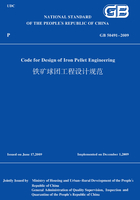
2 Terms
2.0.1 Raw Materials
Iron-bearing materials for pellet production,such as iron ore fines,iron ore concentrates and the likes.
2.0.2 Auxiliary materials
Materials which are auxiliary but indeed needed to be added into pellets for the specific functions and/or satisfying the quality requirements of pellet products.
2.0.3 Binder
Materials added into pellets to improve the balling performance of iron ores,such as bentonite,quicklime,hydrated lime and other kinds of organic matter.It is typically identified as organic binders and inorganic binders.
2.0.4 Additive
Materials containing calcium,magnesium and boron etc.,added into pellets to meet the different quality requirements of pellet products.Compound additive is a mixture of binder with various additives used as an auxiliary material for production of iron ore pellets.
2.0.5 Fuel
Fuel is a substance such as natural gas,blast-furnace gas,coke oven gas,heavy oil and coal etc.that is burned to provide heat for pellets induration.Fuel solid,fuel liquid and fuel gas are three kinds of major classifications.
2.0.6 Carbon source
Materials containing fixed carbon added into pellets for heat supply interiorly,such as anthracite,coke and petroleum coke etc.
2.0.7 Stockyard
The facility for stockpiling and storing of raw materials,fuels,additives,and pellet products.Mainly comprising raw materials stockyard and pellet stockyard.
2.0.8 Grinding
Procedure in which material is ground to obtain desired fineness and/or specific surface area to meet the process requirements,including dry grinding,wet grinding,moist grinding and high-pressure roll press grinding.
2.0.9 Iron ores drying
A system or procedure in which excessive moistures are evaporated to desired levels from iron ores by convective heat transfer from gases to solids.
2.0.10 Automatic weight proportioning
A procedure for control the materials mass flow at predetermined rates automatically.
2.0.11 Mixture
Blended materials from raw materials with auxiliary materials.
2.0.12 Balling
A procedure of processing and obtaining green balls from mixture in balling machine.
2.0.13 Green ball
The balls made from mixture in balling machine which are not subject to drying,preheating and indurating.
2.0.14 Green ball classification
Procedure in which undersize and oversize green balls are separated from green balls.
2.0.15 Induration
A procedure or system in which preheated pellets are heat-harden allowing sufficient oxidation,recrystallization and crystal growth.
2.0.16 Pelletizing
Process of pellet production in the sequence of materials proportioning & mixing,balling,green balls classification,drying and preheating,indurating and cooling.
2.0.17 Pellets
The final products from pelletizing process.
2.0.18 Hearth and side layer
Pellets with certain thickness lined on the grate plates and the inner sides of sideplates in straight grate indurating machine.
2.0.19 Bed depth
The level of pellets bed on induration machine.
2.0.20 Bed permeability
The capacity of air flow across through the pellets bed under certain bed level and pressure.
2.0.21 Straight grate productivity
The throughputs of final products of straight grate indurating machine calculated on unit effective grate area per day,t/m2/d.
2.0.22 Traveling grate productivity
The throughputs of final products of traveling grate calculated on unit effective grate area per day,t/m2/d.
2.0.23 Kiln productivity
The throughputs of final products of the kiln calculated on unit net volume per day,t/m3/d.
2.0.24 Shaft furnace productivity
The throughputs of final products of the shaft furnace calculated on unit effective furnace cross section area per day,t/m2/d.
2.0.25 Pyro-process system
The heat supply and heat transfer systems for pelletizing process.
2.0.26 Firing regime
Parameters applied for process zones of induration system based on the given raw material characteristics,including solid and gas temperatures,residence time,gas velocity and flowrates,heat supply rates etc.
2.0.27 Green balls drying
A procedure in which green ball moistures are evaporated by convective gas-solid heat transfer.
2.0.28 Downdraft drying(DDD)
The green balls drying is processed by a downward air flow across the pellets bed.
2.0.29 Updraft drying(UDD)
The green balls drying is processed by an upward air flow across the pellets bed.
2.0.30 Tempered preheating(TPH)
The procedure for dried pellets further dehydration,commencing magnetite and carbon and sulfur oxidation,calcinations,by further heating up pellets.
2.0.31 Preheating(PH)
The procedure for pellets further calcinations,oxidations,improving crystallization,allowing pellets having certain strength.
2.0.32 Heat recuperation
Reclaiming the heat in hot process gases by recycling.
2.0.33 Temperature adjustment
Adjusting gases temperatures by heating or cooling of recuperated gases to satisfy the requirements of temperatures for the relevant process zones.
2.0.34 Mass balance
Calculation of materials inputs,outputs and losses on the basis of mass conservation for the given process,where mass variations caused by reactions shall be involved if applicable.
2.0.35 Heat balance
Calculation of inputs and losses of heat flux for the given process,where heat generations and consumptions due to reactions shall be involved if applicable.
2.0.36 Gas balance
Calculation of inputs,outputs and losses for gas/air flux on the basis of mass conservation for the given process,where gas mass variations from reactions shall be included if applicable.
2.0.37 Bleed-off stack
Device to vent high temperature gases quickly for protection of equipment in the event the gas temperature and/or flowrate exceed critical limits,or the equipment accident appeared.
2.0.38 Duct air heating furnace
The heat supply device attached to the recuperation gas ducts.
2.0.39 Cooling
The procedure to cool down fired pellets to a certain temperatures by forced updraft air flow across the pellets bed,where the hot pellets exchange heat with ambient air.
2.0.40 Pellet screening
The procedure for classification of cooled pellets to remove any fines from pellets.