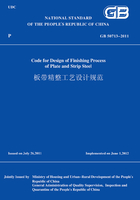
2 Terms
2.0.1 Plate
Plate can be classified into three categories in terms of thickness:medium plate ranging from 4mm to 20mm thickness,heavy plate ranging from 0mm-60mm and thick and extra-heavy plate over 60mm thickness.
2.0.2 Air cooling
To cool hot steel plate in air after it is rolled.
2.0.3 Slow cooling process
It is a technological process to slowly cool hot steel plate by means of slow cooling pit,slow cooling cover or by simply stacking the plates in pile.
2.0.4 Ultrasonic test
It is a method to detect the internal defect of plate by ultrasonic wave.
2.0.5 Shearing & cutting process
Head cutting,tail cutting,trimming,splitting,cutting-to-length,sample cutting may be done by mechanical shearing in accordance with yield strength and thickness of plate.
Head cutting,tail cutting,trimming,splitting,cutting-to-length and sample cutting may be done by flame cutting,plasma cutting,laser cutting and so on if mechanical shear can not cut or to compensate for insufficient capacity of mechanical shear.
2.0.6 Shot blasting process
It is a technological process that takes steel shot as carrier,accelerates steel shot through centrifugal force of shot blasting machine,hits steel plate surface to remove oxide scale on its surface.
2.0.7 Painting process
It is a technological process that sprays paint evenly onto steel plate surface by automatic or manual painting device.
2.0.8 Pickling process
It is a technological process that groups heat treated stainless steel plates and continuously passes them through pickling line to clean mill scale on the plate surface and to passivate the plates.
2.0.9 Hot rolled temper rolling process
It is a technological process that applies small deformation elongation over yield point on hot rolled strip to eliminate Luders wrinkles on strip.
2.0.10 Hot rolled dividing process
It is a technological process that divides hot rolled coil into several small coils.
2.0.11 Hot rolled recoiling process
It is a technological process that recoils hot rolled coil to check strip surface quality or improve coil shape quality.
2.0.12 Hot rolled cut-to-length process
It is a technological process that cuts hot rolled strip to length.
2.0.13 Hot rolled slitting process
It is a technological process that slits hot rolled strip width-wise into strips and then recoils the strips.
2.0.14 Rolling force control
It is a technological control process that controls rolling force to reach preset value and keeps it constant.
2.0.15 Roll bending control
It is a technological control process that controls properly roll bending mode and roll bending force.
2.0.16 Elongation control
It is a technological control process that controls elongation along the strip length direction to reach preset value and keeps it constant.
2.0.17 Side trimming process
It is a technological process that trims strip edge.
2.0.18 Flying shear cut-to-length process
It is a technological process that detects steel plate length and starts flying shear for synchronous cutto-length.
2.0.19 Leveling process
It a technological process that controls roll gap value of leveling roll stack to ensure strip plastic deformation ratio reaches the set value.
2.0.20 Plate piling control
It is a control process that controls piling by plate piler based on production plans such as plate number or pile weight.
2.0.21 Cold rolled recoiling process
It is a technological process that trims cold-rolled coil,inspects surface quality and recoils according to specified coil weight.
2.0.22 Cold rolled cut-to-length process
It is a technological process that cuts cold rolled strip to length.
2.0.23 Cold rolled slitting process
It is a technological process that slits cold rolled strip width-wise into strips and then recoils the strips.
2.0.24 Packing process
It is a technological process that straps and packs cold rolled coil.