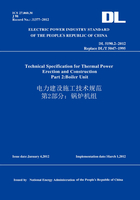
10.2 General Rules for the Erection of Auxiliary Machineries
10.2.1 The foundation inspection and lineation shall meet the following requirements:
1 The foundation of coal mill submitted to installation shall be accepted according to the requirements of Appendix N.Other foundations shall be accepted according to the requirements of Appendix F,and the installation shall be started when the strength of foundation concrete reaches 70% of the regulated strength.
2 The foundation lineation shall be carried out with reference to the main plant building benchmark location or the boiler longitudinal and transverse center lines.The allowable deviations of the elevation and the longitudinal and transverse center lines shall meet the requirements of Appendix N or Appendix F.
10.2.2 When the secondary grouting is carried out with common fine stone concrete,the installation of anchor bolts and pad irons shall meet the following requirements:
1 Before the erection of the foundation frame,the upper surface of the foundation shall be processed into the rough surface and cleaned up.Any foundation surface shall not be contaminated with oil stains during construction.
2 The clearance between the upper surface of the foundation and the bottom of equipment foundation frame shall not be less 50mm,and the secondary grouting concrete shall meet the design requirements.
3 The foundation framework fixed with the anchor bolts shall meet the following requirements:
1)The allowable deviation in verticality of anchor bolts shall be 1/100 of the bolt length and it shall not exceed 10mm.
2)If the motion anchor bolts are used,the back caps or locking devices shall be provided in the upper and lower ends,and the support bottom plate and the concrete bearing force surface shall be in good contact.
3)After the screw caps(including the back caps or locking devices)have been tightened,2 bolt threads-3 bolt threads shall be exposed.
4)The anchor bolts for grouting shall be clean,and the threaded portion shall be pasted with grease.
5)The bottom ends of the anchor bolts for grouting shall not be contacted with the hole ends or hole walls,and the spacing between the hole ends shall not exceed 100mm.
6)For the anchor bolts being equipped with the pre-buried sleeves,the grouting to the anchor bolts shall be carried out according to the design requirements after the alignment of machineries.
4 The concrete surfaces for placing the pad irons must be processed in the flat mode and the longitudinal and transverse direction shall be in the level situation.The contact surfaces between the pad irons and concrete shall be even,and its proportion shall not be less than 75%.
5 The width of each group of pad irons shall be among 80mm-200mm.The length shall be 20mm longer than the width of the foundation framework.The inclination of the tilted pad iron shall be within the range of 1:10-1:20,and the thin edge shall not be less than 4mm.
6 The area for the required pad iron group may be calculated by the following equation.
If a group of pad irons are placed on the concrete foundation or floor,its area may be calculated by the following approximation equation.

Where:A—The pad iron area,mm2.
Q1—The weight of the equipment and other items load on the pad iron groups,N.
Q2—The pressure in the pad iron groups due to the tightening force of the anchor bolts,N,which may be taken as the allowable tension stress for the bolts.
R—The unit area compressive strength of the foundation or floor concrete,MPa,which may be taken as the concrete design strength.
C—The safety coefficient,which may be taken as the value among 1.5-3.
7 Each pad iron group shall include two flat pad irons and one pair of tilted pad irons.The thicker pad iron shall be placed in the lower layer.Both ends of pad irons extending out of the base frame shall be even,and pad irons shall be placed orderly.
8 The pad iron surface shall be flat.The contact between the pad irons and the pad irons and the foundation framework shall be good.For any large scale auxiliary machinery,inspection shall be carried out with a feeler gauge(accuracy:0.1mm)and the inserting depth shall not exceed 20% of the contact length for the pad iron.
9 According to the equipment situation,one group of pad irons shall be equipped beside each anchor bolt.One group of pad irons shall be arranged beside the both sides of each anchor bolt for the large scale fans and coal mills,respectively.Under the condition of not influencing the secondary grounting,pad irons shall be close to anchor bolts as far as possible.The maximum spacing between two groups of pad irons shall not exceed 500mm.
10 After the erection of machineries,the pad irons shall be inspected by slightly tapping with the small hammer so that there shall be no loosening and all pad irons shall be fixed tightly by spot welding.The re-inspection shall be carried out again to the erection and alignment data for machineries after the spot welding has been carried out and the erection and alignment data shall be recorded.
10.2.3 When the secondary grouting is carried out with cement base grouting material,it shall comply with the related requirements of GB/T 50448-2008 Code for Application Technique of Cementitious Grout.The buried pad iron method(also known as base slurry method,shown in Figure 10.2.3)shall be used preferentially,and the configuration of pad irons and anchor bolts shall still meet the requirements of Article 10.2.2.The elevation of buried pad irons shall be 0-2mm lower than the design value.The thickness of the buried concrete from the bottom of pad irons to the rough surface of the foundation shall not be less than 40mm,and the thickness of pad irons shall not be less than 20mm.After pad irons have been pre-buried for 48h or the strength of concrete has achieved 75% of the design value,the equipment can be in place.The equipment elevation shall be adjusted by washers during the alignment of the equipment.

