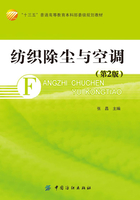
第一节 纺织工艺对环境条件的要求
在纺织工艺中,各道工序对纺织纤维性能(如强力、伸长度、导电性、柔软性、回潮率、摩擦系数等)有着不同的要求。特别是空气的温度和相对湿度与纤维的吸湿性能之间有着密切的关系。因此,必须在纺织车间里创造一个良好的纺织工艺环境条件。只有当纺织工艺在温度和相对湿度处于严格控制的环境中进行时,才可能顺利地生产合格的纺织产品。
一、纤维的吸湿性及其影响因素
纺织纤维放在车间里,会吸收空气中的水蒸气,也会向空气释放水蒸气,其吸收和释放是一个动态平衡过程。如以前者为主称为吸湿过程,如以后者为主则称为放湿过程。纤维材料在空气中吸收或释放水蒸气的能力称为吸湿性。
纤维的吸湿机理是比较复杂的物理化学现象。一般认为,吸湿时水分子先吸附停留在纤维表面,吸附水分子的数量与纤维的结构、表面积和周围环境有关。然后水分子向纤维内部扩散,被纤维内大分子上的亲水性基团吸收。其他水分子还会重叠在已被吸收的水分子上,松松地保持着。
通常采用回潮率来表示纺织纤维吸湿程度的指标。回潮率是指纺织纤维中所含的水分质量对纺织纤维干质量的百分比,其计算式如下:

式中:W——回潮率;
Gsh——纤维吸湿后的质量,g;
Gg——纤维不含水分时的干质量,g。
当空气条件一定时,经过6~8h或更长时间后,单位时间内被纤维吸收的水分子数等于从纤维内脱离而返回大气的水分子数时,纤维的回潮率会趋于一个稳定的平衡状态值。处于平衡状态时的纤维回潮率就称为平衡回潮率。放湿过程达到的平衡回潮率会大于吸湿过程达到的平衡回潮率,这种现象称为纤维的吸湿滞后性。图1-1所示为纤维吸湿、放湿过程中的回潮率—时间曲线。由图1-1可见,开始时回潮率变化幅度较大,随着时间的延长,回潮率逐渐趋于一个稳定的值。

图1-1 纤维吸湿、放湿过程的回潮率—时间曲线
影响纤维回潮率的外在因素有周围空气的温度、相对湿度和放置时间。另外,当纤维周围空气流速增加时,纤维的平衡回潮率会有所下降。
温度对纤维吸湿性影响的一般规律是温度越高,平衡回潮率逐渐降低。这主要是因为在相对湿度相同的条件下,空气温度低时,水分子热运动能量小,一旦水分子与纤维亲水基团结合后就不易再分离。空气温度高时,水分子热运动能量大,纤维大分子的热振动能也增大,削弱了水分子与纤维大分子中亲水基团的结合力,使水分子易于从纤维内部逃出。温度高时存在于纤维内部空隙中水的饱和压力也随温度的上升而升高,会加速水分子气化。但在高温、高湿的情况下,由于热膨胀等原因使得纤维的平衡回潮率反而略有增加。
纤维在相对湿度一定时,平衡回潮率随温度变化的曲线称为纤维的吸湿等湿线,如图1-2所示。纤维的吸湿等湿线表明了平衡回潮率随温度变化的情况。

图1-2 羊毛、棉的吸湿等湿线
相对湿度对纤维吸湿性影响的一般规律是相对湿度越高,平衡回潮率越高。这主要是因为在一定温度条件下,相对湿度越高,空气中水气分压力越大,单位体积空气内的水分子数目越多,水分子到达纤维表面的机会越多,纤维吸附的水分子就较多。羊毛的吸湿性最高,其次是粘胶纤维、蚕丝、棉纤维。
纤维在温度一定时,平衡回潮率随相对湿度变化的曲线称为纤维的吸湿等温线,如图1-3所示。纤维的吸湿等温线表明了平衡回潮率随相对湿度变化的情况。

