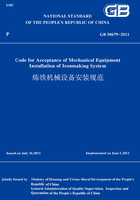
6.4 Part Fabrication and Assembly of Process Steel Structure
6.4.1 Setting out and marking off shall be in accordance with the following requirements:
1 Before setting out,Construction drawing and process requirements shall be known well,the geometric dimension for connecting the elements shall be checked,and problems,in case of discovering,shall be put forward to the relevant departments.The modification of the construction drawing shall be in accordance with those specified in Article 3.0.5 of this standard.
2 For parts of shell and frame and coiled materials of large-diameter coil-welded steel pipe,a computer shall be adopted for setting out and discharging.
3 During setting out and marking off,contraction allowance for welding during manufacturing and installation and working allowance for cutting,edge planning and milling shall be reserved according to the process requirements.
4 The sample plate of elements,such as shell should be made of the steel plate with thickness of 0.8mm-1.0mm and its chord length shall not be less than 1500mm.The sample plate shall be used till passing through self-inspection and special inspection.
5 Before marking off,the oil stain,soil and other contaminations on the surface of the steel shall be cleared away,the steel specification,material,batch shall be checked and the appearance quality of the steel surface shall be inspected.The appearance quality of the steel surface shall be in accordance with those specified in Article 5.3.7 and Article 5.3.8 of this standard.
6 During marking off,the check line,the central line and the bending line shall be marked off,wherein the depths of the lines should not be larger than 0.5mm.A steel scriber should be adopted for marking,and a deviation of 0.5mm is allowable.A slate pencil or chalk line may be used for marking a big workpiece,and a deviation of 1.0mm is allowable.
7 Joint preparation character of weld and blanking method shall be strikingly marked by oil paint.
8 Allowable deviation of marking off shall be in accordance with the following requirements:
1)The allowable deviation of dimension of part is±1.0mm.
2)The allowable deviation of pitch of part is±0.5mm.
9 The external surface of bending part and the places easily causing defects shall not be marked by chisel and punch.
6.4.2 Cutting and planning shall be in accordance with the following requirements:
1 Before cutting,water,oil stain and rust on the surface of the steel shall be cleared away.After cutting,the gas cutting surface shall be free of cracks,slag inclusion and layers,as well as missing edges of larger than 1mm.
2 Parts of elements,such as shell and frame and coiled plate of large-diameter coil-welded steel pipe should be cut by a NC cutting machine or automatic and semi-automatic cutting machine.The low alloy steel plate shall be cut at the ambient temperature of above 0℃.Corresponding measures shall be taken when the temperature is below 0℃.
3 The carbon structural steel at the ambient temperature of below-20℃and the low alloy structural steel at the ambient temperature of below-15℃must not be sheared and punched.
4 The purity of oxygen for gas cutting shall be above 99.5%,that of acetylene shall be above 96.5%,and that of propane shall be above 98%.
5 The edge after gas cutting shall be smooth,the notch may be welded for repairing and polished a bit according to the welding procedure stipulation,and molten overlap at the edge and splash shall be cleared away.The allowable deviation of dimension of workpiece after gas cutting as well as in flatness and roughness of the cutting surface shall be in accordance with those specified in Table 6.4.2-1 and Table 6.4.2-2.
Table 6.4.2-1 Allowable deviation of dimension of workpiece after gas cutting(mm)

Note:The allowable deviation of Table is applicable to the dimension of undeclared tolerance in figure,such as workpiece with length-width ratio of less than or equal to 4:1,and those with cutting perimeter of larger than or equal to 350mm.
Table 6.4.2-2 Allowable deviation of flatness and roughness of cutting surface(mm)

Note:The flatness shall be measured by subtracting the height of the molten angle h.
6 The cut plate shall be corrected.For the defects,including deformation due to cutting,the workpiece number or element number of the part shall be marked to enter the next procedure.
