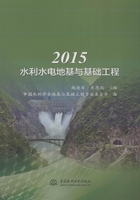
混凝土防渗墙工程
西藏甲玛沟尾矿库119m超深塑性混凝土防渗墙施工
刘典忠,潘文国,邢书龙,杨永强,潘金伟,肖恩尚,孙亮
(中国水电基础局有限公司)
1 引言
西藏自治区墨竹工卡县驱龙矿区铜多金属矿开发建设工程由选矿厂、尾矿坝(库)含防渗墙、1号拦水坝(库)含防渗墙、溢洪道、库外排水隧洞、库内排水(井)隧洞、下游拦沙坝、回水池、库外公路等工程组成。
尾矿库 (坝)采用 “中线法”筑坝,粗砂区下游坝坡1∶3.5,中线处设置基础坝,采用面板堆石坝,坝顶标高4080m,坝高90m,坝顶宽5.0m,上下游边坡均为1∶1.6,坝轴线长817m,基础坝 (又称初期坝)上游坝坡坡脚以下基础设置0.8~1.0m厚的塑性混凝土防渗墙,深入基岩1.5~2.0m;尾矿库 (坝)上游坝坡坡脚以下基础设置0.8~1.0m厚的塑性混凝土防渗墙,深入基岩1.5~2.0m。
本项目防渗墙总工程量5.5万m2,其中厚0.8m墙1.76万m2,厚1.0m墙3.74万m2,最大深度达到119m。
甲玛工程作业面最大海拔高度4100m,寒冷多风、常年缺氧。且防渗轴线多位于沼泽区,局部基础炭质土接近7m,冻土深度超过1m,施工机械效能下降严重;生态环境脆弱,环境保护压力很大。
2 地质条件和防渗墙设计要求
2.1 地质条件
防渗墙中心线处出露地层有:侏罗系中统叶巴组二段(J1-2y2)糜棱岩,第四系更新统冰水堆积(Qpfgl)卵石、黏质卵石、黏质砾砂,第四系坡积(pdlQ)碎石、角砾、粉土,第四系冲洪积(hal+plQ)漂石、粉土、泥炭质土。
2.2 防渗墙设计要求
充分结合库区防渗要求,对基础坝设置垂直防渗,为防止坝基产生渗透管涌破坏和尾矿渗滤液下泄,在坝基上游坡脚12m处设置一排地下连续墙,连续墙墙体采用塑性混凝土。防渗墙施工轴线桩号为0.00~966.09m,全长966.09m。设计要求地下连续墙深入强风化糜棱岩以下1.5~2.0m,地下连续墙渗透系数要求在5×10-6~5×10-7cm/s;连续墙墙深和墙宽对应关系见表1,主要设计指标见表2。
表1 甲玛防渗墙墙深与墙宽对应关系表

表2 防渗墙主要设计指标明细表

3 防渗墙施工工艺(图1)
图1 甲玛防渗墙施工工艺流程图
4 防渗墙施工
4.1 槽段划分
根据工程特性,综合考虑地层、墙体深度等,本防渗墙槽段划分为两种形式。
(1)126.07~295.65及755.10~881.12段。槽段一期槽、二期槽槽长均为6.4m,墙厚0.8m,分为3个主孔和2个副孔,主孔为0.8m,副孔为2.0m;槽段防渗墙典型槽段划分见图2。
图2 深度小于60m槽段防渗墙典型槽段划分图
(2)295.65+~755.10段。对于深度大于60m的槽段,墙厚1.0m,一期、二期槽段长度均为6.6m,主孔1.0m,副孔1.8m。其防渗墙典型槽段划分见图3。
图3 深度大于60m防渗墙典型槽段划分图
4.2 成槽方法
4.2.1 造孔施工
本工程防渗墙成槽采用“两钻一抓”法。主孔采用冲击钻机钻凿成孔,副孔覆盖层部分采用抓斗抓取,底部基岩采用冲击钻机钻凿。槽孔施工过程中孔斜控制及槽孔验收采用钻具悬垂法测量孔斜。
4.2.2 入岩深度检查
接近设计基岩面1m时,每50cm取样一次。进入基岩后,每30cm取样一次,编号保存。据以判断和计算入岩深度;左右岸陡坡段或对基岩面发生怀疑时,则采用岩芯钻机取岩样进行验证。
4.2.3 固壁泥浆
采用改进型MMH正电胶基高性能泥浆,提高了固壁效果,保证了深墙的顺利施工。
4.2.4 清孔换浆及接头孔的刷洗
(1)清孔换浆。采用气举反循环法,即借助空压机输出的高压风进入排渣管经混合器将液气混合,利用排渣管内外的密度差及气压来升扬排出泥浆并携带出孔底的沉渣。结束标准如下:
清孔换浆结束1h后,槽孔内淤积厚度不大于10cm。使用膨润土时,孔内泥浆密度不大于1.15g/cm3;泥浆黏度不小于32s(马氏);含砂量不大于6%。
(2)接头刷洗。接头孔的刷洗采用具有一定重量的圆形钢丝刷子,通过调整钢丝绳位置的方法使刷子对接头孔孔壁进行施压,在此过程中,利用钻机带动刷子自上而下分段刷洗,从而达到对孔壁进行清洗的目的。结束的标准是刷子钻头基本不带泥屑,并且孔底淤积不再增加。
4.3 混凝土配合比和浇筑
4.3.1 混凝土设计指标
混凝土防渗墙墙体材料性能指标满足C5塑性混凝土的要求。混凝土物理特性指标要求如下:
(1)入槽坍落度18~22cm。
(2)扩散度34~40cm。
(3)坍落度保持15cm以上,时间应不小于1h。
(4)初凝时间不小于6h;终凝时间不大于24h。
(5)混凝土密度不小于2100kg/m3。
4.3.2 配合比
甲玛项目最早采用的是膨润土基塑性混凝土,在施工过程中发现有地层中存有质量较好的土粉,随即进行试验并最终获得成功,节约了成本,提高了效益。对此,我们将另文详述。本文仅将最终的黏土基塑性混凝土配比列于表3,请参考。
表3 甲玛防渗墙塑性混凝土配比表