Figure 10.2.3 The pre-buried pad iron erection schematic diagram
10.2.4 The installation of the sliding bearing shall meet the following requirements:
1 The babbitt surface of bearingbush shall be smooth without sand inclusion,porosity and cracks.There shall be no shelling between bearingbush and babbitt surface when inspecting with hammering method.The surface shall be silver without yellow spots.If any bearingbush surface needs to repair,the same material shall be selected and the approval shall be obtained from the manufacturer.
2 The coordination between the journal and the bearingbush shall meet the requirements of equipment technical documents.If there is no requirement,the following requirements shall apply:
1)The contact angle between the journal and the work bearingbush surface shall be 45°-90°.The work bearingbush surface shall be inspected by color printing method,and the contact surface shall not be less than 1point/cm2-2points/cm2.The journal shall be assembled in the bearingbush and their coordination clearance shall meet the requirements of Table 10.2.4.In accordance with the rotation direction of the shaft,there shall be a longitudinal oil guide groove at the edge of bearingbush.The schematic diagrams for the clearance between the journal and bearingbush top and that of both sides are shown in Figure 10.2.4-1.

Figure 10.2.4-1 The schematic diagram of the clearance between the journal and bearingbush top and that of both sides
Table 10.2.4 Coordination clearance between the journal and the bearingbush(mm)

Notes:the side clearance is s/2.
2)The schematic diagram for the axial clearance between the bearingbush end and the baffle ring is shown in Figure 10.2.4-2,and the following requirements shall apply:
The axial clearance of the thrust bearings:a+b=0.30mm-0.40mm
The expansion clearance of the load-bearing bearings shall be determined by the thermal elongation of the shaft,which may be calculated by the following equation:

Where:l—The value of thermal elongation,mm.
t—The maximum temperature of the medium surrounding the shaft,℃.
L—The length of the shaft between two bearings,m.
The other side clearance for the loaded bearing:d>b.
The contact plane between the thrust ring and the thrust bearing shall be good,and the color printing inspection shall be carried out according to 1point/cm2 at least,and the clearance deviation|b1-b|≤0.05mm.

Figure 10.2.4-2 The schematic diagram of the clearance between the bearingbush end and the baffle ring
3 The bearingbush shall not rotate within the bearing shell.There should be 0.02mm-0.04mm interference(tightening force).The joining surface of the spherical bearingbush shall be inspected with the color printing inspection method.There shall be no less the 1point/cm2 for the color printing inspection,and the distribution of the contact points shall be uniform.The rotation shall be flexible,and there shall be no jam.
4 The bearingbush end for the axial location of the rotor and the shaft shoulder end shall be in good contact,and there shall be no less the 1 point/cm2 for the color printing inspection.
10.2.5 The erection of the rolling bearing shall meet the following requirements:
1 The bearing types shall meet the design requirements.There shall be no crack,double skin,rust or other defects on the surfaces.The total travel clearance of the bearing shall meet the requirements of equipment technical documents.
2 The assembly tightening force in the bearing journal shall meet the requirements of equipment technical documents.There shall be no sliding between the inner sleeve and the shaft,and washers shall not be placed.
3 The axial and radial coordinations between the bearing outer sleeve and the shell shall meet the requirements of equipment technical documents.There shall be enough expansion clearance for the bearing at the expansion end.If there is no requirement,its expansion value may be calculated by the equation(10.2.4).
4 When the bearing is heated by hot oil,the oil temperature shall not exceed 100℃.And the bearing shall not contact with the bottom of the heating container during heating.
10.2.6 The erection of the bearing seat shall meet the following requirements:
1 There shall be no crack,sand inclusion or other defects in the bearing seat,and there shall be no burr and molding sand in the inner and outer surfaces of the bearing seat.
2 Before erection,cooling-water pipes of cooling-water chamber or oil chamber in the bearing seat shall pass hydrostatic test.The test pressure shall be 1.25 times the cooling-water design pressure.
3 There shall be 3 adjustment washers(excluding the insulation piece)between the bearing seat and the bedplate at most,and the area of the washer shall not be smaller than that of the supporting surface of the bearing seat.
4 The radial clearance between the shaft and the shaft seal clamp ring shall meet the requirements of equipment technical documents.The shaft seal shall be tight without leakage.
5 The filling lubrication grease amount of the rolling bearing shall not exceed 2/3 of the whole bearing chamber volume for the low speed machineries,and it shall not exceed 1/2 of the whole bearing chamber volume for the machineries whose rotating speed is more than 1500r/min.
6 When installing the oil level gauge,the marking scale shall be re-inspected.The bottom roller of the rolling bearing shall immerge into the 1/3-1/2 position of the oil depth.
10.2.7 The installation of the coupling shall meet the following requirements:
1 The couplings shall be used in pair,and they shall not be misused.
2 When assembling the coupling,washers shall not be placed or the shaft shall not be struck to get the tightening force.
3 When centering two half couplings,the allowable deviation of the circumference and the end shall meet the requirements of Table 10.2.7.
Table 10.2.7 Allowable deviations of the circumference and the end(mm)

