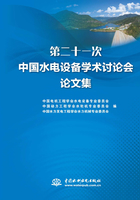
4 计算结果
本文对带有双隔板三蜗室蜗壳和单隔板双蜗室蜗壳的离心泵进行转速n=1450r/min下7个工况的非定常流动计算,计算流量分别为0.20m3/s、0.25m3/s、0.30m3/s、0.35m3/s、0.40m3/s、0.45m3/s和0.50m3/s。时间步取1/100的转动周期,为0.0004s,收敛容差为0.00001。经过多个周期计算,取计算充分收敛后的5个周期的模拟结果进行分析。其中,效率、扬程、径向力取5个周期的平均值。径向力脉动幅值为5个周期的径向力混频幅值。
图3给出了小流量工况(Q=0.25m3/s,n=1450r/min)双隔板三蜗室蜗壳与传统的单隔板双蜗室蜗壳中心对称截面流线分布的对比情况。从图3中可以看出,双隔板三蜗室蜗壳内水流在双隔板的引导下,流线分布相比单隔板双蜗室蜗壳分布更加均匀,尤其在隔舌位置,流态得到了明显的改善。图4为双隔板三蜗室蜗壳和传统的单隔板双蜗室蜗壳过转轮中心与蜗壳出口平行的过流截面流线分布的对比情况。从图4(b)中可以看出,过流截面存在较大的涡流,大涡的存在使压力脉动剧烈,致使叶轮四周流体产生的压力分布不均,从而导致径向力脉动幅值增大。通过增加隔板对流动加以引导,从图4(a)中可以看出,涡流情况得到改善,涡的尺寸明显减小,改善了压力脉动,从而大大降低了径向力脉动幅值。

图3 中心对称截面(z=0)流线分布
(Q=0.25m3/s,n=1450r/min)

图4 过转轮中心与蜗壳出口平行的过流截面流线分布
(Q=0.25m3/s,n=1450r/min)
经对数值模拟结果分析对比,双隔板三蜗室蜗壳与单隔板双蜗室蜗壳相比,其径向力和脉动幅值均有了明显的降低,图5给出了各个工况下双隔板三蜗室蜗壳与单隔板双蜗室蜗壳效率、扬程、平均径向力和径向力脉动幅值的对比情况。在小流量时,双隔板三蜗室蜗壳的平均径向力和径向力脉动幅值均明显小于单隔板双蜗室蜗壳;在设计流量时,双隔板三蜗室蜗壳的平均径向力和径向力脉动幅值与单隔板双蜗室蜗壳差值较小;在大流量时,双隔板三蜗室蜗壳的平均径向力小于单隔板双蜗室蜗壳,径向力脉动幅值则与单隔板双蜗室蜗壳相当。在整个运行范围内,双隔板三蜗室蜗壳的平均径向力的最大值和径向力脉动幅值的最大值均小于单隔板双蜗室蜗壳。蜗壳内壁和流场产生的摩擦损失,与水流速度的平方和蜗壳内壁的面积成正比,因此随着隔板的增多,蜗壳内壁面积增大,使摩擦损失增加,尤其在大流量工况时,随着水流速度的增加,可能导致水泵效率的下降。从图5中可以看出,增加了一个隔板后,在设计工况效率和扬程略有降低;随着流量的增加效率和扬程有所降低,但是降低幅度不大,效率在1.25%内,扬程在1.15%内;在小流量时效率优于单隔板蜗壳,扬程也有所增加。因此,增加隔板后并没有明显影响该水泵的能量特性,但是大幅度提高了稳定性。

图5 水泵效率、扬程、平均径向力和径向力脉动幅值的对比