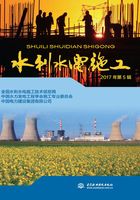
3 人工砂石料生产质量控制关键技术
3.1 砂石料原料的质量控制
砂石料原料本身的质量应满足《水工混凝土施工规范》的要求,一般避免采用具有碱活性的原料。凡采用砂岩等岩性变化大的原石料制砂时必须通过试验,取得可靠的资料。对于转运次数多、抛落高度大的系统,一般应做石料磨耗试验。在符合质量要求的条件下应选取可碎(磨)性好、磨蚀性低、粒型好、相对密度大、弹性模量和热膨胀系数小的岩石。不同类型的岩石,具有不同的特性,岩石标本取自不同的地区、不同的采场或同一采场探洞、但不同深度的同一岩类两个标本,有时也有不完全相同的特性。岩石性质极大地影响着破碎设备的选用,影响着人工砂石料产品的质量和成本。因此,在大中型水电站混凝土坝工程中,选用人工砂石料原料时必须细致地分析了解岩石性质,并通过小型试验,试验室试验,甚至组合性的半工业性试验来鉴定岩石性质对设备及混凝土的影响,然后经过技术经济比较,做出最终的合理选择。
3.2 软弱颗粒含量的控制
软弱颗粒的含量对一般和内部混凝土不应超过15%,对外部和有抗磨要求的混凝土不应超过5%。过量的软弱颗粒对混凝土的强度、抗磨和耐久性有明显的影响。由于软弱颗粒处理工艺复杂,费用较高,因此通常在料源源头采用人工控制,主要是肉眼分析判断。一般工程以弱风化带下部作为料场无用层与有用层的分界线,将料场无用层作为弃料。另外合理组织采石场施工,采用先剥离无用层、后开采有用岩石的开采程序,达到减少软弱颗粒含量的目的。
对于岩石强度与吸水率的大小变化与岩石埋藏深度关系不太明显,没有明显的强弱风化层之分,出露岩性和深埋岩性接近,采石场的质量控制主要是对溶洞和夹泥层地带含泥量的控制。例如,石灰岩地区主要化学成分是CaO,风化物容易流失,因此石灰岩地区多见溶洞、溶沟、岩石出露,形成“喀斯特”现象。如光照水电站基地料场采石场,工程区岩溶中等发育或强发育,其粒径为0.5~2cm的小晶孔、小溶孔特别发育,白云岩多溶蚀风化呈砂状。因此在有用层中分布断层、挤压面、岩溶等软弱夹层,在采料过程中就应预先剔除。如阿海水电站新源沟砂石系统采石场,据地质测绘和勘探揭露,灰岩喀斯特弱—中等程度发育,溶洞、溶蚀裂隙、溶孔、溶穴多处有分布。推测溶洞、溶蚀裂隙占总开采量的4%~5%,在开采过程中也应预先弃除。对于这种强弱风化层不太明显、多溶沟、多溶洞的岩石首先采取肉眼分辨,预先弃除,也有采用高压水冲洗的方法,以使软弱颗粒含量满足砂石料质量要求。
3.3 含泥量的控制
人工砂石料生产工艺一般不会产生泥块,主要是对砂石料含泥量的控制。成品砂石料含泥量的控制分源头控制、系统加工工艺控制及生产组织措施。
源头控制工序主要是合理组织料场施工,严格区分弱风化和强风化界限,将强风化料作为弃料。
系统加工工艺控制程序:在干式生产中,将经粗碎后的岩石中的微量含泥进行分离加工,筛去0~20mm的颗粒,阿海新源沟砂石系统就是采用这种方法弃除原料中的部分含泥量大的部分。在湿式生产中,一般设计多级冲洗机,并设置专门的清洗设备进行处理,即将0~40mm岩石全部进入洗泥机,为了洗去泥块,专门设置冲洗脱水工序对成品粗骨料进行清洗,有效保证骨料含泥量达标。
生产组织措施主要禁止无关设备和人员进入成品料堆场;堆料场地面应平整,并有适当的坡度和截排水设施;对于大型堆料场,地面应有粒径40~150mm的干净料、压实的石料垫层做护面;成品料的堆存时间不宜过长,尽量做到及时周转使用,如系统中无二次筛分设施,而粗骨料污染又较严重时,还应在进入拌和楼(站)前设冲洗脱水设施。
3.4 针片状含量的质量控制
人工粗骨料针片状含量的质量控制措施主要通过设备的选型,其次是在生产工艺上调节进料的块度。
由于各种岩石的矿物成分、结构和构造的不同,岩石破碎后的粒形和级配也不尽相同。质地坚硬的石英砂岩及各种侵入火成岩粒形最差,针片状含量多,而中等硬度的石灰岩、白云质灰岩针片状含量很少。通过大量的试验证明,不同的破碎机产生针片状含量效果不同。颚式破碎机比旋回及圆锥破碎机生产的粗骨料的针片状含量略高,而反击式特别是锤式破碎机生产的粗骨料的针片状含量显著降低。在五强溪工程开采的石英岩、石英砂岩呈块状构造、粒状结构,一般为硅质胶结,主要矿物成分为石英(SiO2),无节理,因而质坚性脆。通过试验证明:用圆锥式破碎机破碎时粉碎状成分多,而且骨料中针片状颗粒含量高;用锤式破碎机或反击式破碎机破碎时,骨料粒形相对较好。因此,为了有效地控制针片状含量,对于岩性不太好的,尽量避免采用颚式破碎机和圆锥破碎机,一般采用反击式破碎机。