图1-3 棉、毛纤维的吸湿等温线
二、温度对纤维性能的影响
温度的高低能反映物质微观粒子运动的强弱。在纤维回潮率一定的条件下,当空气温度升高时,纺织纤维受热使纤维分子热动能增高,因而纤维分子间结合力减弱,纤维拉伸断裂强度σ降低,断裂伸长率ε增大、拉伸断裂强力P0、拉伸初始模量下降。温度对蚕丝和羊毛的拉伸性能的影响如图1-4所示。

图1-4 温度对蚕丝和羊毛的拉伸性能的影响
由于纺织纤维属不良导体,比电阻随温度的升高而降低,故空气温度升高后纤维导电性能会有所增加。对于大多数纺织纤维来说,温度每升高10℃,其比电阻约降4/5。另一方面,纤维内部的水分子在高温时活动强烈,离开纤维的概率就大,因而回潮率减小会使得比电阻升高。
随着环境空气温度的升高,纤维内部大分子的运动活力提高,由分子运动传递的热能也会增加,纤维的导热系数就会增加。表1-1中的几种纤维集合体导热系数与温度的关系说明了纤维的导热系数随温度升高而增加的趋势。
表1-1 几种纤维集合体导热系数与温度的关系

几乎所有的纤维的弹性都会随温度的升高而增加。这是因为当温度较高时,分子热运动能较大,大分子链节的旋转、大分子链的伸展和皱曲、基原纤方向和位置的调整移动等都比较容易,结晶区的结合力也较弱,黏滞性减小,因而缓弹性变形较大并发展较快。
对于棉纤维,因其表面具有棉蜡而要求温度控制在19~27℃之间。使棉蜡处于软化但不发黏状态,容易分离成单纤维,有利于除杂和牵伸,纺成优质条干的棉纱。对于羊毛,因其表面有毛脂以及加工时所加入的乳化油剂,纤维性能均会受到温度的影响。
三、相对湿度对纤维性能的影响
空气相对湿度对纤维性能的影响取决于纤维分子中亲水性基团的多少。对于天然纤维(棉、毛、丝、麻)或利用自然界的纤维素制成的再生纤维(粘胶纤维、再生蛋白纤维等),其外皮层和主体层都含有亲水基团的羟基OH、羧基COOH和酰胺基CONH,并且有多孔性。因此,当环境空气中的水汽分压力变化时,纤维会出现吸湿或放湿反应。故相对湿度对这类纤维的性能影响较大。相对湿度增高时,这些有亲水性基团的纤维将吸湿,水分子被吸入纤维内部,使纤维分子间距离增大,故纤维的初始模量下降,柔软性、延伸性均增加。摩擦系数、导电性亦是增加的。对于动物纤维和再生纤维,因水分子进入纤维内部后增大了纤维分子间距离,故强力降低;而对于植物纤维,由于水分子被纤维吸入非结晶区,改善了分子的整列度,强力反而有相应的增强。

图1-5 合成纤维表面的吸湿
对于利用煤、石油、天然气等作原料,经过化学作用合成的合成纤维(维纶、锦纶、腈纶、涤纶、氯纶、丙纶),由于其亲水性基团极少,吸湿性就差甚至没有吸湿性。合成纤维的绝缘性能强,因此在纺织工艺过程中极易因摩擦而产生静电,妨碍工艺生产的正常进行。通常会加入润滑性能好并具有吸湿性能的抗静电油剂,使其表面摩擦系数减少并具有一定的吸湿性能。其吸湿情况如图1-5所示,第一批水分子由纤维表面为数不多的亲水基团直接吸住,以后的水分子可重叠在已被吸收的水分子上,所以合成纤维有外吸湿纤维之称。由于吸湿、放湿只在合成纤维的表面上进行,故只对纤维的导电性能和回潮率有影响,而对纤维的强度和伸长率几乎不受相对湿度的影响。
