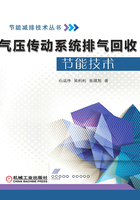
1.2 气压传动系统排气节能研究现状
目前,气缸排气节能的研究已经得到了足够的重视。对气压传动系统来说,减少耗气量就是节能,因此,气缸排气节能主要应从这几方面考虑:在气动系统中设计一些节能型的气动回路,以实现节能;开发节能气动元件和新的气压传动系统;正确安装、加强维护保养、消除泄漏等等。具体讲,主要有以下几种节能方式。
1)将气缸排气腔的能量转换成其他形式的能量(电能、真空压力能等)再利用。
2)设计节能回路减少耗气量。
3)利用气罐回收气缸排气腔的部分能量再利用等。
1.2.1 将排气能量转换成其他形式能量的节能研究状况
日本学者永井提出了一种节能研究思想,如图1-2所示,通过设置能量转换装置将气缸排气能量转换成真空再利用,可达到节能的目的[19]。但该装置要产生足够的真空度,气缸排气腔的压缩空气必须以足够高的速度流经真空喷嘴,否则气缸排气腔压缩空气相当于还是直接排向大气,造成了能量的浪费。

图1-2 能量转换再利用节能系统
南京理工大学SMC气动技术中心提出了一种将排气能量转换成电能的节能思路,即将气缸排气腔排出的压缩空气的压力能转换成电能,以便供给气动系统中需要电能驱动的元器件(如电磁阀等)使用,从而达到节能的目的[21],其节能原理如图1-3所示。但该节能方法中能量转换装置尺寸较大,不能作为附件直接使用。

图1-3 气缸排气能量转换节能回路
1.2.2 设计节能回路减少排气腔耗气量以实现节能的研究状况
1.活塞到位后停止供气以节省耗气量
日本的河合素直教授在1996年提出了用进口节流方式,在活塞到位后切断充气过程,来降低充气侧的压力,减少空气消费量达到节能的目的[6,16,19]。其节能思路为:对于往复运动的进气节流气压传动系统,当气缸活塞到达行程末端后,气源仍会向气缸的充气侧充气,造成了不必要的能量损失,如图1-4所示行程末端切断供气节能系统试验曲线示意图,如果在气缸活塞到达行程终端后,立即切断供气气源向气缸进气腔充气,这样气缸进气腔的压力就可维持在较低的压力下,从而节省压缩空气的消耗。日本明治大学的小山纪也对此种节能方法进行了理论和试验研究,日本SMC株式会社对此原理进行改进并开发出了节能阀[6]。但该节能方法仅适用于进气节流回路,应用范围较窄。

图1-4 行程末端切断供气节能系统试验曲线示意图
2.在气动系统中使用不同的工作压力以减少耗气量
在一定温度条件下,一定体积的压缩空气所具有的能量与其绝对压力成正比。在允许的条件下能使用低的工作压力去完成同一工作(例如驱动同一气缸),则可减少能量消耗。因此,气动系统节能的重要途径之一就是对系统的不同部分根据不同情况使用不同的工作压力。例如气压传动系统用高压气源,气动控制系统用低压气源工作;而在气压传动系统中,在很多情况下是正行程有外加负载,回程无外加负载或只有很小的负载,这时就可如图1-5所示在换向阀输出端多装一个减压阀或各种节能元件,使气缸活塞在正行程时用高压气源,回程用低压工作。这种系统在正行程用高压气源(>0.5MPa),回程用(0.1~0.2)MPa表压工作,节能可达25%~35%[20]。尽管采用降压供气驱动活塞返回可以达到节能的目的,但高压气源在降压过程中也要损失一部分能量。文献[22]中也介绍了一种差动回路即气缸的两个运动方向采用不同压力供气的回路,比一般的双作用气缸回路节省压缩空气消耗量,但是在气缸速度比较低的时候,容易发生爬行现象。

