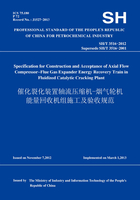
5.4 Shaft End-to-end Distance Confirmation and Shaft Alignment
5.4.1 When confirming the shaft end-to end distance,the axial position of each shaft shall comply with the following requirements:
a)Thrust disk of gearbox's low-speed shaft shall be tightly against thrust pads and the distance between the end face of high-speed rotor and the machining face of the casing shall conforms to provisions of product technical documents;
b)The thrust disk of axial compressor and flue gas expander is tightly against the main thrust pad;c)The rotor of motor/generator is located at the center of magnetic force.
5.4.2 When confirming the shaft end-to-end distance,take two shaft ends as the measuring datum.The space of each shaft ends shall conform to the product technical documents.Meanwhile,verify the dimension of spacing shaft.
5.4.3 When measuring and calculating the distance between diaphragm coupling ends or flange surfaces of half coupling,pre-tensile/pre-compression amount shall be considered.The allowable deviation shall be in conformity with the design documents.If not specified in the design documents,it shall conform to Table 5.4.3.
Table 5.4.3 Allowable deviation of space between diaphragm coupling ends(mm)

5.4.4 The shaft alignment of the machine train shall be in accordance with the alignment curve in cold state provided in the technical documents and measured by means of the laser or dial indicator.If the dial indicator is used,the stand of it should have enough rigidity and be marked with deflection value on obvious position.For laser alignment and double dial indicator alignment,see SH/T 3538 and for single dial indicator alignment,see Appendix B.
5.4.5 The preliminary alignment(primary alignment)of the machine train shall comply with the following requirements:
a)Take the gearbox as the benchmark and conduct primary alignment after rotor of axial compressor seated in situ and before the upper casing to be covered;
b)Achieve the primary alignment by adjusting the base screws or shims;
c)Verify the shaft end-to-end distance after primary alignment.
5.4.6 The secondary alignment shall comply with the following requirements:
a)Conduct the secondary alignment upon completion of machine examination,cleaning and assembly;
b)Fine tune vertical direction with adjusting shim under body support and horizontal direction with support horizontal adjusting screws.
5.4.7 The secondary alignment shall comply with the following requirements if the bearing seat and casing of the axial compressor are separate.
a)Complete the adjustment of axis position as per the alignment curve prior to covering of the axial compressor;
b)Use dial indicator to check the displacement of casing and shaft;
c)Recheck the dynamic/static clearance of axial compressor in conformity with the provisions of product technical documents after the machine train alignment.
5.4.8 The re-examination of the alignment shall comply with the following requirements:
a)The re-examination shall be done prior to machine running test;
b)Adjusting shim could be used to correct deviation;
c)The influence of ambient temperature should be considered;
d)The allowable deviation shall comply with provisions of product technical documents.If not specified,radial displacement is 0.04mm and axial incline is 0.02mm.