图1-6中示出几种纤维在不同相对湿度下纤维强度的变化情况。在纤维强力方面,锦纶、羊毛和蚕丝纤维随着空气相对湿度增加而回潮率增加时,其强力是下降的。这是因为水分子进入纤维内部无定形区,减弱了大分子间的结合力,使分子间容易在外力作用下发生滑移。粘胶纤维由于大分子聚合度和结晶度较低,纤维断裂主要表现为大分子间的滑脱,而水分子进入后对大分子结合力的减弱很显著,因此吸湿后强力下降非常显著。但是空气相对湿度增加时植物纤维(棉、麻)吸湿后强力却是增加。这是由于棉和麻纤维的大分子聚合度、结晶度较高,纤维断裂主要表现为大分子本身的断裂,而水分子进入后对大分子间结合力的减弱不显著,并且可将一些大分子链上的缠结拆开,分子链得以舒展和受力分子链的增加使得纤维强力增加。合成纤维由于吸湿能力较弱,所以相对湿度增加后强力降低不显著。

图1-6 相对湿度对纤维强度的影响
空气相对湿度减低时,纺织纤维将放湿回潮率降低,纤维分子间距离缩小而结合力强,延伸性、柔软性均降低,摩擦系数减少,导电性能亦差。
由于相对湿度越高纤维的回潮率越高,纤维内部的水分就会越多,纤维导热系数就越大,而且这个变化要比温度引起的变化大得多。导热系数上升,冰凉感增加,纺织纤维的保温性能下降。
相对湿度对纤维的弹性回复率的影响因纤维而异,粘胶纤维和醋酯纤维的弹性主体上是下降的,蚕丝、羊毛、锦纶的弹性主体上是上升的,棉纤维的弹性则是交叉的。
四、纺织工艺对温度和相对湿度的要求
从上述情况可知,空气的温度和相对湿度对纤维性能的影响很大,特别是相对湿度对回潮率的影响尤为重要。
在纺织企业各个不同的车间里,为了纺织生产的顺利进行,纤维的回潮率就会有所不同,需互相配合好前后工序的回潮率。例如,纯棉纺各工序产品控制的回潮率范围见表1-2。由于纺织机械对纤维的加工情况不同,有时还要精确控制纤维在纺织工序中是吸湿还是放湿,可参考表1-3安排。对于吸湿过程的车间,相对湿度就应较前一工序上调一些;对于放湿过程的车间,相对湿度就应较前一工序下调一些。另外,有些纺织器材如胶辊、梭等性能也会受到温度和相对湿度的影响。故各个车间所要求的空气温度和相对湿度亦不相同。
表1-2 纯棉纺各工序产品回潮率控制范围

表1-3 纺纱工序中吸湿、放湿的安排

1.棉纺织工艺 清花车间要求相对湿度较低。清花车间的任务是把棉块开松并除去杂质。相对湿度低可以使得原棉的回潮率减小,开棉效率高、除杂顺利,棉卷均匀度好。但相对湿度过低时棉纤维脆弱易断,影响成纱强力,且落棉增多,空中飞花也多,制成的棉卷会太膨松。
梳棉车间要求相对湿度与清花车间相近或稍低。让棉卷在梳棉车间有少量放湿,使纤维呈内湿外干状态。外干有利于棉束、棉块分梳成单纤维状态,且有利于除杂。内湿则有利于棉纤维的强力和延伸性,使纤维不易被梳断,并且可减少静电现象。如果相对湿度过高,则会造成许多不好现象,如棉卷粘层、生条均匀性差、纤维分梳困难、杂质不易清除、棉结增加、棉网下垂、断头增多、纤维黏附罗拉、针布生锈等。
