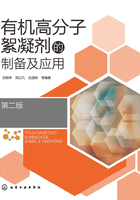
4.3 聚合型絮凝剂的制备
聚合型絮凝剂的制备方法归纳起来,主要有水溶液聚合、反相悬浮聚合和乳液聚合,其中乳液聚合又包括反相乳液聚合和反相微乳液聚合。
4.3.1 聚二甲基二烯丙基氯化铵
二甲基二烯丙基氯化铵(DMDAAC)的均聚物和其他单体的共聚物用于水处理方面作为絮凝剂,能获得比常用的絮凝剂更好的处理效果。因为聚丙烯酰胺等阴离子絮凝剂存在残留单体的毒性问题,使其应用受到限制,PDMDAAC(聚二甲基二烯丙基氯化铵)作为一类新型的阳离子型有机高分子絮凝剂,其分子中含有季铵基,正电性强,不易受pH值等因素的影响,而且使用时溶解时间短,0.5h就可以完全溶解。此外还具有电荷密度高、水溶性好、高效无毒的特点,是我国絮凝剂的更新换代产品,是最具有代表性的季铵盐类絮凝剂。国外从20世纪50年代初期就已经开始研究,并于60年代后期确定它的五元环结构。我国科研工作者亦在这方面做了大量的研究,如我国山东大学的高宝玉等在20世纪90年代开始对这类絮凝剂从合成方法,结构的IR、H NMR表征,到除浊性能以及脱色性能等各个方面进行了系统的研究[5-7]。
聚二甲基二烯丙基氯化铵(PDMDAAC)为白色易吸水粉末,溶于水、甲醇和冰醋酸,不溶于其他溶剂。在室温下PDMDAAC水溶液在pH=0.5~14范围内稳定[8]。PDMDAAC的化学结构式有两种——五元环结构和六元环结构,示意式如下所示:

聚二甲基二烯丙基氯化铵的制备主要是利用二甲基二烯丙基氯化铵通过自由基聚合反应而成,其反应式如下:

聚二甲基二烯丙基氯化铵的制备方法有水溶液聚合、非水相溶液聚合、沉淀聚合、乳液聚合和悬浮聚合等,其中水溶液聚合法工艺简单,成本较低,产品可直接应用,不必回收溶剂,因此应用最为广泛。张跃军等[9]以一步法工业单体二甲基二烯丙基氯化铵(DMDAAC)为原料,以过硫酸铵(APS)为引发剂,采用一次性加入引发剂、梯度升温、分步引发水溶液聚合反应的方法进行了优化,此制备方法工业化程度高。
4.3.1.1 水溶液聚合
水溶液聚合法制备聚二甲基二烯丙基氯化铵,可采用化学引发、紫外线引发、γ射线引发、荧光引发等引发方式。化学引发聚合采用的引发剂有无机过氧类,如过硫酸钾、过硫酸铵等;氧化还原引发体系,如过硫酸盐-脂肪胺、过硫酸盐-亚硫酸钠等;此外还有水溶性偶氮类引发剂等。本节主要介绍二甲基二烯丙基氯化铵(DMDAAC)单体和聚合物的制备方法。
方法1:双液法合成DMDAAC是由两步反应完成的,其反应式为:

中间产品可以分离出来,并能完全除去氯化钠杂质,最终得到高纯度的固体阳离子单体。采用有机溶剂双液相反应,可以有效抑制烯丙基氯的挥发和自聚,并能方便地将中间产物分离,避免了蒸馏分离所带来的耗时、挥发损失、高温自聚和残留物损失等不利因素。鉴于有机溶剂能够反复套用,该方法不会带来环境污染,并可将过量的烯丙基氯回收利用,达到或接近无气、液排放水平。第一步反应得到的水相溶液在分离固体氯化钠后,部分液体与作干燥剂使用的氢氯化钠可以配成原料溶液返回利用,另一部分经多次积累后制成DMDAAC水溶液产品,使水相液体得到全部利用。
单体制备步骤:在装有搅拌器、温度计的三口烧瓶中,加入150mL 33%的二甲胺水溶液(1.0mol)及100mL有机溶剂,剧烈搅拌呈乳白色,在3h内滴加82mL烯丙基氯(1.0mol)和84g 50%的氢氧化钠水溶液(1.05mol),缓缓升温并维持体系回流3h。冷却后,分出上层有机相,水相含有氯化钠固体,用少量有机溶剂萃取两次,合并有机相,加入10g氢氧化钠干燥,过滤,收集滤液备用。取上述1/3有机相滤液,在室温下加入51mL(0.62mol)烯丙基氯于40℃搅拌反应5h,冷却后滤出DMDAAC固体,经丙酮洗涤后减压干燥、称重,滤液经气相色谱法测定烯丙基氯含量后返回套用。在上述水相滤液(滤除氯化钠后)中加入100mL套用有机相溶液,于45℃搅拌反应5h,分出有机相,水相在60~70℃减压蒸出20mL液体,得DMDAAC水溶液产品。
聚合步骤:将6g DMDAAC固体、14g丙烯酰胺溶于62g蒸馏水中,加入一定量的引发剂,在室温下用紫外灯引发聚合,至体系温度升至最高点(约1.5h,47℃)后,冷却,得弹性胶状聚合物[10]。
