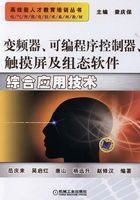
1.6 三相永磁同步电动机的变频调速传动
1.6.1 三相永磁同步电动机的发展过程
世界上第一台电动机就是利用永久磁铁制造的。由于早期的永磁材料磁性能很低,所制造出的永磁电机非常笨重,工业应用受到极度限制,很快被电流励磁电机所取代。随着铝镍钴和铁氧体等永磁材料的出现,永磁电机在20世纪30年代又开始得到发展,铝镍钴具有较高的剩余磁通密度,但矫顽力很低,容易失磁;铁氧体具有较高的矫顽力,但剩余磁通密度较低,两者均不是理想的永磁材料。直到20世纪60年代,稀土永磁材料的发现推动了永磁电机的迅速发展。稀土材料具有铝镍钴和铁氧体两种永磁材料的优点,到目前为止,在永磁电机上实际采用的钕铁硼稀土材料,剩余磁通密度高达1.06T,矫顽力达到720kA/m,磁能积达286kJ/m3。
永磁同步电机转子上装有永磁体,定子铁心上绕有三相电枢绕组。在电动机轴的非负载端装有检测永磁体磁极位置的传感器,实现电子换向。电枢绕组接在可控制的变频电源上,由磁极位置信号控制同步伺服电动机电枢电流的相位,保证转子磁场方向与电枢电流矢量在空间正交。电枢绕组空间的磁场是由转子上的永磁体产生的,转子上没有励磁绕组,也不需要引入励磁电流,电动机内部的发热只取决于电枢电流,定子铁心直接裸露于外界空间,保证了散热条件。同时,永磁体产生的恒定磁场总与可控制的定子电流正交,电磁转矩和定子电流具有线性关系,这一点与直流伺服电动机相同。
图1-33 早期的铝钴镍永磁 同步电动机转子结构
永磁同步电动机的磁极结构型式随永磁材料性能的不同和应用领域的差异,具有多种方案。早期的铝镍钴永磁同步电动机转子结构沿用了传统的同步电动机结构型式,其转子结构如图1-33所示。根据铝镍钴材料矫顽力小、剩余磁通密度高的特点,磁极采用截面小、极身长的形状。后来永磁电动机中较多地采用铁氧体,它的矫顽力比较大,而剩余磁通密度比较小,磁极形状需做成扁平式,这种磁极的截面大,而长度比较短。为了便于把永磁体固定在转子上,铁氧体永磁同步电动机的转子常采用图1-34a所示的结构。在采用稀土永磁体的电动机中,由于稀土永磁材料的磁能积很大,矫顽力和剩余磁通密度都很高,往往只要一片磁体即能满足产生电动机磁场的要求。因此,在稀土永磁电动机中,永磁体常做成瓦片式(薄片式)贴在转子的表面,或嵌在转子铁心中。图1-34b为内转子式永磁同步电动机磁极结构,永磁体嵌在铁心中。图1-34c为外转子型,永磁体贴在转子的内表面上。
永磁无刷电动机按磁场和电流波形,可分为梯形波磁场方波电流型和正弦波磁场正弦波电流型。前者系统比较简单,转矩波动较大,不宜用作直接驱动;后者伺服系统较复杂,转矩波动小。目前用于直接驱动的主要是后一种型式。
1.6.2 永磁同步电动机的结构和变频调速传动基本原理
同步电动机是以其转速n和供电电源频率f之间保持严格的同步关系而命名的,即只要供电电源的频率f不变,同步电动机的转速就恒定为常值。永磁同步电动机的定子与异步电动机一样,只是在转子表面嵌有永磁铁(钕铁硼),因此转子就没有集电环和电刷了,如图1-35所示。
当定子的三相绕组通入对称的三相电流后,就会产生一个空间旋转磁场,旋转磁场的同步转速n0为
n0=60f/pn
式中 f——定子电源频率;
pn——电动机极对数。
永磁同步电动机的永磁磁场可以设计得较高,因此永磁同步电动机的功率密度可以做得较大,也就是同容量的永磁同步电动机比异步电动机小很多。此外,多极、低速、大转矩的特性非常适用于电梯驱动系统。
根据图1-36所示的永磁同步电动机矢量图,永磁同步电动机运转前,必须设法检测转子的位置θ=∫ωdt。然后希望Is与d轴,即与M轴的夹角θs≈90°,这样:Ism=Id=Im=Iscosθs≈0,即定子电流没有励磁分量。Ist=IQ=Issinθs≈Is,即定子电流完全为转矩分量。
T=CmψRIst=CmψRIs
所以永磁同步电动机必须有转子位置检测器随时检测转子的位置,然后控制定子电流矢量。为使变频器工作在最佳状态,还需使变频器对所驱动的电动机进行参数自学习。
