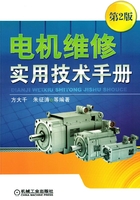
第二节 三相异步电动机定子绕组的基本概念及计算
一、三相异步电动机定子绕组的基本概念
1.绕组元件数s
电动机绕组由很多线圈构成,每一个线圈就是一个绕组元件。双层绕组的元件总数与定子槽数z相等,即s=z;单层绕组的元件总数是定子槽数的一半,即s=z/2。
2.极距τ
极距是指沿定子铁心内圈上每个磁极所占有的定子槽数,即
式中,z为定子铁心的总槽数;p为电动机极对数。
3.线圈节距(跨距)y
每个线圈的两个有效边分别嵌入铁心的两个不同槽位中,这两个边所间隔的槽数叫做线圈的节距(或称跨距)。如一边嵌在第1槽中,另一边嵌在第6槽中,则y=6-1=5。
1)整距绕组:当线圈的节距等于极距时,称为整距绕组,即。
2)短距绕组:y<τ。短距绕组的节距一般采用,以削弱5、7次谐波的影响。
3)长距绕组:y>τ,一般很少采用。
4.槽距角(每槽所占的电度角)α
槽距角是指相邻两槽之间的电角度。三相绕组对称分布在定子槽中,各相在空间应相互间隔120°电角度,所以每槽所占的电角度应为
式中符号意义同前。
5.相带q
相带是指一个极相组线圈所占的范围,以电角度表示。一般一个极距τ对应的电角度为180°,三相交流电相带占180°/3=60°。按上述规律安排的绕组又称为60°相带绕组。对于正弦绕组,每一相带内又分成星接和角接两部分,所以对于每种接法有60°/2=30°,叫30°相带。有些电动机采用120°相带。
定子绕组每极每相槽数
式中,m为定子绕组相数。
q为整数者,叫做整数槽绕组;q为分数者,叫做分数槽绕组。
绕组安放和连接时,往往是将一个相带内的q个元件串联为一组,称为极相组,俗称联。
二、交流电动机绕组型式及适用范围
交流电动机绕组分为定子绕组和转子绕组。定子绕组有单层、双层和单双层之分。单层绕组又有同心式、同心链式、等元件链式和交叉式绕组。双层绕组又有叠绕组和波绕组等。
转子绕组有笼型绕组和绕线转子电动机转子用波绕组。
交流电动机定子和转子的绕组型式及适用范围见表2-25。
表2-25 交流电动机定子和转子的绕组型式及适用范围
(续)
注:p为电机的极对数;q为每极每相槽数;q为分数时,p′为其分数的约净后的分母。
三、三相异步电动机定子绕组的计算及绝缘规范
在修理铭牌失落或数据不全的电动机,以及需要改变某些性能的电动机时,应通过计算得出电动机的各种技术数据。
1.定子绕组匝数的计算
(1)每相串联匝数
式中,W1为每相串联匝数(匝);Ke为降压系数(又称电势系数),小型电动机取0.86,中型电动机取0.90,大型电动机取0.91;Ux为相电压(V);kdp为绕组系数,kdp=kd1kp1,见表2-28、表2-29;f为电源频率(Hz);Φ为每极气隙磁通(Wb)。
(2)每极磁通
式中,Bpj为气隙中平均磁通密度,它与气隙中最大磁通密度Bδ的关系为;S为每极下的气隙面积(m2);Φ为每极磁通(Wb);Bδ为气隙磁通密度(T),应根据电动机的具体情况选取,当铁心材料差、气隙大、极数少时应取小值,另外可根据电动机工作是否间歇、短时,以及通风冷却条件等情况适当调整,参见表2-26;D1为定子内径(cm);p为电动机极对数;l为定子铁心长度(cm)。
定子、转子铁心间的气隙应符合表2-27中的规定,也可以用以下经验公式计算,即
式中,δ为定子、转子铁心间的气隙(mm)。
表2-26 三相异步电动机的气隙磁通密度Bδ(单位:T)
表2-27 三相异步电动机的气隙
若气隙过大,应降低Bδ值,以保证电动机的空载电流不致过大,功率因数不致过低。
(3)绕组系数kdp
1)分布系数kd1。kd1是由于一个极相组的各个线圈分嵌在不同槽内引起的,kd1的大小和每极每相槽数q有关。q越大,kd1越小。当q>6时,kd趋于一个常数。kd1的值可由表2-28查得。
表2-28 分布系数kd1值
2)短距系数kp1。双层绕组的线圈都采用短距,其节距y小于极距τ。y越小,kp1也越小。kp1可由表2-29查得。
表2-29 短距系数kp1值
(续)
3)绕组系数kdp:kdp=kd1kp1。对于单层绕组,当采用全距线圈时,kp1=1,故kdp=kd1。
(4)每相串联导线根数N1
(5)每槽导线根数 每槽导线根数N与每相串联导线根数N1之间有如下关系:
经推算,得
将f=50Hz,m=3(三相异步电动机)代入上式,得
式中,a为电动机绕组并联支路数。
(6)每个线圈的匝数Wy
1)双层绕组:由于每一槽中有上、下两个线圈边,故Wy=N/2。整个电动机绕组的线圈总数等于槽数z,每相线圈数为z/3。
2)单层绕组:Wy=z。整个电动机绕组的线圈总数等于z/2,每相线圈数为z/6。
按以上公式求得的线圈匝数,在电动机气隙正常的情况下才适用。若气隙不在规定范围内,则需适当增加线圈匝数以减小空载电流,使电动机的性能满足要求。
(7)极对数的估算 对于无铭牌的电动机,极对数p可按下式估算:
式中,hc为定子铁心实际轭高(cm),,如图2-1所示。
图2-1 定子尺寸图
2.额定功率的估算
1)估算方法一:用定子铁心尺寸来估算额定功率,即
Pe=KD31l式中,Pe为电动机的额定功率(kW);K为估算系数,见表2-30;其他符号意义同前。
表2-30 估算系数K的值
【例2-1】 有一台电动机,其定子内径D1为15.5cm,铁心长度l为9cm,极对数为4极,试估算其功率。
解:查表2-30得K=1.4×10-4,故电动机额定功率约为
Pe=KD31l=1.4×10-4×15.33×9=4.7kW,可认为此电动机额定功率为4.5kW。
2)估算方法二
Pe=KD21ln1
式中,K为电动机的功率系数,见表2-31;n1为电动机的同步转速(r/min);其他符号同前。
试算时,可取K=1.75×10-6,也可从表2-31中查得。
表2-31 电动机功率系数与极距τ的关系
3)估算方法三:用三相功率公式估算额定功率,即
Pe=3UxIxηcosφ×10-3=3 U1I1ηcosφ×10-3(kW)式中,Ux、U1分别为电动机额定相电压和线电压(V);Ix、I1分别为电动机额定相电流和线电流(A);cosφ、η分别为电动机的功率因数和效率,可由同类电动机的技术数据中查得。
4)估算方法四:用额定线电流估算,即
小电机分母取大值,大电机分母取小值。
3.导线截面的选择
(1)根据额定功率选择导线截面积
1)根据估算出的额定功率Pe,求出额定电流:
式中,Ie为电动机额定电流(A);Ue为电源额定线电压(V)。电动机绕组的相电流Ix的计算方法如下:星形联结时,Ix=Ie;三角形联结时,
2)求出定子导线截面积:
