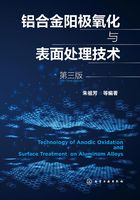
第1章 引论
铝材是有色金属中使用量最大、应用面最广的金属材料。国民经济各部门无不大量使用铝及铝合金,而且其应用范围还在不断扩大之中。全世界铝的总消费量从1991年的1874.4万吨增加到2000年的2477.98万吨,十年中增加了32%。而我国的铝总消费量的增加更为惊人,从1991年的86.8万吨迅速增加到2000年的353.27万吨,达到3倍之多。到了2001年我国铝的总消费量又大幅提高到370万吨,占全世界铝消费量的15.1%,仅次于美国,成为全世界第二大铝消费国。就原铝生产量而言,2001年我国已一跃成为全世界第一大原铝生产国,产量占全球总产量的13.98%。2007年我国各种铝材总产量达到1275万吨,2008年的铝材总产量达到1427.4万吨,多年连续保持世界第一。随后的十年中,我国铝材总产量不断迅猛上升,成为全世界第一铝材生产大国。
进入21世纪以来,我国铝挤压工业随整个铝加工业的加速发展,跨入了迅速上升的黄金时期,企业数量和行业整体规模均有明显增加和提高。根据广东有色金属加工协会的统计报道,在2003—2012年间,我国铝加工行业的铝材产量年增长率达到26.8%。2006—2012年的6年间,中国铝挤压材年产量连续突破500万吨、1000万吨和1200万吨。到2012年,中国铝挤压材的产能已经达到大约1500万吨/年,产量为1213万吨。根据中国有色金属工业协会的统计,2017年我国铝型材产销量在1900多万吨,产业规模稳居世界各国之首。实践表明,我国的铝挤压型材产量大幅度增加的同时,其他铝材产量也得到大幅度提升,据统计铝材的总产量已经达到3073.3万吨。为此,铝材表面处理也不能只关注建筑用铝型材门窗,必须扩展到各种形式的铝材,如铝板带、铝制品以及交通运输业的铝合金部件,才可能满足我国的工业迅速发展和社会需求全面提升。
2012年以来,中国铝挤压行业由于产能总体过剩、竞争激烈,导致开工率有所降低,又由于国际范围内的贸易保护加剧,导致多数企业利润下降。尽管近年来我国铝挤压材生产量与消费量的增幅有所下降,但是总产量仍然保持一定的增长态势。同时我们应该清醒地看到,在我国大量出口铝挤压材的同时,还有一部分高端挤压铝材产品需要进口,因此我国铝型材行业的技术改造和创新努力仍需加强,其中铝表面处理工艺发展围绕环境友好和节能降耗的目标进行创新改造尤为突出。
铝制品种类繁多,不胜枚举,据统计已超过70多万种,应用遍及各个行业。铝合金材料具有一系列优良的物理、化学、力学性能及特征,可以满足并正在拓宽从厨餐用具到尖端科技、从建筑门窗到交通运输、从民用机械到航空航天等各行各业对于铝合金材料提出的千差万别的使用要求。但是,铝合金的某些性能还不太理想,如硬度、耐磨耗性和耐腐蚀性等一些表面性能尚不能满足使用要求。铝的表面处理技术正好弥补了这个弱点,通过阳极氧化膜或表面涂层等技术加以弥补、改进和提高,成为铝合金扩大应用范围和延长使用寿命不可缺少的关键步骤和措施。近年来对于铝制品的外观装饰和光亮保持提出了更高的要求,透明清澈无缺陷的铝阳极氧化膜又增加其用武之地,并对铝阳极氧化、多种多样着色技术和高品质封孔提出更高的品质要求。
铝及铝合金有很多优越的性能,其特点如下。
(1)密度低。铝的密度约为2.7g/cm3。在金属结构材料中是密度仅高于镁的第二轻的金属。它的密度只是铁或铜的1/3。
(2)塑性高。铝及其合金延展性好,可以通过挤压、轧制或拉拔等压力加工手段制成各种型、板、箔、管和丝材。
(3)易强化。纯铝的强度并不高,但通过合金化和热处理容易使之强化,制造高强度铝合金,其比强度甚至可以与合金钢媲美。
(4)导电性好。铝的导电性和导热性仅次于银、金和铜。设铜的相对电导率为100,则铝是64,而铁只有16。若按照等质量金属导电能力计算,则铝几乎是铜的2倍。
(5)耐腐蚀。铝是一个负电性很强的金属,与氧具有极高的亲和力,即钝化能力很强。铝在自然条件下,表面会生成保护性氧化物,具有比钢铁好得多的耐腐蚀性。
(6)易回收。铝的熔融温度较低,约为660℃,碎屑废料容易再生,回收率很高,回收的能耗只有冶炼的3%。
(7)可焊接。铝合金可用TIG或MIG法惰性气体焊接,焊接后力学性能高,耐腐蚀性好,外观美丽,满足结构材料的要求。
(8)易表面处理。表面处理可以进一步提高或改变铝的表面性能。铝阳极氧化工艺相当成熟,操作简便,已经广泛应用。铝阳极氧化膜硬度高、耐磨,而且耐腐蚀、绝缘性好,并且可着色,能显著改变和提高铝合金的外观和使用性能。通过化学预处理,铝合金表面还可以进行电镀、电泳、喷涂等处理,赋予铝表面以金属镀层或有机聚合物涂层,进一步提高铝的装饰性能和保护效果。近年来,铝表面处理工艺的环境管理水平有极大提高,如零排放阳极氧化工艺、无铬化学转化工艺等都实现了大生产的工业化。
1.1 铝的耐腐蚀性能
金属材料与周围环境介质之间发生的化学或电化学作用而引起的金属性能的变化甚至破坏称为金属的腐蚀。有时候某些物理作用也可以归入腐蚀的范畴,例如金属在液体金属中的物理溶解也称为液体金属腐蚀。金属腐蚀过程中机械作用或生物作用也可能参与其中,与化学或电化学作用产生协同作用而加速金属的腐蚀,例如液体冲击与腐蚀的协同作用称为冲蚀(erosion),固体颗粒摩擦与腐蚀的协同作用称为磨蚀(abrasion)等。有机聚合物涂层与周围环境的作用发生的性能变化,以前称为“老化”“失效”等,现在有时候也开始笼统称为“腐蚀”,因此技术术语“腐蚀”(corrosion)一词在实际应用方面已经明显拓展,而且已经不仅是金属特有的现象和称谓了。
众所周知,金属腐蚀是当代工业和生活中一种重大的破坏因素,造成巨大的经济损失和社会危害,其影响面与危害程度远远高于各种自然灾害的破坏。金属腐蚀的经济损失可以分成直接损失和间接损失两大部分,直接损失指设备或构件的更换、防腐蚀措施的投入等,比较容易统计。间接损失如设备更换或停车的利润损失、腐蚀引起的产品污染和失效等,其影响和损失远比直接损失大得多,但是这方面往往难于直接用数字统计。此外,腐蚀的影响还不止于经济损失,还会威胁人身安全和造成环境污染等,因此金属腐蚀与经济、安全、卫生、环境等方面都直接相关。金属的表面处理技术的推广,可以有效抑制腐蚀并提高金属制品服役寿命。铝的阳极氧化处理及有机聚合物涂覆等铝表面处理技术,可有效弥补和提高铝及铝合金的耐腐蚀和耐候性能,成为大幅度延长铝合金制品使用寿命的必要措施。
从金属热力学的稳定性分析,如表1-1所示的金属的电位序,金属铝确实是一个非常活泼的金属,在结构金属中铝的活性仅次于镁和铍,因此铝的耐腐蚀性不高是可以预见的。但是,热力学分析只是提供金属腐蚀的可能性,并不能真实,反映金属铝的实际腐蚀进程与腐蚀形式,因为这是属于腐蚀的动力学的技术范畴,而金属腐蚀的动力学(即腐蚀速度)问题恰恰又是工程技术人员和使用部门最关心的问题。
表1-1 金属的电位序

①标准氢电极:SHE,standard hydrogen electrode。
尽管从热力学角度考虑,铝是非常活泼的金属,但实际上铝及铝合金的腐蚀速度并不快,具有比较好的耐腐蚀性能。即使不像一些广告词说的铝“永不生锈”,铝在中性大气、天然水、某些化学品以及大部分食品中都可以使用许多年。这完全是由于铝表面与空气反应形成的自然氧化膜的钝性,也就是说铝的耐腐蚀性能实际上取决于铝表面形成的氧化物膜的状态和本性。这种表面氧化膜如果人为地强化形成,例如通过众所周知的阳极氧化处理,就可以得到铝的阳极氧化膜,其表面耐腐蚀性要比自然氧化膜更加优良和可靠。当然,在使用过程中需要考虑表面氧化膜破损的可能性,尤其在铝与其他金属电偶接触时,不能只考虑氧化膜的耐腐蚀性,还应该考虑氧化膜破裂后的金属铝的活性,这样才不至于发生意外事故。特别值得注意的是,自然氧化膜的耐腐蚀性的保持是相当有限的,因此利用金属的电位序,从热力学角度出发密切关注与考虑铝材本身实际腐蚀的可能性,仍然不能认为是完全没有意义的,也就是说表1-1中金属电位序中铝的活性位置,对于铝的腐蚀可能性的判断和预防,仍然有非常现实的预警作用。

图1-1 铝的电位-pH图
铝是一种两性金属,在酸性介质中生成铝盐(如硫酸铝),在碱性介质中生成铝酸盐(如偏铝酸钠)。图1-1为铝的电位-pH图,用铝的电位与溶液的pH之间关系揭示铝在溶液中的热力学稳定性状态,或者说铝在水溶液中的电化学行为,对于预防铝的腐蚀非常重要。当铝在酸性溶液中(pH小于4),电位处于-1.8V(SHE)以下时,铝位于免蚀区,理论上是以“金属铝”的状态存在,即铝处于阴极保护的状态,不发生任何腐蚀;当铝的电位处于-1.8V(SHE)以上时,理论上铝以三价铝离子形式(Al3+)存在,即处于腐蚀区。如果在中性溶液中,即pH大约在4~8时,当铝的电位约大于-2.0V(SHE)时,其表面形成氧化膜,即处于钝化区;如铝的电位小于-2.0V(SHE),则其也以“金属铝”的状态存在。当溶液pH大于9,即在碱性溶液中,铝处于腐蚀区时,则生成铝酸盐()。
应注意的是,上述的“铝的电位”并不是电解池的“外加电压”,它们的差别必须分清,不可以混淆。实际上外加电压包括铝(铝还有氧化膜存在)的阳极电位、阴极电位和溶液电阻造成的电位(即IR降)三个部分。一般说来,铝的腐蚀形态,在酸性溶液腐蚀区以局部腐蚀形式为主,而在碱性溶液腐蚀区则往往呈全面腐蚀形式。铝的腐蚀程度和形式不仅取决于接触的环境介质及其环境温度,而且与铝合金的成分、杂质以及铝合金状态关系十分密切。此外,尽管铝在酸性或碱性溶液中处于腐蚀区,但在阳极氧化处理时还是可以成膜的。此时只要铝阳极氧化膜生成速度大于氧化膜的溶解速度,则铝的阳极氧化膜仍然可以继续生成。
自然氧化膜的厚度随大气中放置时间而增大,可以达到200nm左右。为了提高铝的耐腐蚀性,可以在铝材表面采用化学方法或电化学方法强化生成较厚的氧化膜。表1-2是铝在几种条件下生成氧化膜的情况。干燥大气中形成的氧化膜最薄,只有纳米级别。化学氧化膜一般为1~3μm厚,可以作为有机聚合物膜的底层。普通阳极氧化处理可以生成厚3~30μm的铝阳极氧化膜,建筑用铝合金门窗的阳极氧化膜厚度一般只要求在20μm以下。耐磨耗的机械零部件,可能要求生成厚60μm左右的铝硬质阳极氧化膜。
表1-2 铝在几种条件下生成的氧化膜厚度

(1)铝的大气腐蚀。在通常的大气条件下,铝处于钝化区,此时在铝表面生成一层很薄的自然氧化膜,阻止了铝与周围环境的继续接触,所以铝甚至比黄铜的腐蚀速度还要慢。由于各地大气成分差别很大,铝材在不同地区的大气腐蚀速度与腐蚀形态也相差悬殊。表1-3是铝与常用有色金属在美国不同地区的大气环境中经过10年或20年的平均腐蚀速度,工业纯铝1100比铜、铅、锌腐蚀速度小得多。表中所列长达10年(即表中10a)或20年的现场(美国各地大气腐蚀试验站)挂片的腐蚀试验数据,尽管某些数据的“规律性”似乎欠佳,但是这些长期挂片的腐蚀数据还是非常难得和珍贵的,并有其一定的规律性,即沙漠和农村大气腐蚀慢,海洋大气腐蚀快,工业污染大气腐蚀最快。这些数据的珍贵之处是与现场使用状况比较接近,这是实验室快速试验数据无法模拟推算得到的。
表1-3 铝与常用有色金属铜、铅、锌在各种大气条件下的腐蚀速度

不同铝合金牌号、不同铝合金形式的板材或型材,在不同的大气腐蚀环境下得到不同的腐蚀速度是很正常的。铝合金通常并不发生全面腐蚀而是出现点腐蚀等局部腐蚀现象,这是由铝合金的成分、状态和加工历史决定的,也是不同的大气环境造成的。海洋大气和工业大气对铝合金腐蚀要比乡村大气(或干燥的沙漠环境)严重得多,表1-4是不同铝合金型材或板材在各种大气条件下的十年大气腐蚀数据,包括平均腐蚀深度(μm)、平均点腐蚀深度(mm)和最深点腐蚀深度(mm)。数据选自日本各地的大气腐蚀试验站,平均腐蚀深度是通过腐蚀试验前后的质量之差得到的,平均点腐蚀深度是选择最深12个点的平均值得到的,最深点腐蚀深度是选择测量得到最深的12个点的最大值。数据表明,点腐蚀深度(mm)与平均腐蚀深度(μm)的数据显示出数量级的差别,提示我们更应该关注铝合金的点腐蚀状态,点腐蚀才是铝合金构件破坏的决定性因素。
表1-4 不同铝合金在日本各大气腐蚀站的十年大气腐蚀数据