6.4.3 Correction and molding shall be in accordance with the following requirements:
1 The carbon structural steel at the ambient temperature of below-16℃and the low alloy structural steel at the ambient temperature of below-12℃shall not be subject to cold correction and cold bend.
2 The minimum radius of curvature and maximum bending rise of arc of cold correction and cold bend shall meet the relevant requirements of the current national standard GB 50205 Code for Acceptance of Construction Quality of Steel Structures.
3 The steel should be corrected by mechanical equipment at room temperature.The blast furnace shell steel plate may be corrected by a press machine or by flame heating.The surface of the corrected steel shall be free of obvious recess,indenture and other damages.The depth of scratch shall not be larger than 0.5mm.The allowable deviation of the corrected steel shall meet the relevant requirements of the current national standard GB 50205 Code for Acceptance of Construction Quality of Steel Structures.
4 When heating to correct the carbon structural structure and the low alloy structural steel,the heating temperature shall be selected according to the steel performance but shall not exceed 900℃.The heated and corrected low alloy steel shall cool slowly under the natural state and must not be chilled with water.
5 When the part is molded by hot working,its heating temperature should be at 900℃-1000℃and shall avoid"overheating".When the carbon structural steel cools at 700℃and the low alloy structural steel cool at 800℃,machining shall be ended.The low alloy structural steel shall be cooled naturally.
6.4.4 Edge processing and end face processing shall be in accordance with the following requirements:
1 When performing edge processing for the parts subject to gas cutting and mechanical cutting,their planning volume shall not be less than 2.0mm.
2 The allowable deviation of edge processing shall meet the relevant requirements of the current national standard GB 50205 Code for Acceptance of Construction Quality of Steel Structures.
3 End face processing shall be in accordance with the following requirements:
1)When milling both ends flatly,the allowable deviation of length of the element is±2.0mm.
2)When milling both ends flatly,the allowable deviation of length of the part is±0.5mm.
3)The allowable deviation of flatness of milling plane is 0.3mm.
4)The allowable deviation of perpendicularity of the axis of the milling plane is 1/1,500 of the length of the element.
6.4.5 Hole shall be made in compliance with the following requirements:
1 Hole may be processed by a NC machine tool,drilled by a drilling machine and milled by a milling machine.
2 The allowable deviation of surface roughness of the hole wall as well as aperture and pitch of bolt shall be in accordance with those specified in Table 6.4.5-1 and Table 6.4.5-2.
3 When processing the same type of parts in batch,the quality of the aperture,hole locationand hole wall of the first product shall be checked in accordance with those specified in design document and Table 6.4.5-1.In this way,the parts shall be produced in batch.The holes of all part plates shall be scribed and drilled after flattening the element.
Table 6.4.5-1 Allowable deviation of surface roughness of bolt,bolt hole and hole wall

Table 6.4.5-2 Allowable deviation of pitch of bolt(mm)

Notes:1 All bolt holes of the connecting plate connected with a rod piece in node are taken as one group.
2 The bolts of butt joint at one side of the splice plate are taken as one set.
3 Screw holes between two adjacent nodes or joints are taken as one set,but not including the bolt holes as specified in Article 1 and 2 of this note.
4 The connection bolt holes on the flange of bending part within every meter are taken as one set.
4 The surrounding of the manufactured bolt hole shall be free of burrs,horn openings or concaveconvex traces.The cutting chips shall be cleaned.
5 When the allowable deviation of pitch of bolt exceeds those specified in Table 6.4.5-2,the welding electrode matched with the material of the base metal shall be adopted for repairing welding and the hole shall be reproduced after polishing.
6 The great number of high-strength bolt holes should be processed by the digital controlled drill.When adopting a radial drill due to larger side of element,a drill plate shall be adopted for drilling.
6.4.6 The processing of the friction surface shall be in accordance with the following requirements:
1 The friction surface shall be processed by a mechanical shot blasting method.The mechanical shot blasting method is difficult to cover the local surface,so a grinding wheel polishing method may be adopted for processing.