并粗车间要求相对湿度较高。相对湿度增高可使纤维的柔软性和抱合力增加,粗纱容易获得稳定和均匀的捻度。纤维强力也有所增加,有利于提高罗拉对纤维的控制能力,使纤维在牵伸过程中伸直平行。纤维中水分子增加使得导电性好,所以不会因产生静电现象而影响纤维正常的排列,条干均匀度好。如果相对湿度过低,在并条机上会造成棉条蓬松,棉网破裂,短纤维飞扬,并易产生静电吸绕胶辊;在粗纱机上会粗纱松散,飞花增多,加捻困难,断头增加,纤维间抱合力减弱而影响条干均匀及粗纱强力。
细纱车间要求相对湿度比并粗车间低些。这样使粗纱在细纱车间保持放湿状态,会使纤维内湿外干。内湿使材料柔软,易加工,易导电。外干使摩擦及粘着力小。如果细纱车间相对湿度高了,纱线与钢丝圈之间的摩擦力增加会使断头率增高,罗拉胶圈表面会附着飞花导致牵伸不良而造成条干不匀、胶辊发粘甚至纱线缠绕胶辊。
对于织部工艺,一般要求相对湿度比纺部高。织部的工艺包括络筒、整经、浆纱、穿综穿筘、卷纬、织造、整理等工序,大多数车间要求纱线强力好,断头少,以提高产量和质量。故一般来说织部的相对湿度宜大些。
络筒、整经车间要求保持较高的相对湿度。在络筒、整经过程中每根纱都与空气进行较长时间接触,车间里的温度和相对湿度对纱线的回潮率和强力等有较大影响。为了增加纱线的强力,并考虑到细纱经过加捻后内部的纤维不易吸湿的情况,络筒、整经车间的相对湿度一般比细纱车间高。相对湿度增高可增加纱线的强力,有利于清除纱疵使纱表面光滑,减少断头。整经车间保持稳定的相对湿度,可使纱线平稳地卷在经轴或织轴上,经受均匀的张力。
浆纱车间的任务是使经纱浸透浆液,把纱线表面耸起的纤维或毛茸黏附住,然后烘干浆液形成浆膜,以增加纱的光洁度,耐磨性和弹性并减少织造时产生的静电。充分发挥浆膜作用的前提是控制好浆纱的回潮率。若浆纱的回潮率过低,浆纱发脆易断头,这时就要求车间里有较高的相对湿度。若浆纱回潮率过高,在织布车间来不及放湿会使含浆的经纱彼此黏合,织造困难并易造成织轴发霉。含浆经纱的回潮率大小还与上浆率有关。上浆率大时,回潮率应高些,相反则小些,重浆时可适当高些。浆纱车间的相对湿度要稳定,以利于控制回潮率和上浆率。
在织布车间,织机将按一定组织、密度和宽度把纱线织成合符一定标准的织物。织机各部件的运动要尽可能减少断头率和回丝率,保证织物的品质优良。若车间空气相对湿度过低,则经纱和纬和纬纱发脆而强力降低,经受不起织机的剧烈冲击,使落浆率增大,断头增加。由于空气干燥,还会引起纬缩现象以及在经纱交织摩擦时产生静电效应,造成布面起毛影响织物的质量和外观。所以,织布车间相对湿度不宜过低,而应适当偏高。这样,纱线强力好落浆率少,断头率减少,有利于织布质量的提高。另外,还要注意控制好车间的相对湿度与经纱上浆率和回潮率的关系。
整理车间主要是修补织物疵点,将织物打包入库。织物的回潮率有一定的要求,车间的相对湿度只要符合此要求即可。
2.混纺织工艺 涤纶具有弹性好、高电阻、吸湿性很小的特点。这些特点与温度、相对湿度关系密切。如果温度低,则纤维发挺。在纺部不易成卷,胶辊胶圈等发硬打滑,造成纺纱断头。如果温度太高,则抗静电油剂容易发黏和挥发,胶辊等也较湿,纤维黏附胶辊胶圈。在织造工艺中,由于温度高会使得浆膜变软产生粘连,不耐摩擦,容易断头。如果车间相对湿度偏低,则纤维刚挺,易使卷层蓬松,层次不清。涤纶表面在纺丝时虽加有抗静电油剂,但在湿度低时纤维与机件摩擦仍会产生静电,使纤维吸附卷绕机件。在织造工序中则因摩擦产生的静电使纱线相互排斥或吸并,纤维成团聚结在综眼上。