4.3.3 混凝土浇筑
采用直升导管法,浇筑过程按《水工建筑物防渗墙施工技术规范》(DL/T 5148—2012)执行。
4.4 墙段连接
墙段连接采用接头管法,即一期槽孔清孔换浆结束后,在槽孔端头下设接头管,混凝土浇筑过程中及浇筑完成一定时段之内,根据槽内混凝土初凝情况逐渐起拔接头管,在一期槽孔端头形成接头孔。二期槽孔浇筑混凝土时,接头孔靠近一期槽孔的侧壁形成圆弧形接头,墙段形成有效连接。
5 地下高压气体对墙体破坏的预防
5.1 地下高压气体的基本情况
在尾矿坝区位于甲玛沟沟床中部的钻孔施工中,在钻进中、终孔起拔套管后均存在不同程度的涌水、气体溢出,在第四系覆盖层及基岩中均有此现象,水头涌出地面高度达5.0~13.0m,实测水头压力0.20~0.50 MPa,气体主要分布在0~45m深度之间。
分别采集水、气送检,结果表明:钻孔中喷出的气体主要成分与含量分别为CO2 (63.37%%~71.59%%)、N2(22.85%%~29.51%%)、O2(5.33%%~7.15%%)及少量的氦气、氩气、甲烷;地下水水温5~7℃,水化学类型为 HCO3—Ca,矿化度1749.50~2651.50mg/L,属低矿化中性水,其 HCO3-离子含量1244.85~2945.72mg/L、Na+离子含量54.88~254.22mg/L、Cl-离子含量4.70~50.15mg/L、偏硅酸含量91.42~105.18mg/L、游离CO2含量73.74~599.50mg/L,并分别检出锶、砷、汞等。
由于混合气体分布广,压力大,对防渗墙造孔成槽势必产生破坏作用,必须进行处理。
5.2 预防设计方案
根据地质资料,在防渗墙上游侧距防渗墙轴线15m处,沿平行轴线位置设置10个减压井,减压井间距为50m;深度为50m,大于所含气体最大深度5m;直径采用φ300的带孔钢管作为滤管,滤管上梅花孔布置φ3的孔,滤管外侧用土工布进行包裹。然后在滤管外侧用反滤料进行充填,保证该滤管具有自然排水功能。
5.3 减压井施工
5.3.1 减压井施工工艺
减压井施工过程包括:测量、造孔、清孔、下井管、回填反滤料和洗井等多项施工流程。
5.3.2 减压井施工方法
(1)井位测量。根据三角控制网点和水准控制网点,按规范和设计要求对井位进行测量定为,确定减压井准确位置,同时测定减压井井口高程,并按照图纸进行编号。
(2)反滤料准备。反滤料规格按设计要求准备D15=2.5mm,D50=3.5mm,D60=5mm, Dmax=15mm,Dmin=1.5mm,进行筛选,每孔按理论计算值总量的1.2倍进行备料。
(3)井管制作。井管采用的钢管进行制作,长度为9m,按孔隙率20%进行布置滤孔,井管外侧焊接4道
的龙骨筋,然后在外侧用200g/m2的土工布进行包裹,再用
的铁丝扎牢在龙骨架上,滤管底部采用直径为350的木板封口。
(4)机械就位。经孔位测量成果验收合格后,将CZ-6A冲击钻机就位,钻头对准孔位,调平并加以固定,校核钢丝绳的铅直度,在钻进过程中,孔斜控制在0.2%以内。
(5)钻孔、成孔。钻机就位后就可以开始钻进,钻进过程中采用膨润土泥浆进行护壁,不同的地层采用不同的钻进参数,根据地层土质的不同采用不同的泥浆比重,钻进最终深度比设计深度大于50cm,以备孔底先填50cm的反滤料。
(6)清孔、清渣。造孔结束后,及时对孔进行清洗、清渣,其方法采用反循环方式进行,置换后的泥浆比重在1.05~1.1之间,沉渣控制在10cm以内。
(7)下井管、填反滤料。造孔、清孔结束并验收合格后进行井管下设,井管下设前,先在孔底填50cm反滤料,然后立即安装井管,加工好的滤管利用井架采用人工下设的方法进行及时下设,井管采用套管焊接的方法进行连接,井管下设完毕后,在井管与井壁之间一次性填筑准备好的反滤料,填至设计高程。
(8)洗井。回填结束后,采用清水在压缩空气配合的水气轮换法进行洗井,在大约洗井24h后,测其含沙,视觉为清水即可终止。
5.3.3 实施效果
减压井施工完成后,地下高压气体对防渗墙墙体带来的危险得以消除。
6 小结
(1)完成了甲玛工程塑性防渗墙总工程量5.5万m2,最大深度达到119m,作业面最大海拔高度4100m,工程效果显著。
(2)在工程实施过程中,发现并利用了当地黏土粉代替膨润土,制成了合乎要求的塑性混凝土,节约了大量成本。
(3)通过在防渗墙上游侧实施减压井,消除了地下高压气体对墙体的潜在破坏。