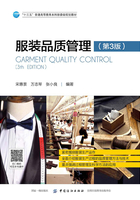
第五节 抽样检验法
无论是在企业内部还是在企业外部,供求双方对交付的产品如原材料、半成品、外协件等进行验收时,都要进行检验,以保证和确认产品质量。
一、检验方案的分类
按检验数量的多少来分类,检验有全数检验和抽样检验两种方式。
1.全数检验
是对全部产品逐个进行检测,从而判定每个产品合格与否的检验。它又称全面检验、100%检验,其处理对象是每个产品,这是一种沿用已久的检验方法。相对而言,全数检验可以较好地保证产品质量,但检验费用高。
(1)全数检验适用的场合:
[1]不合格的产品会造成严重的不良后果,如影响人身安全、引起生产严重混乱或给企业在经济、信誉上造成无法弥补的损失等,这种情况必须进行全数检验。
[2]条件允许,能容易地进行质量检验时,如灯泡的亮度检验等,应进行全数检验。
[3]批量比较少,没有必要进行抽样检验。
[4]同检验费用相比,产品价值特别昂贵,应进行全数检验。
(2)全数检验的缺点:
[1]有些产品的检验具有破坏性,如寿命、拉力等。很显然,破坏性的检验就不能进行全数检验。
[2]有些产品的产量很大,如电子元件、手表、钻石等。对它们进行全数检验势必花费大量人力、物力,很不经济。
[3]在数量多、速度快、时间长等情况下,全数检验容易产生错检和漏检。
[4]从某种意义上说,全数检验是一种消极的检验方法。全数检验采取将检验出的不合格品剔除的办法来保证产品的质量,它不能引起生产者对产品质量的关心。
2.抽样检验
就是从一批产品中随机抽取一部分进行检验,通过检验这少量产品来对这批产品的质量进行评估,并对这批产品做出是否合格、能否接收的结论。它是根据数理统计的原理,在对供货方和收货方的利益、要求以及双方承担的风险都作了考虑之后规定了产品的质量水平,并据此对批量、样本大小、判断标准等都作出适当的规定的一种检验方式。
与全数检验不同,实施抽样检验时,一旦一批产品判为不合格,成批产品要退还生产者,或要求生产者逐个挑选,这时,生产者不是对个别不合格品负责,而是对成批的产品负责,从而可增强生产者的质量责任感,促进生产者不断地提高质量水平。因此,对提高产品质量来说,抽样检验是一种积极的检验方式。
实施抽样检验需要事先确定抽样方案,按方案的要求,从一批产品中随机地抽取一部分进行检查,并通过检查结果与标准对比,对该批产品的质量状况进行估计和推断。
(1)抽样检验适用的场合:
[1]破坏性检验,如产品的可靠性试验、产品寿命试验、材料的疲劳试验、零件的强度检查等。
[2]产品数量很大,质量要求又不是很高,如螺钉、销钉、垫圈等。
[3]测量对象是连续体。如煤、矿石、铁液、重油的化学成分等,不能进行全数检验,而必须采取抽样检验。
[4]检验项目过多、周期长,进行全数检验有困难,采用抽样检验就能保证产品质量。
[5]希望节省检验费用的场合。
[6]督促供方改进质量的场合等。
(2)抽样检验的缺点:
[1]合格批内包含的不合格品数比全数检验多。因为抽样检验仅能剔除样本中的不合格品,而全数检验基本剔除批中全部的不合格品。
[2]判断批产品是否合格时,存在弃真和存伪的错误。由于抽样的随机性,存在把优质批判断为不合格批和把劣质批判断为合格批的可能性。任何抽样检验都避免不了这两种错误产生的可能。
(3)抽样检验应注意的问题:
[1]抽样检验只能相对地反映产品的质量,不能把样品的不合格率与整批产品的不合格率等同起来。经过抽样检验合格的产品批只能保证其统计质量,不可能保证整批产品100%都是合格品。这是因为抽样检验存在一定的局限性,还要承担一定的风险。
[2]经过抽样检验被判定为合格的批,并不等于批中每个产品都合格;同样,经过抽样检验被判定为不合格的批,也不等于批中每个产品都不合格。
[3]并非任何抽样检验都能达到正确地判断整批产品质量的目的。所指的抽样检验是建立在概率论和数理统计基础上的科学的抽样方法,即抽样检验时应该使所抽取的样本容量达到一定水平,这样才能保证检验结果具有统计特征,如果样本容量太少,所得到的检验结果往往不能反映整批产品的质量特性。
综上所述,全数检验和抽样检验两种检验方式各有其利弊。近年来,由于自动化检测的发展,生产中应用全数检验有上升的趋势。
二、抽样检验的概念
抽样检验就是从交验的每批产品中随机地抽取预定样本数量,对照标准逐个检验样本的性能。如果样本中所含不合格品数不大于抽样方案预先最低规定数,则判定该批产品合格,予以接收;反之,则判定该批产品不合格,予以拒收。简言之,按规定的抽样方案随机地从一批或一个过程中抽取少量个体进行检验称为抽样检验。计数抽样检验方案是以数理统计原理为基础,适当兼顾了生产者和消费者双方风险损失的抽样方案,具有科学的依据,并提供一定的可靠保证。