基于以上分析,各车间在织涤纶混纺织物时,应根据不同工序确定不同的温度和相对湿度。一般涤纶纺纱,在夏季车间温度宜较棉纺工艺的温度低些,在冬季车间温度与棉纺织工艺相类似。在交织化纤织物的车间,由于涤纶清洁杂少,但极易产生静电,故应以减少静电为主。在纺部清棉车间相对湿度宜大,有利于减少静电,纤维柔软成卷也好。以后各道工序宜在逐步放湿状态下进行,即车间相对湿度宜逐渐降低。如果纤维在以后工序中吸湿的话,则因水分仅吸附于纤维表面,易粘胶辊等部件,增加断头。在织造工序,应根据浆料成分控制相对湿度。如果采用聚乙烯醇浆料(PVA)给涤纶上浆,成膜性能良好,浆膜强韧耐磨性好,故相对湿度可低些,控制在62%~68%为佳。
腈纶、锦纶等合成纤维均具有高电阻和吸湿性差的特点,与涤纶相似易起静电,加抗静电油剂后吸湿时水分吸附在纤维表面。这些纤维混纺时的车间温、湿度要求与加工涤纶相似,即清棉车间的相度对湿度要大,以后各道纺纱过程均以放湿为宜,车间的相对湿度应逐渐降低。而织造车间同样应视浆料性质而定。
维纶为聚乙烯醇纤维,有亲水性基团,是合成纤维中回潮率较高的一种纤维,但与天然纤维相比仍然较低。导电性虽比涤纶、腈纶等强,但比天然纤维差,在摩擦时仍易起静电,并难以消失。对于维纶混纺工艺,各车间的相对湿度基本上与棉纺织工艺相似。对温度的要求,因加有抗静电油剂的关系,在夏季车间的温度比棉纺织低些,在冬季则比棉纺织略高一些。织造车间的温度和相对湿度也应根据浆料成分而定。
粘胶纤维为纤维素纤维,吸湿性强,延伸性大,摩擦所产生的静电现象比较轻。但由于粘胶纤维表面光滑,抱全力差。根据这些特点,在前纺车间为了成卷成条良好,相对湿度要求比棉纺工艺低些。在织造工序,若采用的是纯淀粉浆料,由于它与棉纤维及粘胶纤维结合较好,故相对湿度宜在68%~76%;若采用羧甲基纤维素浆料(CMC)或海藻浆料,则相对湿度要比棉织工艺降低些,为66%~68%。粘胶纤维对温度的要求与棉纺织工艺相近。
3.毛纺织工艺 动物纤维在含水率增加后变得比较柔软,容易伸长,但强力反而降低,与植物纤维的特性不大相同。羊毛的摩擦系数与鳞片的顺逆向有关,逆向时摩擦系数大。在和毛间及精纺厂的混条机上,为了减少摩擦系数以利于梳理和纺纱,通常要加油润滑。
羊毛在干燥时的导电性能比合成纤维要好些,但比棉纤维差,故比棉纺厂静电现象严重。其所含水分对导电性能影响极为显著。所以,为消除静电现象,毛纺厂的相对湿度应比棉纺厂高些。这样,由于羊毛的吸湿性很大,且不易发生湿粘胶辊和罗拉,有利于消除静电和保持纤维的柔软性。毛纺厂的毛条库和粗纱库的作用就是使毛条和粗纱在库存时进行充分的吸湿,以消除毛纤维在加工过程中的静电和弹性。毛条和粗纱的含水量充足,可使毛条在进入前纺车间,或粗纱进入细纱车间的后续工序中能逐步放湿。逐步放湿的结果使纤维内湿外干。纤维内湿有利于在加工过程所产生的静电散逸,外干则表面滑爽不粘绕胶辊,以达到提高纱线产量和质量的目的。在绒线厂的细纱车间,由于其捻度较少,强力低,故更应注意控制适宜的相对湿度。