方法2:DMDAAC的制备采用一步法,即用二甲胺和烯丙基氯在强碱性条件下一次反应完成。但该法所得单体溶液中含有大量副产物如氯化钠、烯醇、烯醛、叔胺盐及未反应完的烯丙基氯等,虽经减压蒸馏但不能完全去除或完全不能去除,这将严重影响后续聚合步骤和作为给水絮凝剂的卫生性能。
采用一步法制备二甲基二烯丙基氯化铵单体,即在强碱性条件下由烯丙基氯和二甲胺反应先生成二甲基烯丙基叔胺,将该叔胺分离出来并再次加入烯丙基氯,于丙酮介质中结晶析出季铵盐晶体。
实验原理:烯丙基氯和二甲胺发生亲核取代反应,先生成叔胺,再进一步反应得季铵盐。步骤:

利用上述单体在一定引发剂下聚合。作为絮凝剂,其分子量越大越好,分子链越长越好。可以选用硫酸亚铁-过氧化氢引发系统,加入EDTA的二钠盐,在氮气保护并抽真空下聚合,以水为溶剂。
由于原料烯丙基氯的市场价格比较高,因而产品PDMDAAC的市场售价比较高,但其投放量远比HPAM要小[11,12]。
方法3:在微波辐射下分别采用一步法、二步结晶法和相转移催化法合成了二甲基二烯丙基氯化铵,其中微波辐射-相转移催化效果最好。
微波辐射一步法制备DMDAAC单体时,其方法是全部二甲胺、氢氧化钠溶液、50%~80%总用量的氯丙烯,在功率75~1000W微波辐射下15~40min内滴完。加入所余氯丙烯,75~1000W微波辐射反应1~2h。减压蒸馏,温度50~120℃,真空度(0.5~0.8)×106Pa,用时20~40min,80℃下过滤得产品。
微波辐射二步法,其方法是全部二甲胺、固体氢氧化钠、50%~80%总用量的氯丙烯,功率75~1000W,微波辐射5~10min,叔胺的转化率以指示剂百里酚酞显示。油水分离,用相当于总用量的40%~120%的固体氢氧化钠干燥脱水,脱水后氢氧化钠回用于第一步反应。第二步将上述干燥后的叔胺与所余的烯丙基氯加入50%~200%的丙酮中,在常温下静置12~72h,得无色针状晶体即季铵盐单体。分离后减压蒸馏精制,温度50~120℃,真空度(0.5~0.8)×106Pa,用时5~10min。
微波辐射-相转移催化法,其方法是全部二甲胺、固体氢氧化钠、50%~80%总用量的氯丙烯,功率75~1000W,微波辐射5~10min,叔胺的转化率以指示剂百里酚酞显示。用相当于总用量的40%~120%的固体氢氧化钠干燥脱水,脱水后氢氧化钠回用于第一步反应。第二步加入所余氯丙烯,同时加入20%~100%的水为相转移催化剂升温回流1~3h。减压蒸馏,温度50~120℃,真空度(0.5~0.8)×106Pa,用时10~20min。
采用微波辐射和相转移催化的聚合方法可提高反应速率,增加产率,降低成本。
微波辐射一步法,用冰水浴控制温度,反应速率为常规反应的一半。其中微波对叔胺化作用明显,季铵化作用一般。微波辐射和相转移催化联用二步法,叔胺化反应5~10min完成,速度快,减少水解、消除等副反应。油水分离的目的是脱水除氯化钠,用相当于总用量的40%~120%的固体氢氧化钠干燥脱水,脱水后氢氧化钠回用于第一步反应,低成本下彻底脱盐效果好。第二步于丙酮中结晶,微波辐射因需1h以上,不实用,所以未采用,但明显可加速转化率50%之前的反应速率[13]。
方法4:以碱金属碳酸盐、络合剂摩尔比(1~20):1的混合溶液作为净化剂,以0.1%~0.2%的净化剂水溶液对氯丙烯进行一次或多次洗涤;在氯丙烯溶液中滴加二甲胺溶液和碱金属氢氧化物溶液,氯丙烯:二甲胺:碱金属氢氧化物的摩尔比为2.1:1:1,并加入催化剂,催化剂为碱金属氟化物和高效络合剂摩尔比为(50:1)~(1:20)的混合溶液;控制温度在40~70℃,反应时间2~4h,减压抽出水及低沸点物,得到DMDAAC;在DMDAAC溶液中加入引发剂,调pH值为6左右,常温下自动聚合。该方法原料洗净效果好,反应易于控制,可得到高分子的聚合物[14]。
方法5:一种用于高纯二甲基二烯丙基氯化铵的合成方法[15]。该工艺采用低温下半干碱法自热催化快速合成叔胺;然后油水分离,干燥脱水、脱盐;最后油相结晶或发生相转移催化反应,减压蒸馏得产品。具体方法为加入全部二甲胺、部分氢氧化钠溶液、适量氯丙烯,在冰水浴或盐水浴(<5℃)下反应数分钟,分批加入固体氢氧化钠控温自热催化快速完成叔胺反应。然后油水分离,油相用固体氢氧化钠干燥。加入所余氯丙烯升温回流1~3h,减压蒸馏精制10~30min即可。单体制备后在一定条件下加入引发剂进行聚合。