三、抽样检验常用名词术语
1.单位产品和样本大小
单位产品就是要进行检验的基本产品单位。单位产品的划分有随意性,根据具体情况而决定。样本是指从群体中随机抽取部分的单位体,样本大小用n表示。
2.交验批和批量
交验批是提供检验的一批产品,交验批中所包含的单位产品数量称为批量,用N表示。
3.合格判定数(Acceptance Number)
在抽样方案中,预先规定的判定批产品合格的样本中最大允许不合格数,通常记作Ac,或c。
4.不合格判定数(Rejection Number)
抽样方案中预先规定判定批产品不合格的样本中最小不合格数,通常记为Re。
5.合格质量水平(Acceptable Qualtity Level)
合格质量水平(用AQL表示)也称可接收质量水平,是在抽检中供需双方可接收的连续的交验批的平均不合格率的上限值,是供方能够保证稳定达到的实际质量水平指标,是用户所能接受的产品质量水平。
6.缺点
产品的单位品质特性不符合契约所规定的规格或购买说明书的要求者,称为缺点,缺点一般可分为:
(1)致命缺点:有危害产品的使用者及携带者的生命或安全的缺点。
(2)重缺点:不能达到产品使用目的的缺点。
(3)轻缺点:不影响产品使用目的的缺点。
四、抽样方案的分类
1.按照质量特性值的性质以及供求双方的需要分类
(1)计数抽验方案:即根据规定的要求,用计数方法衡量产品质量特性,把样品中的单位产品仅区分为合格品或不合格品(计件),或计算单位产品的缺陷数(计点),根据测定结果与判定标准比较,最后对其制定出接受或拒收的抽验方案。由于计数抽验仅仅把产品区分为合格与否,它具有手续简便、费用节省,且无需预先假定分布规律等优点。
例:从某1000个产品中随机抽样20个进行检验,并规定样本中的不合格数若小于或等于2,即为批合格;若不合格数在3个及以上即为批不合格。用符号表示如下:
批量:N=1000(个或件);
抽样样本:n=20(个或件);
合格判定数:Ac=2;
不合格判定数:Re=3。
(2)计量抽验方案:即对样本中的单位产品质量特性进行直接定量计测,并用计量值作为批判定标准的抽验方案称为计量抽验方案。这类方案具有如下特点:计算检验提供的信息多,判定明确,一般更适用于质量特性较关键的产品检验。
对成批成品抽验,常采用计数抽验方法;对于那些需作破坏性检验以及检验费用极大的项目,一般采用计量抽验方法。
2.按抽样次数分类
根据在检验批中最大限度地进行抽样作出批合格与否的判定这一准则,抽样方案可分成一次、二次与多次抽样等类型。
(1)一次抽样:即从批中只抽取一个样本的抽样方式,其操作原理示意图如图2-11所示。图中n为样本大小,d为样本中测得的不合格品数,c为合格判定数。
一次抽样具有以下优点:

图2-11 一次抽样检验示意
[1]方案设计、培训与管理比较简单。
[2]抽样量是常数。
[3]有关批质量的情报能最大限度地被利用。
其缺点是:抽样量比其他类型多,仅依据一次抽样结果就作判定使生产者在心理上难以接受。
(2)二次抽样:所谓二次抽样是指最多从批产品中抽取两个样本,最终对批产品作出接受与否判定的一种抽样方式。此类型需根据第一个样本提供的信息,决定是否抽取第二个样本,其示意图见图2-12。二次抽样中,一般设定n1=n2。此类型具有平均抽样量少于一次抽样以及在心理易于接受的优点。但其抽样量不定,管理稍复杂,需对管理人员进行一定的培训。

图2-12 二次抽样检验示意
例:当N=1000,n1=36,n2=59,c1=0,c2=3,则这个方案可表示为(1000,36,59,0,3),其含义是指从批量为1000件的交验产品中,随机抽取第一个样本n1=36件进行检验,发现n1中的不合格数为d1。
若d1≤0(实际为零),则判定该批产品合格,予以接收;
若d1>3,则判定该批产品不合格,予以拒收;
若0<d1≤3即在n1中发现的不合格数为1件,2件或3件,则不对该产品合格与否作出判断,需要继续抽取第二个样本n2,即从同批产品中随机抽取n2=59件再进行检验,记录n2中的不合格数d2。
若d1+d2≤3,则判定该批产品合格,予以接收;
若d1+d2>3,则判定该批产品不合格,予以拒收。
(3)多次抽样:多次抽样是一种允许抽取两个以上具有同等大小样本,最终才能对批产品作出接受与否判定的一种抽样方式。因此它可以取多达k(k≥3)个样本,是否需抽取第i(i>k)个样本,需由前(i-1)个样本所提供的信息而定。多次抽样在心理是最感安全的,但操作复杂,需作专门训练。ISO 2859中规定的多次抽样多达七次,我国GB 2828—87中规定的多次抽样达五次。由于操作比较复杂,这里不作介绍。