式中,q1为定子导线截面积(mm2);a为并联支路数;n为导线并联根数;j为定子电流密度(A/mm2),铜导线一般可按表2-32选取或参照相近规格的电动机技术数据。
表2-32 中小型电动机定子电流密度j(A/mm2)
表中数据较适用于新产品,对老产品应酌情减小10%~15%。一般功率大者取小值,功率小者取大值。
3)导线直径的选择原则:当导线直径过小时,绕组电阻将增大5%以上,从而影响电动机的电气性能;当导线直径过大时,漆包线的绝缘厚度过大,则会导致嵌线困难。常用聚酯漆包线的绝缘厚度见表2-33。
表2-33 常用聚酯漆包线的绝缘厚度
为了使嵌线顺利、槽利用率高,绕组的导线直径不宜超过1.68mm。但若导线过细,机械强度就较差,嵌线时容易拉断。一般对于5号机座以下的电动机,单根导线的直径最好不超过1.25mm;对于6~9号机座的电动机,单根导线的直径最好不超过1.68mm。导线并联根数n最好不超过4根。若所需导线总的截面积过大,则可增加电动机并联支路数a。
图2-2 槽尺寸
确定导线线规后,还应校验槽满率Fk。校验槽满率的方法如下:把实际槽形描印下来进行测量,如图2-2所示。槽楔厚度h可根据拆下的实物量取,一般为2~4mm。
槽内导线总面积(即槽有效面积)为
Sux=Ss-Si
式中,Ss为槽面积(mm2);Si为槽绝缘占的面积(mm2)。对于图2-2a所示的圆底槽有
单层绕组 Si=Ci[2(hs1+hs2)+πR+bs]
双层绕组 Si=Ci[2(hs1+hs2)+πR+2R+bs]对于图2-2b所示的平底槽有
单层绕组 Si=Ci[2(hs1+hs2)+bs1+bs2]
双层绕组 Si=Ci[2(hs1+hs2)+2bs2+bs1]
式中,h为槽楔厚度,一般取2~4mm;Ci为槽绝缘材料的厚度(mm),可按电动机的工作电压和绝缘等级来确定(见表2-34和表2-35),或按下面数值估计;A级绝缘:Ci=0.35~0.45mm;B级绝缘:Ci=0.44~0.50mm;E、F级绝缘:63~112号机座,Ci=0.25mm;132~355号机座,Ci=0.40。
表2-34 Y、Y2、YX3系列定子绕组槽绝缘规范
槽满率为
式中,n为导线并联根数;N为每槽导线根数;d为绝缘导线外径(mm)。
槽满率Fk是表示导线在槽内填充程度的重要指标。Fk应控制在0.60~0.75的范围内。对于小型异步电动机,Fk=0.75~0.80。若槽满率过高,则会使嵌线困难,容易损伤绝缘层。为了降低槽满率,可适当减小槽楔厚度,或适当提高电流密度j,使线径细一些。
表2-35 旧式中小型异步电动机定子绕组槽绝缘规范
注:1.相间绝缘、层间绝缘材料和厚度与槽绝缘基本相同。
2.槽楔常用竹楔、玻璃层压板、布质层压板等。楔厚不应小于3mm。
(2)根据铁心槽形选择导线截面积 对于没有铭牌的电动机,由于,所以只要得到上述参数,便可求出导线直径,从而确定导线截面积。
1)决定极数及绕组形式:极数2p与定子铁心内、外径之比D1/D的关系见表2-36。
表2-36 D1/D与2p的关系
绕组形式主要由每极每相槽数q及层数确定,即q=z/(2pm)。
当定子外径D≤245mm时,采用单层绕组,常用节距见表2-37。
表2-37 根据不同相带q来选用绕组形式及节距y
2)每槽导线根数为
式中,Ux为相电压,绕组为星形联结时为220V,绕组为三角形联结时为380V,可同时作两种计算,最后根据可能有的导线尺寸确定一种联结;K′为系数,对于单层绕组的小电动机,取0.85;对于双层绕组的大电动机,取0.80。
对于计算出的N,单层绕组应取整数,双层绕组应取偶数。
3)导线截面积q1的选择有以下两种方法。
方法一:按槽满率Fk来计算线直径d,即,修理电动机的Fk取75%为宜。
方法二:按填充系数Kq来求导线的截面积q1,即先根据槽形尺寸算出槽楔下的截面积Ss,然后按下式算出槽内导线的总面积,即
S=KqSs
式中,Kq为填充系数(见表2-38),Kq值大,槽的空间利用率就高,但这也增加了嵌线的难度。
表2-38 填充系数Kq值
填充系数与槽满率的定义不同,但含义一样。
每根导线的截面积q1为
q1=S/N
(3)额定电流的计算 计算出导线截面积后,便可求出额定电流。
先根据导线截面积q1来估算支路电流I支,即
I支=q1j式中,j为电流密度(A/mm2),对于铜导线,可根据表2-32选取;对于铝导线,可根据表2-39选取。对于封闭式电动机,取小值;对于四极以上电动机,取大值。
表2-39 铝导线电动机定子铁心外径D与电流密度j的关系
额定相电流Ix为
Ix=Ia=qja式中,a为并联支路数,见表2-40,或按2p/a必须是整数来选取。
表2-40 并联支路数a与极数2p的关系
注:有“()”的并联支路数只适用于双层绕组。
电动机的额定电流Ie为:星形联结,Ie=Ix;三角形联结,。
四、三相单层绕组及展开图分析
1.三相单层绕组的安排原则与展开图
现以三相四极24槽等元件式单层整距绕组为例来说明。可按下列原则和步骤画出其接线展开图。
1)各绕组在每个磁极下应均匀分布,以便使磁场对称。
①分极:按定子槽数z画出定子槽,并编上序号。按磁极数2p等分定子槽z,磁极按S、N、S、N……的顺序交错排列,如图2-3所示。
图2-3 槽的分极及分相
该例中z=24,2p=4,相数m=3,故
②分相:每个磁极下的槽数均匀分成3个相带,每个相带占60°电角度,每极每相槽数为
2)画出各相绕组的电源引出线。绕组的起端或末端应彼此间隔120°电角度,图2-3中U1、V1、W1之间或U2、V2、W2之间各相隔120°电角度。每槽所占电角度α为
若U相的起端U1在第1槽,则V相的起端V1应在第5槽,W相的起端W1应在第9槽。由于每极每相槽数为2,故U相在各极相带的槽号是1、2、7、8,13、14、19、20,V相在各极相带的槽号是5、6、11、12,17、18、23、24,W相在各极相带的槽号是9、10、15、16,21、23、3、4。可以看出,在每个磁极下三相绕组的排列顺序是U、W、V,如图2-4所示。
3)标出电流方向。同一相绕组的各个有效边在同一磁极下的电流方向应相同,而在相异磁极下的电流方向应相反,见图2-3b。此时应注意:
①U、V、W对应相带(U1、V1、W1,U2、V2、W2等)均应间隔120°;
②在同一个磁极下各相带槽中电流的方向相同。
图2-4 三相等元件式单层整距绕组展开图
4)确定绕组形式。绕组可分为单层绕组和双层绕组。单层绕组元件总数为定子槽数的一半。按节距的不同,单层绕组又可分链式绕组、交叉链式绕组、同心式绕组和等元件式整距绕组等。双层绕组元件总数等于定子槽数。按元件的样式分布的不同,双层绕组又可分为叠绕组和波绕组。
