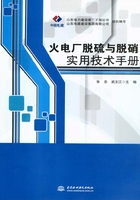
第三章 脱硫设计
第一节 脱硫工艺选择及基本条件
火电厂在建设脱硫工程前期阶段,必须对使用的脱硫工艺进行科学的、合理的选择,其选择的正确与否,直接关系到电厂的投资、今后的生产运行和社会、环境、经济效益。所以,正确的脱硫工艺流程,优化设计策略,合理配置设备,是保证脱硫效率、降低投资和运行维护费用、节约利用场地的根本所在。
通过近十几年脱硫工程实践,脱硫工艺在脱硫效率、运行可靠性、运行成本等方面已取得了显著地改进,运行可靠性可达95%以上。目前,脱硫技术已经成熟,并全面步入实用化、商业化阶段。
脱硫工艺选择的复杂性主要体现在:
(1)脱硫工艺种类繁多,在火电厂应用过的有200多种,但能长期稳定运行,且技术成熟、经济合理的有20多种。
(2)决定一种脱硫工艺适应性的因素很多。每个工艺都有其自身的优缺点,这些优缺点是动态的,而不是静止不变的。一个工艺的特点对某个电厂而言是最大的优点,但对另一个电厂而言,可能就不是优点。因此,脱硫工艺的适应性很大程度上取决于电厂的具体情况,其他电厂的经验教训只能作为参考。
(3)脱硫工艺的选择除了与脱硫工艺本身有关外,在很大程度上还取决于与之相配的电厂及机组的具体情况,受到诸多因素的限制,如国家和地方的环保法规、电厂所在地的环境状况、环境容量和外部资源状况、燃煤硫分、机组容量、机组寿命、机组年利用时间、副产品处置、建设难度等,而且这些因素对每个具体电厂的重要性都是不同的。
因此,针对一个具体的电厂,必须根据建设项目的具体要求,因地制宜,因厂制宜,按照一定的准则,采用科学合理的方法选择在某种意义下“相对最优”的脱硫工艺。
一、脱硫工艺选择的主要技术原则
(1)根据SO2污染现状和环境的可容纳性,结合国家和地方环境法规的要求,提出合理、可行的控制目标,包括脱硫效率、SO2排放浓度和排放量。
(2)结合机组的现状,包括新机组或老机组、机组容量、机组剩余寿命、燃煤硫分等,充分考虑当地资源条件、建设条件,包括场地条件、施工条件、施工周期等,技术成熟、运行可靠、投资少、运行及检修维护成本低、国产化程度高的脱硫工艺,选用操作上是能控制的、在进度上是能实现的、在法律上是允许的、在政治上能被各方接受的工艺。对于老厂增设脱硫改造工程,要特别注意所选工艺与现场预留场地和技术条件是否匹配。
(3)脱硫工程实施后,在允许的时间内,在最大的投资允许限度内,能达到预期的、最终的技术目标和最终要实现的经济效益。
(4)脱硫工程实施后,应确保脱硫系统的安全可靠运行,且不会影响机组的正常运行和安全发电,努力构造资源节约型和环境友好型电厂。
(5)脱硫工程实施后,不能造成二次污染,或将二次污染降至最低,脱硫副产品要尽力实现资源化、无害化目标。
(6)选用高效率的辅机设备,提高运行效率,降低系统能耗。
(7)提高自动化程度,提高运行操作可靠性,降低事故风险概率。
二、影响脱硫工艺选择的综合因素
(1)环境影响。脱硫工程虽然属于环保工程,但作为一个建设项目也同样存在环境影响问题,如考虑不够周全,则脱硫工程建成投运后会产生新的环境污染。潜在的环境影响主要有四个方面:①脱硫吸收剂制备系统的扬尘污染和噪声;②脱硫副产品的处理,特别是副产品抛弃堆存时对环境的影响;③脱硫废水对水体的影响;④脱硫后的净烟气的提升高度影响。
(2)电厂对脱硫工艺选择的要求。电厂应充分考虑自身的实际情况,对脱硫工艺的选择提出切合实际的原则性意见和具体要求。
(3)设计技术参数的可靠性问题。电厂提出的设计基础参数,必须尽可能准确可靠。
(4)性能要求问题。电厂对脱硫工程提出的性能要求,既要有先进性、适用性和前瞻性,更要切合实际。
(5)设计裕量问题。以锅炉实际燃用煤种和烟气特性为基础,考虑脱硫系统设计裕量,最大程度地降低初始投资,同时避免裕量不足带来二次增容改造等后续投资。以某电厂为例,脱硫系统设计煤种含硫量为1.8%,而锅炉设计煤种含硫量为1.6%,实际燃用煤种含硫量为0.8%,致使脱硫系统设计负荷条件较实际大1倍之多,设备性价比大大下降。
三、外部条件要素
1.机组条件
新机组或老机组、机组容量、机组剩余寿命,以及燃煤硫分、含尘量、漏风率等设计输入参数,必须准确可靠。特别是老机组要注意脱硫系统设计寿命应与机组剩余使用寿命相符,老机组主要有以下几种情况:
(1)机组漏风率大。烟气量过大,导致脱硫投资增加。(2)实际燃煤含硫量远超过设计输入值,不能全烟气
脱硫。
(3)烟气含尘量过高,导致石膏品质不合格。
(4)设计裕量过大,系统低负荷运行,功耗增加,可利用率不高。为此,在选择脱硫工艺之前,应对机组的自身条件及今后若干年燃煤情况进行评估,慎重确定设计参数。
2.资源条件
(1)脱硫剂:火电厂脱硫装置处理的烟气量非常大,通常年消耗的脱硫吸收剂量十分可观。为节约成本,脱硫吸收剂的供应以电厂所在地附近区域为宜。目前,大部分脱硫工艺采用钙基化合物作为吸收剂,其主要原因是它们的储藏量丰富、价格低廉,而且生成的脱硫产物十分稳定,不会对环境造成二次污染。
(2)脱硫用水:不同的脱硫工艺对用水的要求各不相同。3.建设条件
建设条件包括场地条件、施工条件、施工周期等。石灰石
—石膏湿法脱硫、氨法和电子束法脱硫所需的场地空间较大,喷雾干燥法脱硫在考虑安装吸收塔后部烟气除尘装置时,需要的脱硫场地也相当大,较难适应老厂改造的条件。相对来说,烟气流化床及烟气悬浮吸收(GSA)脱硫工艺所需场地空间较小,特别是GSA脱硫工艺,由于其吸收塔烟气流速高,吸收塔直径小,可以利用有限的空间位置灵活布置,适用于空间限制条件严格的中小机组的脱硫改造。
四、技术选择要素
1.脱硫效率
在进行烟气脱硫工艺选择时,首先应考虑的因素是SO2排放的控制水平,即环境保护法规、标准、总量控制指标等对脱硫项目消减SO2排放量的具体要求。几种常见脱硫工艺的脱硫效率比较见表1311。
表1311
常见工艺的比较

2.钙硫比
钙硫比是用来表示达到一定脱硫效率时需要的钙基吸收剂的过量程度,在脱硫效率相同时,钙硫比越高,脱硫工艺的运行费用也越高。
3.水、电、气的消耗
以300MW机组为例,以下列出了几种工艺配套的FGD的各种动力消耗,见表1312。
表1312 几种脱硫工艺的动力消耗

① 蒸汽参数压力0.9MPa,用于GGH清扫。
② 不包括新增加的静电除尘器的电耗。
五、经济选择要素
经济选择要素主要综合考虑工程总投资、年运行费用、单位容量造价、脱硫成本、电价补贴等价格要素。
脱硫关键参数设计上,要从经济性和技术性指标两个角度权衡。以脱硫效率为例,脱硫系统的投资与脱硫效率呈指数关系,设计脱硫效率从30%增加到50%时,系统投资增加1倍;脱硫效率增加至70%时,系统投资是脱硫效率为30%时的4倍。因此,在设计时,要避免出现片面追求高的脱硫效率,而使投资及运行成本大幅攀升的现象。
第二节 工艺参数设计计算
典型湿法烟气脱硫工艺的主要设计参数有烟气流量(Q)、
烟气流速(μ)、原烟气SO2浓度、液化比(L/G)、浆液pH
值、钙硫摩尔比(Ca/S)、循环浆液固体物浓度、固体物停留时间、吸收区高度、塔内流速、浆液在吸收区的停留时间、浆液雾化粒径等。按参数用途可以分为设计输入参数、工艺设计参数、性能指标参数、设备选型参数、运行控制参数五类。
一、液气比(L/G)
液化比(L/G)是指与流经吸收塔单位体积烟气量相对应的浆液喷淋量。它不仅与脱硫效率有直接的关系,而且还直接关系到投资(如塔、泵、管道)和运行费用(如电耗)。所以,液气比是直接影响系统的一个重要因素。
1.液气比的计算和选择
液气比(L/G)计算式:
L/G=VL×103
VG
式中:VL为循环浆液体积,L;VG为烟气体积(标态),m3。
烟气标准状态是1个大气压(atm)、273.15K(0℃)。
国际上有些FGD装置供应商取1000m3[latm,298.15K
(15℃)]作为烟气体积的基数,以洗涤此1000m3烟气所需浆液量的体积[以升(L)为单位]来表示液气比,即用VL/
1000m3 (STP、latm、298.15K)来表示液气比。
与液气比有关的另一个问题是烟气干、湿状态。在FGD装置设计中,液气比的计算是取吸收塔出口标准状态下的饱和湿烟气流量,但有些资料中则取吸收塔入口湿基或干基烟气流量。因此,在提到液气比时应明确烟气的状态。
利用液气比可以确定吸收剂的单位用量。如汽化损失为常数,则液气比也可间接作为衡量物质交换面积的一个尺度。根据烟气的SO2浓度,也可借助液气比调节单位洗涤液的SO2浓度。所以液气比是决定脱硫效率的一个主要参数。
在实际工程中,允许最小的L/G由吸收剂浆液特性、控制结垢和堵塞决定。可根据以下原则考虑:
(1)对于喷淋塔,气—液接触面积与L/G成正比,因此L/G与脱硫效率为正比关系,而与SO2浓度无关。
(2)实际运行中,L/G比L/Gmin要大得多,为L/Gmin的
1.2~1.5倍。在设计中石灰石洗涤塔的液气比一般在8~25之间。
2.液气比对设计及运行的影响
液气比是湿法FGD系统设计和运行的重要参数之一,液气比的大小反映了吸收过程推动力和吸收效率的大小,对FGD系统的技术性能和经济性具有重要的影响,是必须合理选择的一个重要设计参数。液气比直接决定了循环泵的数量和容量,也决定了氧化槽的尺寸,对脱硫效果、系统阻力、设备投资和运行能耗等影响很大。
(1)液气比的第一作用是增大吸收表面积。在大多数吸收塔设计中,循环浆液量决定了吸收SO2可利用表面积的大小,喷淋塔和喷淋/托盘塔尤其如此。逆流喷淋塔喷出液滴的总表面积基本上与喷淋浆液流量成正比,当烟气流量一定时,则与液气比成正比。图1321示出了我国某电厂石灰石湿法烟气脱硫逆流喷淋塔液气比与脱硫效率的关系,在其他条件不变的情况下,增加吸收塔循环浆流量即增大液气比,脱硫效率则随之提高。因此,对于一个特定的吸收塔,在烟气流量和最佳烟气流速确定以后,液气比是达到规定脱硫效率的重要设计参数。由于喷淋液滴的大小、液滴的密度、液滴停留时间、填料类型和高度等因素会影响吸收SO2可利用表面积的大小,因此液气比的确定还应考虑上述因素。

图1321 液气比(L/G)与脱硫效率的关系
(2)液气比的第二个作用是降低SO2洗涤负荷。液气比提高,降低了单位浆液洗涤SO2的量,增大了传质表面积,提高了总体传质系数。
(3)液气比的第三个作用是控制浆液的过饱和度,防止结垢。当浆液中CaSO4 ·2H2O的过饱和度高于1.3时,将产生石膏硬垢。在循环浆液固体物浓度相同时,单位体积循环浆液吸收的SO2量降低,石膏的过饱和度就越低,高液气比有助于防止结垢。当依据脱硫效率和防止结垢选择的液气比不相同
时,应选择其中较大的液气比作为设计值。另外,吸收塔吸收区中的SO23-和HSO3-的自然氧化率与浆液中溶解氧量密切相关,高液气比将有利于循环浆液吸收烟气中的氧气。因此,提高液气比将有助于提高吸收区的自然氧化率,减少强制氧化负荷。
3.实例
表1321给出美国和我国一些已投运的FGD装置的实际性能数据,并注明了L/G的设计值。
表1321
一些石灰或石灰石基FGD吸收塔的性能数据

① 吸收剂筛孔尺寸为74μm。② 吸收剂筛孔尺寸为61μm。③ 吸收剂筛孔尺寸为43μm。④ 吸收剂筛孔尺寸为30μm。⑤ 吸收剂筛孔尺寸为60μm。
⑥ 烟气标准状态为273K、1atm。
⑦ 抛弃运行。
表中,美国(1)喷淋塔对于中等含硫燃料,90%脱硫率的石灰石FGD喷淋塔来说,该L/G具有代表性。但是,上述石灰石的细度相对较粗,石灰石的利用率也较低。美国(2)~(5)吸收塔通过装有多孔塔盘或喷淋填料,增强了传质面积,在达到相同脱硫率90%的情况下,这些吸收塔较之(1)喷淋空塔可以在较高的石灰石利用率和较低的L/G下运行。比较(1)~(5)吸收塔可看出,入口SO2浓度最低的吸收塔,其L/G也最小。从该表给出的中国(2)、(3)、(5)液柱塔和喷淋塔的例子可看到,对于含硫较高,要求有较高脱硫率的这两种类型的吸收塔来说,需采用较高的L/G比。另外,影响L/G的因素除了入口SO2浓度、脱硫率外,对于石膏质量有较高要求的FGD系统,往往以保证石膏质量为前提,确定吸收剂允许最低利用率,因为未反应的过量吸收剂往往是影响石膏质量的主要成分,而吸收剂的利用率与吸收剂本身的特性和运行pH值密切有关。通常,为了达到较高的吸收剂利用率,就要选取较低的运行pH值,较高的固体物在反应罐中的停留时间。而较低的运行pH值反过来又影响脱硫效率,在这种情况下提高L/G,增加烟气流速,或采用组合型吸收塔(例如顺、逆流组合,喷淋与填料组合或喷淋加多孔塔盘等)成了必须考虑的因素。当入口SO2浓度较高时,要求有较高脱硫率,较高石膏品位的FGD系统,如不能采用较高的pH值,往往就需要更
高的L/G比。
对于强制氧化工艺,特别是对于高硫燃料,必须谨慎地设计低L/G的吸收塔。在这种情况下,防止结垢所要求的最低L/G可能大于达到SO2脱除效率所需要的L/G。对于这种情况,可以应用FGDPRISMTM计算机模式来预测L/G对吸收塔浆液中石膏饱和度的影响,并计算出最低L/G,作为吸收塔设备技术规范的参数。
从表中还可看到,采用镁石灰作吸收剂,其液相的碱度是如此之高,以致在L/G比其他吸收塔低得多的情况下还可以达到96%的脱硫效率和98%的吸收剂利用率。
二、停留时间
吸收塔中的停留时间是指液体与烟气在吸收塔中的接触时间,分为液气接触时间和在液体内的接触时间。在空塔结构中,液气接触时间是指烟气在液气混合区接触的时间,是吸收SO2的时间,这一时间决定了SO2的去除率;在液体内的接触时间是指SO2被吸收后融入吸收液与吸收液反应产生最终产品被排出吸收塔的时间,这一时间影响氧化率和石膏结晶过程。
停留时间长有助于浆液中石灰石颗粒与SO2的完全反应,并使反应生产物CaSO3有足够的时间完全氧化成CaSO4,形成粒度均匀、纯度高的优质脱硫石膏;但是停留时间长会使浆液池的容积增大,氧化空气量和搅拌器的容量增大,将增加土建和设备费用。
一般将停留时间设为2.8~3.2s。
三、烟气温度
在吸收塔内,烟气温度降低时,吸收液面上的SO2平衡分压也将降低,将有助于气液传质,使脱硫效率增加,一般将吸收塔进气温度降至80℃左右。
四、烟气流速
石灰/石灰石湿法FGD系统中不同工艺部位的烟气流速是不同的,根据烟气最佳流速的不同可以将烟气流道分成以下三个区域:烟道、吸收塔/除雾器、烟囱。下面介绍这前两部分烟气流速的设计范围。通常,FGD技术规范可以允许
FGD制造商自己确定这些部位的烟气流速,对吸收塔的烟气流速,电厂可以规定一个最高设计流速以确保设计具有一定程度的保守性。但是,提高烟气流速相当于提高了设备的处理容量,限定吸收塔最高流速则可能提高吸收塔的造价。实际上,烟气流量是整个FGD系统设计的基础,在确定烟气设计流量时往往已留有一定的裕度,这一裕度将反映到FGD的整个设计中,使设计具有一定的保守性。对烟气流速来说,如果烟气流量留有一定的裕量,烟气设计流速也就具有一定的裕度。
1.烟道中的烟气流速
FGD系统入/出口烟道设计烟气流速的确定要权衡烟道材料费用、风机克服烟道压损所需要的能耗,烟气流速对烟道结构稳定性的影响也是技术规范应考虑的问题。通常在满负荷工况下,国外对入/出口烟道的设计烟气流速大约限定为20m/s,我国在《火力发电厂烟风煤粉管道设计技术规范》(DL/T
5121—2000)中推荐的烟道流速为10~15m/s,而FGD工程
招标书一般规定不大于15m/s。
吸收塔入口烟道是FGD入口烟道与吸收塔之间一个特殊的过渡段,吸收塔入口烟道的设计对吸收塔的性能有密切的影响。吸收塔入口烟道的形状和大小使该处烟气流速有可能高于、或低于上游侧烟道的烟气流速,这取决于吸收塔的断面和塔内烟气流速。吸收塔入口烟道的设计要求烟气压损小,进入塔内的烟气分布均匀;入口烟道的高/宽比适当,不过分影响塔的高度(对逆流塔而言);使干/湿界面远离入口烟道,避免入口烟道中累积沉积物。特别是吸收塔入口烟气分布的均匀性对发挥吸收塔和除雾器固有的性能是非常重要的,因此通常要根据模拟实验结果来设计吸收塔入口烟道。必要时,可以要求FGD设计制造商提供吸收塔入口烟气流速分布图,以了解设计的正确性。
2.吸收塔、除雾器烟气流速
一个吸收塔,当循环浆流量不变时,提高烟气流速,SO2脱除效率会下降。这是因为烟气流速的增大,意味着流量的增加,L/G下降,烟气与循环浆液在塔内的接触时间减少了。但是,随着塔内烟气流速的增大,改变了气/液流体界面状,气/液膜减薄;下落的液滴变成悬浮或沸腾状态,吸收区的浆液量增加了,延长了液滴在吸收区的滞留时间,增大了吸收液滴的表面积。这些因素的变化将提高吸收塔内气/液接触效率,提高吸收速率。因此,尽管脱硫效率随着烟气流速的提高而有所下降,但以每升吸收浆液吸收的SO2mmol数表示的吸收量
(即mmolSO2/L浆液)以及以每分钟吸收的SO2mmol数表示
的吸速率(即mmolSO2/min)却是随着烟气流速的增大而明显增大。当然,对于不同类型的吸收塔,烟气流速对其性能的影响是有差别的。
逆流塔典型的设计烟气流速范围大约是2.5~5m/s,许多装置采用3m/s的设计流速。近年的设计趋势是向着高流量、大容量和紧凑吸收塔的方向发展,流速趋向这一范围的高端,特别是空塔型的洗涤器。表1322列出了我国近年引进的一些湿法石灰石烟气脱硫吸收塔的空塔烟气流速,从该表可看出我国近年引进的逆流喷淋空塔的烟气流速仍趋低流速,液柱式逆流塔的烟气流速已达到了较高流速。顺流塔有利提高烟气流速,某电厂吸收塔中的顺流塔烟气流速高达10m/s,这是采用先顺流后逆流液柱式组合塔所特有高流速,这也可能是吸收塔体积明显较小的原因之一。我国近年引进的一些FGD吸收塔烟气流速见表1322。
表1322 我国近年引进的一些FGD
吸收塔烟气流速

对一个特定的喷淋塔来说,提高吸收塔烟气流速即意味烟气流量的增大,如果要保持SO2脱除效率不变则需要适当增加循环浆液流量。而对于两个不同直径的吸收塔,如果流量相同,要达到相同的脱硫效率。直径小的吸收塔由于烟气流速需要的L/G比直径大的吸收塔所需要的L/G小。也就是说,提高吸收塔烟气流速可以减少L/G,降低循环泵的能耗。但是,较高的烟气流速会增加吸收塔的压损,循环泵节省的一部分电耗将被脱硫风机增加的电耗所抵消。然而,高流速带来的吸收塔断面的减小和循环泵容量的降低可以获得节省投资成本的净经济利益。
吸收塔的烟气流速也不能无限提高,对于逆流喷淋塔,当流速大约超过6m/s时,大液滴将被烟气从除雾器中夹带出来,因而除雾器的性能限制了烟气流速的进一步提高。在烟气高流速的情况下,被除雾器捕获的液滴在顺着除雾器板片下流时会被高速烟流剥离板片表面,重新带入烟气中。对于垂直烟气流的除雾器(即除雾器水平布置在吸收塔内的顶部)。目前设计烟气流速的上限约为6m/s,当烟气流速不超过6m/s时,不会出现浆液大量被重新带走现象。考虑到除雾器的支撑结构要占据一部分空间和塔内流速分布不均匀,实际最大设计烟气流速大约为5m/s。如果吸收塔流速大于此值,那么必须扩大除雾器所处位置的吸收塔容器的断面,并使最上层的喷淋层与除雾器的端面有足够的距离,这样有利于改善除雾器端面处烟气流速的均匀性。
水平烟气流除雾器(即垂直布置)可以使吸收塔/除雾器的实际流速范围扩大到7~8m/s。这种布置方式的除雾器重新夹带液滴的临界流速较高,这是因为水平烟气流除雾器板片上捕获的液滴向下流淌,与烟气流向垂直。而垂直烟气流除雾器板片上的液滴是逆着气流方向下流。因此后者的液滴易于被重新夹带。但水平烟气流的布置占据的空间较大。目前有一种布置方式是第一级为垂直烟气流,第二级为水平烟气流布置,这样兼顾了两种布置方式的优点。
吸收塔/除雾器烟气流速一般由FGD制造商来确定,电厂应要求除雾器供应商提供除雾器的详细性能数据,以便核查设计烟气流速。也可以在工艺技术规范中对吸收塔平均流速规定一个最大偏差值,以免由于烟气流速分布不均匀出现除雾器局部夹带液滴的情况。对于吸收塔烟气流速接近除雾器极限运行流速的高流速设计,有必要实测吸收塔整个断面的烟气流速分布。
五、钙硫比(Ca/S)
1.概念
钙硫比是指注入吸收剂量与吸收SO2量的摩尔比,反映单位时间内吸收剂原料的供给量,通常以浆液中吸收剂浓度作为衡量度量。在保持浆液量(液气比)不变的情况下,钙硫比
增大,注入吸收塔内吸收剂的量相应增大,引起浆液pH值上升,会使中和反应速率增大,反应表面积增加,使SO2吸收量增加,脱硫效率提高。一般认为,吸收塔的浆液浓度选择在
20%~30%为宜,Ca/S在1.02~1.05的范围内。
2.吸收剂利用率
选择吸收剂供应点时主要考虑的问题是,成分符合要求、供应充足可靠、运输距离短和费用合理。对于吸收剂的化学成分,一个重要的项目是惰性物含量要低。惰性物质不仅增加了运输成本,还加剧了FGD工艺管道、阀门和浆泵等过流设备的磨损。对于石灰吸收剂,供应的石灰中应含有适量的 MgO。如果可能,可以要求供应商将 MgO含量不同的两种石灰掺混供货。对新建FGD系统,如果有多个可供选择的吸收剂货源,可以在技术规范中列出它们的地点,运输距离、吸收剂的化学成分和价格,以便投标者在设计中考虑这些因素。
合适的吸收剂供货点确定后,吸收循环浆液中过剩吸收剂的数量是吸收剂最重要的工艺设计参数之一,此数据反映了吸收剂的利用程度,一般用Ca/S摩尔比或吸收剂利用率(%)定量地表示吸收剂的利用程度。Ca/S摩尔比定义为投入FGD工艺中钙吸收剂的摩尔流量(mol/h)与SO2脱除摩尔率
(mol/h)之比。Ca/S比是无量纲比值。吸收剂利用率(%)
的含义是参与脱硫反应的吸收剂量占投入工艺中吸收剂总量的百分率。投入工艺过程中吸收剂总量和参与反应吸收剂量的单
位可用kg/h,也可用mol/h。Ca/S与吸收剂利用率(%)两
者在数值上是互为倒数的关系,即Ca/S摩尔比=l/吸收剂利用率(%)。吸收剂利用率是一个对石灰/石灰石湿法FGD工艺的性能和经济效益有重要影响的设计参数。如果对FGD固体副产物有质量要求,吸收剂利用率往往受这一质量要求的限制。对于抛弃工艺,通常FGD供应商是在权衡投资和运行成本的基础上选择最佳吸收剂利用率。

图13224种不同吸收塔石灰石利用率(ηCa)
与SO2脱除效率(ηSO2)的关系
通常吸收塔循环浆液中石灰石稍微过量一点,就可在非常高的石灰石利用率(>98%)的情况下获得较高的SO2脱除效率。但在石灰石基工艺中,中和已吸收SO2的大多数碱度是依靠吸收塔内固体石灰石本身的溶解来获得的,所以石灰石FGD工艺特性对循环浆液中石灰石固体的总表面积十分敏感。从工艺设计的角度来说,可以通过改变吸收剂的粒度和循环浆液中过剩吸收剂的数量来调节石灰石的总表面积,涉及到Ca/S比问题。提高石灰石细度可以提高其利用率,但是细度的确定还需要综合权衡吸收剂进厂费用、研磨费用(如电厂自己研磨吸收剂)、吸收塔循环泵的能耗费用。
图1322是表1321中美国的四种不同类型吸收塔在L/G不变的情况下,石灰石利用率与SO2脱除效率的关系。从图中可看出:①在每种吸收塔的石灰石利用率范围内,SO2脱除效率随着过量吸收剂的增加(即随着石灰石利用率的下降)而迅速增加;②当吸收剂过量至一定程度时,SO2脱除效率的增加变得缓慢。但需要注意的,图1322中的曲线是根据4种不同类型的FGD装置所特有的许多工艺参数得出的,虽然大多数石灰石湿法FGD系统的这种性能曲线具有类似的走势,但不能用该图中的曲线对这几种类型的其他吸收塔的有关性能进行任何通常的比较,这是因为,SO2脱除效率即是石灰石用量也是L/G的函数。不同的FGD装置有各
自最佳吸收剂利用率,在吸收剂最佳利用率工况下运行,才能获得循环泵电耗和吸收剂的最低综合费用。
根据绘制图1322中喷淋直接影响塔的性能数据,对喷淋塔不同L/G(直接影响循环泵电耗费用)、吸收剂利用率作了一个经济比较,结果列于表1323。这种比较是在不考虑脱硫副产品石膏质量,达到相同脱硫效率(85%)的情况下,在不同L/G和石灰石利用率的三种组合方式下,比较吸收剂费用、循环泵电耗费用以及总费用。考虑到吸收剂价格和电价的高低将影响经济比较结果,假定了两种吸收剂价格和电价。另外,进行比较的喷淋塔的设计基础调整至容量为500MW、燃煤
含硫2%。
表1323
喷淋塔L/G(泵电耗)与吸收剂利用率的经济比较实例
(调整至500MW机组、燃煤含硫2%)



从表1323可看到,投运3台循环泵,运行pH值为5.7,石灰石利用率80%,脱硫率可达85%,当投运4台泵,
L/G为12.3L/m3提高了34%,可在pH值5.5的情况下达到
相同的脱硫率,而石灰石利用率提高到87%。如投运5台泵,L/G较投运3台时提高了约68%,保持相同脱硫率,运行pH值可继续下降至5.3,但石灰石利用率仅较投运4台泵提高了2%,为89%:上述情况体现了L/G、pH值、脱硫率和石灰石利用率四者的关系;增加循环泵投运台数即相当于提高L/G比,如果保持pH值不变,可以提高脱硫率,这时石灰石利用率变化不大;如果保持脱硫率不变,则可降低运行pH值,石灰石利用率也将随之提高;当pH值从5.7降至5.5时,石灰石利用率提高幅度较大(7%),继续再降低pH值,石灰石利用率提高较小(仅2%),投运5台泵时仅较投运4台泵节省
石灰石用量0.3t/h。
表1323列出了两种情况。情况1假定电价相对较低而吸收剂价格相对较高,在投运3台泵,石灰石利用率80%的情况下,泵电耗和吸收剂费用的总和是303美元/h,当4台泵运行,石灰石利用率达到87%,石灰石节省的费用超过电耗增加的费用,总费用下降到294美元/h。但是,当5台泵运行时,总费用增加了,这是因为此时能节省的石灰石很少。另外,脱硫效率的下降对石灰石利用率的进一步提高很敏感(在L/G不变时,见图1322曲线中的陡斜部分),要维持脱硫率不变,仍需较大幅度地提高L/G。这种情况也说明,降低运行pH值可以获得较高的石灰石利用率(即较高的石膏纯度),但必须有足够大的L/G来维持要求的脱硫效率。品质较低的石灰石,要想获得商业质量较高的石膏副产物,措施是提高L/G和固体物停留时间,或提高石灰石的细度。
对于表1323中的情况2,假定电价相对较高,吸收剂价格相对较低,费用比较结果显示,投运3台泵,石灰石利用率仅80%是最佳运行工况,再增加循环泵投运台数,由于电价较高造成电费的增加超过了减少石灰石用量所节省的费用。
从上述两种情况的比较结果可看出,一些工艺参数将影响吸收剂最佳利用率,在不考虑脱硫副产品石膏质量的情况下,吸收剂最佳利用率主要取决于电价和吸收剂的价格。
需要指出的是,还有一个重要的因素制约石灰石最佳利用率的确定。当石灰石利用率低于85%时,除雾器堵塞可能成为运行中的严重问题。附着在除雾器板片上、含有大量过剩石灰石的浆液可以继续吸收烟气中剩余的SO2,加速了除雾器板片上垢的形成。因此,即使费用评价表明较低石灰石利用率有较好的经济效益,从全面考虑,工艺技术规范仍应要求石灰石利用率始终保持高于85%。
应该再次指出的是,对石膏副产物有质量要求的FGD系统,满足石膏品质所要求的石灰石利用率是设计允许的最低利用率。
如果进行更详细的分析,还应考虑吸收剂粒度对性能的影响。如果石灰石较贵而电价较便宜,那么在达到要求的脱硫效率情况下、应通过较细地研磨石灰石和采用较高的L/G来获得较高的石灰石利用率。相反,如果吸收剂便宜而电价较高,那么可以采用过量较多的吸收剂来减少循环泵和研磨石灰石的电耗费用。
六、浆液Cl—浓度
FGD工艺浆液中氯化物来源于燃煤、工业补加水和吸收剂。一般石灰石中氯含量很少,工业补加水含氯1.2~150mg/L,我国
大多数煤中氯含量不大于0.05%,少数煤0.06%~0.15%,个别
高灰分煤可达0.47%,因此FGD工艺浆液中大部分氯化物来源于燃煤。
燃料含氯量是FGD工艺技术规范中需要说明的一个重要数据。在燃烧过程中,燃料中的氯转变成烟气中的 HCl,烟气中的HCl基本上全部在FGD吸收塔中被捕获,并主要以
CaCl2和 MgCl2形式富集在FGD浆液中。烟气带入 HCl的数
量、补加水引入的氯化物、随固体副产物带离系统的工艺液量以及废水排放量决定了FGD浆液中氯化物的浓度。在正常运行工况,浆液中氯化物的浓度是稳定的。浆液中的Cl-浓度对FGD系统结构材料的选择有很大的影响。高浓度的Cl-还影响脱硫效率和石灰石利用率,石膏中可溶性氯化物含量过高将影响石膏综合利用价值。
可以用以下方式在工艺技术规范中确定浆液Cl-浓度。(1)仅给出物料含氯量和工业水中氯化物含量,由FGD
供应商根据其物料平衡计算结果来确定氯化物的设计浓度。
(2)电厂可以对工艺浆液中的氯化物设计浓度规定最低和最高值。
(3)对石膏副产物有质量要求的,可以规定固体副产物中氯化物的最高含量。
对上述任何一种情况下,电厂还必须规定是否允许有单独的废水排放。如果允许,应对废水排放量和排放废水的质量提出限制。
近年美国已安装的石灰或石灰石湿法FGD系统浆液的氯化物设计浓度的范围大致为10~50g/L,通常石灰基系统的Cl-浓度处于上述范围的低端。因为高Cl-浓度可能会增加固体副产物脱水难度。石灰石基系统,特别是强制氧化系统,Cl-浓度处于这一范围的较高一侧。但据2000年有关资料报道,由于日益严格的环保法规,要求脱硫装置零排放和闭路运
行,Cl-浓度按数据级增加,一般在20000×10-6~70000×
10-6范围。我国近年建成的湿法石灰石FGD系统一般规定反应罐浆液Cl-浓度的设计值不超20g/L,实际运行浓度大约1
~15g/L。
据试验数据,当浆液氯化物浓度超50g/L,吸收塔的传质能力将下降30%~40%,因此,Cl-浓度较高的吸收塔需要较高的L/G,较多的石灰石或改变FGD系统其他性能参数来抵消氯化物对脱硫效率的影响。如果FGD系统业主不允许排放废水,那么FGD供应商就必须根据工艺过程物料平衡确定的氯化物含量进行FGD系统设计,而无论得出的Cl-浓度有多高,如果允许排放废水,那么需要考虑回收石膏允许Cl-浓度,还须对废水处理达标排放所需的费用与高Cl-浓度的设计方案进行比较。
目前还缺乏石灰FGD系统在类似这样高的Cl-浓度下的运行资料。但是,石灰基系统液相碱度比石灰石基系统的高得多,因此Cl-浓度对吸收塔传质能力的影响要小得多。
第三节 FGD工艺过程的物料平衡
根据质量守恒定律,任何一个生产过程,其原料消耗量应为产品量与物料损失量之和。通过了解FGD工艺过程的物料平衡,可以知道输入系统的原料转变为脱硫副产物以及流失的情况,以便寻求改善这一转变过程的途径。在FGD系统设计中需进行物料平衡计算,确定原料、产出物和损失物的数量关系以及系统热平衡关系,物料平衡计算是FGD系统设计的重要数据,也是运行管理的重要参数。
一、物料平衡
图13 3 1是石灰/石灰石湿法FGD工艺总物料平衡示意图。系统的主要输入流体是烟气和吸收剂。烟气进入FGD系统之前,先经除尘装置(EP或布袋除尘器)除去烟气中99.5%以上的飞灰。虽然一些石灰/石灰石湿法FGD工艺

图1331 石灰/石灰石湿法FGD系统总物料平衡示意图
能除去烟气中的飞灰(一般除尘效率不超过80%),或采用碱性飞灰作吸收剂,但飞灰对工艺过程会产生一些有害的影响。这种有害影响主要是:①降低石膏质量;②加重了浆液对设备的磨损性;③增加了脱硫石膏脱水难度;④“封闭”吸收剂,使其失去活性。后一种情况在运行中的表现是,浆液pH值、脱硫效率降低,虽向吸收塔内大流量地注入吸收剂浆液,反应罐pH值仍不上升,吸收率也没有明显回升。其原因多半是进入吸收塔的烟尘含量较高,运行pH值控制又较低,由飞灰带入的Al3+与浆液中的F-形成的络合物达到一定浓度,吸附在吸收剂固体颗粒表面,“封闭”了吸收剂的活性,显著减慢了吸收剂的溶解速度。随飞灰引入系统的其他化学物质,如镁、锰能起到氧化催化剂的作用。随飞灰带入的一些重金属除了会影响工艺的化学反应外,还会影响排放废水的质量。因此,一般不希望有过量的飞灰带入吸收系统。入口烟气的主要气体成
分是N2、CO2、O2、水蒸气、SO2、NOx、HCl、HF和硫酸
蒸气,微量化合物有NH3、CH4、CH3Cl等。烟气或飞灰中
还存在一些有害微量元素,例如目前较为重视的汞及汞的化合物。
在FGD系统中,烟气中的大部分SO2和部分O2被吸收进入浆体的液相。在石灰石基工艺中每吸收1molSO2,理论
上要消耗1molCaCO3,产生1molCO2进入烟气中。而在石灰
基工艺中,可能会从烟气中吸收少量CO2(一般每吸收1mol
SO2,吸收的CO2小于0.1mol)。一个脱硫率为95%的FGD
系统,基本上也应能脱除烟气中几乎全部HCl和HF。由烟气带入FGD系统的氯化物会影响脱硫效率、石灰石的溶解和耐腐蚀材料的选择。入口烟气中的NO通常不被吸收,NO2仅少部分被吸收。
入口烟气中通常含有少量气态硫酸,气态硫酸浓度大约是
SO2浓度的0.5%~1%,当烟气被冷却时,气态 H2SO4迅速
凝结成亚微米大小的气态胶酸雾。一般吸收塔仅能除去约50%的这种酸雾,剩余的酸雾进入吸收塔下游侧的设备中将造成酸腐蚀,最后从烟囱排出的酸雾以及其他颗粒物由于对光的散射使烟气形成一种看得见的白色烟流。目前控制这种酸雾的方法主要是向炉内或烟道中喷入吸收剂减少酸雾的形成;另一种方法是通过与吸收塔一体化的湿式EP来除去。
烟气在吸收塔内被洗涤时,很快达到水汽饱和,这是水平衡中水耗的主要部分。吸收塔内水蒸发量取决于煤的组成、入口烟气温度和烟气含水量,洗涤1MW电所产生的烟气通常蒸
发的水量大约是0.1m3/h左右(有 GGH),0.13~0.2m3/h(无GGH)。
造成系统水损失的其他原因有:①为控制浆液中某些有害成分的浓度而设置的废水排放。这种废水排放量从每小时几吨到几十吨,这取决于煤中Cl、F含量、浆液有害成分的控制浓度、脱硫副产物的处理方式以及对耗水量控制的严格程度。如果固体副产物采取水力输送湿排的方式废弃,仅此项造成的水耗就可能高达100m3/h以上;②随脱硫固体副产物带离系统的附着水和化学结晶水,由此损失的水相对较少。也有些系统不单独设置排污口,随固体副产物带离系统的液体成为带走FGD系统中可溶性物质(例如Cl-)的唯一渠道,这样,带离系统的水量就控制了工艺过程浆体液相中可溶性物质的浓度。
在FGD工艺过程中,必须向系统不断补加水以弥补水分蒸发和其他原因所损失的水量,以保持系统水平衡。但在有些情况下,尤其当锅炉低负荷运行时,补加水量可能超过系统损失的水量。因此,必须将工艺过程中过量的液体临时贮存或
排放。
采用工业水作补加水、密封水或 ME冲洗水时,一般不考虑工业水中的可溶性盐的影响,除非工业水中Cl-浓度较高。
脱硫产生的固体副产物与脱除的SO2有一定的比例关系,在抑制氧化工艺中,固体副产物的摩尔质量大约是131g/mol,因此,理论上每脱除1kgSO2可产生干亚硫酸钙/硫酸钙固体物大约2.05kg。对于强制氧化工艺,石膏副产物摩尔质量是
172g/mol,每脱除1kgSO2,干石膏固体物的理论产出率是
2.69kg。在这两种工艺中,固体产物的实际产出率要稍高些,因为副产物中还含有烟气带入的飞灰,石灰/石灰石吸收剂中的惰性物质以及一些未反应的吸收剂。
通常将亚硫酸盐固体副产物废弃于专用坑或池中,或填埋。如果填埋这种固体物,那么需要经过处理,即将脱水后的固体副产物与飞灰混合(稳定作用)或与飞灰和石灰混合(起固定作用)以改善其物化特性。硫酸钙(石膏)可以筑池填埋或堆放在地面而无需经过稳定化或固定化处理,石膏还可以作为商品出售。
二、工艺水平衡
表1331列出了三种主要湿法FGD工艺中水平衡的典型补、耗水项目和数量。表中“其他补加水”一项是指系统其他冲洗水、冷却水和为保持系统中某些罐池液位所需加入的水。在运行工况稳定的情况下,进入工艺过程的水量应等于离开系统的水量。为便于比较,三种 FGD工艺均处理来自500MW燃煤锅炉的烟气,燃用煤为烟煤,含硫量为2%,
FGD系统装有GGH。
表1331 石灰/石灰石FGD工艺水平衡中
的典型补、耗水项目和数量