图1-5 降压驱动节能回路
3.分压供气方式
北京航空航天大学蔡茂林、石岩教授[7-12]等针对工厂中只使用一组空压机为全厂区提供压缩空气,且因各处所需压力不同,气源压力须为气动系统所需的最高压力,对于需要低压的场合,则用减压阀进行减压,这样会造成能量损失,据此提出了分压供气的概念。分压供气的方法主要是空气压缩机分组供气和采用局部增压技术。前者是将一个空气压缩机组分为多个组,每个空气压缩机组根据用气设备的需要提供不同压力的压缩空气;后者则是直接使用低压空气作为气源,在气动系统局部采用增压设备对低压气源进行增压,将低压气源的压力增至驱动设备所需压力,主要包括电动增压和气动增压。其中电动增压机结构简图如图1-6所示,通过使用电能使压缩空气增压提供能量,但是由于其效率较低,且对工厂电网、气动回路冲击较大及对设备本身损坏严重,因此并未广泛投入使用。气动增压阀的结构简图如图1-7所示,通过改变压缩空气回路,利用活塞对空气进行压缩,实现增压的目的。通过分析对比这两种分压供气的方式,得出两种供气方式的优缺点,见表1-1。

图1-6 电动增压机结构简图
表1-1 分压供气方式优缺点对比


图1-7 气动增压阀的结构简图
1—活塞 2—单向阀 3—换向阀 4—减压阀
1.2.3 气罐式排气回收节能研究状况
1.重复利用无杆腔中有压空气使活塞退回,变双程耗气为单程耗气
对于实际生产中广泛使用的气缸来说,许多是正行程有外加负载,回程无外加负载,只需克服自身的摩擦阻力。针对这种情况,日本SMC筑波技术中心小根山尚武和我国华南理工大学的李建藩教授分别提出了一种节能气压传动系统(简称ESPS),如图1-8a、b所示[17,19]。

图1-8 变双程耗气为单程耗气的节能回路
如图1-8a所示,气缸完成一个工作行程后,重复利用原工作腔内有压空气驱动活塞返回,以实现节能,并根据实际需求设计了回收阀。由图1-8b可见,该节能系统由双作用气缸A,双控二位五通阀DV1、双控二位三通阀DV2和蓄能气罐C组成,通过重复利用活塞杆伸出后气缸无杆腔内的压缩空气驱动活塞返回,从而变双程耗气的常规系统为单程耗气的节能系统,可以节省耗气量近50%。
同样,如图1-8c所示,通过几种气动元件的有效组合将气缸排气腔的压缩空气回收起来[24,25],让它再次做功,推动气缸活塞返回,这样也可以减少压缩空气的用量,节省了能源。
但上述三个节能回路中,存在以下问题。
1)每个气缸均需配备一个适当大小的蓄能气罐,增加了安装的困难。
2)要使气缸可靠完全地退回,气罐所蓄能量必须供给气缸驱动腔足够的能量,因此,所需气罐容积的选取较复杂,如气源压力降低,气罐容积也必须相应减小,否则气缸活塞便不能完全返回等。
2.气缸垂直向上安装回路中的气罐节能方法
文献[19,25]中介绍了如图1-9所示的节能回路,气缸在往复运动中进行排气时,将排气部分地回收,也能减少压缩空气消耗量。此回路中的减压阀2被调定为较低的压力,气缸无杆腔不排放压缩空气,由气罐3引出的气体,经减压阀减压引入气缸有杆腔。电磁阀1通电,气缸上升,压缩空气进入气缸的无杆腔,气缸有杆腔的低压气体经电磁阀向大气排出。电磁阀断电,气缸在负载重力的作用下缩回,气缸无杆腔的压缩空气被压回气罐,由此将回路耗气量降至最小。

图1-9 气缸垂直向上安装节能回路
但该节能方法只适用于气缸垂直向上安装回路,应用范围较窄,而且活塞杆伸出时,气缸有杆腔的压缩空气直接排向了大气。