4.3.1.2 反相乳液聚合
反相乳液聚合制备聚二甲基二烯丙基氯化铵的具体工艺为:在反应器中加入规定量的油相、乳化剂、螯合剂以及其他添加剂并开启搅拌。同时在一定质量浓度的离子交换精制的二甲基二烯丙基氯化铵单体水溶液和分散相中通入氮气驱氧20~30min后,在单体中加入引发剂,摇匀后,在快速搅拌下加入油相中进行聚合,待出现放热高峰后于30~70℃范围内保温3.0~6.0h,冷却至室温加入终止剂后出料。在聚合过程中,定期取样测定单体的转化率和PDMDAAC乳液的分子量。
赵明等[16]以液体石蜡为连续相、丙烯酰胺和二甲基二烯丙基氯化铵水溶液为分散相、N,N-亚甲基双丙烯酰胺为交联剂、过硫酸铵为引发剂、司盘80和OP 10为复合乳化剂,制备了丙烯酰胺(AM)/二甲基二烯丙基氯化铵(DMDAAC)阳离子共聚物;考察了引发剂含量、单体AM与DMDAAC的摩尔配比、复合乳化剂司盘80与OP 10的质量配比及含量、聚合温度、聚合体系pH值等对AM/DMDAAC阳离子共聚物性能的影响。较佳的聚合条件为:过硫酸铵占单体总质量的1.0%,n(AM):n(DMDAAC)=1.6,m(司盘80):m(OP 10)=96:4(司盘80和OP 10复合乳化剂的亲水亲油平衡值约为4.7),司盘80和OP 10占油相质量的6%,聚合温度40℃,聚合体系pH值约为5.0。在此聚合条件下,制得的AM/DMDAAC阳离子共聚物的黏度较大,稳定性较好。
Morgan和Boothe[17]利用乳液聚合制备聚二甲基二烯丙基氯化铵的具体工艺为:往反应器中加入321.5g苯、138.5g 72.2%DMDAAC水溶液和40g 20%辛烷基-苯氧基乙氧基-2-乙醇硫酸钠水溶液。上述混合物在170~180r/min的转速下搅拌,并升温至(50±1)℃,通氮驱氧1.0h后,加入1.4mL质量浓度为3.51g/L的硫酸亚铁铵溶液,然后再加入0.336mL 75%过氧酰基叔戊酸丁酯醇溶液,并在50℃下通氮搅拌反应20h。通过蒸发分离出苯溶剂,就可得到玻璃状聚二甲基二烯丙基氯化铵固体产品。
4.3.2 聚甲基丙烯酰氧乙基三甲基氯化铵
聚甲基丙烯酰氧乙基三甲基氯化铵是一种具有特殊功能的水溶性阳离子高分子聚合物,广泛用于石油开采、造纸、水处理等众多领域。聚甲基丙烯酰氧乙基三甲基氯化铵的制备采用水溶液聚合,质量分数为40%聚甲基丙烯酰氧乙基三甲基氯化铵溶液制备的具体工艺为[1]:在反应器中160份质量分数为75%的甲基丙烯酰氧乙基三甲基氯化铵单体溶液中加140份去离子水和0.12份偶氮引发剂——2,2'-偶氮双[2-(2-咪唑并基)丙烷]二盐酸盐,通氮气驱氧,并在室温下搅拌反应1.0h,将反应体系温度升至44℃,连续加热搅拌21h,冷却至室温,出料。聚甲基丙烯酰氧乙基三甲基氯化铵聚合物溶液的黏度约1.4mPa·s。
刘福胜[18]以丙烯酰胺(AM)和甲基丙烯酰氧乙基三甲基氯化铵(DMC)为原料,在金属卤化物灯照射和引发剂作用下,通过水溶液聚合法合成阳离子型聚丙烯酰胺P(AM-DMC),考察了单体质量分数、引发温度、引发剂质量分数、溶液pH值和单体配比等对聚合物特性黏数和溶解性的影响。在单体质量分数30%、阳离子度10%~30%、引发剂质量分数0.0048%、pH值为4、引发温度15℃条件下,产物的特性黏数可达10dL/g以上,溶解时间低于40min。
4.3.3 聚甲基丙烯酸二甲氨基乙酯
聚甲基丙烯酸-N,N-二甲氨基乙酯(PDMAEMA)结构中既含有亲水性的氨基、羰基,也含有疏水性的烷基,是一种两亲性功能高分子。PDMAEMA的结构式为[19]:

聚甲基丙烯酰氧乙基三甲基氯化铵的制备可采用水溶液聚合和悬浮聚合两种方式。
4.3.3.1 悬浮聚合[19]
单体制备:甲基丙烯酸二甲氨基乙酯单体一般由甲基丙烯酸甲酯(易挥发液体)与2-二甲氨基乙醇,在有锂、氧化锂、乙酰丙酮化锂或Bu2Sn(OOCMe)2存在的情况下,通过酯交换反应制得。
