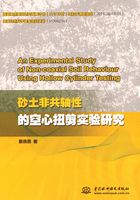
2.3 Hollow Cylinder Apparatus
2.3.1 Introduction
It has been widely recognized that soil behaviour depends on the stress path.Therefore,the stress path method or a generalized model for behaviour which incorporates the dependence on stress path should be used to predict the performance of soil or soil-supported structure(Lambe,1967).In order to study generalized mechanical characteristics of granular materials,a device with the ability to monitor and independently control the principal stresses and the direction of the major principal stress is urgently required.The conventional laboratory testing devices(e.g.triaxial cell,direct shear box,plane-shearing apparatus)are not capable of rotating the major principal stress direction and controlling the relative magnitude of the intermediate principal stress.
In this situation,a hollow cylindrical apparatus(HCA)is an extremely valuable tool for studying constitutive behaviour under generalized stress conditions.The HCA allows independent control of the magnitudes of the three principal stresses and rotation of the major-minor principal stress axes while recording the specimen deformational and pore pressure responses.When each of these boundary stresses can be controlled independently,both the principal stress direction,α,and the relative magnitude of the intermediate principal stress,b,can be controlled,thus the HCA can facilitate more generalized stress path testing than the conventional test apparatus.It is also possible to control(or measure)the pore water pressure and apply back pressure,so that drainage conditions can be controlled and both drained and undrained tests can be performed.As a result,the HCA offers an opportunity of extending the stress path approach to include simulation of both principal stress rotation and variation in intermediate principal stress,as well as conducting fundamental research into the effect of principal stress rotation under a reasonably generalized stress state.Moreover,laboratory tests normally performed in the other devices,such as in triaxial compression and extension or simple shear tests can be simulated with the HCA.
2.3.2 Principles of Hollow Cylinder Testing
Figure 2.3 illustrates idealized stress conditions in a hollow cylindrical element subjected to axial load,W,torque,MT,internal pressure,Pi,and external pressure,Po.
During shearing,the torque,MT,develops shear stresses,τθz and τzθ(τθz=τzθ)in vertical and horizontal planes,the axial load,W,contributes to a vertical stress,σz.Pi and Po determine σr,σθ.The relationship between σr and σθ is established by the differences between Pi and Po.
where r is the radial distance to a point in the hollow cylinder,and dσr is the radial stress increment.When Pi=Po,σr becomes identical to σθ.
The state of stress in a hollow cylinder test is defined with reference to cylindrical coordinates,in terms of the stress components shown in Figure 2.4.
Figure 2.4 Idealized stress and strain components within the HCA subjected to axial load,W,torque,MT,internal pressure,Pi,and external pressure,Po.
(a)hollow cylinder coordinates;(b)element component stresses;(c)element component strains;(d)element principal stresses
(after Zdravkovic and Jardine,2001)
Since the stresses will not be uniform across the wall of the cylinder for various loading conditions,to consider the hollow cylinder as an element,it be comes necessary to calculate average stresses,.Hight et al.(1983)used the following expressions:
Average vertical stress
Average radial stress
Average circumferential stress
Average shear stress
In hollow cylinder tests,the radial stress,is usually equal to the in termediate principal stress(σ2).The major and minor principal stresses,σ1and σ3,are observed from the average stress components
and
as fol-lows:
By regarding the specimen as a single element,the state of strain is presented in cylindrical coordinates in terms of the following components:
Also,it is necessary to calculate the average strains.According to the paper of Hight et al.(1983),the average strains are calculated using the following equations:
Average axial strain
Average radial strain
Average circumferential strain
Average shear strain
Where the definitions of average stresses and strains are shown in Figure 2.5.
