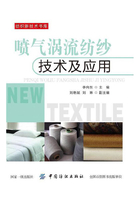
第三节 喷气涡流纺原料预处理及配棉
一、喷气涡流纺原料的预处理
不同纤维中由于天然纤维含有亲水性基团,吸湿等温线与放湿等温线不重合,同样相对湿度条件下,放湿过程纤维回潮率要高于吸湿过程纤维回潮率,因此,应根据纺纱工艺要求和质量要求,合理掌握和控制好纺纱生产过程中不同工序的温湿度。原料的预处理是指针对原料在投产之前对纤维进行预先处理,以保证纤维能在一定的回潮率或者适纺条件下投入纺纱工序,从而保证纤维顺利成纱,降低纤维在生产过程中的消耗,品质能得到提升。由于目前在喷气涡流纺生产中使用纤维类别多,性能差异大,故为提高纺纱可纺性,以生产出品质优良的各种喷气涡流纺纱线,纤维预处理工作十分重要。
从纤维性能分析,成纱中需要特别处理的纤维主要有两类,一类是刚性较强、吸湿性能较差的纤维;另一类是吸湿性强,但表面光滑、抱合性较差纤维,这两类纤维在纺纱生产中均易产生静电缠绕罗拉、胶辊,增加断头,降低生产效率。因此,纺前预处理的重点是要减少静电荷,提高可纺性。本节对不同种类纤维的预处理过程分别进行介绍。
1.天然纤维的预处理
棉纤维进厂若回潮率偏小,应考虑在投产之前在分级室进行加湿平衡。加湿区域的湿度设定以及加湿时间可根据实际进行要求。棉纤维的湿度对纤维强力影响较大,强力在相对湿度逐步增加时,纤维强力逐步增加。相对湿度在60%~70%时棉纤维强力增加较明显,但湿度超过80%时,强力增加率则很小。同时,相对湿度对纤维伸长影响较大,加湿后的纤维由于分子之间的距离增大,在外力作用下易产生相对位移,因为纤维的伸长也随着湿度的增加而随之增大。棉纤维在适度的相对湿度条件下,纤维横断面膨胀,延展性增加,纤维柔软,黏附性和摩擦因数增加,纤维牵伸过程中更容易控制,从而提高了成纱的条干均匀度。适度的回潮也会使绝缘性能下降、介电系数上升,从而有利于消除纤维在生产过程中的静电排斥现象,增加纤维的抱合力。但是不是一味地增加湿度就是最合理的,湿度过大会造成纤维之间摩擦力过大,纤维之间纠缠不易梳理,从而形成棉结。
亚麻纤维由于其独特的性能,在投产之前,需要在容器中加适量的水,对纤维进行4~6天的闷料,以保证纤维充分吸湿。对使用亚麻纤维纺纱时,因纤维刚度大,在常态温湿度下的打击和梳理易造成纤维脆断,影响质量与制成率,故必须采用水和抗静电剂对亚麻进行养生处理,并将喷洒油剂后的亚麻在25℃下存放96h,并要多次翻仓以降低纤维黏结。
羊毛、羊绒纤维需要在投产之前加入一定的抗静电剂和水进行预处理,以达到减轻纺纱过程中产生的静电现象,提高适纺性能。
2.化学纤维的预处理
对使用莫代尔、竹纤、天丝原料时,由于纤维表面较滑,在生产过程中也易产生静电,生产前必须进行给湿处理,其方法是将原料进车间开包存放24h,并在抓棉机上进行喷雾给湿,使原料含水率达到13%左右,使整个纺纱过程处在放湿状态下生产。天丝纤维由于纤维刚性比较大,适当的原料加湿可以提高纤维的柔软性,降低纤维在纺纱过程中因静电原因造成的绕胶辊、绕罗拉现象。
二、喷气涡流纺原料的配棉要求
为了保持生产和成纱质量的稳定,优质低耗地进行生产,要求生产过程和成纱质量保持相对稳定。保持原棉性质的相对稳定是生产和质量稳定的一个重要条件。如果采用单一批号纺纱,当一批原料用完后,必须调换另一批原料来接替使用称接批,这样次数频繁地、大幅度地调换原料,势必造成生产和成纱质量的波动;如果采用多种原料搭配使用,只要搭配得当,就能保持混合原料性质的相对稳定,从而使生产过程及成纱质量也保持相对稳定。