当然,在相同的检查参数条件下,不论采用何种抽样方案,其对批产品质量的判别能力基本上是相同的。
3.按照产品特点和生产特点分类
分为逐批型抽样和连续型抽样。
(1)逐批型抽样是指对生产过程所产生的每一批产品逐批抽样检验,从而判断每批产品的合格与否。
(2)连续型抽样方案。连续型抽样是指对连续提交的在制品的检验,主要用于通过检验点并不成批交检的单位产品。它的主要特点是边抽样检查边评价样本,从而减少抽查的工作量与费用。通过全验与抽验的交替连续检查,保证流动批通过检验后的产品质量控制在规定的限值以下。CB8052—87即属此型。
4.按照抽样方案能否调整分类
可以分为调整型抽样方案和非调整型抽样方案。非调整型抽样方案根据实际需要又可分为标准型抽样方案和选择型抽样方案。
(1)调整型抽样方案:方案设计时,首先考虑生产者的利益,一旦质量变化时,通过方案调整或进一步鼓励生产者提高质量以保护使用者的利益。它适用于连续多批且有多个供应者的检验类型,GB2828—87即属此型。下文将重点介绍计数调整型抽样方案。
(2)标准型抽样方案:它能同时满足生产方和使用方双方要求,适用于孤立批产品的检验。我国目前尚未颁布计数标准型抽样方案。
(3)选择型抽样方案:又称选剔型,允许对拒收的不合格批产品退回筛选,从中剔出不合格品将其调换或修复合格,然后再重新交验。根据质量保证形式不同,本方案又可分为分批质量保证与多批质量保证两种形式。本方案适用于连续多批固定供应者的检验。
五、计数调整型抽样方案
调整型抽样方案是对批量相同且质量要求一定的检验批进行连续接收检验时,可以根据检验批的历史资料和以往的检验结果按照预先规定的规则对方案进行调整的一种抽验方案。这种抽样方法可以进行动态调整,具有灵活、合理的优点,所以是目前国际上最为广泛采用的一种方案。方案调整方式分为三种,即宽严程度的调整、检验水平的调整和检验方式的调整,其中第一种最为常用。
1.合格质量水平(AQL)
设产品批可接受的水平值为P,凡P≤AQL,使用方认为质量是可以接受的合格批,愿以小于1-α的概率接受。在调整型方案中,AQL共有如下26种值以备选用:0.010,0.015,0.025,0.040,0.065,0.10,0.15,0.25,0.40,0.65,1.0,1.5,2.5,4.0,6.5,10,15,25,40,65,100,150,250,400,650,1000。在选用时,AQL并非无级自由值,需从上列26个值中选取。
(1)当AQL≤10时,对计件、计点数据均适用。
(2)当AQL>10时,则只能适用于计点数据。
(3)在计件数据中,P值以%表示。如AQL=0.10,实为0.10%,即合格批的不合格品率上限值允许为1‰。
2.检验水平
检验水平是指n与N之间比值大小的分级水平,即提交检验批的批量与样本大小间的等级对应关系。
ISO 2859和国家标准GB2828都规定了七种检验水平,由低到高按S—1,S—2,S—3,S—4,Ⅰ,Ⅱ,Ⅲ排列。其中S—1至S—4为特殊水平,一般在确信品质较为稳定条件下才能使用。Ⅰ与Ⅱ称为一般水平,其中Ⅰ为低水平,Ⅱ为标准水平,Ⅲ为高水平,相应的样本比例为1:2.5:4。若无特殊规定,一般采用Ⅱ。批量与检验水平对应的样本大小字码表见表2-13所示。一次正常检验抽样方案如表2-14所示。
表2-13 样本大小字码


3.抽样方案的确定
抽样方案的确定就是确定n、Ac和Re,其实施程序为:
(1)规定产品的质量标准:区分合格与否以及不合格的等级。
(2)确定检验水平:检验水平的确定结合实际(参考本节前面所述)。
(3)规定合格质量水平AQL:AQL过小,会导致生产成本和检验工作量的增加,对供方不利;AQL过大,需求方难以得到质量满意的产品。因此,合格质量水平AQL可以按顾客的质量要求、检验项目或生产者协商来确定。
(4)确定抽样方案的类型:一般指进行一次抽样还是二次抽样。
(5)确定样本字码:根据检验的批量和检验水平来确定样本字码,利用表2-13样本量字码表,找到批量N所在的行,检验水平所在的列,确定的行和列的交叉栏的文字即样本字码。样本字码从A到R共16个字母。
(6)确定抽样方案:由样本字码确定对应的样本大小n,样本字码所在的行与AQL所在的列相交的格中有两个数,其中左边的为合格判定数c,右边为不合格判定数Re。如果交叉栏中是箭头,则按箭头指向查找c和Re,直到找到为止。