Figure 2.5 Definitions of average stresses andstrains
(after Hight et al.,1983)
Since the average values of εz and γθz are based on strain compatibility only,the expressions for the average strains are valid and independent of the constitutive law of the material.The average values of εr and εθ are based on a linear variation of radial displacement across the wall of the specimen.In the hollow cylinder test,the radial strain(εr)is usually the intermediate principal strain,ε2.The major and minor principal strains can be observed from the average strain components:
Parameters α and b are two variables of stress path to describe fundamentally different aspects in the applied state of state of stress.α(as shown in Figure 2.4(d),is the inclination of major principal stress direction with respect to the vertical axis,which can be varied from 0° to 90°.It can be computed from the known average stress components:
b is defined as the relative magnitude of the intermediate principal stress,which can be varied from 0 to 1:
For the particular case of equal internal and external pressure,Pi=Po=P,σr and σθ are usually assumed to be equal to P.From Equation(2.10)σ2 is equal to P as well.Therefore,changes in the α angle are accompanied by changes in magnitude of b,When Pi=Po:
The direction of strain increment αdε can be calculated from the incremental strain components:
The amount of non-coaxiality was defined as the difference between the directions of principal stress and that of principal strain increments as αdε-α.
2.3.3 Stress Distribution in Hollow Cylinder Specimens
Even though hollow cylinder devices offer highly promising capabilities for the study of soil behaviour,their use has been subjected of criticism.These objections arise principally due to the non-uniform distribution of stresses and strains within the specimens.Stress non-uniformities occur across the wall of a hollow cylinder due to the specimen geometry,end restraint,the application of torque or different internal and external pressures.The tested specimen size affects significantly the stress non-uniformity level.When the wall thickness is reduced or the inner radius is increased,the stress distribution becomes more uniform(Sayao and Vaid,1991).
Because it is not easy to measure either the stresses or the strains across the wall of the hollow cylinder directly,it becomes essential to set bounds to the differences between the calculated and real averages and the magnitude of deviations from the real averages.By using the finite element method and assuming that material behaves as either isotropic or elasto-plastic(modified Cam-clay),Hight et al.(1983)defined the non-uniformity coefficients β1 and β3 for individual stress components,as shown in Figure 2.6.The magnitude of the difference between calculated and real stress average can be characterized by normalized parameter β1:
where σ* is the real average,σ is the calculated average and σL,which is defined as,is a measure of the stress level.Therefore β1 is inversely related to accuracy.β3 is the parameter to quantify the level of non-uniformity of stresses:
where σ(r)is the distribution of the particular stress,σz,σθ or τθz under consideration across the hollow cylinder specimen.β3 may be used to minimize the difference between the actual stress distribution and the real average.
For differences in strain averages and strain non-uniformities,similar definitions for β1 and β3 are used.According to Hight et al.(1983),the magnitudes of β1 and β3 are dependent on stress state,specimen geometry and the constitutive law of the specimen's material.The authors recommended keeping stresses within a limit where the ratio of outer to inner cell pressures is 0.9<Po/Pi<1.2,and keeping β3 below 11%.
Figure 2.6 Definitions used for stress non-uniformity and accuracy
(after Hight et al.,1983)
Vaid et al.(1990)analyzed non-uniformities in hollow cylinder specimens by using a linear elastic model.By comparing the results with those of a finite element method,they argued that the use of the parameter β3defined by Hight et al.(1983)could lead to an underestimation of the HCA non-uniformities and proposed a different stress non-uniformity parameter across the wall of the specimen in terms of the stress ratio R(R= σ′1/ σ′3):
where Rmaxand Rminare the maximum and minimum stress ratios and Ris the average value.
Figure 2.7 shows a comparison of the two definitions of non-uniformities for two stress states.The specimens had an outer radius of 7.1cm and an inner radius of 5.1cm.The result shows that the level of stress non-uniformities increases with the increase of R.The authors suggested that the stress non-uniformities were considered acceptable if the maximum difference between Rmax and Rav was below 10%,which corresponds to a value βR≤ 0.2.In order to keep the non-uniformities levels acceptable,they also recommend keeping the stress ratio R below 2.5.The authors also pointed out,that the assumptions used to define the non-uniformities of Hight et al.(1983)were inconsistent as an elastic constitutive law was used for the stress component of τθz while a plastic law was used for the other components.By applying the elastic law to τθz,the idea that keeping outer and inner cell pressures constant would help to minimize the stress non-uniformities,would not be suitable.