由于羊毛须加油后进行纺纱且羊毛本身亦有油脂,所以对温度有一定的要求。在冬季天冷时,因羊毛脂凝固,纤维容易凝聚在一起不易拉开,故冬季选毛车间须要采暖升温。在梳理与纺纱车间,如果温度较低,油的润滑性能差,纤维的摩擦系数大,柔软性也差。为使毛纺工艺能正常进行,冬季温度须维持在20℃以上。在夏季时各车间的温度应在32℃以下,以免高温使油脂发黏,出现粘绕胶辊现象。
至于毛织工艺的温度控制范围,可与棉织厂相类似。而相对湿度通常控制得比棉织厂低些,这是因为毛纤维的延伸性、回弹性均较棉纤维优越,且羊毛纱线不耐虫蛀和不耐霉。
4.绢纺织工艺 绢纺厂的开茧车间宜维持较低的相对湿度,以利于开茧机抓开废茧和清除杂质。其余车间的相对湿度均比棉纺厂高些。制绵车间的主要任务是梳理丝纤维,并把丝中残留的蛹屑除去。丝纤维在分梳时与机件间相互摩擦,极易产生静电,虽然丝纤维的吸湿性比棉纤维略大,但导电性远比棉差,则产生的静电现象就十分严重。扰乱纤维的平行,影响梳理,并吸绕罗拉与锡林。故制绵车间的相对湿度宜控制得较高些。要预先给湿,使丝纤维的回潮率达11%~13%,才能送入制绵车间进行制绵。但相对湿度亦不宜太高。因太高后丝纤维吸湿过多而黏附,将不利于梳理清杂,而且丝纤维也因湿度大而强力低。制绵车间相对湿度宜在75%~80%范围内。
在制条、粗纱车间,相对湿度应该控制得比制绵车间低些。这是因为在制绵车间出来的丝纤维的回潮率较高,导电性已较好,不会产生静电现象。如果维持稍低的相对湿度则丝纤维可处于放湿状态。由于丝纤维放湿的结果,纤维表面干燥滑爽,不会粘绕胶辊,有利于制条与粗纱工艺的进行。在细纱车间,相对湿度又应稍降低些,使丝纤维继续放湿,呈内湿外干状态。
绢织厂的相对湿度比棉织厂还要高些。因为相对湿度低了,绢丝在交织时发生摩擦比棉纱更易产生静电。以致在织造过程中纡子塌纬,织物起毛,吸附灰尘,浆膜发脆脱落引起断头,等等。这不利于丝织物表面的光亮平挺。
5.麻纺织工艺 麻纺有黄麻纺、苎麻纺、亚麻纺之分。麻纤维的共性是纤维比较粗硬,柔软性差,不易伸长,吸湿性强、摩擦系数大。为了增加麻的柔软性,其加工过程中增加了软麻机加工工序。在软麻机的前段设有许多轧辊以除去杂质,因而要求干燥些有利于轧辊除杂。在软麻机后段设有给油给湿装置以增大麻纤维的吸湿率,从而增加纤维的柔软性和强力,降低摩擦系数,增加导电能力。为了维持麻纤维有较高的吸湿率,在软麻机以后的各工艺过程中,车间空气的相对湿度比棉纺工艺要高些。黄麻纺要求达75%左右。麻织厂的相对湿度也要求比棉织工艺高些。
在夏季,麻纺厂的温度要求比棉纺厂低些,以减少麻纤维上残留胶质因温度高而发黏的现象。在冬季,各车间的温度不能太低,因温度过低使纤维的柔软性差,不利于纺纱工艺过程进行。麻织厂的温度要求与棉织厂相似。
6.针织工艺 针织工艺要求纱线容易弯曲成圈,少断头。对纱线的要求是柔软、光滑、强力好以及纱线通过钩针时摩擦力小。
如果相对湿度低于40%则纱线的强力会大降低,在织造过程中易断头。由于断头多,会形成洞眼和脱套等。在成圈过程中,因纱线干燥不柔软而成圈困难。纱线干燥会使钢片与纱线的摩擦系数减少,台车上的弯纱轮弯纱时不易将线圈带至针钩内,产生漏针的疵点。对于织造锦纶袜工艺,由于相对湿度小锦纶丝发硬不柔软,断头多,静电现象严重。对于整经车间在处理化学纤维时,相对湿度低会使静电现象严重,丝线相互排斥。混纺的纱线还会出现极性相反的电荷,纱线间发生相互吸引的现象,造成牵引困难、断线和残疵。
