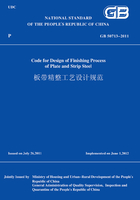
4.2 Finishing Process of Carbon Steel Plate
4.2.1 The finishing process of steel plate should include cooling after rolling,shearing or cutting,surface quality and overall dimensions inspection,grinding of defect,flaw detection,sampling,marking,flattening,finished product storage and other process steps.
4.2.2 Incoming material should be steel plate rolled by plate mill.
4.2.3 The designed output of shearing line should meet the requirements as specified in Table 4.2.3 below:
Table 4.2.3 Designed output of shearing line

Note:The lower limit of designed output may be selected for producing product of wider range of varieties,narrower average width and thinner average thickness.
4.2.4 Production process and equipment shall meet the following requirements:
1 Dedicated cooling bed or table should be provided,disk or walking type cooling bed is preferred.
2 Slow cooling mode and slow cooling time shall be determined according to steel grade of plate to be rolled,size,chemical composition,smelting and casting process conditions and other factors.
3 Inspection and grinding table should be provided after cooling bed.
4 Plate with internal quality requirement shall be detected by automatic ultrasonic testing device for detecting internal defects,which shall be done fully automatically and continuously.Automatic ultrasonic testing device should be arranged online.
5 Plate mill workshop shall be provided with mechanical shearing line and offline plate cutting equipment.Offline cutting of plate should be done by automatic flame,plasma or laser cutting device.Plasma cutting shall be provided with dust collecting equipment or the cutting shall be done underwater.
6 Plate cutting should be provided with head cutting(tail cutting)dividing shear,double-side trimming shear and cut-to-length shear.5000mm production line should be provided with slitting shear and located near the double-side trimming shear.
7 Trimming should be done by rolling cut type double-side shear or disc trimming shear.
8 Shearing line shall be provided with automatic marking and centering device,head and tail scrap,slitter edge and sample(mother plate)transportation and collection equipment,and finished plate detection and automatic marking machine and other process equipment.
9 Inspection and grinding table should be provided before storage of finished products.
10 Cold straightener should be provided on plate finishing line,and shall be installed withmill scale cleaning and collecting device.
11 Continuous heat treatment line should be provided for plate.Nitrogen protected radiant tube heating roller-hearth,open flame heating roller-hearth furnace or open flame heating dual-walking beam furnace,and continuous rolling type quenching machine and other process equipment should be provided.
Heat treatment of small order,special steel grade,special-sized plate should be done by noncontinuous heat treatment furnace.
12 Shot blasting device should be provided for nitrogen protected radiant tube heating roller hearth furnace.
13 Heat treatment line should be provided with heat treatment straightener.
14 Plate finishing mill may be provided with plate coating line.
15 Plate coating line must be provided with exhaust emission treatment facilities;paint storage room must be designed according to relevant anti-hazard classification when organic coating is used.
4.2.5 Electric drive and automation equipment shall meet the following requirements:
1 Variable speed motor shall be provided with AC speed control system.
2 Shearing line,heat treatment line shall be provided with basic automation and process control computer system.
3 Finishing line should be provided with the same production control computer system as the rolling mill.
4.2.6 Working system and annual working time shall meet the following requirements:
1 Shearing line shall be provided with the same working system and annual working time as the rolling mill.
2 Heat treatment line may be provided with working system and annual working time different from those of the rolling mill.
3 Shot blasting line,painting line and cutting line may be provided with working system and annual working time different from those of the rolling mill.
4.2.7 Process layout shall meet the following requirements:
1 Proper equipment configuration,compact layout,smooth and short process flow and proper buffer storage shall be designed according to such characteristics as diversified product varieties and sizes,small production lot,multiple finishing routes and frequent crossing to and fro with an aim to save land occupation and investment,as well as to reseve the possibility for future expansion with respect to increasing product varieties and improving rolling mill production capacity.
2 Shearing line and rolling mill should be arranged in a straight line,but may be foldback type if limited by general layout and project site.The span of cooling bed bay and shear bay shall be defined according to the configuration of cooling bed and shearing line equipment.
3 Buffer storage area shall meet all kinds of requirements for buffer storage of steel plate.
4 Multiple finished product storages may be arranged according to process flow and general layout;the layout of finished products storage,plate transport means in and out of the storage and the arrangement of crane in finished product storage shall ensure logistics pace of the transport means in and out of the storage.
5 In case of railway as the main transport means,finished product bay should be arranged in parallel with the rolling mill bay;in case of truck transport,finished products bay should be arranged in vertical to the rolling mill bay;the storage time of finished products should be designed for 7 days.Additional finished product storage may be provided outside the workshop if finished product storage is insufficient due to limitation of general layout.
6 Scrap collecting area of shearing line should be located outside the main building of workshop.
7 If heat treatment line is provided with quenching line,separate quenching water treatment station should be provided outside the main building.
4.2.8 The consumption targets per ton product of heat treatment line with quenching machine shall be no higher than those specified in Table 4.2.8-1,the consumption targets per ton product of shearing line shall be no higher than those specified in Table 4.2.8-2.
Table 4.2.8-1 Consumption targets per ton product of heat treatment line with quenching machine

Table 4.2.8-2 Consumption targets per ton product of shearing line