Figure 2.7 Effect of stress ratio level on non-uniformitycoefficients
(after Vaid et al.,1990)
Wijewickreme and Vaid(1991)indicated that relatively large stress and strain non-uniformities could arise in hollow cylinder specimens,particularly in the small stress/strain(near elastic)region,for certain loading conditions.On the other hand,when large differences between Po and Pi occurred,the stress non-uniformity across the wall became very large.According to their study with non-linear elastic soil,the stress non-uniformity coefficient βR only increased continuously with the stress ratio R at lower values of R.βR reached a peak point or even started to decrease when R was higher.
Menkiti(1995)and Porovic(1995)found that in cases free from end restraint,the equations defined by Hight et al.(1983)to calculate average stresses and strain were sufficiently accurate for interpreting hollow cylinder tests.Furthermore,very good agreement was observed between the stress-strain and strength response of hollow cylinder simulations and a uniform single element.
Rolo(2003)used a classical elasto-plastic non-linear,modified Cam-clay soil model with a finite element method to analyze most of the features that were thought to influence the development and magnitude of non-uniformities.The non-uniformity increased as the specimen approached the failure surface,which agreed with the observations by Hight et al.(1983)on specimens with fixed ends.The specimen with free-ends resulted in more uniform conditions.The results revealed that non-uniformities could result in either over or underestimation of certain stress and strain parameters.
Naughton and O'Kelly(2007)studied the stress distribution in smaller sand specimens with the dimension of I.D=71mm,O.D=100mm,H=200mm.The stress non-uniformity levels were found to be acceptable with the ratio of outer and inner cell pressure Po/Pi kept between 0.9-1.2,as well as the stress ratio R kept under 2.0.
2.3.4 Specimen Geometry
The uniformity of the stress distribution across the wall of hollow cylinder specimens is affected by the specimen geometry,both the curvature and end restraint.This result came from the detailed study of stress distributions using both isotropic linear elastic and plastic formulations to represent the soil in specimens of different geometries under different load combinations.A suitable height of the specimen can engender reasonably uniform distributions of stress(Hight et al.,1983).The differences between real and calculated averages of stress and strain were attributed to the selected specimen geometry and the stress path.As the ratio of inner to outer radii,ri/ro,approaches unity,both β1 and β3 reduce.Figure 2.8 was produced by Porovic(1995)by assuming a linear variation of applied shear stresses,τθz,and a linear elastic constitutive law,to display the ratio of maximum and minimum shear stresses to average shear stress for three different specimen dimensions.As the diagram shows,the level of non-uniformity for a fixed wall thickness would reduce with the increase of specimen diameter.Therefore,the degree of the stress difference between the calculated and real average was minimized as the inner radius of specimen increased.The selection of a suitable geometry for the hollow cylinder specimen would reduce stress non-uniformities to an acceptable level.Saada(1988)also quoted that selecting particular specimen geometry played a major role in reducing non-uniformity of stress distribution.
Figure 2.8 Shear stress distribution in hollow cylindertorsional shear test specimens
(after Porovic,1995)
Firstly,for sand specimens,an appropriate wall thickness should be applied to meet the following criteria:
1)A wall thickness sufficiently large enough relative to the maximum grain size of the tested specimen so the failure mechanisms would not be constrained.
2)A specimen volume sufficiently large in relation to the potential volume change resulting from membrane penetration.
3)A uniform density across the wall.
In order to determine a reasonable specimen geometry,based on elasticity theory and the assumption that the central zone,free from end effects should be the same length as the zone influenced by the platens,Saada and Townsend(1981)suggested the following criteria for the specimen geometry:
Height:
Inner radius ri:
where H is the height,ri and ro are the inner and outer radii of the specimen,and n is the ratio of inner and outer radii.
The criteria proposed by Sayao and Vaid(1991)are as follows:
Wall thickness
Inner radius:
Height:
2.3.5 Membrane Penetration Errors
In the hollow cylinder test,rubber membranes are used to enclose the specimens.The effect of membrane penetration on the external measurement of volumetric deformations is attributed to the flexible membrane penetrating into or withdrawing out of the external voids of the soil specimen.The membrane penetration(MP)may influence the computed specimen's volume change in a drained test,and the magnitude of the pore water pressure measured in an undrained test.Therefore this effect should be accounted for to make a confident assessment of actual stress-strain behaviour of saturated granular materials in a test.For materials of medium sand size having mean particle size of D50≥ 0.1mm,particularly for the large diameter specimens,correction for the membrane penetration is of great importance and should be applied(Molenkamp and Luger,1981).
