的开清棉机是完全封闭的,机台之间的纤维材料由气流输送,并且在喂棉部分设计吸尘罩进行局部排风,防止粉尘逸出。由于棉箱、打手下部的落棉采用连续或间歇式吸落棉系统,大大减少了向环境的散尘量。高效能梳棉机在除尘方面有许多具体措施,一般都备有完整的吸尘除尘设备,采用全封闭式机台。在并条机速度加快的情况下,为防止游离纤维的散失,应将牵伸机构及卷条部分全部罩起来,并装上完整的吸风系统。粗纱机的牵伸和卷绕部分也应有吸风装置,防止游离纤维及飞花往车间扩散。在转杯纺纱机的纺纱头部分应封闭起来,并装备完善的吸尘、滤尘系统。
三、降低车间含尘浓度的措施
加强全面通风,降低车间含尘浓度。在纺织厂的梳棉、并条、粗纱、细纱、络筒、整经、织布、整理等车间里,如果生产条件的限制,不能采用局部排风,或者采用局部排风后车间空气含尘浓度仍超过卫生标准,在这种情况下应加强全面通风。全面通风就是对整个车间进行通风换气,用新鲜空气或混用部分过滤后的回风把整个车间的有害物浓度冲淡到最高容许浓度以下。利用全面通风排出粉尘,实质上是稀释车间空气的含尘浓度,将车间内的粉尘浓度稀释到卫生标准规定值以下,所以有时也称稀释通风。
在开放型的纺织机械上,如环锭细纱机、捻线机、络筒机、整经机、浆纱机直至织布机,尘源的散尘情况比较复杂,无法使用封闭式集中吸尘装置。络筒机和整经机的棉尘主要是从退绕时的纱线线圈中以及管纱上部的锥面上散发出来,而散发出来的部分棉尘又趋向于伴随经纱层一起缠绕到织轴上,当经纱退绕时,棉尘又散发出来。在细纱机散尘量中,牵伸部分散发的粉尘占80%~85%,卷捻部分散发的粉尘占15%~20%。另外,还有大面积敞开的地方,如棉卷、棉网、棉条、粗纱、细纱等半成品,是无法采用局部排气罩的,它们在运输过程中不断有灰尘散发出来。目前在这些工序中,主要是通过改进和完善车间通风系统,用全面通风方法,即增加车间换气次数来降低空气含尘浓度。所谓车间换气次数,就是通风量与车间的体积的比值。表2-2为棉纺织厂主要车间全面通风换气量设计参考值。
表2-2 棉纺织厂主要车间全面通风换气量设计参考值

四、控制车间空气环境的措施
合理组织车间气流,控制车间空气环境。纺织厂各车间的气流组织是否合理,与厂房形式、跨度大小、车间面积和送排风口的类型和尺寸及布置方式等因素有关。纺织工厂里常用的气流组织有下送风上排风、上送风集中侧排风、上送风下排风等几种形式。
对某些同时散发有害气体、余热和粉尘的热车间,可采用下送风上排风的气流组织方式。清洁空气从车间下部进入,先进入工人操作区,然后带着有害气体和粉尘由设在车间上部的排风口排出。这种气流组织的特点是符合热车间的热流线分布规律,且新鲜空气在途中受污染的可能性较少。但是,对于车间下部散发粉尘量多的场合,下送风上排风的气流组织会造成纺织粉尘飞扬,故不宜采用。
上送风集中侧回风的形式在有些老厂的技术改造中常被采用。在改造过程中因无法布置回风管路,只能在空调室回风窗直接集中侧回风。在这种气流组织下,大量回风穿过车间进入回风窗时,车间内会形成较强的高度在纺织机械顶部左右的横向气流。横向气流不仅使含尘空气污染了横向流过的区域,且因空气横向流动受机器阻碍而形成许多涡流区,花毛和粉尘到处飞扬,致使纺织生产受到影响。这种横向气流,特别是超过30m以外的回风,在某种程度上又破坏了车间上部的均匀送风,会造成车间区域温差增大。
上送风分散下排风的气流组织形式常应用于发热量大、粉尘分散的细纱、捻线、织布等车间,在车肚下或车弄中设排风口。细纱机产生粉尘处是牵伸卷绕部分,采用上送下排风之后,就不会有大量含尘气流流过工作区。此种送排风气流组织除使车间温湿度更加均匀,有利于排出工艺设备散热外,对消除车间气流的涡流滞止区和排出机台产生的粉尘均有利。因车间气流运动方向同棉尘靠重力作用沉降方向相一致,没有将已经沉降的粉尘又重新二次飞扬的问题。在空气中不能自由沉降的细小粉尘,也将随下排气流的方向而被排出车间。
五、控制棉尘释放的措施
用添加剂控制棉尘的释放。将添加剂加到纤维材料上对减少车间空气的棉尘是有效的,一般能使纺织工厂各工序的平均含尘量降低39%~59%。常用的添加剂为矿物油加表面活性剂,其中矿物油约占90%。添加剂用量一般为棉花重量的0.1%~0.4%。添加剂应较早地在开棉工序上加入,其目的是提高添加剂在纤维材料中分布的均匀度。可将添加剂加于棉箱给棉机后边的输送帘上的原料内,或在管道内将添加剂加到纤维材料上。
使用添加剂虽然可控制棉尘,减少空气中和机台上的飞花,但也有不良作用。如可能会在并条机的罗拉上形成残渣。气流纺的纱线强力和坚韧性明显降低。在梳棉工序会出现棉网松坠或漏底网眼。在并条机也会出现缠绕胶辊现象。而添加剂会渗入纤维,油脂不易除掉,加工困难。因此,只有当其他除尘措施不易达到较好净化纺织环境效果时,才采用添加剂。