2 Pneumatic or electric grinding machine may be adopted for the friction surface processed by the grinding wheel polishing method.The grinding wheel polishing method shall be in accordance with the following requirements:
1)The polishing direction shall be perpendicular to the forcing direction of the element.
2)The polishing range shall not be less than 4 times of the diameter of the bolt hole.
3)The polished surface shall be metallic luster.
4)After polishing,the bolt shall be installed after producing rust period and removing it.
6.4.7 Assembly shall be in accordance with the following requirements:
1 Before assembling,the assembling personnel shall be familiar with the construction drawing,the assembling process and the provisions related to the design document,and check the appearance,material,specification and quantity,etc.of the assembling parts.
2 Rust,burrs,contamination,ice and snow and rainwater within the range of 30mm-50mm to the edge of the assembled joint surface and welding seam shall be cleaned before assembling.
3 The concealed part of the element shall be welded,coated,and assembled till passing through the examination.The completely enclosed internal surface may not be coated.
4 The element shall be assembled on a working platform,a rack or a molding bed for assembling.After shaping,the working platform,the rack,the molding bed or the assembling bulk sample shall be assembled after passing through examination.
5 The contraction allowance shall be pre-released for the geometric dimension of the welding element according to the contraction distortion condition of the welding seam.
6 The space between the flange plate splicing seam and the web splicing seam of the welding Hshaped steel in elements,including frame,corridor and truss shall not be less than 200mm.The splicing length of the flange plate shall not be less than double of its width,and the splicing width of the web shall not be less than 300mm.Its length shall not be less than 600mm.The butt weld in longitudinal and transverse directions may adopt crossed intersection or T-shaped intersection.When adopting the T-shaped intersection,the space of the intersection shall be larger than or equal to 200mm.
7 The allowable deviation of dislocation of axis crossing point of trusswork rod is 3.0mm.
8 When assembling by the clamp,the base metal must not be damaged during disassembling the clamp,and the residual crater shall be polished smoothly.
9 More than 75% of the supporting contact surface shall be supported closely,a 0.30mm feeler gauge shall be used for checking,its filling area shall not be less than 25%,and the edge gap shall not be larger than 0.8mm.
6.4.8 Preassembly of the element shall be in accordance with the following requirements:
1 For the elements with ultra-long and ultra-wide process steel structure,the ordering organization shall put forward technical requirements of subsection,blocking,fragmentation or subdivision manufacture and transportation to the manufacturer according to the installation and transportation conditions.
2 The following preassembly shall be conducted for the following structures in the manufacturer:
1)Shells of blast furnace and smelting reduction ironmaking furnace.
2)Hot air ring pipe.
3)Main truss of blast furnace frame and rigid frame as well as support of furnace top equipment.
4)Hot-blast stove bottom and first ring connected therewith.
5)Arched shell of hot-blast stove,arched ring beam of external combustion hot-blast stove and corresponding shell.
6)Tapered part of shell of dust remover,washing tower and Venturi-tube washer and shell of bearing.
7)Main truss of charging skew bridge and upper discharging section of skew bridge.
8)Corridor and truss of belt charging equipment.
9)Frame of head and tail of vertical charging equipment.
10)Elements specified in design document or appendix to contract.
3 Preassembly in plant or grouping on installation site shall be conducted on solid and stable platform,bearing stool or molding bed and the foundation shall be compacted or padded with gravel to flatten.Structural steel or steel track should be used as base frame for assembling platform for furnace shell.The base frame made of structural steel or steel track shall be paved with steel plate thereon according to the requirements for assembly.The height difference of the upper surfaces of the platform,the bearing stool or the molding bed must not be larger than 2mm.
4 The element number,center line and butt mark shall be marked for the element,of which the preassembly is qualified.The elements,including shell shall be obviously marked with 4-core point of 0°,90°,180° and 270° through sample punch marks and paint.
5 The allowable deviation of preassembly of process steel structure of blast furnace shall meet the requirements of Appendix B of this standard.