图1-34 新型的永磁同步电动机转子结构
a)铁氧体 b)稀土永磁体内转子 c)稀土永磁体外转子 1—起动笼 2—极靴 3—永磁体 4—转子轭 5—转轴 6—定子
图1-35 永磁同步电动机结构
图1-36 永磁同步电动机矢量图
1.6.3 永磁同步电动机变频调速直接驱动伺服系统
所谓永磁同步电动机直接驱动伺服系统就是电动机与其所驱动的负载直接耦合在一起,中间不存在任何减速机构。可以说直接驱动系统是伺服系统的必然发展趋势,是一种较为理想的驱动方式。直接驱动系统消除了存在于传统驱动方式(电动机+减速机构+负载)中的诸多弊病,具有很高的伺服刚度和传输效率快速的动态响应和精密确定位精度。
直接驱动系统主要由以下几个部分组成:低转速、高转矩电动机,高精度、高分辨率角度传感器,快速响应的功率放大器,高分辨率、高精度的速度控制环节,高性能速度、位置伺服控制器,计算机接口和保护环节等。角度和速度测量环节是角度传感器的接口与信息变换电路。它的功能是实现位置的高精度测量,实现位置闭环控制,同时还可以给出电动机转子磁场的精确位置,从而实现电动机的换相控制。速度测量用于实现速度闭环和电流幅值控制。在现有的磁性材料下,由于低转速高转矩电动机的几何尺寸较大,所以其电感较大。因此,为了提高电动机的响应速度,电动机的功率放大器采用PWM技术,同时在功率放大器内设有高增益反馈电流环,以减小电流的响应时间。电动机的换相控制是根据转子的磁极位置信号、电动机的转速及转矩大小来改变电动机各相绕组电流的相位角和幅值实现的。除电流环外,系统的其他功能分别由计算机来完成。接口电路的功能是接收计算机的指令(位置、速度或转矩等),有并行和串行两种工作方式。保护环节是系统工作所必需的安全保护措施。
1.永磁同步电动机的控制方式
永磁同步电动机控制方式的选择一般是根据电动机转矩和电流之间关系的线性度、控制过程中电动机端电压的允许变化程度、功率因数和电枢反应的去磁效应等四个方面的因素综合比较来确定的。常用的控制方式有以下四种。
(1)id=0控制方式
永磁同步电动机的相量图可用图1-37a来表示。图1-37a中,ψf为永磁体产生的磁链;Eo为由ψf引起的电动势,为电动机负载运行时电枢电流;
、
分别为
在d、q轴上的分量;Ψ∂d、Ψ∂q分别为
、
在d、q轴上产生的磁动势引起的磁链;Ψm为电动机的合成磁链;Em为Ψm引起的电动势;
为电动机端电压;θ为
和
的夹角;γ0为电枢电流与q轴的夹角,δ为同步电动机的功角。
图1-37 永磁同步电动机的相量图
a)永磁同步电动机的相量图 b)id=0控制方式的相量图 c)cosΦ=1控制方式的相量图 d)总磁链恒定控制方式的相量图
如控制逆变器的导通相位角γ0=0,则i0=0,电枢电流中没有励磁分量,图1-37a中的Ψ∂d 为零,不会引起永磁电动机退磁现象;此时的同步电动机相量图如图1-37b所示。这时,电动机的电枢反应只存在于交轴(即q轴),功角和电动机端电压均随负载增加而增大。这种方法曾广为采用,这种控制方案要求逆变器的输出电压高,容量比较大。
(2)cosϕ=1控制方式
在这种控制方式中,通过控制γ0角,使γ0=δ,始终保持功率因数cosΦ=1。此时电动机的相量图如图1-37c所示,电枢电流I与γ0角之间应保持以下关系:
在永磁同步电动机中,由于转子励磁不能调节,在负载变化时,电枢绕组的总磁链无法保持恒定,所以电枢电流和转矩之间难以保持线性关系。
(3)转矩线性控制方式
为了在永磁电动机中能够获得电磁转矩和电流之间的线性关系,应满足式(1-60)所列条件:
这时,电动机的电磁转矩与电枢电流成正比T∞I,电动机有较好性能。
(4)总磁链恒定控制方式
采用此种控制方式,在电动机运行过程中,始终保持电动机内电枢电流与永磁体的合成磁动势引起的磁链Ψm大小不变,因而电枢绕组电动势Em保持不变,从而使电动机的端电压基本保持恒定,其相量图如图1-37d所示。这时
根据式(1-61)可以计算出不同转子结构、在不同控制方式下的永磁同步电动机特性。综合这些特性的规律,将各控制方式的特点列表比较,见表1-1。