聚合方法:将甲基丙烯酸二甲氨基乙酯单体加入由无离子水200份、分散剂羟基异丙氧基纤维素0.2份、引发剂2,2'-偶氮双-2,4-二甲基-4-甲氧基戊腈0.8份和偶氮二异丁腈0.2份组成的混合物中,在50℃和搅拌作用下,使单体30%得以聚合,然后,再加入无离子水16份和硫酸钠5份,搅拌(250r/min)10min,最后,在50℃下继续搅拌(150r/min)聚合反应3h,由此可得到颗粒状的聚甲基丙烯酸二甲氨基乙酯,产率为94.3%。
4.3.3.2 水溶液聚合
胡晖和范晓东[20]利用紫外线引发甲基丙烯酸二甲氨基乙酯进行溶液聚合制备PDMAEMA。具体工艺为:称取适量安息香乙醚溶于无水乙醇-水混合溶剂中,加入DMAEMA单体,用浓盐酸调节(或不调节)溶液的pH值,通氮气至少20min后,密封于玻璃容器中,在紫外灯下引发聚合。
他们研究了引发剂安息香乙醚(BE)用量、单体浓度、光引发时间等因素对聚合速率、产率与分子量的影响,并确定了对DMAEMA进行光引发自由基聚合的最佳工艺条件为:DMAEMA单体的质量浓度为0.5g/mL,用HCl调节溶液pH值为1.5~2.0,BE的用量为1%,紫外线引发时间为30min。
4.3.4 丙烯酰胺/二甲基二烯丙基氯化铵共聚物
丙烯酰胺/二甲基二烯丙基氯化铵共聚物属于阳离子型絮凝剂,是一种带有阳离子基团的线型高聚物,它的大分子链上所带的正电荷密度高,具有水溶性好、絮凝能力强、用量少、不污染环境等优点,已被广泛用于废水处理。
丙烯酰胺/二甲基二烯丙基氯化铵共聚物是由丙烯酰胺和二甲基二烯丙基氯化铵通过自由基聚合成的共聚物,反应式如下[8]:

丙烯酰胺/二甲基二烯丙基氯化铵共聚物可通过水溶液聚合、反相乳液聚合两种方法来制取,在共聚过程中,应注意两种单体在反应过程中的活性差异,避免因两种单体在长链上分布不均引起的组分差异;另外,也要防止少量的二烯丙基二甲基氯化铵(DADMAC)单体因侧基双链引发支化产生交联聚合物,导致共聚物水溶性下降。
4.3.4.1 水溶液聚合
司晓慧等[21]在室温下将不同种乳化剂按照一定配比分别溶于有机溶剂配成油相,溶于水配成水相。将两相混合,高速搅拌乳化后,制成了分子量较高且速溶的粉状共聚物。步骤:将一定量的油相加入装有搅拌棒、温度计、导气管的150mL四口烧瓶中,置于恒温水浴中,调至适宜温度,开启搅拌器。①一次法,是将单体水溶液一次性加入四口烧瓶中,通N2 20min,加入引发剂(KPS和Na2S2O3),继续搅拌并持续通入N2 30min后停止通入。②滴入法,先将水相和引发剂加入分液漏斗中,通N2驱氧20min后,在N2的保护下,将水相缓慢滴入烧瓶中,滴加完毕后继续通氮20min。
毕可臻等[22]采用非极性溶剂作为连续相,借助乳化剂把聚煤油作为分散剂,过硫酸钾作为引发剂,在油水体积比为3:7时,采用逐步聚合的方法得到了单体质量分数为45%、特性黏数为8.0dL/g(用丙酮和无水乙醇洗涤产物除去水分和未反应单体后测量)、溶解迅速且絮凝效果好的20%阳离子度的产品。此方法采用价廉的单体原料、引发剂和易于工业化应用的工艺使得制备效率大大提高。
4.3.4.2 反相乳液聚合
反相乳液聚合是用非极性溶剂为连续相,聚合单体溶于水,然后借助乳化剂分散于油相中,形成“油包水”(W/O)型的乳液而进行聚合。它为水溶性单体提供了一个具有高聚合速率和高分子量产物的聚合方法。采用反相乳液聚合法可以制备丙烯酰胺/二甲基二烯丙基氯化铵共聚物乳液和固体两种产品。
赵明[23]以丙烯酰胺(AM)为单体合成了聚丙烯酰胺(PAM),研究了溶剂、乳化剂种类及用量、单体浓度、交联剂和通氮等因素对聚合产物黏度与稳定性的影响,确定了最佳合成工艺条件,即:当单体AM含量为40%,油/水质量比接近1.0,交联剂的用量为单体质量的2.5%,引发剂(过硫酸铵)为单体含量的0.9%,使用司盘80/OP 10为复合乳化剂时,产物黏度达到0.84Pa·s。采用反相乳液聚合技术,以有机溶剂液体石蜡为介质,在乳化剂、交联剂等的存在下,一定温度范围内反应3~4h,可制得P(AM/DMDAAC)共聚物反相乳液;确定最佳工艺条件:OP 10的含量占复合乳化剂总质量的4%,乳化剂的含量占油相总质量的6%,单体AM的含量为40%,油/水质量比接近0.9,DMDAAC/AM的摩尔配比为1.6,引发剂过硫酸铵为单体含量的1.0%,pH值为5,聚合温度控制在40℃,HLB=5.05。由于改进了合成工艺,所得P(AM/DMDAAC)共聚物反相乳液黏度大、稳定性能高,可望在制备阳离子高分子絮凝剂以及造纸等领域得到更为广泛的应用。