在镁石灰基工艺例子中,系统总耗水率达到72.3m3/h,其中耗水最大的是蒸发至烟气中的水量53.2m3/h,约占总耗水量73.6%,固体副产物带走的水量占总耗水率26.4%。这种工艺产生的固体物最难脱水,通常最大脱水率大约50%。固体副产物结晶水带离系统的水很少,不到总耗水量的2%。供入镁石灰工艺中的水包括熟化生石灰并配置成浓度为35%吸收剂浆液用水,这部分用水必须采用含可溶性固体物较少的水,而不能采用回收水。在镁石灰工艺中,可以用回收水来冲洗ME,因此冲洗 ME不增加水耗。为防止可溶性盐加剧对转轴的腐蚀,转动机械所需的密封水也要采用品质较好的工业水。另外,为保持系统水平衡,需另外供入系统的补加水量为
33.2m3/h。
在石灰石抑制氧化工艺中,可以用工艺回收水来制备吸收剂石灰石浆液和冲洗 ME。本工艺的转动机械密封水量(20.1m3/h)比上一例稍多些,是因为这种工艺的吸收塔循环泵的台数要多些。固体副产物通常脱水至含水约30%,因此,随石灰石抑制氧化工艺固体副产物带走的水量仅为镁石灰基系统带走的62.3%,这是造成上述两种工艺总耗水量差异的根源。
在石灰石强制氧化工艺的例子中,固体副产物是具有商业总量的石膏,因此随副产物带走的自由水相当少,而蒸发消耗的水量(60.4m3/h)较前两例较高些,这是因为鼓入浆液中未饱和的氧化空气增加了水分的蒸发。另外,由于对石膏质量的要求,石膏滤饼中氯离子的最高浓度限值为200m3/h(干基),因此,需冲洗石膏滤饼,但冲洗滤饼的水是来自水环真空泵的密封水,后者用水量9~15m3/h。加上对工艺性能和防腐材料的考虑,需要向系统外排放一定量的废水,以限制工艺浆液中的Cl-浓度。上述两个原因使得石灰石强制氧化工艺的耗水量最高。
对氯化物浓度的不同控制、吸收塔性能对氯化物浓度的敏感程度以及是否对耗水量(或废水排放量)提出了严格的设计要求等因素,可能造成废水排放量相差很大。例如北京
某电厂FGD系统(2炉1塔、喷淋塔),设计煤含硫1.04%、
含氯0.035%,处理烟量950000 m3/h(W),控制浆液Cl-
浓度小于20000×10-6(20g/L),设计排往废水处理系统的废水仅1.9m3/h。而某电厂3号、4号机组的FGD系统(1
炉1塔),设计煤含硫4.02%、含氯0.035%,单塔处理烟量915000m3/h,由于Cl-浓度控制的较低,小于1000×10-6
(1g/L),对废水排放量未提出要求,因此设计废水排放量高
达71.6m3/h(该FGD系统未设计废水处理装置)。从表1
331所列系统消耗水项目和耗水量看出,蒸发和排放废水是造成石灰石强制氧化工艺较前两种工艺总耗水量高的主要原因。
在强制氧化工艺中,回收的工艺液被石膏饱和,主要用来制备吸收剂浆液和调整反应罐液位。早年建设的强制氧化FGD系统曾采用回收水与一定量的淡水混合,作为 ME的冲洗水。目前一般仅用工业水冲洗 ME,冲洗后的水流回吸收塔。系统另一个补加水源是真空皮带脱水机水环式真空泵和其他泵、搅拌器等转动设备的密封水和冷却水。
在上面的例子中并没有列出所有加入工艺过程中的各种水源,例如吸收塔入口干/湿界面、氧化配气管的冲洗水和一些转动机械的冷却水,在进行实际水平衡计算时需要做全面核算。表1331仅比较了这三种工艺的补加水和耗水有差别的主要项目。
上述例子是基于锅炉连续满负荷运行,当锅炉在低于额
定工况下运行时,使烟气饱和以及随固体副产物带离系统而造成的水耗量将按比率减少,但转动机械密封水,冷却水以及 ME冲洗水往往不会按比例下降,在这种情况下,补加水量有时会多于损失的水量,这种情况称作“正水平衡”。通常设置一个平衡水箱来接纳短时间正平衡时排出的过量补加水。当出现负水平衡时,用作补充水。如果长时间出现正平衡,则要么增加排放水量,要么采取措施减少加入工艺中的补加水量。
三、氯化物浓度对废水排放量的影响
当石膏脱废气处理时,可以脱水至含固量约70%(含水
30%);石膏商用时,可以脱水至90%(含水10%)。这样从
系统排出的水就只是随固体副产物带离的水,由于这部分水与蒸发的水量相比要少得多,因此进入FGD系统的可溶性化合物将在工艺过程液中逐渐累积起来。工艺液中Cl-浓度主要受固体副产物脱水程度和煤中氯硫比(Cl/S)的影响,高Cl/S,高脱水率使得工艺液中Cl-浓度较高。而高硫煤由于产出的固体物增多,随固体副产物带走的水量也增多,煤中氯含量低则减少了随烟气带入系统的Cl-量,因此高硫低氯煤(即Cl/S低)使得工艺液中Cl-浓度相对较低。对同一种FGD工艺、同一种煤,补加水质量不同也会影响工艺液中Cl-浓度,但影响程度要小些。
如果要求生产具有商业质量的石膏,就必须从工艺过程中排放适当的废水,以维持循环浆液中适当的杂质含量,图1 332示出了为维持排放废水中一定的Cl-浓度(亦即循环浆体液相中的Cl-浓度),废水排放量与锅炉容量和煤中含氯量的关系。从该图可看出,当锅炉容量在300~600MW范围内,燃煤含氯为0.05%时,维持浆液中 Cl-浓度不超过
20g/L,需排放废水量在3.3~6.0m3/h范围内。废水排放量
随锅炉容量和煤中含氯量增大而增加。两种FGD工艺“闭路”运行时工艺液中Cl-浓度与燃煤和补加水的关系见表13
3 2。

图1332 废水排放量与锅炉容量
和煤中含氧量的关系
表1332 两种FGD工艺“闭路”运行时工艺液中
Cl—浓度与燃煤和补加水的关系

注 1.高Cl/S比煤含S:2.0%;含Cl:0.10%;Cl/S=0.05。
2.低Cl/S比煤含S:4.0%;含Cl:0.04%;Cl/S=0.01。3.高Cl-补加水含Cl-:200mg/L。
4.低Cl-补加水含Cl-:100mg/L。
第四节 烟气系统设计要点
烟气系统由烟道、烟气挡板、增压风机、烟气换热器、烟道补偿器等组成。
一、烟道
1.概述
脱硫烟道通常根据其在FGD系统中的位置和所起的作用来定义和划分,考虑到不同部位烟道所处的腐蚀环境不同,从FGD系统入口开始将烟道划分如下:
(1)FGD系统入口烟道,从FGD系统入口至GGH原烟气入口,输送从引风机、除尘器或其他设备到FGD系统的未处理的热烟气。
(2)吸收塔入口烟道,从GGH原烟气侧出口至吸收塔入口,输送经GGH降温后的未脱硫烟气。为区分这部分烟道所具有的不同腐蚀环境,将靠近吸收塔入口2m左右的烟道称为吸收塔入口干/湿交界区(也称为干湿界面)。
(3)吸收塔出口烟道,从吸收塔出口至GGH净烟气侧入口,输送来自吸收塔的低温、饱和净烟气。
(4)FGD系统出口烟道,从GGH净烟气侧入口至与旁路烟道交接处,输送经GGH升温后的净烟气。
(5)旁路烟道,又称为混合烟道,从FGD系统入口至烟囱入口的直通烟道。FGD系统未启动时输送来自引风机的原烟气,FGD系统正常运行时旁路挡板上游侧烟道接触原烟气,旁路挡板下游侧烟道接触经GGH升温后的净烟气。由于旁路挡板下游侧烟道有时要输送原烟气,有时要输送已处理的中温净烟气,所以将这段烟道称为FGD系统公共出口烟道。
(6)如果是湿烟囱系统,不设置烟气换热器时,则可简单地将烟道划分为:吸收塔入口烟道(从系统入口至吸收塔入口)、吸收塔出口烟道(从吸收塔出口至与旁路烟道交接处)和旁路烟道。同样,距吸收塔入口2m处的烟道为吸收塔入口干/湿交界处;旁路挡板至烟囱入口的旁路烟道仍称为系统公共出口烟道。
2.烟道设计要点
(1)脱硫烟道的设计应依据《火力发电厂烟风煤粉管道设
计技术规程》(DL/T5121—2000)及其配套设计计算方法,
且脱硫净烟道应尽可能少设或不设内撑,脱硫原烟道的内撑设
计应考虑防磨等措施。
(2)急转弯头应考虑烟气导流设计,使流场均匀,降低系统阻力。
(3)场地允许的条件下,可考虑采用圆形烟道以利于气流分布、节约钢材用量。
(4)防腐:烟气换热器前的原烟道可不采取防腐措施。烟气换热器和吸收塔进口之间的烟道,以及吸收塔出口和烟气换热器之间的烟道应采用鳞片树脂和衬胶防腐。烟气换热器出口和主机烟道接口之间的烟道宜采用鳞片树脂或衬胶防腐。
二、烟气挡板
1.概述
烟气挡板门的主要作用是隔离设备、控制烟气流量和排空烟气。一般根据其安装位置和功能分为FGD入口原烟气挡板、FGD出口净烟气挡板、FGD旁路挡板,为保证烟气的密封隔离效果一般挡板门需要安装相应的密封风系统。当多炉共用一塔时,如果设有多台增压风机往往还需配置相应的隔离门。
2.挡板门设计要点
(1)脱硫装置烟道挡板宜考虑采用带密封风的挡板,应有良好的操作和密封性能。
(2)脱硫挡板门密封风系统可考虑每个挡板设一套密封风系统,即采用“1对1”配置,也可以考虑脱硫系统出口、入口、旁路挡板共用一套1用1备的密封风系统。
(3)挡板门密封风宜设置电加热器,至少旁路挡板要设电加热器。电加热器建议设置旁路管道,考虑节能,夏季温度较高时可以停用。
(4)烟气挡板对锅炉的安全性有很大影响。为保护FGD系统及减少对锅炉的影响,在设计时,可将原烟气挡板、旁路挡板的电源由FGD系统380V开关柜改在主厂房380V工作段或公用段,保证在紧急情况下能正常操作,从而提高FGD系统安全性。
(5)通常FGD系统内的挡板门有三种类型:①单百叶窗式挡板;②双百叶窗式挡板;③闸板门。目前主要采用带密封风的双百叶挡板门。在烟气温度较高的场合,单百叶窗式挡板用碳钢制作。每片挡板设有金属密封元件,以尽可能减少烟气泄漏。驱动装置设在烟道外部,由控制系统控制其开关位置。采用双百叶窗式挡板门除了每层挡板上配备密封元件外,在两层挡板中间还通入密封空气。双百叶窗式挡板门和闸板门应用于严密性要求特别高的场合。但由于闸板门的空间要求大,因而在电厂应用不太普遍。
(6)密封风机采用分散就地布置,系统简单,维修方便,且对其他系统无影响。
3.脱硫旁路及旁路挡板设计要点
(1)烟气脱硫装置在设置旁路烟道时,旁路挡板常设置双执行机构,以提高机组及脱硫系统运行的安全可靠性。
(2)旁路挡板门的开启时间应满足脱硫装置故障不引起锅炉跳闸的要求,以便对锅炉和FGD起到保护作用。
(3)烟气脱硫装置在不设置旁路烟道时,吸收塔进口应设置预洗涤装置或预喷淋装置。在锅炉点火、锅炉投油助燃时,该装置起到除油、预除尘作用;在烟气温度超过设置范围时,起到喷淋降温作用;目的是保护FGD系统。
(4)烟气脱硫装置在不设置旁路烟道时,脱硫系统的可靠性应按不低于主机的要求进行系统设计、设备及材料的选择、施工等。
三、增压风机
1.概述
在脱硫系统中,烟气的输送依靠增压风机来克服烟道、烟气挡板、GGH、吸收塔、烟囱和其他设备的阻力,因此,一个很重要的问题是增压风机的可靠性和经济性,与此问题相关联的是增压风机类型的选择和布置方式。风机类型、风机的调节和布置方式等可以有多种不同的搭配,因此针对具体情况要做到合理的选择,需要全面考虑。目前,脱硫系统中常用的风机形式主要有静叶可调轴流风机、动叶可调轴流风机、离心风机,目前普遍采用增压风机与引风机合一的形式。
2.脱硫增压风机的设计要点
脱硫增压风机可根据当地气象条件及设备状况等因素研究可否露天布置。当露天布置时应加装隔音罩或预留加装隔音罩的位置。脱硫增压风机宜装设在脱硫装置进口处,在综合技术经济比较合理的情况下也可以装设在脱硫装置出口处。当条件允许时,也可与引风机合并设计。
(1)目前脱硫系统克服烟风系统阻力,一般有两种情况:①增压风机引风机合一,部分新建机组采用该方式;②单独设置脱硫增压风机,技改机组中一般单独设置脱硫增压风机。
(2)当场地紧张或条件允许时,经论证若对锅炉主机系统基本无影响、引风机有足够的裕度,也可考虑用原有引风机代增压风机,增容或更换引风机,不设置增压风机。
(3)大容量吸收塔的脱硫增压风机宜选用静叶可调轴流式风机,当风机进口烟气含尘量能满足风机要求,且技术经济比较合理时,可采用动叶可调轴流式风机。机组容量为300MW及以下时,也有少数机组采用高效离心风机。
(4)300MW及以下机组原则采用静叶可调轴流风机,600MW及以上机组原则采用1台动叶可调轴流式风机,或配置2台静叶可调轴流风机。
(5)300MW及以下机组每座吸收塔宜设置1台脱硫增压风机,不设备用。对600~900MW机组,经技术经济比较确定,也可以设置2台增压风机。
(6)多炉一塔脱硫时,可采用一台动叶可调轴流风机或每炉对应一台静叶可调轴流风机。采用“一对一”方式设计时,烟风系统设计应考虑防止抢风和内耗。
(7)脱硫增压风机的风量和压头按下列要求选择:
1)脱硫增压风机的基本风量按吸收塔的设计工况下的烟气量考虑。脱硫增压风机的风量裕量不低于10%,另不低于10℃的温度裕度。
2)脱硫增压风机的基本压头为脱硫装置本身的阻力及脱硫装置进出口的压差之和。进出口压力由主体设计单位负责提供。脱硫增压风机的压头裕量不低于20%。
3)由于脱硫后烟囱进口的净烟气温度比原烟气低,烟囱的自拔力相应减少,增压风机的压头应考虑此项因素。脱硫装置的进口压力参数应取用脱硫装置的原烟气烟道与主机组烟道接口处的压力参数,而不是引风机出口的压力参数。脱硫装置的出口压力参数原则上也应采用脱硫装置的净烟气烟道与主机烟道接口处的压力参数,而不是完全等同于烟囱进口的压力参数,烟囱进口的压力参数应考虑脱硫后烟温降低导致烟囱自拔力减少,其进口压力应相应增大的因素经核算后由设计单位提供。
四、烟气换热器
1.概述
烟气换热器有回转式烟气换热器(GGH)、管式换热器
等,其主要功能是改善污染物扩散、减少烟囱可见烟羽、避免下游烟道腐蚀、避免烟囱液滴“下雨”等。在环境影响评价许可情况下,也可以不设置烟气换热器。
2.烟气换热器设计要点
(1)设置烟气换热器时,设计工况下脱硫后烟囱入口的烟气温度一般应达到80℃及以上;在满足环保要求且烟囱和烟道有完善的防腐和排水措施并经技术经济比较合理时也可不设烟气换热器。
(2)烟气换热器可以选择回转式换热器或以热媒水为传热介质的管式换热器,当原烟气侧设置降温换热器有困难时,也可采用在净烟气侧装设蒸汽换热器。用于脱硫装置的回转式换热器漏风率应使脱硫装置的脱硫效率达到设计值,一般不大
于0.5%。
(3)按设计项目环境影响报告书的审批意见确定烟气系统是否装设烟气换热器,在满足环保要求且烟囱和烟道有完善的防腐和排水措施并经技术经济比较合理时可不设烟气换热器。
(4)烟气换热器的受热面均需考虑防腐、防磨、防堵塞、防沾污等措施,与脱硫后的烟气接触的壳体也应考虑防腐,运行中应加强维护管理。
(5)对于设有烟气换热器的脱硫装置,应从烟气换热器原烟道侧入口弯头最低处至烟囱的烟道采取防腐措施,防腐材料可采用鳞片树脂或衬胶。经环境影响报告书审批批准不装设烟气换热器的脱硫装置,应从距离吸收塔入口至少5m处开始采取防腐措施。防腐烟道的结构设计应满足相应的防腐要求,并保证烟道的振动和变形在允许范围内,避免造成防腐层脱落。烟气换热器下部烟道应装设疏水系统。
(6)脱硫装置原烟气烟道设计温度应采用锅炉最大连续工况下燃用设计燃料时的空预器出口烟气温度并留有一定的裕量。对于新建机组,应保证运行温度超过设计温度50℃,叠加后的温度不超过180℃的条件下的长期运行。烟气换热器下游的原烟气烟道和净烟气烟道设计温度应至少考虑30℃超温。
五、烟道补偿器
1.概述
FGD烟道中大多数膨胀节采用非金属膨胀节。非金属膨胀节由纤维或金属丝加强的、或者纤维和金属丝网复合加强的氟塑料或氟橡胶片,保温材料,内部挡板和连接法兰构成。
2.补偿器设计要点
(1)原烟气补偿器应耐磨耐温,净烟气补偿器应耐腐、防渗,必要时考虑疏水措施。
(2)补偿器均应考虑足够的轴向和径向位移,蒙皮应利于更换。
(3)如果采用金属补偿器材料,应耐腐耐温耐磨。
第五节 GGH设置
一、设置GGH的有关规定
吸收塔出口烟气温度在50℃左右,目前有加热排放和不加热直接排放两种方式。《火力发电厂脱硫设计技术规程》
(DL/T5196—2004)中规定:“烟气系统宜装设烟气换热器,
设计工况下脱硫后烟囱入口的烟气温度一般应达到80℃及以上排放”,但同时也说明:“在满足环保要求且烟囱和烟道有完善的防腐和排水措施并经技术比较合理时也可不设烟气换热
器”。在《火电厂烟气脱硫工程技术规范》(HJ/T179—2005)
中第5.2.5条规定:“现有机组在安装脱硫装置时应配置烟气
换热器。新建、扩建、改建火电厂建设项目,在建设脱硫装置时,宜设置烟气换热器,若考虑不设置烟气换热器,应通过建设项目环境影响报告书审查批准。”
二、设置GGH的目的
烟气再加热系统一般是根据需要传递给烟气流的热量来设计,加热烟气的总热量等于抬升和扩散烟气、消除(或降低)烟羽可见度、蒸发液滴以及防止烟气在烟道和烟囱中发生冷凝所需热量的总和。目前,我国FGD系统最常见的烟气再加热方式是:采用回转式预热器 GGH,蒸汽加热SGH,以及从日本引进的以水为媒体的管式 MGGH。其中GGH得到了最广泛的应用。从脱硫系统来看,设置GGH的主要目的是:
(1)在GGH的吸热侧将未脱硫的高温原烟气在进入吸收
塔前由120~150℃降至100℃,一方面提高烟气中SO2与脱
硫吸收剂的反应效率,另一方面保护吸收塔内的防腐层免受高温的伤害。
(2)在GGH的放热侧将经洗涤脱硫后的净烟气温度由50℃左右加热至80℃后,再经烟囱排放到大气。一方面烟气排放温度虽然依然低于亚硫酸或硫酸的露点温度150℃,但高于腐蚀性极强的氯化氢和氟化氢的露点温度(65℃左右),从而大大降低了对下游烟道、烟囱和其他设备的腐蚀;另一方面烟气排放温度的提高对大气环境质量的改善非常有益。从环境质量来看,设置GGH后将脱硫烟气温度提高,对区域大气环境治理有益,主要体现在:
1)污染物抬升高度和扩散程度得到提高。2)烟羽的可见度得到降低。
3)降低了烟囱降落液滴。
三、关于GGH设置的发展趋势
在湿法脱硫工艺中,不设置GGH最重要的依据依然是烟气排放温度的要求,其次是GGH难于克服的故障。我国从2003年开始,在实施的湿法脱硫工程中开始出现不设置GGH的现象,由于不设置GGH没有明确规定,政府也无法明令禁止,其后不设置GGH的湿法脱硫工程越来越多,到2005年底在已建成投产的湿法 FGD中,无 GGH的仅占7%,但在在建的湿法FGD工程中,无GGH的比例大幅增加,2007年后多数电厂脱硫基本不采用GGH,特别是取消旁路烟道后。
在欧洲,由于大部分欧盟成员国对烟气排放温度没有法规上的要求,普遍认为,不安装GGH是今后FGD发展的趋势。已经有越来越多的电厂将脱硫后的烟气通过冷却塔排放,这样既可以不安装GGH,又可以节省湿烟囱的投资,而且也大大提高了烟气中污染物的扩散能力。
第六节 GGH设置方案比较
加热烟气是指吸收塔出口已处理烟气在经烟囱排放前提升烟温的工序,是否采用加热装置取决于各国环境保护法规对排烟温度的要求。在国外,虽然现有的许多电厂FGD装置采用了烟气加热器,但大量新建的电厂已不再安装烟气加热器。我国则无排烟温度要求,提高FGD排烟温度将会显著增加FGD系统的投资和运行费用,因此,如果环境保护法规对加热烟气不做要求,湿烟囱工艺是较为经济的选择。
一、加热烟气的理由
1.加强污染物的扩傲
提高烟气温度,增大了烟羽的浮力,能提高烟气离开烟囱
后的抬升高度,使烟羽能更好地扩散。有利防止发生烟羽下洗,降低污染物稀释后的落地浓度,推迟或减少了水雾的形成。另外,在一定程度上能提高烟羽的透明度。在世界上有些地区,尤其在发电厂靠近人口聚居区的情况下,有些地方环保法规可能要求提升烟温高达90℃,使排放物充分扩散,满足污染物落地浓度的限值。另外,有些电厂为了加强烟气扩散,可能规定了烟囱出口烟气最低温度。
我国虽然未明确规定火电厂FGD装置排烟温度,对白色烟羽也未加限制,但提高排烟温度将增大烟囱烟气抬升高度,使火电厂能获得较高的SO2最高允许排放量。因此,从加强污染物的扩散,降低污染物落地浓度来说,加热FGD排放烟气仍是一种行之有效的方法。
2.降低烟羽的能见度
如果没有将烟气加热到足够的温度,从烟囱中排放的脱硫烟气将呈现出大量的白色蒸汽。为防止出现白色蒸汽烟羽,烟温需提升的程度在一定程度上取决于环境温度和风的情况。如果烟温提升不够,将会出现白色蒸汽烟羽,但是蒸汽烟羽在离开烟囱很短的一段距离后会很快被分散而消失。在大多数天气情况下,要防止形成任何可见的蒸汽烟羽需要提升排烟温度50~100℃,在寒冷的天气里,需要加热到更高的温度。因此,虽然加热烟气可以降低烟羽的能见度,但是很难做到在任何气候条件下都不形成白色蒸汽烟羽。
另外,烟气的其他成分,包括颗粒物(飞灰),H2SO4和NO2也可以造成烟气黑度,加热烟气可以提高烟气这些成分的扩散率,但无助于降低这些物质造成的烟气黑度。
3.防止降落液滴
来自湿法FGD系统的饱和烟气总会含有一定量的液滴,其含量的多少取决于ME的效率和其他一些因素。过去认为加热烟气能蒸发这些液滴和防止烟气中的水分冷凝形成液滴。实际上,由于烟气在烟道和烟囱中停留的时间很短,加热烟气只能蒸发非常小的液滴,汇集在烟道壁上的液体被烟气二次带出所形成的较大液滴在它们离开烟囱前是不会被蒸发的。当然,加热烟气可以减少甚至有可能消除烟气在烟道壁上形成的冷凝液,烟道壁面冷凝液的减少也会降低烟气中形成大液滴的几率。
有以下原因会造成烟气通过烟道和烟囱时产生热损失:①经烟道和烟囱内壁散发热量;②漏风;③烟气顺烟囱上升时的绝热膨胀。热损失导致了烟气在烟道和烟囱中的冷凝。烟气的热损失率主要取决于烟道和烟囱的结构、保温材料以及环境温度。因此,这种热损失因地而异。烟气在烟囱中因绝热膨胀造成的烟温下降可以根据烟囱高度去估算,当烟气沿着150m高的烟囱上升时,由于压力下降,烟气限度大约降低0.3℃。由此产生的冷凝液大约是18mg/kg(干烟气)。对于一个500MW的机组,冷凝液可能多达1.2L/s,加热烟气对于弥补这一温度下降和降低由此形成的冷凝液是一种有效的方法。
4.避免腐蚀
早期FGD系统采用烟气再加热的主要理由之一是避免腐蚀吸收塔下游侧烟道和烟囱的内烟道;但是,许多这种加热装置下游侧的设备仍然遭受了大面积的腐蚀。在有些情况下,加热装置下游设备的腐蚀速度和腐蚀程度实际上比采用类似材料的湿烟囱的腐蚀更厉害。这些设备的腐蚀情况清楚地说明,如果有酸性冷凝物存在,在较高的温度下材料的腐蚀要快得多。
虽然通过精心设计再加热器和改进结构材料已减少了与加
热烟气有关的腐蚀问题,但是腐蚀问题的减少还难以认为有理由采用烟气加热器。
二、可供选择的烟气加热方式
净烟气再加热的方法主要以下几种:
(1)气—气加热器。即GGH,它利用脱硫系统上游的热烟气加热下游的净烟气,其原理与锅炉的回转式空预器完全相同。其初投资和运行维护费用都很高,且有腐蚀、堵塞、泄漏等问题,国外早期的脱硫系统上应用很多,但目前已不太用,而国内大多数脱硫系统中都装设有GGH。
(2)水煤式GGH也称无泄漏型GGH(MGGH)。在日本
基本上采用这种型式,该加热器可分为两部分:热烟气室和净烟气室,在热烟气室热烟气将部分热量传递给循环水,在净烟气再将热量吸收。它不存在原烟气泄露到净烟气内的问题,管道布置可灵活些。
(3)汽—气加热器。即用热蒸汽加热净烟气,此种加热器属于非蓄热式间接加热工艺,这一工艺流程是在管内流动的低压蒸汽将热量传给管外流动的烟气,蒸汽流量根据净烟气加热后的温度来调节。其特点是设计和运行简单,初投资小,在场地受限时可用,但能耗大,运行费用很高,也易出现因腐蚀、管子附沉积物而影响换热效果的问题。
(4)热管换热器。管内的介质在吸热段蒸发,蒸发沿管上升至烟气加热区,然后冷凝放热以及加热低温烟气,如图1 361所示。它不需要循环泵,然而多数热管安装都要求入口和出口管接近,并且一个再热系统会用到大量热管,目前在火电厂脱硫系统中应用较少。

图1361 热管换热器
(5)旁路再热器。烟气部分脱硫时,未脱硫原热烟气与脱硫系统净烟气混合排放,混合后的烟气温度取决于旁路烟气量和烟气相对温度。假设烟气完全混合,烟气总量中约1%的旁路烟气可以提高吸收塔出口烟气温度0.9℃,烟气再热的程度受到净烟气中液滴量的影响,净烟气中存在水分越多,混合烟气温度越低,因为大部分热量被用于蒸发这些液滴。旁路再热系统设计简单,安装和运行费用低廉,一个主要的缺陷是旁路中未处理的原烟气降低了脱硫系统总的脱硫效率,因此只适用于脱硫效率要求不高(<80%)的机组。此外,旁路再热导致烟气混合区域非常严重的腐蚀,需很好地进行防腐处理和定期维护。
不加热的脱硫系统烟气排放有两种:通过冷却塔排放及湿烟囱排放。利用冷却塔循环水余热加热烟气也有两种工艺系统:一种是脱硫系统设置在冷却塔外,脱硫后的烟气引入电厂冷却塔,如图136 2所示;另一种工艺是将脱硫系统设
置在电厂的冷却塔内。近年来,我国有大量的脱硫系统也开始采用湿烟囱。

图1362 冷却塔排放烟气
表1361列出了各种脱硫系统烟气排放方式的比较,在选用排放方式时,应从技术性能、经济性、环保要求等方面综合考虑。从国外运行经验来看,湿烟囱和冷却塔排烟是更合理的选择。
表1361 各种脱硫系统烟气排放方式的比较

续表

第七节 旁路改造设计要点
一、旁路挡板拆除及烟道系统优化
随着环保治理力度的加大,对环保设施要求越来越高,设有烟道旁路的FGD装置,要求限期拆除旁路挡板,确保脱硫与机组同步串联运行,以满足新的环保排放标准。
(1)根据脱硫旁路烟道具体布置、烟道结构和荷载核算,在脱硫烟道整体强度满足相关标准要求的情况下,可在拆除旁路挡板门后进行旁路烟道封堵,或者完全拆除脱硫旁路烟道,旁路烟道有明显断点。可使用6~8mm钢板或保温砖等材料封闭烟道,与脱硫后净烟气接触的封堵钢板或墙体需进行防腐处理。
图1371是典型的FGD系统旁路烟道拆除的做法,将旁路挡板左、右两侧用钢板完全封死,可见明显断点,这是环保局的强制要求。用钢条将旁路挡板焊死,并在一侧开检查孔来保证环保监测人员能够观察封堵情况的做法已不被认可了。

图1371 典型的FGD系统旁路烟道拆除的封堵
(2)拆除FGD系统进口原烟气挡板、净烟气挡板及外部执行机构等;如多台锅炉合用1个烟囱,考虑停运检修时可能的烟气反窜,可保留FGD系统净烟气挡板及相应的密封风系统,包括挡板密封风机、加热器及其管路配套设备。
(3)根据GGH实际运行堵塞情况,优先考虑将GGH换热元件更换为大通道形式,必要时在满足环保、烟囱防腐的要求下,也可拆除GGH。
(4)在经济比较合理的情况下,增压风机可以与引风机合并以提高烟气系统的可靠性。
(5)对增压风机动叶零位、全开位重新整定。
(6)电厂可根据锅炉实际运行情况决定是否在吸收塔前烟道的合适位置增加事故喷淋系统。如安装事故喷淋系统,则应保证供水可靠,可采用消防水供水;喷淋气动门应配可靠的控制电源,喷嘴应有可靠的防堵塞措施。
(7)核实烟道的承压能力,如需要,则在引风机和增压风机之间的烟道上设置防超压装置,防止增压风机故障后烟道超压,引起烟道事故。
二、GGH解决方案
对于老机组FGD系统一般设有GGH和增压风机,这与新建机组有很大不同。经过多年的运行,各电厂在防止GGH堵塞方面都积累了许多经验,如更换GGH换热元件形式,采用蒸汽吹灰和高压水相结合,或者采用可调频声波吹灰器,在各种检修期间进行换热元件化学清洗等方法,大大地减缓了GGH堵塞的速度,若能确保GGH的堵塞不会影响系统的正常运行,则可以保留GGH;否则,应考虑拆去GGH或采用其他形式的净烟气加热方法。
三、增压风机解决方案
新建机组增压风机与引风机合并,使得在技术和经济上都是十分可行的;但对老机组(特别是刚建不久的)来说,合并意味着原有FGD增压风机不能再使用,而需要更大更贵的新引风机,这在经济上是不太合算的。因为合并后运行电费节省不会太多,回收期很长,因此,有许多电厂拆除旁路烟道后仍然保留增压风机,一些电厂利用SCR、电袋除尘器的改造机会,用新引风机来代替增压风机,这对运行操作来说是大大简便了,可有效地提高无旁路FGD系统的可靠性,相比增压风机和引风机的串联自动运行的复杂性,这是十分有利的一面。
四、吸收塔入口烟气降温方案
拆除FGD旁路烟道后,需新增加一套事故喷淋系统,以防止吸收塔入口烟气温度过高损坏防腐层及设备。一般该系统采用消防水作为事故冷却水源,喷淋管路设置压力变送器,用于监控喷淋压力,以达到良好的喷淋效果。事故冷却水来水阀门、喷淋阀门等均采用气动执行机构,气动执行机构采用单电控、三断保护(失电、失气、失信号保护打开),为提高气动执行机构的可靠性,其电源取自仪表电源柜,该电源柜采用一路UPS电源,一路保安电源。同时,增加消防喷淋水压力。整个过程控制由DCS实现。
五、无旁路烟气系统设计要点
(1)取消FGD增压风机,即增压风机、引风机合二为一。
(2)取消烟气加热器(如 GGH、MGGH、蒸汽加热器
等),采用“湿烟囱”排放。
(3)取消烟气加热器,采用“烟塔合一”技术。
(4)简化进口烟道设计,大多数情况下无需设置事故喷水装置。如锅炉排烟温度高,可考虑设置热回收装置(如低压省煤器等)。
(5)如果设置烟气加热器,则其运行的阻力增加为第一考虑。优先选择大通道元件的回转式换热器。采用可靠的吹灰装置,吹灰介质应采用蒸汽而不宜用压缩空气,烟气换热器的受热面均应考虑防腐、防磨、防堵塞、防沾污等措施,与脱硫后的烟气接触的壳体也应考虑防腐,运行中应加强维护管理。
(6)如要设置FGD增压风机,动叶可调轴流式风机优先选用并布置在高温位置。增压风机的风量和压头按下列要求选择:
1)增压风机的基本风量按吸收塔的设计工况下的烟气量考虑。风量裕量不低于10%,另加不低于10℃的温度裕量。
2)增压风机的基本压头为FGD装置本身的阻力及FGD装置进出口的差压之和,压头裕量不低于20%;当净烟气设
有加热器,如GGH时,增压风机的压头应考虑GGH阻力增加了1倍时FGD系统的阻力。
某电厂2×300MW机组无旁路FGD装置的总体布置如图
1372所示。

图1372 某电厂2×300MW机组无旁路FGD装置的总体布置情况
1、2—6、5号吸收塔;3、4—6、5号循环泵房;5—石灰石粉仓;61、62—6、5号氧化风机房;7—事故浆液箱;8—工艺水箱;9—电控楼(操作室);10—工艺楼;11—CEMS(continuousemissions monitoringsystem,在线烟气监测)小间;12—脉冲悬浮泵
道中。
第八节 吸收塔系统设计要点
一、吸收塔系统组成
吸收塔系统是烟气脱硫的最核心部分,包括吸收塔、搅拌器或脉冲悬浮装置、循环浆泵、氧化风机、氧化空气分布装置或氧化喷枪、喷淋层、喷嘴、除雾器及冲洗装置、排浆泵等关键设备。湿法脱硫吸收塔一般采用逆流喷淋空塔,也可以采用托盘塔、双向洗涤塔、鼓泡塔、动力波塔等其他塔形,少数工艺采用填料塔,塔形及尺寸可结合场地因地制宜。吸收塔的数量应根据锅炉容量、吸收塔的容量和可靠性确定。300MW及以上机组宜1炉配1塔。200MW及以下机组宜2炉配1塔。
二、逆流喷淋空塔概述
逆流喷淋空塔是石灰或石灰石湿法FGD装置中应用最广的洗涤吸收装置。通常烟气从塔的下部进入吸收塔,然后向上流,在塔的较高位置布置了多层喷淋管网,循环泵将循环浆液输送至喷淋层,经喷淋管上的喷嘴喷射出雾状液滴,形成吸收烟气SO2的液体表面。每层喷淋管网布置了足够数量的喷嘴,相邻喷嘴喷出的水雾相互搭接叠盖,不留空隙,形成完全覆盖吸收塔的整个断面。虽然对各层喷淋管可以采用母管制供浆,但最通常的做法是一台循环泵对应一层喷淋层。这样可以根据机组负荷、燃煤含硫量以及不同工况下所要求的洗涤效率来调节喷淋泵的投运台数,从而达到节能效果。也有的按满负荷工况设置一台备用泵,作为事故备用,或当燃用高硫校核煤种时作备用喷淋层投运。
通常将塔体与反应罐设计成一个整体,反应罐既是塔体的基础,也是收集下落浆液的容器。由喷嘴喷出的粒径较小的液滴易被烟气向上带出吸收区,当这种饱含液滴的烟气进入除雾器后,液滴被截留下来。最为通常的做法是将除雾器水平布置在吸收塔顶部,当然,也可以垂直布置在吸收塔出口水平烟
逆流喷淋空塔的优点是损失小,吸收浆液雾化效果好,塔内结构简洁、不易结垢和堵塞,检修工作量少;不足之处是,脱硫效率受气流分布不均匀的影响较大,循环浆泵能耗较高,除雾较困难,对喷嘴制作精度、耐磨和耐蚀性要求较高。
三、系统设计及优化设计原则
(一)吸收塔
吸收塔一般设计要点:
(1)吸收塔宜采用钢结构,内部结构应根据烟气流动和防磨、防腐技术要求进行设计,吸收塔内壁采用衬胶或衬树脂鳞片或衬高镍合金板。在吸收塔底板和浆液可能冲刷的位置,应采取防冲刷措施。
(2)装在吸收塔内的除雾器应考虑检修维护措施,除雾器支撑梁的设计载荷不小于1000N/m2。
(3)吸收塔内与喷嘴相连的浆液管道应考虑检修维护措施,每根管道的顶部应有屋脊性支撑结构,以便检修时在喷淋管上部铺设临时平台,强度设计应考虑不小于500N/m2的检修荷载。
(4)吸收塔外应设置供检修维护的平台和扶梯,平台设计载荷不小于4000N/m2,平台宽度不小于1.2m,吸收塔内不设置固定式的检修平台。
(二)吸收塔的入口水平烟道设计
逆流喷淋空塔入口烟道通常设置在反应罐液位以上和塔体吸收区下部之间,处于高温烟气与下落浆液第一次接触的交界面上。当烟气进入吸收塔时被绝热饱和,沿入口烟道和干/湿交界区形成一个很大的温度梯度,在这一区城烟气温度通常从80~150℃迅速降至50℃左右。由于旋涡作用或入口烟气分布不均匀,下落的浆液会被带入入口烟道,带入的浆液接触到烟道的热壁面后水分蒸发,于是形成了固体沉积物。固体物的不断堆积将减小入口烟气流道面积,增大系统的流动阻力,严重
时被迫停机清除堆积物。入口烟道的这种环境决定了此处是湿法FGD系统腐蚀最严重的区域之一。
另外,烟气在吸收塔上游侧烟道中的流速一般高达每秒十余米,而湿式吸收塔内烟气流速通常是3~4m/s,因此吸收塔入口烟道还起着流速过渡作用,入口烟道的设计不仅会影响压损,而且还会影响进入塔内烟气分布的均匀性。所以对吸收塔入口烟道的设计有以下要求:
(1)烟道的接入尺寸及插入角度,需综合考虑,以减小压损,确保进入塔内的烟气分布均匀。
(2)烟道与塔壁交接处,应设置帽檐挡板或挡棚,防止飞溅的浆液倒流,在烟道内沉积固体物。
(3)干湿交界面设计要综合考虑,结构材料的选择应考虑高温、沉积物中高浓度腐蚀物质和沉积物引起的点蚀和缝隙腐蚀。