注:a—平均腐蚀深度,μm;b—平均点腐蚀深度,mm;c—最深点腐蚀深度,mm。
(2)铝在碱性溶液中的腐蚀。碱能与表面氧化铝膜反应生成偏铝酸钠和水,然后再进一步与金属铝反应生成偏铝酸钠和氢气。随碱浓度的增加和环境温度的升高,铝的腐蚀速度迅速加快,如图1-2和图1-3所示。工业上利用铝在碱中发生全面腐蚀这一特点,选择合适的碱溶液浓度和腐蚀温度,广泛采用碱洗除去铝表面的氧化物。

图1-2 铝在25℃不同浓度NaOH溶液中的腐蚀

图1-3 铝在不同温度10%NaOH溶液中的腐蚀
(3)铝在酸溶液中的腐蚀。铝在不同的酸中有不同的腐蚀行为。一般来说,铝在浓的氧化性酸中会生成钝化膜,具有较好的耐腐蚀性,而在稀酸中存在“点腐蚀”现象。铝在20℃的硫酸、磷酸、硝酸和乙酸中的腐蚀速率随酸浓度的变化如图1-4和图1-5所示。由图1-4和图1-5可见,铝在磷酸中随酸浓度增大腐蚀速率上升。铝在硫酸中,当硫酸浓度小于30%时,腐蚀速率很低;浓度大于30%后,腐蚀速率陡然增加。当浓度达到80%以后,铝又转入钝态,腐蚀速率明显下降。铝在硝酸或乙酸中的腐蚀速率较小(请注意两图的纵坐标其腐蚀速率的量纲不同,左侧纵坐标为硝酸,右侧为乙酸),在乙酸中随乙酸的浓度增加整体呈下降趋势。铝在硝酸中,当硝酸浓度在30%以下时,腐蚀速率随酸浓度增加而上升;当硝酸浓度大于30%以后,铝的腐蚀速率随酸浓度增加而减小;直至硝酸浓度大于80%后,铝又完全进入钝态而腐蚀速率极小。

图1-4 铝在20℃硫酸和磷酸中的腐蚀

图1-5 铝在20℃硝酸和乙酸中的腐蚀
(4)铝在中性无机盐溶液中的腐蚀。在中性无机盐溶液中,铝可以处于钝态,也可能由于某些阳离子或阴离子的作用发生腐蚀。铝材在海水中点腐蚀比较严重,是由于海水中氯离子的作用。卤素元素氟和氯等元素的离子半径很小,容易穿透氧化膜造成点腐蚀。无机盐溶液中的氧化性阴离子,如等可以促使铝的钝化。如果铬酸盐溶液中同时加入F-或Cl-等活化性离子,可以得到较厚的钝化膜,这就是铬酸盐处理在活化离子存在下得到较厚的铬化膜的原因。无机盐溶液中的阳离子对铝腐蚀也有很大影响,如果盐溶液中存在电位比铝正的金属离子(Fe2+,Cu2+,Ni2+等),则会加速铝材的点腐蚀。电位差别愈大,铝的点腐蚀愈严重。专门用来加速检测铝阳极氧化膜盐雾腐蚀的CASS试验,就是铜加速的乙酸盐雾试验,即利用铜离子的加速腐蚀作用,实现对铝阳极氧化膜的快速盐雾腐蚀试验。
铝的腐蚀影响因素有两个大的方面,第一方面是铝的耐腐蚀性,铝合金成分、杂质及其加工状态决定了铝的耐腐蚀性。笼统地说,纯铝的耐腐蚀性最强,随着铝的纯度下降和合金化元素的添加,铝合金的耐腐蚀性呈现不同程度的降低。在通常添加的合金化元素中,铜的负面影响最明显,镁的影响最小。表1-5列出了主要合金化元素和杂质对于铝耐腐蚀性的影响。Cu的负面影响最明显,Fe+Si和Si其次,其他元素的不利影响比较小。铝合金成分(即牌号)固定后,其冶金状态是由加工过程决定的。变形铝合金冶金状态由加工硬化过程和固溶热处理过程决定,铸态(含压铸)铝合金也有热处理过程。第二方面是环境的腐蚀作用,环境状态复杂多样,从室内外大气到各种介质,例如水、土壤、食物、多种化学品及建筑物材料等五花八门。而室外大气根据其地域不同,又大致可以分为农村大气、海洋大气和工业大气。农村大气比较清洁,污染程度最小,加速腐蚀作用也小;海洋大气的氯化物会加速腐蚀;工业大气的污染类型和污染程度不同,其腐蚀加速程度的差别也非常明显。
表1-5 主要合金化元素和杂质对于铝耐腐蚀性的影响

1.2 铝的腐蚀形态
铝属于钝化型金属,除了在碱和磷酸等溶液中呈现全面腐蚀以外,铝合金出现的主要腐蚀形态,是由于钝化膜局部破坏而发生的局部腐蚀。局部腐蚀正是铝合金结构破坏的主要危险,通常的腐蚀速度难于表征局部腐蚀的程度。各种腐蚀形态并非一定相互排斥,可能同时存在互相关联渗透,甚至彼此促进。因此在分析判断腐蚀事例时,必须在掌握金属腐蚀理论和不断增长防腐蚀经验的基础上,充分注意细致考察铝合金腐蚀的原因。
铝合金的局部腐蚀形态主要有点腐蚀(pitting corrosion,又称小孔腐蚀)、缝隙腐蚀(crevice corrosion)、电偶腐蚀(galvanic corrosion)、晶间腐蚀(intergranular corrosion)、应力腐蚀(stress corrosion)或应力腐蚀开裂(SCC)、丝状腐蚀(filiform corrosion)和层状腐蚀(layer corrosion,又称剥落腐蚀)等。其中点腐蚀、缝隙腐蚀和晶间腐蚀是钝化型金属的最典型的腐蚀形态,而丝状腐蚀和层状腐蚀是铝合金特殊的常见腐蚀形态。相对于全面腐蚀而言,金属的局部腐蚀是金属设备或构件腐蚀破坏的重要原因和形式。铝合金的应力腐蚀开裂与腐蚀疲劳较多见于高强铝合金。由于破坏发生比较突然,大多发生在受力的结构件上,具有极大的瞬间破坏的危险,已经引起学术界和工程界的广泛关注。研究人员对其进行了细致深入的机理研究,形成了从实验研究到机理探讨等大量的相关著作。在民用铝合金的腐蚀事例中,一般没有大的外加应力被忽视的情况,但值得注意的是应力腐蚀可能隐藏在其他的腐蚀形态之中。

图1-6 铝、钢、镀锌钢的腐蚀程度-时间关系
(1)点腐蚀。点腐蚀(又称点蚀、小孔腐蚀、孔蚀)是铝及铝合金最常出现的腐蚀形态之一。在大气、淡水、海水以及中性水溶液中都有发生点腐蚀的可能,严重的点腐蚀将导致穿孔。幸运的是腐蚀孔最终可能会自行停止发展,腐蚀量到达一个极限值。图1-6所示为典型的铝腐蚀程度-时间的关系,并与钢和镀锌钢的腐蚀行为进行比较,可以发现铝与钢的腐蚀行为差别很明显,铝的腐蚀随时间会自行减缓。铝合金点腐蚀的严重程度还与周围介质和铝合金成分有关,图1-7所示为6063合金和6351合金挤压材在不同大气条件(海洋、工业和农村大气)下的腐蚀程度-时间关系。实验表明,铝合金点腐蚀的介质中必须存在破坏氧化膜局部钝态的阴离子,如氯离子、氟离子等。还必须同时存在促进阴极反应的物质,如水溶液中的溶解氧、铜离子等。从铝合金系来看,高纯铝一般较难发生点腐蚀,含铜的铝合金的点腐蚀最敏感,而Al-Mn系和Al-Mg系合金的耐点腐蚀性能较好。

图1-7 6063合金和6351合金挤压材在不同大气中的腐蚀程度-时间关系(1in=0.0254m,下同)
(2)电偶腐蚀。铝的自然腐蚀电位很负,电位较负的金属铝与电位较正的金属(如铜等)或非金属导体(如石墨)在导电性水溶液中直接接触或电接触时,铝发生的加速腐蚀现象称为电偶腐蚀。如果腐蚀电池作用发生在两个金属之间,也称为双金属腐蚀(bimetallic corrosion),有时也称为接触腐蚀(contact corrosion),但是其腐蚀的本质就是腐蚀电位不同形成的电偶作用,并不是简单的接触。电偶腐蚀不可与缝隙腐蚀相混淆,其腐蚀原理与过程都不相同。电偶腐蚀发生的可能性和腐蚀的严重程度,除了与环境有关,还可以从相互接触金属的腐蚀电位的差别大小来预估。它们的电位差别愈大,则电偶腐蚀愈严重。如果阳极金属铝的面积与阴极面积相比较很小,即所谓小阳极大阴极,则腐蚀会显著加速,面积比相反则电偶效应就不明显。电位较负的金属铝处于电偶腐蚀状态时,有可能加速铝的其他腐蚀形态的发生,例如提高应力腐蚀开裂的敏感性等。两种金属之间存在电绝缘体(如铝阳极氧化膜),可以防止电偶作用引起的腐蚀,为此铝阳极氧化膜、有机聚合物膜、塑料垫片垫圈都可能起到防止电偶腐蚀的作用。
几乎所有铝合金都不能避免电偶腐蚀,表1-6所示为几种常见金属对于铝材电偶腐蚀的影响。杂散电流腐蚀虽然也是一种电偶腐蚀,但是杂散电流腐蚀并不是自然腐蚀的形式,因为杂散电流腐蚀的电流来源,是非指定回路上的外加电流或外界的感应电流(交流电或直流电)。只要消除这种电流,杂散电流腐蚀就可以避免。由于裸露部位的金属铝没有氧化膜的保护,在氧化膜破坏或开裂的部位的自然电位非常负而面积又很小,因此铝及铝合金的电偶腐蚀现象应该引起高度重视,需要细致观察方能减轻或避免发生。
表1-6 几种常见金属对于铝材电偶腐蚀的影响

(3)缝隙腐蚀。缝隙腐蚀是金属铝与其他金属材料或与非金属材料(不论是否导电)之间的表面相互不紧密接触形成狭缝或间隙,由于缝隙内外差异充气电池的作用,缝隙内部或近旁(为阳极区)的钝化膜局部破坏,从而发生局部加速腐蚀的现象。缝隙腐蚀也是钝化型金属的一种特殊腐蚀形式,而铝合金的缝隙腐蚀则比较常见。一些其他的腐蚀形态,原理上也可能是缝隙腐蚀引起的。铝表面的沉积物下面或铝表面的污垢下面也可以认为形成了缝隙,因此从腐蚀原理上讲,沉积物下腐蚀(deposit corrosion)或垢下腐蚀(scale corrosion,poultice corrosion)也就是一种缝隙腐蚀。建筑门窗用6063铝合金挤压材表面灰浆下的腐蚀,除了灰浆的腐蚀作用外,也往往有垢下腐蚀,即缝隙腐蚀的一个实例。值得重视的是,缝隙腐蚀的缝隙尺寸应该是一个临界指标,过宽或者过窄的缝隙都不能构成缝隙腐蚀发生的条件。但是,临界尺寸并不是一成不变的数值,它与铝合金的成分、杂质、溶液或介质成分等诸多参数有关。
缝隙内部与外部表面氧和铝离子的浓度不同,有外部大面积阴极就可能构成缝隙中腐蚀加速甚至发生局部阳极腐蚀孔的条件。当电流从缝隙内的活性阳极区流到缝隙外的大面积阴极区,就建立起了电偶电池,这就是铝的缝隙腐蚀机理。在富氯离子的垢下面,腐蚀孔内铝的羟基氯化物在热力学上是不稳定的,但是生成凝胶后在动力学上就稳定了,凝胶使缝隙酸化并且使之活化。如果缝隙或外部阴极变干燥了,腐蚀可能就停止了。当缝隙处于异种金属之间,此时可能同时存在电偶腐蚀,则腐蚀发展更快,破坏性也更大。缝隙腐蚀往往与铝合金品种关系不大,一些耐腐蚀的铝合金也不能避免缝隙腐蚀的发生。
(4)晶间腐蚀。纯铝一般不会发生晶间腐蚀,Al-Cu系、Al-Cu-Mg系和Al-Zn-Mg系合金的晶间腐蚀敏感性较大。
晶间腐蚀的原因一般与热处理不当有关系,由于合金化元素或金属间化合物沿铝合金晶界的沉淀析出,析出物相对于晶粒是阳极从而构成腐蚀电池,引起晶界腐蚀加速。晶间腐蚀是沿着金属晶界或紧靠晶界所发生的局部选择性腐蚀现象,晶间腐蚀的原动力是晶界或晶界两侧与晶粒本身(即铝基体)的电位差异。晶粒边界可能由于第2相的析出,晶间与相邻晶粒或晶间与近侧贫化区形成电位差,从而引起晶间腐蚀而破坏了晶间与相邻晶粒的结合力。晶间腐蚀的金相特征为网络状,在铝合金腐蚀中比较常见。例如在2024铝合金中,晶间CuAl2的第2相析出物比基体的钝性更强,在晶界的第2相析出物两侧都存在一条贫铜的窄带,加速晶间附近贫铜区的腐蚀。Mg含量小于3%的铝合金(例如5XXX系中某些铝合金),是铝合金中比较抗晶间腐蚀的品种。而Mg含量大于3%的铝合金(如5083),由于晶间析出的Mg2Al3是阳极相,会发生优先腐蚀而引起比较严重的晶间腐蚀。一般来说,如果晶间的第2相析出物呈连续链状分布,则晶间腐蚀的敏感性最强。当晶间第2相析出物呈断续分布时,晶间腐蚀不容易发生。第2相析出物的宽度越大,则晶间腐蚀敏感性也越大。
由于晶间腐蚀很难用通常的表面腐蚀现象加以分辨,实际上用肉眼很难从表面直接观察到是否发生了晶间腐蚀,而且几乎也不引起材料的质量损失或减薄,因此晶间腐蚀成为铝合金设备或结构中危险性很大的一种腐蚀破坏形态。
(5)应力腐蚀。铝合金腐蚀形态中应力腐蚀是最隐蔽的腐蚀形态之一,由于材料晶界开裂的发展,可以导致铝合金构件或设备的全面破坏或解体,所以应力腐蚀开裂(SCC)是既隐蔽又危险的腐蚀形态。SCC是外加应力或残余应力与环境(尤其含有氯离子时)的共同作用引起的腐蚀从而导致的开裂。为此发生SCC一般需要三个条件,即铝合金的成分与组织状态,外加应力或残余应力(铝合金存在达到其合金屈服强度50%以上的张应力),以及腐蚀性环境(尤其含氯离子等离子)。如果外加的应力是交变的应力,则称之为腐蚀疲劳。
Al-Cu、Al-Mg、Al-Zn-Mg、Al-Li等铝合金都有SCC的敏感性,其中Al-Mg系的SCC敏感性因Mg含量的大小而不同,只有在Mg含量大于3%时,在晶界析出β-Al-Mg金属间化合物第2相时才发生SCC。Mg含量在4.5%以上时SCC的敏感性可能更大。为此在大约65℃以上的环境中使用的铝合金的焊接结构件,不能使用Mg含量超过3%的铝合金材料。Mg含量达到4.5%的5083铝合金,即使在室温下使用,也需要关注调质和加工率以降低SCC敏感性。高强度铝合金,如7000系的Al-Zn-Mg或Al-Zn-Mg-Cu的SCC敏感性最大。通常需要经过双级时效适当牺牲一些强度,来提高抗SCC的性能。在Al-Zn-Mg合金中,晶界的局部氢脆起着一定的促进SCC的作用,研究表明腐蚀产生的新生态氢沿着晶界扩散,导致铝合金强度下降直至最终发生开裂。压力加工的精心操作可以降低铝合金SCC的敏感性,但是以后的加工过程或使用过程中可能会恢复SCC的敏感性,例如铝合金设备的焊接过程、涂层加热固化工艺过程、铝合金设备在升温下操作等,都可能恢复应力腐蚀开裂的敏感性。关于铝合金成分及其组织结构(调质状态)对于SCC的影响参见表1-7。对SCC敏感的铝合金有Al-Cu系、Al-Zn-Mg系、Al-Zn-Mg-Cu系、Al-Mg系(约含3%以上的Mg),以及Si含量较高的Al-Mg-Si系铝合金。
表1-7 各种铝合金应力腐蚀开裂敏感性(3.5%的氯化钠溶液)的比较

