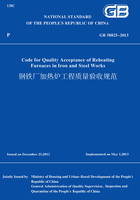
4.8 Supporting and Skid System
4.8.1 Construction quality acceptance of the skid in reheating furnace with design pressure not larger than 4.0 MPa shall comply with the requirements in this Section.
4.8.2 Following requirements shall be met for the heat resistant pillow block of skid in walking beam type furnace and the sliding block of skid in pusher type reheating furnace:
1 The heat resistant pillow block and sliding block of skid shall be made by vacuum smelting and precision casting.
2 The chemical composition and purity of the alloy of heat resistant pillow block and sliding block shall comply with the following requirements:
1)The material used shall be new,no waste pad or recycled scrap shall be used as material.
2)The chemical composition of alloy of the heat resistant pillow block and sliding block shall meet relevant requirements in the design documents or asked by the user comply with.
Check method:Checking the quality documents or sampling inspection and analysis.
Sample size:At least 1 sample for each kind of material.
3 The size,shape and surface quality of the heat resistant pillow block and sliding block shall comply with the following requirements:
1)The size,shape and allowable deviation of the castings shall comply with the requirements in the design drawings.
2)When checked with visual and fluorescent penetration inspection,the surface shall be without any crack,cold shut,misrun,slag inclusion,subsurface porosity or penetrating porosity.The Quality grade of the fluorescent penetration test shall be Grade 2.
3)The clear cavitation diameter of depression,sand hole,pore,impurity,shrink hole and other casting defects shall not be larger than 1.5mm,the depth of them shall not be larger than 0.6mm,and the total number of them shall not exceed 2 pieces within 400mm2.
4)The surface roughness of the top surface of the pad and the contact area with the steel pipe shall reach Grade 12.5.
Check method:Visual inspection,fluorescent penetration test,Checking with steel ruler and other tools.
Sample size:At least 1 sample for each kind of material.
4 Each heat pad shall have an alloy grade mark on it.
4.8.3 The elbow,T-joint and plug of the supporting and skid system should not be casting.Those of the evaporative cooling skid should be steel forging;the elbow and T-joint of the water cooling skid may be made by stamping or pushing,and its plug should be steel forging.
Check method:Checking the quality records or sampling inspection.
Sample size:10%.
4.8.4 For the butt welding of longitudinal or cross beam,and of column,and for the butt welding between longitudinal or cross beam and column of skid in furnace,tungsten inert gas welding(TIG)shall be adopted for root welding,and the welding wire shall be ER50-4 or ER50-6 in the ER50 series stipulated in current national standard GB/T 8110 Welding Wires for Gas Shielding Arc Welding of Carbon and Low Alloy Steels.All other welding beads shall be manual electric arc welding,and the electrode shall be E5015 stipulated in current national standard GB/T 5117 Covered Electrodes for Metal Arc Welding of Non-alloy and Fine Grain Steels.
4.8.5 Anyone who performs the welding of evaporative cooling supporting beam must have the certificate of special equipment operating personnel of the People's Republic of China.
Check method:Checking the certificate.
Sample size:100%.
4.8.6 The delivery quality of the supporting and skid system shall meet the following requirements:
1 The steel pipes to be used for making skid column shall be of the same specification and be produced in the same batch and by the same manufacturer.Dimensional tolerance of the steel pipes shall comply with the high accuracy class requirements stipulated in current national standard GB/T 17395 Dimensions,Shapes,Masses and Tolerances of Seamless Steel Tubes.
Check method:Check the quality documents.
Sample size:100%.
2 The steel pipes to be used as skid and column shall be straightened before cutting,the full length bending shall be less than 1mm,the smoothness of the machined groove surface shall be Class 12.5,the arc transition shall be smooth,the concentricity shall be maintained,the joint misalignment shall not exceed 1mm,and all the machined surfaces shall be treated with oxidation protection measures.
3 When the heat resistant pad or slider is being welded to the skid,good contact shall be guaranteed between the block or slider and the steel pipe of the skid,and there shall not be any gap in between.Any single continuous welding along the length of the block or slider should not exceed 200mm.
4 Allowable tolerances of the main components shall comply with the requirements in Table 4.8.6-1.
Table 4.8.6-1 Allowable tolerances of main components

5 TIG(based on argon arc welding)shall be adopted in the first welding pass of the skid,and the subsequent welding passes shall be performed with electric arc welding.The welding seam quality of the accomplished skid shall comply with the requirements in Table 4.8.6-2.
Table 4.8.6-2 Welding seam quality

Check method:Checking the flaw detection documents and the reserved negative films.The radiographic detection shall comply with the requirements in current national standard GB/T 3323 Radiographic Examination of Fusion Welded Joints in Metallic Materials;the ultrasonic detection shall comply with the requirements in current professional standard JB/T 4730 Nondestructive Testing of Pressure Equipment-Part 3:Ultrasonic Testing.Sample size:100%.
4.8.7 Field installation dimensions of the skid shall meet the following requirements:
1 The reference line of the skid installation shall accord with the furnace center line and the charging table center line.
2 The allowable errors of installation dimensions of the skid shall comply with the requirements in Table 4.8.7.
Table 4.8.7 Allowable errors of installation dimensions of skid

4.8.8 The operation and inspection of field welding shall comply with the following requirements:
1 The procedure qualification of the welding of evaporative cooling skid shall be carried out according to the requirements in the design documents.
Check method:Checking the qualification documents of welding procedure.
Sample size:100%.
2 The welding procedure for water cooling skid may refer to the requirements in current national standard GB 50235 Code for Construction and Acceptance of Industrial Metallic Piping.
3 The post-welding nondestructive testing of skid shall be conducted after stress relief.
4 The welding seam quality of skid shall reach GradeⅡin the quality grading in Table 11.3.2 of current national standard GB 50683-2011 Code for Acceptance of Field Equipment,Industrial Pipe Welding Construction Quality and the requirements in Table 4.8.8.
Table 4.8.8 Welding seam quality

5 If any defect is found in the radiographic detection of butt joint,double times of additional radiographic detections shall be conducted.If the result of the additional detection is still unqualified,radiographic detection shall be conducted for all the butt joints welded by the welder.A reworked crater may be repaired twice at most,and if a weldment is still unqualified after being repaired twice,it shall be discarded.
Check method:Checking the flaw detection documents and the reserved negative films.Radiographic detection shall comply with the requirements in current national standard GB/T 3323 Radiographic Examination of Fusion Welded Joints in Metallic Materials;ultrasonic detection shall meet the requirements in current professional standard JB/T 4730.3 Nondestructive Testing of Pressure Equipment-Part 3:Ultrasonic Testing.
Sample size:100%.
4.8.9 System flushing shall be conducted for the skid before commissioning.The technical requirements and results of the flushing shall comply with the requirements in current national standard GB 50235 Code for Construction and Acceptance of Industrial Metallic Piping.
Check method:Checking the flushing records.
Sample size:100%.
4.8.10 Hydraulic test of the skid in furnace shall comply with the following requirements:
1 Hydraulic test of the evaporative cooling skid shall comply with the requirements in Chapter 8 of this code.
2 The test pressure of hydraulic test of the water cooling skid shall be 1.5 times of the working pressure and be kept for 15 to 20 min.The test result shall be accepted if no leakage is found.
Check method:Field bulge test and making relevant records.
Sample size:100%.