(a)传通入口烟道设计;(b)垂直搭壁入口烟道过渡段;
图1381(a)、(b)示出了适合传统吸收塔烟气流速(3~4.6m/s)的入口烟道过渡段的结构。采用遮挡帽檐结构将湿/干界面推向塔内,使之离开入口烟道壁面,这样可以防止入口烟道中沉积过多的固体物。在吸收塔常规流速情况下,由于入口烟气的动量接近喷淋区烟气的动量,烟气在吸收区的分布大致是均匀的,入口处的压损也增加不多。图1381(c)是吸收塔烟气高流速(4.6~6m/s)时入口烟道的一种设计方式。这种设计方式是将入口烟道过渡段布置在反应罐与塔体之间的斜锥面上,将干/湿界面进一步推进至塔内,远离了烟道的下底板面。由于塔体直径小于反应罐直径,在下落液滴形成的水帘与斜锥面之间形成了一个入口烟气环形带区域,烟气可以顺利地先进入这一环形区域再向上流动,这样不仅降低了入口压损,而且使烟气在塔内的分布较为均匀。按这种方式设计的入口烟道过渡段的压损仅为传统设计压损的2/3,水力模型试验以及流体动力计算机模拟分析均证明,这种入口烟道设计更适合高烟气流速,但这种设计的结构布置较困难。
入口烟道过渡段的结构材料通常选择耐高温、耐高浓度氯化物、氟化物、低pH值腐蚀和耐点蚀以及沉积物缝隙腐蚀的
高镍合金材料,如C275、59号合金等。当采取措施使吸收塔入口烟温降至100℃左右时,也可以采用价格较低的耐高温玻璃鳞片树脂防腐。
(三)喷淋装置
1.概述
喷淋装置主要用于将湿法脱硫循环浆液输送至吸收塔截面的各个点,通过喷嘴均匀喷洒,确保浆液覆盖全塔,并均匀分布。吸收塔内部的喷淋系统,是由分配母管/支管和喷嘴组成。母管和支管在吸收塔端面内平行对称布置,形成一个网状管路系统,该系统能使浆液在吸收塔内分布均匀。一般每个喷淋层设置一台吸收塔浆液循环泵,可以保证每个喷淋层的浆液流量相等。每个喷淋层上安装有足够数量的喷嘴,可以保证浆液进行充分的雾化,喷入烟气中。合理优化布置设计喷淋层网状管路,才能保证浆液在整个吸收塔断面上进行均匀的喷淋。
2.喷淋层布置
喷淋母管最重要的设计是母管层数(高度)以及母管之间的垂直间距。这些因素影响塔的总高度,而塔高是投资成本中的关键组成部分。
对于石灰石基工艺,喷淋空塔典型设计喷淋层是3~6层,交错布置,覆盖率达200%~300%。在石灰基工艺中,由于获得相同脱硫效率所需要的L/G较低,所以需要的喷淋层也较少。通常每层布置一个喷淋管网,每层应装有足够多的喷嘴,应尽量减少连接喷嘴的管道长度。第一层或称最下层喷管以及多孔托盘距入口烟道顶部必须有足够的高度,这一高度一般大约是2~3m。这样可以使得喷出的浆液能有效地接触进入塔内的烟气,并避免过多的浆液带进入口烟道;每层喷管以及最下层喷管与多孔托盘之间应相隔大约1~2m,最上层的喷淋管网与除雾器底部至少应有2m的距离。当烟气流量和SO2浓度高时可取上述范围值上限。
图1381 吸收塔入口烟道
喷淋层数和喷淋层的间距是影响吸收区高度的主要因素,吸收区的高度一般指吸收塔烟气入口中心线到最上层喷淋层之间的高度,以下因素决定吸收塔直径和吸收区高度:烟气量和SO2浓度;脱硫效率;吸收循环浆量;烟气入口流向(顺流或逆流)及入口型式;喷淋层数和喷淋覆盖的叠加面积;吸收剂反应活性系数。
(c)喇叭锥顶入口烟道过渡段
近年研究开发了一种对插喷淋层技术,即每层布置两组喷淋管网(如图1382所示),将母管置于塔外,喷淋支管相互平行、交替、成梳状地插入塔内。这种布置方式的特点是:①对插布置的每组喷淋管网的覆盖率为100%,每层的喷嘴数增加了1倍,增大了液滴密度,减少了塔内烟气“短路”的可能性,使气/液分布更均匀;②降低了塔高,如4层减至2层。塔高至少可以降低3m;③与分层布置相比,造成的压损增加很少;④可以降低喷淋泵的压头。现场全规模商业运行装置的试验数据证明,这种布置方式不影响脱硫效率。
3.喷嘴特性和布置
喷淋塔的脱硫效率主要取决于液滴大小和数量(这两个因素决定了吸收SO2液体的表面积)以及塔内烟气流速。液滴的大小和数量又取决于喷淋浆液的总流量和喷嘴的特性。喷嘴雾化特性主要包括喷嘴压力—流量—平均粒径的关系、喷嘴雾化均匀性、雾化角和雾化粒径分布特性等。研究应用于烟气吸收的喷嘴特性时,常用索特尔平均直径(SMD)来表示喷淋液滴的大小,SMD的含义是:对于一个实际的液滴群,假想一个粒度均匀的液滴群,此假想液滴群与实际液滴群的总体积和总表面积相同,那么,假想液满群的液滴直径就是实际液滴群
的SMD。在FGD应用中,液滴的SMD通常在1500~3000μm

范围内。液滴越细,单位体积循环浆液产生的洗涤效果就越好。但是,由于受喷嘴特性的限制以及吸收塔所具有的流体状况,对FGD吸收塔来说有一最佳液滴直径。在实际工况下并非液滴越小越好,细液滴易被烟气带离吸收区,在一个典型烟气流速为3~4m/s的逆流喷淋塔中,直径小于500μm的液滴会被烟气夹带进入除雾器,如果烟气夹带的液滴过多,将给除雾器下游侧的设备带来不利的影响。过分追求细小液滴需要较高的压力,能耗增大。通常在FGD应用中,直径小于500μm的液滴数量不应超过总量的5%,小于100μm的液滴则要尽量减少。
电厂应要求喷嘴供应商提供喷嘴雾化粒径分布数据,以便掌握所选喷嘴的特性。需要指出的是,喷嘴生产厂提供的喷嘴雾化粒径分布数据是在实验室条件下用室温水测得的,只能作为近似参考值,而且有多种表示平均粒径方法,例如除了上面提到的SMD外,还有算术平均直径、表面积平均直径、体积平均直径、体积中位直径、粒数中位直径、蒸发平均直径等。对同一个液滴群,用不同的直径表示方法表示的滴径差别很大。
在工作压力相同时,通常较小口径的喷嘴产生的液滴较细。但是喷嘴必须大到足以让垢片这类碎块通过喷嘴而不至于发生堵塞。喷嘴布置的间距应合理,要使喷嘴喷出的锥形水雾相互搭接,不留空隙。否则烟气可能不接触到液滴就从这些空隙中“溜走”。调整喷嘴布置密度和喷淋层数,可获得不同的喷雾重叠度。重叠度越高,脱硫效率也就越高,但阻力也会增加。一般喷雾重叠度为200%~300%。对喷嘴布置的另一要求是不冲刷塔壁,喷淋母管和支撑件。
对于石灰石烟气湿法FGD喷淋空塔,喷嘴的典型设计特
性是工作压力(表压)0.5~2kg/cm2 (50~200kPa),喷嘴出口流速约10m/s,每个喷嘴的流量36~80m3/h,雾化角90°。
采用这种规格的喷嘴,喷嘴的典型分布密度是吸收塔截面每平方米布置0.7~1个喷嘴。
通过一个全规模喷淋塔的试验证实了喷雾有效吸覆范围的
图1382 对插入式喷淋管布置方式
重要性以及喷嘴大小的影响。在该试验中,最初喷淋塔设计为每个喷淋层装有25个口径130mm的喷嘴,每个喷嘴流量是
31.5L/s(126.4m3/h),该塔的脱硫率大约仅80%。后来改为
每层布置口径为50mm的喷嘴60~84个,每个喷嘴的流量为
12.6L/s(45.4m3/h),喷嘴压力大致相同。此外,在喷淋塔
的入口区加装了多孔塔盘以改善烟气分布。经过这些改进后,该塔的脱硫效率提高到96%以上。分析认为,脱硫效率的提高主要归因于喷雾有效覆盖范围的提高以及采用较小口径的喷嘴显著地减小了液滴的平均直径。
在湿法FGD工艺中,一般采用压力式雾化喷嘴。喷嘴结构、工作压力和流量影响喷出液滴的大小。对同一喷嘴,工作压力和流量越大,即喷嘴喷出的平均速度越高,液滴的平均粒径越小。不同设计结构的喷嘴喷出的立体状的水雾分布形态是不相同的,不同的喷雾形态将影响不同大小液滴的数量。目前国内外在湿法FGD工艺中常用的浆液喷嘴有以下5种:
(1)空心锥切线型。采用这种设计的喷嘴,循环吸收浆液从切线方向进入喷嘴的涡旋腔内,然后从与入口方向成直角的喷孔喷出,产生的水雾形状为中空锥形,可以产生较宽的水雾外缘,在相同流量和压力下可以形成较小的液滴,允许自由通过的最大颗粒尺寸大约是喷孔尺寸的80%~100%,喷嘴无内部分离部件,其外形如图1383(a)所示。
(2)双空心锥切线型:这种喷嘴在空心锥切线型喷嘴的腔体上设计两个喷孔,一个喷孔向上喷,另一个喷孔向下喷,喷嘴允许通过的颗粒最大尺寸为喷孔直径的80%~100%,我国重庆电厂21号、22号喷淋塔就是采用这种类型的喷嘴,喷嘴
材质为SiC。
(3)实心锥切线型:这种喷嘴的设计思想与空心锥切线型喷嘴近似,所不同的是在涡旋腔封阻端的顶部使部分液体转入喷雾区域的中央,产生的水雾形态为全充满锥形,其外形如图1383(b)所示。这种喷嘴允许通过颗粒的尺寸为喷孔直径的80%~100%,产生的液滴平均粒径比相同尺寸的空心锥形喷嘴的大30%~50%,而且液滴粒度范围相当宽。

图1383 应用于FGD的几种常用喷嘴
(a)空心锥切线图;(b)实心锥切线型;(c)实心锥型;(d)螺旋型
(4)实心锥:这种喷嘴通过内部的叶片使浆液形成旋流,然后以入口的轴线为轴从喷孔喷出,产生的水雾形态为全充满锥形,根据不同的设计,这种喷嘴允许通过的最大颗粒直径从喷孔直径的25%~100%不等,在同等条件下,这种喷嘴雾化粒径相当于相同尺寸的空心锥的切线型喷嘴的60%~70%,
其外形如图1383(c)所示。
(5)螺旋型:又称为猪尾巴型。在这种喷嘴设计中,随着连续变小的螺旋线体,浆液水柱体被切除一部分,形成在一个空心锥水雾中还有1~2个同轴的锥形水雾,所以称为实心锥形水雾,或用剪切力使水柱沿螺旋线体旋转成空心锥形水雾形。其外形如图138 3(d)所示,这种喷嘴设计无分离部件,自由畅通直径等于喷孔直径的30%~100%,在同等条件下这种喷嘴的平均粒径相当于相同尺寸的空心锥切线型喷嘴
的50%~60%。
螺旋型喷嘴可以在很低的压力下提供很强的吸收效率,所以这种喷嘴推出后迅速得到脱硫系统的认可,典型操作压力在0.05~0.1MPa。但也有资料指出,这种喷嘴停用时易结垢。
在螺旋型明喷嘴中还有一种大通道螺旋型喷嘴,这种喷嘴是通过增大螺旋体之间的距离后设计出来的,允许通过的同体颗粒直径与喷孔直径相同,最大可达38mm。
4.喷淋系统的设计要求
喷淋系统的设计要求主要有以下几点:
(1)喷淋装置的设计应结合吸收塔结构及烟气量、循环浆液量等综合考虑。喷淋层数量一般不少于3层,可以采用双向喷嘴、也可以采用单向喷嘴,喷嘴的布置确保浆液覆盖率为200%~300%。在取消烟气旁路时,喷淋层至少应设置1层备用层。
(2)喷淋母管和支管管径、变径等设计要合理,以保证各个喷嘴处流量及压力均匀稳定。变径、接口、接头处要光滑过渡,以减小阻力。
(3)喷淋管应适应浆液的特性,包括浆液成分、含固量、温度、压力、黏度、pH值、氯离子浓度等。
(4)喷淋管的安装设计可以采用母管固定式,也可以采用独梁支撑或组合梁支撑。采用支撑梁时应考虑相应的喷淋管与
梁及卡箍接触部位,应设有耐腐减振橡胶和PP垫板,梁应做耐腐耐磨耐冲刷的处理。
(5)喷淋母管设计时底部要考虑排空措施,以防止浆液残留结垢结块,导致喷嘴堵塞。
(6)喷嘴的选型和设计对流量和压力应有一定的适应性。雾化粒径与烟气流速要匹配,粒径太大气液接触不充分,粒径太细雾滴容易被烟气带走。近塔喷嘴的扩散角和安装位置要合理,以减小壁流量和对塔壁的冲刷。顶层喷淋采用双向喷嘴时,与除雾器安装间距应考虑喷嘴上喷的喷射高度。
(7)喷淋层间距的设计不仅要考虑到满足性能要求,而且应充分考虑到便于工作人员进入吸收塔对浆液分配管网及喷嘴进行检修和维护。
(8)喷淋主管材质为碳钢内、外衬橡胶,支管材质为FRP,喷嘴材质为碳化硅。泵入口设有特殊设计的过滤网,以防止喷嘴的杂物堵塞,喷淋层相互叠加并错开一定角度。为了达到预期的脱硫效率,液滴直径必须保持在适当范围内,过大、过小均不适宜,切向空心锥形喷嘴可以实现液滴直径的优化。为减少烟气在吸收塔壁的逃逸,在每层喷淋层下设置一圈性能增强板,碳钢涂鳞。对无旁路吸收塔,一般采用大口径空心锥形喷嘴。
(四)烟气流速
逆流喷淋塔烟气流速设计直接影响系统阻力、塔高、烟气带水带浆等诸多方面,综合技术、经济、场地等诸多因素考
虑,烟气流速3~6m/s,多数设计取3.5~4.5m/s,流速太高
容易导致吸收塔带浆,流速太低则设计不经济。
(五)氧化浆池
浆池直径可以与吸收区塔径相同,也可变径。在场地许可的情况下,采用变径塔可有效降低塔高,减少搅拌器层数,利于节能。浆液停留时间为2~5min,非浓浆(含固量大于25%)洗涤工艺,浆液停留时间应不小于3.5min,一般设计
停留时间为4~5min。
(六)浆液悬浮系统
浆液悬浮系统采用搅拌器或脉冲悬浮装置。搅拌器根据浆池结构、浆液特性可以两层布置也可以一层布置。搅拌器及脉
冲悬浮装置的布置应确保浆液充分悬浮无死角,同时促进氧化空气的有效分散,确保氧化效果。所有储存循环浆液的箱罐应有防腐措施并装设搅拌装置。目前常用机械搅拌器,而脉冲悬浮系统也有应用案例,下面作以简单介绍。
脉冲悬浮系统采用几组带有朝向吸收塔底的带喷嘴的管子,通过脉冲悬浮泵(1台运行1台备用)将液体从吸收塔反应池上部抽出,经管路重新打回反应池内,当液体从嘴中喷出时就产生了脉冲,依靠该脉冲作用可以搅拌起吸收塔底固体物,进而防止发生沉淀。实际应用过程中,与机械搅拌器相比,脉冲悬浮系统最大的一个优点是提高了FGD装置的可用率和操作安全性,可以在吸收塔正常运行期间更换或维修脉冲悬浮泵,无需中断脱硫过程或排空吸收塔。重新投运时,先启动脉冲悬浮泵,将吸收塔浆池上部清液泵至吸收塔底部进行冲刷扰动,待吸收塔底部浆池悬浮起来后,将泵的高位入口切换为低位入口,达到均匀悬浮的目的。
(七)氧化系统
氧化系统由氧化风机、风管、氧化喷枪或塔内氧化空气分布管组成,氧化系统对脱硫效率和副产物品质有着直接影响。
(1)氧化风机一般采用罗茨风机,设置备用,流量超过10000m3/h,可采用高效离心风机。风机流量确保氧化倍率为1.8~2.5,扬程保证喷枪或氧化空气分布管出口压力高于临界压力。压力太低出力不够,压力太高不利于氧化空气分布。
(2)氧化喷枪或塔内氧化空气分布管可由耐腐耐磨材料制
成,如FRP、合金材料。
(3)氧化喷枪一般与搅拌器组合使用,两者的安装位置应确保氧化空气均匀分散。
(4)采用氧化空气分布管时,可与搅拌器组合使用,也可与脉冲悬浮装置组合使用,应考虑好防堵和冲洗措施。
(5)每座吸收塔应设置2台全容量或3台50%容量的氧化风机,其中1台备用;或每两座吸收塔设置3台全容量的氧化风机,2台运行,1台备用。
(八)除雾器
吸收塔应装设除雾器,在正常运行工况下除雾器出口烟气中的雾滴浓度应不大于75mg/m3(标准状态,干基)。除雾器应设置水冲洗装置。
目前,常用的除雾器为屋脊形除雾器,液滴分离是在两级屋脊形(人字形)除雾器中完成的,其优点是:
(1)每个单元除雾器之间设有走道,便于安装和维护。(2)优化冲洗过程,节约冲洗水量。
(3)改善气流分布,降低气体压降。
(4)可节省空间体积,降低吸收塔高度。(5)除雾效率高,且不易结垢堵塞。
(九)浆液循环泵
当采用喷淋吸收塔时,吸收塔浆液循环泵(简称吸收塔循环泵)宜按照单元制设置,每台吸收塔循环泵对应一层喷嘴,并宜设仓库备用泵叶轮一套;按照母管制设置(多台吸收塔循环泵出口浆液汇合后再分配至各层喷嘴)时,宜现场安装一台备用泵。吸收塔循环泵入口宜装设滤网等防止固体物吸入的措施。
吸收塔循环泵的数量应能很好地适应锅炉部分负荷运行工况,在吸收塔低负荷运行条件下有良好的经济性。
(十)事故浆液箱
脱硫装置应设置事故浆池或事故浆液箱,其数量应结合各吸收塔脱硫工艺的方式、距离及布置等因素综合考虑确定。当布置条件合适且采用相同的湿法工艺系统时,宜全厂合用一
套。事故浆池的容量应根据技术论证后确定。当设有石膏浆液抛弃系统时,事故浆池的容量也可按照不小于500m3设置。
四、无旁路FGD吸收塔系统的设计要点
FGD系统取消旁路后,一般不再设增压风机和烟气加热器,这样整个FGD系统中的设备故障点集中在吸收塔上,吸收塔安全可靠运行直接影响到主体发电机组的连续运行,因此,吸收塔设计时必须从各个方面提高其运行后的可靠性。无旁路FGD吸收塔系统的优化设计要点如下:
(1)尽可能采用1炉1塔,无需备用吸收塔、并联启动吸收塔及预洗涤塔。
(2)在吸收塔入口烟道上设置预洗涤系统是一个很好的选择。
(3)在合理的基础设计参数下(含硫量、烟气量等),吸收塔喷淋层无需备用,但当考虑到今后煤质有很大不确定性,可在吸收塔内预留一层喷淋空间。为防止浆液循环泵磨损后检修时间较长,循环泵因检修停运而使机组降低负荷,减少发电量,循环泵备用了1台,相应增加1层喷淋层,吸收塔体高度也相应增加。
(4)循环泵采用衬胶泵、全金属泵及陶瓷泵皆可。
(5)氧化风系统优先采用喷枪式AIS,并且吸收塔段的氧化空气管道宜采用合金管道。氧化风机在出力上裕量足够。
(6)除雾器优先选用屋脊式,冲洗水宜用干净的工艺水,不宜用真空皮带脱水机的过滤水;除雾器冲洗水阀门是动作十分频繁的阀门,质量要可靠。
(7)其他关键设备的质量一定要可靠且性能优良。如搅拌器、脉冲悬浮泵、石膏浆液排出泵、液位计、密度计等。
(8)pH值计安装采用浸入式为最佳。
五、对脱硫效率的几个影响因素
1.塔内烟气流速对脱硫率的影响
塔内烟气流速对喷淋塔SO2的脱除也有重要的影响。由式
NTU=ln(Yin/Yout)=KA/G[其中Yin为吸收塔入口烟气SO2
浓度;Yout为吸收塔出口烟气SO2浓度;NTU为传质单元数,无量纲,表示吸收塔脱硫性能;A为传质界面总面积(m2);G为烟气总流量(kg/s)]可得出,假定K、A与烟气流速无关,那么NTU与烟气流速成反比(烟气流量G=烟气密度×烟气流速×吸收塔截面面积),即提高烟气流速,脱硫效率下降。但是,在逆流喷淋塔内,增大烟气流速,由于提高了液滴和烟气之间的相对流速,加剧了湍流,减薄了液膜和气膜的厚度,将有助于K值的增大。同时,提高烟气流速则延长了液滴在塔内的停留时间,提高了吸收区的持量,使A值增大。在一个石灰
石FGD喷淋塔的试验显示,NTU与I/G0.3成正比。假定K、A
不受烟气流速的影响,烟气流量增加一倍(相当烟气流速提高一倍),NTU仅下降18.8%。也就是说,适当提高烟气流速,从对喷淋塔性能综合影响的结果看,仍然能提高脱硫效果。
需要指出的是,烟气流速对喷淋空塔入口烟气的分布影响较大,后者又会显著地影响脱硫效率。对要求高脱硫效率的现代吸收塔来说,特别在入口SO2浓度较高的情况下,塔内烟气分布的均匀性成为影响洗涤效果的重要因素之一。烟气流速对吸收塔入口烟气分布的影响与吸收塔类型、入口过滤烟道的结构和布置方式有关,需通过流体动力试验来确定这些因素的影响。
2.喷淋总流量对脱硫率的影响
改变循环喷淋泵的投运台数可以增加或降低喷淋塔内的喷淋总流量(L)。多数情况下,每层喷淋母管单独由一台浆泵供浆,采用这种布置方式,吸收塔内液滴总表面积大致与喷淋
总流量成正比。这是因为循环泵投运台数的改变不会影响喷嘴工作压力的稳定性,因而液滴粒度分布也不会随之变化。当然,塔内液滴总表面与喷淋总流量的这种正比例关系是假定液滴不会因为相互碰撞而聚积,或因液滴碰撞喷淋母管以及支撑件而消失。一个石灰石逆流喷淋塔的试验显示,NTU与砂L0.7成正比,而横向气流喷淋塔的NTU与L1.0成正比。
3.嘴淋层高度(吸收塔高度)对脱硫率的影响
在一个装有多个喷淋层的喷淋空塔内,每个喷淋层向吸收区贡献的液滴表面积随喷淋层高度增加而增加,这是因为上层喷管产生的液滴在塔内运行的轨迹较长。但是,另外一些因素则降低了喷淋层高度对SO2脱除的影响。例如,液滴离开喷嘴出口一段距离后,速度下降,于是气—液膜厚增大,另外液滴越往下降,其表面的碱度下降越大,而且,液滴还可能相互碰撞聚集成大液团。最后的结果是,顶部喷淋管雾化的液滴当落至塔体较低部位时其对SO2脱除的影响不如低位喷管产生的“新鲜”液滴的作用。实际情况也是如此,在一个有4个喷淋层的全规模喷淋空塔中的试验结果是,仅投运底部两个喷淋
管时,SO2脱除效率是73%(NTU=1.31),而只投运顶部两个喷淋层时,脱硫率也只有76%(NTU=1.43)。所以,过分
依靠提高喷淋层的高度来增加脱硫效率并非上策。喷淋区的典
型高度是7~18m。
4.入口SO2浓度对脱硫率的影响
在石灰和石灰石FGD系统中,在其他运行条件不变的情况下,SO2脱除效率通常随着入口烟气SO2浓度增加而下降,各种类型的吸收塔都存在这种关系。特别当SO2浓度超过设计点时,由于鼓入的氧化空气严重不足,脱硫效率将急剧下降。入口SO2浓度对SO2脱除效率影响的大小取决于液相碱度,pH值越高,浆液的缓冲作用越大,当入口SO2浓度上升时,脱硫率的下降要小些,特别对于石灰FGD以及采用有机酸添加剂的石灰石基工艺,这种影响将会小得多。在石灰石FGD工艺喷淋空塔中进行的全规模试验得出,NTU与l/Yi0n.25(Yin为吸收塔入口烟气SO2浓度,摩尔分率)成正比。
第九节 无旁路烟道原烟气预洗涤设计
一、烟气预洗涤概述
石灰石—石膏湿法烟气脱硫工艺取消FGD烟气旁路后,锅炉全烟气都必须全时段进入脱硫系统,因此,需要考虑进入吸收塔的原烟气中油污、高浓度粉尘及高温对吸收塔运行的影响。
根据运行经验,若进入FGD系统的原烟气中油污及粉尘含量长时间过多,这些油污和粉尘首先会被吸收塔中浆液吸收,吸收塔浆池油污和粉尘累积过多,则会影响石灰石的活性,粉尘会包裹石灰石颗粒,导致吸收塔浆池中的浆液“中毒”,从而导致吸收塔脱硫效率大幅度降低;同时,若油污和粉尘聚集在吸收塔除雾器上,会加重除雾器阻塞,并使得除雾器冲洗困难,进一步使得除雾器效率下降,严重的会导致除雾器坍塌,当然油污也会影响除雾器自身的寿命;最终油污和粉尘有可能会加重吸收塔内搅拌器、氧化喷枪等金属部件的腐蚀情况,使得这些设施寿命降低。另外,当这些被污染的浆液送至真空皮带脱水机脱水时,油污和粉尘会黏结在滤布上,不仅会影响真空皮带脱水机的脱水效果,影响石膏品质,还会降低滤布的寿命。高温烟气会影响防腐层和吸收塔内设备的寿命。
目前,我国新建火力发电厂无烟气旁路的FGD装置还没
有长期成熟的运行经验,为了解决锅炉启动阶段进入FGD吸收塔烟气中烟尘及油污过量的问题,一方面要对现有干式除尘器进行技术升级及提高运行水平,使其能最大限度地在锅炉投油启动时去除烟气中的油污及粉尘;另一方面需要通过加设有效的除尘除油装置,从而保护FGD系统,使其真正有效地做到能够处理任何时段的锅炉烟气。
已经运行的FGD系统主要采取以下办法来减少油污和粉尘的不利影响:
(1)未采取任何烟气预处理措施。随着锅炉点火燃烧技术的进步,对于使用高挥发分燃煤的锅炉可使用无油点火,此时锅炉启动后就可以投入除尘器,同时结合各种启动优化操作,从而减轻锅炉启动阶段的烟气含尘及含油的不利问题。有的系统仅在吸收塔入口段设置事故烟气降温喷淋装置。
(2)设置一个锅炉启动吸收塔。对于燃用低挥发分燃煤的锅炉仍需要使用大油枪点火,在投油阶段由于烟气中含有黏性油污,为降低油污对除尘器的损害,此时可能无法正常开启除尘器,因而烟气中含有大量的油污和粉尘。有的电厂通过设置一炉两塔方式来解决,即除了设置正常的脱硫吸收塔外,再根据锅炉启动投油时的最大烟气量并列设置一个小直径“启动吸收塔”。在锅炉投油启动阶段通过烟道挡板门开启运行“启动吸收塔”,该启动吸收塔此时等同于湿式除尘器,主要起到除尘、除油的作用;锅炉投油结束且除尘器正常运行后,通过切换烟道挡板门,再开启运行脱硫吸收塔,进入正常脱硫模式。
(3)设置串联吸收塔。即在主吸收塔前设置一个串联的预洗涤塔,锅炉启动初期的粉尘及油污被洗涤外排,同时,在正常运行情况下,预洗涤塔同样有一定的脱硫效果。
(4)在吸收塔前烟道上设置烟气预洗涤装置。与预洗涤塔不同的是在吸收塔前烟道上设置喷淋层来洗涤粉尘及油污,从而保护主吸收塔不被污染。
二、并联吸收塔
某电厂2×600MW机组烟气脱硫工艺采用石灰石—石膏湿法脱硫系统,不设旁路烟道,采用1炉2塔,一个为处理锅炉BMCR工况时40%烟气量的启动吸收塔,一个为处理锅炉BMCR工况时100%烟气量的主吸收塔。燃烧煤种含硫量按1.5%设计,脱硫效率按不小于95%设计,表1391为FGD系统主要设计参数。
表1391 FGD系统主要设计参数

续表

锅炉启功投油点火,在负荷小于40%BMCR工况电除尘器未投运时,关闭主吸收塔入口、出口挡板门,开启吸收塔入口、出口挡板门,原烟气进入启动吸收塔脱硫洗涤,然后排入烟囱。当锅炉负荷超过40%BMCR并且电除尘器正常投运后,开启吸收塔入口、出口挡板门,关闭启动吸收塔入口、出口挡板门,烟气进入吸收塔脱硫洗涤,脱硫后净烟气经烟囱排放至大气。启动吸收塔包括2层喷淋层和1套两级除雾器,单台吸收塔循环泵流量为5720m3/h,每层设置88个喷嘴,每个喷嘴流量为65m3/h,设3台搅拌器,1台运行1台备用的2台浆液排出泵;主吸收塔包括4层喷淋层和1套两级除雾器,吸收塔循环泵单台流量为7750m3/h,每层设置120个喷嘴,每个喷嘴流量为65m3/h,设4台搅拌器,1台运行1台备用的2台石膏排出泵,2台运行1台备用的3台氧化风机为两个吸收塔共用。两个吸收塔的主要设计参数见表1392。图13 91为现场并联吸收塔。
表1392
并联吸收塔的主要设计参数

续表


图1391 并联吸收塔(启动吸收塔和主吸收塔)现场
采用并联吸收塔实际上相当于设置了一个具有除尘、除油功能的FGD系统旁路装置,不仅造价高昂且占地面积较大,运行切换要求高,不宜提倡。在FGD系统某次调试过程中,机组升负荷较快,而启动吸收塔还来不及切换到主吸收塔运行,造成进入启动吸收塔的烟气量大大超过40%BMCR工况,导致了启动吸收塔内的二级除雾器完全被吹翻,损失很大。对于目前的微油点火、等离子点火,电除尘器在锅炉启动后就投入运行,进入吸收塔的粉尘油污并不多,设置一个并联吸收塔完全没有必要。
三、串联吸收塔
某电厂4×600MW机组配套石灰石—石膏湿法脱硫工艺,原设计每炉1个吸收塔,收到基硫Sar(wt)=1.6%,校核为2.0%,脱硫效率不小于95%。投运后,由于实际煤种含硫量远远大于设计值,烟气量也有所增加,因此,对原FGD系统进行改造,改造要求煤收到基硫Sar(wt)=4.0%,校核为

图1392 改造后600MW串联吸收塔示意画面
表1393600MW预洗涤塔主要设计情况

4.8%,净烟气SO2浓度不大于400mg/m3。改造方案采用了
“预洗涂塔+原吸收塔”串联吸收塔,拆除原GGH,原吸收塔保留不变,在原吸收塔前新增一套SO2吸收系统,包括预洗涤塔、预洗涤塔浆液循环泵、石膏浆液排出泵、氧化空气及辅助的放空、排空设施等,其主要设计情况见表1393。图1392是改造后FGD串联吸收塔流程示意图。
续表

四、烟道预洗涤装置
无论采用启动吸收塔还是预洗涤塔,都需要设置一个独立的吸收塔,不仅投资大,而且占地也大,运行操作不方便。为此,设计了吸收塔前加装烟道预洗涤装置,并在1000MW机组无旁路FGD系统中成功应用。根据吸收塔前原烟气烟道接口标高的不同,该烟道预洗涤装置位置选取分为下述两种情况。
1.垂直烟道预洗涤装置
垂直烟道预洗涤装置指两台引风机出口烟道汇合后低位水平接出,引接至吸收塔附近后再垂直上升,引接到吸收塔入口。此时,可以在吸收塔入口前的原烟气烟道垂直上升段设置烟气预洗涤装置。
该垂直上升段烟道增加用材厚度(烟道壁板厚度为8mm),从而提高结构强度,锅炉投油启动阶段产生最大的烟气量在该段的流速应小于5m/s,另外,该段烟道横截面应适当加大,以克服增加内部喷淋件产生的阻力。在垂直上升直段烟道上部横截面均匀布置预洗涤喷淋层,喷淋管外接预洗涤液供给管路,烟道内底部弯头部分增加设置多个导流板,起到烟
气导流及洗涤格栅的功能,另外,该弯头底部设置洗涤液收集及排放箱体,该箱体与烟道设计为一体化结构,并保证全密封,该箱体同时起到防止任何液体倒灌至引风机的作用。预洗涤装置还需要在附近的地坪下设置预洗涤液收集地坑,通过地坑泵将预洗涤液打入到洗涤液缓冲箱,该缓冲箱设有预洗涤液

图1393 垂直烟道预洗涤装置流程
1—预洗涤烟道段;2—预洗涤喷淋层;3—烟道集水槽;4—导流板;5—底流管;6—预洗涤液集水地坑;7—搅拌器;
8—地坑泵;9—预洗涤液缓冲箱;10—搅拌器;11—预洗涤液循环泵;12—预洗涤液外排泵
图1394是某1000MW机组无旁路FGD烟道预洗涤
系统的具体设计,该FGD增压风机与引风机合并,不设置
GGH,吸收塔直径为19m,总高为43.85m,设4层喷淋层,
2级SO2浓度为3900mg/m3,脱硫效率不低于95%。烟道预
洗涤用于锅炉投油启动阶段预洗涤原烟气中超量的烟尘及油污。以保证FGD系统安全经济运行,事故情况下还作为降低吸收塔入口烟气温度、粉尘浓度和油污的一种应急手段。原烟气预洗涤管和喷嘴的材质为1.4529,预洗涤地坑尺寸:
4000mm×4000mm×4000mm,预洗涤液缓冲箱尺寸为φ9m×
10m,有效容积为636m3,采用玻璃鳞片防腐,配1台离心式
预洗涤液循环泵,扬程为550kPa,体积流量为400m3/h,1台
离心式预洗涤液外排泵,扬程为250kPa,体积流量为30m3/h。图1395是预洗涤系统设备现场照片。
2.水平烟道预洗涤装置
该种情况指两台引风机出口烟道汇合后垂直地坪上升接出,从高位水平引接至吸收塔入口。此时,可以在吸收塔入口前的原烟气水平烟道直段处设置烟气预处理装置。
该水平段烟道同样增加用材厚度(烟道壁板厚度为8mm),从而提高结构强度,锅炉投油启动阶段产生最大的烟气量在该段的流速应小于5m/s,另外,该段烟道横截面应适当加大,以克服增加内部喷淋件产生的阻力;在该水平段烟道上横向均匀设置几排预洗涤液喷淋管,喷淋管外接顶部洗涤液供给管路,在喷淋管范围内,根据需要设置两排斜管格栅,起到烟气洗涤格栅的功能,在吸收塔入口前段设置洗涤液收集及排放箱体,该箱体与烟道设计为一体化结构,并保证全密封,该箱体同时起到防止任何液体倒灌至引风机及吸收塔的作用。该预洗涤装置无需在设置任何地坑,可以通过管道将烟道自身的水封箱排液口与预洗涤液缓冲箱连接,此时,预洗涤液缓冲
循环泵及预洗涤液外排泵,预洗涤液循环泵起到向烟道预洗涤喷淋层供洗涤液的作用,预洗涤液外排泵起到外排预洗涤液的作用,可以根据具体情况考虑,将两类泵功能合并,单台泵的出力需结合最佳经济运行方式选取。其完整工艺系统流程如图
1393所示。
箱需要保持工作液位用作“水封”。其完整工艺系统流程如图
1396所示。
当锅炉启动前,先将预洗涤液缓冲箱及涤液收集地坑(如果有)注水至工作液位,将地坑泵切到自动运行,并将预洗涤液外排泵切到自动运行(根据预洗涤液密度变化控制),然后,开启预洗涤液循环泵向装置的喷淋层供液。运行稳定后,允许锅炉投油启动,在对烟气预洗涤过程中,预洗涤液稳定向预洗涤喷淋层供液。烟气被有效除尘、除油,洗涤液通过地坑收集后再通过地坑泵预洗涤液缓冲箱,洗涤液外排泵在监视到洗涤液密度达到一定值时开启,同时,工艺水阀门打开,以保持预洗涤缓冲箱的工作液位。
锅炉投油结束后,关闭预洗涤喷淋装置(关闭预洗涤液循环泵及管道阀门,并冲洗管道及设备),继续开启预洗涤液外排功能,直到预洗涤液缓冲箱中洗涤液密度到达设置低值。外排的预洗涤液可根据电厂实际需要,外排至脱硫废水处理系统、煤场沉灰池、脱硫石膏皮带冲洗口等位置。
FGD系统正常运行后,仍需将预洗涤液缓冲箱保持在工作液位,预洗涤浆液缓冲泵处于热备用状态,用于高温烟气的降温喷淋。
烟道预洗涤装置具有如下突出特点:
(1)流程简单,启停方便,简单改动就可以达到所需的对原烟气除尘和除油的效果。
(2)充分利用了现有常规设施,费用低,能耗低,对FGD系统无任何不良影响。
(3)可以有效地降低烟气中所含的粉尘和油污,从而使得FGD系统利用率更高,对整个系统的稳定运行、全时段脱硫和石膏品质有积极作用。

图1394 某100MW机组无旁路FGD烟道预洗涤喷淋系统

图1395(一)某1000MW机组FGD垂直烟道预洗涤系统及设备

图1395(二)某1000MW机组FGD垂直烟道预洗涤系统及设备

图1396 水平烟道预洗涤装置流程
1—预洗涤烟道段;2—预洗涤喷淋层;3—烟道集水槽;4—棒格栅;5—底流管;6—预洗涤液缓冲箱;7—搅拌器;8—预洗涤液循环泵;9—预洗涤液外排泵
第十节 除雾器设计要点
经吸收塔处理后的烟气夹带了大量的浆体液滴,特别是随着当今吸收塔烟气流速的不断提高,烟气携带液滴量将加剧。如果不除去这些液滴,这些浆体液滴会沉积在吸收塔下游侧设备表面,形成石膏垢,加速设备的腐蚀,对烟气再加器还会影响热交换。如果采用湿排工艺,则会造成烟囱“降雨”(排放液体、固体或浆体)、污染电厂周围环境。因此,在吸收塔出口必须安装除雾器(ME)。除雾器的性能不仅直接影响吸收塔烟气
流速的确定,而且影响湿法FGD系统的可靠性,因除雾器故障造成FGD系统停运的事例并不少见。所以,科学合理地设计除雾器,了解除雾器的一些重要参数,正确操作和管理除雾器,对保证湿法FGD整个系统的可靠性非常重要。
一、除雾器的基本工作原理
常用的气水分离器有折流板式(又称V形板式)除雾器、旋流板除雾器、丝网层雾沫分离器、旋风分离器等。湿法FGD洗涤后的烟气中的含液量相对较高,液滴大小的范围很宽,直径从几个微米到2000μm,而且这种水雾是一种具有化学反应活性的浆液,这种液滴可以引起ME结垢或堵塞,因此
对除雾器有特殊的要求。全世界湿法FGD系统20多年的运行经验表明,折流板除雾器具有结构简单、对中等尺寸和大尺寸雾滴的摘获效率高,压降比较低、易于冲洗,具有敞开式结构便于维修和费用较低等特点。最适合湿法FGD系统除去烟气中的水雾。

图13101 折流板ME工作原理

图13102 折流板ME几种结构形式的板片
不同结构的 ME板片各有其特点,图13102(a)型板片结构简单,加工方便,可用聚丙烯(PP)、不锈钢或FRP制作,易冲洗。主要应用于垂直向上流的高流速吸收塔,通常
2级布置,烟气流速可以超过6.2m/s。图13102(e)、
(f)型板片临界流速较高,易冲洗,特别是图13102(f)型比折线型的除雾效率高,但有堵塞的倾向,多用作要求高除
雾效率的ME的第二级。图13102(e)、(f)的板片只
能用PP材料制作,其性价比较好,目前在大型FGD装置中
采用较多。13102(c)型板片ME是一种专为FGD吸收
塔设计的气水分离装置,具有除雾效率高,易清洗、低压损和坚固耐用的特点。这种板片的ME可用于垂直烟气流也可用于水平烟气流,可单级也可多级使用,可采用不锈钢、PP、No-
ryl或FRP制作。
图13102(d)型是一种4通道板片,通常仅用一级ME,要求较高除雾效率时也可以考虑设置两级。在最大设计烟量时,烟气流速在4.0~4.5m/s范围内。这种板片制作的
折流板除雾器利用水膜分离的原理实现气水分离。当带有液滴的烟气进入人字形板片构成的狭窄、曲折的通道时,由于流线偏折产生离心力,将液滴分离出来,液滴撞击板片,部分黏附在板片壁面上形成水膜,缓慢下流,汇集成较大的液滴落下,从而实现气水分离,其工作原理如图13
10 1所示。
由于折流板除雾器是利用烟气中液滴的惯性力撞击板片来分离气水,因而除雾器捕获液滴的效率随烟气流速增加而增加,流速高,作用于液滴的惯性大,有利于气水分离。但当流速超过某一限值时,烟气会剥离板片上的液膜,造成二次带水,反而降低除雾器效率。另外,流速的增加使除雾器的压损增大,增大了脱硫风机的能耗。
二、折流板除雾器板片的形状和特点
折流板除雾器的板片按几何形状可分为折线形[见图1
3102(a)、(b)、(c)、(d)]和流线形[见图13102
(e)、(f)]。根据烟气在板片间流过时折拐的次数,可分为2~4通道的除雾器板片。烟气流向改变90°为一个折拐,亦称为
一个通道。因此图13102(a)、(e)、(f)为2通道板片,图13102(b)、(c)为3通道板片,图13102(d)
为4通道板片。通道数和板片间距是 ME板片的两个重要参数。有些板片上设计有特殊的结构,如图13102(f)中的倒钩、凸出的肋条(见图13101)或沟槽和狭缝,以便捕获液滴和排走板片上的液体。
ME除雾效事高,由于通道多,除 ME的正面和背面需定时冲洗外,其顶部也装有定时冲洗管道,如图13103(a)所示。
三、除雾器布置方向及优缺点比较
除雾器布置方向是根据烟气流过除雾器截面的方向来定义。烟气的流向可以是水平流向也可以是垂直向上流,因此除雾器有两种布置方向:垂直流除雾器和水平流除雾器。对于垂直流除雾器,除雾器的组件水平放置。烟气垂直向上流过除雾器组件,如图13104所示。水平流除雾器的组件是垂直布置,烟气流沿水平方向通过除雾器,如顺流填料塔(见图
13105)和喷射鼓泡反应器(见图13106)的除雾
器。虽然可以不依据吸收塔的流程(顺流或逆流)来确定除雾器的布置方向,例如也可以在逆流塔出口水平烟道中布置水平流除雾器;或者除雾器的第一级在塔内水平放置,第二级垂直安装在吸收塔出口烟道。但是,一般吸收塔的类型决定了除雾器的布置方向。