5)确定线圈节距y。采用等元件式单层整距绕组,其节距为
即一个元件的起端边若嵌在第1槽中,则末端边应嵌在第7槽中。根据线圈的节距,即可将两有效边连为一个元件。
6)沿电流方向将同相线圈串联。如图2-4所示,每相绕组均由两组线圈组成,顺着电流方向,U相第一组线圈的尾(第8槽)与第二组线圈的头(第13槽)相连,这就联成U相绕组。同样,可画出V相和W相绕组。最后剩下6个接线头,即U相绕组的U1、U2,V相绕组的V1、V2,以及W相绕组的W1、W2。
2.三相单层绕组的分类
三相单层绕组可分为链式绕组、交叉链式绕组和三相单层同心式绕组。
(1)链式绕组
链式绕组是由相同节距的线圈组成的。它的线圈连接形状像链子一样一环连着一环。
例如,一台三相四极24槽异步电动机展开图的绘制步骤如下:
1)求出每极槽数(极距)τ、每极每相槽数(相带)q,即
所以,节距。
2)画出各相绕组的引出线。各相绕组首端U、V、W和尾端X、Y、Z应相差120°电角度。每槽所占电角度为。每相相差的槽数为
,即4槽。三相绕组的排列顺序为U、V、W。根据以上原则可以得出U相绕组由(1—6)、(7—12)、(13—18)和(19—24)4个线圈组成。而V、W相绕组的首端应分别在5、9槽内,如图2-5所示。
图2-5 三相四极链式绕组展开图
3)假定电流方向。各相各槽按图2-5所示方法标明电流方向。
4)连接端部,形成链式绕组。如图2-5所示,U相的4个线圈应分布在4个极,并交替为N、S、N、S排列。因此,根据电流方向应为反串联。根据以上原则,画出三相绕组的连接方式,如图2-6所示。
(2)交叉链式绕组
电动机每对磁极下有两组大节距线圈和一组小节距线圈。采用不等距线圈连接而成的绕组叫做交叉链式绕组。
图2-6 三相绕组的连接方式
例如,一台三相四极36槽异步电动机展开图的绘制步骤如下:
1)求出每极槽数τ和每极每相槽数q,即
确定节距:大节距y1=8,小节距y2=7。
2)求出每槽电角度α,假定电流方向。
各相应相隔6槽,每极9槽。由此可知,36至8槽电流向上,9至17槽电流向下,18至26槽电流向上,27至35槽电流向下。根据电流方向连接各线圈端部接线。如以第1槽为U相首端,根据上述原则,可画出U相绕组的连接图,如图2-7所示。
3)连接三相绕组。各相首端间隔持120°电角度,即6槽。因此,V、W相首端应分别在第7槽和第13槽。每对磁极下均有两组大节距线圈和一组小节距线圈。这既保持了电磁平衡,又实现了短节距要求。连接情况如图2-7所示。
图2-7 三相交叉链式绕组展开图
交叉链式绕组具有端部线圈连线短的优点,可以节约铜线。
(3)三相单层同心式绕组
同心式绕组的线圈布置如图2-8所示。由于线圈的轴线是同心的,因此每个线圈具有不同的节距。
例如,一台三相两极24槽异步电动机展开图的绘制步骤如下:
1)求出每极槽数τ和每极每相槽数q,即
2)求出每槽电角度α,画出各相首端。
图2-8 同心式绕组线圈布置示意图
各相首端应相差120°电角度,各相相隔槽数为。这时,如U相首端在第1槽,则V、W相首端应分别在第9槽和第17槽。
3)确定线圈节距,连接三相绕组。为了使每个线圈获得尽可能大的电动势,大线圈节距取12,小线圈节距取10。如U相首端在第1槽,该线圈的另一有效边应在第12槽,小线圈为2、11槽。根据以上原则,就可以知道U相绕组的槽号为1、2、11、12、13、14、23、24,V相绕组的槽号为7、8、9、10、19、20、21、22,W相绕组的槽号为3、4、5、6、15、16、17、18。其绕组展开图如图2-9所示,连接方式如图2-10所示。
图2-9 同心式绕组展开图
图2-10 同心式绕组连接方式
五、三相双层绕组及展开图分析
1.三相双层整数槽叠绕组
双层叠绕组在嵌线时,两个串联的线圈总是后一个叠在前一个上面,因此叫做叠绕组。双层叠绕组的节距可以任意选择,一般选择短节距,以便减小谐波电动势,使电动机的磁场分布更接近正弦波,从而改善电动机性能。
例如,一台三相四极36槽异步电动机展开图的绘制步骤如下:
1)求出每极槽数τ和每极每相槽数q,即
确定节距:取,因此取y=7(或y=8),本例取y=7。
2)求出每槽电角度α,画出各相首端。
每相首端应相差槽。如U相首端在第1槽,则V、W相首端应分别在第7槽和第13槽。
3)假定电流方向。将展开图的36个槽分为4个极(2p=4),即N、S、N、S。将电流方向标在每一个极相带的绕组边上,如图2-11所示。
4)连接端部接线。如图2-11所示,将U相首端连接在1号线槽上层,第1个线圈的另一个有效边则在8号线槽的下层。因为每极每相槽数为3,所以U相应占有1、2、3号槽的面槽及8、9、10号槽的下层。依此类推,可画出U相绕组的连接展开图。为了分清上层和下层有效边,习惯上将上层有效边画成实线,下层有效边画成虚线。
图2-11 三相双层整数槽叠绕组展开图(U相)
由于各相首端互差120°电角度,所以V1、W1相首端分别在第7槽和第13槽,尾端(V2、W2)分别在第34槽和第4槽。
U相连接方式如图2-12所示(有两种不同方式)。
并联支路数最大等于2p,即支路数a最大可能等于每相的极组组数,但2p必须是a的整倍数。
由于展开图的绘制比较麻烦,实际工作中往往使用端部接线图,如图2-13所示。
端部接线图的作图方法如下:
1)按极相组总数将定子圆周等分,本例中有2pm(即2×2×3=12)个极相组。
2)根据60°相带分配原则,按顺序给极相组编号。U相绕组由1、4、7、10号极相组构成,V相由3、6、9、12号极相组构成,W相由2、5、8、11号极相组构成。
图2-12 两种支路连接
图2-13 定子绕组端部接线图
3)三相绕组首端(或尾端)之间应相差120°电角度。若U相首端为1号极相组的头,则V、W相首端应分别为3、5号极相组的头。
4)根据各极相组之间采用“反串联”连接方式的规则,连接各极相组。相邻极相组电流的方向相反,用箭头表示。再按电流方向将各极相组引出线连接起来,就构成了三相绕组端部接线图。
2.三相分数槽双层叠绕组
在有些容量较大或多速异步电动机中,定子绕组每极每相槽数q不为整数而为分数,称之为分数槽绕组。这种绕组在排列上必然是某些磁极下线圈多一些,某些磁极下线圈少一些。这样就形成了不均匀组。对于分数槽绕组,不能按照前面介绍的关于整数槽绕组的规律来排列和连接。这种绕组的分布及连接应符合以下基本要求:
1)三相绕组必须含有相同的线圈数。
2)各相首端和尾端应互差120°电角度。
3)线圈多的极相组和线圈少的极相组应布置在对称位置,使电磁力矩平衡,以减少电动机的磁性振动。