表1-1 不同磁极结构、不同控制方式下永磁同步电动机特点比较
2.永磁同步电动机的主电路、永磁同步无齿轮曳引机及变频调速驱动系统
(1)永磁同步电动机的主电路:永磁同步电动机没有励磁绕组,因此节省了励磁供电电路,省去了同步电动机的电刷—集电环装置,使电动机结构紧凑、体积减小、效率提高。
图1-38 永磁同步电动机的主电路
a)矢量控制变频电源供电 b)自控式变频供电
永磁同步电动机的主电路就是对定子三相绕组供电的电路,其主电路如图1-38所示。
图1-38a是一个采用大功率晶体管(GTR)或绝缘栅双极型晶体管(IGBT)组成变频器给同步电动机供电的主电路,为提高系统性能,通常采用矢量控制方式进行控制。
图1-38b是一个采用晶闸管组成变频器给同步电动机供电的主电路,在这种供电方式下,通常采用自控式变频方式进行控制。在这种控制方式下,控制系统不断地检测转子位置,在自然换相点之前γ角(γ角被称做换流超前角)触发需要导通的晶闸管,利用电动机的反电动势来关断应退出的晶闸管,实现晶闸管之间的换相。这样就不需要设置晶闸管的关断电路,控制电路结构简单。在自控式方式下,同步电动机不会失步,工作比较可靠。由于这种方式相当于直流电动机供电,因此把这样的系统称作无换向器(直流)电动机。无换向器电动机多用于大功率场合。
(2)永磁同步无齿轮曳引机:采用永磁同步电动机的电梯曳引系统通常为无齿轮曳引方式,这样可以充分发挥永磁同步电动机易于做成低转速、大功率的优点。一种新开发的永磁同步无齿轮曳引机的结构如图1-39所示。它集曳引电动机、曳引轮、电磁制动器、光电编码器于一身,结构紧凑,功能齐全,易于安装,便于使用。
(3)永磁同步无齿轮曳引机变频调速驱动控制系统:原理如图1-40所示。与异步电动机变频调速系统相比,当负载变化时,异步电动机通过调整转差来适应,而同步电动机则只是调节夹角δ(见图1-37),因此同步电动机响应速度更快。因磁场的大小、方向随时都要确定,其控制系统需要配置精确的转子位置检测装置和电压电流检测装置。转子位置的精确控制是永磁同步无齿轮曳引技术的重要组成部分之一,它将直接关系到电梯起动、制动的舒适性和平层精度。
图1-39 永磁同步无齿轮曳引机结构
图1-40 永磁同步无齿轮曳引机变频调速驱动系统
1—永磁同步电动机 2—转子位置传感器 3—曳引轮 4—对重 5—轿厢 6—轿厢负载检测传感器
永磁同步电动机转子位置传感器常使用光电编码器和旋转变压器等。光电编码器有增量式和绝对式两种。增量式光电编码器具有结构简单、使用方便等优点,但长期使用容易造成累积误差,停电时由于惯性作用使电动机转子位置信号丢失,所以多用于中、低速电梯。绝对式光电编码器是按二进制读数设计的,一般需要8~12个码道才能得到精确的位置信号。由于编码器从码盘读到的值就是转角信号二进制输出,由此可直接得到转子的绝对位置。
光电编码器的优点是检测位置操作简单,但容易受电气噪声干扰,而旋转变压器不存在这方面问题。根据变压器原理在定子、转子都装上两相交流绕组。在定子绕组U和V上分别通以互差90°的对称电压,则可在其气隙中产生旋转磁场。当转子从基准位置转过θ角时,转子u和v两绕组中分别感应出比定子电压超前(或落后)θ角的电压。测量转子的感应电压和定子的基准电压之间的相位差就可以判断转子的位置。
轿厢负载检测装置在无齿轮曳引驱动中显得尤为重要,因为系统对电动机的起动转矩要求更高。有齿轮曳引系统的减速机构有较大的传动比,一些低速梯的蜗轮蜗杆副还具有自锁功能。无齿轮曳引驱动中,电动机和曳引轮同轴,要求曳引起动转矩的输出应力求精确。所以采用具有线性变化规律的轿厢负载检测装置来预先测量并计算,从而可解决松闸瞬间由于不同负载引起轿厢起动过慢(倒溜)或起动过猛的问题。系统可预先测量计算并给出恰当方向和大小的转矩,使系统运行全过程由被动控制变为主动控制。
负载检测装置有位置型、压力型等多种形式,输出有开关量、模拟量(电压)和频率量(高频抗干扰性能强,能远距离传送)等。
将上述反馈信号与给定控制信号相比较、运算,按预定的控制方式加以控制,可以得到优于其他驱动系统的性能。