注:“应力腐蚀敏感性”中数字含义为1—实际使用和实验室都没有问题;2—实际使用没有问题,但经实验室试验,沿板厚方向存在一点问题;3—实际使用只要在板厚方向有张应力,就有产生裂纹的危险,实验室在氯化钠溶液中产生裂纹;4—实际使用在压延方向容易产生横向裂纹。
对应力腐蚀开裂不敏感的铝合金有纯铝、Al-Mn系、Al-Si系、Al-Mg-Si系,以及含Mg 3%以下的Al-Mg系铝合金。Cr、Mn、Zr有防止应力腐蚀开裂的效果,这些微量成分的添加在热加工时有提升再结晶温度的效果,有助于保持热轧板材、挤压材的纤维组织,纤维状组织的铝材的耐SCC性能比再结晶组织铝材优异。
铝合金中添加Cu一般会降低耐腐蚀性,同时也会降低耐SCC性。Al-Zn-Mg系铝合金添加Mn、Cr、Zr、Cu、Ag,可以细化再结晶晶粒,有效形成纤维状组织,同时降低由不溶性化合物的析出引起的晶界周边的电位差,并抑制晶界的应力集中。T4处理最容易发生SCC,T6和T7处理可显示最好的SCC特性。7075-T6铝合金容易发生SCC。采用过时效处理(T7)可防止SCC发生。过时效处理使晶界析出的状态发生变化,晶粒与晶界的电位趋同,从而降低内应力。5083铝合金的热处理温度影响SCC性能,180℃处理在晶界析出β相,其SCC寿命最短。在铝合金中添加Mn、Cr元素抑制其晶界析出可改善SCC性能。在2000系铝合金中,人工时效的T8铝材具有比较好的耐SCC性和机械强度。
铝合金的SCC发生机理,早期以阳极溶解学说为主,之后氢脆学说占了上风。氢脆产生的SCC,其破坏面没有析出物溶解。Al-Zn-Mg系和Al-Mg系铝合金SCC中的裂纹扩展就是如此,证实氢脆为SCC的主要破坏机理。应力腐蚀开裂还可能与层状剥落腐蚀有关,这是非常危险的破坏形式。层状腐蚀是变形铝合金特有的腐蚀形态,在研究层状腐蚀时,发现腐蚀沿着晶界平行于金属表面发展,而腐蚀产物聚集在层间又提供足够的拉应力,从而加快层状剥落。在大部分可热处理的铝合金和加工硬化的Al-Mn和Al-Mg合金中,都可能发生这类腐蚀情况,但是Al-Cu和Al-Zn-Mg-Cu铝合金在海洋性气候中更容易发生这类腐蚀情况。
(6)丝状腐蚀。丝状腐蚀最早于1960年代在航空器的有机涂层下发现,至1990年代,欧洲陆续报道在北欧沿海地区建筑铝型材门窗喷涂层下也发现丝状腐蚀导致喷涂层的脱离。我国东南沿海地区也发现过建筑铝门窗粉末喷涂层下的丝状腐蚀引起涂层的鼓泡和脱离,由此在国内外逐渐引起对有机聚合物涂层下丝状腐蚀的广泛关注。近年来,在涂层工艺路线的改进(如采用阳极氧化膜作为底层)和新检验标准的颁布(GB/T 26323—2010和ISO 4632:2003)等方面都有新的变化,虽然铝阳极氧化薄膜可以避免发生喷涂层下的丝状腐蚀,但是这条工艺路线在技术和经济方面的实用性、可行性和可靠性尚需论证,至少需要与铝阳极氧化/电泳涂漆复合膜进行全面对比之后,证明效果可靠才可能顺利实施。
丝状腐蚀是一种在铝合金有机涂层下发展的特殊腐蚀形式,一般发生在有机聚合物涂层或搪瓷膜等绝缘性表面膜的下面。丝状腐蚀从表面膜层与金属铝基体的界面开始发生,并在涂层下面呈蠕虫状生长发展的膜下纤维状的腐蚀形态。丝状腐蚀生长发展时,具有难以横向扩张的特征。丝状腐蚀从涂层/金属切断部位的端面、涂层的损伤位置、钝化膜的破坏点,或折弯加工的破损部位作为起点开始生长,最长可能形成25~30mm的涂层肿胀。
丝状腐蚀尖端的活性头部(阳极区)存在pH约为1的酸性液体,腐蚀产物堆积成白色的氢氧化物(阴极区)常呈现碱性,丝状腐蚀的活性头部会产生氢气。
生成的氢氧化铝在头部周围的中性区域沉淀,向头部的扩散受到抑制,形成缺氧状态。头部内外就形成了一种氧浓差电池,这使丝状腐蚀可以继续进行。
丝状腐蚀还与铝合金材料有一定的关系,随着铝合金中Cu含量的增加,在同一电位下的铝合金基体的耐腐蚀性变差。日本的实验表明,6000系铝合金通过制备化学转化膜抑制丝状腐蚀的效果是不太理想的。Mg2Si析出较多的位置或Fe、Si及其金属间化合物的析出位置,容易成为丝状腐蚀的起点,结晶析出物还会加快丝状腐蚀的发展。
丝状腐蚀的机理在一定意义上可以理解为另一种形式的缝隙腐蚀,它总是开始于有机涂层与铝金属基体的界面位置。丝状腐蚀通常由卤素离子触发,并在一定湿度和温度环境下迅速发展。实验证明相对湿度为75%~95%、温度为20~40℃时,铝合金丝状腐蚀比较容易发展生长。还有报道在相对湿度<30%的盐酸蒸气中也发现过丝状腐蚀现象,并且随着湿度的提高丝状腐蚀加快。据报道,典型的丝状腐蚀的平均生长速度可能达到0.1mm/d,甚至发现更快的达到0.45mm/d。理论预测和实践证明,变形铝合金的加工方向的丝状腐蚀发展速度要比垂直加工方向更快些。
既然丝状腐蚀发生在铝合金的有机聚合物涂层的下面,因此有时候也将其称为膜下腐蚀(undercoating corrosion)或膜下丝状腐蚀,强调丝状腐蚀是在有机涂层下面发生并呈蠕虫状发展的特征。如果有机物涂层是透明或半透明膜,那么肉眼甚至可以透过透明膜清楚地看到膜下丝状腐蚀的发展踪迹。这个腐蚀细丝由活性的头部(阳极区)与具有腐蚀产物的尾部(阴极区)组成,腐蚀过程由头部与尾部的差异充气电池所驱动,其腐蚀原理与缝隙腐蚀相同。当然简单地将丝状腐蚀作为缝隙腐蚀的一种形式,完全忽视有机聚合物膜本身的可渗透性可能对于金属铝基体腐蚀的影响,并不全面。在发现膜下丝状腐蚀并探讨丝状腐蚀的原因和防治措施时,可能需要深入观察和调查,至少应该考虑有机聚合物涂层的渗透性对于具体腐蚀过程的影响程度。丝状腐蚀的发生与严重程度与铝合金成分及其第二相金属间化合物在铝材中的分布状态、涂层前的预处理工艺和环境因素等都有关系。环境因素除了环境类型和成分以外,还包括湿度、温度、氯化物含量等变动参数。铬酸盐预处理的粉末喷涂膜下也已经发现存在丝状腐蚀,但是在无铬化学转化预处理工艺出现以后,发现粉末喷涂膜下面的丝状腐蚀更容易发生。由于铬酸盐预处理和无铬预处理的粉末喷涂膜下都有丝状腐蚀的报道,所以近年来开始研发铝阳极氧化薄膜作为有机聚合物涂层的预处理膜,并且已经迅速导入国际标准、欧洲Qualicoat新版规范和我国国家标准(GB/T 26323—2010,GB/T 5237.3—2017)中。
铝合金涂层前化学预处理会影响丝状腐蚀敏感性,试验表明铬酸盐预处理比磷铬酸盐预处理或无铬预处理的丝状腐蚀敏感性低得多。采用0.4~0.6g/m2的铬化物预处理膜是目前最有效的涂前预处理方法,但铬酸盐并不环保,为此了解一些影响因素的信息对于防止或降低丝状腐蚀发生有益。
①Cl离子是触发丝状腐蚀的条件,并且在丝状腐蚀部位已经检测出较多的Cl离子。故可知海洋性大气是触发丝状腐蚀的条件,大陆性干燥气候可能不会发生丝状腐蚀。
②在Cl离子触发丝状腐蚀的条件下,适合的温度和湿度是丝状腐蚀生长发展的条件。在日本,6~8月间的高温多湿的时期最容易发生丝状腐蚀。我国从浙江到海南的沿海地区也可能是丝状腐蚀的高发区,但是我国广大的内陆地区基本不必顾虑丝状腐蚀的严重性。
③降低涂层的内应力,能够缓解丝状腐蚀尖端部位的应力,有利于抑制丝状腐蚀的发展。喷涂层的附着力较强,也有利于抑制丝状腐蚀生长。
④涂层透水性越小同时膜厚越厚,丝状腐蚀越容易发生,这是由丝状腐蚀机理所决定的。普通腐蚀应该是涂层渗透性越大,环境的腐蚀性溶液越容易渗入,涂层下面的腐蚀越快。然而丝状腐蚀由氧浓差电池所驱动,因此情况正好相反。
试验结果和现场服役都表明,在阳极氧化预处理的有机涂层中没有发生丝状腐蚀的实例,铝阳极氧化预处理具有抑制丝状腐蚀的效果。即使是1μm厚的薄阳极氧化膜也能起到防止丝状腐蚀发生的作用,为此欧洲标准建议涂层下采用铝阳极氧化膜来防止丝状腐蚀的发生。铝阳极氧化膜是在金属铝的晶粒表面共格生长形成的,没有传统意义上“涂层/金属的界面”的概念,所以丝状腐蚀一般不会发生在铝阳极氧化膜下面。而电泳涂漆膜是在铝阳极氧化膜上而不是在铝合金基体上形成的,理论和实践都证实不存在丝状腐蚀问题,为此铝阳极氧化电泳涂漆复合膜一般不需要进行丝状腐蚀检验。
(7)层状腐蚀。层状腐蚀又称剥落腐蚀或简称剥蚀(exfoliation corrosion),是变形铝合金常见的一种腐蚀形式,更多见于挤压铝合金型材。其腐蚀特征是沿着平行于铝合金表面的晶间而扩展的一种选择性腐蚀,从而使铝合金发生层状剥离或分层开裂。当铝合金与其他金属处于电偶接触状态时,层状腐蚀可能会加速。如果层状剥离程度比较轻微,一般只产生一些裂片、碎末,或者形成一些泡状突起。如果层状腐蚀严重,则发生大片连续的层状剥落,直至金属结构完全解体。
Al-Cu-Mg合金发生层状腐蚀的情况最普遍。Al-Mg合金、Al-Mg-Si合金和Al-Zn-Mg合金也有层状腐蚀发生的报道。对于Al-Mg合金而言,Mg含量越高,β相数量越多,同时变形量越大,晶粒被拉得越长,β相沿晶间析出的网络越连续,此类铝镁合金的层状腐蚀可能性就越敏感。调整高强Al-Cu合金的时效处理工艺,基本上可以克服此类铝合金的层状腐蚀问题。有些专家认为,层状腐蚀与铝合金内部存在的应力而引起的应力腐蚀有关系,在适当消除铝合金内应力的情形下,似乎可以降低甚至消除层状腐蚀的发生,这可能表明了各种腐蚀形式的相互影响和关联。
层状腐蚀同时伴随剥蚀形态,是由铝合金晶界的选择性腐蚀引起的,尤其在强压延组织时,更容易发生层状剥落腐蚀。在强压延组织的挤压型材的内缘性腐蚀,产生分离并伴随剥落,从铝表面到表面下的金属内部形成引起大块剥落的层状腐蚀。层状剥落腐蚀是由铝合金表面下的活性金属间化合物引起的。如Al-Cu系铝合金中存在CuAl2,在Al-Mg系铝合金中存在Mg5Al8、Mg2Al3、MgZn2等析出物,形成腐蚀电池的阳极区,优先溶解,阳极区的腐蚀沿晶界进行,形成鳞片状的被拉长的层状腐蚀物而引起剥落。层状剥落腐蚀也可能与晶界腐蚀相关联,晶界的析出物和靠近晶界的腐蚀产物之间产生电位差,使阳极区优先腐蚀形成晶界腐蚀而继续进行层状腐蚀剥落。
铝合金的剥落腐蚀从截面来看是一种在铝合金内部进行的晶界腐蚀,一旦形成阳极区,由于晶界的阳极区的面积比阴极区的面积小,小阳极和大阴极的面积差使腐蚀进行得很激烈。而且在晶界阴极析出腐蚀产物的生长,进一步促进了层状剥落的发生。铝合金的层状剥落腐蚀通常在含有氯离子的环境中发生,剥落一般沿压延或挤压的变形方向发展。挤压成形产品中由于表面再结晶,剥落腐蚀会较轻。
铝合金车辆使用的Al-Zn-Mg系合金的底架,焊接热影响区有时发生剥落腐蚀。Al-Zn-Mg系合金中,剥落腐蚀和应力腐蚀开裂的敏感性都增大。因此,在该铝合金的焊接热影响区会有一定程度的剥落腐蚀敏感性。
为了防止应力腐蚀开裂,通过添加微量元素和热处理将金属组织调整为纤维状组织可以取得较好效果。层状剥落腐蚀通常也可以添加微量元素或通过热处理进行防控。在7×××系铝合金中,通过过时效、再结晶和添加元素可以减轻层状剥落腐蚀。在2×××系铝合金中,通过T6或T8的人工时效处理,也可以提高耐剥落腐蚀性。在适用于电化学防腐蚀措施的海水环境中,对铝合金结构件进行电化学防腐蚀处理,将铝合金的防腐蚀电位控制在-1.02V(SCE)左右也是有效的。
1.3 铝合金
铝合金可以分为变形铝合金及铸造铝合金两大类,见表1-8。
表1-8 铝合金的分类