图13103 水平流除雾器冲洗流程图和冲洗时间表
(a)冲洗流程图;(b)冲洗时间表


图13105 顺流填料塔
在比较除雾器上述两种布置方面的优缺点时,涉及到除雾效率以及与其有关的几个概念,现作简要介绍。通过ME后的烟气夹带液体量指ME下游侧烟气流中的液滴量,这些液滴或者是 ME未除去的,或者是被烟气重新带出的所谓二次带水。
图13104 喷淋空塔
夹带液体量用L/(s·m2)或mg/m3 (标准状态)来表示。通


图13106 喷射鼓泡反应器(JBR)工作原理
图13107 ME布置方向对除雾器板片上液体的影响
常在研究除雾器性能时所讲的除雾效率是指除雾器捕获液体量与进入除雾器烟气夹带液体量的比值。除雾效率不仅与除雾器入口烟气夹带液体量有关,而且与液滴粒径分布有关,但对于液滴粒径的分布是个很难限定的入口烟气条件。另外,在实际FGD装置中,烟气夹带的是浆体液滴,而不是纯液体。因此,在实际中很难应用除雾效率这一技术指标。在FGD技术规范或性能保证值中往往以除雾器出口烟气颗粒物含量[mg/(s· m2)或mg/m3 (标准状态)]来规定除雾器的除雾效果,上述颗粒物应该包括液体和固体物。对除雾器入口烟气条件不作限定,但应明确是否在除雾器冲洗期间也应达到除雾效果,一般规定在不冲洗时应达到的除雾效果保证值。
除雾器的这两种布置方向都有优缺点,水平流除雾器可以在较高的烟气流速下达到很好的除雾效果,水平流除雾器在试验装置中的试验显示,当烟气流速高达8.5m/s和入口烟气含液量明显高于许多FGD系统预计的含液量时,通过除雾器的烟气夹带液体量非常少或几乎不含液体。早期的FGD装置中大多数垂直流除雾器的设计烟气流速不超过3.6m/s,但现在先进的垂直流除雾器已证实在烟气流速高达约5.2m/s时仍具有优良的除雾效果,虽然垂直流除雾器最大允许烟气流速低于水平流除雾器,但这一最大允许烟气流速不低于大多数逆流吸收塔的最大设计流速。
从图13107可看到,在水平流除雾器中,从烟气中去除的液滴沿板片凹槽、垂直于烟气流向向下流,而垂直流ME捕获的液滴是沿除雾器板片较宽的一边逆着气流方向向下流。然而,水平流除雾器降低了气流剥离板片上液流形成二次带水的可能性;而垂直流除雾器的情况正好相反,特别当离开板片的液滴较小时,即使烟气流速比较低,也易于被再次雾化进入烟气中。因此,在较高烟气流速下,水平流除雾器表现出来的性能比垂直流除雾器更好。
图13108示出了垂直流除雾器(ME)几种布置方式,将水平布置的垂直流除雾器改成人字形或V形以及组合型布置(菱形或X形),水平流 ME能较好地排放捕获液体的优点就可以在垂直流除雾器上体现出来。人字形布置的ME能处理高达7m/s的烟气流速,这种布置方式改进了液体的排放路径,提高了水雾除去的表面积,但压损和占用的空间比水平放置的大,增加了吸收塔的高度,设备费较贵,冲洗系统较复杂。
由于水平流除雾器能处理较高流速的烟气,因此所需材料和占据的空间比垂直流除雾器少。但是,垂直流除雾器可以布置在吸收塔内,而水平流除雾器则需布置在吸收塔出口水平烟道中,这也使得水平流除雾器的组件可以采用除雾器烟进顶部

图13108 垂直流除雾器的几种布置方式
的固定吊具吊装,组件可以做得比较大,拆装、更换方便。而垂直流除雾器组件的拆装需靠人工搬运,劳动强度大,组件的
质量不宜太重,通常34~45kg。
水平流除雾器的缺点是,由于烟气流速较高,烟气通过除雾器的压损较大,一个二级水平流除雾器在典型设计烟气流速
6m/s的情况下,压损大约250Pa,而设计烟气流速3.4m/s
的二级垂直流除雾器的压损大约75Pa。目前,由于大多数新建电厂FGD系统采用湿烟囱工艺,在一个现有的电厂中加装FGD系统时,有时无需加装脱硫增压风机,在这种情况下,除雾器压降在FGD系统总压降中所占比率有可能影响到是否需要增装脱硫风机。对于新建电厂的FGD系统,除雾器采用何种布置方向应综合考虑这两种布置方向的优缺点,GGH的类型和可供布置的位置。
四、烟气流速对除雾器性能的影响
除雾器的临界流速:通过除雾器的烟气流速有一定限制,速度太低,气流弯曲流动时产生的离心力不足以使细小液滴从烟气中分离出来,但气速过高会撕裂板片上形成的液膜。造成烟气中夹带的液量骤然增大,并且其中大粒径的液滴明显增多,即所谓二次带水,从而破坏除雾器的正常工作。通常将通过除雾器断面的最高且不产生二次带水的烟气流速定义为除雾器的临界流速(或称为二次带水流速,撕裂流速)。除雾器的临界流速是除雾器的一个重要性能参数,是吸收塔烟气设计流速的重要依据之一。
临界流速与除雾器结构、布置方式、系统带水负荷以及气流方向等因素有关。图13109是3种二级垂直流FRP除雾器烟气流速与夹带物含量关系试验的结果。从该图可着出,除雾器C的临界流速最高。当烟气流速低于除雾器的临界流速时,除雾器A、B透过除雾器夹带物含量较高。当气速超过其临界流速时。夹带物含量按数量级递增。由于透过除雾器的夹带物含量对烟气流速十分敏感。因此,无论是水平流还是垂
直流除雾器。使烟气在除雾器的整个端面上分布均匀是极其重要的。烟气分布不均匀或除雾器部分堵塞和结垢是造成除雾器局部烟气流速超过临界流速的主要原因,为了防止高烟气流速区的出现,建议除雾器烟气流速分布偏差不超过平均流速的±15%。对除雾器而言,吸收塔最高允许流速的确定除了要考虑除雾器的临界流速外,还应考虑除雾器烟气流速分布不均匀和除雾器支撑结构和冲洗水管对气流流通面积的减少。例如,一个临界流速为5.8m/s的除雾器,假定除雾器端面中心烟气流速比平均流速高20%,除雾器支撑结构和冲洗水管使气流流通断面面积减少了15%,那么,除雾器端面处烟气平均流
速不应超过4.1m/s。

图13109 三种ME烟气流速与夹带物含量的关系
五、除雾器板片特性对除雾器性能的影响
洗涤后烟气中的液体绝大多数是直径30~40μm的液滴,性能良好的V形折流板 ME基本上可以除去上述粒径范围的液滴。V形板片便于排水,而且板片间距相对较宽,易于在线冲洗板片。V形板片除雾器还具有相对较低的烟气压降,这对于处理大量烟气是十分重要的。其他除雾器,例如丝网层雾沫分离器不易冲洗,因此可能由于结垢或堵塞而堆积固体物,棒束除雾器的除雾效率比V形除雾器低得多,而离心式分离器在达到相同除雾效率的情况下,有较高的烟气压降。
按照板片的形状,烟流方向改变的通道数、排水方法,板片上倒钩状物或其他表面结构,板片的间断以及烟气出口直段的长度。有各种可供选用的板片(见图13102)。除雾器板片特性对除雾器性能主要有下述影响。
1.板片通道数
图13102给出了2~4通道的几种除雾器板片。通道数是除雾器一个重要的设计技术指标。通道越多,去除液滴的效率越高,但增加了充分冲洗掉板片上沉积物的难度。另外,如果V形板片有3个或更多的通道,对除雾器板片的检查较困难,因此在除雾器设计时应综合考虑板片的通道数,一般建议用于湿法FGD系统的V形折流板至少有2个通道,但不超过4个通道。
2.板片间距
板片间距的确定需要在透过除雾器的夹带物量和充分冲洗除雾器之间进行权衡。间距小,除雾器有较高的除雾效率,但压损大,增加能耗和难以将板片冲洗干净,板片易结垢和堵塞,严重时可能造成系统停运。间距大,冲洗效果好,但临界流速下降、除雾效率低,烟气夹带浆液量增多,易在除雾器下游侧的加热器换热元件表面形成固体沉积物。用于FGD系统的多级除雾器,板片间距范围通常大约是20~75mm。由于第一级ME接触的烟气含液体量较多,板片上有较多的浆液要冲除,因此第一级板距稍宽些,约30~75mm。第二级除雾器为
了尽可能多地去除雾滴,提高除雾效率,板距通常较窄,约
20~30mm。
3.板面特殊结构设计
在除雾器板面上可以设计倒钩、凸起的肋条、沟槽或窄缝这类特殊结构,这有利于捕获液滴,提高除雾效果或便于排走聚积在板片上的浆液。水平流除雾器板片上的倒钩具有较好的效果,但不推荐垂直流除雾器板片上采用这类结构。电厂FGD系统的运行经验表明,这些结构易于积聚固体物和引起结垢,原因可能是被捕获的浆液不能从这些地方很顺畅地排走,建议垂直流 ME采用表面平整、光滑的板片。某电厂FGD除雾器总体布置图如图131010所示。

图131010 某电厂FGD除雾器总体布置图
4.板片烟气出口侧直段长度的设计
板片烟气出口侧直段长度也是V形板片设计的一个重要环节。当烟气通过除雾器最后一个通道流出来时,烟气的流向与除雾器所处的烟道或塔体形成一定的角度(见图1310 11),如果第一级 ME的出口部分没有一段有足够长度的直流通道,烟气就会以一定角度离开第一级除雾器,造成下一级除雾器烟气分布更加不均匀,这会导致下一级除雾器局部烟气流速过高,从而降低除雾器性能,一些FGD装置已遇到过这种情况。除雾器板片烟气出口直段必需的长度取决于板片间距和板片的形状。

图131011 V形板片烟气出口直段对烟气流向的影响
六、除雾器的级数和级间距
V形板除雾器通道数和板间距的确定,要综合考虑除雾器的除雾效率和便于冲洗干净板片。为了满足要求,目前几乎所有的FGD系统都采用两级除雾器。第一级板片间较宽,可除去烟气中大部分雾沫(超过95%),同时易于冲洗干净;第二级板距较窄,除雾效率较高,除去剩余的液滴,由于进入第二级的液体量明显低于第一级,所以冲洗干净第二级的板片并不困难。目前普遍采用的二级除雾器可将清洁烟气中的液滴含量降到50mg/m3,除雾器制造商提供的数据甚至可以降到23mg/m3。因此,FGD系统技术规范可以要求卖方提供的 ME除雾效果达到<75mg/m3。设置第三级 ME,除雾效率进一步提高的余地较小,与投资成本和烟气压损的增加相比是不合算的,因此在FGD系统中很少采用三级除雾器。
除雾器两级之间的间距以及各级除雾器与吸收塔中其他部件的距离也是除雾器设计的重要参数。特别在垂直烟气流的吸收塔内。当除雾器布置在吸收塔喷淋区或液柱区的上方时,第一级除雾器与吸收塔最上层喷淋母管或液柱最高点应有足够的距离,这样可以提供一个空间,让一些被烟气夹带的、较大的液滴依靠重力向下坠落,脱离进入除雾器的烟气流,降低除雾器除去雾沫的负荷。另外,有利于使烟气分布均匀,也便于布置冲洗管道。对于高烟气流速(4.6m/s)的逆流塔,适当加大这一间距相当延长了烟气吸收区的高度。对于垂直流除雾
器,建议这一最小距离为1.2~1.5m。
我国从德国引进的逆流喷淋塔,除雾器采用菱形布置,吸收塔喷嘴为双空心锥切线型,最上层喷淋母管中心线与第一级除雾器端面的平均距离为4.1m(最小距离3.5m)。从日本引进的逆流液柱塔,烟气流速3.55~4.56m/s,液柱最高点与平放垂直流除雾器第一级相距3~4.6m。
由于水平流除雾器通常布置在与吸收塔分开的水平烟道中,与喷淋层之间往往有足够的间距。
通过第一级除雾器后的烟气中有二次夹带形成的较大的液滴,为使较大的液滴从烟气中分离出来,便于布置第一级除雾器背面和第二级除雾器迎风面的冲洗水管和水管支架,以及为了方便检修,人工清洗除雾器和更换除雾器板片组合件,两级之间也必须有足够的空高,垂直流和水平流除雾器两级之间的最小间距是1.5~1.8m。目前除雾器的发展趋势是减少板片的通道数,缩小各级ME的厚度和板距,增加第一级除雾器与最上层喷淋层以及除雾器两级间的距离,使除雾器在保持高除雾效率和易冲洗的前提下更适合高流速烟气。在烟气流速较高(4.5m/s)的情况下,水平流除雾器和平放的垂直流除雾器两级间距离大多取上述范围的上限。
在采用垂直流除雾器的逆流吸收塔中,第二级除雾器背面至吸收塔或烟道截面开始变窄处,第二级除雾器后烟气流速开始增大处也应有足够的距离。烟气二次带水形成的液滴一般比依靠烟气流速才能托起的液滴要大得多,留有一定的距离可以使这些较大的液滴从烟气中分离出来落回除雾器上,这样可以减少夹带到除雾器下游烟道和设备中的液滴量。推荐的这一最小间距大约是1m,图131012示出了一个二级除雾器各级之间以及它与塔内其他部件之间的建议间距。
七、除雾器冲洗系统
湿法FGD系统中的除雾器通常由除雾器本体和冲洗系统组成。冲洗系统则由冲洗喷嘴、冲洗管道、冲洗水泵、冲洗水自动开关阀、压力仪表、冲洗水流量计以及程控器等组成。除雾器冲洗系统的作用是定期冲洗掉除雾器板片上捕集的浆体、固体沉积物。保持板片清洁、湿润,防止叶片结垢和堵塞流

图131012 ME各级之间以及它与塔内
其他部件之间的推荐距离
道。另外,除雾器冲洗水还是吸收塔的主要补加水,是系统水平衡中的重要部分。如果冲洗系统设计不合理将会造成ME板片间局部或大面积结垢或堵塞,系统水平衡破坏。全规模试验证实,设计不合理的除雾器冲洗系统仅运行一天,除雾器板片上就出现了结垢。试验也显示,即使除雾器板片表面有薄层垢就会明显降低除雾器性能。实际运行中出现过由于冲洗系统故障,停止冲洗仅2~3天,除雾器一、二级正面板间几乎全部被石膏所堵塞,由此可看出,洗涤后的烟气夹带浆液的严重性,定时冲洗的重要性以及堵塞发展的迅速。在除雾器中,结垢或堵塞一旦发生,那么结垢和堵塞会进一步发展。结垢、堵塞的发生,使得与结垢和堵塞部位相邻区域的烟气流速增大。从而助长了堵塞、结垢的蔓延,加速恶化除雾器性能。因此,正确设计和正常工作的冲洗系统对除雾器乃至整个FGD系统的稳定运行是非常重要的。
1.除雾器结垢和堵塞原因
分析造成除雾器结垢和堵塞的原因,有助于理解冲洗系统的设计思想。造成除雾器结垢和堵塞的原因有:
(1)系统的化学过程:吸收塔循环浆液中总含有过剩的吸收剂(CaCO3),当烟气夹带的这种浆体液滴被捕集在除雾器板片上而又未被及时清除时,会继续吸收烟气中未除尽的SO2,生成亚硫酸钙/硫酸钙,在除雾器板片上析出沉淀而形成垢。
(2)冲洗系统设计不合理:当冲洗除雾器板面的效果不理想时会出现干区,导致产生垢和堆积物。对冲洗系统的研究表明,从保持ME的清洁和可工作性而言,在运行期间,保持除雾器板片表面湿润比在线高压水冲洗更为重要。因此,通常认为采用低压水,较长的冲洗时间对保持ME板片的清洁是更为有效的措施。影响冲洗效果的因素有喷嘴类型、喷嘴布置、喷射角度、覆盖率、冲洗水压力、流量、冲洗保持时间和周期。
(3)冲洗水质量:如果冲洗水中不溶性固体物含量较高,可能堵塞喷嘴和管道造成很差的冲洗效果。如果冲洗水中Ca2+达到过饱和,例如高硬度的地下水或工艺回收水,则会增加产生亚硫酸盐/硫酸盐的反应,导致板片结垢。
(4)板片设计:板片的设计对除雾器的工作效率是至关重要的,板片表面有复杂隆起的结构和有较多冲洗不到的部位,会迅速发生固体物堆积现象,最终发展成堵塞通道。
(5)板片的间距:板片间距的确定也是除雾器设计的关
键。正如前面已谈到,太窄易发生固体堆积、堵塞板间流道;太宽使得临界流速下降,除雾效果下降。
2.除雾器冲洗面
烟气中大部分浆体液滴在V形板片的第一个通道处被捕获,所以对除雾器迎风面这一区域的冲洗最为有效;因此除雾器冲洗系统至少需冲洗ME每级的迎风面。在一个有二级的除雾器中,建议最好还应冲洗第一级的背面。如前所述,通常超过95%的液滴在第一级中被除去,也解是说第一级的正面和背面都易被浆液“污染”,冲洗第一级的背面将有助于防止固体物聚积在板片出口侧的通道上。如果第一级的通道超过两个或板间距相对较窄,就更有必要冲洗第一级的背面。
一般不建议冲洗最后一级的背面,试验证明,在烟气流速为3.0~3.7m/s时,烟流将夹带最后一级背面冲洗水的10%~20%,而且这部分冲洗水被直接带至除雾器下游侧的设备,烟道和烟囱内,对于采用湿烟囱工艺的FGD系统,可能造成烟囱“降雨”。有的设计在第二级除雾器背面布置有冲洗水管,但仅在启停FGD系统时冲洗其背面。
3.冲洗喷嘴与冲洗面的距离
冲洗喷嘴太靠近除雾器表面,则单个喷嘴喷出水雾的覆盖面积下降,保证冲洗水覆盖整个除雾器表面所需要的喷嘴数将增多。喷嘴离除雾器表面远些可以减少所需喷嘴数量,如离得太远,烟气流的作用可能使喷射的水雾形状发生畸变,造成有些区域得不到充分的冲洗。从实际冲洗情况来看,喷嘴离除雾
器表面0.6~0.9m比较合理。
4.冲洗覆盖率
如前所述,如果除雾器得不到全面、有效的冲洗,就会迅速产生结垢和堵塞。冲洗系统的设计,重要的是冲洗要覆盖除雾器的整个表面。冲洗喷嘴一般采用实心锥喷嘴,喷射水雾的断面呈圆形,相邻喷嘴喷射出的水雾必须适当搭接、部分重叠,以确保冲洗水对整个除雾器表面有一定的覆盖程度。常用冲洗覆盖率来表示这种覆盖程度。即
冲洗覆盖率(%)=nπh2tan2(α/2)
×100
A
式中:A为 ME某一冲洗面的有效通流面积(m2);n为该冲洗面的喷嘴数;α为喷射角度;h为喷嘴距 ME表面的垂直距
离(m)。
如果喷嘴按矩形阵布置,为了确保完全覆盖,应使冲洗覆盖率大约为150%,为了得到可靠的覆盖裕量,一些冲洗系统
的设计更接近180%~200%的覆盖率。
为了确保除雾器的表面获得全面、有效的冲洗,另外应注意的问题是,要尽量减少除雾器支撑梁对冲洗的影响,喷嘴的布置要考虑支撑梁和其他障碍物的位置。如果布置不合理会造成除雾器的某些区域得不到冲洗。
5.冲洗喷嘴类型
许多类型的喷嘴都可用于除雾器的冲洗。但经验表明,用于除雾器冲洗的喷嘴在结构、有效流道的大小、水雾形状、喷射角度、雾化粒度分布以及喷射断面上水量分布的均匀程度等方面有特殊要求。
有一种装有固定阀片的喷嘴,喷射出的水雾均匀、呈实心锥形,液滴比较大,建议采用这种喷嘴冲洗除雾器。如果采用的喷嘴喷射出大量细小的液滴(30~40μm),那么,这些细小的液滴就可能被烟气夹带穿过除雾器。由于要求喷嘴能长期可靠的工作,所以不推荐采用有内旋转头的喷嘴,当采用含有较多固体颗粒物的回收水作冲洗水时,冲洗喷嘴还应有较大的
有效流通通道,这样可以减少喷嘴堵塞的可能性。
一般采用的冲洗喷嘴的喷射角为90°~120°对于除雾器冲洗系统,应采用喷射角为90°的喷嘴。当喷射角大于90°时,使锥形水雾边缘部分的水流达到能充分冲洗板片所需要的时间稍长些。因为是间歇冲洗,冲洗持续时间较短,喷嘴开始喷射时以小角度喷水冲击除雾器,随着压力、水流量的稳定、喷射断面上水量分布才逐渐均匀。
最后,要求冲洗喷嘴喷射断面上水量分布均匀、稳定。对一些喷嘴的试验发现,喷射断面边缘的水量明显高于中间的水量(含液比高达3∶1)。采用这种喷嘴,在水雾边缘搭接、重叠的布置中,将造成水雾中心的冲洗水量不足,而搭接重叠区的冲洗水又过多。
6.冲洗水流量、持续时间和周期
除雾器表面冲洗水的瞬时水量常被称作冲洗水流量,单位为L/(s·m2)。冲洗水流量也是设计除雾器冲洗系统的一个重要参数量。如果冲洗水量太小,易造成结垢或堵塞,冲洗水虽太大会使除雾器板片中充满水沫,造成烟气夹带水雾量增多。冲洗水量、冲洗持续时间和冲洗频率除了要满足冲洗除雾器的要求外,还需考虑FGD系统的水平衡,特别当采用全部或部分冲洗水作为吸收塔的补加水时。因此,有些冲洗程序考虑了锅炉负荷,使冲洗时间和频率随烟气流量调整,或将冲洗时间和频率作为控制吸收塔反应罐液位的变量。
经验表明,垂直流除雾器第一级迎风面的冲洗水流量应为1.0L/(s·m2),第一级背面和第二级迎风面的冲洗水流量应为0.34L/(s·m2)。对于水平流除雾器,推荐的冲洗水流量为:第一级迎风面1.0L/(s·m2),第一级背面和第二级迎风
面为0.7L/(s·m2)。
冲洗周期指两次冲洗的时间间隔。冲洗持续时间和冲洗周期的确定要综合考虑保持 ME清洁和避免影响FGD系统水平衡。冲洗时间长、周期短有利保持除雾器清洁,但大量冲洗水进入吸收塔可能破坏系统水平衡,造成正水平衡,并给反应罐浆液浓度的控制带来困难。此外,除雾器冲洗期间烟气带水量增大,一般是不冲洗时的3~5倍。
冲洗的目的是在结垢或堵塞发生之前冲去或稀释粘附在除雾器板面上未流走的浆液。冲洗频率高可以减少浆液在除雾器板片上的停留时间和变成过饱和浆液的时间。冲洗时间只需要足以保证有充足的水流冲洗至板片上,按上述推荐的冲洗水流量在短时间内冲洗干净除雾器的所有板片。冲洗时间必须包括冲洗水阀开启、喷嘴达到额定冲洗水流量所需要的时间、洗净板片所需要的最短时间和水阀关闭时间。
由于除雾器每级以及各级的每面粘附浆液的情况不同,因此每面冲洗周期不同。第一级正面多为30min冲洗1次,每次
持续冲洗时间45~60s,而其背面则30~60min冲洗1次,每
次持续时间45~60s;第二级正面每小时冲洗1次,每次时间为45~60s,而其背面如果装了冲洗水管也仅在启停机时进行冲洗。
对于冲洗水阀的设置,通常一个水阀控制1~2根冲洗水管,执行冲洗程序时每次仅开启一个水阀,在水阀开、闭过程中水压和流量都达不到设计要求,此期间的冲洗效果不理想。如果水阀开、闭时间偏长(采用电动阀往往开、闭时间较长),不仅耗水量大而且要延长单个阀门的冲洗时间,延长单个阀门的冲洗时间就将延长冲洗周期,因此应选用开闭时1.5~2.5s的气动阀,为避免阀门快开快关时出现水锤现象,可使一个阀门未全关时另一阀门开始打开。
为了降低除雾器瞬时冲洗水流量,保持每个喷嘴压力稳
定,在实际冲洗除雾器每个面时,分区依次冲洗。图13 103和图131013分别示出了一个水平流除雾器和垂直流除雾器冲洗流程图和冲洗时间表,从上述两图可看出,在任何时间里,仅开启一个冲洗水阀,每次仅冲洗除雾器一面约25%的面积。除雾器的冲洗按预先编好的程序执行,运行操作
人员应能很方便地从操作屏上监视冲洗程序的执行情况,系统工程师则可根据冲洗效果以及其他需要调整冲洗顺序和冲洗时间。FGD系统除厂除雾器需定时冲洗外,吸收塔入口干/湿交界面也需定时冲洗,因此通常采用DCS控制系统完成冲洗逻辑控制。

图131013 垂直流平放除雾器冲洗流程图和冲洗时间表
(a)ME冲洗流程图;(b)ME、吸收塔干/湿界面、氧化布气管冲洗时间表
7.冲洗水压
冲洗水压影响喷射液滴大小和水雾的形状,压力过高易使冲洗水雾化,增加烟气带水量,而且会降低板片的使用寿命。压力过低有可能形成不了理想的水雾形状。烟气流还会使水雾形状发生畸变,降低冲洗效果。应根据冲洗喷嘴的特性以及喷嘴与冲洗表面的距离等因素来确定冲洗水压,一般冲洗水压力
为140~280kPa较为适合。
8.冲洗水质
冲洗水质量主要指冲洗水中石膏相对饱和度和固体悬浮物含量,这是设计除雾器冲洗系统必须考虑的因素。除雾器冲洗水的一部分会黏附在板片上直到下个冲洗周期,附在板片上的这些水会吸收烟气中残留的SO2而增加其石膏相对饱和度。如果冲洗水原来就具有较高的石膏相对饱和度(例如采用脱水系统回收水作冲洗水时),那么,这种水就会变成石膏过饱和溶液,从而产生结垢。已证实,冲洗水石膏相对饱和度低于50%能成功地防止由于冲洗水质量造成的除雾器结垢。当冲洗水的石膏相对饱和度高于50%时,可以将其与石膏相对饱和度较低的其他补加水或与部分新鲜水混合使用。
冲洗除雾器的目的是清除除雾器板片上的固体物,如果冲洗水中固体悬浮物含量较多,显然无助于达到这一目的。而且还可能最终造成堵塞冲洗母管和喷嘴。冲洗喷嘴被堵塞是采用回收水冲洗时最常见的原因之一,因此近年湿法FGD系统多采用无固体悬浮物的工业水冲洗除雾器,在冲洗水母管上安装滤网有助于防止外来较大的颗粒物堵塞冲洗喷嘴。
八、除雾器系统配置的仪器
为了保持除雾器稳定运行,适当安装一些监测除雾器和冲洗水系统的仪器是十分有必要的。对除雾器应连续显示、记录除雾器两侧的压降,除雾器压降能很好地反映除雾器的清洁状况。虽然除雾器的烟气压降会随处理烟气流量的增加而增大,但除雾器压降不正常地增大往往预示可能存在某种异常情况。
对于冲洗系统,喷嘴的类型和压力决定了冲洗水流量,因此,对每个冲洗母管的压力,除就地应装压力表外,应实现远方监视。在每个冲洗周期中,母管冲洗水流量的瞬时值可以反映母管和喷嘴是否有堵塞。ME冲洗水流量累加值除了可以检查冲洗母管和喷嘴是否有堵塞外,还可以用来查找FGD系统水平衡异常原因和确定冲洗水是否存在泄漏。为降低造价,也可不设置冲洗水流量监测仪表。
九、除雾器的结构材料
除雾器板片结构材料的选择需要考虑的因素有:烟气温度、材料易燃性、耐久性和耐化学腐蚀性。用作除雾器的典型材料是聚丙烯(PP)、玻璃耦合聚丙烯、聚砜、FRPF以及各种等级的不锈钢,采用前两种材料的占多数,但美国采用FRP更普遍,其次是PP材料。美国是基于日本和欧洲的成功经验才接受PP除雾器。国内多数采用PP材料,个别FGD装置第一级除雾器采用PVC制作,运行情况表明,PVC的耐热变形性差,曾发生过热变形事故,建议最好不采用这种材质。
通过除雾器的烟气温度通常是45~65℃,上述材料都能应用于这一温度范围内。但当吸收塔喷淋泵事故停运时,通过
ME的烟温会迅速上升,上升的幅度和持续时间取决于吸收塔入口烟气温度、吸收塔的体积、吸收塔入口烟道是否设置有事故急冷装置以及隔离吸收塔所需要的时间。当吸收塔上游侧装有降温换热器时,吸收塔入口烟温一般约为80~100℃,当出现上述事故情况时,要求旁路烟道挡板能在20s内开启,从降温换热器过来的热烟气与塔内冷烟气混合后再接触到除雾器时,烟温一般不会超过80℃,因此在这种工艺流程中采用PP除雾器是可行的。即使由于某种原因不能隔断吸收塔,只要旁路挡板能迅速开启,必要时开启除雾器冲洗水降温,也能防止PP板片发生热变形。因此,目前国内大多数电厂湿法FGD系统不要求在吸收塔入口设计事故急冷装置。
当FGD系统不采用GGH时,吸收塔入口烟温通常约为120~140℃,当出现吸收塔循环泵全停事故时,吸收塔中的组件都将面临高烟气温度的威胁,如果吸收塔采用橡胶内衬防腐,橡胶内衬将先于PP除雾器遭受更严重的热损坏,PP和玻璃耦合聚丙烯在较短的时间内也将热变形。其他几种材料能够承受较高的温度,因此,在美国,对于没有设置合适的事故急冷保护装置的系统不推荐采用PP或玻璃耦合聚丙烯,建议采用FRP材料,尽管后者比前两者的价格贵,但FRP耐热性比后两者高。然而如果高温时间很长(5~10min以上),制作FRP所采用的树脂不合适,也会发生问题。
国内确有在吸收塔上游未采用降温换热器,也不设置事故急冷保护装置的湿式FGD装置,吸收塔采用橡胶内衬,除雾器采用PP制作。其安全保障全部押在入口和旁路挡板在事故发生时能迅速关闭和开启上。但是,由于旁路挡板不经常动作,可能卡涩,挡板开启设备也可能出现故障而拒动,因此出现“烧”塔的可能是存在的。国外有类似报道,广东某电厂FGD系统2002年就曾4次因系统失电,旁路挡板拒动。需就地手动开启旁路挡板,致使高温烟气流入吸收塔,每次长达10~15min,造成PP材质除雾器严重损坏,但吸收塔橡胶内衬未严重损坏。因此,对于这种工艺流程,设置吸收塔事故急冷装置是防止烧塔的措施之一。
除雾器所处的腐蚀环境,从接近中性到强酸性、浆体液滴的Cl-浓度可能超过10000mg/L。上述有机材料都能耐受这种腐蚀环境。而一些等级较低的奥氏体不锈钢,对于低pH值和高Cl-浓度的耐腐蚀性往往让人担心。一般要求采用高等级不锈钢,例如317L、317LMN或更好的不锈钢,具体采用何种等级的不锈钢,则取决于Cl-浓度。同样,插入塔内的冲洗水管和喷嘴如采用金属材质,也应按上述原则选材。通常不建议采用FRP冲洗水管,在运行中发生过 FRP冲洗水管折断事故。
FGD运行时,除雾器材质易燃性显然不是一个需要担心的问题。在检修吸收塔、与除雾器相邻烟道或除雾器区域的支撑件需要焊接时,应考虑到除雾器板片材料的可燃性。在这种情况下,对PP和玻璃耦合PP制作的除雾器必须采取防火措施,并在现场备有消防设备,派专人监护。FRP可以作成具有阻燃性,聚砜树脂就具有阻燃性,但也不能忽视防火措施。
除雾器板片材料耐久性是一个要综合考虑初期投资成本和使用寿命的问题。除雾器的使用寿命除与材料本身的性能有关外,在一定程度还与使用情况有关,例如易于结垢,垢的清除需用高压水冲洗,则可能损坏板片。PP和玻璃耦合PP在使用数年后会逐渐变脆,高压水会使板片破裂。另外,检修中如在除雾器上行走或让除雾器承受高应力,FRP表面会产生裂缝,FGD工艺液会顺着裂缝渗入纤维中,如果纤维没有经过
很好的树脂饱和处理,纤维将膨胀,导致板片起层。关于耐久性还需注意的是,上面所提到的材料无一在维修期间可以在ME上行走。因此在检修期间为保护除雾器板片,应搭建临时平台和人行通道。
经验表明,PP、玻璃耦合PP、FRP除雾器板片的平均使用寿命是5~8年,国内采用PP制作的除雾器已有十几年的使用经历,目前除质地变硬,有个剔板片开裂外,仍在使用之中。聚砜树脂是一种均匀性与PP相同的柔韧性较好的材料,不像FRP那样易出现破裂。聚砜商业应用于FGD系统的时间不长,安装的数量还不足评价其平均使用寿命,但预计有较长的使用寿命,不过聚砜除雾器比PP和FRF的除雾器初期投资费用高。不锈钢除雾器耐久性很好,选材合理的不锈钢使用寿命应在15年以上。
第十一节 石灰石浆液制备系统设计优化
一、石灰石制备系统方案
石灰石浆液制备系统的主要功能是制备合格的吸收剂浆液,并根据吸收塔系统的需要由石灰石浆液泵直接打入吸收塔内或打到循环泵入口管道,与吸收塔内浆液经喷嘴充分雾化而吸收烟气中的SO2,从而达到脱硫的目的。FGD系统的石灰石制浆制备通常有以下三种方案:
(1)由市场直接购买粒度符合要求的石灰石粉(90%小于44μm),运至电厂储粉仓存储,加水搅拌,制成石灰石浆液。
(2)新建一座干式制粉站。在石灰石矿点附近或厂内空地处自设制粉站,由市场购买的块状石灰石经干式球磨机磨制成石灰石粉,送至储粉仓存储,加水搅拌,制成石灰石浆液,再用泵送至吸收塔作为吸收剂。
(3)厂内湿磨方案。即外购石灰石块,在厂内经湿式球磨机磨制成石灰石浆液的方法。湿式球磨机直接将一定粒度的石灰石块制成浆液,经水力旋流器分离后,合格的浆液送去配浆,不合格的返回再磨,可达到超细粒径325目(44μm),过筛率90%以上。与干式相比,省去了诸如高温风机、除尘器、旋风分离器等附属设备。
国外少数脱硫系统不设单独的制浆罐,而是直接将干粉注入吸收塔,这种装置对石灰石粉的粒度要求较高,要用超细的石灰石粉,国内尚未应用。
二、干式球磨机制浆和湿式球磨机制浆的比较
图13111是干式球磨机制粉车间总貌及现场干式球磨机照片,图13112是某独立石灰石制粉厂设备。外购粒径20mm的石灰石块置于石灰石堆场,然后用装载车运送到石灰石制粉卸料斗,经皮带输送机、电磁除铁器、斗式提升机送至石灰石块仓储存。石灰石块仓下设置称重给料机,通过变频电机实现对给料量的控制。石灰石块料由称重给料机送入石灰石立式辊磨,立式辊磨顶部自带分离器,通过调节风环阀,可改变产品细度,并可使磨内料床负荷均匀、稳定。粉料出磨后,随排风机气流送入袋式收尘器中进行收集,再经水平及垂直输送设备送入石灰石粉仓内储存,根据需要送入制浆池,配成一定浓度的石灰石浆液。辅助工艺系统主要由烘干、除尘、冷却水、充水、仪用及杂用压缩空气、通风和空调、取样、检修起吊等设备/设施构成,这些设备/设施与主工艺设备一起,构成了一套完整的制粉系统,确保制粉车间的安全文明生产。此外,如果入磨物料表面水分大于1.5%时,将影响磨机的产量,在系统中还应设烘干装置。通常,烘干采用蒸汽热风系统。

图13111 干式球磨机制粉车间及干式球磨机

图13112 厂外独立的干式球磨机制粉厂

图13113 湿式球磨机及水力分离器设备
图13113为湿式球磨机及水力分离器设备。一定粒径的石灰石块(外购或自制,粒径一般不大于20mm)由自卸卡车直接卸入地下料斗,经振动给料机、石灰石输送机、斗式提升机、石灰石布料装置送至石灰石储仓内,再由称重式皮带给料机送到湿式球磨机内。在湿式球磨机内被钢球砸击、挤压和碾磨,在湿式球磨机入口加入一定比例的滤液水(或工艺水),此水汇同石灰石旋流器的底流流经湿式球磨机筒体,将碾磨后的细小石灰石颗粒带出筒体,进入再循环箱,而石灰石中的杂物则被湿式球磨机出口的环形滤网滤出,进入置于外部的杂物箱。进入再循环箱的石灰石浆液被再循环泵打入石灰石浆液旋流站进行分离,浆液中的大颗粒被分离到旋流器的底部,并被底流带回到湿式球磨机入口重新碾磨。满足粒度要
求、含固率(wt)为25%~30%的石灰石浆液溢流储存于石灰石浆液箱中,然后经石灰石浆液泵送至脱硫系统的吸收塔中。为保证系统物料平衡、浆液浓度和细度合格,旋流系统设有再循环管道及浓度、液位、细度调节阀门。根据不同设计要求,水力旋流器可分为一级或两级。系统还设有冲洗水用于设备停止或切换时冲洗泵、管路和旋流器。为使石灰石浆液混合均匀、防止沉淀,在石灰石浆液箱和石灰石浆液循环箱内装设浆液搅拌器。
干式球磨机制浆和湿式球磨机制浆两者比较如下:
(1)干式球磨机制粉、制浆和湿式球磨机制浆方案在石灰石块入磨之前的工序基本相同,从入磨后到制成浆液,湿式球磨机所用的辅助设备要比干式球磨机少得多,因而投资较低,
占地面积小,发生故障的可能性也大为减小。一般干式球磨机制浆方案的初投资要比湿式球磨机高20%~33%。
(2)虽然湿式球磨机本体电耗比干式球磨机的电耗大,但就整个系统而言,电耗还是低,因而其运行费用大约要低
10%~15%。
(3)干式球磨机主要通过调整球磨机的运行参数来调节粉量和粒径,而湿式球磨机还可通过调整出口水力旋流器的性能参数来达到目的,从实际运行情况看,湿式球磨机的石灰石浆液粒度常常达不到设计要求,偏大,而出力也不足,主要是因为钢球量难以保持最佳状态,另外,旋流子磨损严重,影响粒径的调节。
(4)湿式球磨机需防止因泄漏外流的浆液造成厂区的环境污染问题,厂内干式球磨机制浆系统需注意扬尘造成的环境污染和噪声污染,不过干式球磨机制粉系统可独立设置在电厂外面。厂外设置粉站的优点是电厂少占地,可以利用矿区贫瘠的地域建站,避免了制粉中扬尘及设备噪声对厂区的影响。但厂外建站,电厂需另设一套生产管理机构和运行值班人员,从而使投资和运行费用有所增加,对大机组烟气脱硫比较适用。
(5)吸收剂制备系统的选择应综合考虑吸收剂来源、投资、运行成本及运输条件等,进行综合技术经济比较后确定。采用石灰石碎石的优点是原材料易获得,可以在户外或户内大量储存,而且一般比采用石灰石粉要便宜些,但系统较大且较复杂,增加FGD系统占地面积。外购合格的石灰石粉最省事,脱硫系统占地面积最小,节省初投资。但电厂用粉受外界条件的制约,必须确保可靠供粉。随着环保要求的提高和对脱硫系统取消旁路烟道的限制,直接外购石灰石粉可使脱硫系统更简单,从而大大提高脱硫系统的可用率。在资源落实、价格合理时,应优先采用直接购买石灰石粉方案;当条件许可且方案合理时,可由电厂自建湿式球磨机吸收剂制备系统。当必须新建石灰石加工粉厂时,应优先考虑区域性协作即集中建厂,且应根据投资及管理方式、加工工艺、厂址位置、运输条件等因素进行综合技术经济论证。
三、外购石灰石粉与湿式石灰石制浆方案经济性比较
按年运行5500h、电价0.3476元/(kWh)、石灰石粉单价
250元/t、石灰石块单价150元/t计,干、湿式石灰石制浆方案设计,相同容量机组在同一建设时期,采用外购石灰石粉方案与湿式石灰石制浆方案经济性对比情况见表13111。表13111 外购石灰石粉与湿式制粉
续表