配棉的原则讲究质量第一、全面安排、统筹兼顾、保证重点、瞻前顾后、细水长流、吃透两头、合理调配。质量第一、统筹兼顾、全面安排、保证重点就是要处理好质量与节约用棉的关系,在生产品种多的基础上,根据质量要求不同,既能保证重点品种的用棉,又能统筹安排。瞻前顾后就是充分考虑库存原料、车间半成品、原料采购的各方面情况,保证供应。细水长流就是要尽量延长每批原料的使用期,力求做到多批号生产,为6~8个批号。吃透两头,合理调配就是要及时摸清用原料趋势,随时掌握产品质量反馈信息,机动灵活,精打细算地调配原料。
1.配棉的目的
(1)保持生产和成纱质量的稳定。合理使用原棉,尽量满足纱线的质量和纱线支数的要求,因为纱线质量和特性要求不尽相同,加之纺纱工艺各有特点,因此,各种纱线对使用原棉的质量要求也不一样。另外,棉纺厂储存的原棉数量有多有少,质量有高有低,如果采用一种原棉或一个批号的原棉纺制一种纱线,无论在数量上还是在质量上都难以满足要求。故应采用混合棉纺纱,以充分利用各种原棉的特性,取长补短,满足纱线质量的要求。
(2)节约用棉,降低成本。原棉是按质论价的,不同纤维长度,不同等级的原棉价格差别很大,原棉投资在棉纱成本中占50%~85%(视品种而异),如果选用的原棉等级较高,虽然成纱质量可以得到保证,但是生产成本增加,意味着吨纱利润的降低。因此,配棉要从经济效益出发,控制配棉单价和吨纱用棉量,力求节约原棉成本,例如:在纤维长度较短的配棉中,适当混用一定比例的长度较长的低级别原棉,不仅不会降低成纱质量,相反可以提高成纱强力,对于原棉下脚、回花、精梳落棉、再用棉等成分,可按一定比例回用到配棉中,也可以起到降低用棉成本,节约用棉的效果。
2.配棉的方法
目前,棉纺企业普遍使用分类排队法的配棉方法,分类排队法即根据原棉的特性和纱线的不同要求,把适合纺制某品种纱线的原棉划分为一类,排队就是将同一类原棉按产地、性质、色泽基本接近的排在一队中,然后与配棉日程相结合编制成配棉排队表。分类排队法的优点是可以有计划地安排一个阶段的纱线配棉成分,可以保证混用效果,是一种科学的配棉方法。
(1)原棉的分类。
①可以按照纺制产品的规格对原棉进行分类:比如,精梳32~40英支针织用纱使用同类原棉。
②每个配棉类别的成分根据原棉具体的技术指标来确定:要求每批原棉技术指标差别不要过大,例如,控制范围如下:品级:1~2级;长度:2~4mm;含杂率:1%~2%;含水率1%~2%。
③棉纺工艺流程不同,配棉分类时也要灵活掌握:比如,同样的原棉在不同季节出现不同成纱质量时,配棉分类时就应及早调整。
(2)原棉的排队。在分类的基础上,将同一类原棉排成几队,把产地、技术指标相对接近的原棉排在一个队内,以便当一个批号的原棉用完以后,用同一个队中的另一个批号的原棉接替上去,使正在使用的原棉的特性无明显变化,达到稳定生产和保证成纱质量的目的,为此,原棉排队应遵循以下几点。
①主体成分:为了保证生产过程和成纱质量的稳定,在配棉中一般有意识地安排几个批号技术指标相对接近的原棉作为主体成分,一般以产地为主体,也有的用长度作为主体。主体成分一般占到总配棉的70%左右,这样可以避免品质特好或特差的原棉混用过多。但是由于原棉的性能是很复杂的,在具体生产中,如果很难用一队原棉作为主体成分时,可以考虑用几批原棉,但是注意使用时不要出现双峰接批现象。
②队数和混用百分比:队数和混用百分比有直接的关系,队数多,混用百分比小;队数少,混用百分比就大;队数过多时,生产管理难度较大,还容易造成混棉不匀;队数过少时,混用百分比较大,当接批时容易造成原棉性能的较大差异。