铝合金的品种繁多,国际上有据可查的变形铝合金牌号已达400多个,实际上各企业根据用户性能要求可以派生出更多的铝合金成分与状态。我国早在1996年就颁布了三个相关的标准,即GB/T 16474《变形铝及铝合金牌号表示方法》,GB/T 3190《变形铝及铝合金化学成分》和GB/T 16475《变形铝及铝合金状态代号》。目前新标准改变了原标准的牌号表示方法,直接按照国际标准的牌号注册组织的命名原则,采用四位数字表示。这样我国变形铝及铝合金的牌号,与国际上大多数国家的表示方法基本一致。我国标准目前已经列出143个化学成分的变形铝合金牌号,按主要合金元素分为8大系列铝合金,在1.3.1节“变形铝合金系”中说明。铸造铝合金按照合金成分分为9个系列,见表1-8。压铸铝合金的工业应用日渐广泛,尤其直接作为机械零部件使用,但是其阳极氧化处理与变形铝合金有所不同,本书第7章有关于压铸铝合金的阳极氧化处理的介绍。
1.3.1 变形铝合金系
变形铝合金系是按主要合金元素来分类确定的。1×××是工业纯铝,铝含量不小于99.00%,其最后两位数字表示最低铝百分含量中小数点后的两位。2×××~8×××是铝合金系列,最后两位数字只用于识别同一系列中的不同铝合金,第二位数字为0表示原始铝合金,如为1~9表示改型铝合金。或牌号第二位英文字母表示原始铝合金的改型,即A表示原始铝合金,B~Y表示改型铝合金。
(1)1×××系工业纯铝。1×××系是纯度在99.00%以上的工业纯铝,主要杂质为铁、硅等。纯铝的加工性能和耐腐蚀性优良,其阳极氧化膜的透明度佳。杂质含量越低其加工性、耐腐蚀性、焊接性和阳极氧化膜透明度越好。但是工业纯铝强度较低,不适合用于结构件,可用于家庭用品、厨房用具、电器器具、化学工业和食品工业的设备等,高纯铝还在输电电缆或散热板上大量应用。纯铝阳极氧化处理的性能好,其阳极氧化膜无色透明,适于制备装饰品和反射板等。
(2)2×××系铝合金。2×××系铝合金是Al-Cu系可热处理(固溶处理和时效处理)强化的铝合金,有管、板、棒、型、线和锻件,代表性的主要2×××铝合金目前有2014、2024和2017三个牌号。2×××系铝合金成分除铜之外,镁也是主要合金化元素,还有少量锰、铬、锆等。铜含量一般在2%~10%,其中含4%~6%时强度最高。铜和镁能提高铝合金的强度和硬度,但是影响其伸长率。锰、铬等可细化晶粒,提高铝合金再结晶温度和可焊性。2×××系铝合金强度高,适用于制作机械部件和飞机零部件等。由于熔化焊接性能较差,通常采用铆钉或螺钉连接或电阻焊接。当需要高耐腐蚀性时,可以在表面包覆铝板轧制成为复合铝板使用。
(3)3×××系铝合金。3×××系铝合金是Al-Mn系热处理不可强化的铝合金,以薄板状态使用较多。锰既能提高铝合金的力学性能,又不使耐腐蚀性下降。添加少量铜有利于将点腐蚀变为全面腐蚀,添加1%的Mg可以提高强度。3×××铝合金有好的成形性、可焊性和耐腐蚀性。3×××系的代表性铝合金有3003、3004、3005、3104和3105等,适用于一般器物、饮料罐、食品器具、电机用品和建筑用装修板材。
(4)4×××系铝合金。4×××系铝合金属Al-Si系热处理不可强化的铝合金,硅含量一般在4%~10%,常用铝合金为4043和4032。当用于轧制钎焊板的变形铝合金时,硅含量甚至达到12%。添加少量镁、铜和镍有助于提高高温强度和硬度,4032锻造铝材适合制造活塞或高温工作的铝合金零部件。含7.5%Si的4343铝合金,熔融温度低,可以作为钎焊材料。阳极氧化处理时由于硅微粒分散在铝阳极氧化膜中,视含量多寡外观呈灰色至黑色,也是铝阳极氧化呈合金发色的例证。
(5)5×××系铝合金。5×××系铝合金是Al-Mg系热处理不可强化的铝合金,镁含量一般不超过5.5%,其焊接性、成形性、耐腐蚀性和阳极氧化性都比较好,用途非常广泛。镁既提高强度,又不会使延展性过分降低,添加少量锰使得含镁相沉淀均匀,对耐腐蚀性有利。除含锰之外,还含有少量铬、钛等。5×××系铝合金有板、薄板、管、线、棒和异形材。代表性的5×××系有5052、5056和5083铝合金,适合于建筑、车辆、船舶的结构材料,以及用作机器部件等。5N01合金通过化学抛光/阳极氧化可以保持高光泽,被称为高光泽铝合金,多使用于装饰品。镁含量高的容易发生应力腐蚀开裂,如果考虑不发生应力腐蚀开裂,一般镁含量上限是3%。
(6)6×××系合金。6×××系铝合金是Al-Mg-Si系热处理可强化的铝合金,析出的Mg2Si相就是众所周知的强化相。加入锰和铬可以中和铁的有害作用,添加铜和锌提高铝合金的强度,又不降低耐腐蚀性。该系合金具有很好的综合性能,阳极氧化性能优良,其应用面相当宽。其中6063铝合金的挤压加工性能优良,广泛用于建筑门窗铝合金型材,也用于车辆、家具、台架等处。6061铝合金由于强度高于6063铝合金、可焊性和耐腐蚀性都比较好等原因,其管、棒、型材常作为工业结构件。而6463铝合金由于阳极氧化处理后保持光亮外观,常用于建筑、汽车及各种器具的内外装饰件。6005铝合金用于强度要求大于6063的结构件。
(7)7×××系铝合金。7×××系铝合金是Al-Zn-Mg系热处理可强化的铝合金。该系铝合金有Al-Zn、Al-Zn-Mg、Al-Zn-Mg-Cu合金。加入镁和铜及其他微量元素,制成了一批有商业竞争力的高强度铝合金。如再添加钛和锆,可以细化晶粒并提高可焊性。该系代表性铝合金有7075、7N01等,其中不少铝合金由于强度高而在高铁列车及航空航天方面得以应用。
(8)8×××系铝合金。8×××系铝合金是以Al-Li系为主的热处理可强化的铝合金。添加Li可以降低合金的密度,每添加1%的Li,密度可降低3%,并增加6%的弹性模量。其力学性能特点是强度高、低温抗疲劳性好、高频抗疲劳性能好等,但是,合金的伸长率低,低周抗疲劳性能差,断裂韧性低,而且该合金的各向异性比较大。
变形铝合金的应用范围非常广,各系列的变形铝合金都有其性能特点、主要形态及其相应的应用范围。表1-9扼要地介绍了各系列铝合金中几种常用铝合金的特点及其应用实例。表1-9的铝合金不仅是最常用的铝合金,也是在铝阳极氧化和表面处理中遇到比较多的铝合金。
表1-9 一些常用变形铝合金的特点及应用

本书的附录1“我国主要变形铝及铝合金牌号以及主要合金化元素的成分”,列出了我国7个系列58个变形铝合金的牌号以及主要合金化元素的成分与含量。附录2“我国主要铸造铝合金的牌号及主要合金化元素成分”,可供读者参阅。有关铝合金材料的详尽技术信息请参阅本章参考文献[2]。有关各类铝合金的微观组织结构,尤其是有关第2相金属间化合物析出的知识和信息,请参阅本章参考文献[26]。
1.3.2 铸造铝合金系
模具铸造和压力铸造的铝合金均属铸造铝合金。模具铸造或低压铸造的铝合金铸件,在国标GB/T 1173—2013《铸造铝合金》中已经明确规定。我国铸造铝合金代号由“ZL”(铸铝)及其后面三位数字组成,后面第一位数字表示合金系列,其中1~4分别表示Al-Si、Al-Cu、Al-Mg、Al-Zn系列合金,第二、三位数字表示合金顺序号。
铸造铝合金用于机械零部件大部分是压铸件,压铸铝合金牌号在国标GB/T 15115—2009《压铸铝合金》中有所规定。铝合金代号由“YL”(压铸铝)及其后面三位数字组成,第一位数字1~4分别表示Al-Si、Al-Cu、Al-Mg、Al-Sn系列合金,这与铸造铝合金的规定是相同的。第二、三两个数字为合金顺序号,与铸造铝合金的命名原则相同。由于本书中的压铸铝合金试验数据常常引用国外文献,为读者阅读方便,将主要压铸铝合金的中国代号与几个国外代号对照列于表1-10中。
表1-10 国内外主要压铸铝合金代号对照表

本书第7章有关于压铸铝合金的阳极氧化的介绍,涉及压铸铝合金的成分和状态对于铝阳极氧化和铝阳极氧化膜性能的影响,也涉及铸态铝合金的相关性能。
1.4 铝合金表面技术概述
为了克服铝合金表面性能方面的缺点,提高表面硬度、耐磨耗和耐腐蚀性,扩大应用范围,延长服役寿命,表面处理技术是铝合金使用中不可缺少的重要环节。建筑用门窗铝合金的表面处理,在我国已经形成体量极大、工艺完善、装备上乘和标准齐全的强大体系,铝阳极氧化膜、铝阳极氧化电泳涂漆复合膜和有机聚合物喷涂膜(包括喷粉和喷漆)三大技术体系的生产线,集世界各国先进工艺之大成。在相当长一段时间中,似乎有一种错误概念,认为非建筑用铝材(所谓工业用铝材)不需要进行表面处理,因为当时非建筑的“工业铝材”比较简单,一般应用可能没有经过表面处理。然而,近年来的工业实践表明,高铁和汽车的铝装饰件及零部件、机械产品零部件、电子产品的铝合金外壳、铸态铝合金的表面改性产品(提高表面硬度和耐磨耗性)等,都已经成功采用阳极氧化膜的保护,以提高其外观装饰性和延长服役寿命。
从根本上说,表面处理是为了解决或提高铝合金的保护性、装饰性和功能性三大方面问题。众所周知,铝的腐蚀电位较负,电化学活性较强,全面腐蚀比较严重,在与其他金属接触时,由于电偶作用还会加速腐蚀。同时铝又是典型的钝化型金属,除了全面腐蚀以外,由于表面存在氧化膜,局部腐蚀为其主要的腐蚀形态。因此提高防护性是首要的问题,阳极氧化和聚合物涂覆是两种最常用的有效保护手段。装饰性是从美观靓丽的要求出发,着重提高外观品质,如均匀性、光亮度、颜色丰富美观等。为了持久保持装饰效果,必须同时考虑晶莹透明的铝阳极氧化膜或有机化合物膜保护,以增加一道防护措施。功能性的范围很宽,一般指赋予铝材表面在工程方面需要的一系列物理或化学特性,如高硬度,良好的耐磨耗、绝缘性、亲水性、吸热性等。甚至可以利用铝阳极氧化膜的多孔型特征,引入新的特殊功能(如光电性、电磁性、润滑性、抗菌性、催化性等)材料,逐渐形成具有潜在用途的各种各样功能性的铝阳极氧化膜研究领域。1985年在东京召开了一次国际会议,专门讨论过这种功能性铝阳极氧化膜的应用前景,当时关注度很高,30多年来功能性铝阳极氧化膜的应用并未达到当时预期的高度和规模。在实际应用中,防护性、装饰性和功能性三方面性能可能总是互相依赖、彼此补充的,一般不会单独解决一个方面问题,但是保护性总是其基本要求。尽管从实用的角度出发,可能侧重某项功能,但还是需要综合考虑多方面性能和功能,才可能解决实际使用问题。
铝合金的表面技术有:表面机械处理(机械抛光、机械扫纹等);化学处理(化学抛光、化学转化处理、涂覆前化学预处理、化学镀等);电化学处理(电化学抛光、电镀、阳极氧化处理等);物理处理(静电喷涂、金属喷镀、等离子喷镀、离子注入、搪瓷珐琅化及其他物理表面改性技术)等。在实际表面处理工程中一般很少采用单一方法,而是采用一系列串联的工艺过程完成表面改性或获得新的表面性能。
铝阳极氧化是铝合金通用的表面处理技术,使用量和应用面都很广,以下举三个不同领域的阳极氧化工艺过程的实例。这三个工艺过程只是说明其工艺路线、实施步骤和操作参数有所不同,并不表示工艺流程规范一成不变。
实例Ⅰ,建筑铝型材阳极氧化处理及静电喷涂处理流程:

实例Ⅱ,通用工业用铝合金部件(机械部件、电气部件等)阳极氧化处理流程:

实例Ⅲ,装饰用铝合金部件(汽车装饰零部件、照相机零部件等)阳极氧化处理流程:

其中实例Ⅰ表示建筑铝型材门窗的表面处理,目前有四种工艺过程,可以得到三种表面保护膜,即阳极氧化膜、阳极氧化电泳涂漆复合膜以及静电喷涂膜(包括化学转化+静电喷涂或者阳极氧化+静电喷涂)。传统的静电喷涂工艺采用喷涂前的化学转化处理,其中铬酸盐处理工艺最为成熟,膜层性能比较可靠。鉴于六价铬的环境危害性极高,近年开发了无铬化学转化工艺并已经用于生产。为了克服有机聚合物喷涂膜下丝状腐蚀的困扰,正在研发铝阳极氧化作为喷涂前预处理工序,该工序已经纳入各国的标准或规范。我国虽在行业标准和国家标准中将阳极氧化膜作为过渡层,但目前喷涂工业化生产基本上并未采用阳极氧化处理。实例Ⅱ是通用工业的铝合金阳极氧化工艺,视产品要求可以分别采用草酸或硫酸阳极氧化,或硬质阳极氧化(硬质阳极氧化一般不封孔)。实例Ⅲ是装饰用铝合金部件的阳极氧化工艺,在铝阳极氧化之前一般要进行表面机械修整、化学抛光或电化学抛光,以提高铝基材表面均匀性、平整度与光亮度。此外铝合金的化学转化(如铬化),在汽车或飞机的某些部件上,作为最终表面处理措施还在使用。不过化学转化处理大量用于喷涂之前制备中间过渡层,以改进有机聚合物喷涂层的附着性,提高涂层的耐蚀性,降低或消除涂层下丝状腐蚀的危险。在一些特殊场合,如要求表面导电、表面金属质感的情况时,电镀或化学镀也不失为一个好的方法。铝合金部件表面搪瓷珐琅化也有应用,可以提高铝表面外观的装饰效果,改进耐腐蚀与耐候性能。
微弧氧化也叫微等离子体氧化、微等离子体表面陶瓷化或电火花放电沉积等,顾名思义,是在高外加电压下,使原来的非晶态的阳极氧化膜在微弧作用下发生相和结构的转变,生成结晶态的Al2O3,欧美文献常称之为火花阳极氧化或火花沉积。微弧氧化是普通电化学阳极氧化向物理方面的技术延伸,是电化学过程与物理放电过程共同作用的结果。微弧氧化最早在苏联研究开发并得到工业应用,应用范围从飞机、舰船的铝合金部件,到民用的纺机纺杯和电熨斗底板等。微弧氧化膜的特点是低孔隙率(低于4%)、高硬度(高于1000HV)、高耐磨性和高绝缘性,有独特的性能优点和使用优势。然而表面陶瓷化失去了金属质感,在装饰感觉上有些不同,很难满足目前电脑和手机等产品外壳的外观要求。当前微弧氧化的应用并不很广泛,不仅有其技术层面(高外加电压和大电流密度、表面疏松层休整等)和经济层面(生产效率低,火花放电引起能耗很高)等方面的问题,还有用电安全和尖端放电等人身防护的问题,为此除非有特殊需要,通常不会采用微弧氧化工艺。微弧氧化与其他通用技术(包括硬质阳极氧化等)的市场竞争中,既需要完善和提高微弧氧化技术水平和安全措施,还需要对微弧氧化工艺进行有效的技术引导和示范推广工作。为了降低能耗,近年发展了无火化微弧氧化技术,新西兰开发的镁合金的Anomag技术就是一例。通常微弧氧化膜表面有一定厚度的疏松层,使用之前应该除去,这又增加了工艺的复杂性和不可避免的能量损耗。
在物理方法中,包括一些尖端表面技术,如离子注入、激光合金化等尚处在研发阶段。还有一些技术,如离子镀、离子溅射、真空镀及化学气相沉积等,虽然工艺本身比较成熟,但在铝合金方面工业应用不多。本书将不涉及尖端表面技术的内容,而分章节叙述工业应用比较普及和深入的技术,具体内容和工艺细节详见本书有关章节。鉴于环境友好目标的不断增长的需要,传统工艺技术也有不少改进和创新,我国目前工艺革新重点主要不在提升性能和降低成本,主要应该着眼于提高环境效应,本章第1.7.2节“从环境友好出发对铝表面处理工艺创新”,请读者参考阅读。此外,还可以详阅本章参考文献[16]~[21]以及本书第20章的内容。
1.5 铝的阳极氧化技术
铝的表面处理技术中阳极氧化是应用广泛的技术,铝阳极氧化的技术研发、理论研究和工艺开发也是最深入与最全面的。在建筑铝型材门窗的表面处理工艺中,铝阳极氧化应该是技术含量较高、工艺操作较精准的工艺,而且对于铝型材基体品质要求最严格的工艺。铝阳极氧化膜(可以含电泳涂漆膜)是目前建筑用铝合金门窗的一种服役寿命最长、使用效果最好的表面处理工艺。
铝的阳极氧化膜具有一系列优越的物理、化学和工艺特性,可以满足多种多样的功能需求,因此被誉为铝的一种万能的表面保护膜。本书将用五章篇幅分别叙述铝阳极氧化处理技术,再以四章篇幅叙述铝阳极氧化膜的后处理,还有三章与阳极氧化处理相关的前处理过程。
1.5.1 铝阳极氧化膜的特性
铝阳极氧化膜具有很多功能特性,通过微孔可获得强大的功能。概括说来,其功能特性包括物理特性、化学特性、机械特性和装饰特性等。物理特性包含光学的(镜面反射、选择性吸收等)、电学的(导电、绝缘等)、机械的(硬度、耐磨耗、润滑等)、热学的(导热、热放射等)等;化学特性有耐各种介质的腐蚀、抗菌、不燃烧等以及装饰特性的色彩、光亮等。有些特性是铝阳极氧化膜多孔性本质派生改型的结果。以下对于某些特性作简要说明,然后从特性引入应用。
(1)耐腐蚀性。铝阳极氧化膜可以有效保护铝基体不受腐蚀,阳极氧化膜显然比自然形成的氧化膜的厚度更厚、性能更好。铝阳极氧化的工艺与氧化膜的性能直接相关,铝阳极氧化膜的完整性、均匀性、厚度和封孔品质直接影响性能水平和使用寿命。同时铝阳极氧化膜的耐腐蚀性使得铝合金的应用范围明显扩大,使用寿命显著延长。
(2)硬度和耐磨耗性。铝阳极氧化膜的硬度比铝基体高得多,铝基体硬度一般为HV100左右,普通铝阳极氧化膜的硬度约为HV300,而硬质铝阳极氧化膜硬度可以达到HV500左右,微弧氧化膜的硬度在HV800~1000甚至更高一些。耐磨耗性与硬度尽管不是同一性能,但是通常有一定的相关性。
(3)装饰性。铝阳极氧化膜可保持和保护铝表面的金属光泽。铝阳极氧化膜还可以用各种工艺措施进行染色和着色,得到并保持丰富多彩的外观。其中多色化电解着色(日本称之为三次电解),是利用干涉效应着色,可得到色彩比普通电解着色更丰富、耐候性明显优于染色的新的电解着色技术。
(4)有机涂层和其他涂层的附着性。铝阳极氧化膜作为中间过渡层是铝合金表面接受有机聚合物涂层和其他涂层的一种方法,它可以有效地提高表面涂层的附着力和耐蚀性。铝阳极氧化膜是最有效防止丝状腐蚀的有机涂层前处理过渡层,其技术效果优于铬酸盐处理膜。铝阳极氧化膜是在铝合金晶格上共格生长的表面膜,不存在所谓的涂层/金属的“界面”,所以不存在膜下丝状腐蚀的困扰,性能检测标准也无需规定丝状腐蚀检测项目。
(5)电(热)绝缘性。众所周知,铝是一种良导体,而铝阳极氧化膜却是高阻抗的绝缘膜。绝缘击穿电压一般大于30V/μm,特殊制备的高绝缘氧化膜甚至可以达到大约200V/μm。
(6)透明性。铝的阳极氧化膜本身透明度很高,铝的纯度愈高,则透明度愈高。铝合金材料的纯度、合金成分和热处理工艺都影响铝阳极氧化膜的透明性,其中铁和硅含量及其分布尤其值得注意。透明的铝阳极氧化膜容易暴露铝合金材料的表面瑕疵,为此铝阳极氧化工艺对于铝合金基材的品质有更加严格的要求。
(7)功能性。利用铝阳极氧化膜的多孔性,在微孔中沉积各种功能性微粒,可以得到各种功能性材料。正在开发中的功能部件有抗菌功能、电磁功能、催化功能、传感功能和分离功能等部件,都是基于多孔性本质派生的新功能特性。利用多孔性本质赋予新的功能,在20世纪80年代已经引起国际科技界的密切注意,只是目前的实际应用范围明显逊于理论预测。
1.5.2 铝合金的阳极氧化工艺适应性
金属铝的新鲜表面暴露在大气中,立刻会覆盖一层很薄的自然氧化膜,这层膜一旦破损还会很快重新生成,这就是“自修复性”(即自愈性),自愈性由铝的自钝化性本质所决定。这层自然氧化膜的重要特征是,氧化膜的分子体积的化学计量比是铝基体的1.5倍,这意味着自然氧化膜处于压应力状态下,自然氧化膜不仅能够连续覆盖住全部金属铝的表面,而且在一定形变量下也不至于破裂。
在室温普通大气下放置1天,自然氧化膜的极限厚度大约为2~3nm。自然氧化膜的厚度与铝合金成分、环境和温度等诸多因素都有关系。氧化膜的完整性、均匀性及其厚度决定了氧化膜保护性能的好坏程度。化学氧化膜的厚度一般为2.5~5μm,比自然氧化膜的厚度约增加了一千倍,通常具备了一定的保护作用。铝阳极氧化膜的厚度可以更大,其厚度随着工艺及其参数的不同而变化,通常要求在5μm或10μm以上。硬质阳极氧化膜一般为50μm左右,甚至达到100μm以上。表1-11是铝及铝合金各种氧化膜厚度的比较,读者可以按照需要选择相应氧化膜及其生成方法和生成条件。
表1-11 铝和铝合金各种氧化膜的厚度

不同成分的铝合金适合于不同的阳极氧化,比如2×××系铝-铜合金的阳极氧化性能(尤其是光亮阳极氧化)一般并不理想。表1-12是各种铝合金成分的变形铝合金的阳极氧化适应性。其中纯铝是最容易阳极氧化的,而且其阳极氧化膜的透明度最好,可以较好地保护铝合金原表面的高镜面反射率。但是铝材的杂质含量的增加,首先影响铝阳极氧化膜的透明度,也就是影响铝材的表面光亮度(即镜面反射率)。当镁含量超过3%,不仅影响表面的光亮度,而且逐渐影响染色性和耐腐蚀性。从表1-12可以看到铜、镍、硅、锰及其联合添加所产生的影响。铝合金的杂质成分与含量,合金化元素的成分与含量、特别是金属间化合物的第二相析出状态及其分布,都直接影响铝阳极氧化膜的性状,也就是直接影响所谓“阳极氧化工艺适应性”,在第7章将展开论述。
表1-12 变形铝合金的阳极氧化工艺适应性