由表13111可见,在一次性投资上,石灰石湿磨制浆方案总投资高于石灰石粉制浆方案。在运行费用上,石灰石湿磨制浆方案的电耗和设备年维护费用比石灰石粉制浆方案高,但由于石灰石单价比成品粉要便宜100元/t,因此,石灰石湿磨制浆方案的年运行总费用比石灰石粉制浆方案节省约
696万元。
从长期运行的角度考虑,石灰石湿磨制浆方案在经济上要优于石灰石粉制浆方案,但湿式制浆系统在实际运行中故障率较高,运行维护量大,实际设计中应根据当地石灰石资源、场地等条件,综合考虑选择制浆方案。如选用干式制粉方案,可考虑周边数厂合建石灰石干粉制备场,在保证石灰石品质的同时,可大大降低石灰石成本。
四、某电厂无旁路FGD制浆系统的设计
该电厂附近石灰石储量丰富,有专门的制粉厂,因而电厂采用外购石灰石粉制浆。石灰石粉制浆系统主要包括石灰石粉仓及除尘器、石灰石浆液罐及搅拌器、石灰石浆液泵、石灰石粉给料机及计量装置、流化风系统等,现场设备如图1311 4所示,表13112为制浆系统主要设备参数。
表13112 某电厂石灰石粉制浆系统
主要设备参数
系统经济性对比



续表
序号 设备名称
规格
单位 数量

由罐车运来的石灰石粉(外购,粒度90%小于44μm),利用压缩空气,通过上粉管气力输送到石灰石仓中,石灰石粉仓容积按两台锅炉在BMCR工况下运行3天的吸收剂耗量考虑,粉仓设有料位指示器防止满仓或空仓,粉仓顶还设有布袋除粉器,并设有防爆门。为防止底部石灰石粉搭桥,在仓底四周还注入流化空气,使石灰石粉呈流态化,均匀地下到给料机,通过设置在粉仓底部的两部电动锁气器和两部螺旋给料机将石灰石粉送至1个石灰石浆液箱制备浆液,石灰石浆液箱的容积按储存2台锅炉BMCR工况不小于6h浆液量设计,石浆液箱设有一台顶进式搅拌器以保证浆液浓度均匀和不发生沉淀。在浆液箱中石灰石粉与工艺水进行混合搅拌,直至达到所需的浓度(wt)25%~30%,对应的石灰石浆液密度大致在1190~1250kg/m3。石灰石浆液经由石灰石浆液泵输送直接进入吸收塔,再由循环泵打上喷淋层。每个吸收塔设置2台石灰石供浆泵,1台运行1台备用。为防止机组负荷变化时,浆液管道发生沉积现象,供浆系统采用环管输送方式,在石灰石浆液泵出口管道上设有密度计和流量控制阀来控制石灰石浆液的流量,控制阀为调节阀。

图13114 某电厂石灰石粉制浆系统设备
五、无旁路FGD制浆系统的设计优化
在满足一般的制浆系统设计原则下,对无旁路FGD制浆系统的设计建议如下:
(1)优先用石灰石粉制浆而不用湿式球磨机,这样可以减少许多故障环节。
(2)如采用湿式球磨机或干式球磨机制浆,则宜独立设置一个制浆车间,由独立人员操作运行。厂内湿式球磨机出力不宜选的太大,应有1台备用为佳,必要时增加1套石灰石粉制浆系统做备用。
(3)FGD制浆系统宜公用,石灰石浆液箱容量宜大不宜小;可以采用两个相同容量的石灰石浆液箱,石灰石浆液泵交
叉布置。
(4)每个吸收塔的供浆管道宜设置两条独立的石灰石浆液管道。
(5)石灰石浆液供浆阀宜采用全开、全关阀。
六、石灰石浆液制备系统的一般设计原则
FGD石灰石浆液制备系统的一般设计原则如下:
(1)原料选择。根据地区原料供应及厂内场地条件综合考虑买石灰石粉或石灰石块制浆。如采用石灰石块,当厂内设置破碎装置时,宜采用不大于100mm的石灰石块。当厂内不设置破碎装置时,宜采用不大于20mm的石灰石块。
(2)整体规划。吸收剂制备系统宜按公用系统设置,可按
两套或多套脱硫装置合用一套设置,但吸收剂浆液制备系统一般应不少于2套。当电厂只有1台机组时,可只设1套吸收剂浆液制备系统,并相应增大石灰石浆液箱容量。采用磨制系统时,宜考虑硫分超标时临时买粉作为备用措施。
(3)系统出力。吸收剂制备系统的出力原则上应结合脱硫负荷变化,最大理论消耗量等综合考虑,尽可能考虑设备备用因素,至少应按设计工况下石灰石消耗量的150%选择,且不小于100%校核工况下的石灰石消耗量。
(4)吸收剂原料卸料、输送、储存及供应系统。为便于设备检修、提高系统可靠性。吸收剂原料卸料、输送、储存及供应系统应设置两套,石灰石块仓或石灰石粉仓的容量应根据市场运输情况和运输条件确定,一般不小于设计工况下3天的石灰石耗量。当采用石灰石块进厂方式时,根据原料供应和厂内布置等条件,考虑是否设置石灰石破碎机。
(5)磨制系统。当两台机组合用一套吸收剂浆液制备系统时,每套系统宜设置2台石灰石湿式球磨机及石灰石浆液旋流器,单台设备出力按不低于设计工况下石灰石消耗量的75%选择,且不小于50%校核工况下的石灰石消耗量,对燃煤硫分有潜在超设计值风险的情况,单台设备出力宜按100%石灰石消耗量设计。采用干磨时,每套干磨吸收剂制备系统的容量宜不小于150%的设计工况下石灰石消耗量,且不小于校核工况下的石灰石消耗量,对燃煤硫分有潜在超设计值风险的情况,单台设备出力宜按100%设计工况下石灰石消耗量的100%设计。对于多台炉合用1套吸收剂浆液制备系统时,宜设置N+1台石灰石湿式球磨机,N台运行1台备用。磨机的台数和容量经综合技术经济比较后确定。
湿式球磨机浆液制备系统的容量宜不小于设计工况下6~10h的石灰石浆液耗量,干磨浆液制备系统的石灰石浆液箱容量宜不小于设计工况下4h的石灰石浆液耗量。
(6)石灰石浆液箱。考虑系统的可靠性及在线检修,石灰石浆液箱宜设置2座,并可相互切换,浆液箱应设有浆液搅拌悬浮系统。湿式球磨机浆液制备系统的石灰石浆液箱总容量宜不小于设计工况下6~10h的石灰石浆液消耗量,干式磨机浆液制备系统的石灰石浆液箱总容量宜不小于设计工况下2h的石灰石浆液消耗量。
(7)石灰石供浆泵。每座吸收塔应设置两台石灰石供浆泵,一台运行,一台备用,浆液容量选择应结合系统供浆量、经济运行方式综合考虑。
(8)浆液管道。浆液管道设计时应充分考虑工作介质对管道系统的腐蚀与磨损,一般应选用衬胶、衬塑管道或玻璃钢管道。管道内介质流速的选择既要考虑避免浆液沉淀,同时又要考虑管道的磨损和压力损失尽可能小。浆液管道上的阀门宜选用蝶阀,尽量少采用调节阀。阀门的通流直径宜与管道一致。浆液管道上应有排空和停运自动冲洗的措施。
(9)浆液密度测量方式的选择宜结合工艺及浆液特性确定。
(10)吸收剂的制备贮运系统应有防止二次扬尘污染的措施。
七、材料选择
石灰石储存仓用碳钢制作,仓体取料口是高磨损区,应采用专用的耐磨衬层。石灰石粉储存仓可用碳钢或混凝土制作,但倒锥形出料口宜采用不锈钢,这样有利于粉料下滑。用碳钢管气动输送生石灰,管道的弯头以及料仓的取料口是易磨损部位,应选用耐磨铸铁。
石灰石浆液磨损性较强,需采用耐磨性强的材料。如石灰
石磨制时采用了回收水,石灰石浆液中有一定浓度Cl-,则需采取防腐措施。因此,如果石灰石浆液储存罐采用碳钢或混凝土作结构材料,表面应衬橡胶或玻璃鳞片树脂涂层,建议罐体底部增加耐磨增强树脂涂层,避免罐体搅拌器造成对罐底的磨损。搅拌器的轴和桨叶采用衬胶碳钢,使之能耐较严重的磨损环境。
含固量30%~40%的石灰石浆液对无衬层的碳钢管和一般的FRP管会造成磨损,多采用橡胶内衬碳钢管输送石灰石浆液,高密度聚乙烯(HDPE)管有在FGD系统成功替代橡胶内衬碳钢管的业绩,HDPE管价格较低,在输送石灰石浆液的工况下有与衬橡胶管道相同的使用寿命。可以采用橡胶衬铸铁浆泵输送石灰石浆液,也可采用耐磨合金铸铁浆泵。
第十二节 石膏脱水系统的设计优化
一、概述
石膏脱水系统的主要功能是将吸收塔内吸收SO2生成的石膏浆液脱水成含水量小于10%的石膏,这些石膏可作为商用副产品,也可抛弃不用。脱水系统的主要组成部分有石膏水力旋流器(一级脱水)、脱水机(二级脱水)及附属设备如真空泵、滤液箱、废水旋流器及废水箱、石膏仓或石膏库等。
二、典型的石膏脱水系统
吸收塔石膏浆液是含有石膏晶体、CaCl2、少量未反应石灰石、CaF2和少量飞灰等的混合物,经过石膏水力旋流器后,可实现与杂质一定的分离效果,此后再经石膏脱水机实现石膏的洗涤和脱水。石膏脱水系统具体过程描述如下。
1.一级脱水过程
吸收塔内的石膏浆液通过石膏浆液排出泵(l台运行1台备用)先送至石膏一级水力旋流器进行浓缩和石膏晶体分级。水力旋流器主要由进液分配器,若干个旋流子、上部溢流浆液箱及底部浆液分配器组成。旋流子利用离心分离的原理,浆液以切向进入水力旋流器的浆器,在离心力的作用下,大颗粒和细微颗粒得以分离。这样进入水力旋流器的浆液被分成两部分,一部分是含固率高的底流(含固率约为40%~50%),另一部分是含固率低的溢流,大部分细小的粉尘和颗粒相对集中在溢流内,溢流返回吸收塔或被送去废水处理系统。如有二级水力旋流器(即废水旋流器),则溢流部分先送到二级水力旋流器给料罐,通过废水旋流器给料泵送到废水旋流器进行浓缩分离。废水旋流器的底流返回吸收塔或先自流到石膏浆液缓冲箱,溢流液被送去废水处理系统。通过控制废水的排放量达到控制脱硫系统浆液中氯离子浓度,以保证脱硫系统安全、稳定运行的目的,同时,排出细小的灰尘以保证石膏的品质。
2.二级脱水过程
水力旋流器的底流至脱水机有两种设计:①直接流到脱水机上脱水;②依靠重力流至石膏浆液缓冲箱,再用石膏浆液给料泵送至脱水机进行脱水。在二级脱水系统中,浓缩后的石膏浆液经过脱水机进行脱水,石膏在该部分经脱水后含水量(wt%)降至10%以下,直接落到石膏库中。为保持滤布清洁及控制脱硫石膏中的细灰杂质、可溶性盐类、Cl-等成分的含量,确保脱硫石膏品质,在石膏脱水过程中用工艺水对滤布及石膏滤饼进行冲洗。石膏过滤水收集在滤液水箱中,然后由滤液水泵送到吸收塔或制浆系统重复利用。
三、FGD石膏浆液脱水系统的一般设计原则
(1)工艺设计。脱硫工艺设计应尽量为脱硫副产物的综合
利用创造条件。若脱硫副产物暂无综合利用时,可经一级旋流浓缩后输送至储存场,也可经脱水后输送至储存场,但应与灰渣分别堆放,并预留以后综合利用的可能性,且应采取防止副产物造成二次污染的措施。
(2)整体规划。石膏脱水系统宜按公用系统设置,可按2套或多套脱硫装置合用一套设置,但石膏脱水系统一般不少于2套。300MW及以上机组的石膏脱水系统宜每2台机组合用一套。当规划容量明确时,也可多炉合用一套。对于一台机组脱硫的石膏脱水系统宜配置一台石膏脱水机,并相应增大石膏浆液箱容量。200MW及以下机组可全厂合用。
(3)系统出力。石膏脱水系统的出力应按不低于设计工况下石膏含量的150%选择,且不应小于100%校核工况下的石膏产量。
(4)设备容量。每套石膏脱水系统宜设置2台石膏脱水机,单台设备出力按设计工况下石膏产量的100%选择,且不小于50%校核工况下的石膏产量。对于多炉合用一套石膏脱水系统时,宜设置n+1台石膏脱水机,n台运行1台备用。在具备水力输送系统的条件下,石膏脱水机也可根据综合利用条件,先安装1台,并预留再上1台所需的位置,此时水力输送系统的能力按全容量选择。
(5)石膏储存。脱水后的石膏可在石膏仓内堆放,也可堆放在石膏库内。石膏仓的容量,应根据石膏的运行方式确定,且不小于24h石膏的产生量。石膏仓应采取防腐措施和防堵措施,在寒冷地区,石膏仓采取防冻措施。脱水后的石膏可在石膏筒仓内堆放,也可堆放在石膏储存间内。石膏仓或石膏储存间宜与石膏脱水车间紧邻布置,并应设顺畅的汽车运输通道。石膏仓下面的净空高度不应低于4.5m。
(6)其他。采用石膏抛弃方案时,应设置一级旋流装置,以回流大部分的溢流浆液,降低水耗。
四、某电厂无旁路FGD石膏浆液脱水系统的设计
某电厂石膏浆液脱水系统为两台机组FGD装置共用,是一个典型的FGD脱水系统,设有2台石膏浆液旋流站,2台真空皮带脱水机和相应配套的真空泵、滤布冲洗水箱、滤布冲洗水泵、滤饼冲洗水箱、滤饼冲洗水泵、气水分离器等,2台皮带卸料机,1个石膏库,1台回流水箱,2台回流水泵(1台运行1台备用),1台废水旋流站,2台废水旋流站给料泵(1台运行1台备用),来自吸收塔的石膏浆液经吸收塔排浆泵后进入石膏旋流站,石膏旋流站底流进入真空皮带脱水机脱水,脱水的同时对石膏进行冲洗,以满足石膏综合利用的品质要求,脱水后石膏含水量(wt)不大于10%。石膏旋流站溢流以及石膏滤液自流至回流水箱,一部分通过回流水泵送回吸收塔作为补充水,以维持吸收塔内的液面平衡;一部分通过废水旋流站给料泵进人废水旋流站,其底流返回回流水箱,溢流排至废水处理系统,以控制浆液中氯离子含量。
每台真空皮带脱水机出力为BMCR工况下2台脱硫装置75%的石膏产量。每台石膏浆液旋流站处理量为1台锅炉BMCR工况下FGD装置石膏排浆量。每台真空皮带脱水机对应设置1台皮带输送机,以使脱水后的石膏尽量均匀地堆积于石膏库内。两套机组共用1个石膏库,其容积按2台锅炉BMCR工况运行5天(每天24h计)的石膏量进行设计,石膏由铲车搬到卡车上外卖。图13121、图13122是FGD石膏浆液脱水楼总貌及现场主要设备,FGD废水处理系统与石膏浆液脱水楼相连,表13121为设备主要参数。

图13121 某电厂石膏浆液脱水楼和废水处理楼总貌
表13121 某电厂FGD脱水系统主要设备参数
序号 设备名称
设备参数
单位 数量


图13122 石膏浆液脱水系统现场及设备
可见无旁路FGD石膏浆液脱水系统与常规的带旁路系统设计基本一致,为提高无旁路FGD石膏浆液脱水系统的可靠性,可从以下几方面进一步优化改进。
(1)石膏旋流器宜直接布置在脱水机上方,这样更为简洁紧凑。采用石膏浆液缓冲箱的设计因石膏浆液密度大,泵的磨
损大,运行易出故障。
(2)尽量取消石膏输送皮带机,让石膏脱完水后直接从皮带机上落到石膏库中。许多电厂原设计有石膏输送皮带机,但运行中常出故障,且大量石膏会泄漏到地面,影响环境卫生,从投资上看,还增加了石膏楼的高度。因此,为提高石膏脱水
系统的可靠性,系统应尽量简化。
图1312 3为某1000MW机组的二级石膏输送皮带
机,它在输送机下面使用了格栅,石膏可以直接落到石膏库中,其设计值得借鉴。

图13123 改进的石膏输送皮带机设计
(3)在石膏脱水操作画面上增加水力旋流器入口压力监视,方便运行人员判断系统是否正常运行,将水力旋流器各个旋流子入口手动门更换为电动门。
(4)石膏水力旋流器溢流不应与石膏滤液一道汇至回流水箱,而应单独分开。滤液中除Cl-浓度可能高些外,其水质相对溢流来说还是比较干净的,大部分影响脱硫反应的细小粉尘和颗粒存在溢流中,应将溢流的一部分排放至废水处理系统。
(5)石膏水力旋流器旋流子宜采用更耐磨的不锈钢材料,代替常规的聚氨酯材料,许多电厂都已更换,如图1312
4所示。

图13124 石膏旋流器旋流子更换为不锈钢材料
五、无旁路FGD石膏浆液脱水系统的设计优化
(1)石膏脱水系统应有2台及以上脱水机。对2台机组共用的,单台脱水机宜能处理100%的2台机组产生的石膏量;或单台脱水机处理100%的1台机组产生的石膏量,并备用1台。
(2)将石膏旋流器直接布置在脱水机上方最为简洁可靠;旋流子宜采用更耐磨的不锈钢材料。
(3)尽量少设置石膏输送皮带及转运设备。
(4)采用石膏库而不用石膏仓,可进一步提高系统的可靠性。
六、真空圆盘式脱水机
目前,FGD石膏浆液脱水系统普遍使用的设备是真空皮带脱水机,其系统复杂,占地面积大,电耗高,检修维护繁琐,备品、备件耗量大,特别是滤布的频繁更换,直接影响了整个FGD系统的可用率。为此,国内某公司开发了一种新型的脱水机———微孔陶瓷圆盘石膏脱水机,其具备节能、占地面积小、维护方便等优点。
1.脱水原理
圆盘脱水机运用毛细微孔盘片的毛细现象,在抽真空时,只能让水通过,空气和矿物质颗粒无法通过,无真空损失的机理,极大地降低了能耗和物料水分。其工作过程分为六个区域:吸浆区、过滤区、淋洗区、干燥区、卸料区、反冲洗区,反复循环,图13125为圆盘脱水机工作的流程。
(1)吸浆区。通过管路将待处理的石膏浆液[≥20%(wt%)浓度]连续输入到圆盘脱水机浆液槽中,浸没在浆液槽的盘片在真空负压的作用下,盘片表面吸附形成一层滤饼,滤液通过盘片过滤至分配阀到达排液罐。
(2)过滤区。吸附滤饼在此区域进行过滤。
(3)淋洗区。滤饼转出浆液槽后对滤饼进行喷淋洗涤。(4)干燥区。在主轴减速机的带动下,吸附在盘片上的滤
饼转到干燥区,在真空的作用下滤饼继续脱水。
(5)卸料区。滤饼干燥后,转子转动到卸料区(无真空),在刮刀装置作用下进行卸料。
(6)反冲洗区。卸料后的盘片进入反冲洗区,此时用过滤液或自来水(如不含固体杂质,工业用水也可用)在一定压力
下(0.075~0.1MPa),从分配阀进入盘片内腔,由内而外冲
洗盘片的微孔,同时将残留在盘片表面的残余矿物冲洗下来。盘片经过一定的工作时间后(一般为7~12h),盘片微孔因逐渐被堵塞而降低过滤效率,为保证盘片微孔通畅,启用混合清洗系统,使自动清洗、化学清洗和反冲洗相互作用,达到最佳清洗效果。清洗时间一般为45~60min,通过混合清洗使盘片的微孔进一步疏通,这样就可保证后续过滤高效率。
2.实际运行效果
从运行情况看,真空圆盘脱水机出力及脱水后的石膏含水量未达到设计要求,石膏厚度在10~20mm,含水率(wt%)
在13%~16%。

图13125 圆盘脱水机工作流程
3.圆盘式脱水机的特点
(1)节能效果显著。以该厂为例,3台真空圆盘脱水机可基本代替1台真空皮带脱水机,其耗电不到原来的20%,主要是它不需要大功率的真空泵。加上设备初投资、安装运行维护费用的降低,真空圆盘脱水机的经济效益显著。
(2)占地面积小。圆盘式脱水机脱水车间面积约为真空皮带脱水机的1/3左右,因其设备结构紧凑、体积较小,既适用于新建机组,也适用于现有机组改造。设备可在吸收塔之间布置,可大幅节省FGD总占地面积。
(3)自动化程度高,操作简单,安装维护方便,可靠性较高。圆盘式脱水机主要传动部件采用免维护设计,可降低故障几率,槽体耙子采用不锈钢结构,使用寿命可达10年以上;总体结构简单,维护点少,主要备件更换简易,与真空皮带机相比,维护量大幅度降低,节约人力、物力。高性能系列机型采用程序自动控制、自动进料、自动清洗,可接入DCS,实现远程控制,降低操作人员数量。另外,圆盘脱水机无高转速设备,系统振动,噪声极小,运行环境良好。
(4)其他。1台圆盘脱水机制造周期约45天,安装周期约3天/台,因安装时间短,可实现不停机改造,脱水机整体吊装,施工安全风险小。
微孔陶瓷真空圆盘石膏脱水机还需要在提高脱水性能、降低石膏含水率以及优化微孔陶瓷的清洗方面进一步进行研究。对无旁路FGD系统而言,该种脱水机的开发应用无疑可大大提高FGD脱水系统的可靠性和灵活性,对老系统的改造尤为有益。
第十三节 保证石膏质量的设计要点
一、石膏副产品质量保证值的提出
选择湿法石灰石FGD工艺时,通常会在技术规范中提出石膏保证值,目前国内对石膏质量的保证项目有两种表示方法:一种是在设计条件下(即额定工况下的烟气条件、达到规定的脱硫率和给定的石灰石品质)要求石膏副产品的以下组成成分含量达到规定的保证值:游离水含量(wt%)、CaSO4·
2H2O含量(wt%)、可溶性Cl-、F-、Mg2+含量(mg/kg干
基)或总可溶性盐含量;另一种表示方法是对石膏副产品游离
水、未反应的 CaCO3和 MgCO3 (wt%)、CaSO3 · 1/2H2O
(wt%)以及可溶性Cl-、F-、Mg2+含量提出保证值要求。
保证石膏质量的前提条件:
(1)单位时间SO2脱除量(mol/h或kg/h)。(2)石灰石等效CaCO3含量(wt%)。
(3)石灰石中酸不溶物含量(wt%)。
(4)Ca/S比,可在1.02~1.06范围内取值(即ηCa94%~98%)。
(5)烟气中飞灰含量(mg/m3)以及烟气流量(m3/h)。
根据CaCO3脱除SO2的总化学反应方程式可以计算出单
位时间CaSO4 ·2H2O产量、石灰石耗用量,根据Ca/S比可
得出未反应CaCO3量。假定石灰石中的酸不溶物、飞灰和未反应的CaCO3全部进入石膏中,并假定氧化率为100%,即忽略石膏中CaSO3 ·1/2H2O含量,由此可得出石膏产出量,从
而计算出石膏中CaSO4 ·2H2O、未反应CaCO3含量(wt%),
以此作为石膏质量保证值。石膏中CaSO3 ·1/2H2O含量保证值可取0.1wt%~0.35wt%。石灰石的细度对石膏质量保证值有直接的影响,细度的确定涉及到研磨设备和吸收塔模块的设计和运行pH值的选择。
电厂在确定石膏质量保证值时,可以参考已建电厂的技术规范。表13131列出了我国一些电厂FGD系统石膏质量保证值,并附有石灰石主要特性供参考,图13131示出了珞璜电厂一期FGD系统石灰石纯度与石膏成分的关系。可以看出脱硫石膏的主要杂质是石灰石中惰性物,未反应的石灰石以及飞灰,大多数脱硫石膏质量保证值取CaSO4 ·2H2O含量不低于90%。
二、循环浆液在吸收塔中停留时间对石膏质量的影响
由于石膏中CaSO3 ·1/2H2O的含量通常在0.4%以下,
因此对于特定的石灰石、特定的烟气条件,提高石膏纯度的主要途径是降低石膏中未反应CaCO3的含量。循环吸收浆液pH值、浆液中CaCO3浓度与脱硫效率有密切关系,提高pH值

图13131 某电厂FGD装置石灰石纯度与石膏成分的关系
和浆液中CaCO3浓度,脱硫效率增大。而提高浆液中CaCO3浓度则会降低石灰石的利用率和石膏纯度。解决这一矛盾的方法之一是增大吸收塔反应罐的有效体积,即提高循环浆液固体物在反应罐的停留时间。据计算,循环浆液通过吸收塔吸收区1次,浆液中仅约1%的CaCO3参与了反应,绝大部分CaCO3在反应罐中进行反应。
表13131 我国一些电厂FGD系统脱硫
石膏质量保证值

三、强制氧化程度对石膏质量的影响
影响强制氧化率的因素很多,当强制氧化装置设计不当
时,很可能造成氧化率达不到接近100%的要求,特别是高硫煤。当氧化率下降时,循环浆液中的可溶性亚硫酸盐浓度增大,严重时石膏中会出现较高含量的固体CaSO3 ·1/2H2O。浆液中可溶性亚硫酸盐浓度的增大将抑制CaCO3的溶解,使浆液中未反应的CaCO3浓度增大,从而导致石膏纯度下降。因此完全氧化不仅有利提高脱硫效率,而且是保证石膏质量的重要因素。通常氧化率每下降1.4%,石膏纯度将下降1%。表13132列出的分析结果能很好地说明上述观点。随着循环浆液中可溶性亚硫酸盐(I SO3)浓度的增大。浆液中全
亚硫酸盐(T SO3)、CaCO3、(T CO3)浓度增大,石膏副
产物中未反应的CaCO3含量也随之增加,石膏纯度下降。表13132 某电厂FGD系统吸收塔循环浆液和
石膏副产物对比分析结果

对于搅拌器和空气喷枪组合式强制氧化装置来说,造成氧化不充分的主要原因有:①布置的喷枪数不足;②氧化空气流量不足或各喷枪氧化空气流量不均衡;③搅拌器功率不足或氧化罐体直径过大,使氧化空气泡分布不均匀;④喷嘴浸没深度不足、氧化空气泡在浆液中停留时间过短;⑤吸收塔循环泵吸入浆液对罐体浆液流态的影响,使氧化空气泡分布不均,甚至大量被吸入循环泵中。
对于高硫煤的脱硫系统,强制氧化量较大,易发生氧化不完全的现象,国内有些高硫煤FGD系统已出现氧化不完全的情况。因此,在技术规范中,规定循环浆液中可溶性SO23-浓度低于1~2mmol/L,对于防止氧化不完全是有益的。
四、水力旋流分离器分离效率对石膏质量的影响
通常从吸收塔反应罐排出的浆液先送至第一级脱水装置———水力旋流分离器,浓缩至含固量(40~60)wt%然后再经真空皮带过滤机脱水。旋流器有浓缩浆液的作用,由于石灰石和飞灰较石膏结晶粒度小,容易分离在旋流器的溢流稀浆液中,降低了底流浓浆中石灰石和飞灰的含量,因而具有提高石膏质量的作用。旋流器溢流稀浆液中的石灰石返回吸收塔,有利于提高石灰石利用率。
分离效果较好的液力旋流器可提高石膏纯度1%左右。
第十四节 脱硫石膏处置
电厂在总体规划FGD系统时,脱硫固体副产物的处理方式与选择吸收剂类型一样,是首先要进行评价并初步做出决定。图13141示出了处理FGD副产物的一些常用的方法,其中有些方法是由于美国早年普遍采用抛弃法FGD工艺以及美国人少地广的具体国情而形成的,我国人多地少,经济实力有限,抛弃法形成的脱硫废渣的处理使电厂需要扩大征地,增大了处理废渣的费用,还可能带来严重的二次污染。因此,大规模抛弃法不适合我国国情。尽管如此,但部分脱硫副产物抛弃的方式在目前已建的FGD系统中仍有采用。因此,我们仍向大家介绍美国脱硫副产物废弃处理方法,目的是为大家提供可选择的方案。

图13141 处理脱硫副产品可供选择的方案
一、脱硫副产物处理流程及设备配置
脱硫副产物的处理可以分成4道工序,但并非每个FGD系统都必须具备这4道工序,这取决于脱硫副产物的最终处理方式。这4道工序是:一级脱水;二级脱水;为改普固体副产物物化特性的第三道处理工序和副产物的最终处理。表13 141列出了三种脱硫工艺的副产物各道处理工序可选择的设备。在确定脱硫副产物处理系统时,必须综合考虑每道工序的设备选择,如果最终生产商业石膏,可以有多种工序组合:
(1)第一级脱水选用水力旋流分离器,二级脱水采用卧式真空皮带过滤机,无需上面提到的第三道工序,最终外销处理副产物,这是目前国内采用最流行的流程。
(2)不设一级脱水,二级脱水采用卧式真空皮带过滤机,无需第三道工序,最终外销处理。这种工艺流程已出现在国内计划建设的FGD系统中。工序组合方式以及设备选择在很大程度上取决于副产品的最终处理方法、经济性、环保要求、设备占用空间及技术性能。
表13141 脱硫副产物处理设备的选择

图13142、图13143,是两个典型的废固副产
物处理系统,该系统可以处理抑制氧化、自然氧化或强制氧化FGD系统副产物。
二、一级脱水
一级脱水设备有3种组合形式;仅采用一级旋流分离器或浓缩池;两级旋流分离器;一级旋流分离与溢流澄清槽相组合。
一级脱水有如下作用:
(1)提高浆液固体物浓度,减少二级脱水设备处理浆液的体积。进入二级脱水设备的浆液含固量高,将有助于提高石膏滤饼的产出率。
(2)用分离出来的部分浓浆和稀浆来调整吸收塔反应罐浆液浓度,使之保持稳定。
(3)分离浆液中飞灰和未反应的细颗粒石灰石,降低底流浆液中飞灰和石灰石含量,这有助于提高石灰石利用率和石膏品质,有助于降低吸收塔循环浆液中惰性细颗粒物浓度。
(4)向废水处理系统排放一定量的废水,以控制吸收塔循环浆液中Cl-浓度。
(5)经一级脱水装置获得含量较低的回收水,用来制备石灰石浆液和返回吸收塔调节反应罐液位。
从反应罐输送至一级脱水设备的浆液含固量约是10wt%
~30wt%,一般取范围的下限10wt%~15wt%。经一级脱水后浆液可浓缩至40wt%~60wt%。图13142中的一级
脱水设备采用浓缩池,抑制氧化和自然氧化工艺适合采用浓缩池作一级脱水设备,浓缩池占地面积大,随着抛弃工艺的逐渐被淘汰,已很少有采用浓缩池的FGD系统。在图13 143中,一级脱水设备由水力旋流分离器和溢流澄清槽组成。水力旋流分离器能有效地从浆液中分离出较大的颗粒物,提高浆液浓度,非常适合强制氧化FGD工艺产出的硫酸钙固体物。反应罐排出浆液中未反应石灰石颗粒的平均粒径(d50)大约10~20μm,而脱硫副产物二水硫酸钙结晶的平均
粒径(d50)大约40μm左右,其中较大的可超过100μm,因
此,细颗粒的石灰石将富集在溢流液中并返回吸收塔反应罐,这样既提高了石灰石的利用率,又降低了成品石膏中石灰石含量。
脱硫副产物最终处理采取筑池填埋或湿石膏堆放方式的FGD系统,一般不设置一、二级脱水工序,从吸收塔排出的浆液直接送至废弃池或湿石膏堆放地。另外,也有一种强制氧化工艺的石灰石FGD系统,其反应罐液浓度控制在20%~30%,不设置一级脱水,从反应罐排出的浆液直接送至二级脱水设备。从理论上讲,即使反应罐浆液浓度为10wt%~
15wt%也可以省除一级脱水,但这会使二级脱水设备所要求的容量增大,造成总投资成本比有一级脱水设备的FGD系统还大。此外,如前所述,有些一级脱水设备还担负着调节反应罐浆液浓度和系统排污的作用。实际上,这种流程布置还是要设置一台容量较小的旋流分离器,承担调节装液浓度的作用,
这种系统的脱水工艺流程如图13144所示。其优点是对反应罐浆液浓度的调节和皮带脱水机的运行不相互干扰,可以较灵活地布置旋流分离器和皮带脱水机,无需从上向下依次布置旋流分离器和皮带脱水机,这样可降低皮带脱水机高度和给浆泵的压头。

图13142 典型的废固副产物处理系统(一)

图13143 典型的废固副产物处理系统(二)
一级脱水回收的工艺水送入回收水罐供FGD系统再使用。图13143中的浓缩池的溢流液可以直接进入回收水罐,而一级水力旋流器的溢流液由于仍含有5%左右的固体物,须经溢流澄清槽或二级水力旋流器处理后送入回收水罐。回收水大部分返回吸收塔,部分送往废水处理系统,这样可以减少回收水含固量,从而减少废水处理系统对废水固体物的处理量。
目前,有些FGD系统为简化一级脱水设备,不设置溢流澄清槽,设计两级旋液分离器,一级旋液分离器处理容量大,其溢流液全部进入回收水箱,从回收水箱抽取少量废水送入处
理容量较小的二级旋液分离器(又称为废水旋流分离器),以获得含固量较低的废水,送往废水处理车间。
系统补加水可根据情况加入回收水罐(见图13142、
图13143)或滤液回收水罐(见图1 3 14 5),或直
接加入吸收塔内。
经一级脱水设备浓缩的浆液流入底流储存罐,此罐起缓冲作用,使一、二级脱水设备能相互不影响地独立运行。一级脱水设备必须24h连续运行,当一级脱水设备故障停运,吸收塔液位偏高,需临时将反应罐排出浆液改送至灰浆池,作短时废

图13144 无一级脱水设备的FGD系统
1—吸收塔;2—排浆泵;3—皮带脱水机给浆泵;4—水力旋流分离器;5—回收水罐;6—废水泵;7—真空皮带脱水机;8—滤液接收器;
9—真空泵;10—冲洗水;11—滤液器;12—滤液泵
弃处理。为使二级脱水设备在一个稳定给料量下运行,一种典型设计给料罐大小的方法是使二级脱水设备每天工作一定时间(例如10h),根据给料罐的液位启停二级脱水设备,尽量减少对二级脱水设备运行的调整。另一种设计方法是,不考虑给料罐液位对二级脱水设备运行的影响,二级脱水设备连续运行,调整其转速,跟踪锅炉负荷,即真空皮带过滤机的给浆,跟踪吸收塔入口烟量以及烟气SO2浓度变化(相当石膏产出量)。真空皮带过滤机的走速随皮带上石膏饼厚度变化,维持石膏饼有一定的厚度,以保证石膏的脱水。
三、二级脱水
二级脱水设备的作用是降低脱硫副产物的含水量,便于运送和石膏再利用,或用作回填。如果废固体产物废弃排至废弃池或灰场,就不需要二级脱水设备。根据亚硫酸盐在FGD吸收塔内的不同氧化程度,二级脱水产物的含固量在45%~90%,抑制或自然氧化石灰FGD工艺的二级脱水产物含固量通常在上述范围的低限,石灰石基工艺生产出的商业等级的石膏通常在上述范围的高限。
有各种不同类型的二级脱水设备,应用得最多的是卧式真

图13145 采用二级水力旋流器处理废水的工艺流程
1—吸收塔;2—吸收塔循环泵;3—吸收塔出浆泵;4—石膏浆水力旋流分离站;5—废水旋流分离站;6—过滤机给料罐;7—一级脱水溢流液罐;8—皮带过滤机;9—工业水罐;10—回收水罐;11—真空泵;12—滤液回收罐;13—石膏仓;14—石灰石浆旋流分离器;15—球磨机;16—磨机循环浆罐;17—石灰石储仓;18—破碎机;19—石灰石浆储存罐
空皮带过滤机、转鼓真空过滤机和离心过滤机。无论亚硫酸盐的氧化程度如何,转鼓真空过滤机和离心过滤机都能用于处理FGD各种类型的副产物。美国湿式FGD多以抛弃法为主,大多采用转鼓式真空过滤机。卧式真空皮带过滤机更受生产商业品质石膏的FGD系统青睐。德国除燃用褐煤机组的FGD装置以及原东德的一些FGD系统生产的副产物采用回填煤矿的废坑道或作临时填埋处理外,其他石灰石FGD系统都采用强制氧化石膏工艺,产生的石膏均得到工业再利用。日本由于石膏矿床已几乎消耗完,石膏矿山被封闭,制造水泥的石膏主要来自FGD石膏以及化工行业的副产石膏。另外,日本天然石灰石极其丰富,纯度很高,脱硫石膏的品质高于天然石膏,再加上日
本国土狭窄,无法提供堆放FGD废渣的场地,所以,日本是采用石灰石商业石膏FGD工艺比例最高的国家。因此,德国和日本的FGD系统大多采用真空皮带过滤机。真空皮带过滤机在国内电厂投入商业运行的系统中也应用得很成功,故障率低,维修工作量少。因此,国内已建或设计建设中的电厂湿法石灰石FGD装置几乎都采用这类过滤机。
对于一个特定的FGD系统,如何选择最佳脱水设备,主要取决于FGD工艺类型、脱硫副产物的特性以及副产物最终用户的质量要求,这种质量要求除了纯度外,含水量和可溶性氯化物含量也是重要的指标。
真空皮带过滤机的脱水性优于转鼓真空过滤机,前者生产的
石膏饼含水量8%~12%,后者15%~20%,而且后者冲洗石膏饼的效果要差些;但后者投资成本明显低于前者和离心过滤机。
选择真空过滤机还是离心过滤机仍是个有争议的问题。就全世界现有的FGD装置而言,脱水设备选用的类型有一种明显的倾向。抑制氧化FGD多选用离心过滤机,在一些新建的强制氧化系统中,真空过滤机和离心过滤机都有采用。
对一个特定的石膏脱水工艺来说,直空皮带过滤机和立式离心过滤机的基本投资可能很接近,虽然经常有报道说真空皮带过滤机的能耗比离心过滤机低,但如果包括所有辅助设备的能耗进行比较,真空皮带过滤机的能耗优势就大为降低了。
离心过滤机的主要优点是:脱水性能高,能获得较干的产品,离心机的布置更紧凑,需要的辅助设备较少,不需要真空过滤机所需要的诸如真空泵、真空罐和工艺浆池等辅助设备。因此,离心机降低了辅助设备的费用,减少了占用的空间和维修费用。另外,真空过滤机的真空泵对密封水水质要求较高,过滤机滤布需定期更换,离心机的维修费用低于真空过滤机。
但是,真空过滤在有些方面优于离心机,除了转鼓过滤机投资成本低外,真空过滤机可连续运行,运转速度较离心机低得多,这使得过滤机磨损和振动之类的故障较少,运行中发生故障易于发现。另外,离心机滤液含固量通常比真空过滤机的高。真空皮带过滤机除了机架和冲洗水管外,大多数部件用耐腐蚀材料制作或衬覆,几乎不存在腐蚀问题。
美国电力研究协会曾做过一项有关比较卧式真空皮带过滤机、转鼓真空过滤机以及立式和卧式离心机设备选择的试验。
将含Cl-5000mg/L和40000mg/L的石膏浆液,先经浓缩池或
水力旋流分离器脱水至含固量40wt%~60wt%,二级脱水的要求是产生的石膏饼含固量85%,并将石膏饼冲洗到含Cl-200×10-6(干基)。试验结果表明,真空过滤机和立式离心机都能满足七述两项要求,而立式离心机的技术性能最好,生产出的石膏饼含固量达90%。但转鼓过滤机的工程费用最低,卧式离心机在进行石膏饼冲洗时达不到石膏饼含固量85%的要求。
不管采用何种类型的二级脱水设备,一般要平行地安装多台脱水设备,以保持一定的备用容量。其设计原则是每套石膏脱水系统宜设置2~3台石膏脱水机。如设置2台,单台设备出力按设计工况下石膏产量的75%选择,且不小于50%校核工况
下的石膏产量。如设置3台,单台容量按50%考虑。对于多炉合用一套石膏脱水系统时,宜设置N+1台石膏脱水机,N台运行,一台备用。
如果二级脱水设备没有备用容量,当设备故障停运时,应有将二级脱水设备浆液废弃的输送管线。
二级脱水的回收水一般送至供FGD系统再利用,如果回收水含有较多的固体副产物,回收水需再一次脱水。
四、脱硫固体副产物第三道处理工序
来自二级脱水的固体副产物有两种,一种是用抛弃法生产出来的含固量40%~71%泥浆状固体副产物;另一种是具有商业价值的含水量约8%~12%的脱硫石膏。第三道处理工序是处理来自二级脱水的这两种固体副产物,目的是改善副产物的物理、化学特性。
在对二级脱水后的废弃固体副产物的处理中,主要改善的物化特性是:①装运特性,使废弃固体产物便于装卸、运输;②承压强度,当废弃固体产物作回填处理时,副产物具有一定的承载能力;③浸出液的特性,当副产物作填埋,堆放处理时,降低其透水性以及改变浸出液的化学特性。对商业品质脱硫石膏的处理是指石膏造粒或烘干,以满足石膏最终用户的使用要求。
1.对二级脱水后废弃固体副产物的稳定化和固定化处理在二级脱水废弃固体副产物的第三道处理工序中,最常见
的做法是对废弃副产物进行稳定化和固定化处理。稳定化处理是将副产物与飞灰混合,这种混合物便于装卸、运输,可以提高废弃副产物的承压强度和降低废副产物的透水性。飞灰与废副产物混合的重量比通常是1∶3~1∶1。固化处理类似稳定化处理,所不同的是向副产物与飞灰的混合物中加入混合物重量1%~3%的石灰,激发飞灰活性,使亚硫酸钙和硫酸钙参与的磺化凝固反应,使混合物具有水凝固性,能逐渐产生固化强度,从而提高混合物抗压强度,降低压实后混合物的透水性,抑制飞灰、脱硫废渣中的重金属溶解渗出,减少亚硫酸盐造成的二次污染。可以用泥浆搅拌机混合脱硫废弃副产物、飞灰和石灰,搅混均匀混合物在临时堆放区停留数小时,使混合物发生初期化学反应。这种固定化处理的产物在美国和日本称为烟灰材料,图13146是生产这种烟灰材料的工艺流程。这种材料的