Notes:1 If the work bearingbush is the upper bearingbush,the shaft center displacement during operation shall be taken into account for finding the center.
2 The shaft center lifting value for the bearing seat,the bearing and the shaft during operation due to the thermal expansion shall be taken into account for finding the center.
3 During the alignment of couplings,magnetic force center line of the motor shall be taken into account.
4 The clearance between two half couplings shall meet the requirements of equipment technical documents.The minimum clearance shall exceed the total of the shaft elongation and the shaft offset during operation.
5 When installing the styluspin couplings,the metal part of the styluspin and the styluspin hole shall be consistent,and the rubber ring shall be sheathed tightly in the styluspin.The clearance between the styluspin hole and the rubber ring shall be 0.5mm-2mm,and the styluspin screws shall be equipped with the locking devices.
6 After installing all styluspins,the manual barring gear shall be inspected to verify the contact situation of all action surfaces between styluspins and rubber rings.
7 After the gear sleeve of the gear coupling meshes with its gear,it shall be ensured that the gear sleeve twists flexibly on the gear.After assembly,filling oil shall be carried out according to the requirements of equipment technical documents.
8 The coupling shall be equipped with the protective cover,which shall be fixed tightly and which shall be beautiful and neat as well as convenient for disassembling.
10.2.8 The erection of the shaft and the key shall meet the following requirements:
1 When assembling the shaft,the ellipticity and conicity of the bearing journal shall be reinspected,whose deviation values shall meet the requirements of equipment technical documents.In general,the deviation of the sliding bearing shall not exceed 1/1000 of the diameter,and the journal diameter deviation of the rolling bearing shall not exceed 0.05mm.
2 If necessary,re-inspection shall be carried out to the shaft bending value,which shall not exceed 0.05mm.
3 For the coordination between the key and the keyway,there shall be no clearances in the both sides and the key tightening force shall not be increased with the adding pad method.The top(namely radial direction)clearance shall be among 0.10mm-0.40mm.
4 The erection horizontality deviation of the shaft shall not exceed 0.2/1000.
10.2.9 The erection of the reducer shall meet the following requirements:
1 The assembling condition of the gear and shaft shall be inspected.And there shall be no loose.
2 The meshing situations between the gear,worm gear and worm screw shall be inspected with color printing method.In general,the meshing size shall not be less than 40% of the tooth height and not be less than 80% of the tooth width.
3 The tooth side clearance and the tooth top clearance on the meshing shall meet the requirements of equipment technical documents.
4 The joining surface between the machine cover and the machine body shall be tight without leakage.
5 The reducer with the pressure oil lubrication mode shall meet the following requirements:
1)The oil cooler and the inner and outer walls of the oil pipes shall be clean,and there shall be no dust,sand and rust.The filter screen shall be in good condition.
2)Hydrostatic test for the oil cooler shall be qualified and the test pressure shall be 1.25 times of the cooling water design pressure.
3)The installation of the oil system shall be firm and tight.
6 After the assembly has been carried out,the manual barring inspection shall be carried out to the reducer.The rotation shall be flexible and the meshing shall be smooth.
10.2.10 The installation of actuators shall meet the following requirements:
1 Gear actuators shall be installed according to the requirements of Articles 10.2.9-2-4.
2 Belt actuators shall be installed according to the following requirements:
1)The central plane in the width direction of two belt pulleys equipped in two parallel shafts shall be in the same plane,whose allowable offset value a(as shown in Figure 10.2.10)shall not exceed 1mm.