注:适应性程度分为:极好,很好,好,中,不可。
1.5.3 铝阳极氧化膜的应用
在铝的表面处理技术中,阳极氧化的研究最为深入,应用最广泛,一度被誉为万能的铝表面处理工艺。建筑门窗用铝合金挤压型材的生产体量极大,铝阳极氧化后广泛用于建筑物的门窗、幕墙和卷帘等方面。21世纪初,我国建筑用铝材占铝的总消费接近30%,而建筑铝型材中阳极氧化技术曾占据市场70%以上。近年来,尽管国内外大量实践证明,铝阳极氧化膜(或含电泳涂漆)可能是保证建筑铝型材使用寿命最长的表面处理手段,日本基本上采用阳极氧化/电泳涂漆或沸水封孔的工艺,但是从国内市场分析,静电粉末喷涂占有明显的市场优势,2017年铝阳极氧化膜(含电泳涂漆)的市场占有率估计只在30%。2010年以来,国内市场分析表明,铝合金阳极氧化在非建筑领域,诸如汽车零部件和电子产品装饰件以及诸多功能部件等方面发展极为迅速,已经出现工艺技术水平、辅料品质及装备研发落后于产品性能需求的情况。此外,如果将微弧氧化放在铝阳极氧化的应用方面来讨论,那么微弧氧化应用还是非常有限的,其滞后原因有其技术经济本身的缺点。微弧氧化技术及其应用今后可以得到进一步发展,只不过需要踏踏实实的基础性研究和切实可行的工艺措施方能实现。
众所周知,铝阳极氧化膜有两大类,一类是壁垒型膜,主要用于电解电容器等方面,另一类多孔型膜的使用面非常广阔。就多孔型阳极氧化膜而言,除了建筑和装饰用铝材之外,还可用于PS印刷板、光(热)反射器、汽车零部件、电子产品装饰件,还有机械工程用硬质阳极氧化膜等。另外利用铝阳极氧化膜的可控制孔径和孔隙度的十分有规律的多孔型结构,掺入功能型材料,制成一系列功能性铝阳极氧化膜,在抗菌膜、分离膜、催化膜、传感膜、光电膜、电磁膜等方面都已经得到应用。例如垂直记录高密度磁盘、超微过滤介质、土壤湿度测量等方面,铝阳极氧化膜技术均得到应用。20世纪80年代国外就已经对铝的功能性阳极氧化膜给予极大关注,专门召集过多次国际性学术会议,描绘出极其美好的应用前景,然而后续的工业发展并没有达到当年预计的规模。
1.6 铝的其他表面处理技术
铝的表面处理除了阳极氧化工艺之外,已经工业化的表面处理技术还很多,包括化学转化处理、静电喷涂、电泳涂装、电镀、化学镀和表面搪瓷化等工艺。
1.6.1 铝的化学转化技术
铝的化学转化处理既可以作为喷涂层的中间过渡层(也叫底层),也是一种最终保护性处理措施。长期以来铝合金采用铬酸盐处理,考虑到六价铬严重的环境影响,从降低铬含量角度出发,改用三价铬,使用磷铬化处理或磷化处理逐渐变化升级。近期出现无铬无磷化学转化处理,有望彻底告别铝表面化学转化处理中有毒六价铬的时代。
当然,铝的铬化膜目前还是耐腐蚀性最好和性能最稳定的铝的化学转化膜,工业操作管理方便,因此实际上国内外仍未彻底弃用。铬化膜又称黄铬化膜,磷铬化膜也叫绿铬化膜,它们的膜都有颜色,但耐腐蚀性前者是后者的两倍。近年来由于我国加强了环境治理的力度,建筑铝型材喷涂前处理的六价铬使用量已经明显减少,估计很快就会完全弃用。目前铬酸盐处理的铬化膜,作为最终表面处理手段,国外报道仍在航空和汽车部件某些方面采用,只是需要配套完善的六价铬治理措施。完全无铬的化学转化处理,目前工业上主要用钛和锆与氟的络合物为主成分的无机化学成分,还有以有机物为主成分(如有机硅烷或其他有机物)的。鉴于单一无机物的裸膜的耐腐蚀性比较差,而单一有机成分存在性能时效退化的可能性,目前国内外都趋向研发无机成分与有机成分的复合成分。无铬化学转化技术已经可靠地用在铝板带、啤酒罐和饮料罐等方面,铝型材方面正在大力推广应用中。由于受到喷涂膜下丝状腐蚀的困扰,近年阳极氧化作为喷涂前的预处理手段首先在欧洲引入,并纳入欧洲规范Qualicoat之中。这个变化意义很大,实际上认可了在亚洲已经使用多年的铝阳极氧化膜+有机聚合物膜是建筑用铝合金性能最可靠的保护手段。
有关铝化学转化处理请参阅本书第5章“铝的化学转化处理”,环境保护参阅第20章“铝表面处理生产的环境管理”。
1.6.2 铝的涂装技术
本书第14~17章叙述铝的有机高聚物的涂装工艺,铝的涂装工艺包括电泳涂漆、静电喷粉、静电喷漆和辊涂四大类,读者可以阅读上述四章内容。铝阳极氧化+电泳涂漆技术在1960年代起源于日本,目前在日本、东南亚地区和我国使用较多。由中日两国起草的国际标准ISO-28340:2013《铝复合膜-铝阳极氧化膜与电泳涂漆膜的复合膜总规范》已颁布实施(见本章参考文献[22]),此标准从立项到通过历时近十年。尽管此前已经在欧美地区有使用阳极氧化电泳涂漆复合膜的报道,在西班牙和美国也已经设厂生产电泳漆,但是在欧美地区电泳漆的使用毕竟还不普遍,随着阳极氧化电泳涂漆复合膜国际标准的颁布,预计后续会在欧美等地更好得到推广应用。
阳极电泳涂漆膜属于铝阳极氧化复合膜的一部分,可以进一步提高铝阳极氧化膜的耐候性,尤其在海洋大气和沿海地域或工业污染大气中显示出优势,在技术上可以看作铝阳极氧化膜的有机聚合物封孔,从而明显提高耐腐蚀性能和延长服役寿命。日本在20世纪60年代成功开发复合膜,即在铝阳极氧化膜上阳极电泳聚丙烯酸树脂层,至今仍广泛使用并占有日本铝合金建筑门窗型材近90%的市场。电泳涂装铝阳极氧化膜的特点是,它比单一铝阳极氧化膜的耐候性更优异,在污染大气和海洋大气中优势更加明显。电泳涂漆膜的另一个特点是复杂形状工件的表面有机聚合物涂层的均匀性,特别在难于涂覆的边缘棱角都有满意的涂层,这方面明显优于喷涂处理技术及其他涂层技术。实践证明,阳极氧化复合膜的铝合金门窗的使用寿命最长,笔者现场观察到在海洋性气候地域,有已经成功使用50多年的建筑物铝合金门窗的实例。
静电喷涂在欧洲是建筑铝门窗型材应用最广的表面处理方法,我国建筑铝型材静电粉末喷涂层的市场份额目前已经超过铝阳极氧化膜和复合膜。2010年我国静电喷涂的市场份额至少占有60%,长三角以北地区静电喷涂的产销量为80%的企业比比皆是。静电喷涂以静电聚酯粉末喷涂和静电氟碳液相喷涂为主要内容。粉末喷涂层尽管其使用服役寿命不及铝阳极氧化复合膜,但是具有涂层色彩鲜艳丰富、涂层与材质关系较弱、喷涂技术操作方便、生态环境好等优点,受到生产方和用户方的欢迎,其应用范围逐渐扩大,市场份额不断提升。家用装饰目前主要使用静电粉末喷涂环氧树脂系,建筑门窗采用静电粉末喷涂聚酯树脂系,以及静电液相喷涂氟碳树脂系。
静电粉末喷涂的喷枪有高压静电枪与摩擦静电枪两种,后者消除尖端放电现象,喷涂层的均匀平滑度较好。氟碳树脂涂层是耐腐蚀性和耐候性最好的表面喷涂层,但涂覆成本很高,常用于使用寿命需要特别长的建筑物上。近年来欧洲已经开发出使用寿命接近氟碳涂料的粉末涂料,即高耐用性聚酯/无TGIC粉末,在欧洲标准中称为Ⅱ类(typeⅡ)粉末。此类涂层经过国际通用Florida现场挂片,10年试验结果与氟碳涂层相当,15年试验仅光泽下降大于氟碳涂层。由于Ⅱ类粉末价格比氟碳涂料低,则构成了对氟碳涂层的严重挑战。
尽管静电粉末喷涂工艺本身的环境效应好,但是目前的铬酸盐预处理工艺存在严重的环境污染,已经引起各国的广泛关注。无铬预处理工艺已经工业化多年,虽然涂层品质目前可能还不如铬酸盐,但是取代铬酸盐(Cr6+)的方向是不可动摇的。鉴于铝合金喷涂膜下丝状腐蚀的频繁发生,而无铬前处理比六价铬前处理更加严重,欧洲对此进行了广泛研究,并且已经将阳极氧化处理纳入欧洲的涂层规范(Qualicoat),建议将阳极氧化作为喷涂层的前处理工艺。静电液相喷涂还存在有毒的挥发性有机溶剂的大气污染问题,即VOCs的污染。为此研发水性涂料替代溶剂型,并且达到附着力和耐蚀性的指标也是不可动摇的技术研发目标,但是水性涂料中也必须关注可能存在的非挥发性的毒性有机化合物的存在。
1.6.3 铝的电镀和化学镀
电镀或化学镀是比较成熟的传统表面处理工艺,也是金属或非金属表面获得金属镀层的主要方法。电镀既可以得到保护层,装饰层,有时也用于赋予某些特殊的功能。也就是说电镀层不仅保护铝不被腐蚀,又有光亮的金属外观,同时还可以保持良好的导电和导热性等。铝及铝合金上直接电镀相当困难,因为铝对氧的亲和力很大,表面总是存在自然氧化膜,使电镀层对铝的附着力很差。又由于铝的膨胀系数大于大多数金属,因此电镀层很容易脱落。因此如果没有特殊的镀前表面预处理,电镀过程会十分困难。这种情形在镁合金上同样存在,因此镀前预处理是铝或镁这类活性金属上电镀的技术关键。
铝制品与铝部件电镀前的表面预处理包括两个大的方面,一是常规方法,二是专用方法。前者指机械处理(喷砂、抛光等),化学处理(酸浸洗、碱浸洗)等。后者专门对铝表面进行特殊处理,在铝表面与电镀层之间形成一层中间过渡层,既保证与铝基体附着好,又与电镀层保持良好结合。事实上只要镀前预处理正确得当,随后的电镀或化学镀就可以按常规工艺进行,原则上不发生困难。当然由于中间过渡层较薄,要考虑电镀溶液pH值不宜太低,以免电镀溶液腐蚀过渡层而引起电镀层的附着不良。有关铝及铝合金电镀的具体工艺请见本书第18章。
1.6.4 铝的珐琅和搪瓷涂层技术
珐琅和搪瓷化是将无机氧化物的混合物熔融成不同熔点玻璃态物质的涂料进行涂覆。它们的基本成分是硼砂、石英、萤石、长石以及金属硝酸盐和碳酸盐、重金属氧化物等。就铝合金而言,珐琅成分应调整到使其熔点在550℃以下,同时要考虑膨胀系数与铝合金相匹配。珐琅和搪瓷以粉末状态存在,选择好的铝合金经过表面预处理,可以用喷涂、浸涂、刷涂等方法涂覆,欧美有许多设备进行铝合金上静电喷涂珐琅层。铝合金珐琅涂层的使用历史很长,1929年已出现建筑用铸铝板的珐琅涂层,但高耐用有机聚合物涂层的优势,制约了铝建材的珐琅涂层的工业发展。目前主要还是用在器具、浴室和厨房的配件、冰箱内衬、照明灯具等方面。由于珐琅涂层有其外观特点和性能特性,英、美等国也在建筑业上使用,例如招牌、路标、装饰、屋顶、外墙等。美国一个建材生产商报道,到1968年已经使用了大约50万平方米。我国搪瓷钢铁制品和日用品比较多,但搪瓷铝制品和搪瓷建筑用铝部件相当少。
1.7 我国铝表面处理的工艺现状和创新前景
铝表面处理是铝材延长使用寿命、扩大应用范围、提高市场价值必不可缺的重要工艺,是铝合金加工的延伸工序,其重要程度随市场发展更显突出。我国铝型材表面处理工业是在20世纪80年代从日本和意大利引进建筑铝型材加工生产线开始的,现在已经形成具有中国特色的工艺和装备的技术路线,产量约占全世界60%以上。我国铝型材表面处理的工艺路线、装备水平、产量质量、人才培养、标准制定和膜层品质等方面,当之无愧已经位于世界大国与强国的地位。其中铝表面处理工序与国际先进水平的接轨程度,远高于同行业的熔铸、模具和挤压工艺。当前我国铝型材表面处理的工艺创新的重点,应该放在补足环境效应短板,淘汰落后工艺,坚持和发扬新兴技术,全面提升产品品质,创造高端效益的目标上。就建筑铝型材表面处理而言,我国的阳极氧化、阳极氧化+电泳涂漆、无铬前处理+静电喷涂等工艺的总格局不会改变。但是必须按照以环境保护为前提,审视现行工艺路线,检查添加剂成分,全面提升产品质量,减少地域和企业之间的差距,以全面达到国际先进技术水平。我国非建筑业装饰与保护用铝合金的表面处理技术,如汽车内外装饰件和电子产品外装等(我国习惯称“小氧化”)的发展相对较晚,规模较小,当前虽已形成一定的生产能力,但应该强化和深化工艺研发,严格生产工艺管理制度,提升各类产品质量,深化品质监督检测,全面加快添加剂研发的国产化进程。
近年来,剖析铝型材表面处理领域的技术革新项目,已经开始围绕环境效益开发,例如涂层前的无铬转化处理技术、铝阳极氧化膜的中温无镍封孔技术、铝阳极氧化薄膜作为涂层前处理的工艺措施、消光电泳漆(消除光污染)的引入,以及一些新涂料如氟碳粉末和水性氟碳涂料等,都反映出铝表面处理技术的发展与进步已经与环境保护紧密相关,而且基本上是与国际先进水平同步发展的。由于过去我国对于环境保护的意识与措施相对薄弱而形成环境短板,当前我国加强环境保护、加快环境治理是十分必要和非常正确的。
1.7.1 我国当前铝材表面处理的环境效应的评价
20世纪80年代是我国铝建筑型材表面处理的发展初期,当时强调工艺成本与产品效益,相对忽视了环境友好效应,导致了当前环境保护措施和环境管理的短板。目前的工艺改革与创新均在环境保护的基础上开发,这是弥补环境保护短板和工艺技术进步的明显标志。但是,在不断强化环境保护的措施时,如果无端提高“污染物排放”的限值指标,不一定是工艺开发创新的科学之举。在环境、工艺、品质、效益之间应该找到最佳平衡点,其中在一个时期某一方面强化是必要的,但是强调过度恐有失衡之虞。
我国目前有《污水综合排放标准》(GB 8978)和《大气污染物综合排放标准》(GB 16297)可供执行。但是这些标准发布距今已超过20年,排放限值明显偏松。为此,广东省铝型材表面处理的地方标准要求执行更为严格的其他行业的排放标准,如《电镀水污染物排放标准》(DB 44/1597)《表面涂装(汽车制造业)VOC排放标准》(DB 44/816)及《锅炉大气污染物排放标准》(GB 13271)等。尽管如此,目前仍面临着污染物排放限值的行业针对性和技术操作性方面的困扰。2017年环境保护部已经下达制定《铝型材行业污染物排放标准》,确定由环境保护部华南环境科学研究所为项目主持单位,中国有色金属加工工业协会、清华大学、广州华科环保工程公司和广州环境保护工程职业学院为协作单位完成标准的制定。
近十年来,笔者已经多次在有关技术会议提出环境问题(见本章参考文献[19]、[20]),早在2010年广东有色金属协会年会上,发表《从环境效应的新视角对于我国铝型材表面处理技术的再思考》的报告,首次从环境保护的角度,回顾和审视目前我国铝型材表面处理工艺路线和管理规程,包括添加剂的成分和使用,提出了一些工艺设想和技术建议。又在2013广东会议发表《铝合金阳极氧化工艺之环境问题》,进一步深化分析我国铝型材阳极氧化生产工艺的环境问题,明确提出不仅需要行之有效的环境保护的治理措施,更应该检查探讨表面处理的污染源头,从工艺路线的内因和源头入手,彻底提升生态效应。直至2016年,在中国有色金属加工协会年会上发表《环境友好对铝表面处理技术创新的挑战》,提出环境友好要从表面处理工艺源头出发,要与工艺革新和产品质量提升挂钩,全面综合考虑。2018年在一系列反复推敲环境、生产协调发展思路的基础上,按照中国有色金属加工协会的要求,在2018年年会发表《环境效应是我国铝材表面处理工艺创新的基础,兼谈环境/工艺/品质/效率的最佳化》,再次全面深入剖析以环境友好为基础和前提的工艺改革与技术创新的思路。
很多国家目前已经有了比较完善的控制污染物排放的标准或法规,这是铝表面处理的工艺发展进步的基础。美国、日本及欧洲在1950年代至1970年代,逐步建立并完善各项有关环境的标准或法规。铝表面处理污染物排放限值,各国的标准执行的情况不尽相同。日本按照统一的国家标准执行,如《水污染防治法》和《大气污染防治法》等,各行各业一视同仁都必须统一执行。美国标准的分类比较细,铝表面处理的水排放污染物限值可以按照《金属表面精整业(Metal Finishing)污染源类别》(法规号40 CFR PART 433)执行。欧盟各国标准的分类也比较细,污染物排放的限值大体与美国、日本相当。
表1-13列出了我国三家企业执行的水排放污染物9个检验项目,并对比我国执行的排放限值与美国、日本、意大利标准的排放规定。所列出的检验项目,广东标准和太湖流域规定执行的水污染排放物限值均比国外严格,但是检测项目明显偏少而且不够细致,意大利和日本的水污染排放物限值的检验项目较多(未在表中全部列出),意大利有31项,日本的有害物质检验项目28项,还有健康项目15项。
表1-13 我国三家企业执行的水排放污染物限值与美国、日本、意大利排放标准的比较

