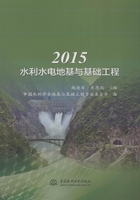
小型洞室充砂溶洞地基防渗处理施工工艺
周发海,刘文,刘阳,谭红斌
(中国水利水电第八工程局有限公司基础公司)
1 引言
黔中水利枢纽一期工程由水源工程、输配水一期工程组成,水源工程选在三岔河中游六枝与织金交界的平寨河段,坝址位于平寨—木底下寨之间的峡谷河段,水库正常蓄水位1331.00m,总库容10.89 亿m3,死水位1305.00m,水库电站装机136MW。工程等别为Ⅰ等,属大(1)型工程。拦河大坝采用钢筋混凝土面板堆石坝,防渗帷幕采用“坝基及两岸近坝段+左岸远端”的方案。左岸帷幕灌浆工程工程地质条件复杂,大坝水头高,帷幕灌浆工程量大,设计灌浆下限及边界最终根据先导孔资料确定,帷幕下限的最大深度达236m,分成4层灌浆,即ZⅠ层、ZⅡ层、ZⅢ层、ZⅣ层,帷幕线平面投影总长1851m。
在施工过程中各层廊道在不同程度均遇大型溶洞、溶槽、软弱夹层带等不良地质情况,其中底层廊道ZⅥ层灌浆平洞桩号0+296~0+230m段全断面为中细砂致密充填,有少量孤石,形态极不规则,沿灌浆平洞方向长约66.0m、方向约N34°E,洞顶高程最高1214.40m,洞底最低高程约1189.00m,溶洞断面一般高15~20 m,最大高度25m,一般宽13~15m,最宽24m,溶洞体积约1.6万m3,充填物主要为细沙土夹崩块石。由于溶洞处于底层灌浆平洞帷幕轴线上,其充填的砂层渗透性较强,将影响水库正常蓄水功能,因此需要对该溶洞进行防渗处理,降低其渗透性,并保证其渗透稳定和防渗体结构安全。
2 砂层基础防渗处理结构设计
2.1 砂层防渗结构形式
充砂溶洞防渗结构,上部大部分采取全挖全填,考虑到安全问题,边墙局部留有砂层的地带,后期采取灌浆处理的施工方法进行;底板以下采取防渗墙结构形式,防渗墙沿水库的帷幕防渗线方向布置,远离水库的一侧布置有传力墙,传力墙与防渗墙垂直布置,防渗墙和传力墙均采取嵌入式孔桩依次交替布置,以提高墙体整体连接性,而传力墙则与基岩相结合,进一步提高防渗墙体结构的稳固性,待完成后再进行灌浆加固处理。
2.2 配合比设计
黔中工程施工任务紧而繁重,为顺利按时完成施工生产任务,确保充砂溶洞处理后满足设计防渗要求。这就需从工程经济角度出发,合理选择施工技术方案,根据现场实际情况,寻求专家的意见,最终决定对充砂溶洞上部采取全挖全填,下部采用防渗墙辅以灌浆的方式进行,同时根据现场实际情况和设计防渗标准要求,对混凝土配合比进行了经过近3个月的试验和研究,从材料用量的理论计算与实际值之间的差异关系,改进泵送混凝土配合比的设计,延长混凝土凝结时间,改善混凝土的流动性,以确保工程质量。最终上部采用C20混凝土回填,下部防渗墙采用C30W8F100混凝土。
3 施工程序
结合现场实际情况,将砂层段防渗墙施工分成A、B、C3个区域(见图1),3个区域可同时施工,各区域具体施工程序如下:
图1 砂层现开挖现状图
(1)A区:利用挖机将0+260~0+230段孔桩整体开挖深度约2m→充填物、杂物清除→测量放样→钢筋制安→立模板→0+260~0+230段混凝土衬砌→1号、2号、3号、A1号′、A2号′孔桩开挖、护壁、灌注施工→1号′、2号′、3号′、A1号、A2号孔桩开挖、护壁、灌注施工。
(2)B区:利用挖机将0+280~0+260m段孔桩整体开挖深度约2m→充填物、杂物清除→测量放样→钢筋制安→立双层模板→0+280~0+260m段混凝土衬砌→4号、5号、6号、B1号′桩开挖、护壁、灌注施工→4号′、5号′、B1号、B2号桩开挖、护壁、灌注施工。
(3)C区:施工准备→充填物、杂物清除→测量放样→钢筋制安→立双层模板→0+296~0+280m段混凝土衬砌→7号、8号孔桩开挖、护壁、灌注施工→6号′、7号′、8号′、C1号桩开挖、护壁、灌注施工。
4 防渗墙施工
4.1 工艺流程
测量放样及定桩位→开挖第一节桩孔砂层(整体2.0m)→桩基中心位置检测→放置附加钢筋、支护壁模板→浇筑第一节护壁混凝土→安装运输架→安装卷扬机→安装活底吊桶、照明灯、通风机、水泵等→开挖、吊运第二节桩孔砂层→放置附加钢筋、支护壁模板→桩基中心位置检测→浇筑第二节护壁混凝土→依次往下循环作业→开挖扩底部砂层→检查验收桩孔→安装混凝土导管或串筒→浇筑桩身混凝土→桩顶位置→桩基成品检测、验收。
4.2 开挖桩孔砂层及出渣通道
(1)开挖顺序。先利用小型挖机将整体挖槽2.0m,然后分两序进行人工挖孔桩施工,地下水位或渗水量不大的可同时开挖,但渗水量较大的孔,应超前开挖,集中抽水,以降低其他孔的水位。
