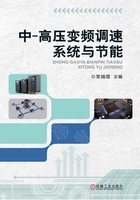
2.9 工程实例:PLC控制4台胶带输送机的典型流程和梯形图
早期胶带输送机的电气控制大多采用继电器、接触器控制及手工操作的方式,存在劳动强度大、能耗严重、维护量大、可靠性低等缺点。随着技术的进步,许多行业中胶带输送机系统的继电器控制已被PLC控制取代。
后文第9章介绍的港口胶带输送机系统PLC集中控制和计算机管理,涉及的胶带输送机、单机和保护设备都比较多,本书介绍的PLC控制4台胶带输送机的典型流程和梯形图,简化了一些条件,如未设集中手动控制、未介绍胶带输送机起动前应联系给料机和收料机(或堆料机)的方式(实际应用中应该有),也未介绍胶带输送机起动前在沿线报警铃给出30s报警(实际应用中应该有的安全措施)等,仅用PLC的程序流程图和梯形图说明控制多台胶带输送机的流程联锁和逻辑控制,以供参考。
2.9.1 胶带输送机的构成和控制功能要求
选用西门子公司的S7-200 PLC控制4台胶带输送机,[8]如图2-40所示,PD1、PD2、PD3和PD4分别为胶带输送机的代号,箭头方向为散料的料流方向。
图2-40 4台胶带输送机的输送散料示意图
4台胶带输送机的简化主电路如图2-41所示,真空接触器KM1控制PD1输送机的电动机M1,真空接触器KM2控制PD2输送机的电动机M2,真空接触器KM3控制PD3输送机的电动机M3,真空接触器KM4控制PD4输送机的电动机M4。每台胶带输送机都由对应的真空接触器来切断电路进行保护,隔离开关QS起电源隔离作用。回路中省略了过载、短路保护部分。
图2-41 4台胶带输送机的简化主电路
当采用“自动集中控制”方式时,完全由PLC按照多台胶带输送机的工艺要求(见9.2.2节)来操作生产线上的各台设备。
输送系统起动时先起动最后一台输送机PD4,然后间隔几秒或更长时间,从后向前依次起动各台输送机。
输送系统停车时,先停止最前面一台输送机PD1,物料运送完毕后,以适当时间间隔依次从前向后停止各台输送机。
当某台输送机发生故障时,该输送机和前面的输送机立即停车,而该输送机以后的输送机待物料运送完后停车。例如,当胶带输送机PD2发生故障时,PD1、PD2立即停车,延时适当时间后PD3停车,再经适当时间间隔后,PD4停车。
当电动机的容量不超过电源变压器的15%~20%、电动机的起动转矩大于负载转矩,并且在起动时不影响同一供电母线上的其他用电设备的正常使用时,可实行直接起动或进行变频起动。电动机应配有短路、过载、过电流、断相和必要的过热等保护。
真空接触器的容量应根据电动机功率来选取,所有真空接触器控制线圈的电压选为AC 220V。
S7-200 PLC的CPU单元选用CPU224,主机的I/O点数为24点(14点输入,10点输出),可扩展到168点数字量。
2.9.2 PLC的I/O表分配和外围电路
1.输入信号
起动按钮SB1,需要1个输入端,地址号为I0.0。
停车按钮SB2,需要1个输入端,地址号为I0.1。
4台胶带输送机相对应的故障信号(参见9.2.2节的有关内容)按钮,需要4个输入端(SB3、SB4、SB5、SB6),故障信号经它们输入PLC,它们的地址号分别对应为I0.2、I0.3、I0.4和I0.5,当其中任何一台胶带输送机发生故障时,故障指示灯HL便开始报警。各种故障信号(如过电流、断相、短路、过载、胶带输送机跑偏等)均可由这4个输入端输入。
故障复位按钮SB7,需要1个输入端,地址号为I0.6。
检修转换开关SA1(1个常开触点,1个常闭触点),常开触点需要1个输入端,地址号为I1.0;常闭触点和SB1串联,共用一个输入地址号。
4台胶带输送机相对应的现场控制开关,需要4个输入端(SB8、SB9、SB10、SB11),它们的地址号分别对应为I1.1、I1.2、I1.3和I1.4。
以上共需12个输入信号点,考虑到以后系统的调整与扩充,需要留有备用点,确定共需14个输入点。
2.输出信号
4台胶带输送机的电动机(M1、M2、M3、M4)对应需要4个输出端(KM1、KM2、KM3、KM4),它们的地址号分别对应为Q0.0、Q0.1、Q0.2和Q0.3。
4台胶带输送机的故障报警灯(HL1、HL2、HL3、HL4)对应需要4个输出端(HL1、HL2、HL3、HL4),它们的地址号分别对应为Q1.0、Q1.1、Q1.2和Q1.3。
