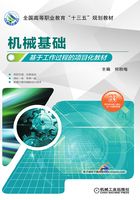
0.2 机械设计与制造的基本要求、基本原则及一般程序
1.机械设计与制造的基本要求
机械设计与制造可以是开发新产品,也可以是改造现有的机械;既可以生产出功能不同的机械,又可以生产出结构不同的机械。但应满足的基本要求大致相同。
(1)使用性要求 使用性要求是指使机械在规定的工作期限内能实现预定的功能,并且操作方便,安全可靠,维护简单。
(2)工艺性要求 工艺性要求是指在保证工作性能的前提下,尽量使机械的结构简单,易加工,好装备,维修方便。
(3)经济性要求 经济性要求是指在设计、制造方面周期短、成本低;在使用方面效率高、能耗少、生产效率高、维护与管理的费用少。
(4)其他要求 除了要使机械达到以上要求外,还要考虑:
1)外观造型和色彩符合工业美学原则,具有时代感。
2)产品新颖独特,符合人们求新、求异、求变化的心理特征。
3)尽量减少对环境的污染,特别是降低噪声。
4)某些特殊要求,如食品机械要考虑干净、卫生、易于清洗,设计飞机要考虑重量轻、可靠性高等。
2.机械设计与制造的基本原则
为了满足上述要求,机械设计与制造应注意遵循以下原则。
(1)以市场需求为导向的原则 机械设计与制造作为一种生产活动,与市场紧密联系在一起。从确定设计项目、使用要求、技术指标、设计与制造工期到拿出总体方案、进行可行性论证、综合效用分析(着眼于实际使用效果的综合分析)、盈亏分析直至具体设计、试制、鉴定、批量生产、产品投放市场后的信息反馈等都是紧紧围绕市场需求来运作的。设计与制造人员要时刻想着如何设计与制造才能使产品具有竞争力,能够占领市场、受到用户青睐。
(2)创造性原则 创造是人类的本质。人类如果不发挥自己的创造性,生产就不能发展,科技就不会进步。设计与制造只有作为创造性活动才具有强大的生命力,因循守旧,不敢创新,只能永远落在别人后面。特别是在当今世界科技飞速发展的情况下,在机械设计与制造中贯彻创造性原则尤为重要。
(3)标准化、系列化、通用化原则 标准化、系列化、通用化简称为“三化”。“三化”是我国现行的一项很重要的技术政策,在机械设计与制造中要认真贯彻执行。
标准化是指将产品(特别是零部件)的质量、规格、性能、结构等方面的技术指标加以统一规定并作为标准来执行。我国的标准已经形成了一个庞大的体系,主要有国家标准、部颁标准、专业标准等。为了与国际接轨,我国的某些标准正在迅速向国际标准靠拢。常见的标准代号有GB、JB、ISO等,它们分别代表中华人民共和国国家标准、机械工业标准、国际标准化组织标准。
系列化是指对同一产品、在同一基本结构或基本条件下,规定出若干不同的尺寸系列。
通用化是指在不同种类的产品或不同规格的同类产品中,尽量采用同一结构和尺寸的零部件。
贯彻“三化”的好处主要是:减轻了设计工作量,有利于提高设计质量并缩短生产周期;减少了刀具和量具的规格,便于设计与制造,从而降低其成本;便于组织标准件的规模化、专门化生产,易于保证产品质量、节约材料、降低成本;提高了互换性,便于维修;便于国家的宏观管理与调控以及内、外贸易;便于评价产品质量,解决经济纠纷。
(4)整体优化原则 设计与制造要贯彻“系统论”和优化的思想,要明确:性能最好的机器其内部零件不一定是最好的;性能最好的机器也不一定是效益最好的机器;只要是有利于整体优化,机械部件也可以考虑用电子或其他元器件代替。总之,设计与制造人员要将方案放在大系统中去考察,寻求最优,要从经济、技术、社会效益等各个方面去分析、计算,权衡利弊,尽量使设计与制造效果达到最佳。
(5)联系实际原则 所有的设计与制造都不要脱离实际。设计与制造人员特别要考虑当前的原材料供应情况、企业的生产条件、用户的使用条件等。
(6)人机工程原则 机器是为人服务的,但也是需要人去操作使用的。如何使机器和操作部件适应操作者的要求,人机合一后,投入产出比最高、整体效果最好,这是摆在设计与制造人员面前的一个问题。好的机器或部件一定要符合人机工程学和美学原理。
3.机械设计与制造的一般程序
机械的种类繁多,用途各异,但其设计与制造的程序却差不多。机械设计与制造一般可分为9个阶段。
(1)明确任务与设计准备阶段 此阶段应根据市场信息(含预测)或用户要求确定设计任务。要在反复调查研究,分析、收集、整理信息资料的基础上进行论证,明确机械的功能要求、使用条件等,做出决策。此阶段的成果表现为设计任务书。
(2)方案设计(或称总体方案设计)阶段 明确了设计的任务后,还需要进一步确定机械的具体参数(性能指标、总体尺寸、重量、适用范围等),并进行总体方案设计。此阶段要解决的主要问题有:机械依靠什么原理完成任务,工作装置、动力装置、传动装置各采用什么方案,这三大装置如何连接、怎样布置,操纵控制它们的装置采用什么方案。总体设计方案的优劣对最后的设计结果影响最大,要反复推敲、科学论证、全面评价、寻求最优。如果经过筛选之后还剩下两个方案难分伯仲,条件允许时可以齐头并进。此阶段的主要成果表现在机械示意图、工作原理图、机构运动简图、传动系统图和对它们的说明中。
(3)技术设计阶段 此阶段就是要将总体方案具体化,主要包括机械的运动设计、动力计算、零部件的材料选择、结构设计和主要零部件的工作能力(主要是强度)计算,绘制各种图样等。此阶段的技术成果有总体设计草图、部件装配草图、零件工作图、部件装配图、总装配图、标准件明细栏和有关的设计计算草稿等。在此阶段,由于影响设计质量的因素太多,它们之间又存在相互联系、互相制约的关系,所以具体设计很难一次成功,常常出现设计工作多次反复、不断修正、绘图与计算交叉进行的现象。
(4)整理技术文档阶段 此阶段要编写设计计算说明书、使用说明书,还要整理图样,将全部图样装订成册、编写图样目录。必要时可以将全部技术文档存入计算机硬盘、制成光盘或进行微缩处理。
(5)试制阶段 新产品投入批量生产之前,最好先制造出样机,以便进行性能检验、市场试探、成本核算等。
(6)生产准备阶段 此阶段的工作很多,主要有编制工艺文件、添置生产设备、设计制造工艺装备(工具、量具、夹具等)、采购原材料和外购件(标准件、成品部件、塑料件、电子元器件等)等。
(7)毛坯制造阶段 许多零件需要先制成毛坯再加工成符合图样要求的成品。铸造、锻造、冲压是常用的毛坯制造方法。
(8)零件加工阶段 零件加工阶段是制造的关键阶段。保质保量地将毛坯加工成符合图样要求的零件对整个生产影响很大,对降低成本也是至关重要的。
(9)装配试机阶段 严格按装配工艺将自制件和外购件组装成整机并调试合格是保证产品性能的最后一关。工艺水平的高低和检测手段先进与否将起到决定性作用。
在整个设计与制造的过程中,要注意充分利用计算机的强大功能(如上网查寻、学习与咨询、辅助设计与制造、资料的存储与修改、生产管理、信息传递等),从而提高设计与制造的质量和工作效率,取得最好的效益。
以上程序也不是一成不变的,在工作中,应根据实际情况进行灵活处理。