例如,一台三相6极27槽异步电动机,其绕组安排如下:每极每相槽数
每个极相组中含有个线圈,因此只能使其中三个极相组各用两个线圈,另外三个极相组各安设一个线圈。同时为了使电磁力矩平衡,应使线圈多的极相组和线圈少的极相组对称分布。于是,就可以得出表2-41所示的分配方法。
表2-41 线圈分配方法
3.三相双层波绕组
多极电动机或导线截面积较大的电动机,为了节约极间连接线的铜材,常采用波绕组。波绕组从展开图来看有些像波浪,所以叫做波绕组。它的连接规则是把所有同一极性下属于同一相的线圈按一定规律连接起来,然后再将两个异极性的同一相线圈“反串”连接,就成为一相的全部绕组。
例如,一台三相4极24槽异步电动机展开图的绘制步骤如下:
1)求出每极槽数τ和每极每相槽数q:
确定节距:取
2)求出每槽电角度α:
即各相首端及尾端应相隔(即4)槽。
3)用表标明各极相组的分配,见表2-42。
表2-42 各极相组分配
4)由表2-42可知,N1下U相极相组包含1、2号槽,按节距y=5,将U相两个线圈连接起来,如图2-14所示。也就是说,将第一个线圈(1—6)与N2下第二个线圈(13—18)连接起来。这两个线圈上层边(或下层边)之间相隔12槽,这个距离叫做线圈的合成节距,用符号Y1表示,Y1=2τ。在整数槽绕组中,合成节距Y1应加长一槽(或缩短一槽)。因为,如果始终保持2τ节距的话,则(13—18)线圈就和1号槽连接而形成一个闭合回路。因此,本例中采用(2τ+1)的综合节距,使(13—18)线圈和2号槽连接。按这一原则,将N1、N2下的U相线圈全部连接起来就成为以下顺序:
图2-14 双层波绕组U相展开图
u1—(1—6)→(13—18)→(2—7)→(14—19)→x1
括号内代表一个线圈,前一个数字代表上层有效边的槽号,后一个数字代表下层边所在的槽号。用同样方法,就可以写出S极下U相线圈的连接顺序:
u2—(7—12)→(19—24)→(8—13)→(20—1)→x2
再运用“反串”原则将N极与S极下的U相线圈连接起来,就构成了U相全部绕组,即
同理可得V、W相全部绕组的连接顺序:
波绕组在绕线型异步电动机转子上应用较广泛。它也可做成分数槽绕组。它的连接规则和分数槽叠绕组类似。
六、异步电动机改变极数绕组重绕的计算
改变极数绕组重绕要求,改极前、后电动机极数不能相差过大,例如不宜将6极电动机改成2极,否则改后定子轭部磁通密度会显著增加;同样理由,也不宜将4极电动机改为10极。
改极计算公式如下:
1)改极后,定子、转子槽数z1和z2的配合应满足以下要求
z1-z2≠±2p,z1-z2≠1±2p,z1-z2≠2±4p式中,p为极对数。
否则,电动机可能发生强噪声,甚至不能转动。
笼型异步电动机改极的经验数据见表2-43。
表2-43 笼型异步电动机改极的经验数据
2)线圈节距。
式中,y、y′分别为改极前、后线圈节距(槽);p、p′分别为改极前、后电动机的极对数。
3)每槽导线数N′。
①极数改少时,每槽导线数应按定子轭部磁通密度的条件计算
式中,Ke为降压系数;Ux为定子绕组相电压(V);z1为定子铁心槽数;he为定子铁心轭高(cm);l为定子铁心长度(cm);Bc1为铁心轭部磁通密度(T),不应超过1.7T;kdp为绕组系数,kdp=kd1kp1,见表2-28和表2-29。
②极数改多时,每槽导线数为
式中,N为改极前每槽导线数(根/槽)。
4)导线直径d′。
式中,d为改极前绕组导线直径(mm)。
5)电动机功率估算。或P
式中,Pe、Pe′分别为改极前、后电动机的功率(kW)。
【例2-2】 有一台10kW 6极笼型三相异步电动机,额定电压Ue为380V,额定电流Ie为21.5A,联结,现欲改为4极,试求新绕组数据。
解:拆除绕组时记录以下数据:定子槽数z1为36,转子槽数z2为44,每槽导线数N为26,导线采用QZ型漆包线,直径d为1.56mm,两根并绕,线圈节距y为5,绕组一路△联结,双层选绕,定子铁心内径D1为21cm,长度l为10.5cm,轭高he为2.5cm。
(1)定、转子槽数的配合因为所以可以由6极改为4极。
(2)新绕组计算线圈节距,可取8槽每极每相槽数
极距
查表2-28和表2-29得分布系数kd1=0.96,短距系数kp1=0.985。
绕组系数kdp=kd1kp1=0.96×0.985=0.945
(3)每槽导线数
因为是改少极数,所以应按轭部磁通密度Be计算。选择压系数ke=0.94,Bc1=1.60T,原电动机相电压每槽导线数为
(4)新绕组导线直径
查线规表,选用标称直径ϕ1.81的QZ型高强度漆包圆铜线(截面积为2.57mm2)。
(5)改极后电动机功率
电动机改为4极后,绕组形式不变,即仍采用双层选绕一路星形联结。
七、电动机重绕圆导线代换计算
1.保持导线截面积不变的代换
(1)用2根直径相同的导线d′代替原来的一根导线d。
d′=0.71d
(2)用3根直径相同的导线d′代替原来的一根导线d。
d′=0.58d
代用的导线数不可超过3根,否则不满足槽满率要求,嵌不下线。
2.改变绕组接线方式
(1)△联结绕组改成联结绕组
导线直径 d=1.32d△
线圈匝数 W=0.58W△
(2)联结绕组改成△联结绕组
导线直径 d△=0.76d
线圈匝数 W△=1.73W
式中,d、d△分别为
联结和△联结的导线直径(mm);W
、W△分别为
联结和△联结的线圈匝数(匝)。
【例2-3】 有一台5.5kW三相异步电动机,已知原导线直径为1.25mm,每槽42匝,链式绕组,重绕时无此导线,欲用2根导线并联代换,试求代换导线。
解:代换导线直径为
d′=0.71d=0.71×1.25mm=0.887mm
取标称直径为0.9mm,即用2根0.9mm导线代替原来的一根1.25mm导线,其他参数不变,如绕组形式(链式)、跨距(1~6)、并联路数(1)等均不变。
【例2-4】 有一台22kW三相异步电动机,已知绕组为△联结,并绕根数n为2,并联支路数a为2,每联线圈为14匝,双层绕组,导线直径d为1.2mm(QZ型漆包线),要求a和n保持不变的条件下,只改变绕组联结,试计算代用导线。
解:绕组由△联结改为联结时,有
d=1.32d△=(1.32×1.2)mm=1.58mm,取标称导线ϕ1.56mm。
W=0.58W△=(0.58×14)匝=8.12匝,选8匝
有了绕组导线直径和线圈匝数两个参数,就可方便地改变电动机绕组的接法。
八、铜、铝导线的代换
在绕制电动机线圈时,由于选材等原因,可能碰到以铜代铝或以铝代铜的情况。这时需进行换算后才可代换。
1.以铜代铝