注:1.意大利标准中有水和污水之别,加括号者为污水对应标准;
2.日本水污染物限值未列镍,在大气污染物中规定限值为0.1mg/L;
3.美国数据未作细致调查,主要取其镍和铬的数据。
从表1-13的水污染排放物限值的比较以及国内外企业环境效应的调研,可以简单地对比分析并总结如下。
①在可以相互比较的相同的水污染物排放项目的限值上,我国在广东或太湖流域企业执行的标准实际比日本或意大利更为严格。关键在于我国企业的生产与环保实施是否得到有效监管,小型企业的污染排放和治理措施是否到位。
②日本水质标准有两个方面,即水污染物排放标准和水质环境标准(健康项目),后者基本上比前者提高一个数量级甚至更多。意大利排放污水和普通水质的限值也不相同。我国可以考虑是否采用这种规定办法,以获得在水污染排放物限值与水质环境标准之间的一个缓冲过渡区域。
③我国和外国都没有明确规定单锡盐或镍-锡混合盐添加剂中的有机还原剂和络合剂等的限值(日本可能考虑到锡盐电解着色而规定了硫酸联胺排放限值),无法进行有效监管。在锡盐电解着色中使用的有机还原剂大多是有害的,如萘酚、苯酚和硫酸联胺等,即便苯酚也有邻苯二酚、间苯二酚和对苯二酚之别,它们毒性也有高低之分。虽然COD及BOD控制可能在一定程度上监控到还原性有机化合物,但是并不全面。
④日本对水污染排放物的镍没有作出限值规定,日本专家多次询问我国情况,这是我们没有想到的。日本规定了水污染排放物的羰基镍不得超过0.001mg/L,气相镍化合物限值为0.1mg/L。目前我国对于污染水中镍离子的控制十分严格,规定为0.1mg/L,是否科学还有待检验。
⑤由于我国目前镍的排放限值很严格,添加剂生产企业突出宣传单锡盐是最环保的电解着色系统,兴起转向单锡盐电解着色的趋势,回避亚锡盐着色中添加剂的危害。事实上不注意监管硫酸亚锡电解着色中有机添加剂的危害是很危险的。结合上述第③点和第④点,我国应该加强锡盐着色添加剂等各类添加剂的环境监管。
⑥六价铬主要来自喷涂前的铬酸盐预处理等,六价铬的严重危害已经很明确。总铬量中除六价铬以外还有三价铬,由于有些国家目前还允许使用三价铬的化合物,为此总铬与六价铬的限值不可能相同。我国目前不允许使用所有含铬化合物(不论三价还是六价)的规定是明确的,但是目前无铬预处理的涂层的实际可靠性还不够。
⑦我国目前对于镍的排放限制已经提到铬的高度,而铝阳极氧化工艺中立式自动化电解着色生产线和高品质常温或中温封孔均使用镍盐,此两项技术分别来自日本和意大利,并且不仅在中国还在许多国家使用,绝对禁用镍盐可能会影响采用先进工艺和影响产品品质。
⑧镍、铜、锰、锌等金属元素可能来自某些电解着色体系或铝合金的成分,尽管国际上目前没有一概称之为有害重金属,也应该通过国内外的系统调查研究,科学地、实事求是地规定这些重金属水污染排放物的限值。
⑨水中磷和氮的含量与化学抛光或电化学抛光及其他工艺添加剂有关,需要按照技术规范严格管控。磷可以回收进行资源化再利用,日本对水污染排放物磷的规定明确为有机磷,我国应该关注添加剂中含磷和氮的浓度,以便得到必要及时的处置。
⑩氟及其化合物目前主要来自冷封孔及化学预处理添加剂等,其浓度尽管明显低于氟化氢铵前处理,但是必须明确监管。原则上氟的有效治理相当简单,并不存在技术障碍,因此似乎不必禁止使用含氟化合物,严格监管含氟化合物的治理是必需之举。
⑪有机聚合物涂层工艺中的挥发性有机化合物VOCs,目前集中关注有机化合物为溶剂的喷漆,例如氟碳漆喷涂等,这显然是必要的。但是还应该关注喷粉固化等工序中产生的VOCs,全面检查表面处理各生产环节中产生的VOCs,配套相应的治理措施。
⑫以往固体废弃物通常在一个沉淀槽中处理,没有严格区分无害的以铝化合物为主成分的铝渣与有害的固体废弃物,由此造成严重的固废污染,也没有充分变废为宝。发达国家都是分工序单独形成污水治理回路,值得我们参考学习。
⑬我国铝型材表面处理的地方标准的限值尽管严格,但是检测项目偏少,限值是否科学有据还值得调查探讨。建议环境管理部门、协会学会、学术团体等部门不仅关注污染排放的限值,更应该指导治理路线、方法和措施,促进行业向高水平健康发展。
我国已经形成世界上体量最庞大、技术最齐全的建筑铝型材表面处理生产线,既有欧美惯用的静电喷粉和静电喷漆生产线,又有亚洲的阳极氧化和电泳涂漆生产线。为此,工艺污染源头相对复杂。在某种意义上,铝表面处理工艺又是铝型材企业水排放污染物的主要来源。目前国外明确规定的有害重金属元素是铬、镉、汞、铅四种,镉和汞一般不会出现在铝材表面处理工艺中。而铅曾经作为处理槽内衬或电极使用,但已经弃用多年。在四种有害重金属中,只有六价铬是有机涂层前预处理的主要污染物。尽管镍、锰、铜、硒在国外尚未被认定为有害重金属元素,但是不能认为完全无害任其排放,实际上各国都有排放控制措施。在水排放污染物中,日本未明确规定镍的限值,美国规定为3.98mg/L,意大利规定为4mg/L(河水为2mg/L),我国目前规定均为0.1mg/L(见表1-13)。
日本在2006年,由官方组织调查日本和欧美广大地域的镍离子的生态和环境危害,并通过一定的动物试验(如小白鼠实验),撰写了报告《镍的详细(环境)风险评估》(文献[30])。报告认为,大气中镍化合物吸入人肺有发炎或致癌的风险。日本标准规定大气污染物的镍化合物限值为0.1mg/L,但是没有明确规定水污染排放物的限值。表1-13列出了铝表面处理主要水污染物的工艺源头,提醒我们不仅可以切断污染物的源头,而且可以在工艺与环境之间寻找最佳平衡,更有利于引导工艺创新,在保证环境效益的前提下提高工艺水平和铝阳极氧化膜品质。
1.7.2 从环境友好出发对铝表面处理工艺创新
欧盟在2006年全面实施RoHS(有害物质管制)指令,这是针对电子电器业的有害物质处理或最终废弃物不得对环境产生有害影响而出台的指令,其他行业具有相同或类似有害物的也必须执行。2007年又出台实施REACH(化学品登记、评价、认可及管制)规则,规定欧盟的生产商或进出口商,有义务将有害性/危险性评价信息向ECHA(欧洲化学物质厅)登记申报,方可进入市场。RoHS指令和REACH规则的核心不仅涉及污染排放物的限值,还关注产品的流向和由此引起污染的可能性,为此产品的服役寿命及回收原则也成为关注的目标,这样的环境管控思路更加科学、有效。RoHS指令规定的对象有害物质为铅(Pb)、汞(Hg)、镉(Cd)、六价铬(Cr6+)、聚溴化联二苯类(PBBs)、聚溴化联苯醚类(PBDEs)。但是欧洲一些国家还没有明确规定三价铬和镍,意大利和德国专家称,由于吸入硫酸镍或氧化镍等气相化合物对健康有害,皮肤接触镍有引起过敏的记载,欧洲正在考查镍及其化合物的水污染排放的限值问题。
日本执行的PRTR(污染物排放和转移登记制度)中有关铝表面处理的主要对象物质有二甲苯、铬与三价铬化合物、六价铬、二氯乙烷、水溶性铜盐、三乙烯胺、三氯乙烯、甲苯、三乙胺、镍、镍化合物、氟化氢及其化合物、硼及其化合物、锰及其化合物等,此处属排放及转移登记,没有水污染排放物限值的明确规定。日本在铝阳极氧化工厂中,作为一般的排水基准的监控管理项目有:pH、SS(悬浮物)、COD、BOD、铅、磷、氟、硼、硝酸性氮及亚硝酸性氮等。请读者注意PRTR中规定了镍化合物为表面处理工艺的主要对象物质,而在日本水污染物排放限值中依然没有列入镍及其化合物。
鉴于上述分析,我国铝材表面处理的工艺创新以环境保护为前提是必要的。彻底治理铝表面处理污染的关键,是从铝表面处理的工艺源头(尤其是被忽视的添加剂)着手,改变甚至限时关停确有证据的污染源头。但是希望既杜绝或减少污染排放物,使之达到污染物排放标准,又促进铝表面处理技术的创新发展。根据这个思路,以下提出当前铝材表面处理工艺技术改革创新的一些意见,谨供读者参考。
①必须坚持已经实施或已有共识的以环境友好为宗旨而关停的不良工艺的改革措施。我国越来越重视表面处理工艺路线的环境效应,应该继续坚持环境友好的工艺改革措施。以下已经实施的环境治理项目必须坚持:a.废除涂层前处理中六价铬的铬酸盐化学转化处理工艺,目前已经在行业中推广无铬涂前预处理工艺,没有推广无铬的地区或企业必须完善六价铬的环境治理措施。b.全面废除阳极氧化前为去除挤压条纹的氟化氢铵浸渍工艺,杜绝高浓度氟离子造成环境的大范围氟的污染。c.因Ni-Sn混合盐电解着色的污水难于实施无害化处理,而单镍盐或单锡盐的污水处理比较方便可行,所以,继续限制和逐步淘汰目前广泛采用的Ni-Sn混合盐电解着色工艺,使环境污染的治理方法简单可靠。d.清理和弃用铝型材三酸化学抛光处理,杜绝氮和磷等污染源头,而且三酸化学抛光还会引起二氧化氮、硝酸等气体的严重大气污染。在需要光亮表面的情况下,推广机械抛光加无硝酸化学光亮化处理是一种可行的方法,也可以推广以钼酸盐或钨酸盐替代硝酸的新型抛光技术。
②建议调查研究单锡盐添加剂成分的毒性程度,选择使用无毒或低毒的有机还原剂及络合剂。30年前笔者首次研发硫酸亚锡电解着色配方时,已经注意到防止亚锡氧化的有机物添加剂具有不同程度的毒性,当时鉴于性能与成本等原因,更由于并不细致了解添加各类有机化合物的环境效应,始终留下一点遗憾。30年来我国研发生产电解着色添加剂队伍已经壮大,现在已经有条件进行国内外系统调查,研究硫酸亚锡电解着色的有机添加物的毒性,提高环境友好程度。建议Sn盐(目前包括还在使用的Ni-Sn混合盐)电解着色的添加剂生产部门,研究开发硫酸亚锡着色溶液的新成分,努力寻找无毒或低毒有机还原剂(如抗坏血酸等)和络合剂(如磺基水杨酸),替代目前的有毒化学品,从根本上改变添加剂成分来降低或消除对于环境的污染。相应的标准或规范应考虑调研并规范一系列有机还原剂(如苯酚或萘酚)的品种和浓度,引导添加剂生产企业研发低毒高效锡盐电解着色添加剂,步入国际先进水平。水污染排放物中的金属离子容易检控,而有机化合物难于分辨限定,因此工艺源头把关只能由添加剂生产企业负责,相关部门和铝型材企业强力监督。
③镍和镍化合物的“环境污染”是目前国内特别关心的问题,在我国由于源于日本的自动化立式生产线的电解着色工艺和源自欧洲的冷封孔工艺都使用镍盐,也都是镍离子排放物的主要源头,如果强制停用镍盐可能存在技术和市场的困扰。如上所述,日本标准规定大气中镍盐限值为0.1mg/L,水污染物排放未规定镍的限值数据。但是关于饮用水(非排放污水!)日本似有限值0.01mg/L的规定。而意大利的限值为自然水<2mg/L,污水<4mg/L,美国的污水的限值为<3.98mg/L,与意大利基本相同。笔者最近从日本菊池先生(日本铝制品协会原专务,长期从事标准制定,2017年退休)、意大利Dr. Strazzi(原Cisart和Itatecno公司)处获得相关技术资料。其中日本在2006年发表的调研和试验报告(文献[30]),全面评估镍的环境和生态风险,总结欧美对于镍化合物危害性的评价,还系统研究和实验验证水和大气中镍化合物的危害风险程度,并推定各种化合物的暴露浓度,报告很有参考价值。报告结论为,人体吸入镍化合物有炎症和癌变之危险,通过白鼠试验的镍的LOAEC(最小风险剂量)为1mg/m3,影响肺与鼻子发炎的剂量为0.027mg/m3。而通过给白鼠反复口服NiSO4(H2O)6导出的对生殖毒性和死胎的NOAEL(无可见有害作用水平)是2.2mg/(kg·d)。日本的水排放污染物不做规定与这份报告数据有关系。生活实践经验告知我们,不锈钢仍然是食品、饮料行业和人们长期接触使用的“可靠”的金属材料,不锈钢含有金属镍并未发现不妥之处。菊池先生认为既然大量研究并没有证实水中镍化合物的危害,无需规定明确的限值。笔者对此并无细致研究,此处转述有关技术信息供同行参考。综上所述,一概禁用含镍工艺似乎并不恰当,应进一步分析论证。