Figure 10.2.10 The schematic diagram of the center offset for two belt pulleys
2)The triangle belt type shall be consistent with the belt pulley groove type,and the belt shall be tightened consistently.
3 Two shafts in the sprocket actuators shall be parallel,and the coordination between the sprocket and the chain shall be good.The rotation shall be flexible,and there shall be no jam fault.
4 The exposed actuator shall be fixed and assembled firmly and beautifully,and the protective cover being convenient for disassembly shall be equipped.
10.2.11 The equipment secondary grouting shall meet the following requirements:
1 The following conditions shall be ready before the secondary grouting:
1)The equipment alignment and fixing have been completed.
2)The welding quality for the welding locations shall meet the requirements.
3)There shall be no loosening for the pad irons and anchor bolts based on the inspection.
4)The dirt,welding slag and so on in the foundation surfaces and the foundation frameworks shall be removed completely,and the certification for any concealed work shall be handled.
2 The secondary grouting shall meet the design requirements and the related requirements of GB 50204 Code for Acceptance of Constructional Quality of Concrete Structures.
3 Before the strength grade of the secondary grouting layer achieves 70% of the design strength grade,the works such as tightening anchor bolts,the secondary alignment of couplings and connecting the pipes and so on shall not be carried out.
10.2.12 The sub-section trial operation shall meet the following requirements:
1 The sub-section trial operation shall meet the requirements of equipment technical documents,and the approved technical scheme or measures shall be taken.
2 The following conditions shall be ready prior to the sub-section trial operation:
1)The equipment needing trial operation shall have been installed and pass the inspection.
2)The strength grade of the secondary grouting concrete has achieved the design strength grade.
3)The erection of piping system related to the equipment has been completed and the trial operation conditions of the equipment are ready.
4)The lubricant has been added and it shall meet the quality requirement by inspection.
5)The marks such as the rotation direction of the rotating equipment,the opening and closing of dampers and so on shall be clear and correct.
6)The work of the related majors(such as electricity,thermal control,corrosion protection and insulation and so on)has been carried out so as to meet the requirements of the trial operation.
7)The site conditions for the trial operation(including the lighting and communication,fire fighting facilities and so on)shall meet the requirements of the trial operation.
3 The following inspections shall be carried out before the sub-section trial operation:
1)The internal condition of machineries and the connection system(such as flue gas ducts,air ducts,raw coal pipes boiler setting and so on)shall be inspected to confirm that there is no sundry or woker inside.
2)Anchor bolts and connecting bolt shall not be loose.
3)The exposed rotating part shall be equipped with the protective cover or fences.
4)The flushing for the matched cooling water system has been qualified,and the cooling water shall be sufficient and the return water shall flow smoothly.
5)The ventilation system of the motor shall be clean and sealed well.
4 The motor which can be disconnected with the mechanical parts shall be firstly put into trial operation for at least 2h.The rotating direction shall be correct.The accident button shall work normally and reliably.After passing the trial operation,it shall make a test run with the mechanical parts.
5 For the start-up of the mechanical equipment,the following safety matters shall be noticed:
1)All couplings shall have been installed.
2)The moving of the couplings shall be without abnormal condition(except those couplings unable to move).
3)For the first start-up,the mechanical equipment shall be stopped by the accident button after achieving the full speed.And then,after observing the bearing and rotating parts to confirm that there is no friction and other abnormal conditions,it can start formally.
6 The trial operation time of mechanical parts shall meet the requirements of equipment technical documents,and mechanical parts shall run continuously for 4h-8h.
7 During sub-section trial operation,the temperature,vibration and current,inlet and outlet pressures and so on ofeach machinery parts shall be inspected and recorded,which shall not exceed the regulated values in thedesign.
8 The indexes for sub-section trial operation shall meet the requirements of equipment technical documents,and the following requirements shall apply:
1)There shall be no abnormal condition for the bearing and the rotating parts.
2)The work temperature of the bearing shall be stable.The work temperature of the sliding bearing shall be no higher than 65℃,and the work temperature of the rolling bearing shall no higher than 80℃.
3)The bearing vibration value(dual-amplitude)shall meet the requirements of Table 10.2.12.
Table 10.2.12 Allowable deviation of the bearing radial amplitude(mm)

4)There shall be no oil,water and air leakages and other phenomenon.
5)When using the circulating oil lubrication system,the oil pressure and the filling oil amount shall meet the requirements.If there is a valve in the oil pipes,the measures shall be taken to prevent the mis-closing or vibration self-closing.
6)The noise for the important auxiliary machineries(such as fans,coal mills and so on)shall meet the guarantee value in the manufacturers'contracts.
9 After sub-section trial operation,the certification for the sub-section trial operation shall be handled in time.