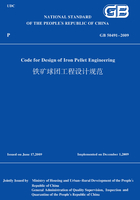
7.3 Induration
7.3.1 The following requirements shall be applied for both Grate-kiln,straight grate and shaft furnace systems:
1 Firing regime to be applied shall be advanced,reasonable and energy economized.Based on simulative tests,design of mass balance,heat balance and gas balance as well as process gas flow diagram shall be performed for finalizing all process parameters.
2 Where using 100% hematite ores carbon sources should be added in pellets.
3 Where updraft drying applied,air leakage from windboxes and to upper hoods shall be reduced as much as possible,and the gases exhausted from upper hoods shall be cleaned to comply with environmental requirements.
4 Heat insulation,expansion joints,tempering ducts and control valves shall be considered for windboxes and process ducts.The shell temperature of windboxes and ducts shall be lower than 80℃and internal heat insulation is preferred.
5 PH circulation fans shall be heat-resistant with heat-resistant temperatures not less than 550℃.The life span of impeller shall be more than a year,and the rotating speed should be variable.Multicyclone dust collector of efficiency and heat resistance shall be installed ahead of circulation fan with efficiency more than 90%.
6 The firing systems and process ducts shall be safe,reliable and energy effective.All of the control valves and switches shall be flexible,precise and automatic controlled.
7 Measurement of the fuels shall be accurate.Fuel gases shall be measured with orifice meters or other precise flowmeters.
8 The refractory materials,thickness and installation methods shall be selected to satisfy the requirements of indurating process and firing regimes.Methods and curves for dry-out and heating-up of refractory lining shall be provided based on its natures in the design.
9 Large process fans should be furnished with variable speed controls,vibration and temperature monitoring.
10 Reliable and high efficient dust collectors shall be provided for process gases dedusting in accordance with environmental requirements before emitted into atmosphere.Dusts collected from dust collectors should be pneumatically conveyed and recycled in process.
11 Flowrates and pressures of process fans shall be determined with reference to the results of pelletizing tests and considering the factors of raw material characteristics,bed depth,pressure drops on ducts and dust collectors and site levels etc.,and necessary margins shall be applied.
12 Process exhaust gases temperature shall be above acid dew points.
13 The pellets shall be sufficient cooled to the temperatures not exceeding 120℃.
7.3.2 The following requirements shall be applied for Grate-kiln systems:
1 Traveling grate,rotary kiln and annular cooler shall be properly sized to allow reasonable matching with each other.
2 The recommended ratios for the width of grate conveyor chain to kiln shell diameter is a range between 0.7 and 0.9.
3 Fuel coal should be used as main fuel,or fuel gases with high heat values.
4 Where firing coal is applicable,direct coal firing system should be applied.
5 Where indirect coal firing system is applied,an intermediate bin for pulverized coal storage shall be provided.This bin shall be capable of storage for 4 to 5 hours operation.Roots blowers should be utilized to supply high-pressure conveying air for pulverized coal delivery from intermediate bin to kiln burner via coal pipe.Roots blowers shall be provided with sound insulation and noise reduction devices.And pulverized coal should be measured by Rotor feeder scales.
6 Kiln burners shall be provided with abilities allowing movement along its axis and adjustment in heat supply as well as flame shape and length.
7 A well leveled bed of green balls on traveling grate ranged between 160mm and 200mm is recommended,and the height of sideplates should be 10-20mm lower than the bed level accordingly.
8 When the traveling grate is divided into four process zones of UDD,DDD,TPH and PH,each zone should be provided with gases as specified below:
1)UDD:an upward flow of warm gases from annular cooler at proper temperatures of 200-300℃for initial drying.
2)DDD:warm gases from PH zone for complete drying by a downward flow at about 300-400℃.
3)TPH:pellets are subject to a downward flow of gases from annular cooler at proper temperatures of 600-750℃.
4)PH:hot kiln off-gases at temperatures of 950-1050℃and 1150℃or higher for preheating magnetite pellets and hematite pellets,respectively.
9 When the traveling grate is assigned with DDD1,DDD2,TPH and PH zones,the gas flow for each zone should be:
1)DDD1:green balls initial drying is performed by a downward flow of warm gases from annular cooler at about 250-350℃.