导线代用的原则是保持电动机绕组铜损不变。在保持绕组匝数和节距不变的情况下,铜导线与铝导线的换算公式如下:
式中,dCu、dAl分别为裸铜线和裸铝线的直径(mm);ρCu、ρAl分别为铜导线和铝导线的电阻率(Ω·mm2/m)(对于A、E、B级绝缘,ρCu=0.0219,对于F、H级绝缘,ρCu=0.0245;对于A、E、B级绝缘,ρAl=0.0346,对于F、H级绝缘,ρAl=0.0392)。
若以A、E、B级绝缘电阻率代入上式,则
dCu≈0.79dAl
若以F、H级绝缘电阻率代入上式,则
dCu≈0.79dAl
因此,不论何种绝缘,取dCu≈0.8dAl即可。由于铜导线比铝导线直径细0.8倍,代用后将引起槽满率下降。为了保证槽满率不变,在改用铜导线时,可直接按铝导线绝缘外径选用,这时绕组电阻将降低,即RCu=0.63RAl。绕组铜耗降低40%左右,电动机效率可提高2%~4%。
2.以铝代铜
可以用聚酯漆包圆铝导线代替双纱包圆铜导线或单纱漆包圆铜导线,以节约铜材。
QZL型聚酯漆包圆铝导线属于B级绝缘,只要把槽绝缘改用E级、B级或F级绝缘材料,就能使A级绝缘等级提高到E级、B级或F级绝缘水平。若原电动机为A级绝缘,提高到B级绝缘时,铝导线直径只要比原来铜导线直径大1.1倍即可。而槽绝缘也可由原来厚度为0.6mm降至0.27mm左右。通常能在不降低电动机功率的情况下直接改为铝导线。必要时重新校验一次槽满率。
九、改变线圈导线的并联根数以适应导线截面积要求的计算
电动机绕组重绕时有时会碰到原绕组导线太粗、无货的情况,这时可以采用改变线圈导线的并绕根数的方法以选择替代的导线。
当电动机绕组选用的导线太粗时,可用几根导线并绕代替。5号机座以下的电动机,单根导线的直径最好不超过1.25mm;对于6~9号机座的电动机,最好不超过1.68mm。代用后要求并绕的几根导线的总截面积应等于或接近于原导线的截面积。
q′=q/n′式中,q′为改用并绕后每根导线的截面积(mm2);q为原来导线的截面积(mm2);n′为改用导线的并绕根数。
导线直径可查线规表或按下式换算:
线圈并绕的导线,应采用相同直径的导线。
用并联导线代替单根导线时须注意,并联根数一般不超过3~4根。过多的并绕根数,会造成嵌线困难。因此,必要时要新校验槽满率。对于高强度聚酯漆包圆铜线,如QZ型或QQ型,槽满率应控制在75%左右;铝导线或单纱漆包圆铜线,可控制在75%~80%;对于油性漆包线,如Q型或氧化膜铝线,可控制在65%~70%。若达不到上述要求,可采用增加绕组的并联支路数来减少线圈的并绕根数。
十、改变绕组并联支路数以适应导线截面积要求的计算
异步电动机改变绕组并联支路数以适应导线截面积要求时,可按以下方法选择导线。
1)绕组改变并联支路后的导线截面积为
式中,q为绕组原来的导线截面积(mm2);a为绕组原来的并联支路数;a′为绕组改变后的并联支路数;d为绕组原来的导线直径(mm)。
2)绕组改变并联支路后,为保持每相的串联匝数不变,需增加每槽导线数。改变前后电动机的每槽导线数的关系如下:
每槽导线数为
式中,N、N′分别为绕组改变前、后的每槽导线数;a、a′分别为绕组改变前、后的并联支路数。
3)改变并联支路数后还应满足zp/a为整数,否则并联支路数不能成立。
在改变a时,要考虑电动机极数和绕组型式的限制。电动机允许最大并联支路数见表2-44。
表2-44 各种绕组允许最大并联支路数
注:表中p为极对数,q为每根每相槽数。
【例2-5】 有一台6极电动机,绕组为一路星形双层叠绕,导线截面积q为5.9mm2,每槽导线数N为16,试选择导线。
解:查线规表得最接近的标称导线截面积是5.43mm2和6.29mm2,直径分别是2.63mm和2.83mm。
由于线径过粗,嵌线困难,若改选ϕ1.12mm的导线,则需用6根并绕,并绕根数太多,不可取。现拟改为三路并联,以满足极数与并联支路数关系的条件。
2p/a′=6/3(整数)
绕组导线截面积q′为
可选用标准线规ϕ1.12mm两根并绕,截面积为
q=(2×0.985)mm2=1.97mm2改变后的每槽导线数N′为
采用双层叠绕,每个绕组为24匝,电动机绕组的接线方式不变。
十一、三相空壳电动机绕组重绕计算之一
1.参数计算
先记录下定子铁心内径D1、铁心长度l、定子槽数z、齿宽bt、铁心轭高hc等数据。
(1)估算电动机极对数为 或
(2)查表:在电动机产品的技术数据表中,查出一个形式相同、极数相同、定子内径、铁心长度等尽可能与空壳电动机铁心尺寸接近的电动机作参考,并查出其每个线圈匝数、导线直径和额定功率、绕组形式、接法、节距等。
设参考电动机的定子铁心内径为D′1、铁心长度为l′、定子槽数为z′、每个线圈匝数为W′、导线直径为d′和额定功率为P′;空壳电动机的上述数据分别为D1、l、z、W、d和P。
(3)计算每个线圈的匝数为
(4)导线直径的选择为
(5)电动机功率估算为
用此法计算出的电动机绕组数据,如接法、并联路数、绕组形式、并绕根数、节距等,应与参考电动机接近。
2.电动机功率的估算
测量出定子铁心内径D1和铁心长度l,根据D1、l和极数2p,再对照Y、JO2、JO或J等系列电动机的相应极数的定子铁心尺寸(一般电工手册中均有),便可得到所估计的功率。当然,也可按下列公式估算功率:
对于2极电动机
对于4极电动机
对于6极电动机
对于8极电动机
式中D1和l的单位均为cm。
3.电动机工作电流的计算
式中,I1为电动机线电流(A);P为电动机功率(kW);U1为电源线电压(V);cosφ为电动机功率因数;η为电动机效率。
cosφ及η可取由电动机性能数据表查得的相近功率电动机的相应参数值作为参考。
4.绕组的计算
(1)选定绕组型式 参照同类型电动机,确定绕组型式,计算出绕组的各项参数。
一般10kW以上的电动机采用双层绕组,10kW及以下的电动机采用单层绕组。在单层绕组中,当每极每相槽数q=2时,采用单层链式绕组;当q=3时,采用单层交叉绕组;当q=4时,采用单层三平面同心绕组或单层链式同心绕组。
(2)确定每槽的有效导线数
式中,Nn为每槽的有效导线数(根/槽),对于双层绕组,Nn为偶数;Ux为电动机相电压(V);t为定子槽距(cm);Bδ为气隙磁通密度(T),可参照表2-26选取(对于旧式电动机,应取表中略小的数值)。
(3)导线截面积的选择
式中,S1为导线截面积(mm2);Ix为电动机相电流(A),采用星形联结时Ix=I1;采用三角形联结时Ix=I1/3;j为电流密度(A/mm2),见表2-32;a为并联支路数,见表2-45;或按2p/a必须是整数来选择;n为并绕根数,一般不超过3~4根。
表2-45 三相绕组并联支路数