图13146 脱硫废弃固体副产物固定处理流程
1—吸收塔;2—沉淀槽;3—脱硫泥浆罐;4—真空泵;5—滤液收集罐;6—滚筒式真空过滤机;7—飞灰仓;
典型物理特性是,4周后单轴抗压强度为10~50kg/cm2,压
实后的质量轻,干燥密度1.2~1.4t/m3,透水率10-5~10-7,
处于黏土与混凝土之间。这是一种符合美国和日本土壤污染防止条例的回填材料,其主要用途是:
(1)公路、铁路路基或道路建设用回填材料。(2)用作工业区、公园、绿化区等的填土材料。(3)堤、坝隔水性材料。
(4)作为隔水性的内衬材料。
(5)挡土墙、桥墩、码头等的内部填充材料。(6)建筑用轻型板块的骨料。
(7)地表土质松软地区的地表铺垫材料。
以上用途已有多年历史,近年来,这种固化处理材料用来减缓地面下沉和减少地下矿井排放酸水已显成效。
2.脱硫石膏的造粗和烘干处理
当电厂FGD系统生产商业品质的石膏时,通常不设第三道处理工序,直接外销。但有的FGD系统将商业石膏造粒或
加热烘干后外销,虽然一些石膏副产品用户(主要是水泥工业)更喜欢采用粒状或烘干石膏,这样便于装运、储存和计量,但石膏造粒或干燥后的价格较高,这成为脱硫石膏不能广泛应用于水泥生产的原因之一。
国内第1套用于烘干脱硫石膏的装置在山西太原第一热电厂投入使用,其烘干流程见图13147(a),脱硫石膏经烘干、炒制,以半水石膏外售,设计生产能力为5×104t/a。该烘干工艺用煤作燃料,产生的热烟气经除尘器4进入烘干筒,松散状脱硫石膏经皮带送料机8、螺旋给料机7送入烘干筒,在烘干筒中粉状石膏随气流上升,烘干并脱水,结块的石膏落入打散机6,打碎后再随气流上升,烘干后的石膏大部被旋风分离器10收集,其余部分经风机11由布袋除尘器12收集。烘干后的成品经螺旋送料机9、斗式提升机14,储存在成品料仓15中。该工艺选用较廉价的煤作燃料,热烟气中未除尽的飞灰,对石膏白度有些影响,但用作纸面石膏板或石膏砌块的原料完全满足要求。

1—送风机;2—热风锅炉;3—调节阀;4—除尘器;5—进风阀;6—打散机;7—螺旋给料机;8—皮带送料机;9—螺旋送料机;
1—送风机;2—燃烧器;3—炒锅;4—料仓;5—稳定器;
6—旋风分离器;7—排风机;8—布袋除尘器;
10—旋风分离器;11—循环风机;12—布袋除尘器;13—循环风机;14—斗式提升机;15—石膏料仓
9—循环风机;10—皮带送料机;
11—循环风机;12—料仓
图13147 太原一热和北京一热脱硫石膏烘干流程
北京第一热电厂于1998年引进国外技术建造了一套集FGD、石膏烘干、脱硫石膏砌块生产于一体的装置,石膏烘干装置的产品为半水石膏,设计生产能力为5×104t/a,工艺流
程见流程图13147(b),其原理与图13147(a)
所示的基本相同,所不同的是北京一热的烘干装置采用重油作燃料,石膏白度好,产出的石膏粉可作粉刷石膏。另外,从旋风分离器6出来的气体少部分经布袋除尘后排空,大部分经循环风机9、11返回炒锅3,由于热空气采用了闭式循环方式,可减少燃料消耗。
重庆发电厂在引进两套机组脱硫装置的同时,建成了一套年产1×105t脱硫石膏造粒车间。石膏造粒的基本原理是,将二级脱水后的石膏副产物送入造粒机内,加入黏结剂,在加压和加热的情况下,石膏形成硬颗粒,装运前将未固化的石膏颗粒送入临时储存仓中硬化。
还有多种类型的工业加热烘干机也可以用来降低石膏副产物的含水量,使含水量低于5%。
五、脱硫废弃副产物最终处置方法
处理脱硫废弃副产物需占用大量的土地,不适合我国的国情。因此我国电厂湿法石灰石FGD系统大多数采用强制氧化工艺,最终产品为可工业利用的石膏,但由于脱硫石膏尚未被广泛应用,部分石膏以浆液的形式被废弃。另外,国内有相当一部分电厂将未经处理的脱硫废水直接排向灰场、还有些电厂将销售不了的石膏直接倒入未经防渗处理的坑内作回填处理,这些都有可能对周围环境造成不良影响。
本小节主要介绍国外发电厂FGD系统处置脱硫废弃副产物通常采用的方法,将有助于我们正确选择处理脱硫废弃副产物的处理方式。
处置FGD系统产生的废弃副产物的方式必须对周围环境不造成危害,在美国,最终处置脱硫废弃副产物的方式主要有下述三种。
1.筑池湿排填埋
图1314 8示出了一个典型的废弃池的平面和剖面
图。电厂根据现场附近的地势建一个或多个废弃池,通过管道将废弃浆液排入池中,由于废弃浆液中的固体物在进入废弃池后会很快在靠近排放口的地方沉淀出来,因此排放口应设计成移动式,以便有效地利用废弃池的整个库容。废弃池的出水门能控制废弃池水位,因为随着废弃固体物填入池底,溢流水位随之提高。为了防止污染地下水,在池底应敷设防渗层,可以用黏土或人造防渗材料作防渗层。有些电厂用抗渗黏土层作废弃池的基础,不另外再加铺垫层。当采用人造衬层时,必须安装浸出液收集设施,以防浸出液进入地下水层。在美国,即使采用了防渗层和浸出液收集设施,有关管理机构可能还要求设置一个地下水监测井,用来监视废弃池对地下水质的影响。从废弃池回收的水既可以返回废弃池任其蒸发,也可以供FGD系统再使用。废弃池填满后,在废弃物上铺防渗覆盖层,防止雨水经池中浸出。在多数情况下,这种方式用来填埋抗压强度很低的固体物,这种废弃物很少有再利用的商业价值。

图13148 脱硫废浆液废弃池
2.地面堆放填埋处理
填埋是美国处置FGD固体副产物常采用的一种方法,固体废物中约80%仍用填埋方式处置。固体副产物地面堆放场地的典型剖面图如图13149所示。用卡车将固体副产物送至堆放现场摊开,每次铺垫厚度不超过600mm,然后充分压实。每个堆放区堆放前要铺设防渗面层。地面堆放位置比废弃池填埋要灵活些,地面堆放宜采取多个分隔开来的小堆放区进行堆放,每个堆放区不宜过大,尽可能减少雨水冲刷。由于

图13149 脱硫固体废弃副产物地面堆放填料处理
地面堆放的固体副产物产生一定强度,因此可供今后各种可能的商业用途或加工再利用,但更多的是用作回填矿山废弃的坑井、铺垫路基等。
像废弃池填埋一样,地面堆放也必须有衬层和收集浸出液的设施。经固化处理的脱硫副产物适合用作衬砌材料,有些电厂就是用经固化处理的脱硫副产物来封闭经稳定化处理的副产物或没有经过第三道工序处理的固体物。另外,往往将收集的浸出液和地面雨水喷洒在回填堆上,以防止扬尘,使堆放的固体物更密实,同时让收集的废水蒸发。
在美国,由于受地形、地下水深度、土质条件或其他特定因素的限制而不宜采用废弃池填埋的地方,往往采用就地地面堆放。地面堆放处置的最大缺点是必须有一、二次脱水设备,堆放占地面积大,并可能产生扬尘。
3.湿石膏堆放
在美国,湿石膏堆放是处置FGD副产物较新的一种方法。多年来,磷酸盐工业废料处理就一直采用类似的做法。湿石膏堆放的典型剖面图如图131410所示。类似废弃池的做法,将吸收塔排放的浆液送入沉淀区,待固体副产物沉淀出来后,将澄清水引入溢流池中,回收水返回FGD系统重新使用。定期将沉积的固体物挖出来填高四周的围堰。像废弃池填埋一样,湿石膏堆放可以筑成单个或多个堆放池。停止堆放后,雨水会从料堆中浸出,因此要铺防水面层。这种石膏堆的抗压强度较低,封闭后很少有商业价值或加工再利用。

图131410 湿石膏堆放
第十五节 FGD废水处理系统的设计优化
一、概述
在湿式石灰石/石膏FGD工艺中,不可避免地要产生一定量的废水,主要是要排放吸收塔浆液中累积的Cl-离子和粉尘。因为氯化物对工艺性能有负面影响,而且还影响耐蚀合金材料的选择,为保证商用石膏的纯度和系统浆液正常物化性质,需要对系统内的微细粉尘浓度进行控制。另外,排放废水还可降低浆液中金属离子的浓度,因为某些金属离子的累积最终会影响FGD系统的性能。FGD废水的水量和水质,与脱硫工艺系统、燃料成分及吸收剂等多种因素有关,因此不存在典型的FGD废水水质,表13151是《火电厂石灰石—石膏
湿法FGD废水水质控制指标》(DL/T997—2006)中规定的
FGD废水处理系统出口污染物最高允许排放浓度。对于有FGD废水产生的发电厂,在厂区废水排放口增加硫酸盐浓度监测项目。
表13151 FGD废水处理系统出口要检测的
项目和最高允许排放浓度值

注 化学需氧量的数值要扣除随工艺水带入系统的部分。
二、FGD废水处理系统的一般设计原则
(1)脱硫废水处理方式应结合全厂水务管理、电厂除灰方式及排放条件等综合因素确定。当发电厂采用干除灰系统时,脱硫废水应经处理达到复用水水质要求后复用,也可经集中或单独处理后达标排放;当发电厂采用水力除灰系统且灰水回收时,脱硫废水可作为冲灰系统补充水排至灰场。
(2)处理合格后的废水应根据水质、水量情况及用水要求,按照全厂水务管理的统一规划综合利用或排放。处理后排放的废水水质应满足《污水综合排放标准》(GB8978—2002)和建厂所在地区的有关污水排放标准。
(3)脱硫废水处理工艺系统应根据废水水质、回用或排放水质要求、设备和药品供应条件等选择,宜采用中和沉淀、混凝澄清等去除水中重金属和悬浮物的措施以及pH值调整措施。当脱硫废水COD超标时还应有降低COD的措施,并应同时满足《火力发电厂废水治理设计技术规范》(DL/T5046—
2006)的相关要求。
(4)脱硫废水系统出力按脱硫工艺废水排放量确定,系统宜采用连续自动运行,处理过程宜采用重力自流。泵类设备宜设备用,废水箱应装设搅拌装置。脱硫废水处理系统的加药和污泥脱水等辅助设备可视工程情况与电厂工业废水处理系统合用。
(5)脱硫废水处理系统的设备、管道和阀门等应根据接触介质情况选择防腐材料。
(6)脱硫废水排放处理系统可以单独设置,也可经预处理去除重金属、氯离子等再排入电厂废水处理系统进行处理,但不得直接混入电厂废水稀释排放。
(7)脱硫废水的处理措施及工艺选择,应符合项目环境影响报告书审批意见的要求。
(8)脱硫废水中的重金属、悬浮物和氯离子可采用中和、化学沉淀、混凝、离子交换等工艺去除。对废水含盐量有特殊要求的,应采取降低含盐量的工艺措施。
(9)脱硫废水处理系统应采取防腐措施,适应处理介质的特殊要求。
(10)处理后的废水,可按照全厂废水管理的统一规划进行回用或排放,处理后排放的废水水质应达到 GB8978—
2002、DL/T997—2006和建厂所在地区的地方排放标准要求。
三、FGD废水处理方法
国内外采用的FGD废水处理方法,综合起来主要有如下
几种:
(1)FGD废水与飞灰混合。用废水来湿化飞灰,或者FGD废水与经浓缩的副产物石膏混合后排至电厂灰场堆放,飞灰本身的CaO含量可作为黏合剂固化脱硫石膏。我国少数电厂是将废水混入石膏浆液中,排放至湿灰场堆放储存,废水中的重金属与碱性灰水作用,在灰厂发生沉淀。
(2)喷入烟道蒸发。FGD废水在电除尘器和空气预热器之间的烟道中完全蒸发,所含固态物与飞灰一起收集处置。例如,美国和日本的一些脱硫系统中,在电除尘器前设置废水蒸发系统,达到工艺基本无废水排放。在德国,燃煤电厂的FGD废水若不经化学处理,也必须蒸干。
(3)废水蒸发池蒸发。当电厂所处地区气候干燥,要求电厂废水零排放时,可排入蒸发池,利用太阳能蒸发废水。
(4)经废水处理系统处理后排放。针对FGD废水的水质特点,为满足国家规定的废水排放标准,需采用专门的废水处理系统。典型的FGD废水处理流程如图13151所示,主要包括4个步骤:废水中和、重金属沉淀、凝聚和絮凝、浓缩澄清。通过加碱中和FGD废水,并使废水中的大部分重金属形成沉淀物,加入絮凝剂使沉淀物浓缩成污泥,污泥脱水后被送至灰场等堆放。废水悬浮物达标后直接外排。

图13151 典型的FGD废水处理系统流程
由于对排放的废水有化学需氧量COD限制,如果废水中亚硫酸盐浓度超过150mg/L,为了降低COD,废水处理系统中还有氧化这一步骤。氧化工序是将空气鼓入废水中,使亚硫酸盐氧化成硫酸盐。如果FGD采用强制氧化工艺,氧化较彻底,可以不需要此工序。在此步骤中,废水在氧化罐中应有足够的停留时间,以使所有的亚硫酸盐氧化。如果废水中有氮-硫有机化合物,采用这种氧化工序不一定能达到废水排放COD标准,出现这种情况时,需要在澄清和浓缩池下游侧设置专门降低COD的设备,即氮-硫分解罐和曝气罐。在分解罐中将废水pH值调至1.0~1.5,加入NaNO3并加热到大约50℃,然后,将废水引入曝气罐,去除分解过程中产生的氮,再经清水池用NaOH溶液调整pH值后进入热交换器,冷却废水至一定温度,排放或回收利用。
(5)废水处理后的废物处置方法。
除去废水中污染物后,最终都会产生两种物质,一种是相对较清洁的水,在有些情况下可以再循环使用;另一种是浓缩废物。对于这种废物必须采用不危害环境的方式进行处置。这种废物可能是液体或湿淤泥,沉淀金属离子产生的淤泥可能只含有50%的固体物,采用板框压滤机或离心过滤
机,可使淤泥脱水至含固率75%~80%;然后通常作填埋处理。也有的电厂将这种淤泥或经脱水处理的淤泥在煤棚中与煤混合,再送入锅炉中燃烧,使淤泥中的金属物最终进入灰渣和飞灰中。
对浓缩废液也需要处理成干态,这可以采用喷雾干燥或采用结晶的方法来除去水分。喷雾干燥即前面谈到的将废水喷入烟道的方法。结晶法是使废液中的溶解盐结晶析出,再离心过滤,这样可以得到较干、较纯的固体物,这种固体物有销售价值。但由于费用较高,电厂通常不采用结晶法。
另外,可以将湿废料与生石灰、水泥或飞灰混合,进行稳定化处理。对废物进行稳定化处理的优点是产生出一种无危害的废料,与废弃有害废物相比可以降低废弃费用,减少短期和长期的环境责任。对特殊的废物则需进行试验,以确定选择哪种添加剂才能形成稳定的废物。
四、FGD废水系统的优化实例
1.FGD废水系统运行问题
这里以某发电有限责任公司2×600MW机组FGD废水处理系统为例,来说明系统设计优化和改进情况。电厂FGD废水处理系统为典型的三联箱系统,运行中出现了下述问题:
(1)废水中固体物质含量超标。脱硫废水处理系统设计废水中的固体物质浓度(wt%)为1%,由于吸收浆液受到粉煤灰、外购石灰粉中杂质等诸多因素的影响,浆液本身品质不佳,加上脱硫浆液一、二级旋流效果不佳,造成脱硫废水中固体物质的实际浓度在5%~8%之间,导致脱硫废水整个系统长期超负荷运转,废水调节曝气池曝气管道频繁堵塞,池底经常积泥;中和箱、沉降箱、絮凝箱搅拌器速度和强度与脱硫废水中的固体物质浓度不匹配,造成中和箱、沉降箱、絮凝箱底部积泥严重,流水不畅,排污管堵塞。此外,部分泵出、入口管道未设置冲洗水管,设备停运后没有冲洗,致使浆液沉积。
(2)澄清池结构不合理。脱硫废水在经过三联箱后自流至澄清池,通过布置在澄清池中下部的布水堰进入污泥区,再自下而上通过蜂窝斜管达到澄清分离的目的。澄清池采用周边进水和周边出水的形式,这种结构的不合理之处在于布水堰、蜂窝斜管都靠近污泥区,很容易被浆液覆盖。布水堰淤积石膏后,由于进水不畅,浆液在澄清池内很难均匀分布。此外,蜂窝斜管被淤积石膏压垮,严重影响沉淀、分离效果,导致悬浮物严重超标、出水浑浊。再者,澄清池内清水区、污泥区比例失衡,清水区空间较大,污泥区空间相对偏小。
(3)运行调整方式不合理。加药量与实际废水浓度不匹配,脱硫废水中的沉淀物沉降、絮凝没有达到预期效果;板框压滤机压泥过程中产生的清水又回流到废水调节池,增加了系统负荷;中和箱未设置pH值计,靠人工检测致使调节滞后,浪费药剂;板框压滤机故障频繁,板框压滤机污泥含水率偏高,压缩空气正吹无效,泥饼黏结滤布严重,造成不能自动卸泥,增加了人工清扫的难度。同时,污泥螺杆泵在向板框压滤机输送泥浆过程中泵压经常过载,导致该泵跳闸频繁,泥饼厚度达不到要求。
2.FGD废水系统的优化改进
为此,该厂采用了相应的措施,对工艺流程及运行方式进行了下述优化改进。
(1)原有废水旋流器改造成高效废水旋流器,定期更换石膏旋流器喷嘴,自上而下提高浆液一、二级旋流系统的旋流水平,尽量降低脱硫废水中固体浓度。
(2)设置初沉池。脱硫废水中的悬浮物主要由硅、铝化合
物组成,其本身沉降性、浓缩性较好,直接沉淀2h左右即可去除。因此,在脱硫废水进入废水调节曝气池前设置初沉池,对废水中的大颗粒悬浮物进行固液分离,浓缩的泥浆由初沉池附带的自动刮泥装置清除,再通过底部设置的污泥输送管道输送至板框式压滤机压滤制饼,上清液则自流至废水调节曝气池。
脱硫废水进水管道设置为两路:一路引至初沉池,一路引至废水调节曝气池。正常运行状态下,脱硫废水进入初沉池,进行初步分离后再流入废水调节曝气池。当初沉池处于事故或检修状态时,脱硫废水直接进入废水调节曝气池。增设初沉池后大幅减小了脱硫废水处理系统后续工序的负荷。
(3)提高中和池、沉淀池、絮凝池搅拌器转速,中和箱、沉降箱、絮凝箱中的搅拌器主要起加强反应的作用,由于脱硫废水来水的悬浮物含量很高,且悬浮物的沉降性能良好,使得脱硫废水中的悬浮物极易沉降在箱体中,特别是加入药剂后很快形成较大的絮凝颗粒沉降下来。此外,当单台机组运行时废水在各反应箱中的停留时间均在2~3h,甚至更长,这大大增加了悬浮物质沉到箱体的可能性。所以,在不将絮凝大颗粒打碎的前提下,使搅拌器处于较高的转速,以防止中和、沉淀、絮凝箱底固体物质沉积。为此将原设计的搅拌机转速提高,加大搅拌强度,很好地解决了箱底积泥的现象。
(4)增设废水调节曝气池机械搅拌器,原气力搅拌器在对废水搅拌的同时,使空气与水充分接触,促使水中亚硫酸盐进一步氧化,有利于降低系统出水的COD值。由于曝气管道极易堵塞,可靠性较低,因此,废水调节曝气池在保留曝气管道的基础上,增加了机械搅拌装置,以防止固体沉淀。
(5)澄清池改造成中心筒进水、周边出水形式。改造后更加有利于澄清池的污泥浓缩和澄清。具体做法是:取消原设计布置于四周的布水堰,设置中心筒,所处理的废水从中心筒内进入污泥区,将斜管支撑上移1m左右,并采用高强度的蜂窝斜管。这样不但增加了斜管澄清面积,扩大了污泥区,使废水有足够的澄清空间和时间,确保出水悬浮物达标。同时,在澄清池污泥区每隔一段距离布置监测视镜,以便监视泥位,及时排泥。
(6)调整加药量。根据各种重金属形成沉淀所需的pH值,同时考虑到F-的沉淀反应以及废水排放允许的pH值为6~9,最终选取中和沉降pH值为9.0,石灰的最佳加药量为1300~
1400mg/L,运行过程中发现,脱硫废水在加入Ca(OH)2后沉
降性很好,这是因为Ca(OH)2有阳离子混凝剂的特性。为此,
所需的FeClSO4、和PAM(Polyacrylamide,聚丙烯酰胺)量均较少。最终选取PAM配制为0.1wt%,加入体积比为50mL/m3;FeClSO4配制为10wt%,加入体积比为0.5L/m3。
脱硫废水处理工艺中加入有机硫化物TMTl5,主要作用是进一步强化对金属离子的去除能力,特别是对镐和汞。由于废水中的镐和汞含量较低,所以最终确认 TMT15配制为
10wt%,加入体积比为350mL/m3,处理后脱硫废水中镉、汞
和硫化物的含量均满足国家标准的要求。
(7)改善压滤机功能。一般情况下,板框压滤机每天运行4~6次,每次运行2h左右,每小时产生的水约7m3,每天可产生清水70m3左右。原来的设计是将这部分水回流到废液收集池,导致对其进行二次处理,既浪费药品又浪费能源。对板框压滤机出水进行化验,其水质完全符合排放标准,故将其直接引到清水池回用。
实践证明,板框压滤机出泥时仅靠压缩空气正吹扫是不够的,还需要增加压缩空气反吹扫,以完全将泥饼中的水分去
除,避免泥饼对滤布的黏结。在板框压滤机自身不能保持工作压力时,需要开启出口管路上的回流管路,以延长板框压滤机的压泥时间,使泥饼厚度能够满足要求。
(8)增加在线检测仪器仪表。在中和箱设置pH值在线调节系统,通过石灰乳加药装置的启停来控制石灰乳的投加量,以维持中和箱中的pH值在8.5~9.5之间。在清水箱中也设置pH值在线调节系统,通过添加盐酸将出水pH值控制在6~9之间,若出水pH值不达标,则出水回流至清水箱再次调节,直到达标为止。此外,在清水箱设置浊度计和COD在线监控设备,若出水浑浊度或COD含量超标,则回流到废水调节曝气池中再次处理,直到达标为止。初沉池、澄清池设置泥位计,当初沉池或澄清池底部污泥积累到设定高度时,启动污泥输送泵排泥。
(9)脱硫废水处理设备材质一般设计主张用塑料,不用金属,但是脱硫废水固体颗粒物较大,对泵壳、叶轮等过流部件磨损较为严重。实践证明,塑料泵磨损泄漏严重,不适宜脱硫废水使用,需要采用耐磨损、耐腐蚀的金属泵。此外,调节池提升泵、板框压滤机及污泥输送泵的前、后须增设压力冲洗水管道,中和箱、沉降箱、絮凝箱、澄清池底部排泥管上也须增设压力冲洗水管,防止泵和管道堵塞。优化改造后,脱硫废水处理系统已正常投入并能稳定运行,各项排放指标均符合标准要求。改造方案也已在多个脱硫废水处
理工程中得到应用且效果良好,可为同类型火力发电厂脱硫废水处理系统所借鉴。
第十六节 公用系统的设计要点
FGD公用系统一般包括工艺水系统、仪用/杂用压缩空气、事故浆液排放系统、生活水及暖通消防等。
一、工艺水
FGD系统工艺水通常从电厂循环水系统接入1个工艺水箱,然后由工艺水泵送至FGD系统各用水点,工艺水主要用水有:
(1)FGD系统补充用水,主要有吸收塔除雾器冲洗水、球磨机入口补充水、再循环水箱补充水或石灰石粉制浆用水等。
(2)管路和泵的冲洗用水。如真空皮带脱水机滤布、滤饼冲洗,GGH的高/低压冲洗水,设备冷却水,所有浆液输送设备、输送管路、储存箱的冲洗水,pH值计、密度计、液位计、各取样点冲洗水及废水系统用水等。
(3)各类水泵和浆液泵的密封水。
工艺水系统一般设置工艺水泵3台,2运1备,除雾器冲洗水设有单独的冲洗水泵,每个吸收塔独立设置2台泵,如图
13161所示。

图13161 某电厂FGD除雾器冲洗水系统
根据具体情况,闭式循环冷却水一般从炉后闭式循环冷却水管接出供增压风机、氧化风机、球磨机等大设备冷却用水,其回水回收至炉后闭式循环冷却水回水管。
二、仪用/杂用压缩空气
FGD系统的阀门控制方式为电动或气动,供仪表吹扫的仪用空气和供设备检修的杂用空气可由专设的FGD系统仪用/杂用空气压缩机提供,或直接从主厂房接入FGD系统。GGH吹扫用压缩空气一般由专设的GGH空气压缩机提供,若采用蒸汽吹灰,则蒸汽一般取自锅炉辅助蒸汽母管,或直接取自再热蒸汽冷段,经调压后用于GGH吹灰。某电厂FGD系统仪
用/杂用空气系统如图13162所示。
三、事故浆液排放系统
事故浆液排放系统主要包括事故浆液箱及搅拌器、事故浆液返回泵、排水坑、排水坑搅拌器、排水坑泵等。在FGD系统正常运行、设备检修及日常清洗维护中都将产生一定的排出物,如运行时各设备冲洗水、管道冲洗水、吸收塔区域冲洗水等,排出物首先集中到各自相应的排水坑内(吸收塔区、脱水区、制浆区等),排水坑内浆液集到一定量后,排水坑泵就将坑内液体输送到事故浆液池中。在FGD系统各区域的排水坑均进行防腐处理并配有搅拌器,以防止沉积。
程一致。