李琪等[24]以丙烯酰氧乙基三甲基氯化铵(DAC)和丙烯酰胺(AM)为原料,通过反相乳液聚合技术,合成阳离子高分子聚合物乳液。该聚合体系以煤油为分散介质,以司盘80和OP 10为乳化剂,以过硫酸钠和亚硫酸钠为引发剂。
丙烯酰胺和功能性阳离子单体的反相乳液共聚合体系中合成乳液稳定性最好、固含量及分子量较高的最佳反应条件为:单体总质量分数为40%,单体摩尔比为2:3;油相为5号白油,乳化剂占油相质量分数的12%;引发剂为氧化-还原引发剂或高效水溶性引发剂;油水体积比为1:1.2。
4.3.5 丙烯酰胺/(2-甲基丙烯酰氧乙基)三甲基氯化铵共聚物
(2-甲基丙烯酰氧乙基)三甲基氯化铵(DMMC)是一种重要的水溶性阳离子单体。具有阳离子功能基团的(2-甲基丙烯酰氧乙基)三甲基氯化铵与丙烯酰胺共聚,可以赋予阳离子聚丙烯酰胺许多独特的性质,生成的线型阳离子型水溶性共聚物,可广泛应用于污水处理、脱色工艺、石油开采、纺织印染等领域[25]。丙烯酰胺/(2-甲基丙烯酰氧乙基)三甲基氯化铵共聚物的制备方法以水溶液聚合和反相微乳液聚合为主。
4.3.5.1 水溶液聚合法
刘月涛等[26]在聚乙二醇20000(PEG)水溶液中,以(2-甲基丙烯酰氧乙基)三甲基氯化铵(DMMC)和丙烯酰胺(AM)为单体原料,聚(2-甲基丙烯酰氧乙基)三甲基氯化铵(PDMC)为稳定剂,制备了稳定型阳离子聚丙烯酰胺(CPAM)双水相体系。重点探讨了阳离子单体DMMC浓度、分散介质PEG浓度和稳定剂PDMC用量对体系的黏度及共聚物分子量的影响,并利用激光粒度仪测定了共聚物颗粒大小及其粒度分布。结果表明,CPAM双水相聚合体系能避免分散聚合黏度剧增的过程,反应始终平稳进行。制备稳定CPAM双水相体系的适宜条件是:w(DMMC)为8%~15%(单体)、w(PEG)为15%~25%、w(PDMC)为0.5%~1.0%。制备方法为:在装有冷凝管、温度计、氮气导入管和搅拌装置的四口烧瓶中加入一定量的单体、分散剂、稳定剂和去离子水,在室温下搅拌,使物料溶解并混合均匀,通氮除氧30min,升温至反应温度后加入一定量的引发剂V-50,恒温搅拌反应8~10h,反应液由无色透明逐渐变为灰色,最终形成乳白色、均匀平滑的CPAM双水相体系,产品具有良好的流动性和稳定性。
4.3.5.2 反相微乳液聚合法
王姗姗等[27]以白油为连续相、司盘80为乳化剂,通过反相乳液聚合法制备了聚丙烯酰胺,确定了反相乳液体系的制备方法:先将乳化剂溶解在油相,搅拌的同时将单体溶液以滴液的方式加入。结果表明,最佳合成条件为:单体质量分数22.5%(对水相),乳化剂质量分数2%(对油相),油水比为1:2。合成步骤:在装有搅拌器、滴液漏斗、通气管的250mL三口烧瓶中,加入定量白油、乳化剂;开动搅拌,水浴加热至设定温度,使乳化剂完全溶于白油中,将单体及其他助剂溶于水,在高速搅拌下将单体溶液逐滴加入白油中,使其充分乳化后通氮除氧30min,加入引发剂,反应一段时间后结束反应;用丙酮沉淀、抽滤、真空干燥得产品。
4.3.6 丙烯酰胺/甲基丙烯酸二甲氨基乙酯共聚物
丙烯酰胺/甲基丙烯酸二甲氨基乙酯共聚物的制备方法有水溶液聚合和乳液聚合等,但溶液聚合所得产品有效成分含量低,易于降解,不便于运输和贮存。此外,为了提高共聚物的水溶性,甲基丙烯酸二甲氨基乙酯单体常以甲基氯化季铵盐形式参加反应。丙烯酰胺/甲基丙烯酸二甲氨基乙酯共聚物的结构式为:

4.3.6.1 水溶液聚合
杭春涛等[28]以过硫酸铵/亚硫酸钠为引发体系,利用水溶液聚合法制备丙烯酰胺(AM)与丙烯酰氧乙基三甲基氯化铵(DAC)的共聚物P(AM-DAC)。制备方法:准确称取单体AM、DAC,搅拌均匀,用氢氧化钠调节pH值至8~9;再加入适量EDTA、抗交联剂,待溶解后倒入四口烧瓶中,水浴恒温,通氮气保护;30min后,用滴液漏斗一次性滴加过硫酸铵;再过30min,开始缓慢分批滴加亚硫酸钠,n(亚硫酸钠):n(过硫酸铵)=1:1;恒温聚合6~8h。将得到的透明胶状液体用甲醇沉淀,过滤,丙酮洗涤,于50℃真空干燥得白色粗产品;然后,用V(乙二醇):V(冰醋酸)=3:2的混合液抽提12h,除去均聚物,得P(AM-DAC)共聚物固体,所得聚合物在50℃下真空干燥24h至恒重。