然后根据S1查标称线规表,确定绝缘导线外径d。
须指出,若为旧式电动机,表2-32中所列定子电流密度数值应酌情降低10%~15%。
(4)每槽实际导线数N=aNn
(5)校验槽满率
式中,Fk为槽满率(%);Sux为槽有效面积,即槽内导线总面积(mm2);Ss为槽面积(mm2);Si为槽绝缘所占面积(mm2)。
槽满率应控制在0.60~0.75范围内。对于小型异步电动机,Fk=0.75~0.80。若槽满率过大,会使嵌线困难,容易损伤绝缘。为降低槽满率,可适当减小槽楔厚度,或适当提高电流密度j,使线径细一些。
【例2-6】 有一台空壳电动机,无铭牌,JO型外壳。量得其定子内径D1为112mm,铁心长度l为73.5mm,轭高h为18mm,齿宽b为8mm,槽数Z为24。现要嵌线使用,试求绕组数据。
解:(1)估算电动机极对数为
也可用下式估算为
因此,取p=2。
(2)查表。根据以上已知资料,找到型式相同、极数相同、铁心尺寸接近的一台JO41-4型电动机。其数据为:D1′=110mm,l′=80mm,Z′=36槽,单层绕组,每个线圈匝数W′=52,1路接,节距τ=1~8,导线直径d′=1.0mm。
(3)计算每个线圈的匝数
(4)导线直径的选择
采用ϕ1.0mm的漆包线。
(5)电动机功率估算其中,
根据以上数据得,电动机功率为1.5kW,绕组漆包线直径为ϕ1.0mm,单层绕组,4极,每个线圈匝数为83匝,1路联结,节距为1~6。
【例2-7】 有一台国产三相异步电动机,测得定子铁心数据如下:铁心内径D1为245mm、外径D为368mm、长度l为175mm、定子槽数z为48。定子槽形尺寸如图2-15所示。试配最适当绕组(B级绝缘)。
解:由图2-15查得R=5.5mm、b0=3.2mm、bt1=6mm、bs=8mm、hs1=1mm、hs2=21mm、hc=27.5mm。设绝缘厚度Ci=0.22mm,槽楔厚度h为3mm。
(1)确定极对数为
(2)电动机功率的估算为
D21l=24.52×17.5cm2=1.05×104 cm2查图2-16,功率约36kW,取标准功率P=30kW。
图2-15 定子槽形尺寸
图2-16 国产系列三相异步电动机D21l 与功率的关系曲线(近似)
先求出D21l的数值,然后查下图估算出电动机的功率,再选定所接近的标准功率。D1—定子铁心内径(cm);l—铁心长度(cm)
(3)设cosφ=0.87、η=0.92,则电动机工作电流为
(4)绕组计算
①采用双层叠绕绕组。
②求每槽有效导线数Nn。
设电动机为△联结,Ux=U1=380V
定子槽距查表2-26,取气隙磁通密度Bδ=0.7T,则
由于是双层绕组,故取Nn=15根/槽。
③导线截面积的选择:取电流密度j=6A/mm2,并联支路数a=2,导线并绕根数n=2。
查线规表得标准直径d1=1.35mm,外径d=1.46mm。
(5)校验槽满率
绝缘占面积Si=Ci[2(hs1+hs2)+πR+2R+bs]
=0.22×(2×22+π×5.5+2×5.5+8)mm2
=17.7mm2
槽内导线总面积Swx=Ss-Si=(182.4-17.7)mm2=164.7mm2
每槽实际导线数N=aNn=2×15=30根/槽
槽满率为
符合槽满率一般在0.60~0.75的范围。
该电动机绕组采用双层叠绕,用直径为1.5mm的漆包线双根并绕,支路数为2,每只绕组为28匝。
十二、三相空壳电动机绕组重绕计算之二
对10kW以下的小功率电动机,可按以下简化方法计算,计算误差也不算大。
(1)估算电动机极对数
计算公式同前。
(2)计算每槽有效导线数
①当绕组为联结,额定线电压为380V时
②当绕组为△联结,额定线电压为380V时
式中,a为并联支路数;n1为电动机同步转速(r/min);z为定子槽数;SFe为定子铁心内圆周的表面积(mm2),SFe=πD1l。
(3)电动机功率估算
Pe=KD21ln1式中符号同前。系数K,见表2-46。
表2-46 估算系数K
(4)确定电动机额定电流见表2-47。
表2-47 额定电流与电动机功率的简单关系(联结)
注:联结时,线电流即为相电流;△联结时,相电流(绕组中的电流)为线电流的1/3倍。
(5)导线直径的选择联结:
△联结:
式中,d为导线直径(mm);j为电流密度(A/mm2)。
十三、单速电动机改为双速电动机绕组重线计算之一
已知原单速电动机的绕组数据,便可按表2-48简捷地计算出所需双速电动机的绕组数据。
表2-48 单速电动机改为双速电动机的计算
【例2-8】 有一台Y系列电动机,已知额定功率Pe为4kW,4极,联结,定子槽数Z为36,每槽导线根数N1为46,单层交叉绕,导线直径d1为1.06mm,并联支路数a为1,欲改成2/4极双速电动机,试计算改绕参数。
解:根据4极1路联结改为4极△/2极
联结,查表2-48,得改后电动机有关参数为
绕组节距
每槽导线数
导线直径选标准线规为ϕ0.80mm的漆包线。
输出功率P4=Pe×100%=(4×100%)kW=4kW[4极(△)时]
P2=Pe×120%=(4×120%)kW=4.8kW[2极()时]
十四、单速电动机改为双速电动机绕组重线计算之二
改绕前,先记录下单速电动机的有关数据:额定电压Ue、额定功率Pe、额定频率fe、额定电流Ie、额定转速ne、定子槽数z、定子每槽导线数N1、导线直径d1、转子槽数z2、绕组接法、节距y、并联支路数a1、并绕根数n、绕组型(双层或单层)等。如无上述数据,则应按单速电动机重绕计算求得。
(1)选择单绕组变极调速方案 若要求近似恒转矩,则选择数少时绕组系数kdp较高,极数多时kdp较低的方案;若要求近似恒功率,则应选择两个极下绕组系数kdp均较高的方案。
(2)选择绕组联结方式 恒转矩宜采用/
联结;转矩随转速下降而减小的宜采用△△/
联结;恒功率宜采用
/△联结、
/
联结。
(3)确定绕组节距 一般多速电动机均采用双层绕组,绕组节距在多极数时用全距或接近全距。
(4)每槽导线数的计算
1)以双速电动机中与有一极数单速电动机相同为基准,选择每槽导线数如下:
2)根据两个极下气隙磁通密度比选择每槽导线数如下:
式中,Bδ为气隙磁通密度(T);p为极对数;W为每相串联匝数。
其中下角Ⅰ为少极数时的量,Ⅱ为多极数时的量。
(5)导线直径的选择
(6)功率估算
1)与原单速电动机极数相同时的功率:
式中,P′1、U′1、a′1、d′1分别为改绕后多速电动机与原单速电动机极数相同时的功率、相电压、并联支路数和导线直径。
2)两种极数下的功率比:
3)三种极数下的功率比:
式中,K为功率降低系数(因低速时通风散热效果较差等所致),可取0.7~0.9。