以上共需8个输出信号点,考虑到以后系统的调整与扩充,需要留有备用点,确定共需10个输出点。
PLC的I/O分配表见表2-9,PLC与外围设备的连接电路如图2-42。[8]
表2-9 S7-200的I/O分配表
图2-42 S7-200 PLC与外围设备的连接电路
2.9.3 胶带输送机的程序流程图及说明
4台胶带输送机的动作程序流程如图2-43所示,Q2t、Q3t、Q4t分别为PD2(M2)、PD3(M3)、PD4(M4)从起动到额定速度的时间,S1t、S2t、S3t分别为PD1(M1)、PD2(M2)、PD3(M3)停车需要的时间。
图2-43 动作程序流程图
在正常情况的起动与停止控制。
当需要传输物料时,确认各胶带输送机及保护设备状态良好,起动报警铃向胶带输送机沿线发出30s以上的报警后,PLC上电初始化。按下起动按钮SB1(I0.0),胶带输送机PD4(M4)先起动,然后经Q4t时间起动胶带输送机PD3(M3),再经过Q3t时间起动胶带输送机PD2(M2),最后经过Q2t时间起动胶带输送机PD1(M1)。
当物料运送完毕需要停车(即第一台胶带输送机PD1上的散料已送完)时,只需要按下停车按钮SB2(I0.1),第一台胶带输送机PD1(M1)立即停止工作,以免继续送料;然后经过S1t时间,第二台胶带输送机PD2上的散料送完,停止第二台胶带输送机PD2(M2);再经过S2t时间,第三台胶带输送机PD3上的散料送完,停止胶带输送机PD3(M3);最后经过S3t时间,第四台胶带输送机PD4上的散料送完,停止胶带输送机PD4(M4)。
当某台设备出现故障或设备巡检发现隐患时,按下该设备故障按钮,这台胶带输送机以及之前的胶带输送机马上停止工作,其他设备再通过有关延时,按相应的停车顺序停车。
2.9.4 胶带输送机起动的梯形图及说明
根据控制要求及流程图设计的梯形图如图2-44所示。
PLC控制胶带输送机起动的梯形图说明如下:
当按下起动按钮SB1(I0.0)时,PLC内部继电器的线圈M0.0、M0.1、Q0.3相继接通。
图2-44a中,第1行,按下起动按钮SB1(I0.0),I0.0的常开触点闭合,继电器线圈M0.0接通并自锁。第2行,由于M0.0的常开触点闭合,继电器线圈M0.1接通并自锁。
图2-44b中,第10行,由于M0.1的常开触点闭合,继电器线圈Q0.3接通。主电路的KM4动合触点闭合,PD4的电动机M4起动。
图2-44a中,第3行,PLC内部的常开触点(M0.0和M0.1)的接通,使时间整定器T37延时Q4t动作、T37的常开触点闭合。第4行,由于常开触点M0.0的闭合、T37的常开触点闭合,继电器线圈M0.2接通。
图2-44b中,第9行,由于M0.2的常开触点闭合,继电器线圈Q0.2接通。主电路的真空接触器KM3常开触点闭合,PD3的电动机M3起动。
然后,图2-44a中,第3行,PLC内部的常开触点(M0.0和M0.2)的接通,使时间整定器T38延时Q3t动作、T38的常开触点闭合。第5行,由于常开触点M0.0的闭合、T38的常开触点闭合,继电器线圈M0.3接通。
图2-44b中,第8行,由于M0.3的常开触点闭合,继电器线圈Q0.1接通。主电路的KM2常开触点闭合,PD2的电动机M2起动。
同理,起动胶带输送机PD1。
图2-44 PLC控制梯形图胶带输送机
图2-44 PLC控制梯形图胶带输送机(续)
2.9.5 胶带输送机停止的梯形图及说明
梯形图如图2-44所示,PLC控制四台胶带输送机停止的梯形图说明如下:
胶带输送机运行时,M0.1、M0.2、M0.3和M0.4常开触点都处于闭合状态,当需要控制四胶带输送机停止运行时(见2.9.3节有关停止运行的内容),按下停车按钮SB2(I0.1),I0.1的常开触点闭合。
图2-44a中,第8行,由于I0.1的常开触点闭合,继电器线圈M0.1在胶带输送机运行状态时已接通(其常开触点M0.1闭合),停止输出继电器线圈(M0.5)接通,其常开触点闭合并自锁。第6行,停止输出继电器(M0.5)接通后,其常闭触点断开,线圈(M0.4)失电。
图2-44b中,第7行,线圈M0.4失电后,其常开触点(M0.4)断开,线圈Q0.0失电,主电路的KM1的常开触点断开,PD1的电动机M1停止。