粗碎的针片状含量大于中碎,中碎的针片状含量又大于细碎。说明破碎比越大,针片状含量越大,为改善骨料粒形,在生产工艺上应尽量减小粗碎前的块度,并尽量利用粗碎及中碎后的小石及中石制砂,利用细碎后的中小石作为粗骨料的成品,这样也可以严格控制针片状含量。
3.5 石粉含量的质量控制
人工砂石粉含量指人工砂中小于0.16mm的颗粒的含量,人工砂石粉中小于0.08mm的颗粒可以视为一种惰性掺和料,适当的石粉含量可以改善混凝土的和易性,提高混凝土密实性,对提高混凝土性能有利。在国内,绝大多数水电站混凝土用砂技术参数要求中,石粉含量要求在6%~18%,对碾压混凝土用砂的石粉含量要求12%~22%。国内大型人工砂石系统大多碾压砂石粉含量不足,也有工程用砂石粉含量超标现象发生。
干法制砂工艺中人工砂中的石粉含量一般较高,能满足质量标准要求。也有发现存在石粉含量大于标准的情况,这时应考虑部分湿式生产,洗去部分石粉或选用风机吸尘器设备吸出部分石粉,以满足标准要求。三分离选粉机成功用于锦屏一级水电站项目,试验结果取得了良好的效果。阿海新源沟砂石系统也安装了4台三分离选粉机去掉成品砂多余的石粉。
湿法制砂工艺中人工砂中的石粉含量一般较低,大多数工程均要求回收部分石粉,以满足工程需要。水电工程人工砂中的石粉回收主要有机械回收方式和人工回收方式两种。在大型人工砂石料生产中或场地狭窄的工程,工艺上需设计石粉回收车间(或称细砂回收车间),即将筛分车间和制砂车间螺旋分级机溢流水中带走的石粉通过集流池,再回收利用。在小型人工砂石料生产中或场地宽敞的工程,也采用人工回收方式,来控制人工砂中的石粉含量,即对生产过程中洗砂机排放溢流水进行自然存放脱水,自然存放脱水后的细砂可以用装载机配合自卸汽车运输进行添加。为了有效地控制石粉含量,常采取以下措施:
(1)通过不断试验,有效控制石粉的添加量。
(2)在石粉添加斗的斗壁附有振动器,斗下安装一台螺旋分级机,通过螺旋分级机均匀地添加到成品砂入仓胶带机上,使石粉得到均匀混合。
(3)废水处理车间尽量靠近成品砂胶带机,能用胶带机顺利转运,经压滤机干化后的石粉干饼经双辊破碎机加工成松散粉末状,防止石粉成团。
(4)在施工总布置中要考虑一个石粉堆存场,堆存场既可以调节添加量,又可以通过自然脱水降低含水率,在一定程度上调节成品砂的含水率。
3.6 细度模数的质量控制
在湿式生产时,一般配置棒磨机制砂,人工砂的细度模数控制工艺取决于棒磨机和细砂回收工艺。
在干式生产时,其小于0.16mm颗粒的含量已存在砂中,无须考虑回收细颗粒。在成品砂的质量控制中一方面处理立轴破碎制砂与经多级破碎后的粗砂细度模数偏大问题,在工艺上去掉3~5mm部分的粗颗粒,使其自身的细度得到控制。另一方面着重分离处理0~0.16mm微粒的含量,以控制成品砂细度模数。为了有效地控制成品砂细度模数,可采取以下措施:
(1)通过试验测试砂的细度模数,使成品砂细度模数控制在规定的范围内。
(2)若发现细度模数偏大,颗粒级配偏差,应调整棒磨机进料粒径、进料量、装棒量等,或调整筛分楼的开机组数,调整生产量。
(3)调整筛分楼的筛网直径,也可以调整颗粒级配和细度模数。
(4)有许多系统配备超细碎车间进行粗砂整形,有效调整砂的细度模数和级配组成。
3.7 含水率的质量控制
为了使含水率降低到规定范围内且稳定,目前大型工程主要采取机械脱水方式,中小型工程则以自然脱水为主。另外在生产中必须严格遵守操作规程,对堆料砂仓进行合理的改造和堆存,也可以有效控制人工砂含水率。一般采取如下措施:
(1)一般系统工艺中首先要采用机械脱掉砂中大部分水分。目前采用最多的是振动筛脱水工艺,经直线脱水筛脱水后的砂,能将原含水率20%~23%的砂脱到14%~17%;也有采用脱水效果好投资费用相应大的真空脱水和离心脱水。
(2)人工砂下料、堆存脱水及人工砂取料分开进行的,一般堆存脱水3~5天后可使含水率降低到6%以内且稳定。
(3)使干法人工砂和脱水筛的人工砂混合进入成品砂仓,可降低砂的含水率。
(4)在成品砂仓顶部搭设防雨棚,砂仓底部浇筑混凝土地板,并设置盲沟排水设施。每仓放完料后对盲沟进行一次清理,加快自然脱水时间,也可有效降低成品砂含水量。