所以,确定队数时,首先要知道混棉的加工方式,如果采用人工小批量生产,队数最好要少,不超过4队,抓棉机混棉时可以增加到6~9队,后工序如采用并条条混时,还要考虑棉条的搭配比例。其次,确定队数还要考虑总投入原棉的数量多少,棉纱属于小批次生产时,队数不宜过多。再者,确定队数还要考虑原棉的产地、品种、质量指标等因素,原棉产地轧花厂多,品种多,质量差异大时队数宜多。最后确定队数还要考虑产品的品种和要求,如产品的色泽要求较高时,队数宜多,成纱质量波动较大时,队数也要多一些。
当队数确定以后,可以根据原棉的质量情况和成纱质量要求确定各种原棉混用百分比,为了减少成纱质量的波动,最大混用百分比一般为25%左右。
为了减少布面横档等质量问题,每批配棉混棉纤维的马克隆值大小差异要控制在0.4以内。国际市场的原棉交易也通常把马克隆值作为价格的参考指标之一,对于超过或达不到可纺性的马克隆值参数的原棉,做降价或折价处理。
单纤维强力也是决定成纱强力的主要指标之一,棉纤维在纺纱过程中要不断经受外力的作用,纤维具备一定的强力是棉纤维具有纺纱性能的必要条件之一,在正常情况下,棉纤维强力大,则成纱强力大,棉纤维强力不仅与纤维粗细有关,而且与棉花品种、生长条件有关,要求在纺制不同品种时为了达到要求的单纱强力,要特别重视配棉的单纤维强力问题。
原棉疵点是由于棉花生长期间发育不良或轧工不良形成的对纺纱有害的物质,原棉疵点在纺纱工艺流程中不易清除,或包卷在纱中,或附着在纱线中,使得条干恶化、断头增多、外观很差,直接危害纺纱生产和最终产品质量。
棉纤维含有的糖分,是指含有可溶性糖的总称,其中包括纤维自身含有的生理糖和附着表面的外源性物质。当原棉中含糖量过高时,在梳棉、精梳、并条、粗纱、细纱等工序会明显地发生黏附纤维现象,影响正常生产,尤其是逐步投入使用的国产新型设备,对含糖量过高的原棉更是不适应。所以,对于含糖量过高的原棉无论价格多么优惠,均要谨慎使用,尤其是用以制作高档针织面料。
做好原棉试纺可以避免或消除感官检验、仪器检验带来的局限性和误差,所以应在原棉大批量投入生产之前,安排新成分原棉小批量试纺,然后根据试纺情况和纱线质量安排新配棉的混合使用。
在进行新工艺、新技术时也应进行小批量试纺,以确认原棉的正确使用,搞好试纺工作可以减少纱线质量波动,能正确反映纤维的使用价值和经济价值,预测成纱性能,可以保证产品质量不会因时间的跨度而发生波动,才可以使得产品质量受到市场的认可。
三、化纤原料选配技术
化纤原料包括纤维品种及纤维性能方面的选配,混纺比例的确定,除选择适当的长度和细度外,特别要考虑染色性能,以免造成色差。
1.化学纤维品种的选择
化学纤维品种的选择对混纺产品起着决定性的作用,因此,应根据产品的不同用途、质量要求及化学纤维的加工性能选用不同的品种。如棉型针织内衣用纱要求柔软、条干均匀、吸湿性好,宜选用黏胶纤维或腈纶与棉纤维混纺;棉型外衣用料,要求坚牢耐磨、厚实挺括,多选用涤纶与棉纤维混纺。如果要提高毛纺纱性能和织物耐磨性能,可采用两种化学纤维和羊毛纤维混纺,以取长补短,降低成本。为改善麻织物的抗皱性和弹性,可采用涤纶与麻纤维混纺。
2.混纺比例的确定
(1)根据产品用途和质量要求确定混纺比。确定混纺比要考虑多种因素,主要是产品用途和质量要求。如外衣用料要求挺括、耐磨、保形性好、免烫性好、抗起球性好;而内衣用料则要求吸湿性好、透气性好、柔软、光洁等。此外,还要考虑加工和染整等后加工条件及原料成本等。涤纶与棉纤维混纺时,比例大多采用65%涤纶、35%棉纤维,其织物综合服用性能最好。