图2-44a中,第7行,按下停止按钮SB2(I0.1),PLC内部的线圈M0.5接通,其常开触点(M0.5)闭合,前面讲,电动机M1停止时,线圈M0.4已失电,其常闭触点(M0.4)闭合,使时间整定器T42延时S1t动作。第5行,T42延时S1t动作后,T42的常闭触点(T42)使线圈M0.3失电。
图2-44b中,第8行,线圈M0.3失电后,其常开触点(M0.3)断开,线圈Q0.1失电,主电路的KM2的动合触点断开,PD2的电动机M2停止。
以此类推,依次停止胶带输送机PD3、PD4。
2.9.6 胶带输送机故障的梯形图及说明
梯形图如图2-44所示,PLC控制4台胶带输送机故障的梯形图说明如下:
出现胶带输送机故障后需手动控制,按下故障按钮后,出现故障的胶带输送机立即停止运行,该胶带输送机上游的输送机也立即停止运行,下游的输送机按正常停止的延时要求顺序停止运行。
若PD2的电动机M2发生故障,PD2的电动机M2和PD1的电动机M1立即停止运转,随后经S2t延时后M3停止运转,再经S3t延时后M4停止运转。
图2-44b中,第3行,按下SB4(I0.3)故障按钮2,故障信号输入2的输出线圈M1.1接通;随后,在第6行,由于线圈M1.1的常开触点(M1.1)闭合,输出线圈Q1.1接通,故障信号灯2亮。第8行,由于输出线圈M1.1接通,其常闭触点(M1.1)断开,线圈Q0.1立即失电,KM2的常开触点断开,PD2的电动机M2停止运转。第7行,由于输出线圈M1.1接通,其常闭触点(M1.1)断开,线圈Q0.0立即失电,KM1的常开触点断开,PD1的电动机M1停止运转。
接着,PD3延时停车:
图2-44a中,第5行,由于输出线圈M1.1接通,其常闭触点(M1.1)断开,线圈M0.3失电,故其常闭触点(M0.3)闭合,使时间整定器T41延时S2t后动作。第4行,T41延时S2t动作后,T41的常闭触点断开,使线圈M0.2失电。
图2-44b中,第9行,线圈M0.2失电后,其常开触点断开,线圈Q0.2失电,主电路的KM3动合触点断开,PD3的电动机M3停止。
之后是PD4延时停车:
图2-44a中,第4行,如上所述,由于线圈M0.2失电,其常闭触点闭合,使时间整定器T40延时S3t后动作。第2行,T40延时S3t动作后,T40的常闭触点使线圈M0.1失电。
图2-44b中,第10行,线圈M0.1失电后,其常开触点断开,线圈Q0.3失电,主电路的KM4动合触点断开,PD4的电动机M4停止。
故障排除后,在图2-44第1行中按下故障复位按钮(I0.6),其常开触点闭合。
2.9.7 胶带输送机检修的梯形图及说明
梯形图如图2-44所示,PLC控制四胶带输送机检修的梯形图说明如下:
由现场的控制按钮对各胶带输送机进行点动控制。
图2-44b中,第11行,当设备需要检修时,将检修转换开关SA1(I1.0)置于检修位置,此时SA1的常开触点(I1.0)闭合,在胶带输送机没有起动运行即常闭触点M0.0闭合时,接通内部继电器线圈M2.0。
图2-44a中,第1行,由于继电器M2.0得电,其常闭触点断开,将将起动按钮SB1与PLC的输入端I0.0断开,防止胶带输送机起动运行。
同时,图2-44b中,第12~15行,继电器M2.0的常开触点将各胶带输送机检修按钮接通,这时各胶带输送机的运转将由现场控制开关进行点动控制。
例如,通过控制PD1的现场控制开关进行维修介绍如下:
1)PD1电动机M1运行。图2-44b中,第12行,通过控制PD1的现场控制开关SB8(I1.1)的常开触点闭合,使线圈M2.1接通。第7行,由于线圈M2.1接通,其常开触点闭合,使线圈Q0.0接通,真空接触器KM1的常开触点闭合,电动机M1运行。
2)PD1电动机M1停止。图2-44b中,第12行,通过控制PD1现场控制开关SB8(I1.1)的常开触点(M2.1)断开,使线圈M2.1失电,电动机M1停止。
2.9.8 系统调试
PLC程序设计结束后,应经人工反复检查和模拟调试;除此以外,因很多现场因素无法预料,必须通过PLC和现场控制台控制电动机的起动、切换和停止。发现错误后,立即停止调试并进行修正,并且能够对各种意外情况进行处理。系统调试时,将手动与自动操作控制独立分开,自动操作控制保证电动机程序调试成功后,再转入连续控制,最后连接整个系统试运行。