4.3.6.2 乳液聚合
徐东平[29]以丙烯酰胺、甲基丙烯酸二甲氨基乙酯、氯甲烷盐和聚醚分散剂为原料,以过硫酸铵/亚硫酸氢钠为引发体系,采用乳液聚合法制备丙烯酰胺/甲基丙烯酸二甲氨基乙酯共聚物。制备方法:在反应瓶内加入一定量的蒸馏水、分散剂以及丙烯酰胺和甲基丙烯酸二甲氨基乙酯单体,在通氮条件下搅拌,加热升温到60℃左右时,先加一定量的硫酸铵和亚硫酸氢钠,此时内温会自行升至80℃左右,保持此温度反应5h,再补加一定量的过硫酸铵与亚硫酸氢钠,继续反应1h,冷却出料即得丙烯酰胺/甲基丙烯酸二甲氨基乙酯共聚物乳液。其中,单体质量分数为30%~40%,丙烯酰胺与甲基丙烯酸二甲氨基乙酯单体的质量比为4:3,分散剂与单体总质量的比值为(5:100)~(7:100),引发剂浓度控制在6×10-4mol/L,初始反应温度在65℃左右,保温反应温度在80℃左右。
4.3.7 丙烯酰胺/丙烯酸乙酯基三甲基氯化铵共聚物
丙烯酰胺/丙烯酸乙酯基三甲基氯化铵共聚物的制备采用反相乳液聚合法,共聚物的结构式为:

冯大春等[30]以环己烷为连续相、十八烷基磷酸单酯为分散剂、无水亚硫酸钠和VA-044为引发剂,以丙烯酰胺(AM)和功能性阳离子型共聚单体丙烯酸乙酯基三甲基氯化铵(AQ)为单体,采用反相悬浮聚合法,合成丙烯酰胺/丙烯酸乙酯基三甲基氯化铵共聚物。方法步骤:在带有搅拌器、回流冷凝管、滴液漏斗及氮气导入管的四口烧瓶中加入定量的环己烷、十八烷基磷酸单酯,通入氮气逐出瓶中氧气,升温至规定温度使分散剂充分溶解。同时将一定计量的丙烯酰胺(AM)、阳离子单体AQ(液体)、引发剂在烧杯中溶解,将混合液转入滴液漏斗中,在规定的时间内将混合单体匀速滴入四口烧瓶中,保持在60℃下反应,滴毕继续反应1.5h,降至室温,过滤分离、洗涤干燥后即得白色小颗粒状聚合物。其中,AM与AQ的摩尔比为1:1,分散剂用量2.5%(相对于单体总质量),油水体积比为3:1,搅拌速率350r/min,滴加时间1h。在上述条件下,可制得平均粒径为1mm,品质高的AM/AQ阳离子共聚物。
4.3.8 吡啶季铵盐型阳离子聚丙烯酰胺
吡啶季铵盐型阳离子聚丙烯酰胺具有优良的絮凝、缓蚀、杀菌功能,是一种新型的多功能水处理剂[31]。合成思路:先将4-乙烯基吡啶(4-VP)与丙烯酰胺(AM)进行共聚合,然后使用季铵化试剂,使吡啶环正离子化,这样制得的共聚物不仅实现了聚丙烯酰胺的阳离子化,而且又将氮杂环季铵盐引入了高分子链之中。
丙烯酰胺是亲水单体,4-乙烯基吡啶是憎水单体,其共聚物是双亲聚合物。由于双亲聚合物的聚合单体极性差别很大,两者不能互溶,因此4-乙烯基吡啶难以用一般自由基聚合方法合成。迄今为止,为克服这一问题,人们提出了几种可能的共聚合方法:
①采用水溶性单体与油溶性单体的共溶剂进行共聚;
②油溶性单体溶解在胶束中分散在连续的水介质中,即胶束聚合法;
③油溶性单体悬浮在水溶液中。
4.3.8.1 4-乙烯基吡啶/丙烯酰胺共聚物的制备
(1)溶液聚合法[31]
在装有搅拌器、温度计、回流冷凝管的四口反应烧瓶中,依次加入30份丙烯酰胺、15份4-乙烯基吡啶、5份N,N-二甲基甲酰胺(或丙酮)和50份蒸馏水,通入N2保护,匀速搅拌一定时间后,缓慢将温度升到45℃,加入0.015份引发剂K2S2O8的水溶液,并开始计量。反应6h后,冷却出料,将黏稠液体倒入大量水中,并加入适量CaCl2溶液,即可沉淀出4-乙烯基吡啶/丙烯酰胺共聚物。产物用蒸馏水洗涤数次后,用氯仿浸泡24h,最后将产物真空干燥至恒重,置于干燥器中备用。
(2)胶束共聚合法[32]
在装有去离子水、温度计、搅拌器、冷凝器的四口烧瓶中,放入0.41mol/L AM,水浴加热,升温到50℃,高纯氮气保护,加8.4×10-2mol/L十二烷基苯磺酸钠和0.21mol/L 4-VP,保持恒定的温度,搅拌约50min,滴加2.72×10-3mol/L引发剂后,反应5h。
4.3.8.2 吡啶季铵盐型阳离子聚丙烯酰胺的制备[33]