如果相对湿度过大,则机件易生锈。而且纱线弹性差,易伸长,织出的织物偏薄。另外,纱线与钩针间及机件间的摩擦系数大,易断纱断针。
所以,针织厂在编织棉纱类内衣时,其相对湿度控制在65%~75%为宜。对于编织合成纤维作外衣用的经编机车间,相对湿度宜在60%~65%范围内。整经车间因无成圈机构,相对湿度控制范围可适当宽些。
温度对针织工艺的影响比相对湿度的影响小些,但要注意波动幅度的控制。若温度波动幅度太大,由于金属机件的热胀冷缩,会引起机件间的间隙变化,使织出的织物线圈不均匀。
五、纺织工艺对气流组织的要求
纺织车间气流组织对车间生产工艺的影响也很重要。纺织车间里不合适的气流会产生大量飞花,影响生产环境和空气含尘量。而工作区的风速又是保证纺织工艺质量的重要因素。例如,在梳棉、并条、粗纱、细纱的牵伸区,风速过高会引起附加牵伸,造成产品的质量不稳定。采用合理的车间送排风方式和气流组织及工作区的风速,可以减少车间飞花的产生和飘逸,降低工作区含尘浓度,确保工作区的风速稳定和温湿度均匀。
对于产生飞花较多的纺部车间,由于大多数发热量均来自2m以下的机器和人员,热空气的密度较低会形成自然上升的气流。这一上升气流会夹带飞花和灰尘纷纷向上,再加上其他机械部件造成的空气扰动,是造成生产环境恶化的主要原因。此时,这类车间应采用上送下排式气流组织。上送下回式气流组织是通过车间上部均匀布置送风口送风、车间地坪上布置回风口回风的送回风方式来实现的。整个车间形成自上而下的主导气流,可以抑制粉尘飞花的飞扬,使工作区的粉尘和飞花尽快下降排出室外,有利于产品质量的提高和车间环境的改善。
当纺织车间回风长度小于30m时,上送侧回式气流组织也是纺织厂常用的一种送回风方式。在车间上部均匀布置送风口送风,车间附房空调室的侧墙上布置回风窗的方式回风,整个车间形成上部送风水平流向空调室的气流。该送回风方式的车间温湿度差异较大且含尘浓度分布不均,会出现向空调室方向温度逐渐升高、含尘浓度增大的趋势。但是系统设备简单,可利用空调风机的吸力直接从车间侧窗抽取回风,回风通过安装在侧窗上的回风网进行过滤,节省送回风能耗和空调室占地面积。
对于飞花较少、生产工艺要求相对湿度较高的织布、络筒、浆纱、气流纺、丝织车间等,可以采用下送上回式气流组织。下送上回式气流组织是采用在地面上送风、车间上部回风的送回风方式来实现的。这样既可以在工作区维持一个相对湿度较高、温度较低的环境,同时车间自然对流气流和送风气流一致,上部非工作区允许有较高温度,从而减少送风量以节约能源。
对于生产工艺要求相对湿度较高的织布车间,可以采用大小环境分区空调气流组织形式,采用专门的送风口,直接将高湿空气送至织造区,维持一个织造区高相对湿度的小环境。而在人员工作区采用大环境气流组织,保证一定的相对湿度。这样一方面满足了布机生产工艺的需要,另一方面可以使织布车间人员工作区相对湿度适当降低些,有利职工健康并可节约能源。
不管采用哪种送回风形式的车间气流组织,都应该严格控制工作区风速,确保工作区减少飞花和气流稳定。主要纺织工序工作区风速见表1-4。