在黏胶纤维与其他纤维的混纺产品中,黏胶纤维的比例一般为30%左右,此时,毛粘混纺织物仍有毛型感;含黏胶纤维70%时,显现黏胶纤维产品的风格,抗皱性极差。涤纶中混用黏胶纤维,可改善织物的吸湿性和穿着舒适性,缓和织物熔孔性,减轻起毛起球和静电现象。
腈纶和其他纤维混纺,可发挥腈纶蓬松轻柔、保暖和染色鲜艳的特性,混用比例一般为30%~50%。随着混用比例的增加,织物耐磨性、折皱回复性都变差。锦纶与其他纤维混纺时,虽然混用比例很小,但也能显著提高织物的强力和耐磨性。
(2)根据化学纤维的强伸度确定混纺比。混纺纱的强力除取决于各成分纤维的强力外,还取决于各成分纤维断裂伸长率的差异。不同断裂伸长率的纤维相互混纺,在受外力拉伸时,组成混纺纱的各成分纤维同时产生伸长,但纤维内部所受到的应力不同,因而各成分纤维断裂的时刻不同,致使混纺纱的强力通常比各成分纯纺纱强力的加权平均值低很多。因此,混纺纱的强力与各成分间纤维强力的差异、断裂伸长率差异和混纺比三者有关。
从提高混纺纱强力的角度考虑,各混纺成分纤维的伸长选择应越接近越好,以提高各纤维组分的断裂同时性,从而提高各组分的强力利用率。目前,多采用中强中伸涤纶与棉纤维混纺。若涤纶与毛纤维混纺,则应采用低强高伸型,使其伸长率与毛纤维接近。
3.纤维性质选配
化学短纤维的品种和混纺比例确定后,还不能完全决定产品的性能,因为混纺纤维的各种性质,如长度、线密度等指标的不同都会直接影响混纺纱产品的性能。
(1)化学短纤维长度的选择。化学短纤维的长度分棉型、中长型和毛型等不同规格。棉型化学纤维的长度为32mm、35mm、38mm和42mm等,接近棉纤维长度而略长,可以在棉型纺纱设备上加工;中长型化学纤维的长度为51mm、65mm和76mm等,通常在棉型中长设备或粗梳毛纺设备上加工;毛型化学纤维的长度为76mm、89mm、l02mm和114mm等,一般在毛精纺设备上加工。纤维长度还影响其在成纱截面中的分布。通常较长的纤维容易集中在纱线的芯部,所以选用长于天然纤维的化学纤维混纺,其成纱中天然纤维大多会处在外层,使成纱外观更接近天然纤维。
(2)化学短纤维线密度的选择。棉型化学纤维的线密度为0.11~0.17tex,略细于棉纤维;中长仿毛化学纤维的线密度为0.22~0.33tex;毛型化学纤维的线密度为0.33~1.30tex。中长型与毛型化学纤维均略细于与其混纺的毛纤维。纤维越细,同线密度纱的横截面内纤维根数越多,纤维强力利用率越高,成纱条干越均匀,但纤维过细容易产生结粒。细纤维强度高的,在织物表面容易形成小粒子(起球)。
一般认为,化学短纤维的线密度与长度之间符合如下关系式时,化学纤维的可纺性和成纱质量较好:
L=230Tt
式中:L——纤维长度,mm;
Tt——纤维线密度,tex。
原棉、原料是影响产品质量的最关键的基础因素。在同样的生产条件下,一般使用质量好、适纺性能强的原料纺出的纱线质量相对较好,偶发性纱疵也相对较少。
4.化学纤维原料选配方法
(1)单一品种或单唛混配。用同一牌号化纤分包混配,优点是匀染度好,消除染色差异。但一种牌号化纤用完,调换另一种牌号,成品质量会有差异,必须严格分批。
(2)多品种或多唛混配。在化纤牌号变动较大的情况下采用同一种化纤多种牌号混用,逐批抽调,保持混合原料质量基本稳定,但对混和均匀度要求较高,稍有疏忽会产生色档,匀染度也较差。对染色性能差异大的牌号调换时要少量抽调,避免出现色差事故。
选用各种化学纤维于混料中的目的,是为了充分发挥其优良特性,取长补短,满足产品的不同要求,增加花色品种,扩大原料来源并降低成本。化学纤维选配包括品种选择、混纺比例确定及化学短纤维长度、线密度等性质的选择。