称取一定量的4-乙烯基吡啶/丙烯酰胺共聚物,溶解于甲醇或甲醇与乙二醇的混合溶剂中(视共聚物的组成情况而采用不同的溶剂),在搅拌下缓慢加入5倍于共聚物中吡啶环物质的量的硫酸二甲酯,以保证使共聚物中的吡啶环全部被季铵化,于室温下反应约11h,用沉淀剂四氢呋喃沉淀出产物,并多次用四氢呋喃洗涤,将产品于室温下真空干燥24h,最后置于干燥器中保存备用。
4.3.9 聚-N-二甲氨基甲基丙烯酰胺乳液
聚-N-二甲氨基甲基丙烯酰胺乳液的制备主要利用二甲氨基甲基丙烯酰胺单体通过自由基聚合而成,因此制备工艺分为两个步骤:一是单体的制备;二是反相乳液聚合。聚-N-二甲氨基甲基丙烯酰胺乳液主要是通过自由基聚合反应而成,具体反应式如下:
单体制备:

聚合:

聚-N-二甲氨基甲基丙烯酰胺乳液的制备方法为[34]:
(1)单体的制备
于装有温度计、电磁搅拌器和pH电极的三口烧瓶内,加入1份(以质量计,下同)甲醛含量为96%的多聚甲醛和3.71份40%的二甲胺水溶液,控制温度低于45℃反应2h,然后加稀盐酸使反应得到的醛胺pH值降至2。
注意:加酸过程须在冰浴中进行,以保持反应混合液温度不高于20℃。
于上述酸化后的反应物中加入事先酸化、pH值等于2的48%丙烯酰胺水溶液4.72份,升温并控制在65℃反应2h,由此即可得到N-二甲氨基甲基丙烯酰胺单体含量为85%(摩尔分数)的产品,备用。
(2)反相乳液聚合
于聚合釜内加入质量分数为36%的单体水溶液298份(pH=3)、无离子水56份、Isopar M 140份和油酸异丙醇酰胺11份,组成油包水乳化液。升温至30℃,充氮1h,然后加入常用的氧化还原催化剂,反应3h后,再加热至50℃反应1h,由此即可得到聚-N-二甲氨基甲基丙烯酰胺油包水乳液。
聚合反应所用的引发剂可选用氢醌、叔丁基焦儿茶酚、吩噻嗪或硫酸铜,引发剂的加量为丙烯酰胺用量的0.001%~0.1%(质量分数)。反应中所加的Isopar M是闪点为76.7℃(170℉)的异链烷烃混合物。
4.3.10 聚-N-二甲氨基丙基甲基丙烯酰胺[19,35]
由于该产品多为季铵盐,故本方法着重阐述N-二甲氨基丙基甲基丙烯酰胺季铵化聚合物的制备过程和条件。
(1)单体制备
在装有搅拌器、蒸馏塔、滴液漏斗和温度计的2L烧瓶内,加入688.8g甲基丙烯酸、817.6g N,N-二甲基-1,3-丙二胺和8g N,N-二苯基对苯二胺,充入氮气,在220℃温度下反应1~5h,即可制得N-二甲氨基丙基甲基丙烯酰胺黄色液体,备用。
(2)N-二甲氨基丙基甲基丙烯酰胺季铵盐的制备[35]
在装有170g N-二甲氨基丙基甲基丙烯酰胺的1.6L烧瓶中,加入乙酸60g和水176g,升温至50℃,在1h内加环氧乙烷44g,保持此温度反应30min,即可得到有以下结构的季铵乙酸盐:

(3)聚合[35]
将以上制得的甲基丙烯酰胺丙基羟乙基二甲基乙酸铵水溶液50g加去离子水50g稀释,然后在30℃下充氮1h,再加0.4g 2,2'-偶氮双(2-甲基-乙基腈)作引发剂,于65~70℃下聚合反应3h,即可得到N-二甲氨基丙基甲基丙烯酰胺季铵化聚合物。
4.3.11 聚乙烯胺
聚乙烯胺产品有两种:细粉状和无色或淡黄色黏稠液体,其中淡黄色黏稠液体有氨臭味。粉状聚乙烯胺溶于水、稀酸、醇和乙酸,不溶于醚。其盐酸盐易溶于水,但不溶于极性有机溶剂如甲醇、乙醇等。与其他强碱性物质一致,聚乙烯胺及其水溶液应避免与大气中的二氧化碳接触,最好制成聚合物盐酸盐以便于保存。液体商品一般为20%~50%的水溶液。5%水溶液的pH值为8~11。在碱性条件下,贮存稳定性良好,但在有酸存在下会凝胶化。聚合度较低,一般为100左右。
本节主要介绍三种制备聚乙烯胺的方法:a.由乙烯乙酸胺的合成、聚合和水解几步完成;b.聚丙烯酰胺的Hofmann降解重排反应;c.聚(N-酰基)乙烯胺的水解。
4.3.11.1 由乙烯乙酸胺的合成、聚合和水解几步完成[36]
(1)乙烯乙酰胺的合成
将工业乙酰胺(无色透明针状晶体,溶于水、乙醇)462g加入12.45g 6mol/L硫酸中,随之加168mL乙醛,搅拌并加热至70℃,反应9min,再加热至95℃,反应液自发结晶,升温至106℃,制得亚乙基-双乙酰胺。此后加入60g碳酸钙和30g软玻璃粉作催化剂,升温至200℃使亚乙基-双乙酰胺裂解,如此制得乙烯乙酰胺195g(产率76%)。
(2)乙烯乙酰胺的聚合