图13162 某电厂FGD系统仪用/杂用空气系统
通常在FGD系统内设置一个公用的事故浆液箱,用于储存吸收塔检修、停运或事故情况下排放的浆液,事故浆液箱内配有搅拌器,防止浆液发生沉淀。吸收塔浆液可通过石膏浆液排出泵输送到事故浆液箱中,反之,箱中浆液也可以通过事故浆液返回泵送回到各吸收塔。
四、生活水及暖通消防
FGD系统内生活污水是收集盥洗间卫生设施等排放的污水,自流排放至厂区污水排放系统中,雨水排水系统是收集不含浆液和任何化学物质的雨水,纳入厂区污水排放系统中。另外暖通、消防等各系统按规定设计。
五、公用系统设计优化
(1)FGD工艺水、冷却水、仪用压缩空气等的供应量要足够,不能按理论计算,要现场确定,工艺水箱的容量至少满足设计工况2h以上的消耗量。
(2)除雾器冲洗水泵宜单独设置,并有压力、流量在操作员站显示。
(3)仪用压缩空气、杂用压缩空气可以和主机公用,但宜设置独立的储气罐,尽量减少相互间的影响。FGD系统内部各用水、用气点等要能独立隔绝,以方便检修。
(4)应考虑浆液冲洗、外排的紧急措施。(5)在寒冷地区,采取防冻措施。
第十七节 FGD电气系统设计要点
一、FGD电气系统的一般设计原则
FGD电气系统为FGD系统的正常运行提供动力,它一般由高压电源(6kV)、低压电源(0.4kV)、直流系统、交流保安电源和交流不停电电源(UPS)组成。FGD电气系统的设计应从电厂全局出发,统筹兼顾,按照脱硫装置的规模、特点,合理确定设计方案,达到安全、经济、可靠和运行维护方便的要求。电气设备选型应力求安全可靠、经济适用、技术先进、符合国情,积极慎重的采用和推广经过鉴定的新技术、新产品。电气系统的一般设计原则要符合《火力发电厂烟气脱硫
设计技术规程》(DL/T5196—2004)要求。
1.供电系统
(1)脱硫装置高压、低压厂用电电压等级应与电厂主体工程一致。
(2)脱硫装置厂用电系统中性点接地方式应与电厂主体工
(3)脱硫工作电源的引接:
1)脱硫高压工作电源可设脱硫高压变压器,从发电机出口引接,也可直接从高压厂用工作母线引接。
2)脱硫装置与电厂主体工程同期建设时,脱硫高压工作电源宜由高压厂用工作母线引接,当技术经济比较合理时,也可增设高压变压器。
3)脱硫装置为预留,宜采用高压厂用工作变压器预留容量的方式。
4)已建电厂加装烟气脱硫装置时,如果高压厂用工作变压器有足够备用容量,且原有高压厂用开关设备的短路动热稳定值及电动机启动电压水平均满足要求时,脱硫高压工作电源应从高压厂用工作母线引接,否则,应设高压变压器。
5)脱硫低压工作电源应单设脱硫低压工作变压器供电。(4)脱硫高压负荷可设脱硫高压母线段供电,也可直接接
于高压厂用工作母线段。当设脱硫高压母线段时,每炉宜设1段,并设置备用电源。每台炉宜设1段脱硫低压母线。
(5)脱硫高压备用电源宜由电厂启动/备用变压器低压侧引接。当脱硫高压工作电源由高压厂用工作母线引接时,其备用电源也可由另一高压厂用工作母线引接。
(6)除满足上述要求外,其余均应符合《火力发电厂厂用
电设计技术规定》(DL/T5153—2002)中的有关规定。
2.直流系统
(1)新建电厂同期建设烟气脱硫装置时,脱硫装置直流负荷宜由机组直流系统供电。当脱硫装置布置离主厂房较远时,也可设置脱硫直流系统。
(2)脱硫装置为预留时,机组直流系统不考虑脱硫负荷。(3)已建电厂加装烟气脱硫装置时,宜装设脱硫直流系
统,向脱硫装置直流负荷供电。
(4)直流系统的设置应符合相关设计标准规定。3.交流保安电源和交流不停电电源(UPS)
(1)200MW及以上机组配套的脱硫装置宜设单独的交流保安母线段。当主厂房交流保安电源的容量足够时,脱硫交流保安母线段宜由主厂房交流保安电源供电,否则,宜由单独设置的能快速启动的柴油发电机供电。其他要求应符合DL/T
5153—2002中的有关规定。
(2)新建电厂同期建设烟气脱硫装置时,脱硫装置交流不停电负荷宜由机组UPS系统供电。当脱硫装置布置离主厂房较远时,也可单独设置UPS。
(3)脱硫装置为预留时,机组UPS系统不考虑向脱硫负荷供电。
(4)已建电厂加装烟气脱硫装置时,宜单独设置 UPS,向脱硫岛装置不停电负荷供电。
(5)UPS宜采用静态逆变装置。其他要求应符合《火力
发电厂、变电所二次接线设计技术规程》(DL/T5136—2001)
中的有关规定。
4.二次线
(1)脱硫电气系统宜在脱硫控制室控制,并纳入 DCS系统。
(2)脱硫电气系统控制水平应与工艺专业协调一致,宜纳入分散控制系统控制,也可采用强电控制。
(3)接入发电机出口的脱硫高压变压器保护:
1)新建电厂同期建设烟气脱硫装置时,应将脱硫高压变压器的保护纳入发电机变压器组保护装置。
2)脱硫装置为预留时,发电机变压器组差动保护应留有
脱硫高压变压器的分支接口。
3)已建电厂加装烟气脱硫装置时,脱硫高压变压器的分支应接入原有发电机变压器组差动保护。
4)脱硫高压变压器保护应符合DL/T5153—2002中的
规定。
(4)其他二次线要求应符合DL/T5136—2001和DL/T 5153—2002的规定。
二、电气系统的优化设计
(1)脱硫设备供电的可靠性要求按主机设备同等考虑。(2)提高脱硫主要设备的电负荷等级,与机组主要设备等
级相同,如浆液循环泵、石灰石供浆泵、石膏排出泵、氧化风机、搅拌器等从二类提高到一类。
(3)在电源接线上,要充分考虑失电后的安全措施。脱硫6kV电源装设快切装置,提高电源的可靠性,这样只要厂用6kV电源不全部失电,即可保证脱硫6kV不全部失电,从而保证脱硫PC段不失电,脱硫保安段电源可保证。关键设备要连接保安电源或连在不同的工作段上,以避免设备同时停运。如多台浆液循环泵要分别接在不同的母线上,保证至少有1台浆液循环泵的供电是可靠的;1台运行1台备用的设备,2台设备要接在不同的母线上。
(4)为FGD系统设2台变压器供电,2路供电,保证脱硫设备可靠运转。
(5)扩大保安电源范围,除DCS电源、吸收塔搅拌器外,事故喷淋系统、除雾器冲洗水泵采用保安电源等。
第十八节 仪控系统设计要点
脱硫控制应采用集中控制方式,有条件的可将脱硫控制与脱硝、除尘、除灰控制集中在一个控制室内。一般两炉设一个脱硫控制室,当规划明确时,也可采用四炉合设一个脱硫控制室。当条件成熟时,脱硫可纳入机组单元控制室,其中脱硫装置的控制可纳入到机组的DCS系统,公用部分如石灰石浆液制备系统、工艺水系统、皮带脱水机系统等纳入到机组DCS的公用控制网。根据改造机组的设计情况来看,脱硫控制系统独立设计,建立独立的控制室,使脱硫的操作控制在主系统之外,当系统停运及检修时,不影响主系统的正常运行。对于新建机组配套的FGD装置,就地设置电子设备间,FGD控制纳入机组的DCS,或与脱硝、除尘、除灰合用一个控制室。
根据实际情况,控制系统可以有不同的设计原则及不同的控制方式。
(1)直接选用与主系统一致的DCS系统设备,一方面可以减少备品备件,减少维护量;另一方面便于与主机实现网络通信,实现主机和脱硫控制系统一体化。另外,管理系统(MIS/SIS)可以采用统一的数据接口采集数据。
(2)控制系统设计成一个独立的系统。该独立的控制系统可以根据用户的要求设计为DCS、PLC及FCS任意一种形式,也可以设计成三个系统技术的综合控制系统。
一、PLC控制系统
1.PLC的基本概念
可编程控制器是一种数字运算操作的电子系统,专为在工业环境应用而设计的。它采用一类可编程的存储器,用于其内部存储程序,执行逻辑运算、顺序控制、定时、计数与算术操作等面向用户的指令,并通过数字或模拟式输入/输出控制各种类型的机械或生产过程。可编程控制器及其有关外部设备,
都按易与工业控制系统联成一个整体、扩充其功能的原则设计。
2.PLC的基本结构
(1)中央处理单元(CPU)。CPU是PLC的核心,起神
经中枢的作用,每套PLC至少有一个CPU,它按PLC的系统程序赋予的功能接收并存储用户程序和数据,用扫描的方式采集由现场输入装置送来的状态或数据,并存入规定的寄存器中,同时,诊断电源和PLC内部电路的工作状态和编程过程中的语法错误等。进入运行后,从用户程序存储器中逐条读取指令,经分析后再按指令规定的任务产生相应的控制信号,去指挥有关的控制电路。
CPU主要由运算器、控制器、寄存器及实现它们之间联系的数据、控制及状态总线构成,CPU单元还包括外围芯片、总线接口及有关电路。内存主要用于存储程序及数据。CPU控制器控制CPU工作,由它读取指令、解释指令及执行指令,但工作节奏由振荡信号控制。运算器用于进行数字或逻辑运算,在控制器指挥下工作。寄存器参与运算,并存储运算中间结果,它也是在控制器指挥下工作。CPU速度和内存容量是PLC的重要参数,它们决定着PLC的工作速度、I/O数量及软件容量等。
(2)存储器。存放系统软件的存储器称为系统程序存储器,存放应用软件的存储器称为用户程序存储器。
(3)电源。PLC电源为PLC各模块的集成电路提供工作电源。
(4)I/O模块。PLC与电气回路的接口,是通过输入/输
出部分(I/O)完成的。I/O模块集成了PLC的I/O电路,其
输入暂存器反映输入信号状态,输出点反映输出锁存器状态。输入模块将电信号变换成数字信号进入PLC系统,输出模块相反。I/O分为开关量输入(DI)、开关量输出(DO)、模拟量输入(AI)、模拟量输出(AO)等模块。
(5)底板或机架。大多数模块式PLC使用底板或机架,其作用是:在电气上,实现各模块间的联系,使CPU能访问底板上的所有模块;在机械上,实现各模块间的连接,使各模块构成一个整体。
(6)PLC系统的其他设备。
1)编程设备:一般由计算机(编程软件)充当编程器。2)人机界面:一般用计算机充当人机界面。
3)输入输出设备:用于永久性地存储用户数据,如EPROM、EEPROM写入器和条码阅读器、输入模拟量的电位器、打印机等。
(7)PLC的通信联网。PLC具有通信联网的功能,它使PLC与PLC之间、PLC与上位计算机以及其他智能设备之间能够交换信息,形成一个统一的整体,实现分散集中控制。多数PLC具有RS—232接口,还有一些内置并支持各自通信协议的接口。
PLC的通信,还不具备相互操作性,IEC规定了多种现场总线标准,PLC各厂家均有采用。
对于一个自动化工程,特别是中大规模控制系统,选择网络非常重要。首先,网络必须是开放的,以方便不同设备的集成及未来系统规模的扩展;其次,针对不同网络层次的传输性能要求选择网络的形式,这必须在较深入地了解该网络标准协议、机制的前提下进行;再次,综合考虑系统成本、设备兼容性、现场环境适用性等具体问题,确定不同层次所使用的网络标准。
3.PLC的工作原理
当PLC投入运行后,其工作过程一般分为三个阶段,即输入采样、用户程序执行和输出刷新阶段。完成上述三个阶段称为一个扫描周期。在整个运行期间,CPU以一定的扫描速度重复执行上述三个阶段。
(1)输入采样阶段。在输入采样阶段,PLC以扫描方式依次读入所有输入状态和数据,并将它们存入I/O映像区中相应的单元内。输入采样结束后,转入用户程序执行和输出刷新阶段。在这两个阶段中,即使输入状态和数据发生变化,I/O映像区中的相应单元的状态和数据也不会改变。因此,如果输入是脉冲信号,则该脉冲信号的宽度必须大于一个扫描周期,才能保证在任何情况下,该输入均能被读入。
(2)用户程序执行阶段。在用户程序执行阶段,PLC总是按由上而下的顺序依次地扫描用户程序。在扫描每一条梯形图时,又总是先扫描梯形图左边的由各触点构成的控制线路,并按先左后右、先上后下的顺序,对由触点构成的控制线路进行逻辑运算,然后根据逻辑运算结果,刷新该逻辑线圈在系统RAM存储区中对应位的状态,或者刷新该输出线圈在I/O映像区中对应位的状态,或者确定是否要执行该梯形图所规定的特殊功能指令。
在用户程序执行过程中,只有输入点在I/O映像区内的状态和数据不会发生变化,而其他输出点和软设备在I/O映像区或系统RAM存储区内的状态和数据都有可能发生变化,而且排在上面的梯形图,其程序执行结果会对排在下面的凡是用到这些线圈或数据的梯形图起作用;相反,排在下面的梯形图,其被刷新的逻辑线圈的状态或数据,只能到下一个扫描周期才能对排在其上面的程序起作用。
(3)输出刷新阶段。当扫描用户程序结束后,PLC就进入输出刷新阶段。在此期间,CPU按照I/O映像区内对应的状态和数据刷新所有的输出锁存电路,再经输出电路驱动相应的外设。这时,才是PLC的真正输出。同样的若干条梯形图,其排列次序不同,执行的结果也不同。另外,采用扫描用户程序的运行结果与继电器控制装置的硬逻辑并行运行的结果有所区别。当然,如果扫描周期所占用的时间对整个运行来说可以忽略,那么二者之间就没有什么区别了。一般来说,PLC的扫描周期包括自诊断、通信等,即一个扫描周期等于自诊断、通信、输入采样、用户程序执行、输出刷新等所有时间的总和。
4.PLC的发展方向
(1)目前,PLC产品规模向小型化和大型化两极分化。小型PLC的I/O点数一般在128点以下,其特点是体积小、结构紧凑,整个硬件融为一体,除了开关量I/O以外,还可以连接模拟量I/O以及其他各种特殊功能模块。它能执行包括逻辑运算、计时、计数、算术运算、数据处理和传送、通信联网以及各种应用指令。小型PLC基本用于机械设备本体控制,例如石灰石浆液制备湿式球磨机油站控制。大型PLC一般I/O点数在1024点以上,其软、硬件功能极强,具有极强的自诊断功能。通信联网功能强,有各种通信、联网的模块,可以构成三级通信网,实现工厂生产管理自动化。大型PLC还可以采用三CPU构成表决式系统,使机器的可靠性更高。目前,许多大型电厂辅控系统都采用PLC。
(2)目前的PLC具有早期的逻辑运算功能,并不断完善PID闭环控制功能,其他各种功能也在不断得到改进,而且连续过程控制技术正在进一步得到发展。
(3)随着微电子技术的不断发展,冗余技术的不断推广,
PLC厂家不断推出高可靠性通信接口、智能模块、特殊功能模块,通信联网功能更强,指令系统更丰富,内存容量更大,扫描速度更快。
(4)在PLC硬件不断发展的同时,PLC的编程软件也在向前发展。PLC厂家在不断努力开发适合于PLC系统的编程软件,其他软件开发商也在不断推出与之相配套的组态软件,而且每种软件都适合于多种品牌的PLC产品,为用户编程提供了极大的方便。
二、DCS控制系统
1.DCS的基本概念
分散控制系统(DCS)又称为集中分散系统,也称为分布式控制系统,它是利用计算机技术(COMPUTER)、控制技
术(CONTROL)、通信技术(COMMUNICATION)、图形显
示技术(CRT)实现过程控制和过程管理的控制系统。它以多台微处理器分散应用于过程控制,通过通信总线、显示器、键盘、打印机等操作、显示和报警。
DCS系统分为四大部分:输入/输出模板、控制器、人机接口和通信网络。
通信网络分为星形、总线、环形或组合型的网络拓扑结构。
通信总线冗余:
(1)两套平时按规定比例承担通信负荷,其中一套出现故障,另一套承担全部通信负荷。
(2)两套中一套使用,另一套备用,当使用的那套通信网络出现故障,则由备用通信网络来承担系统通信任务。
2.DCS结构
(1)输入/输出模板。
输入/输出模板主要完成模拟和数字信号的转换,通过端子排直接与生产过程相连,读取传感器信号。输入/输出模板有不同的类型,并有相应的端子排。I/O板的差别在于有无智能板卡,但是控制器读取所有I/O数据必须在1s内完成一个循环。
1)模拟量输入:直流电流信号
4~20mA,对于外供电的信号,需装设隔离器
热电阻信号 分度号Pt100输入阻抗
电流输入小于250Ω电压输入大于500kΩ
2)模拟量输出:
直流电流信号 4~20mA,负载能力大于1000Ω
直流电压信号 1~5V,负载能力小于600Ω3)开关量输入:
逻辑电平
48VDC,输入阻抗大于1000Ω
触点输入
常开、常闭干触点
4)开关量输出:电压输出
24VDC
触点输出
常开、常闭干触点
每一触点应能同时满足以下容量:
220VAC,2A(阻性负载)220VAC,1A(感性负载)220VDC,0.5A(感性负载)220V DC5A
5)脉冲量输入:每秒能接受6600个脉冲
6)SOE板件:事故顺序输入信号的分辨力应不大于1ms
(2)控制器。
随着计算机技术的发展,控制器的运算能力不断增强,成为网络上的一个节点,通过网络与人机界面相连。
控制器是 DCS的核心,它相当于一台PC机,主要有
CPU、RAM、E2PROM和ROM等芯片;CPU主要完成各种
运算;ROM用来存储各种运算功能的控制算法(功能库);RAM用来存储CPU的运算结果和I/O信号。按照工艺要求,把功能块连接起来形成控制方案存放于E2PROM,下电时,控制方案不会丢失。E2PROM可以擦写,随工艺改变可以修改控制方案。
控制器的两个接口,一个向下接收数据I/O总线来的信号,另一个是向上把信号送到网络上与人机界面相连。通过DIP开关设定硬地址,在系统组态中设软地址。
DCS控制器功能:
1)与硬件连接的功能块(AI,AO,DI,DO等)。
2)PID、算术、函数、三角、几何、三维矩阵等运算。3)模糊逻辑、模型控制等高级运算。
控制器的运行方式两种:组态和运行。为了系统安全运行,闭环控制器一定是冗余运行的,一用一备,并且是热备。为了保证冗余成功必须满足以下条件:两个控制器的硬件和软件版本一致;冗余的控制器运行正常。
控制器中安装有操作系统、功能块组态软件、通信软件。功能块组态软件安装在工程师站,它是对DCS进行离线的配置、组态工作和在线的系统监督、控制、维护,其主要功能是对DCS进行组态,并在DCS在线运行时实时地监视DCS网络上各个节点的运行情况,使系统工程师可以通过工程师站及时调整系统配置及一些系统参数的设定,使DCS处在最佳工作状态。
通信网络把过程控制器和人机接口连成一个系统。
(3)通信网络。
DCS的基础和核心为通信网络,参加网络通信的最小单位称为节点。网络的三要素:通信介质、网络结构和通信方式。DCS的通信网络一般分为四级:现场总线、I/O总线、控制总线和DCS网络。
当节点连到DCS的通信网络上时,通常有一个网络接口,控制把数据送到接口,人机界面从网络接口读取数据,读取数据应遵守网络通信协议。
为了保证网络通信的实时性和系统可扩充性的要求,系统网络上可接入的最大节点数量应比实际使用的节点数量大若干倍。这样,一方面可以随时增加新的节点,另一方面也可以使系统网络运行于较轻的通信负荷状态,以确保系统的实时性和可靠性。一般数据通信总线在繁忙工况下,负荷率不得超
过30%。
(4)人机接口。
人机接口包括操作员站、工程师站和历史站。控制器把I/O部件与生产过程相连接,操作员站和运行人员相联系,通信网络把这两部分连成系统,操作员站用来监控工艺参数及设备的运行状态。在系统投运前,把存储在控制器中的各种算法按照生产要求连接起来,并填进参数后下装给控制器,称为组态,整个过程在工程师站完成。历史站按设定的时间周期记录生产过程数据。
3.DCS的发展历程
1975年美国霍尼韦尔首先推出TDC2000,只有模拟控制,经过了几十多年的发展,DCS虽然在系统的体系结构上没有发生重大改变,但是经过不断的发展和完善,其功能和性能都得到了巨大的提高。进入20世纪90年代以后,计算机技术突
飞猛进,更多新的技术被应用到了DCS之中。
受信息技术(网络通信技术、计算机硬件技术、嵌入式系统技术、现场总线技术、数据库技术等)发展的影响,以及用户对先进的控制功能与管理功能需求的增加,各DCS厂商纷纷提升DCS系统的技术水平,以 Honeywell公司最新推出的
ExperionPKS(过程知识系统)、Emerson公司的PLantWeb(EmersonProcess Management),Foxboro公司的A2,横河公司的R3(PRM-工厂资源管理系统)和ABB公司的Industrial
IT系统为标志的第四代DCS已经形成。
DCS的起步主要是解决系统中的控制回路的控制算法。20世纪70年代中期,推出的DCS产品仍以模拟量反馈控制为主,辅以开关量的顺序控制和模拟量开关量混合型的批量控制。目前DCS的优势仍然是实现模拟量控制,模拟量控制及其算法是DCS的核心技术。
用户应结合性能价格比及产品生命周期,对DCS进行选型、工程费用、维修费用等方面的综合考虑。更重要的是目前PLC系统、工控机系统(IPC)的价格都是以廉价著称,所以DCS厂商需在降低成本、减少维修费用、发展远程诊断和维护等方面开展工作。
目前,DCS的一个控制器完成几十个回路的运算和几百点的采集、再加适量的逻辑运算,经现场使用,效果是比较好的。控制点数及功能的扩展促进了控制器的升级,控制器与检测元件距离较远问题促进现场总线的发展。
三、FCS控制系统
1.现场总线控制技术的基本概念
现场总线控制技术(FieldbusControlSystem,FCS)系统
的核心是总线协议,即总线标准。一种类型的总线,只要其总线协议一经确定,相关的关键技术与有关的设备也就被确定。就其总线协议的基本原理而言,各类总线都是一样的,都以解决双向串行数字化通信传输为基本依据;但由于各种原因,各类总线协议存在很大差异。为了使现场总线满足可互操作性要求,使其成为真正的开放系统,在IEC国际标准现场总线通信协议模型的用户层中,就明确规定,用户层具有装置描述功能,数字化通信取代4~20mA模拟信号。传统技术现场层设备与控制器之间的连接是一对一(一个I/O点对设备的一个测控点)I/O接线方式,来传递4~20mA(传送模拟量信息)或开关量信号。应用现场总线技术可用一条通信电缆将控制器与现场设备(智能化、带有通信接口)连接,使用数字化通信完成底层设备通信及控制要求。
2.现场总线控制技术的技术特点
(1)要求现场设备智能化,即应用现场总线技术,要求现场设备(传感器、驱动器、执行机构等设备)是带有串行通信接口的智能化设备(可编程或可参数化)。
(2)现场总线采用计算机数字化通信技术连接智能化现场设备,集现场设备的远程控制、参数化及故障诊断为一体,控制器可从现场设备获取大量的、丰富的信息,实现设备状态、故障及参数信息传送,完成设备远程控制、参数化及故障诊断工作。
3.现场总线的自动化监控系统的主要优点
(1)基于现场总线的自动化监控系统增强了现场级信息集成能力。现场总线可以从现场设备获取大量丰富信息,能够更好地满足工厂自动化及CIMS系统的信息集成要求。现场总线是数字化通信网络,它不单纯取代4~20mA信号,还可以实现设备状态、故障、参数信息传送。系统除了完成远程控制之外,还可以完成远程参数化工作。
(2)开放式、互操作性、互换性、可集成性。不同厂家产品只要使用同一总线标准,就具有互操作性、互换性,因此设备具有很好的可集成性。系统为开放式,允许其他厂商将自己专长的控制技术,如控制算法、工艺流程、配方等集成到通用系统中去,因此,市场上将有许多面向行业特点的监控系统。
(3)系统可靠性高、可维护性好。基于现场总线的自动化监控系统采用总线连接方式替代一对一的I/O连线,对于大规模I/O系统来说,减少了由接线点造成的不可靠因素。同时,系统具有现场级设备的在线故障诊断、报警、记录功能,可完成现场设备的远程参数设定、修改等参数化工作,也增强了系统的可维护性。
(4)节省成本。对大范围、大规模I/O的分布式系统来说,省去了大量的电缆、I/O模块及电缆敷设工程费用,降低了系统及工程成本。
四、三种控制系统的性能比较
1.系统比较
(1)DCS系统是一个有机统一的整体,内部接口比较完善,人机界面及软件统一,给系统设计、编程组态等带来很大方便。另外,整个系统运行稳定可靠,主要用于大规模的连续过程控制。PLC系统适合中型及小型系统,其逻辑控制功能强。FCS适合各种控制系统,但必须有数字智能化的现场装置为前提,才能显示其智能化的优势。
(2)DCS系统一次性投资较大,PLC系统投资相对要小,FCS系统要求一次仪表智能化程度高,一次仪表投资要大些。
(3)DCS系统闭环控制功能强。PLC主要用于工业过程中的顺序控制,兼有闭环控制功能,PLC强大的开关量处理能力正好适应脱硫系统开关量多、模拟量少的特点,系统配置灵活特点也较适合改造工程。PLC本身控制器的I/O结构,决定其远程I/O配置方式要比DCS灵活得多。
(4)DCS系统是封闭式系统,各公司产品基本不兼容,事后扩容难度较大。PLC系统可以通过网络扩充同型号PLC单元,而且它可以作为 DCS、FCS系统的前端处理现场I/O。FCS系统是开放式系统,用户可以选择不同厂商、不同品牌的各种设备连入现场总线,达到最佳的系统集成。
(5)DCS、PLC系统的信息全都是由二进制或模拟信号形成的,必须有D/A与A/D转换。FCS系统是全数字化,采用数字信号传递,就不需要D/A与 A/D变换,高集成化高性
能,使精度可以从±0.5%提高到±0.1%。
(6)FCS系统可以将PID闭环控制功能装入变送器或执行器中,缩短了控制周期,目前可以从DCS的2~5次/s,提高
到FCS的10~20次/s,从而改善调节性能。
(7)DCS、PLC可以控制和监视工艺全过程,对自身进行诊断、维护和组态。由于其I/O信号采用传统的模拟量信号,在DCS工程师站上无法对现场仪表(含变送器、执行器等)进行远方诊断、维护和组态。FCS采用全数字化技术,数字智能现场装置发送的是多变量信息,而不仅仅是单变量信息,并且还具备检测信息差错的功能。FCS采用的是双向数字通信现场总线信号制,它可以对现场装置(含变送器、执行机构等)进行远方诊断、维护和组态。
(8)FCS由于信息处理现场化,与DCS、PLC相比可以省去相当数量的隔离器、端子柜、I/O卡件、I/O柜及终端,节省了I/O装置及电子设备间的空间与占地面积,减少大量电缆与敷设电缆用的桥架等,同时也节省了设计、安装和维护费用。
2.选型的主要依据(1)系统的运行方式。
(2)控制系统的资金投入。(3)现场与控制室的距离。
(4)系统中模拟控制回路的数量。(5)系统中开关量的数量。
(6)现场一次仪表智能化的程度等。五、控制系统的选型建议
三个控制系统各有优缺点,如果条件许可的话,也可以设计成综合的控制系统。根据脱硫工艺来看,改造中的脱硫系统一般控制点数在1000点左右,脱硫系统开关量控制数量远大于模拟量控制数量,体现不出DCS控制器优势,系统配置方式相对固定,不如PLC灵活,选用PLC为控制系统更能发挥其特长。FCS系统是比较先进的控制系统,随着一次智能化仪表的发展和普及,FCS将是未来控制系统的主流。由于目前现场条件的限制,在改造机组中选用FCS系统还不能发挥其优势。如果现场要求控制系统先进,一次仪表大多采用智能化仪表,选用FCS控制系统是最为理想的。该系统可以通过网络技术使数据能够方便地上传给主系统DCS,实现集中监视。在改造系统中也可以采用DCS系统,其控制系统的稳定可靠是经过长期证明的,主要是价格昂贵,由于DCS很强大的控制功能在改造系统中没有多少用武之地,造成资源浪费。目前小型DCS系统发展很快,除了首选PLC系统之外,也可以考虑选用小型DCS系统。
六、热工电源
(1)脱硫热工控制柜(盘)进线电源的电压等级不得超过220V,进入控制装置柜(盘)的交、直流电源除故障不影响安全外,应各有两路,互为备用。工作电源故障需及时切换至另一路电源,应设自动切换装置。
(2)脱硫分散控制系统及保护装置一路采用交流不停电电源,一路来自厂用保安段电源。
(3)每组热工交流380V或220V动力电源配电箱应有两路输入电源,分别接自脱硫厂用低压母线的不同段。
七、主要仪表设计优化
1.pH计
对吸收塔内浆液pH值的控制是整套脱硫系统最关键的调节回路,直接影响到最终的脱硫效率。pH计采用冗余配置,常规安装方式为:在石膏排出泵出口设置浆液循环管路;冗余的pH计安装在浆液循环管道上,但该安装方式存在较多弊端。
(1)为了实时检测吸收塔浆液的pH值,需要保持石膏排出泵处于不间断运行状态(常规方式对石膏浆液密度的实时检测,也要求石膏排出泵处于不间断运行状态),这不仅大大缩短了石膏排出泵的使用寿命,而且也增加了电厂后期的运行能耗成本。
(2)石膏排出泵出口压力较高,导致安装pH计循环管道的流速过快,浆液对pH计电极及管道产生很大的冲击、磨损,影响设备寿命。
(3)需要为pH计及所在管道配置一套冲洗系统,在一定程度上增加了系统出现故障的概率。
鉴于以上原因,在设计时,可以将pH计位置由浆液循环管道移至吸收塔本体。考虑吸收塔内浆液分布存在一定的不均匀性,将pH计安装位置确定在循环泵入口的上方(有3台循环泵时,安装在2台循环泵入口中心线上;有4台循环泵或更多时,安装方式相同),此处浆液随着循环泵工作,流动性较大,测量的pH值最具代表性,能充分反映吸收塔内当前的pH值,满足系统设计的需要。经运行调查,该方案应用效果良好。
2.密度计
密度计用于测量石膏浆液及石灰石浆液,当前普遍应用于脱硫领域的密度测量装置有放射性密度计和质量密度计。放射性密度计具有安装方便、测量精度较高、运行稳定等优点,但因其依赖于放射性同位素辐射源,对环境会造成一定的污染,同时,按照国家相关规定,辐射源的管理需要涉及一系列的部门,审批制度比较复杂。质量密度计采用的是常规测量原理,如图13181所示。避免了放射性密度计因为放射源问题在使用工程中带来的很多不便,但质量密度计在使用过程中与浆液有直接接触,长时间使用存在一定的磨损,同时,因使用不当会造成密度计堵塞浆液,维护工作量大。鉴于以上原因,设计时可采用在吸收塔壁上安装压力变送器(该压力变送器同时也用于测量吸收塔内浆液的液位)的方式,通过测量不同高度的浆液压力来计算浆液的实时密度,代替传统的密度测量方式,该设计方案在广西贵港电厂脱硫项目中取得了良好的效果。

图13181 质量密度计测量原理
假设浆液密度为ρ、吸收塔截面积为S、压力变送器1测得压力为p1、压力变送器2测得压力为p2、压力变送器1距离吸收塔浆液液面高度为h1、压力变送器2距离吸收塔浆液液面高度为h2、压力变送器1与压力变送器2之间的距离为h,则浆液密度为
p2-p1=ρghρ=p2g-hp1
考虑现场仪表精度,可以适当增加h值,并增加变送器数量,使得浆液密度测量更加精确。采用以上方式,不仅可以简化系统,节约成本,减少系统的故障点,而且可以有效减少石膏排出泵的运行时间,简化工艺管道设计,使脱硫系统能长期稳定运行。
3.泵出口压力检测
泵出口压力变送器可以省略,改为就地压力表,泵的工作状态可以由泵的工作电流信号进行监控。
4.液位测量
对于北方地区,测量地坑用的超声波液位计因为蒸汽凝结问题而存在测量不准的问题,可改用雷达液位计或磁翻板液位计,或将超声波液位计适当抬高安装来解决上述问题。可以将箱罐的液位测量方式由超声波液位计测量改为压力变送器测量。
八、主要检测参数的测点布置
图13182示意标明了典型石灰石湿法烟气脱硫装置主要工艺过程运行监测参数检测表计的布置位置,包括温度、压力、压差、液位、pH值、浓度(密度)、流量、烟气成分、石膏层厚度等,这些参数均实时显示在控制系统的计算机画面上,并用于运行参数控制。

图13182 典型石灰石湿法烟气脱硫装置主要测点布置示意图
P—压力;ΔP—压差;T—温度;pH—pH计;D—浓度计(密度计);F—流量计;L—液位(物位);
H—石膏层厚度;A—烟气成分:O2,SO2,CO,NO,粉尘
注 当石灰石浆液经再循环泵补入吸收塔,pH计布置在浆液箱出口管道;当石灰石浆液经直接补入吸收塔,pH计可布置在再循环泵出口管道
第十九节 湿烟囱设计要点
“湿烟囱”定义为用以排放饱和的且全部清洁过的烟气的烟囱或烟道。湿烟囱位于湿法烟气脱硫系统的下游,在上游的湿法脱硫系统中,脱硫浆液被喷入烟气流中与其发生化学反应,通过一系列的脱硫化学反应,二氧化硫的含量降低,烟气达到饱和,烟温也降到50~55℃。
电厂湿烟囱由外烟筒和内烟道组成,如图13191所示,通常高度超过200m,外烟筒与内烟道之间的部分称为烟囱的环状央层,外烟筒作为内烟道的结构支撑,使其免受风力作用。FGD装置处理后的清洁烟气经FGD系统出口烟道、烟囱入口烟道,沿烟囱内烟道抬升到烟囱出口一定高度后逐渐扩散到大气中。

图13191 电厂烟囱结构示图
常见的湿法FGD烟气系统主要由脱硫风机(BUF),气—气换热器(GGH),吸收塔模块,FGD旁路烟道,FGD出口烟道,烟囱入口烟道以及相关的挡板门等组成,如图1319 2所示。如果省去GGH,从吸收塔模块排出的经处理的绝热饱和湿烟气则直接经出口烟道和烟囱向大气排放。湿烟气温度通常为45~55℃,吸收塔下游侧的烟道和烟囱处于湿状态下运行,故将这种工艺流程称为湿烟囱工艺。

图13192 湿法FGD主要设备流程图
GGH的省去简化了系统,缩短了进出口烟道,降低了投资和运行成本,省除了故障率较高的GGH带来的大量维修工作。但是,湿烟囱工艺对环境会带来三个问题:①湿烟气的温度比较低,抬升高度较小,影响烟气扩散条件,会提高最大落地浓度,影响地面环境空气质量;②湿烟气含有大量水蒸气,处于饱和状态,排出的烟气会因水蒸气的凝结而使烟羽呈白
色,影响视觉;③饱和湿烟气夹带的液滴以及因水蒸气凝结形成的凝结水,可能造成烟羽在飘散过程中形成少量降水,影响局地环境和气候。此外,湿烟囱工艺对处于湿状态下的烟道,烟囱的设计和材料选择有特殊要求。
一、选择湿烟囱需考虑的因素
虽然世界许多FGD系统都安装了烟气再加热装置,但自20世纪80年代中期以来,美国设计的大多数FGD系统选择了湿烟囱。国内福建后石电厂6×600MW燃煤机组配套的6台海水FGD系统是我国第一个采用湿烟囱工艺的大型火电厂,近年来湿烟囱工艺在国内获得广泛的应用。通常发电厂决定采用湿烟囱运行,最重要的考虑因素是投资和运行成本,在多数情况下湿烟囱方案具有最低的总费用。但是,其他一些因素,例如烟气扩散和烟羽的不透明度可能压倒湿烟囱在经济方面带来的优势。
1.湿烟羽的抬升与扩散
烟气离开烟囱后在周围气象条件的影响下形成形态各异的烟羽并逐渐扩散到大气中去,烟羽的扩散状况有可能影响烟囱附近地区和下风侧较远的区域,如果烟羽下落到烟囱出口高度的下方,而且靠近烟囱的附近地区则发生了称为烟羽下洗的现象。当风吹过烟囱时,也像吹过其他任何障碍物一样,背风侧形成了一个低压区,风速加大,低压区的范围扩大,而且低压区的压力下降越多,如果烟气离开烟囱后,抬升的浮力不足或垂直向上的流速不够时,就会被低压拖入低压区中,发生烟流下洗。烟羽的下冲气流不仅会腐蚀烟囱组件,而且降低了烟羽的扩散程度,在低于0℃气温下会造成烟囱结冰。有多个内烟道的大直径烟筒发生烟羽下洗的可能性较单烟道的烟囱更大,因为外烟筒的直径大会产生较大的低压区。为防止烟囱本身对烟流产生的下洗现象,烟囱出口气流速不宜低于该高度处平均风速的1.5倍;当烟囱出口烟气流速等于烟囱口高度的风速,烟羽下洗会达到一个烟囱直径的高度。
大型火电机组烟气抬升高度与烟囱出口的风速成反比,与烟气热释放速率的1/3次方成正比。对于烟囱出口风速较大的情况,大型火电厂烟囱出口风速对烟气抬升高度的影响,远大于排烟温度对抬升高度的影响;对于烟囱出口风速较小时,排烟温度对抬升高度的影响趋于明显。因此为了有利烟气抬升,烟囱出口烟气流速不宜过低,一般宜在20~30m/s,烟温宜在
100℃以上。
烟囱出口烟温对烟囱排放污染物的落地浓度影响很大,这是因为烟羽的温度越高,浮力就越大,离开烟囱后的拾升就越高,烟羽落到地面前的扩散时间和横向飘浮的时间就越长,扩散范围越宽,污染物稀释后的落地浓度就越低。而湿烟气由于温度低,浮力小,垂直扩散速度低,因此湿烟囱排放的低温烟气造成的地面污染浓度比排放加热烟气的烟囱要大,而且更靠近烟囱,这相当于降低脱硫效率的程度随环境条件而变。具有关资料介绍,当不考虑湿烟气从烟囱排出后会发生的水汽凝结效应时,降低程度最大可达40%以上。如果湿烟羽在离开烟囱时处于饱和状态,在传输过程中,烟羽中的水汽通常会发生凝结。水汽凝结会释放凝结潜热,这部分潜热会增加烟羽的浮力通量,使烟羽获得额外的浮力,造成湿烟羽拾升高度的增大,从而可适当降低地面污染浓度,比如在夏天,这种效应相当明显,最大抬升高度甚至会超过加热至100℃的烟气。在这种情况下,发生凝结的饱和湿烟羽造成的地面最大浓度比加热到100℃时烟气造成的地面最大浓度还低。
湿烟囱运行的另一个问题是烟囱“降雨”,称为烟囱雨或
酸雾沉降,起因是烟气夹带的液滴和湿烟气离开烟囱后形成的凝结水。前者与ME的除雾效果、烟气流速以及烟道和烟囱的设计有关,而凝结水还与过饱和度有关。过饱和度增大,会减少凝结水量。夏季环境温度升高,也会减少凝结水量。这些凝结水也并非全部变成降雨,是否降落地面,降落多少,取决于凝结核的大小、凝结核的多少以及气象条件等多种因素。实际上,大部分凝结水的直径介于200~600μm,因此,凝结水中只有那些较大的液滴才会形成雨水降到地面,大部分较小的液滴在飘散过程中若没有机会形成大液滴,最终会蒸发。此外,由于凝结水量不大,形成雾的几率很小,所以火电厂FGD排出的湿烟羽所形成的凝结水不会对当地的气候产生影响。因此,烟囱“降雨”的主要原因是烟气夹带的液滴。如果湿烟囱造成了降雨,通常发生在烟囱下风侧几百米内。虽然加热烟气的湿法FGD也可能发生烟囱降雨,但湿烟囱出现的几率要高些,通过调整FGD系统设定参数,改进出口烟道和烟囱的设计,可以最大限度地减少烟囱降雨问题。
2.烟羽的黑度
烟羽的黑度是烟气中的固体颗粉物,液体和气体与照射光相互作用的结果,用林格曼图来鉴定的黑度等级是我国控制烟气排放的方法之一。发电厂排放烟气的透明度主要受飞灰颗粒物、液滴和硫酸雾的影响,造成烟气不透明的最主要的气体物质是 NO2。当饱和热烟气离开烟囱后温度急速下降,从而形成了水雾。这种含有较多水汽或其他结晶物质的白色烟气一方面会降低烟气的黑度,使测得的烟气黑度不能真实地反映污染情况;另一方面,居住在采用湿烟囱发电厂附近的人们可能认为烟囱冒出的烟羽透明度不高是因为烟气中含有较多的固体颗粒物,而实际上是烟气中的水雾造成的。因此,打算采用湿烟囱的电厂必须考虑湿烟囱冒出的大量白色烟羽对附近居民的心理影响。应该指出的是,加热烟气可以推迟或减少水雾的形成,但大多数烟气加热装置并不是按照在各种大气情况下都能消除烟羽中的白色水雾来设计的,特别在寒冷的季节里,即使采用了排烟再加热的系统也会形成看得见的水雾烟流。
3.经济性比较
如果发电厂根据技术和环境保护法规的要求以及公众可接受的程度,对排烟扩散和黑度的评价表明湿烟囱是可行的,那么就应对湿烟囱最佳运行方式进行经济评价。一般情况下,湿烟囱FGD装置的总投资、运行和维护等费用较装有烟气加热器的要低得多。
无再加热系统和有再加热系统的年总费用比较应包括出口烟道、烟囱和烟气再加热装置的投资成本和年总费用。湿烟囱工艺对出口烟道和烟囱有特殊要求,不同形式再加热装置的运行费用是不相同的,这对经济评价是尤为重要的。采用蒸汽管排加热烟气的方法会使发电机组的热耗率增加5%及以上,采用气—气换热器将FGD入口烟气的热量传递给出口烟气的加热方式,对机组热耗率影响要小些,但投资费用大。容量为300MW的FGD装置,按国内的报价,回转式换热器的设备费约占整个系统(不含水处理系统)设备费用的14%~16%左右。GGH的压损占系统总压损25%到接近40%。省除GGH后不仅节省了GCH本身的能耗,而且可以显著降低脱硫风机的电耗,如果再考虑取消GGH后入/出口烟道可以大为缩短,系统的总压损还可以再降低约2.5%~5.0%,且FGD系统变得异常简洁,占地面积可以明显减少。
4.我国对脱硫烟气加热升温的指导意见
我国国家环境保护总局环评司于2004年5月20日在北京
主持召开了“火力电厂烟气排放环境影响有关问题讨论会”,同年9月8日以会议纪要的方式,对火电厂烟气湿法脱硫后是否要进行烟气升温问题提出了意见:①湿法脱硫烟气升温主要是在一定条件和程度上提高烟气抬升高度,进而在一定程度上改善烟气扩散条件,而对污染物的排放浓度和排量没有影响;②对燃煤电厂较密集的地区,对环境质量有特殊要求的地区以及位于城市的现有电厂改造等,在满足景观和环境质量要求下,火电厂均应采取加装GGH等设备工艺,进一步改善烟气扩散条件;③在有环境容量的地区,比如农村地区、部分海边地区的火电厂,在满足达标排放、总量控制和环境功能的条件下,可暂不采取烟气升温措施;④新建、扩建、改造火电厂,其烟气排放是否需要升温,应通过项目的环境影响评价确定。
二、冷凝物形成的原因和特点
对于湿烟囱的设计,其中一个主要目标是尽可能减少烟囱降雨。烟囱降雨的直接原因是烟气中的水滴,水滴形成的原因和特点是;①透过 ME夹带过来的液滴,这种液滴直径通常
100~1000μm,少数大于2000μm,其量变化很大,与 ME性
能、清洁状况、烟气流速等因素有关;②饱和烟气顺着烟囱上升时压力下降,绝热膨胀使烟气变冷,形成直径大约1μm细小水滴,烟羽中绝大多数是这种液滴。由于这些液滴非常小,烟囱降雨主要不是这些细小水滴造成的。这些细小水滴从烟囱排出到降落地面之前,大部分蒸发了;③热饱和烟气接触到较冷烟道和烟囱内壁形成了冷凝物,其量取决于出口烟道长度、保温方式、烟囱内烟道衬里材料以及环境温度。
受惯性力的作用,烟气夹带的较大水滴撞到烟道和烟囱内壁上,与壁面的冷凝物结合。壁面冷凝物不断增多也使得细小液滴汇集成较大液滴,这些较大的液滴可能被烟气带离壁面重新进入烟气中。烟气重新夹带水数量取决于壁面的特性和烟气流速,粗糙的壁面和较高的烟气流速使夹带水量增加。这类重新被带出的液滴直径通常比冷凝形成的液滴和透过ME夹带的
液滴大得多,大约1000~5000μm。
三、湿烟囱工艺对设备的设计要求
本小节将介绍收集烟气中形成的冷凝物和尽可能减少烟囱排放液体采取的设计原则。
1.除雾器的设计和运行
在许多FGD系统中,烟囱中的液体主要来源于透过除雾器的夹带液。虽然 ME的正确设计和运行对任何FGD都重要,但对于湿烟囱工艺显得更为重要。除雾器的正确设计和运行主要包括以下几点:①最上层喷淋母管与除雾器端面应有足够距离,除雾器端面烟气分布应尽量均匀;②选用临界速度高、透过夹带物少、材料坚固和表面光滑的高性能除雾器;③在便于布置的情况下选择水平烟气流除雾器;④设置冲洗和压差监视装置,保持除雾器清洁,确保不发生堵塞。
2.出口烟道的设计
接触湿烟气的烟道壁、导流板、支撑加固件上会留有液体。因此,烟道设计应尽量减少水淤积,这样有利于冷凝液汇集和排往吸收塔收集池。膨胀节和挡板不能布置在低位点,同时也要设计排水设施。为了尽量减少烟气重新夹带液体,甚至不允许烟道内有加固件。
每种烟道材料都有其特有的烟气重新夹带液体的临界速度,如果烟气流速始终低于所用结构材料的这一临界流速,就可最大限度地减少烟气重新夹带液体量。对大多数出口烟道材料来说,带液体的烟气流速是12~30m/s,对于表面平整光滑的烟道,临界流速可取该范围的上限。烟囱入口烟道也应避免
采用内部加固。此外,烟囱入口烟道的宽度和布置方向影响液滴在烟道底部的沉积。一般主张烟囱入口烟道的宽度等于烟囱内烟道的半径,这样可以加剧烟气的旋流,有利于液滴沉积到烟囱壁上。
对出口烟道和烟囱的烟气流进行实际模拟和计算机模拟试验,将有助于降低烟气压降,有助于确定烟道尺寸、走向、导流板和集液设施的最佳位置,还可以检侧液体沉积和被烟气重新夹带的情况。
3.烟囱内烟道的设计
湿烟囱内烟道的设计应能最大限度地减少烟囱排放液体,可以通过收集随烟气带入烟囱的较大液滴和防止烟流重新夹带内烟道壁上的液滴来达到这一设计要求。由于绝热膨胀形成的液滴细小,不是烟囱排放液体主要因素,因此FGD出口烟道、烟囱入口水平烟道和烟囱内烟道的设计以及液体排放专用设备的选择和布置,成为尽可能减少烟囱排放液体的关键。
一方面要尽可能地减少进入烟囱的水沫,另一方面可以在靠近内烟道的底部收集进入烟囱的较大液滴。当烟气进入烟囱时,烟气由水平流急转成垂直流,惯性力使较大的液滴撞向烟囱入口烟道对面的内烟囱壁上,因此,在此位置上布置集液装置能有效的收集液滴。这种装置实际上很简单,例如格栅状FRP型材已成功地用于此位置上。另外,烟囱的底部应低于烟囱入口烟道的底部,形成一个集液槽,并配以疏水排放管道和防淤塞装置。
美国基于其20多年湿烟囱的研究和实际运行经验,在有关湿烟囱内壁材料和烟气临界流速方面积攒了经验。表13 191列出了运用模拟试验测得的几种烟囱材料的烟气临界流速。如果烟气中的液体量较少,或在靠近烟囱入口烟道处能有效地收集水滴,烟气流速可以再高些。通烟筒直径的选型最好能保证烟气流速低于二次夹带临界速度,并且还应留有适当的裕度。实践表明,按参考表中数据设计的烟囱,可以避免排放液体。
表13191 不同材料内烟道的烟气临界流速

过去,大多数用耐酸砖砌的内烟囱是圆锥形,现在大部分是等直径圆柱状。从表13191所列数据可以看出,后者
允许烟气临界速度(17m/s)比斜度为3.2mm的(9m/s)高
得多。锥形烟囱每层内衬砖之间有一处砖缝要错位,当水顺着烟道壁的砖缝向下淌时,水在这些错位缝处会漫出来,因而易被烟流重新带离壁面。大量的错位缝会成为烟气重新夹带液体的源头。减少砖砌锥形内烟囱的斜度,可以允许采用较高的烟速,由于烟流在烟囱上部的壁面上形成了边界层,贴近壁面的烟气流速明显低于主流体的流速,因此,烟囱上部的烟流允许有较高流速。增加烟囱出口处的烟速可以减少烟羽下洗和增强扩散,为此,美国的做法是在烟囱出口处装设调节门,但是液滴可能会汇集在节流门的表面上,并被烟流带走,增加排放液体量,因此,节流门的边缘应设计成流线型,操作时应渐进地
改变开度。
对于有多个内烟道的烟囱,可以使内烟道高出外烟囱2倍内烟道直径的高度,这样可以减少烟羽下沉。对单烟道的烟囱则无此必要,因为内外烟囱的直径相差不大。
4.冷却塔排放湿烟气方案
从20世纪80年代初开始,以德国为代表的一些发达国家的火电厂开始尝试省去烟气加热器,利用自然通风冷却塔排放脱硫后烟气。这种排烟方式不改变电厂原烟囱的设计,也无需再建湿烟囱,由此形成了另一种湿烟囱方法。经过多年的发展,至今全世界有很多机组采用了这种技术。
这种湿排放方式是将低温饱和湿烟气用烟气管道送入冷却塔配水装置上方集中排放,与冷却水不接触。由于烟气温度50℃左右,高于塔内湿空气温度,发生混合换热现象,混合的结果改变了塔内气体流动工况。塔内气体向上流动的动力是湿空气产生的热浮力,热浮力克服流动阻力而使气体流动。热浮力为
Z=hc×Δρ×g
(13191)
式中:hc为冷却塔有效高度;Δρ为塔外空气密度与塔内气体密度之差。
通常进入冷却塔的烟气密度低于塔内气体的密度,对冷却塔的热浮力产生正面影响。另外,冷却塔内湿空气流速很低,一般在1.0m/s左右,而进入塔内的烟气占塔内气体的份额一般不超过20%,占容积份额小,对塔内气流速影响不大。
此外,冷却塔的阻力系统主要决定于配水装置,烟气从配水装置上方进入,对配水装置区间段阻力不产生影响。塔内烟道和支撑件的覆盖面积不大(一般在15%以下),由此产生的阻力对总阻力的影响甚微,在工程上也可忽略不计。所以,烟气能够通过自然通风冷却塔顺利排放而对冷却塔原有的热力性能影响不大。
脱硫后的烟气通过冷却塔排放,烟道需穿过塔体进入冷却塔内部,因此冷却塔薄壳结构设计必须考虑塔体开设烟道孔洞对塔体强度的削弱。
湿法脱硫后的净烟气在通过冷却塔排放的过程中,净烟气中一部分水蒸气会遇冷凝结成雾滴,这些雾滴和烟气带入冷却塔的液滴部分会附着在冷却塔壁面上,这些液滴含有酸性腐蚀物质,将对混凝土壳体造成腐蚀。另外,大风天气,风会造成混合湿气下洗,对塔外壁造成腐蚀。因此,塔内部喷淋层以上和塔外部从上向下1/3的部分必须作防腐处理。通常采用玻璃鳞片树脂防腐涂层,德国已有多年成功运用的经验。引入冷却塔的净烟气烟道一般采用FRP管道,这种管道轻,并具有优良的防腐性能。
脱硫后净烟气通过冷却塔排放,可能对循环水产生两方面的影响。一方面,冷却塔的冷却能力可能会发生变化,一般会增加循环水的蒸发损失长。如果循环水排污量保持不变,循环水中的杂质和盐类的浓缩倍率将增加,为维持循环水的浓缩倍率不变,就必须增加排污量,两者都将导致循环水的补水量增加。另一方面,净烟气中残留的酸性气体(CO2、SO2、SO3、HCl、HF和NOx)和固体颗粒物,其中一部分会进入循环水系统,导致循环水pH值下降和可溶性盐类和固体悬浮物浓度的增大,如不采取措施,累计的结果将导致循环水质恶化。有两种控制循环水质的方法:一是增加排污量和补加水量;二是对循环水进行过滤、除盐处理和pH值调整。但德国的运行经验表明,烟气通过冷却塔排放对循环水水质影响不大,无需另设水质处理系统。
采用冷却塔排放湿烟气会对设备的总体布置带来困难,尤其对于已建电厂脱硫改造工程,现有烟道和冷却塔的距离往住较远。
冷却塔排放湿烟气工艺会增加冷却塔的投资成本,但有关方案论证资料表明,采用冷却塔排烟方案,总费用仍低于常规方案;因此采用冷却塔排放湿烟气不仅可行而且经济效益显著。
四、湿烟囱的结构材料
湿烟囱衬里材料的可靠性是至关重要的,如果湿烟气中腐蚀性液体和颗粒物对内烟道造成损坏以致衬里失效将造成严重后果。对于结构材料不适合湿态运行的现有烟囱,必须用合适的材料重新衬覆,或再建一个湿烟囱。对现有烟囱的改造不仅涉及到防腐内衬问题,而且涉及到烟囱原有的倾斜度和烟气流速是否有利防止烟气二次带水。另外,由于饱和湿烟气的温度低,烟囱可能出现正压或扩大正压区的范围。建干、湿两个烟囱,干烟囱排放高温原烟气,湿烟囱仅排放低温湿烟气,这样有利材料选择,可以有针对性地设计湿烟囱,运行方式较灵活,今后维修工作量较少,但占地大,投资成本高。
如仅采用一个湿烟囱,那么湿烟囱会遇到以下三种情况;①排放湿法洗涤后的低温饱和湿烟气;②在FGD系统设计为处理部分烟气的情况下,洗涤后的湿烟气与未处理的旁路原烟气混合排放;③必要时排放未处理的高温原烟气,甚至有可能要排放空气预热器故障时高达300℃以上的烟气,在大多数时间里,湿烟道和湿烟囱的内壁暴露于含有硫酸、亚硫酸、氯化物和氟化物的低pH值冷凝物和固体沉积物的腐蚀环境中。遇到上述②、③情况时,还要遭受高温以及由于高温使水分蒸发而形成的高酸性和高浓度氯化物、氟化物的腐蚀介质,因此对内衬材料的要求较为苛刻。制约湿烟囱材料选择的主要因素是耐高温、耐化学腐蚀。防止二次带水和今后的维修工作量以及经济性,这些因素又相互影响,例如采用FRP增强树脂衬移碳钢等材料,耐化学腐蚀和防止二次带水都不成问题,也较经济,但不耐高温,需定期维修。采用硼硅酸盐玻璃泡沫块衬覆碳钢可耐高温和化学腐蚀,价格适中,防二次带水性能良好,但定期修补工作量大。采用高镍合金如C-276、59号合金或钛板则投资成本高。
在美国,出于费用考虑,耐酸砖成为燃煤电厂衬砌内烟囱的主要材料,但近年趋向于采用高镍合金(C-276、59号合金或钛)复合板或墙纸工艺。前两种镍基合金对许多氧化性或还原性腐蚀介质都具有良好的耐腐蚀性,对无机酸,例如硝酸、磷酸、硫酸和盐酸具有优良的耐腐蚀性,是装有湿式FGD装置的火电厂金属烟囱最合适的防腐用材。
我国是贫镍国,但盛产钛,钛的密度低于镍,钛合金价格低于高镍合金,就耐一般腐蚀和耐由Cl-引起的局部腐蚀(点蚀和缝隙腐蚀)性能而言,这两种合金属同一等级。无GGH的吸收塔入口湿/干界面和早期采用旁路烟气加热饱和净烟气的烟道混合区是FGD系统中腐蚀最严重的区域,美国应用金属防腐材料的经验指出,C-级合金和钛是上述区域可以采用、性能最好的材料。有基于此,认为钛覆盖碳钢板也是湿烟囱可选用的防腐结构材料。例如,福建漳州后石电厂6×600MW燃煤机组配套的6台海水FGD系统采用湿烟囱工艺,电厂烟囱采用集束式,每3台机组设置一根集束烟囱,外烟筒为钢筋混凝土结构,由于采用大量海水洗涤烟气,净烟气温度较低,烟囱内烟道采用进口钛基合金板挂贴,钛板厚1.6mm,一个烟囱总造价8000万元。常熟华润电厂3×600MW FGD装
置也是湿烟囱工艺,采用多管钢内烟囱,烟囱内管采用国产钛
合金覆盖碳钢板(TA2+Q235),钛板厚1.2mm,烟囱总价格为5650万元。
需要指出的是,钛在还原性腐蚀介质(HCl、稀 H2SO4)中的耐腐蚀性下降,且随硫酸浓度和温度的增加,腐蚀率急剧增大。因此,钛是否适用于排放烟气温度较高的烟囱,例如排放经GGH加热后的烟气,是需要惧重考虑的。因为硫酸冷凝液、残留的HCl、HF以及它们的盐类是造成烟囱腐蚀的主要腐蚀物,随着烟温的提高,冷凝硫酸的浓度越高,对钛的腐蚀就越严重。
陡河电厂7号、8号机组的湿法FGD装置采用进口硼硅酸盐玻璃泡沫块衬砌,将原有的烟囱改为湿烟囱,玻璃泡沫块
的价格为1500元/m2。唐山电厂2×300MW新建FGD装置的
湿烟囱则采用国产耐酸釉面砖和玻璃钢复合防腐设计,该湿烟囱为单烟筒,防腐结构为钢筋混凝土、高温涂料+憎水珍珠岩保温层+呋喃树脂玻璃钢网片+耐酸胶泥筑砌耐酸釉面砖,造价较无防腐烟囱增加600万元。上述湿烟囱防腐设计在国外均有应用实例,性能得到证实。表13192列出了部分湿烟囱的材料特性,可供选材时参考。
表13192 湿烟囱结构材料特性