2)DDD2:a downward flow of gases from PH zone at proper temperatures of 350-500℃for complete drying.
3)TPH:hot gases from annular cooler at proper temperatures of 600-750℃for tempered preheating of dried pellets in zone.
4)PH:hot kiln off-gases are introduced to pellet bed at 950-1050℃and 1150℃or higher,for preheating magnetite pellets and hematite pellets,respectively.
10 For large and medium-scale pellet plants,the productivities of traveling grate shall be 30t/m2/d or greater for hematite ores,and 40t/m2/d or greater for magnetite ores.
11 When extra heat shall be supplied to PH and/or TPH zones,the burners with adjustable capacities shall be installed in the related zone.
12 The clearance between the upper hoods and the top of pellets bed shall allow the gases passing through at reasonable speed and also ease for maintenance.Doors for maintenance and observation shall be provided in each zone of grate.Emergency bleed stacks shall be installed on the top of upper hoods in PH zone.
13 Shell temperatures of grate upper hoods should be lower than 120℃or 80℃at high temperature zones or low temperature zones,respectively.
14 Heat resistant components of the grate shall be cooled properly and air cooling should be applied.The conveyor chain shall be provided with necessary devices to prevent snack running.Chain assembly,side & end strippers and carrying rollers in high temperature zones shall be made of heat resistant alloy.Average life of grate plates shall be more than one year and two years for the others.
15 The traveling grate should have lower air leakage less than 20%.
16 Spillages leaked from the grate shall be minimized as much as possible.The spillages from strippers should be less than 5%.Spillages and dust discharged from windboxes should be reground before recycled to balling system.
17 Traveling grate shall be placed in enclosed building and the lifting machine should be installed for maintenance.Mobile cranes may be used for maintenance of rotary kiln.
18 Passenger-and-freight elevators shall be installed in the traveling grate and main electric building.Where the traveling grate building is adjacent to main electric building they may share one common elevator.
19 The predominant rotary kiln for processing iron ores shall be"fat-and-short"type,the suitable ratio of length vs diameter should be 6.5-7.0.The inclination of the kiln should be 3%-5%,and the retention time of the burden in the kiln should be 20-25 minutes and the filling degree 7%-9%accordingly.The temperatures for pellets heat hardened inside the kiln should be 1250-1380℃,while the gases inside the kiln should contain sufficient oxygen at a level greater than 12%.
20 The volumetric productivity calculated from net space inside the kiln should be 9.5t/m3/d or greater for large and medium scale plants.
21 The working life of kiln shell for large and medium-scale plants shall be designed for 25 years or greater.
22 Rotary kiln drives shall be selected to ensure stability for operation,ease for maintenance and convenience for operation.Variable speed control and emergency drive shall be furnished.
23 The kiln foundation shall be designed to satisfy the following requirements:
1)Vertical settlement and top lateral displacement for the foundations of carrying roller assemblies shall not be more than 4mm.
2)Both vertical settlements and top lateral displacements between the adjacent foundations of carrying roller assemblies shall have variations less than 1mm.And the top vertical displacements between the adjacent foundations of carrying roller assemblies shall be controlled less than 6mm.
3)The overall vertical settlements of foundations between the kiln and buildings linked to it shall be restricted within 10mm.
24 The maximum kiln shell temperature shall be lower than 250℃during normal operation.Kiln lining may be divided into different zones of high,medium and low temperature and replaced in batches and periodically.The period for complete replacement should be four years.
25 The kiln feed and discharge ends should be sealed by seal leaves to ensure air leakage less than 1%.Air cooling and spillage collection devices shall be attached to them.
26 Grizzly and door with observation hole shall be set in the firing hood at kiln discharge end.Spillages discharged from kiln feed ends and strippers of the grate should be collected and then fed into the kiln by bucket elevators.
27 Rotary kiln should be installed outdoor,and sufficient space shall be reserved for maintenance.
28 Hot pellets discharged from the kiln shall be cooled sufficiently in annular coolers.Hot gases discharged from the coolers shall be introduced into the kiln and traveling grate via ducts.Duct burners should be provided on recuperation ducts.