【例2-9】 有一台三相单速电动机,已知额定功率Pe为30kW,4极,相电压U1为380V,并联支路数α1为2,绕组系数kdp为0.946,导线直径d1为2×ϕ1.56mm,每槽导线数N1为30,2△双层绕组。欲改绕成4/6极双速电动机,双速电动机的技术参数为:/
联结,双层绕组,节距y为6;6极时U6为220V,a6为1,kdp6为0.644;4极时U4为220V,a4为2,kdp4为0.831。试求改绕参数。
解:(1)每槽导线数的计算
取N1′=20根,每个绕组为10匝。
(2)导线直径的选择
即d1′=2×ϕ1.91mm。为嵌线容易,按等截面积原则换算,选用标准线规4×ϕ1.35mm漆包线。
(3)功率估算4极时,6极时,取功率降低系数K=0.8,则
(4)双速电动机数据
P=26/10.4kW,Ue=380V,/
联结,2p=4/6,双层绕组,y=1~7,每个绕组10匝,选用导线4×ϕ1.35mm漆包线。
十五、三相异步电动机改变接线方式改压的计算
电动机可以由低压改为高压(500V以上)使用,也可以由高压改为低压使用。对于前者,因受槽形及绝缘的限制,电动机的功率会大大降低,所以一般不宜改压。对于后者,因槽绝缘可以减薄,可采用较大截面积的导线,故电动机出力可有所提高。
当需要改变电动机的使用电压时,可改变接线(改变绕组每相串联线圈匝数)以满足电源电压要求。为了使电动机在改接前后的温升和各部磁通密度保持不变,导线电流密度和线圈每匝所承受的电压应不变动。具体计算步骤如下:
1)计算改压前后的电压比Uj%为
式中,U、U′分别为改压前、后电动机的使用电压(V)。
2)查明电动机绕组是星形联结还是三角形联结,以及绕组的并联支路数a。
3)从表2-49中找出与计算出的电压比Uj%最接近的U%,便可根据其他已知条件查出所要改变电压后应有的接法。
表2-49 三相绕组改变联结的电压比(原来绕组电压为100%)
(续)
4)改接后的绕组并联支路数a′与极数2p′的关系应满足:2p′/a′为整数。
5)绕组改接后的电压变动不得超过±5%,即
改接后的电压误差未超过±5%的范围,因此满足要求。
【例2-10】 有一台3kV、8极、一路星形联结的三相异步电动机,现要改在380V电源上使用,应如何改变绕组接线?
解:改接前后的电压比为
由表2-49可知,“八路星形联结”项中的U%=12.5最为接近,可决定改接成八路并联星形联结,即a=8。
校验:改接后的a与2p的关系如下。
2p/a=8/8=1(整数),满足要求。又改接后的电压误差未超过±5%的范围,因此满足要求。
十六、三相异步电动机绕组重绕改压的计算
如果无法改变接线或改接后绕组电压误差超过允许范围,则只得重绕绕组,以满足电源电压要求。
(1)重绕后绕组每槽导线数的计算如下:
式中,N、N′分别为原绕组和新绕组的每槽导线数(根/槽);Ue、Ue′分别为原电源电压和重绕后的电源电压(V);a、a′分别为原绕组和新绕组的并联支路数。
(2)重绕后导线截面积的计算
式中,q、q′分别为原绕组和新绕组的导线截面积(mm2);n、n′分别为原绕组和新绕组的导线并绕根数。
【例2-11】 有一台380V、4极三相异步电动机,绕组为一路三角形联结,现改在220V电源上使用,试进行改压计算。
解:1)改变接线方式改压计算。改压的电压比为
查表2-49得最近的电压比是U%=58,改接后为三路星形联结。
校验:改接后的并联支路数a与2p的关系如下:
2p/a=4/3(非整数)故此种改接不能成立。再试选电压比U%=50的二路三角形联结。
校验:2p/a=4/2=2(整数),满足要求。
改接后的电压误差为
已超过±5%的允许范围,故不能用改接方法来改压,而必须重绕绕组。
2)重绕绕组改压计算。拆除该电动机绕组时,先记录下列数据:
槽数Z=36,每槽导线数N=34,导线直径d=1.12mm,并绕根数n=1,双层叠绕,线圈节距y=7。
每槽导线数为,取20根/槽。原绕组导线直径d=1.12mm,查线规表得标称截面积q=0.985mm2。新绕组导线截面积为
查线规表,可选取标称直径d1=1.50mm的QZ型高强度漆包圆铜线(绝缘外径d=1.58mm)。
改压后,新绕组的型式、接法和线圈节距均可保持不变。
十七、三相异步电动机改频计算
改频计算通常有以下两类情况:
1)要求改频前后,电源电压、极数和转矩不变,而电动机输出功率允许变化。
2)要求改频前后,电源电压、极数和功率不变,而电动机的输出转矩允许变化。
以上两种情况的改频计算见表2-50。需要指出:
①当频率过低或过高时,表2-50中的公式会有一定的误差。
②增加频率,电动机转速也会增加,这就要考虑转子强度能否胜任,为此需校验转子线速度。
式中,v为转子线速度(m/s),对于笼型转子,v≤60m/s;对于绕线转子,v≤40m/s;D2为转子铁心外径(m);n1为同步转速(r/min)。
表2-50 常用的两种改频计算
3)增加频率,转速提高,能增强电动机的通风冷却效果,因此允许电流密度增大10%~15%。
4)60Hz改为50Hz,或50Hz改为60Hz时,可保持原来定子绕组型式、并绕根数、并联支路数和接线方式不变。
十八、铸铝转子改为铜条转子的计算
当铸铝转子断裂时,可将转子槽内铸铝全部取出更换成铜条。
由于铜条的导电性能比铸铝好,铜条的电流密度可取得比铸铝高,因此铜条占转子槽内空间约2/3即可。如果将铜条把转子槽塞满,则会造成起动转矩小,而电流增大等现象。
具体计算如下:
(1)铜条电流计算
式中,Ic为铜条电流(A);Ix为电动机额定相电流(A);W1为定子每相串联匝数;z2为转子槽数。
(2)铜条截面积计算
式中,qc为铜条截面积(mm2);j2为转子导体的电流密度(A/mm2),一般可取5.5~7.5,封闭式电动机取较小值,开启式取较大值;铝条一般取3~4。
(3)转子端环电流计算
式中,Ih为端环电流(A);p为电动机的极对数。
(4)端环截面积计算
式中,qh为端环截面积(mm2);jh为端环电流密度(A/mm2),可取jh小于(20%~35%)j即可。
十九、三相异步电动机改为单相异步电动机绕组重绕的计算
将三相空壳异步电动机改绕成单相使用时,在转速不变的情况下,其容量约为原来的70%。
1.计算方法一
(1)工作绕组串联匝数的计算 工作绕组(即主绕组)串联匝数过多,会使电动机空载电流减小,转矩降低;串联匝数过少,又会使电动机的空载电流增加,转矩增大,电动机易发热。工作绕组的串联匝数W可按下式计算:
式中,U为重绕后的使用电压,市电电压为220V;f为电源频率,50Hz;τ为电动机极距,τ=πd/(2p);d为定子内径(cm);p为极对数;L为铁心长度(cm);B为磁通密度,一般2极取0.25~0.45T,4极取0.35~0.55T。
(2)工作绕组导线截面积的计算
式中,S为导线截面积(mm2);I为改绕后的电动机电流(A);j为电流密度,一般可取5~8A/mm2;P为改绕后的电动机功率(kW);U为单相电源电压,市电电压为220V;cosφ为功率因数,可取0.75。
(3)起动绕组串联匝数及导线截面积的选择 起动绕组,即副绕组。
1)对于起动后立即与电源断开的起动绕组,其在铁心上只占有1/3的槽数,串联匝数为工作绕组的1/3,导线截面积与工作绕组导线相等。
2)对于起动后仍与电源连接的起动绕组,其在铁心上要占有与工作绕组相等的槽数,串联匝数为工作绕组的1.5倍,导线截面积为工作绕组的2/3。
改绕后的电动机,如果起动转矩小(带负载起动吃力),可适当减少起动绕组的匝数;如果起动电流过大,可增加起动绕组的匝数或增加起动绕组电路中的电阻值。
2.计算方法二
【例2-12】 一台三相异步电动机,已知定子铁心内径D1为112mm,铁心长度l为103.5mm,定子槽数z为24,铁心轭高hc为15.5mm,定子槽面积SA为125mm2。现欲改为用于220V电源的单相电容起动型电动机,试求绕组数据。
解:(1)估算电动机极对数为
可见此电动机的最少可能极对数为2。
(2)主绕组和副绕组槽数的确定:由于采用电容分相起动,故主绕组的槽数占定子槽数的2/3,即
副绕组的槽数应占定子槽数的1/3,即
(3)每个极弧面积计算为
(4)主绕组计算 主绕组每相串联匝数
主绕组的实际匝数应等于3倍Wxg,即
W1=3Wxg=3×330匝=990匝主绕组每槽导线数为取62匝/槽,则主绕组实际匝数为W1=62×16匝=992匝
主绕组占槽面积为
Sg=kSA=(0.35~0.45)SA
=0.4×125mm2=50mm2 (取k=0.4)
槽满率Fk=0.4。
主绕组导线直径选择:每根导线所占面积为
可选用直径为d=1.04mm的漆包线。
(5)副绕组计算 副绕组每槽导线数为
Nq=2Ng=2×62匝/槽=124匝/槽副绕组导线截面可取主绕组的一半,即0.806/2mm2=0.403mm2。可选用直径为d=0.69mm的漆包线。
二十、采用电容裂相法将三相异步电动机改为单相使用的计算
不论绕组是联结还是△联结的三相异步电动机均可用并入电容的方法改接成单相使用,接线如图2-17所示。图中,Cg为工作电容,Cq为起动电容。
工作电容器的电容量按下式计算
式中,Cg为工作电容器的电容量(μF);Ie为电动机的额定电流(A);Ue为电动机的额定电压(V);cosφ为电动机的功率因数,小功率电动机可取0.7~0.8。
图2-17 三相异步电动机改为单相使用的接线
选用接近所计算值的标准电容量的电容器。起动电容器的电容量Cq可根据电动机起动负载而定,一般为工作电容器电容量的1~4倍,即
Cq=(1~4)Cg
实际上1kW以下的电动机可以不加起动电容器,只要把工作电容器的电容量适当加大一些即可。一般以每0.1kW用工作电容器约3.5~6.5μF,耐压不小于450V。
电容器可选用CBB22型或CJ41型等。
使用此种电动机时应注意:当电动机起动后,转速达到额定值时,应立即切除起动电容,否则时间长了电动机会烧坏。经此法改用的电动机功率约为原来功率的55%~90%,其具体功率大小与电动机本身的功率因数等有关。
【例2-13】 一台额定功率为600W、额定电压为220/380V、额定电流为2.8/1.6A、额定功率因数为0.76的三相异步电动机,原运行在380V三相电源(定子绕组为联结),欲用于单相220V电源运行,试求工作电容器和起动电容器电容量。
解:可不改动绕组接线,也可将联结改成△联结。
如为联结,将Ue=380V、Ie=1.6A、cosφ=0.76代入公式,则工作电容器电容量为
,实际可选择12μF。起动电容器电容量为
Cq=(1~4)Cg=[(1~4)×10.8]μF=10.8~43.2μF
若该电动机起动负载不大,可取Cq=35μF。
如为△联结,则将Ue=220V、Ie=2.8A、cosφ=0.76代入公式即可,所算得的Cg、Cq值与联结相同。
实测表明,该电动机单相运行的负载电流为1.82A(联结时),折算输出功率为
p=UI=220×1.82W=400W,相当于原电动机功率的67%。
二十一、利用L、C电路的接法将三相异步电动机改为单相使用的计算
【例2-14】 一台额定电压为380V、额定功率为1.1kW、功率因数为0.8的三相电动机,欲用于单相380V电源运行,试求L、C参数。
解:电动机现在功率为
S=P/cosφ=1100/0.8=1375VA
功率因数角为
φ=φ3=arccos0.8=36.87°
所需电感的电感量为
所需电容的电容量为
由于自制电感较麻烦,可用40W荧光灯镇流器代替。因为40W荧光灯镇流器的工作电压为165V,工作电流为0.41A,由U=IX=IωL,得。该电感量与所需的电感量接近,为了能在380V电压下运行,可将三只镇流器串联成一组,再将三组镇流器并联即可。电容器可用10μF、500V洗衣机电容器。为了降低电容器的工作电压,使电容器可靠运行,可将两只电容器串联成一组,再将四组电容器并联即可,电容量为20μF。
【例2-15】 上例中的电动机若用于220V单相电源,试求L、C参数。
解:所需电感的电感量为
所需电容的电容量为
【例2-16】 一台Y100L-2三相电动机,额定功率为3kW,额定电流为6.4A、额定功率因数为0.87、额定电压为380V,欲用于单相220V电源运行,试求L、C参数。
解:将原电动机定子绕组改成△联结,使用Ue=220V电源时,满载时的线电流为
φ=φe=arccos0.87=29.54°
所需电感的电感量为
所需电容器的电容量为
二十二、采用其他方法将三相异步电动机改为单相使用
1.绕组为联结的电动机
可将任意两相绕组串联起来,然后在一相绕组串入一电阻R,按图2-18a所示的方法连接。起动时,按下起动按钮SB,待电动机达到额定转速时,断开按钮SB,这时电动机便可带负载运行了。
图2-18 另外两种改单相运行的接线法
电阻R的选择应能承受电动机起动时所需电流。若需要较大一点的转矩,可将定子绕组长期串入一只5~10倍于定子绕组值的电阻。如果此电阻值太小,则会使电动机的电流增加,同时发出“嗡嗡”的声响。
2.绕组为△联结的电动机
可按图2-18b所示的方法接线。起动时,反复开闭开关S,待电动机达到额定转速时,断开开关S,电动机便可带负载运行了。采用这种方法,电动机的起动转矩较小。