① 以二氧化硅和氧化硼为主要成分的玻璃,这种玻璃热膨胀系数
小,耐温差急变性和化学稳定性好,熔化温度低,易于成型。
五、国内脱硫烟囱防腐现状分析
1.脱硫烟囱防腐现状的总体评价
自2004年1月1日国家环境保护总局颁布实《火电厂大气污染物排放标准》以来,我国燃煤火力发电厂大部分采用石灰石石膏湿法脱硫工艺,相应脱硫烟囱所采用的防腐方案不尽相同。总体上看,目前我国脱硫烟囱防腐设计方案符合国情、是适宜的,但仍需优化和改进。脱硫烟囱运行时间不长,客观存在的问题严重,仍有待于时间的进一步检验。脱硫烟囱防腐存在问题主要表现在:
(1)涉及面广。目前我国脱硫烟囱所采用的防腐方案中很多方案由于防腐材料本身的质量、施工质量等原因造成烟囱防腐出现过不同程度的损坏现象。
(2)比例高。出现开裂、冲刷或脱落、酸液渗漏等问题,较严重的有国产泡沫玻璃砖、玻璃鳞片、OM涂料以及耐酸胶泥砌筑耐酸砖内筒等。
(3)时间短。根据相关规范的规定,烟囱结构应满足设计基准期50年要求,排烟功能设计应满足工艺系统设计寿命30年的要求。但有的工程仅投运2个月即发现由于泡沫玻璃砖脱落对钢内筒造成严重腐蚀;有的脱硫改造单筒烟囱工程项目投运后仅4个月即发生酸液沿烟囱外筒壁渗漏,造成对钢筋混凝土筒身腐蚀。
2.脱硫烟囱防腐工程实际使用情况
根据对脱硫湿烟囱防腐情况进行的调研以及技术交流情况,我国脱硫烟囱防腐工程实际使用情况如下:
(1)采用钛钢板或钛钢复合板的套筒式烟囱的运行情况相对良好,该防腐材料防腐、耐温、耐磨、抗冲刷性能都非常好,且使用寿命长,但价格昂贵,施工控制困难。需要严格检查焊接点,避免出现漏焊,造成焊接处发生腐蚀。
(2)在钢内筒内采用粘贴进口宾高德烟囱防腐内衬的烟囱运行良好;采用粘贴我国生产的以石英砂熔制玻璃为原料、含硼量大于12%的泡沫玻璃砖,粘结剂选用进口材料或国产硅树脂胶的运行情况良好;采用粘贴由废玻璃制作的普通泡沫玻璃砖不适用于运行工况下温度的交替变化,易开裂、冲刷和脱落;采用粘贴泡沫玻化砖与进口或国产硅树脂胶作为粘结剂的防腐内衬系统运行效果基本良好。
(3)采用泡沫玻化砖或耐酸胶泥砌筑耐酸砖的套筒式烟囱,在设置GGH的工况下运行情况良好。
(4)采用整体浇注料的烟囱尚未发现裂缝、冲刷及酸液渗漏现象,运行情况良好,但仍有待进一步观察。
(5)在钢内筒内喷涂玻璃鳞片、聚脲、OM涂料、萨伟真导致烟囱(烟道)防腐受到损坏的状况较多;采用RHF烟囱专用防腐涂料的烟囱运行情况基本良好。因此,工程中应选择性能良好的防腐涂料,以上防腐涂料不应该直接喷涂在以砌体为基层的烟囱内壁上。
(6)采用粘贴国产泡沫玻璃砖对旧烟囱进行的防腐改造项目,出现开裂、冲刷和脱落的状况较为严重。
3.烟囱防腐问题的原因分析
(1)施工质量没有满足相关设计、施工和验收规范,特别是对于粘贴防腐块材类的,由于粘贴量大,高空作业,加之监理旁站等措施不到位,是导致烟囱防腐出现问题的主要原因。
(2)部分防腐材料本身的质量不能满足脱硫后烟气环境的要求,目前我国应用于脱硫烟囱防腐的产品种类繁多,防腐产品的研发、应用及其成果的评审与鉴定等组织机构宽泛,难免鱼目混珠,以致使防腐产品质量存在问题。
(3)电厂对脱硫烟囱防腐的认识和重视程度不够,没有
将脱硫烟囱防腐纳入到脱硫设备管理的范畴,低价中标及不合理的工期要求十分普遍,且疏于巡检,导致部分脱硫烟囱防腐一旦发现问题即对机组运行带来影响,甚至危及烟囱结构安全。
六、旧烟囱防腐改造建议
旧烟囱改造的基本要求是当烟囱内壁出现冷凝酸液时,排烟筒内衬在设计使用年限内,不应受腐蚀而影响结构安全,更不能由于内衬腐蚀受损后,冷凝酸液渗出到钢筋混凝土外筒壁,危及烟囱结构承载能力。针对旧烟囱的防腐改造,应综合考虑以下因素:
(1)旧烟囱改造后服务年限。火力发电设备一般经济运行年限大约25年,设计使用年限一般35年。建筑结构设计使用年限50年。烟囱是发电机组运行的最后一个环节,由于目前环保标准的提高,烟囱逐渐被视为火力发电系统中的一个设备来对待。旧机组脱硫改造带来烟囱防腐改造问题,首先明确改造后的机组运行期限,以此来决定烟囱防腐的标准和防腐设计寿命。预计还要运行30年的烟囱与可能运行10年的烟囱,排烟筒内衬防腐改造显然应区别对待,更不能简单按新建发电机组湿烟囱防腐设计标准来处理。
(2)原来烟囱结构型式。从前我国非脱硫机组配套烟囱一般还是单筒烟囱或套筒烟囱。单筒烟囱内壁有砖砌的,或双滑后水泥砂浆抹面的。套筒烟囱的内筒有砖砌体的和钢的。在防腐改造前一定要查清楚原烟囱内衬的结构形式,一般没有考虑湿烟囱的防腐要求,对于不同的内衬表面,选择适合的防腐材料。对于套筒烟囱,钢排烟筒内壁只要增加耐酸胶泥或涂料作为隔水层即可。
对于过去采用釉面耐酸砖砌的排烟筒,由于国内采购的耐酸砖吸水率在12%~20%,远远不能解决湿烟囱防腐问题,则必须另增加隔水层和防腐层,或者拆除原内衬后,重新由泡沫陶瓷砖砌筑。对于单筒烟囱不论内衬是砖砌或是双滑形成的混凝土表面,都有必要采用2~3cm耐酸砂浆涂抹形成隔水隔气的防腐层。
(3)排烟囱内壁清理。旧烟囱改造首先要清理内筒表面的积灰和缺陷,砖砌内衬由于表面不平,还有一些砖存在破损,必须采用喷砂或高压喷水清除干净,然后填补缺陷。若采用涂料防腐,不可用水冲洗方法来清理,因为水冲洗后,内衬表面一定要晾干才能进行喷涂,延长施工时间。
(4)适用的运行工况。有些脱硫机组的烟气旁路仍然投运,烟囱排烟工况比较复杂,排烟筒防腐设计困难较大。防腐涂层应适用于脱硫工况(湿烟气,45~50℃)和非脱硫工况(干烟气,145℃)交替运行的条件,应保证在烟囱长期运行的145℃工作温度环境下,且短时间应能够承受180℃高温(每次半小时,每年3次)。很多有机材料为主的涂料是很难满足这些要求的。如果脱硫机组不设旁路,烟囱的烟气不出现混合排放,排烟筒防腐设计会相对简单。
(5)工期安排。200~300MW机组一般是2台锅炉共用一个烟囱,通过电力调度的计划安排2台锅炉同时停运大修时,才能进行烟囱内衬防腐改造,一般只能在45天以内完成全部改造工程。所以应该考虑冬季严寒和夏季多雨对防腐工程施工的影响,必要时在施工过程中供暖或加挡雨篷。
(6)现场施工条件。由于是生产改造,施工现场比较狭小,改造工程施工中,烟囱内部工程材料和机具的堆放、运输都会受到限制。如果在旧烟囱内加钢排筒时,应考虑钢内筒现场加工场地,烟囱内安装,焊接,吊装平台等实施条件。
综合考虑上述条件后,对旧烟囱做如下防腐处理。
(1)在进行防腐处理之前,为保证其使用的安全可靠性,请有建筑结构可靠性检测鉴定资质的单位对烟囱的结构进行可靠性鉴定。
(2)目前国内适合旧烟囱防腐改造的材料主要成分是有机树脂和无机材料的组合,有机材料为主的耐温较差,无机材料为主的耐腐和耐温性能较好,但粘接能力差、而且易出现裂纹。它们的组分配比会严重影响防腐材料的性能和耐久性。在旧烟囱防腐改造中应综合考虑。APC杂化聚合材料具有很强的抗腐蚀性、低吸水率、高抗渗性、高强度、抗冲刷性、耐高温、抗温变性、高粘结强度、高韧性、阻燃性、耐久性、整体性以及施工简便等特点,很适合旧烟囱防腐要求,推荐采用新型APC杂化聚合结构层技术。
第二十节 燃煤烟气湿法脱硫系统总体布置
一、概述
燃煤烟气湿法脱硫系统的总体布置,应在安全生产、节约用地、节省投资、降低运行成本的原则下,使整体脱硫岛布局紧凑、合理、通畅,便于施工,有利于检修维护。
对于现有电厂且未预留脱硫场地的项目,一般可因地制宜将脱硫装置布置于烟囱后,一般采用分区布置,吸收塔区域应尽可能靠近主烟道或结合主烟道进行改造,吸收剂制备区及石膏脱水区可适当远离炉后,也可考虑简化该区域的配置,如采用石灰石粉制浆、石膏浆液直接抛弃等方式,以减少占地。进行总体布置时,必须充分考虑电厂原有设施及其地下基础与管道,考虑施工的组织措施、电厂原有设施及新增脱硫装置的检修维护通道。
对于新建项目,脱硫设施应纳入锅炉尾部统一布置。不装GGH时,吸收塔应布置在烟囱主烟道上,一般布置在烟囱轴线上,若装GGH时,吸收塔尽量布置在烟气主通道。其他设施可就近布置在烟囱后的适当位置。若有旁路烟道,旁路烟道可插空布置。
二、脱硫岛总平面布置原则
(1)脱硫岛建筑物的平面和空间组合,应做到分区明确、合理紧凑、生产方便、造型协调、整体性好,尽量采用联合布置、多层布置,并与主体工程相协调,充分体现整体布局的合理性、和谐性、美观性。
(2)脱硫岛布置以吸收塔为中心,以工艺流程合理为原则,注意周围场地特征、设备特点和施工条件的影响,合理安排、因地制宜地布置,以便使管路压损最小,优化运行费用和运行程序,并使所有设备维修方便。
(3)脱硫岛主要建筑物的布置尽量为自然通风和采光提供良好条件,尽可能采用南北朝向,脱硫电控楼应避免西晒,有风沙、积雪地区要采取措施减少有害影响。
(4)石灰石、石膏堆场按生产类别布置。
(5)脱硫配电间位置的确定,要根据电源和负荷要求,缩短电力电缆长度。
(6)脱硫区主要通道宽度根据通道两侧建(构)筑物消防要求、工艺布置、人流和车流,各类管线敷设宽度、绿化设施布置、竖向布置等计算确定。
(7)脱硫岛布置应考虑防振、防噪声,在满足工艺要求的前提下,使防振、防噪声要求高的建筑物远离振动源和噪声源。
(8)FGD装置一般采用室外布置,寒冷地区考虑将循环浆液泵、增压风机、氧化风机等布置在室内,吸收塔采用紧身封闭。
三、脱硫岛竖向布置原则
(1)脱硫岛作为电厂的一部分,其竖向布置应服从于电厂的总体规划,与厂区协调一致。
(2)场地最小坡度及坡向以能较快排除地面水为原则,一般场地坡度不小于0.5%,困难地段不小于0.3%。
(3)场地排水根据具体条件,采用道路雨水口或场地雨水口接入下水系统的主干管窖井内。
(4)脱硫建筑物底层地面标高高出室外地面150~300mm,并应根据地质条件考虑建筑物沉降的影响。
(5)脱硫场地平整、建(构)筑物基槽回填、基槽余土调配纳入电厂主体工程统一规划。
四、脱硫岛主要建(构)筑物及总体布置
根据机组容量、燃煤含硫量、工艺要求不同,脱硫岛的占地面积会有较大的差别,由于工程的具体条件及系统的配置情况不同,建(构)筑物会有适当的增减或合并。按功能区分,脱硫岛主要分为四个区域,即吸收塔区域、吸收剂制备区域、石膏脱水区域、电控区域,后三者或全部合并成一个区域,或两两合并为两个区域。岛内的建(构)筑物也不尽相同,主要的建(构)筑物有增压风机房、GGH、烟道支架、吸收塔、浆液循环泵房、氧化风机房、浆液制备间、石膏脱水间、废水处理间、电控楼等。
吸收塔区域的主要建(构)筑物有增压风机房、GGH、烟道支架、吸收塔、循环泵房、氧化风机房、电控楼等。
烟气系统设备在主烟道后以烟气中心线左右对称布置,循环泵房、氧化风机房宜紧靠吸收塔布置。如条件不允许,氧化风机房可适当远离吸收塔,以实现工艺流程合理、烟道及大型浆液管道布置简捷的原则。
公用区域的建(构)筑物有浆液制备间、石膏脱水间、废水处理间、电控楼。后两者往往不单独布置,而是布置在石膏脱水间内,以减少占地。
与公用区域间通常设置一条岛内道路,如场地紧张,也可不设该通道。
烟气系统中有无GGH、是否设置增压风机、是否取消旁路烟道等,对吸收塔区域的布置有很大的影响,下面就这几种情况分别进行介绍。
1.典型的布置
典型的布置见图13201和图13202。图13
20 1为2×300MW机组脱硫系统典型布置图,增压风机、吸收塔和GGH前后分两列平行于主烟道中心线布置;在吸收塔的外侧布置浆液循环泵房,在GGH内侧烟囱的中心线上布置氧化风机房,2台机组所需的氧化风机均布置其内,工艺水箱也可置于其中;如为南方地区,工艺水箱可室外布置于氧化风机房与烟囱之间的场地上,吸收塔区域的宽度与两台300MW主机组相当。图13202为2×600MW机组脱硫系统典型布置图,布置基本上与2×300MW机组相同,但由于脱硫吸收塔区域的宽度一般大于两台600MW主机组的宽度,常常为满足电厂总体布置要求,要适当缩小吸收塔区域的宽度,因此调整循环泵房的布置方位,图13202中,1台机组的循环泵房旋转了90°布置于吸收塔的后方。另外,电控设备与氧化风机房可合并布置,底层布置氧化风机,其上布置电控设备。

箱
液
浆
故
事
—
1
1
;
箱
液
浆
石
灰
石
—
0
1
;
机
磨
球
式
H)
湿
G
—
G
9
;
有
仓
(
石
置
灰
布
石
型
—
8
典
;
统
间
系
料
硫
卸
脱
—
7
组
;
机
箱
W
水
M
艺
0
工
0
3
—
6
×
;
2
机
1
风
化
0
氧
2
—
3
5
;
1
泵
图
环
循
液
浆
—
4
;
H
G
G
—
3
;
机
风
压
增
—
2
;
塔
收
吸
—
1

箱
液
浆
石
灰
石
—
0
1
;
机
磨
球
式
湿
—
9
;
仓
H)
石
G
灰
G
石
有
—
(
8
;
置
间
布
料
型
卸
典
—
7
统
;
系
箱
硫
水
脱
艺
组
工
—
机
6
W
;
M
机
0
风
0
6
化
×
氧
2
—
5
2
;
泵
0
环
2
循
3
液
浆
1
—
图
4
;
H
G
G
—
3
;
机
风
压
增
—
2
;
塔
收
吸
—
—
—
1
循环泵房为单层结构,泵出口管可直接穿屋面固定支撑于泵房的梁上,循环泵房与吸收塔可适当靠近。增压风机与吸收塔之间需留出足够的通道,作为增压风机转子及电动机的检修吊装场地,氧化风机房与GGH间均留有消防通道。
此种布置烟道最简捷,场地利用非常充分,同时检修维护通道顺畅。
石膏脱水间和浆液制备间布置于吸收塔后方的公用区域,与吸收塔区域由岛内道路隔开。石膏脱水间底层为石膏库及箱罐、沟池,中间夹层布置废水设备;二层布置皮带脱水机层,真空泵也可布置在这一层;三层通常仅设一个柱距的构架,布置石膏旋流站和废水旋流站。浆液制备间通常可视为一单层建筑物,仅在磨机头部局部区域建筑物构架为三层,其目的是高位布置石灰石旋流站,使其底流和溢流有足够的坡度自流至磨机排浆罐和石灰石浆液箱。
公用区设置环形道路,充分考虑石灰石卸料、石膏运输的通道,并与吸收塔区相对独立,有利于工程实施,功能区域明确,便于脱硫岛分区运行管理。
图13201中,电控设备布置于石膏脱水间内,使其成为石膏脱水综合楼,并且是一个完整的四层建筑,其中一层为电缆夹层。图1320 2中,电控设备布置于GGH之间的氧化风机房的上部,该建筑物为三层结构,底层布置氧化风机,二层为电缆夹层,三层是控制室、电子设备间、配电室等。可通过步道通往GGH的运行层,便于运行检修维护。
2.不设置GGH
烟气系统中不设置GGH时,存在松散型和紧凑型两种典型的布置方式。
松散型布置见图1320 3,整个脱硫岛分三列布置于主烟道后。第一列为增压风机和吸收塔,平行于主烟道中心线布置。第二列为浆液循环泵房及电控楼,浆液循环泵和氧化风机布置于吸收塔后方的同一建筑物内,在烟囱的后方与浆液循环泵房之间布置电控楼;电控楼为两层结构,底层布置脱硫变及电气设备,二层为控制室、工程师站、热控电子设备间等。第三列为石膏脱水间和浆液制备间,在吸收塔区域和公用区域间设置4m宽的岛内通道。
整个脱硫岛布局较为宽敞。检修通道非常完善,运输道路也很畅通。施工条件十分理想,各构筑物基本为单元模块,独立车间,两个大区域可同时施工,互不影响,施工周期较短。
紧凑型布置见图1320 4,增压风机和吸收塔平行布置于主烟道后侧,两台机组的吸收塔向烟囱中心线靠拢,其间设一个楼梯构架,连接两座吸收塔的各层平台,将其余所有辅助设备整合于脱硫综合楼内,该建筑呈一凹形结构,两侧分别为浆液制备间和石膏脱水间,中间紧靠吸收塔处底层布置浆液循环泵和氧化风机,其上布置电控设备及控制室,两层之间设一电缆夹层。在综合楼底层的中心位置设置4m宽可以通车的通道,作为吸收塔区域的检修通道。
整个脱硫岛布局相当紧凑,但不拥挤。各系统配置一样不缺,检修运输通道一条不少。如脱硫场地比较狭小,可借鉴此种布置模式。其弊端在于施工组织非常困难,不能全面展开工作面,只能由里向外逐步后退,不适合施工工期要求较短的脱硫项目。
有的工程已将吸收塔出口烟道直接接入烟囱(吸收塔布置在烟气主通道上),可根据工程具体情况优化采用。
3.设置管式换热器
管式换热器不同GGH,由降温段和升温段两部分组成,分别布置于原烟气烟道和净烟气烟道上。管式换热器体积庞
大,还需考虑其检修时更换换热组件,给烟道布置带来很大的
困难,如图13205所示。
4.不设置GGH、无增压风机或旁路烟道
无增压风机或旁路烟道,吸收塔区域的布置变化比较大,典型的布置见图13206,烟囱中心线与主烟道中心线不在同一轴线上,而是向后布置,与吸收塔中心线在同一轴线,吸收塔出来的净烟气直接在高位接入烟囱。吸收塔布置在烟气主通道上,吸收塔的外侧布置浆液循环泵房,氧化风机也置于其中。
以上给出了六种脱硫岛的典型布置,布置方案是极具个性的,每个电厂总平面各不相同、外部环境千差万别,因此在进行脱硫岛规划布置时,需因地制宜、区别对待,考虑得越全面,布置将越完善。FGD装置典型布置占地面积见表13201。表13201 FGD装置典型布置占地面积

对于南方地区,空气湿热,箱罐均可布置于室外,大型设备也可室外布置,仅设抢修构架。北方严寒地区,设备、箱罐尽可能室内布置,依托辅助车间设置室内管廊对于管道的防冻来说也是非常好的选择。图13207为某2×600MW机组脱硫岛室内管廊布置。
五、脱硫岛各建(构)筑物的布置
1.增压风机房
增压风机房多设置为检修构架,仅在北方严寒地区考虑局部封闭。柱梁的布局需充分考虑烟道的支撑及风机叶轮和电动机的检修起吊。
2.浆液循环泵房
受浆液管道影响,浆液循环泵房应布置于吸收塔附近,为一单层建筑物,南方地区可考虑仅设浆液循环泵检修构架。
浆液循环泵多为单列布置,泵体靠近吸收塔,电动机侧留检修通道。
为避免汽蚀,泵入口大小头应设置成顶部平齐的偏心大小头。泵出口管道通常有两种布置方式:一是出口管垂直布置,穿过泵房屋面到达喷淋层,管道固定于泵房屋面框架梁;二是出口管在泵房内水平穿过侧墙,再垂直向上到达喷淋层,管道固定于泵房外侧的管道弯头处。检修起吊装置只能采用移动式电动葫芦,后者还可采用电动单梁(悬挂桥式)起重机,检修更为灵活方便。
3.氧化风机房
氧化风机房为一单层建筑物,其布置位置较为灵活,可靠近吸收塔布置,也可集中布置于两座吸收塔之间的空地,还可充分利用烟囱下部的空间。氧化风机多为靠近风机房一侧单列布置,另一侧留出检修通道,设备之间应留足隔音罩开门的空间。

箱
液
浆
故
事
—
0
1
;
箱
液
浆
石
灰
石
—
9
;
机
磨
球
式
H)
湿
G
—
G
8
;
无
仓
(
石
置
灰
布
石
型
—
7
典
;
组
间
机
料
W
卸
M
—
6
0
0
;
3
箱
×
水
2
艺
3
工
—
0
5
2
;
机
3
风
1
化
氧
图
—
4
;
泵
环
循
液
浆
—
3
;
机
风
压
增
—
2
;
塔
收
吸
—
1

箱
液
浆
故
事
—
0
1
;
箱
液
浆
石
灰
石
—
9
;
机
磨
球
式
H)
湿
G
—
G
8
;
无
仓
(
石
置
灰
布
石
型
—
7
典
;
组
间
机
料
W
卸
M
—
6
0
0
;
6
箱
×
水
2
艺
4
工
—
0
5
2
;
机
3
风
1
化
氧
图
—
4
;
泵
环
循
液
浆
—
3
;
机
风
压
增
—
2
;
塔
收
吸
—
1

)
器
热
换
式
管
置
机
设
风
(
化
氧
置
—
布
3
型
;
典
泵
环
组
循
机
液
W
浆
M
—
0
2
0
;
6
塔
×
2
收
吸
5
—
1
0
2
3
1
图

箱
液
浆
故
事
—
9
;
箱
液
浆
石
灰
石
—
8
;
)
机
机
磨
风
球
压
式
增
湿
无
—
(
7
;
置
仓
布
石
型
灰
典
石
—
组
6
机
;
W
间
M
料
0
卸
0
3
—
5
×
;
2
箱
6
水
艺
0
工
2
—
4
3
;
1
机
风
图
化
氧
—
3
;
泵
环
循
液
浆
—
2
;
塔
收
吸
—
1

4.浆液制备间
浆液制备间柱距宜按6m设计,3个柱距共长18m,跨距视磨机大小按8m或9m考虑,每跨设置一台磨机。该车间一般按三层考虑,第二、第三层仅磨机头部一个柱距,第一层布置磨机,层高不小于11m。为便于管道布置,设置一座石灰石粉仓时,磨机以镜像布置为宜,磨机间距为6~7m,布置3台磨机时,磨机顺列布置,间距为浆液制备间的跨度。旋流站布置于第三层,分配箱可布置于同一层,旋流站采用钢平台支撑。
分配箱的层高应结合石灰石浆液箱的位置,充分考虑溢流管能否自流到石灰石浆液箱。第二层为管道间。可局部封闭设
置 MCC。
在北方寒冷地区,成品石灰石浆液箱优先考虑室内布置,南方地区优先考虑室外布置。石灰石旋流站溢流管坡度应大于0°,底流管坡度应大于40°,底流管道的布置力求简单并注意不与单轨碰撞。
检修起吊单轨应兼顾磨机电动机、减速器、大齿圈、轴承等。
5.石膏脱水间
石膏脱水间一般按四层框架结构考虑,通常分为0m层、8m层(若无转运皮带,石膏库的上方此层取消)、11m层及18m层。一般柱距按不小于6m(标准8m)、跨距按9m设计。当石膏库库容较小(小于等于3跨)时,不设转运皮带。跨距小于12m时,石膏库中间宜不立柱,便于铲车行走及减少二次搬运量。
0m层设石膏库和滤液水箱。石膏库按仓库标准设计,一般不设窗户,在8m层圈梁下设小通气窗用于采光。石膏库按中间堆料设置挡土墙,挡土墙的设置要考虑土建的经济性,一般设为5m左右,原则上不超过6m。滤液水箱视具体情况布置在室内或室外。
8m层布置石膏转运皮带,滤布冲洗水箱及滤布冲洗水泵。滤布冲洗水箱布置在真空泵的下方,并尽量避免布置在上层梁的正下方,以充分利用层高。
11m层主要布置真空皮带脱水机、滤液接收罐、真空泵。真空皮带机采用镜像布置,两条真空皮带机共用一个检修平台。视石膏脱水间的宽度,决定滤液接收罐布置在真空皮带机的侧面或进料端,应尽量减小真空泵与滤液接收罐间的距离。
皮带机周围设挡水围堰,围堰按皮带机支墩外扩200~500mm考虑,在不影响通行的原则下尽量靠上限,围堰的高度为400mm。围堰内应考虑排水及防腐。
在遵照脱硫岛总布置原则下,将吊物孔与真空泵尽量布置在同一端。检修单轨吊应尽量布置在皮带机中心,若有偏移,距离也不宜超过500mm。
真空泵入口的液封对真空皮带机的脱水性能相当重要,且滤液接收罐内液体是自流进滤液水箱。运行时,真空泵入口前的滤液接收罐液面与滤液水箱液面的最小高差需为8.5m。
石膏旋流站底流50%含固量的浆液管道按30°坡度、溢流5%含固量的浆液管道按10°坡度考虑,底流管道的布置力求简短。
18m层布置石膏旋流站、溢流缓冲箱、废水旋流器给料泵及废水旋流站。由于溢流缓冲箱在运行中处于溢流状态,其容积可适当减小。废水旋流站也可按流程布置在箱罐顶部等其他部位。
南方地区的18m层可露天布置,仅设置遮雨防晒的顶棚。
6.废水处理间
废水处理间为两层建筑物,0m层布置废水缓冲储存箱、澄清/浓缩箱、清水箱、石灰乳箱、储酸罐等,对于南方地区,大型箱罐可考虑室外布置。需特别注意的是,盐酸卸料及储存区域必须单独设置围堰,并安装安全淋浴器等设施。4.5m层设置三联箱、加药装置、压滤机等。
7.电控楼
电控楼多为两层结构,占地面积为15m×18m。底层布置脱硫变压器及电气设备,二层为控制室、工程师站、热控电子设备间等。
六、脱硫岛各建(构)筑物联合布置
废水处理车间很少单独设置,通常与石膏脱水车间联合布置。北方严寒地区的工艺水箱及泵可设置于脱水车间的0m层,浆液循环泵房、氧化风机房、浆液制备间、石膏脱水间、废水处理间、电控楼均可两两联合设置,或多个车间组合在一起,抑或全部联合一体布置成为脱硫综合楼。当电控楼与氧化风机、浆液循环泵、磨机等噪声较大的设备布置于同一建筑物内时,控制室需充分考虑隔声设计,尽可能远离噪声源。
七、脱硫设备管线综合布置
脱硫岛内工艺管道、电缆等基本自成一体,与岛外联系较少,且岛内场地较紧张,需采用紧凑布置。除生活污水管、雨水管、冲洗排水沟等无压自流管(沟)及消防给水管、生活给水管等采用地下直埋外,其他工艺管道尽量采用架空布置,如浆液管、工艺水管、脱硫废水管、压缩空气管、电缆桥架等。电缆采用地下和架空相结合的布置方式,在场地狭小处尽量利用工艺管架架空布置,而在室外空地则为地沟布置。架空管架跨道路处的净空高度不小于5.0m,室内管道支架下通道处净空高度不小于2.2m。
吸收塔区域与公用区域间的管道采用架空综合管廊,各区域内的管廊尽量利用建构筑作为支撑。
图13208为某脱硫岛连接吸收塔与辅助车间的综合
管架图。图13209、图132010为前文所介绍的某
2×600MW机组室内管廊。
八、脱硫岛道路及绿化1.脱硫岛道路
脱硫岛的物料运输主要为石灰石和石膏,一般通过汽车运达脱硫岛内,石灰石浆液通过管道送至吸收塔内。石膏浆液通过管道回到脱水车间,脱水后的石膏经由汽车运出。
各物料区域设置专用的汽车回转场地,根据电厂的统一规划,沿专用通道进出厂区。

图13208 某脱硫岛综合管架

图13209 某脱硫岛室内管廊布置(一)

图132010 某脱硫岛室内管廊布置(二)
胶硫岛四周为电厂环形主干道,满足岛区内外交通运物要求。室外道路采用城市型混凝土路面,路面宽4.0m,路面汽车荷载为汽车-20级。
如场地条件许可,在吸收塔区域与公共区域之间设置岛内
道路,路面宽4.0m。
2.脱硫岛绿化
绿化是保护和美化环境的一项重要措施。植物不仅可以吸收电厂生产过程中产生的废气、噪声和粉尘,减少对周围环境的不利影响,而且可以调整厂区的小气候,为生产者提供一个安静卫生的生产和生活环境,从而有利于保护劳动者的身心健康和提高劳动效率,为文明生产创造良好条件。
脱硫岛区域布置非常紧凑,管线比较集中,粉尘较多,岛内设备场地基本为硬化地面处理,在岛区周边种植一些根系浅、有观赏价值、有一定抗SO2和滞尘效果作用的树种,整个电厂绿化率不小于15%。
第二十一节 土建及钢结构设计要点
湿法烟气脱硫工程中,主要建(构)筑物有电控楼、石膏脱水楼、磨煤机房、增压风机房、循环泵房等;构筑物有石灰石(粉)仓、石膏仓、GGH支架、石灰石浆液箱(池)等;大型设备基础主要有吸收塔基础、湿(干)磨基础、增压风机基础。
土建、钢结构设计按以下原则:根据生产工艺流程、使用
要求、自然条件、建筑材料、建筑技术等因素,结合工艺设计,进行平面布置、空间组合及建筑造型设计,并注意建筑群体与周围环境的协调,在满足相关规范的情况下,做到安全、适用、经济、美观。
一、建筑设计
脱硫建筑设计,因受场地工艺流程及其设备布置的约束,在建筑造型上一般不会有很大的发挥空间。总图设计应注重在满足工艺设备使用以及流程的要求下,要尽量使整个脱硫系统尽可能集中布置,力求使各建、构筑物的平面和空间组合,做到分区明确、合理紧凑、生产方便、造型协调、整体性好并节省用地。单体建筑设计,主要是配合工艺专业做好建筑物的平面布置与空间立面规划,使建筑物柱距、层高布置、房间功能分区布置合理,结构受力明确、合理。另外,建筑设计要注意楼梯及疏散通道的设置,建筑材料的选择,满足安全、防火规范的要求。
脱硫建筑物,如石膏脱水楼、电控楼等,主要楼梯一般采用钢筋混凝土结构,室内楼梯的宽度不小于1200mm,扶手采用高1.05m、直径不小于50mm的不锈钢管,立杆采用直径不小于32mm的不锈钢管。室外事故疏散梯,一般采用钢梯,其梯段宽度800mm,钢梯的倾角不宜大于45°。
在楼面的所有洞口处、平台、楼梯平台及没有伸至墙壁的楼面及平台的四周,均需设置带护沿的围栏,以作保护,护沿高度不低于100mm,扶手、栏杆的高度宜为1.2m。
脱硫构筑物的楼梯可采用钢筋混凝土结构,也可采用钢结构梯段及平台。如采用钢梯,其梯段宽度不宜小于800mm,钢梯的倾角不宜大于45°,扶手高度为1.05m(20m以上不小于1.20m),采用直径不小于38mm的钢管,立杆采用直径不小于25mm的钢管。设备平台楼梯栏杆设计同钢梯。
各建筑物的人行通道在管道、风道及其他障碍物之下的净
空不小于2.2m。
要注重防腐设计,使用、装卸或储存化学药品的地方均将按防腐设计,其方法是对地面、墙壁、天棚、门窗及所有建筑配件进行适当的,必要的保护。
脱硫控制室楼层及其他必要的楼层应设置更衣室及洗手、卫生间。
脱硫建筑物各车间的0m及各层,在适当位置应布置洗手盆,洗污池。有积水的楼面或需要水冲洗时,楼面应设防水层。
电子设备间、控制室和电缆夹层等都应设置向外开启的防火门。
控制室的墙,楼面及天棚应能防振,各构件有良好吸声隔热性能。为了改善照明,吊天棚的结构与嵌入式灯具应相协调。室内照度符合设备人工照明的要求,在仪表盘上不出现眩光。
控制室墙面涂料一般采用吸声、亚光、硬质的耐久性材料。
墙体、顶棚和地面具有良好的隔(吸)音和热工性能,并防止产生粉尘,保证控制室内空调系统的有效运行。
控制室及电子间需消声至55dB(A)以下。
在建筑物的造型和色彩以及建筑装饰标准上,应力求与主体工程相适应。
二、建筑结构形式
脱硫系统的建筑属于工业建筑,其建筑结构形式主要根据结构的使用功能、自然、环境条件决定。一般来说,电控楼、石膏脱水楼、磨机房等可采用现浇钢筋混凝土框架结构,混凝
土楼面;石膏仓、石灰石(粉)仓可采用钢筋混凝土筒仓结构,一般大容量筒仓宜采用筒壁支承圆筒仓,小容量的仓可采用框架柱支承结构,石灰石(粉)仓锥斗一般采用钢结构;石膏仓、石灰石(粉)仓,根据需要也可采用全钢结构;石灰石浆液箱一般采用钢结构,石灰石浆液池则采用钢结构混凝土结构;GGH支架、烟道支架有采用钢筋混凝土结构,也有采用钢结构。一般来说,钢结构相对来说较为环保、结构自重轻、受拉性能好、施工速度快,建筑造价相对较高,其缺点主要是耐火极限低、受压性能差。混凝土结构则相反,我国现阶段,脱硫建筑物一般采用现浇钢筋混凝土框架结构,构筑物则根据结构的受力特点、环境状况、项目业主的喜好决定,一般来说,钢结构造价相对较高。
三、结构设计
脱硫系统的建(构)筑物一般均为丙类建筑,脱硫建(构)筑物的结构设计应遵循安全、经济适用原则,结构工程师应充分利用已有知识、设计经验,注重开展结构整体概念设计,努力在满足工艺设备、管道等布置要求下,根据建筑材料的特性,各建(构)筑物的受力特点,优化结构布置,建立合理力学模型。
脱硫系统的建(构)筑物设计,不能简单地套用民用建筑规范,结构工程师需针对不同结构选择具有针对性的设计规范、标准。一般情况下,石膏脱水楼、电控楼框架可按《钢筋
混凝土设计规范设计》GB50010—2010);GGH支架、烟道
支架,如采用钢筋混凝土结构,也应按GB50010规范执行,但对层间位移、位移角的控制,可比多层房屋设计规范适当放宽;石灰石(粉)仓、石膏仓,如采用钢筋混凝土结构可参照
《钢筋混凝土筒仓设计规范》(GB50077—2003)设计,如采用
钢结构则可参照《粮食钢板筒仓设计规范》(GB50322—2011)设计;对于转动设备,如增压风机、循环泵、磨机等,则应按动力基础规范GB50040执行。
结构设计应根据分析对象的特点,建立合理的力学模型,工程设计中不乏因力学模型假定不合理,造成较大浪费或造成重大设计失误的项目。结构工程师应特别注重力学模型的构建,工业建筑因要满足工艺设备、管道布置需要,理想的结构布置很难实现,这就要求结构工程师利用已有知识,多动脑筋,采取结构措施,在满足工艺设备、管道布置需要的情况下,优化结构布置,使结构整体最优,结构受力最合理。
结构设计、分析应选择合适的设计软件,一般来说,对于房屋建筑可采用国内通行的PKPM软件;GGH支架、烟道支架等构架一般宜采用空间结构分析软件;对于石灰石(粉)仓,石膏仓等板、仓结构,小容量筒仓,一般可按规范公式计算,对大容量筒仓则宜采用有限元进行分析。
当结构构件放振动力荷载时,则应进行动力验算;地震区应进行抗震验算。