29 The appropriate bed depth of the cooler should be between 660mm and 760mm.
30 Direct impact on refractory lining at cooler loading hopper from kiln discharge shall be eliminated by properly configuration of the transitions from the kiln discharge end to cooler feed end.The pallet plates of the cooler shall have more openings allowing cooling air passing through,and meanwhile attention shall be paid to avoid opening blocked by spillages in the design.Dumping and resetting of pallets shall be reliable and flexible.Overall air leakage from the cooler should be less than 10%.
31 The cooler should be divided into three or four cooling zones,cooling fans shall be installed accordingly to supply cooling air with sufficient quantity.
32 Cooler upper stationary housing including air-cooled baffle walls and screed walls shall be provided above the pellet bed.The refractory lining of upper housing should be precast shapes attached to steel shell.Sand sealing or water sealing shall be provided for sealing between rotating walls and upper housing,and automatic water sealing should be the best practice.Inspection doors shall be provided in upper housing for each zone.
33 Kiln burner and burner floor should be located on the top of the cooler,and should be configured flexible for operation.Lifting equipment should also be provided for maintenance of pallets.
34 Configuration of cooler drives should be compact and easy maintenance.Platforms shall be provided at inner and outer side of the cooler.
35 Cooler should be installed above the ground level(±0.00m).Apron feeder should be utilized for discharge pellets from cooler discharge hopper.Outlets for emergency discharge shall be provided at cooler discharge hopper.Water spray devices should be provided for belt conveyors outgoing cooler discharge.
7.3.3 The following requirements shall be in accordance with for straight grate systems:
1 The straight grate should include the following seven process zones of updraft drying(UDD),downdraft drying(DDD),preheating(PH),firing(F),after-firing(AF),the first cooling(C1)and the second cooling(C2).
2 Warm gases from the secondary cooling zone should be conducted to updraft drying zone for initial drying.On the both sides of the furnace in preheating and firing zones,burners shall be installed.The afterfiring zone shall be directly heated with hot gases discharged from the first cooling zone.
3 Fuel gases and fuel oils shall be the main fuels used for straight grate systems,and carbon sources to be added in pellets should be auxiliary fuels.
4 The pellets should be leveled on pallets to a depth of 350mm or greater.
5 Hearth layer and side layer shall be applied with thickness between 70mm and 100mm,and they should be sized pellets of 8-16mm separated by pellet screening systems.
6 The specific productivity of straight grate calculated from effective grate areas should be:
1)18-24t/m2/d for hematite ores.
2)20-30t/m2/d for magnetite ores.
7 Overall air leakage of straight grate should be 25% or less.
8 The pallet shall be made of heat resistant alloy to ensure the working life of the pallet exclusive grate bars not less than 12 years and the grate bars not less than 2 years.
9 The material and thickness of refractory lining of the furnaces should be proper selected according to the requirements for different process zones,to ensure the working life not less than 4 years.The furnaces shall be properly refractory lined to lower shell temperatures not exceeding 1200C or 800C where it is located in high temperature zones or low temperature zones.
10 Spare combustion fan(s)shall be provided for firing zone.
11 Straight grate shall be installed in enclosed workshop furnished with ventilation.Dedicated overhead traveling crane for maintenance,pallet storage room and maintenance workshop shall be provided.One straight grate should be housed in one workshop.Process fans and dust collectors should be arranged at the same side of induration machine and installed above the ground level.
7.3.4 The following requirements shall be in accordance with for shaft furnace process:
1 Minimum 90% magnetite ores should be processed in Shaft furnaces for pellet production.The product shall be acid BF grade pellets.
2 Drying bed of newly designed shall be applied.Green balls shall be dried in drying zone for at least five minutes.
3 Pellets shall be heat-hardened under hot gas flow at 1250℃or higher and oxygen level 8% or greater.The cross section shall be optimized to ensure pellets are subjected to a gas flow with uniform and stable temperature.
4 The workshop for shaft furnace shall be provided with five vertical platforms for operation,identified as top vaporization floor,green balls distributing and leveling floor,combustion chambers floor,teeth roller discharging floor and the base floor.
5 External cooling shall be provided to ensure the cooled pellet temperatures less than 120℃.
6 The steam generated from evaporation shall be utilized for waste heat recovery.
7 Top dedusting fans shall be interlocked with gas pressurizing fans and combustion fans.