在以上制得的乙烯乙酰胺红棕色混合溶液460g中加入甲醇570mL,用离子交换树脂处理后,再加甲醇,制成10%~50%的乙烯乙酰胺单体溶液。之后,加入一定量的偶氮二异丁腈(AIBN)催化剂,在65℃下聚合,得到黏稠的聚合物溶液。然后加入大量(15L)丙酮,使聚合物沉淀析出,再经过滤、真空干燥(80℃),制成粗聚乙烯乙酰胺459g。该聚合物为黄色细粒,分子量在200000左右。
(3)聚乙烯乙酰胺水解制取聚乙烯胺
在以上制得的聚乙烯乙酰胺中加入1000mL水,再加入热浓盐酸1000mL,在97~106℃下加热回流19h,再加水回流27h,然后再加浓盐酸1000mL,使聚合物沉淀析出。最后将混合物冷却至18℃,使聚合物滗析分出,再于50~75℃下真空干燥,如此可制得棕色的聚乙烯胺盐酸盐固体颗粒332g(产率77%)。
4.3.11.2 聚丙烯酰胺的Hofmann降解反应
聚丙烯酰胺经Hofmann降解反应进行部分胺化可以制得具有不同胺化度的聚乙烯胺的报道出现于20世纪50年代,其反应式为:
主反应:

副反应:


具体的实验步骤如下[37,38]:将次氯酸钠和氢氧化钠水溶液置于250mL三口烧瓶中,用冰盐浴冷却至-10~-15℃;加入聚丙烯酰胺水溶液,反应1h后,加入第二批氢氧化钠水溶液,继续反应1h,再换作冰浴反应。反应结束后,将反应液倾入4倍体积甲醇中,过滤,用甲醇洗涤滤饼至滤液pH值为7~8。再将滤饼溶于少量水中,用6mol/L的盐酸进行中和,放出二氧化碳气体。中和完毕后保持溶液pH值为2。最后将该溶液倾入4倍体积甲醇中析出固体,过滤、干燥得到聚乙烯胺盐酸盐固体,置于干燥器中保存。胡志勇等[37,38]发现:
①聚丙烯酰胺质量分数小于5%时,产品胺化度随着其质量分数的增加而增加,当聚丙烯酰胺质量分数大于5%时,产品胺化度随着其质量分数的增加有所降低;
②当n(NaOCl)/n(PAA)=1,n(NaOH)/n(PAA)=1(反应初期),n(NaOH)/n(PAA)=30(反应后期),反应时间为10h时,产物的胺化度相应达到极值(88%);
③由聚丙烯酰胺降解重排得到的聚乙烯胺盐酸盐存在两个主要失重区,随着胺化度的提高,产物的热稳定性有所降低。
目前人们普遍认为聚丙烯酰胺的Hofmann降解反应的转化率在60%左右。为了抑制水解副反应的发生,可以用乙二醇作溶剂,用乙二醇单钠盐作催化剂先合成了聚(N-乙烯基-2-羟乙基)碳酸酯,而后水解得到聚乙烯胺,收率可达92%以上。但是由于聚丙烯酰胺在乙二醇中的溶解度有限,因而在反应过程中需使用过量的乙二醇作溶剂,而且乙二醇的沸点较高,不利于溶剂的回收利用。同时聚(N-乙烯基-2-羟乙基)碳酸酯的水解十分困难,从而限制了该方法的使用。
4.3.11.3 聚(N-甲/乙酰胺)乙烯胺的水解[39]
用乙醛和乙酰胺为原料,经缩合、热解、聚合、水解等步骤制得聚乙烯胺,其反应路线为:

中间体聚(N-甲/乙酰胺)乙烯胺的收率可达80%~85%,而水解生成聚乙烯胺盐酸盐的反应收率大于90%。产物的胺化度在97%以上。在该反应中,亚乙基二甲/乙酰胺是合成N-乙烯基甲/乙酰胺最重要的中间体,这主要是因为这种产物比较稳定,而且可以有效地热解为N-乙烯基甲/乙酰胺。
4.3.12 聚乙烯亚胺
聚乙烯亚胺以1,2-亚乙基胺为原料,于水或各种有机溶剂中进行酸性催化聚合而成。聚合温度90~110℃,引发剂可选用二氧化碳、无机酸或二氯乙烷等[19]。根据需要,如制取高分子量产品,可使用双官能团的烷基化剂如氯甲基环氧乙烷或二氯乙烷;而要生产低分子量产品,则可使用低分子量胺如乙二胺进行聚合。由以上方法制得的聚合物分子量可在300~106之间,进而根据需要可制成分子量范围在103~105的系列产品。
实例:将12.2kg水、1.22kg氯化钠和200mL二氯乙烷加入反应器内,该反应器装有搅拌器、温度计,底部出口设有齿轮泵,泵的出口与反应器顶部相连。反应器逐渐升温至80℃,并在2h内将5.9kg 1,2-亚乙基胺加入混合物中进行聚合反应,在加料的同时开动齿轮泵使反应液循环,每循环一次混合液大约10min。在不停的搅拌下,持续反应4h,待测定反应液的黏度逐渐增至最大值时,即达到终点。所得产品固体含量的质量分数为33%,黏度2.13mm2/s(1%溶液),絮凝速率为33cm/min[40]。