(2)桩孔开挖时,先开挖桩孔中间部分的石砂,然后以孔桩中心线分为迎水面和背水面,先开挖迎水面(或背水面)孔桩,背水面(或迎水面)暂用于出渣通道,待迎水面(或背水面)完成护壁之后,再进行背水面(或迎水面)开挖,以保证手推车有足够的出渣通道。用手推车将渣倒入装载机,通过装载机装入自卸车中,近坝段由连接灌浆平洞的ZD5施工支洞运至2号渣场,远坝段由连接灌浆平硐的ZD7施工支洞运至3号渣场。孔桩开挖时应控制好其截面尺寸,根据砂层的不同,确定开挖节段高度(约1m为宜);当遇到岩壁不稳定特殊情况时,开挖节段高度可适当减少,以保证其施工安全和成孔性。
(3)开挖时若能采用挖机配合开挖,将加快施工效率,若无法利用挖机开挖,采用人工开挖。
(4)挖孔过程中做好原始记录,发现地质情况有变化时,应立即汇报,从施工工艺及安全设施上采取措施。
4.3 桩基中心位置检测
每一节段桩孔开挖完成后,检查孔径、垂直度及中心偏位,每一节段挖孔成型后,检查孔位中心是否与桩中心在同一垂直线上,其偏差不大于5cm。每层必须检查其孔位及孔径符合要求后方可支模板,以保证整个桩基的护壁厚度、孔径及垂直度。
4.4 钢筋制安、支护壁模板安装
(1)每一节段桩孔开挖完成后,进行钢筋制安。严格按设计图纸及规范要求制作安装,钢筋的型号、长度、式样符合设计要求,钢筋焊接和绑扎要符合规范要求,钢筋安装要注意预留保护层,并按设计要求在节与节之间必须安放附加钢筋。
(2)护壁模板通过拆上节、支下节的方式重复周转使用,模板必须有足够的刚度,模板用木桩加固支撑,其中轴线与桩中心在同一垂直线上,偏差不大于1cm,以保证桩基的垂直度符合规范要求。模板之间用卡具、扣件连接固定,可在多节模板的上、下端各设一道用槽钢或角钢做成的内钢圈作为内支撑,以防止模板受力变形。为防止模板跑模,应在两对边增设木桩,作为水平支撑。
(3)模板安装牢固后,检测模板的位置,以保证桩孔的平面位置及其垂直度。
4.5 第一节护壁混凝土浇筑
第一节孔桩完成后,应立即放置模板,浇筑护壁混凝土,采用人工浇筑、人工振捣,坍落度控制在16~18cm。混凝土护壁要保证混凝土强度及其厚度,洞内施工温度接近室温,浇筑8h后方可拆模。
4.6 安装垂直运输架
垂直运输架用提升钢框架作为承重结构,配置慢速电动卷扬机提升;门式工字钢梁架作为承重结构,配置电动葫芦提升及横移。第一节段桩孔浇筑完混凝土后,桩孔旁的钢框架,通过三角架的转动横移,门式工字钢梁架安装在桩孔正上方,通过电动葫芦提升,沿工字钢梁横向移动。
4.7 开挖、吊运第二节段及以下节段桩孔
(1)从第二节段开始,利用提升设备运渣,当吊桶在桩孔上方1.0m时,横移或转动,使吊桶离开桩孔上方,吊桶在小推车内卸渣,用小推车经背水侧(或迎水面)或搭设木桥运输至装载机,倒置铲斗内,然后装入自卸车,竖向平均运距约7m,水平平均运距约50m。
(2)桩孔挖至规定的深度,检查孔的尺寸,施工人员修整孔壁使上下垂直顺直。
(3)在检查桩孔尺寸、中心位置合格后,拆除第一节护壁模板。然后进行锚杆安装,锚杆孔深、尺寸、材质、长度应符合设计及规范要求。接下来进行钢筋制安,并按设计要求放置附加钢筋。护壁模板一般采用拆上节支下节的方式依次周转使用,模板上口留出高度为10cm的混凝土浇筑口。
(4)第二节以下开挖存在跨桩出渣的施工难题,为保证施工安全,便于施工,可利用迎水侧(或背水侧)通道,通过手推车将洞渣转移至装载机铲斗内,通道靠桩侧应设置安全防护栏,防止人、车通行时,掉入开挖桩内,必要时可搭设木板桥,为保证手推车安全通过,木板桥两侧应设置不低于50cm的护栏。
4.8 浇筑第二节及以下护壁混凝土
(1)模板支好后,检测模板的中心位置、支撑情况,当符合要求后浇筑第二节段及以下节段护壁混凝土,混凝土用吊桶运送到孔内,人工入模、振捣密实。
(2)节段往下循环操作,将桩孔挖至设计高程,用钢钎插探桩底地质情况是否与图纸相符,清除风化岩石,深入弱风化岩石深度不小于50cm,基底地质情况与设计不符时,应即时上报监理工程师,签署验底记录。
4.9 质量检查
成孔后在自检的基础上,做好施工原始记录、办理隐蔽工程验收手续,经对桩尺寸、高程、桩位、垂直度全面检查签字后,方可灌注混凝土。混凝土浇筑完成后进行芯样检测(包括抗压强度、抗渗、密实度等)。本工程经检测质量满足设计要求。详见表1和表2。
表1 防渗墙混凝土强度检测报告

表2 防渗墙混凝土抗渗检测报告

5 结语
经过一次大汛期的安全有效运行及大坝监控仪器数据表明,利用人工掏槽辅以小型机械成墙施工技术,不仅解决了小型洞室遇大型充砂溶洞处理的难题,而且降低了施工成本,达到了预期目标,其防渗效果较为理想,综合效益显著。小型洞室充砂溶洞处理的关键在于根据资料详细分析其地质情况,确定发育范围,在施工过程中科学合理的组织,不断优化施工方案,确保工程安全可靠运行,本次充砂溶洞的成功处理可给类似工程提供参考。