④铝材表面处理中碱腐蚀造成大量固体铝渣,其主要成分为铝的化合物,体量虽大但基本无害。所以必须改变过去在同一沉淀池中形成“污染铝渣”的错误治理措施,应该将铝渣与有害的固体废弃物从工艺路线上严格分别处置,并加工为无害副产品的原料,既有利于环境保护又可以降低成本增加效益。日本的环境治理工艺就是分工序单独形成环保处理回路,碱腐蚀形成环境处理环路,阳极氧化、电解着色、封孔等都严格分开处理回路,既有利于环境保护,又可以直接回收化工原材料,降低化学品消耗和生产成本。目前我国广泛使用的长寿命碱浸蚀工艺源自欧洲,虽然解决了槽液结块影响连续生产的严重问题,却无法避免产生含水量高达60%的大量铝渣。好在基本上属于无害的固体铝渣,其成分与含量以碱浸蚀产物铝酸钠和偏铝酸钠[可按Al(OH)3计]以及碱洗添加剂的葡萄糖酸钠和硫代硫酸钠为主,可以直接设厂回收。碱腐蚀的铝渣与其他有害固体废弃物分开,不可混装废弃,这是非常重要的原则。至于从根本上改变长寿命添加剂工艺,可规划采用“碱回收系统”以消除回收如此大量固体铝渣的困境。碱回收体系并非新创造工艺,在国外尤其日本已经使用多年,因此技术方面没有任何障碍,只需要投资设备并配合严格管理即可,我国企业已有成功使用的实例。采用没有添加剂的碱回收系统可以直接回收固体Al(OH)3待用并循环利用NaOH,这是既环保又经济的科学措施。近年来国内企业有些新的工艺尝试,应该加以总结完善,使之实现工业化。某些工艺可以考虑变碱浸蚀为酸浸蚀路线,同样可以达到减少固体铝渣之目的,但必须关注酸浸蚀的环境污染。
⑤鼓励热封孔及研发无Ni冷(中温)封孔,彻底消除Ni和F的困扰。在有特殊品质(如高温或拉应力的耐开裂性或铝卷材连续阳极氧化封孔)要求时,提倡使用沸水封孔或高温蒸汽封孔,杜绝可能的污染源头,同时提高铝阳极氧化膜的韧性和抗开裂性。鉴于热-水合封孔工艺的能耗大、水质要求很高,为此在常规工艺下鼓励研发无镍常温封孔技术,这也是当前一项非常重要并值得推广的方向。目前欧洲推出“高性能无Ni冷封孔”是基于Zr/F络合盐体系的冷封孔工艺,据称该工艺的产品在碱性环境中的封孔品质(特别适合于pH为12.5及13.5的碱性溶液中)已经超过热封孔和含Ni冷封孔。据报道这种无Ni封孔(如德国的SurTec 350,意大利的Super seal 2S)的性能,更适合于汽车方面的应用,可以通过耐碱性溶液检测的考验。
⑥涂层前无铬预处理工艺已经在我国推广使用,可能还需要在服役现场检查其使用效果,尤其是发生涂层下丝状腐蚀的程度。我国目前已经有几个体系的无铬涂层前处理方法,无机化合物有锆(钛)/氟体系,但是存在化学转化处理的前处理或蚀刻要求高、转化膜无色难于判别、裸膜耐盐雾腐蚀性差等缺点。而有机化合物(有机硅烷或其他如单宁酸等有机酸)可以得到接近于铬化膜的裸膜耐腐蚀水平,而且已研发成功有色膜便于观察,但是又担心发生有机化合物时效性能减退问题。因此目前国内外基本上都趋于研发无机成分与有机成分的复合型的预处理开发方向。值得注意的是,市场上无铬处理工艺即使已经通过实验室的快速检定,得到满意的结果也还必须继续通过室外耐候性和现场服役的考验,方能达到真正可靠、放心使用的程度。此外,尽管欧洲相关规范已经将铝阳极氧化纳入无铬预处理工艺范围,以期杜绝涂层下丝状腐蚀的困扰,但是从经济和技术的可行性角度考量,目前我们宜密切关注欧洲的工艺动向,静观其变而无需紧跟为妥。有条件的单位可以择时探索铝阳极氧化+静电喷涂的工艺连续性、技术可靠性以及降低生产成本和提升产品性能的措施。
⑦各种表面处理工艺过程中减少或避免挥发性有机化合物(VOCs)的大气污染,工艺途径不仅要管控液相喷涂的VOCs溶剂的污染,还必须注意喷粉或电泳漆固化过程中的挥发性有机化合物的污染。喷粉是环保型的表面处理工艺,由于涂层前铝表面钝化处理涉及六价铬的污染,还由于有机物单体固化聚合过程中可能形成VOCs,所以粉末涂料的品质尤为重要。涂料中挥发性成分非成膜物质的增加,暴露出固化炉的污染日趋严重,由此粉末涂层的孔隙率增加、致密度降低,引起有机聚合物涂层保护性能下降,从而影响喷粉铝型材的使用寿命。为此规范粉末涂料品质就是一项有现实意义的而且刻不容缓的工作。为了避免喷漆溶剂的VOCs的污染,水性液相涂料应运而生,但是水性涂料中也可能存在某些有机化合物,这些有机物对于VOCs的“贡献”值得探讨和管控。
⑧日本推出的电泳涂漆膜综合了阳极氧化膜与有机聚合物膜的优点,既有铝阳极氧化膜的高耐磨性和硬度,也兼具有机聚合物膜对于污染大气和海洋大气的耐腐蚀性,因此这是阳极氧化/阳极电泳涂漆的复合膜。我国GB/T 5237.3—2017规定的也是复合膜,并不是单纯的电泳涂漆膜。铝合金电泳涂漆膜可以直接在铝合金基体上生成,但综合性能包括抗丝状腐蚀性、硬度和耐磨耗性都不能与复合膜相比拟,其检验项目应该按照GB/T 5237.4—2017的性能指标进行。
⑨我国非建筑用铝合金零部件的铝阳极氧化比铝型材开发得晚,其性能要求也随着应用的多样化而比建筑用更复杂丰富,目前工艺技术路线和操作参数尚有不少可商榷、革新之处。例如为了通过pH13.5碱性溶液(12.7g/L NaOH+2g/L Na3PO4+0.33g/L NaCl)中浸渍10min后工件表面不发生明显变化,铝型材通常采用的封孔方法无法满足检验要求。目前采用三次封孔的办法,仔细分析所谓的三次封孔,实际上并不能够产生互相补充或叠加封孔效果。第3次封孔可能覆盖一层水玻璃型表面膜,确实可以提高耐碱性溶液腐蚀的性能,但是可能又损害通用的封孔质量,为此汽车工业铝零部件阳极氧化膜采用三次封孔过程大有改进之余地。对于各种各样的“小氧化”铝阳极氧化工艺,需要制定针对性更强的阳极氧化+电解着色+封孔的工艺路线以及设定合理的操作参数,满足诸如汽车部件、电子产品外装、铝卷材连续阳极氧化等特殊工艺的各种使用要求和不同性能指标。在我国已经建立如此强大的铝型材表面处理的技术基础上,实际上不是遥不可及的事情,期待我国各系统或各部门之间的技术交流更通畅。
⑩以环境保护为前提,并不是单纯以降低污染排放物的限值,甚至无端禁用国内外正在使用的工艺为目的,必须在环境效应/工艺开发/品质提升/效益增加的关系中寻找最佳平衡点。环境保护作为工艺开发的出发点是以广大人民群众的健康为前提,显然是不可动摇的基本原则,也是对过去形成的环境短板的有力补偿,但不应该无端牺牲产品品质和生产效益去单纯考虑污染物排放的“达标”问题,例如镍盐电解着色是最适于自动化立式铝阳极氧化大型生产线的着色方法,目前我国从日本引进的生产线就是一例。由于槽液稳定,工艺先进,着色均匀,尤其适合于自动化连续生产,并且可以配套完善的环境治理措施,镍盐电解着色目前是日本占优势的铝阳极氧化膜的电解着色工艺。即使必须考虑限制镍离子的排放限值,也应该强化和监管环境治理措施,以达到我国目前规定的排放标准而不只是禁用镍盐。
参考文献
[1]朱祖芳等.有色金属的耐蚀性及其应用.北京:化学工业出版社,1995.
[2]王祝堂,田荣璋主编.铝合金及其加工手册.第2版.长沙:中南工业大学出版社,2000.
[3]Tjϕstheim N J. Instructions for Use: Selecting Aluminium Alloys. Aluminium Extrusion, 1999, 4 (1): 26.
[4]Brace W. The Technology of Anodizing Aluminium. 3rd. Modena: Interall Srl, 2000.
[5]Sato T, Kaminaga K. Theory of Anodized Aluminium 100 Q and A. Tokyo: Kallos Publishing Co. Ltd, 1997.
[6]ァルミ表面处理ノ―ト.第5版.东京:日本轻金属制品协会,1999.
[7]朱祖芳.80年代我国铝材氧化及着色技术的进展.轻合金加工技术,1993,21(4):27.
[8]朱祖芳.我国90年代铝型材表面处理技术的回顾.材料保护,2000,33(11):1.
[9]朱祖芳.铝型材表面处理技术发展之过去和未来十年.电镀与精饰,2002,21(2):44.
[10]朱祖芳.铝合金化学转化处理技术进展及工业应用.材料保护,2003,36(3):1.
[11]Osmond M F. Architectural Powder Coatings for 21st Century. Aluminium Finishing, 1998, (2): 19.
[12]Trolho J. Chromate, Phosphochromate and Chrome-free conversion coatings for Aluminium. Motichiari (Brescia) -Italy: 4th world Aluminium congress Aluminium, 2000.
[13]Ling Hao, Rachel Cheng B. Sealing Processes of Anodic Coatings-Past, Present, and Future. Metal Finishing, 2000, 98 (12): 8.
[14]朱祖芳.铝阳极氧化的应用.电镀与精饰,1999,18(1):40.
[15]川合慧著.铝阳极氧化膜电解着色及功能膜应用.朱祖芳等译.北京:冶金工业出版社,2005.
[16]日本輕金属製品協会.ァルミニウム加工方法と使い方の基礎知識.東京:日本輕金属制品協会,2004.
[17]日本輕金属制品協会.ァルミ表面處理ノート.第7版.東京:日本輕金属製品協会,2011.
[18]朱祖芳.中国建筑铝型材的表面处理工艺及发展方向.东京:2004年8月24日国际标准讨论会报告,2004.
[19]朱祖芳.从环境效应的新视角对于我国铝型材表面处理技术的再思考.佛山:广东有色金属加工学会国际技术交流会,2010.
[20]朱祖芳.环境友好对铝表面处理技术创新的挑战和促进.内蒙古:中国铝加工产业创新交流大会,2016.
[21]日本表面技術协会.ァルミニウム表面技術百问百答.東京:KALLOS出版株式会社,2015.
[22]ISO 28340—2013 Combined Coatings on Aluminium-General Specification for Combined Coatings of Electrophoretic Organic Coatings and Anodic Oxidation Coatings on Aluminium.
[23]Sheasby P. G, Pinner R. The Surface Treatment and Finishing of Aluminium and its Alloys. 6th edition. Finishing Publications LTD UK and ASM International USA, 2001.
[24]GB/T 1173—2013铸造铝合金.
[25]GB/T 15115—2009压铸铝合金.
[26]李学朝编著.铝合金材料组织与金相图谱.北京:冶金工业出版社,2010.
[27]朱祖芳.我国铝材表面处理技术现状及发展前景.中国金属通报(2017增刊),2017,9:13.
[28]Simon Meirsschaut. Update of European Legislation Relative to Surface Treatment of Aluminium and Its Impact on the Finishing Industry, Al 2000 congress: 2015.
[29]アルミニウム表面处理の理论と实务,第4版.东京:日本轻金属制品协会,2007.
[30]镍的详细(环境)风险评估(非公开出版物).东京:日本产业综合研究所化学物质风险评估管理中心,2006.