Studies of the effect of membrane penetration have been undertaken and the particle size of the material is identified to be the major factor to influence the membrane penetration(Frydman et al.,1973).
Theoretical expressions for the unit membrane penetration suggested by Baldi and Nova(1984)and Kramer and Sivaneswaran(1989)are as follows:
where νMP is the unit membrane penetration(in mm);AMP is the surface area of membrane(in mm);d is the mean particle size,D50(in mm);D is the Specimen diameter(in mm);Vsoil is the volume of soil specimen(in mm3);Em is the Young's modulus of membrane(in kN/m2);tmis the thickness of membrane(in mm);σ′h is the effective confining pressure(in kPa).
A new approach for the assessment of MP was obtained from the differences between measured volume strain of the specimen and the volume of the inner chamber using a single hollow cylindrical specimen under hydrostatic loading by Sivathayalan and Vaid(1998).The proposed expression for the unit membrane penetration is:
where εm is the unit membrane penetration;ΔVsr and ΔVir are the measured volume changes of the inner chamber and the specimen,respectively;n is the ratio of the outer to inner radii of the specimen,and Aim and Aom are the surface areas of the specimen covered by the inner and outer membranes,respectively.
Kuwano(1999)evaluated the apparent volumetric strains due to MP over the vertical sides of the specimens using Ham River Sand specimens with rough and lubricated ends.By comparing the measured volume deformations with a conventional volume gauge and with local instrumentation,she obtained the following relationship for νMP based on isotropic loading/unloading/reloading tests:
where CMP is a parameter that depends on specimen size and density,membrane thickness and elastic modulus,and on particle shape and size;σ′h and σ′h0 are the current and initial effective confining pressures.From Kuwano's experiments,CMP is 0.015mm for 100mm diameter specimens of Ham River Sand encased in a 0.5mm thick latex membrane.Kuwano(1999)found that Equation(2.32) matched the expressions suggested by Baldi and Nova(1984)and Kramer and Sivaneswaran(1989)very well.
2.3.6 Previous Experimental Studies Using HCA
The HCA is becoming a popular testing device all around the world for geomechnical research.Hight et al.(1983)was one of the researchers who first introduced a hollow cylinder apparatus for investigating the effects of principal stress rotation in sands and clays.His colleagues then used it to investigate anisotropy and principal stress rotation in drained and undrained sand(Symes et al.,1982,1984,1988).HCA has been widely used to study the anisotropy and non-coaxial behaviour of sand(Ishihara and Towhata,1983;Symes et al.,1984,1988;Miura et al.,1986;Pradel et al.,1990;Vaid et al.,1990;Gutierrez et al.,1991,1993;Gutierrez and Ishihara,2000;Zdravkovic and Jardine,2001;Li and Dafalias,2004;Lade et al.,2009).Vaid et al.(1990)presented a HCA with the following dimension:15.2cm(O.D)×10.2cm(I.D)×30.2cm(H),including the design,performance and utility of the equipment.Sayao and Vaid(1996)then investigated the effect of intermediate principal stress on the deformation of Ottawa sand by using the same HCA.The tests were performed following different stress paths with varying parameter b.
The HCA has also been used to study the characteristics of clay.Silvestri et al.(2005)used the HCA to study typical undrained extension behaviour of saturated clay.The HCA was modified from a hydraulic triaxial cell to permit testing of thick-walled cylindrical specimens of different dimensions.The specimens were prepared with the external diameter 100mm,internal diameter 50mm,with height of 100mm,and external diameter 127mm with internal diameter 38mm with the same height.Two different HCAs were employed by Nishimura et al.(2007)to investigate the shear strength anisotropy of natural London Clay from Heathrow Terminal 5.One of the apparatus had a dimension of 70mm(O.D)×38mm(I.D)×(170-190)mm(H),and the dimension for the other one was 100mm(O.D)×60mm(I.D)×200mm(H).Rolo(2003)used the HCA to study the stress-strain and strength anisotropy of a sand-clay mixture.The tests involved a range of fixed values of α and b.